Реферат по теме выпускной работы
- Вступ
- 1. Стан питання. Мета і задачі дослідження
- 2. Характеристика магістрального конвеєрного транспорту як об'єкта автоматизації
- 3. Критичний огляд існуючих технічних рішень в області автоматизованого керування магістральним конвеєрним транспортом шахти
- 4. Розробка імітаційної моделі системи підземного транспорту шахти
- 5. Розробка алгоритму керування підземним конвеєрним транспортом шахти
- 6. Практична реалізація системи автоматичного керування магістральним конвеєрним транспортом шахти
- Висновки
- Список літератури
Вступ
Конвеєрний вид транспорту зайняв домінуюче становище на вугільних шахтах з середини 70-х років минулого століття. Сучасний підземний транспортний комплекс вугільної шахти представлений розгалуженою системою, яка виконує технологічні транспортні завдання.
1. Стан питання. Мета і задачі дослідження
Через особливості технологічного процесу видобутку і транспортування корисної копалини підземний конвеєрний транспорт постійно працює в умовах нерівномірності вантажопотоків.
Продуктивність конвеєрних ліній в більшості випадків є суттєво завищеною, що пов'язано зі змінною топологією транспортної мережі шахти [1]. Таким чином, завантаженість конвеєрних ліній знижується, що зменшує коефіцієнт використання конвеєрів, що входять в лінію [2].
Такий запас по продуктивності закладається при відсутності можливості керування нерівномірністю існуючих вантажопотоків, розподілених в просторі і часі.
Прийнявши до уваги одну з сучасних тенденцій розвитку гірничих підприємств, яка полягає в зниженні витрат електроенергії на видобуток корисних копалин, можна сформулювати мету роботи – підвищення ефективності роботи магістрального конвеєрного транспорту в умовах нерівномірності вантажопотоків шляхом створення системи автоматичного управління.
Для досягнення цієї мети необхідно вирішити такі завдання:
- дослідити особливості технологічного процесу роботи магістрального конвеєрного транспорту шахти;
- проаналізувати існуючі технічні рішення в області автоматизації підземного конвеєрного транспорту;
- розробити імітаційну модель системи підземного транспорту шахти, що працює в умовах нерівномірності вантажопотоків;
- дослідити режими роботи підземного конвеєрного транспорту спільно з накопичувальними бункерами і визначити поєднання параметрів, яке забезпечує мінімальну питому витрату електроенергії;
- розробити технічні рішення щодо практичної реалізації системи автоматичного керування магістральним конвеєрним транспортом шахти.
2. Характеристика магістрального конвеєрного транспорту як об'єкта автоматизації
Підземний конвеєрний транспорт – це послідовний технологічний ланцюг, що складається з дільничного і магістрального транспорту, а також накопичувальних бункерів, який об'єднаний вантажопотоками. У місцях злиття різних елементів транспортної мережі відбувається перевантаження твердого матеріалу з одного конвеєра на інший, або підсумовування вантажопотоків з декількох забоїв на збірний конвеєр.
Для підземного конвеєрного транспорту можна виділити три основні режими роботи: пуск, робота, зупинка.
Пусковий режим є найбільш важким режимом, який може супроводжуватися значними динамічними навантаженнями і моментом опору. З цього випливає необхідність реалізації апаратурою автоматизації плавного пуску, щоб в початковий момент зрушення забезпечити плавний вибір люфтів в трансмісії, запобігти пробуксовку стрічки на приводному барабані. До того ж існує необхідність в мінімальної тривалості процесу пуску, щоб зменшити час впливу пускових струмів на приводні електродвигуни. Пуск конвеєрного транспорту здійснюється в напрямку, протилежному вантажопотоку, при цьому кожен наступний конвеєр запускається тільки після встановлення номінальної швидкості руху тягового органу попереднього конвеєра.
У робочому режимі здійснюється транспортування корисної копалини з очисного забою дільничними конвеєрами до магістральних конвеєрних ліній і далі – до шахтної підйомної установки в головному стовбурі шахти або по похилому стволу прямо на поверхню. При цьому можуть виникати різні аварійні ситуації.
