Реферат по теме выпускной работы
- Введение
- 1. Состояние вопроса. Цель и задачи исследования
- 2. Характеристика магистрального конвейерного транспорта как технологического объекта автоматизации
- 3. Критический обзор существующих технических решений в области автоматизированного управления магистральным конвейерным транспортом шахты
- 4. Разработка имитационной модели системы подземного транспорта шахты
- 5. Разработка алгоритма управления подземным конвейерным транспортом шахты
- 6. Практическая реализация системы автоматического управления магистральным конвейерным транспортом шахты
- Выводы
- Список литературы
Введение
Конвейерный вид транспорта занял доминирующее положение на угольных шахтах с середины 70-х годов прошлого столетия. Современный подземный транспортный комплекс угольной шахты представлен разветвленной системой, которая выполняет технологические транспортные задачи, среди них:
- транспортирование полезного ископаемого от мест выемки к шахтной подъемной установке в околоствольном дворе, либо напрямую на поверхность по наклонному стволу шахты;
- перемещение горной массы из подготовительных забоев к околоствольному двору или на поверхность шахты;
- доставка материалов и технологического оборудования, а также людей (если есть соответствующие типы конвейеров) к местам назначения.
1. Состояние вопроса. Цель и задачи исследования
Из-за особенностей технологического процесса добычи и транспортировки полезного ископаемого подземный конвейерный транспорт постоянно работает в условиях неравномерности грузопотоков.
При проектировании транспортных систем горных предприятий, как правило, задаются максимальной суммарной производительностью по линии очистных забоев, что существенно завышает производительность подземных конвейерных линий и связано с изменяющейся топологией транспортной сети шахты [1]. Таким образом, загруженность конвейерных линий снижается, что уменьшает коэффициент использования конвейеров, входящих в линию [2].
Такой запас по производительности закладывается при отсутствии возможности управления неравномерностью существующих грузопотоков, распределенных в пространстве и времени, что влечет за собой:
- работу подземного транспортного комплекса в непроизводительном режиме;
- значительное повышение затрат на электроэнергию, которые могут превышать нормативные значения в три и более раза, так как для минимизации удельного расхода электроэнергии необходимо, чтобы технологическое оборудование было загружено ближе к номинальной производительности, что не выполняется [3, 4, 5];
- снижение ресурса технологического оборудования и т. д.
Приняв во внимание одну из современных тенденций развития горных предприятий, которая заключается в снижении затрат электроэнергии на добычу полезного ископаемого, можно сформулировать цель работы – повышение эффективности работы магистрального конвейерного транспорта в условиях неравномерности поступающих грузопотоков путем создания системы автоматического управления.
Для достижения этой цели необходимо решить следующие задачи:
- исследовать особенности технологического процесса работы магистрального конвейерного транспорта шахты;
- проанализировать существующие технические решения в области автоматизации подземного конвейерного транспорта;
- разработать имитационную модель системы подземного транспорта шахты, работающего в условиях неравномерности грузопотоков;
- исследовать режимы работы подземного конвейерного транспорта совместно с аккумулирующими бункерами и определить сочетание параметров, которое обеспечивает минимальный удельный расход электроэнергии;
- разработать технические решения по практической реализации системы автоматического управления магистральным конвейерным транспортом шахты.
2. Характеристика магистрального конвейерного транспорта как технологического объекта автоматизации
Подземный конвейерный транспорт – это последовательная технологическая цепочка, состоящая из участкового и магистрального транспорта, а также аккумулирующих бункеров, которая объединена формируемым забоями грузопотоком. В местах слияния различных элементов транспортной сети происходит перегрузка твердого материала с одного конвейера на другой, либо суммирование грузопотоков из нескольких забоев на сборный конвейер.
Структура и топология транспортной сети на каждом предприятии уникальна и напрямую обусловлена технологическим процессом добычи и транспортировки полезного ископаемого на конкретной угольной шахте. Традиционная структура расположения конвейеров являет собой древовидный граф с корнем у главного ствола шахты (рис. 1).