Режим зупинки конвеєрного транспорту здійснюється по команді від оператора, а також при виникненні або загрозі виникнення аварійної ситуації. При цьому повинна забезпечитися автоматична зупинка конвеєрів, що транспортують вантаж на відмовивший конвеєр, а також блокування повторного дистанційного вмикання при спрацьовуванні будь-яких захистів.
3. Критичний огляд існуючих технічних рішень в області автоматизованого керування магістральним конвеєрним транспортом шахти
На сьогоднішній день при автоматизації підземного конвеєрного транспорту застосовуються такі засоби і системи автоматизації: УКЛ.1, АУК.1М і АУК.2М.
Представлені вище засоби і системи автоматизації набули широкого поширення. Однак, їм притаманні такі недоліки: моральне і технічне старіння; неможливість керування протяжними конвеєрними лініями, які складаються з безлічі конвеєрів, а також мають безліч відгалужень; неможливість енергоефективної роботи в умовах нерівномірності вантажопотоків, що надходять з відгалужень на збірний конвеєр, що призводить до роботи конвеєрів в режимі холостого ходу і т. д.
До сучасних мікропроцесорних комп'ютерно-інтегрованих автоматизованих систем моніторингу та керування підземним конвеєрним транспортом шахт відносяться: АУК.3, САУКЛ, АСКУ КЛ, АСУ КЛ, підсистема керування транспортним ланцюгом УТАС.
Зазначені комплекси є представниками сучасної апаратури автоматизації підземного конвеєрного транспорту шахт, однак, їм також притаманні недоліки: неможливість забезпечення в повній мірі функції автоматичного контролю теплових режимів роботи окремих елементів конвеєра (приводний барабан, конвеєрна стрічка, роликоопори), що може призводити до виникнення аварійних ситуацій; неможливість синхронізації в часі роботи бункерного обладнання в умовах нерівномірності вантажопотоків.
За підсумками аналізу функціональних можливостей і складу зазначених комплексів в якості базової апаратури автоматизованого керування магістральним конвеєрним транспортом шахти прийнятий комплекс АУК.3.
Апаратура АУК.3 є багаторівневою системою автоматизованого управління і складається з програмно-апаратного комплексу верхнього рівня і комплексу автоматизованого керування конвеєрними лініями нижнього рівня.
Комплекс АУК.3 є подальшим розвитком функціональних можливостей апаратури АУК.1М і забезпечує виконання більш 70 функцій з управління, блокувань і сигналізації. Основними є такі функції:
- управління конвеєрною лінією (телемеханічний канал);
- управління механізмами конвеєра (пускачі приводних двигунів і гальма);
- контроль захистів і блокувань конвеєра (включаючи пробуксовку приводного барабана);
- відображення та передача інформації (в текстовому вигляді) на пульт управління;
- визначення типу датчика, що спрацював і т. д.
4. Розробка імітаційної моделі системи підземного транспорту шахти
Для аналізу структурної схеми підземної транспортної мережі шахти розроблена імітаційна модель, що враховує
випадковий характер зміни вантажопотоків, технологічні параметри і режими роботи елементів
очисний забій
, конвеєрна лінія
, накопичувальний бункер
і підйомна установка
.
Імітаційне моделювання транспортної мережі вироблялося з використанням
мереж Петрі [8].
Дуги, що з'єднують безліч позицій з безліччю переходів, мають два напрямки – від позиції до переходу і навпаки. Вага дуги визначає кількість токенів, яку переносить дуга в одиницю часу від одного елемента схеми до іншого. Вага дуг моделі конвеєрної лінії визначається конвеєром з найменшою пропускною здатністю (теоретичною продуктивністю). Вага дуг моделі роботи підйомної установки визначається вантажопідйомністю застосованої судини.
На малюнку 1 приведена розроблена імітаційна модель системи підземного транспорту шахти у вигляді мережі Петрі. Дослідження розробленої імітаційної моделі роботи транспортної мережі гірничого підприємства здійснювалося із застосуванням програмного пакету HPSim 1.1.
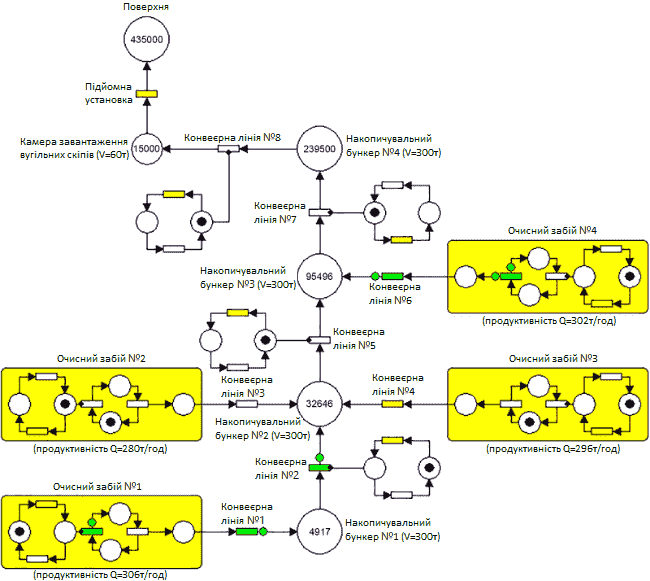
Малюнок 1 – Імітаційна модель системи підземного транспорту шахти
Безперервний потік визначається рухом по транспортній мережі дискретних обсягів вантажу умовної масою один кілограм. Час моделювання склав 21600 одиниць модельного часу, що відповідає шестигодинний робочій зміні на шахті. Результати імітаційного моделювання роботи очисних забоїв, накопичувальних бункерів і процесу транспортування корисної копалини на поверхню шахти представлені на малюнках 2, 3 і 4 відповідно.
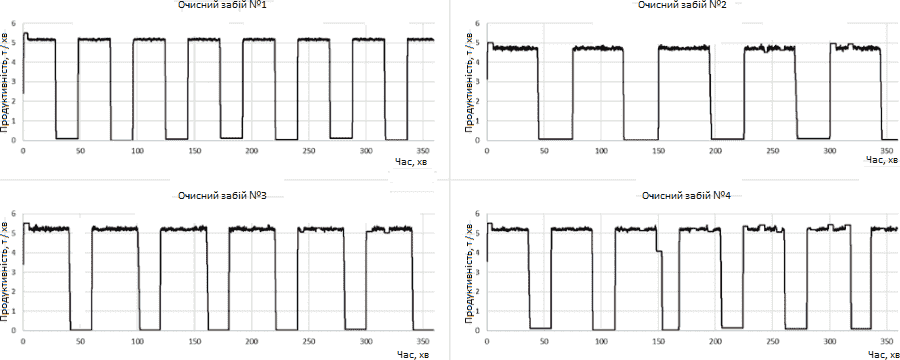
Малюнок 2 – Результати моделювання роботи очисних забоїв
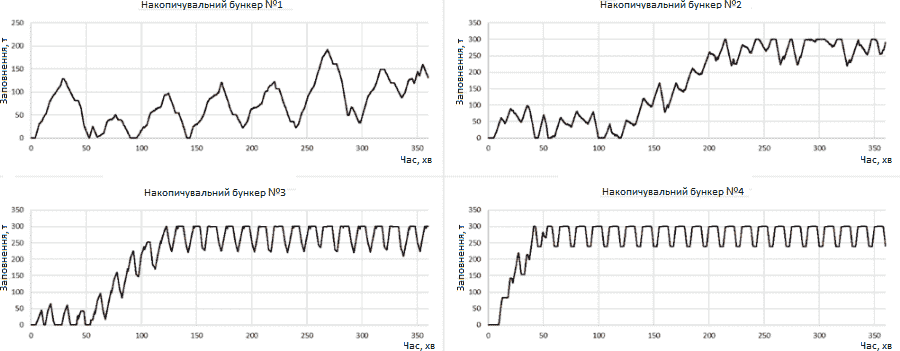
Малюнок 3 – Результати моделювання роботи накопичувальних бункерів
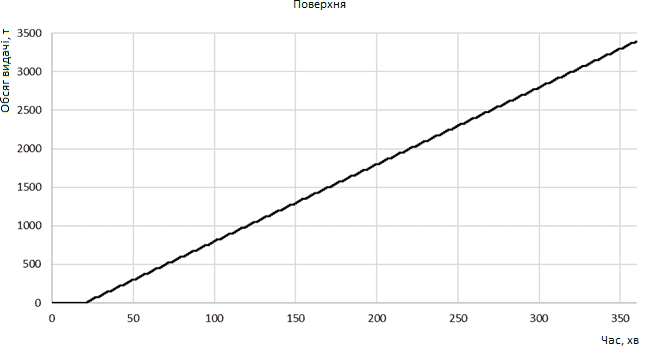
Малюнок 4 – Результати моделювання вантажопотоку вугілля на поверхню шахти
Аналіз результатів моделювання показує, що регулювання продуктивності магістрального конвеєрного транспорту шляхом синхронізації вантажопотоків в часі з використанням накопичувальних бункерів дозволяє знизити час непродуктивного використання транспортного обладнання, підвищує енергоефективність роботи конвеєрного транспорту, збільшує термін служби технологічного обладнання та установок.
5. Розробка алгоритму керування підземним конвеєрним транспортом шахти
Під час зупинки транспортної системи шахти очисні забої повинні мати однаковий часовий інтервал роботи на загальний накопичувальний бункер. Виходячи з викладеного, раціональний рівень заповнюваності бункера твердим матеріалом визначається з виразу:

де Hmaxб – максимальна висота завантаження бункера, м;
Xj – усереднений вантажопотік j-го очисного забою, м3/хв;
Siб – площа перерізу i-го бункера, м2;
Hiб – діючий рівень в i-му бункеру, м;
Sjб – площа перерізу j-го бункера, м2;