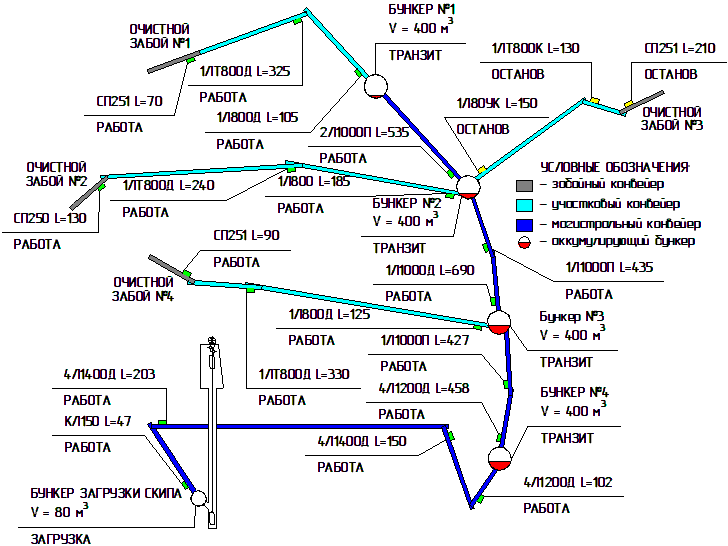
Рисунок 1 – Схема конвейерных линий шахты (анимация: количество кадров – 15; количество повторов – 6; задержка между кадрами – 1 с; размер анимации – 35 КБ)
Достоинства конвейерного транспорта: высокая производительность (от 300 т/ч при ширине ленты 800 мм до 3000 т/ч при ширине 1600 мм) и широкий диапазон рационального использования; непрерывность процесса транспортирования; возможность транспортирования твердого материала по наклонным горным выработкам (±18°); высокая надежность, а также коэффициент готовности (0,90–0,96 – для одиночного ленточного конвейера); простота и удобство сопряжения с технологическим оборудованием очистных и подготовительных забоев; технологическая приспособленность для автоматизации и централизованного управления из чего следует низкая трудоемкость обслуживания (1–4 человека в смену на один конвейер за сутки), высокая безопасность работ и улучшение условий труда [6].
Недостатки конвейерного транспорта: быстрый износ грузонесущего органа; сложность применения промежуточных приводов, что ведет к увеличению степени натяжения ленты с ростом длины конвейера, а значит – к необходимости повышения прочности ленты и мощности приводных станций [7].
В технологическом процессе транспортирования полезного ископаемого на угольных шахтах ленточные конвейеры применяются для организации участкового и магистрального транспорта, а скребковые – для организации доставки полезного ископаемого или горной массы из очистных и подготовительных забоев соответственно. В некоторых случаях скребковые конвейеры используются в качестве перегружателей для подачи твердого материала на другие средства транспорта.
Ленточный конвейер являет собой транспортирующий механизм непрерывного действия, грузонесущий орган которого объединен с тяговым в виде замкнутой гибкой ленты. На рисунке 2 представлена кинематическая схема ленточного конвейера 1Л100, где: 1 – барабан головной секции; 2 – головная секция; 3 – натяжной барабан; 4 – натяжное устройство; 5 – центрирующая роликоопора; 6 – промежуточная секция; 7 – переходные стойки; 8 – роликоопоры; 9 – натяжная стойка; 10 – поддерживающий канат; 11 – промежуточная стойка; 12 – нижний ролик; 13 – загрузочное устройство; 14 – орошение; 15 – концевая секция; 16 – барабан концевой секции.

Рисунок 2 – Кинематическая схема конвейера 1Л100
Для подземного конвейерного транспорта можно выделить три основных режима работы: пуск, работа, остановка.
Пусковой режим является наиболее тяжелым режимом, который может сопровождаться значительными динамическими нагрузками и моментом сопротивления. Из этого следует необходимость реализации аппаратурой автоматизации плавного пуска, чтобы в начальный момент трогания обеспечить безударный выбор люфтов в трансмиссии, предотвратить пробуксовку ленты на приводном барабане. Также существует необходимость в минимальной продолжительности процесса пуска, чтобы уменьшить время воздействия пусковых токов на приводные электродвигатели. Пуск конвейерного транспорта осуществляется в направлении, обратном грузопотоку, при этом каждый следующий конвейер запускается только после установления номинальной скорости движения тягового органа предыдущего конвейера.
В рабочем режиме осуществляется транспортировка полезного ископаемого из очистного забоя участковыми конвейерами к магистральным конвейерным линиям и далее – к шахтной подъемной установке в главном стволе шахты либо по наклонному стволу прямо на поверхность. При этом могут возникать различные аварийные ситуации, например:
- заштыбовка, возникающая в местах перегрузки;
- отклонение скорости движения грузонесущего органа от номинала выше либо ниже допустимых пределов;
- нарушение центрирования хода ленты, что приводит к сходу ленты с роликоопор;
- пробуксовка приводных барабанов относительно ленты;
- перегрев приводных барабанов;
- ослабление натяжения ленты;
- порыв ленты;
- отклонение тока нагрузки приводных электродвигателей и т. д.