Xi – сумарний вантажопотік з очисних забоїв в j-й бункер, м3/хв;
k – кількість бункерів.
Момент включення бункерних живильників визначається за їх умовним номером згідно з критерієм транспортного запізнювання. Таким чином, якщо після бункерного живильника з меншим умовним номером повинен ввімкнутися живильник з більшим умовним номером – для винятку просипання корисних копалин, ввімкнення повинно відбутися після моменту звільнення від вантажу стрічки під живильником. У разі якщо після бункерного живильника з більшим умовним номером повинен ввімкнутися живильник з меншим умовним номером – для винятку режиму холостого ходу конвеєрної лінії на час транспортного запізнювання момент часу включення i-го живильника визначається з виразу:

де ti−1вкл – момент часу увімкнення живильника попереднього бункера;
tцбп – тривалість циклу роботи бункерного живильника, хв;
Tзп – транспортне запізнювання від бункера з більшим умовним номером до бункера з меншим умовним номером, хв.
Включення бункерних живильників здійснюється послідовно, за критерієм максимального відхилення прогнозного значення рівня твердого матеріалу від розрахункового значення на момент розвантаження бункера. Прогнозне значення рівня твердого матеріалу в бункері для даного моменту часу визначається з виразу:

де Hjб – діючий рівень твердого матеріалу в j-му бункеру, м;
Xi – сумарний вантажопотік з очисних забоїв в j-й бункер, м3/хв;
Tjп – транспортне запізнювання останнього розвантаженого пакета, хв;
Tjб – транспортне запізнювання j-го бункера, хв;
X3 – усереднена за один цикл роботи величина хвилинного вантажопотоку з живильника, м3/хв;
Sjб – площа перерізу j-го бункера, м2.
З метою підвищення ефективності роботи підземного конвеєрного транспорту розроблена система автоматизованого керування, алгоритм функціонування якої приведений на малюнку 5.