Также возникают отклонения технологического режима работы подземного конвейерного транспорта из-за неравномерности по величине и дискретности во времени грузопотока. Вследствие этого приводные электродвигатели работают с переменными нагрузками, изменение которых сложно предсказать из-за случайного характера грузопотока.
Режим остановки конвейерного транспорта осуществляется по команде от оператора, а также при возникновении или угрозе возникновения аварийной ситуации. При этом должна обеспечиться автоматическая остановка конвейеров, транспортирующих груз на отказавший конвейер, а также блокировка повторного дистанционного включения при срабатывании каких-либо защит.
Кроме того, работа конвейерного транспорта должна осуществляться в соответствии с правилами безопасности и специальными нормативными документами, регламентирующими эксплуатацию конвейеров в подземных условиях шахт для транспортировки полезного ископаемого и горной массы.
3. Критический обзор существующих технических решений в области автоматизированного управления магистральным конвейерным транспортом шахты
В настоящее время при автоматизации подземного конвейерного транспорта применяются следующие средства и системы автоматизации:
- комплекс автоматизированного управления конвейерными линиями УКЛ.1;
- комплексы автоматизированного управления конвейерами АУК.1М и АУК.2М.
Представленные выше средства и системы автоматизации получили широкое распространение. Однако, им присущи следующие недостатки: моральное и техническое устаревание; невозможность управления протяженными конвейерными линиями, которые состоят из множества конвейеров, а также имеют множество ответвлений; невозможность энергоэффективной работы в условиях неравномерности грузопотоков, поступающих с ответвлений на сборный конвейер, что приводит к работе конвейеров в режиме холостого хода и т. д.
К современным микропроцессорным компьютерно-интегрированным автоматизированным системам мониторинга и управления подземным конвейерным транспортом шахт относятся:
- комплекс автоматизированного управления конвейерными линиями АУК.3;
- система автоматизированного управления разветвленными конвейерными линиями САУКЛ;
- подсистема управления транспортной цепочкой в составе системы УТАС;
- автоматизированная система контроля и управления конвейерной линией АСКУ КЛ;
- система автоматизации конвейерного транспорта на базе устройств ELSAP типа АСУ КЛ.
Указанные комплексы являются представителями современной аппаратуры автоматизации подземного конвейерного транспорта шахт, однако, им также присущи недостатки: невозможность обеспечения в полной мере функции автоматического контроля тепловых режимов работы отдельных элементов конвейера (приводной барабан, конвейерная лента, роликоопоры), что может приводить к возникновению аварийных ситуаций; невозможность синхронизации во времени работы бункерного оборудования в условиях неравномерности поступающих грузопотоков.
По итогам анализа функциональных возможностей и состава указанных комплексов в качестве базовой аппаратуры автоматизированного управления магистральным конвейерным транспортом шахты принят комплекс АУК.3.
Аппаратура АУК.3 является многоуровневой системой автоматизированного управления и состоит из программно-аппаратного комплекса верхнего уровня и комплекса автоматизированного управления конвейерными линиями нижнего уровня.
Программно-аппаратный комплекс верхнего уровня АУК.3 (рис. 3) предназначен для предоставления информации о состоянии комплекса автоматизированного управления конвейерами АУК.3, его защит, блокировок, формирования базы произошедших событий и статистической обработки полученной информации.