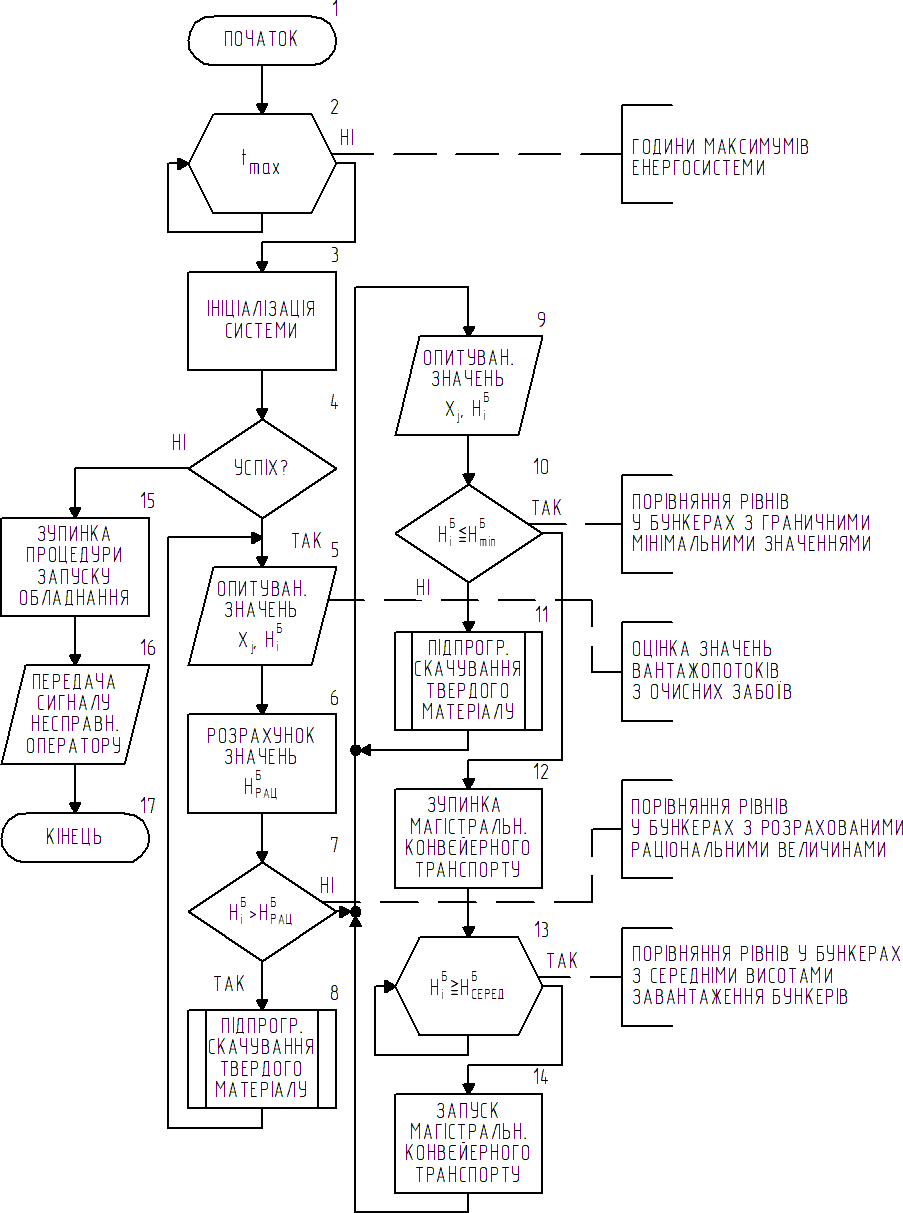
Малюнок 5 – Алгоритм системи автоматизованого керування конвеєрним транспортом шахти
Процес розвантаження бункера включає в себе підготовку транспортної системи до роботи і вивантаження корисної копалини з бункерів до мінімально допустимої висоти завантаження. Перед початком роботи система автоматизованого управління перевіряє умову на заборону роботи в години максимуму енергосистеми tmax з наступною ініціалізацією окремих елементів.
При успішній ініціалізації оцінюються миттєві значення вантажопотоків з дільничних бункерів Xj і рівні твердого матеріалу в бункерах Hiб.
На підставі отриманих даних визначаються раціональні рівні завантаження бункерів корисними копалинами Hрацб. Якщо фактичні значення рівня твердого матеріалу в бункерах перевищують розрахункові значення – виконується підпрограма вивантаження твердого матеріалу (мал. 6).
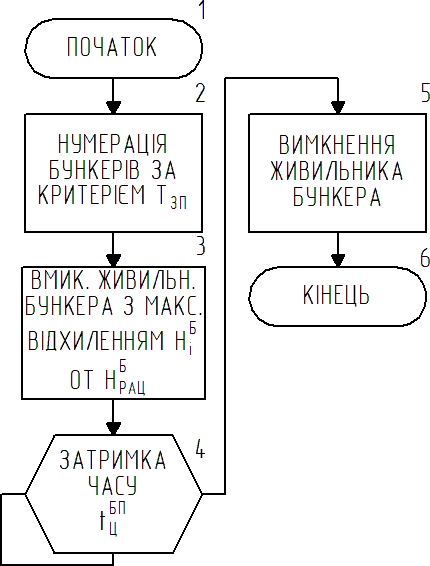
Малюнок 6 – Блок-схема підпрограми вивантаження твердого матеріалу
За оновленими даними проводиться визначення наступного бункера з найбільшим відхиленням рівня завантаження Hiб від розрахункового, раціонального значення Hрацб. Підготовка транспортної системи до роботи триває до моменту, поки фактичні рівні завантаження бункерів твердим матеріалом не стануть меншими або рівними розрахунковим значенням. Якщо ініціалізація системи не відбулася – здійснюється зупинення процедури запуску обладнання. Одночасно з цим відбувається передача інформації про характер несправності оператору системи.
Далі здійснюється вивантаження корисної копалини з бункерів до мінімальних значень завантаження Hminб. При цьому відслідковуються значення вантажопотоків з очисних забоїв Xj і рівні твердого матеріалу в бункерах Hiб. Якщо фактичні значення рівнів твердого матеріалу в бункерах перевищують мінімальні висоти завантаження – ініціюється виконання підпрограми вивантаження твердого матеріалу (мал. 6).
Після досягнення в бункерах мінімальних висот завантаження Hminб магістральний конвеєрний транспорт примусово зупиняється. Відновлення роботи магістрального конвеєрного транспорту відбувається при досягненні середньої висоти завантаження Hсередб окремого бункера, що входить в транспортний ланцюг.
6. Практична реалізація системи автоматичного керування магістральним конвеєрним транспортом шахти
Структура системи моніторингу та автоматичного керування роботою підземного конвеєрного транспорту шахти являє собою комп'ютерно-інтегровану дворівневу систему керування, елементи якої пов'язані між собою промисловою інформаційною мережею.
Верхній рівень являє собою систему централізованого автоматизованого моніторингу та управління підземним транспортом шахти, який виконує наступні функції:
- діагностування та відображення в графічному вигляді стану кожного конвеєра;
- розшифровка причини аварійних і оперативних зупинок в графічній (зміна кольору на схемі) і в текстовій формі (коментарі);
- протоколювання параметрів технологічного процесу та історії процесу управління;
- формування порад з оперативного керування конвеєрним транспортом в залежності від вантажопотоку.
На нижньому рівні система представлена двома підсистемами: підсистема керування конвеєрним транспортом і підсистема керування накопичувальними бункерами. Узагальнена структурна схема приведена на малюнку 7.
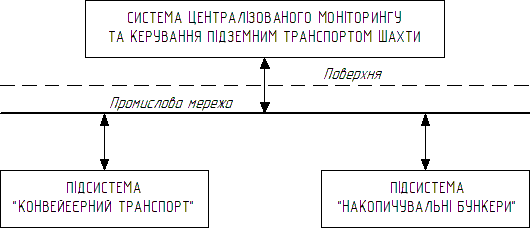
Малюнок 7 – Структурна схема системи автоматичного керування роботою підземного конвеєрного транспорту шахти
Мережа передачі даних верхнього рівня є промисловим Ethernet, що працює за стандартом PROFINET, який використовує протоколи TCP/IP, RT і IRT.