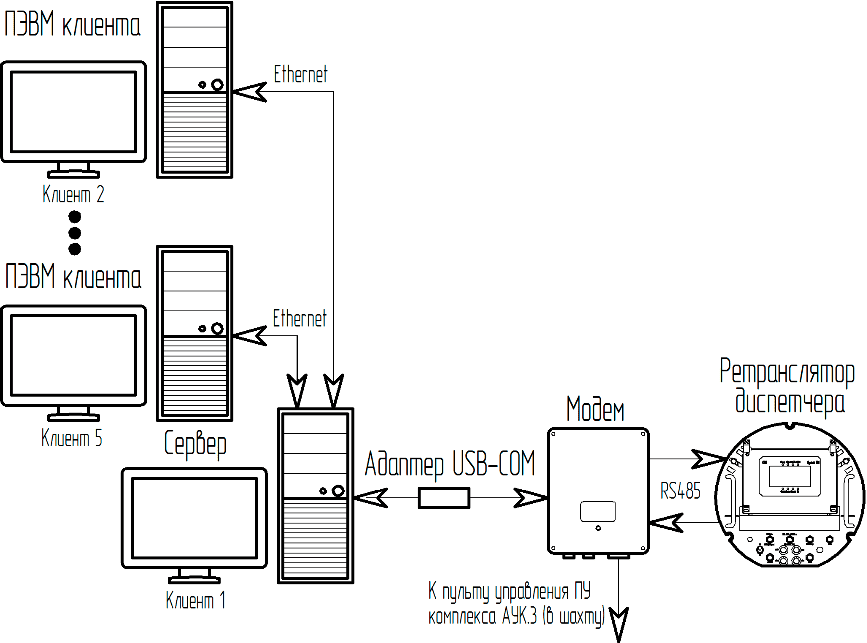
Рисунок 3 – Структура программно-аппаратного комплекса верхнего уровня АУК.3
Комплекс АУК.3 является дальнейшим развитием функциональных возможностей аппаратуры АУК.1М и обеспечивает выполнение более 70 функций по управлению, блокировкам и сигнализации (табл. 1). Основными являются следующие функции:
- управление конвейерной линией (по каналу телемеханики);
- управление механизмами конвейера (пускатели приводных двигателей и тормоза);
- контроль защит и блокировок конвейера (включая пробуксовку приводного барабана);
- отображение и передача информации (в текстовом виде) на пульт управления;
- определение типа сработавшего датчика в конвейерной линии и т. д.
Функциональные возможности: | |
Количество функций по управлению, шт | 9 |
Количество контролируемых защит и блокировок, шт | 22 |
Количество передаваемых сигналов с конвейера на ПУ, шт | 22 |
Количество управляемых приводных двигателей, шт | 2 |
Количество типов контрольных датчиков конвейера, шт | 10 |
Скорость движения ленты: | |
Контролируемая скорость движения ленты, м/с | 1,4–5,0 |
Нижний предел относительно номинальной скорости, не менее, % | 75 |
Верхний предел относительно номинальной скорости, не более, % | 108 |
Скорость, при которой выдается сигнал на наложение тормозов, м/с | 0,2–0,5 |
Значение защитной уставки пробуксовки приводного барабана, не более, % | 110 |
Программная среда построена на основе клиент-серверной модели баз данных, в которой сервер обеспечивает доступ к базе данных клиентских приложений.
Комплекс автоматизированного управления конвейерными линиями нижнего уровня АУК.3 (рис. 4) предназначен для автоматизированного управления неразветвленными конвейерными линиями, состоящими из ленточных и скребковых конвейеров с общим числом конвейеров в линии до 10 включительно, исполнительными органами накопительных бункеров, монорельсовыми канатными дорогами (грузовыми), рельсовыми канатными напочвенными дорогами (грузовыми) и моноканатными дорогами кресельного типа.
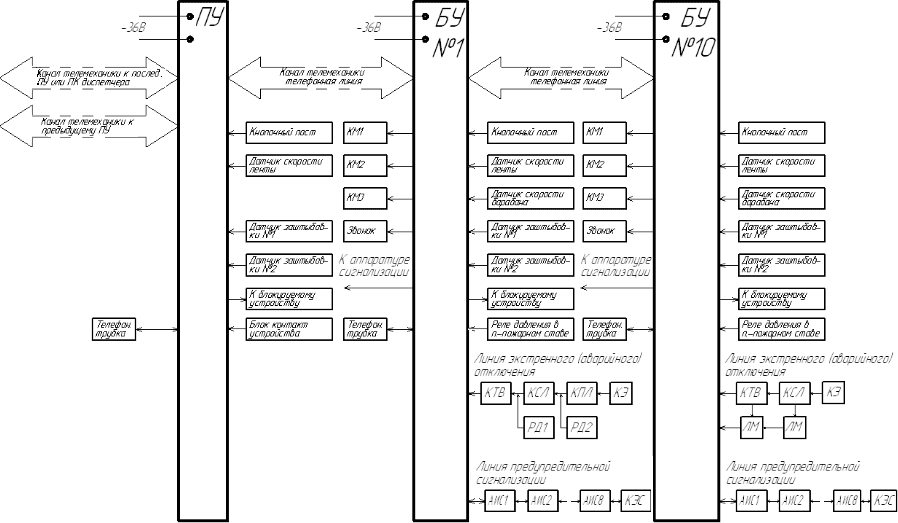
Рисунок 4 – Структурная схема комплекса АУК.3
4. Разработка имитационной модели системы подземного транспорта шахты
Для анализа структурной схемы подземной транспортной сети шахты (рис. 1) разработана имитационная
модель, учитывающая случайный характер изменения грузопотоков, технологические параметры и режимы работы
элементов очистной забой
, конвейерная линия
, аккумулирующий бункер
и
подъемная установка
. Имитационное моделирование транспортной сети производилось с использованием
сетей Петри [8].
Дуги, соединяющие множество позиций с множеством переходов, имеют два направления – от позиции к переходу и наоборот. Вес дуги определяет количество токенов, которое переносит дуга в единицу времени от одного элемента схемы к другому. Вес дуг модели конвейерной линии определяется конвейером с наименьшей пропускной способностью (теоретической производительностью). Вес дуг модели работы подъемной установки определяется грузоподъемностью применяемого сосуда.
На рисунке 5 приведена разработанная имитационная модель системы подземного транспорта шахты в виде сети Петри. Исследование разработанной имитационной модели работы транспортной сети горного предприятия осуществлялось с применением программного пакета HPSim 1.1.
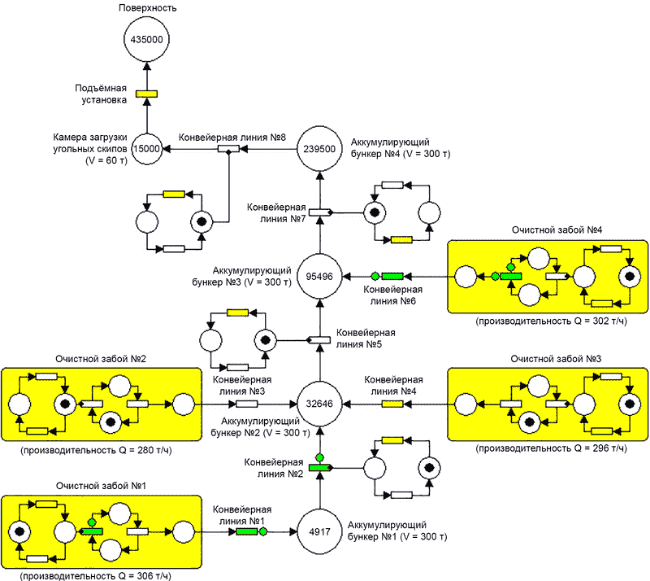
Рисунок 5 – Имитационная модель системы подземного транспорта шахты
Непрерывный поток определяется движением по транспортной сети дискретных объемов груза условной массой один килограмм. Время моделирования составило 21600 единиц модельного времени, что соответствует шестичасовой рабочей смене на шахте. Результаты имитационного моделирования работы очистных забоев, аккумулирующих бункеров и процесса транспортирования полезного ископаемого на поверхность шахты представлены на рисунках 6, 7 и 8 соответственно.