Нижній рівень являє собою електричну мережу з шинної топологією RS-485, яка працює за стандартом Profibus з протоколом Profibus DP.
Для здійснення автоматичного вимірювання маси твердого матеріалу на конвеєрах застосовуються ваги конвеєрні автоматичні ВКАУ.
Автоматичний контроль теплових режимів роботи елементів конвеєра здійснюється апаратурою АКТЛ-1.
Безперервне вимірювання рівнів заповнення накопичувальних бункерів здійснюється апаратурою контролю рівня гірничої маси АГКМ.
Висновки
В результаті аналізу режимів і особливостей технологічного процесу роботи магістрального конвеєрного транспорту сформульовані вимоги до системи автоматичного управління.
Аналіз існуючих технічних рішень в області автоматизації підземного конвеєрного транспорту показав, що представлені на ринку системи і засоби автоматизації мають недоліки, до яких слід віднести неможливість енергоефективної роботи в умовах нерівномірності вантажопотоків, а також відсутність контролю теплових режимів роботи елементів конвеєра.
Розроблено імітаційну модель системи підземного транспорту шахти, що працює в умовах нерівномірності вантажопотоків.
Під час дослідження режимів роботи підземного конвеєрного транспорту спільно з накопичувальними бункерами розроблений алгоритм системи автоматизованого управління конвеєрним транспортом шахти, що дозволяє знизити нерівномірності вантажопотоків, підвищити енергоефективність роботи шахтного конвеєрного транспорту, збільшити ресурс роботи технологічного обладнання.
Система автоматичного керування магістральним конвеєрним транспортом шахти реалізована на двох рівнях із
застосуванням промислових мереж. У підсистемі верхнього рівня прийнятий стандарт промислового Ethernet з
використанням протоколів: TCP/IP, RT і IRT. Підсистеми нижнього рівня Конвеєрний транспорт
та
Накопичувальні бункери
організовані за допомогою промислової мережі стандарту Profibus з
використанням протоколу Profibus DP.
При написанні цього реферату магістерська робота ще не завершена. Остаточне завершення: червень 2021 року.
Список літератури
- Шахмейстер, Л. Г. Вероятностные методы расчета транспортирующих машин [Текст] / Л. Г. Шахмейстер, В. Г. Дмитриев. – М.: Машиностроение, 1983. – С. 67–69.
- Петков, О. Н. Разработка и исследование системы автоматического управления скоростью
ленточного конвейера по входному грузопотоку: автореф. дис. на сосиск. уч. степени
канд. техн. наук: спец. 05.13.07
Автоматизация процессов управления
/ Петков О. Н. – Москва, 2007. – 20 с. - Заика, В. Т. Методы повышения эффективности электроснабжения и энергоиспользования подземных горных машин и установок угольных шахт: Дис. д-ра техн. наук: 05.09.03 / [Национальная горная академия Украины]. – Днепропетровск, 2001. – 350 c.
- Шахмейстер, Л. Г. Тяговые расчеты ленточных конвейеров / Шахмейстер Л. Г., Дмитриев В. Г. – М. [МГИ]. 1969. – 108 с.
- Разумный, Ю. Т. Энергосбережение / Разумный Ю. Т., Заика В. Т., Степаненко Ю. В. – Днепропетровск: [НГУ], 2008. – 164 с.
- Рудничный транспорт и механизация вспомогательных работ / Под ред. Б. Ф. Братченко. – М.: Недра, 1978. – 423 c.
- Шахмейстер, Л. Г. Подземные конвейерные установки / Л. Г. Шахмейстер, Г. И. Солод. – Москва: Недра, 1976. – 429 с.
- Васильев В. В., Кузьмук В. В. Сети Петри, параллельные алгоритмы и модели мультипроцессорных систем. – Киев.: Наук. Думка, 1990. – 212 с.