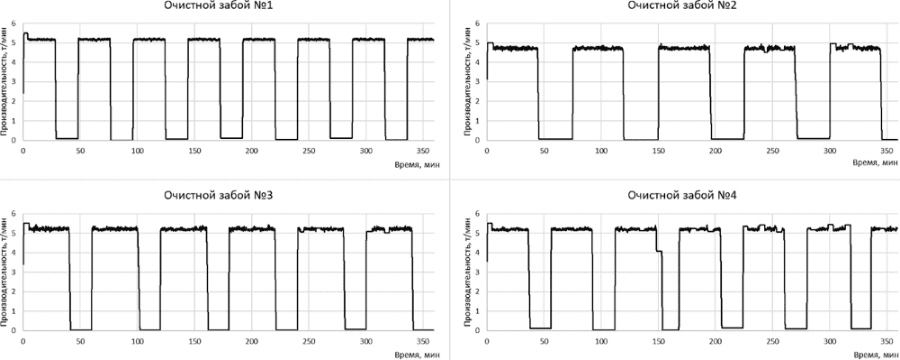
Рисунок 6 – Результаты моделирования работы очистных забоев
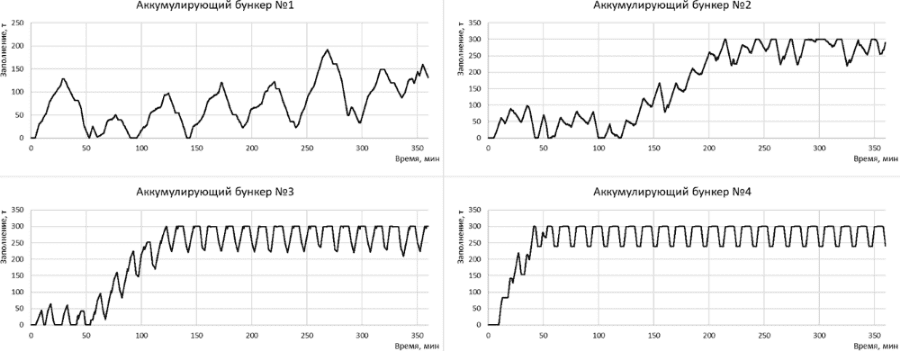
Рисунок 7 – Результаты моделирования работы аккумулирующих бункеров
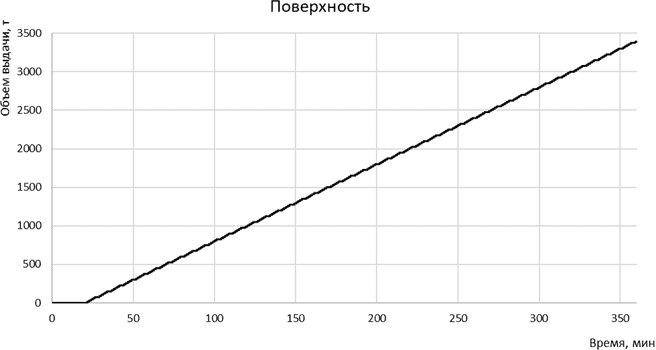
Рисунок 8 – Результаты моделирования грузопотока угля на поверхность шахты
Анализ результатов моделирования показывает, что регулирование производительности магистрального конвейерного транспорта путем синхронизации грузопотоков во времени с использованием аккумулирующих бункеров позволяет снизить время непроизводительного использования транспортного оборудования, повышает энергоэффективность работы конвейерного транспорта, увеличивает срок службы технологического оборудования и установок.
5. Разработка алгоритма управления подземным конвейерным транспортом шахты
Технологический процесс погрузки полезного ископаемого в бункер представляет собой марковский процесс, состоящий из загрузки при отключенном питателе и разгрузки при включенном питателе. Во время остановки транспортной системы шахты очистные забои должны иметь одинаковый временной интервал работы на общий аккумулирующий бункер. Исходя из вышеизложенного, рациональный уровень заполняемости бункера твердым материалом определяется из выражения:

где Hmaxб – максимальная высота загрузки бункера, м;
Xj – усредненный грузопоток j-го очистного забоя, м3/мин;
Siб – сечение i-го бункера, м2;
Hiб – текущий уровень в i-м бункере, м;
Sjб – сечение j-го бункера, м2;
Xi – суммарный грузопоток из очистных забоев в j-й бункер, м3/мин;
k – количество бункеров.
Момент включения бункерных питателей определяется по их условному номеру согласно критерию транспортного запаздывания. Таким образом, если после бункерного питателя с меньшим условным номером должен включиться питатель с большим условным номером – для исключения просыпания полезного ископаемого, включение должно произойти после момента освобождения от груза ленты под питателем. В случае если после бункерного питателя с большим условным номером должен включиться питатель с меньшим условным номером – для исключения режима холостого хода конвейерной линии на время транспортного запаздывания момент времени включения i-го питателя определяется из выражения:

где ti−1вкл – момент времени включения питателя предыдущего бункера;
tцбп – длительность цикла работы бункерного питателя, мин;
Tзп – транспортное запаздывание от бункера с большим условным номером к бункеру с меньшим условным номером, мин.
Включение бункерных питателей осуществляется последовательно, по критерию максимального отклонения прогнозного значения уровня твердого материала от расчетного значения на момент разгрузки бункера. Прогнозное значение уровня твердого материала в бункере для текущего момента времени определяется из выражения:

где Hjб – текущий уровень твердого материала в j-м бункере, м;
Xi – суммарный грузопоток из очистных забоев в j-й бункер, м3/мин;
Tjп – транспортное запаздывание последнего разгруженного пакета, мин;
Tjб – транспортное запаздывание j-го бункера, мин;
X3 – усредненная за один цикл работы величина минутного грузопотока из питателя, м3/мин;
Sjб – сечение j-го бункера, м2.
Текущее значение уровня твердого материала в i-м бункере позволяет скомпенсировать погрешность, вызванную отклонением фактического грузопотока из очистного забоя от заданного по условиям безаварийной работы значения.
С целью повышения эффективности работы подземного конвейерного транспорта разработана система автоматизированного управления, алгоритм функционирования которой приведен на рисунке 9.
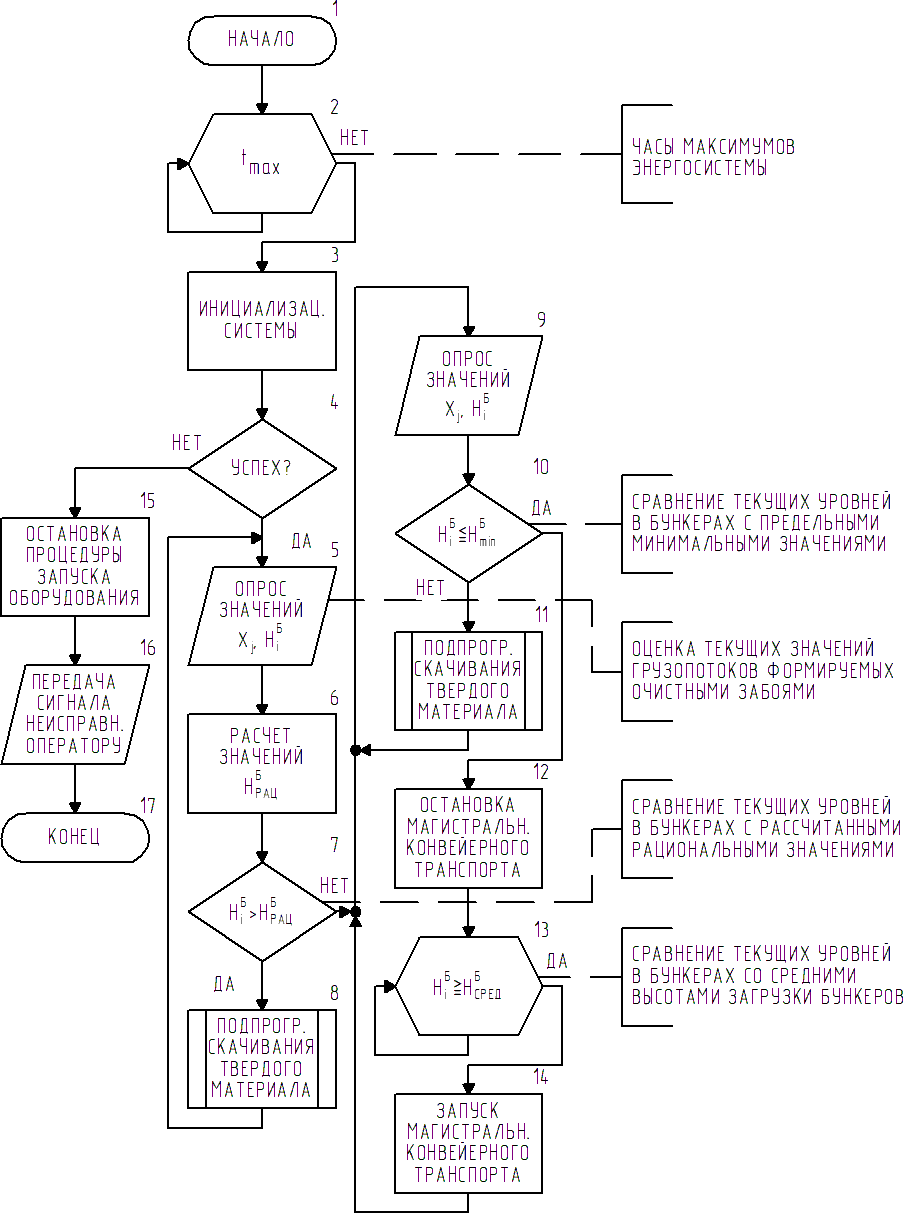
Рисунок 9 – Алгоритм системы автоматизированного управления конвейерным транспортом шахты
Процесс разгрузки бункера-питателя включает в себя подготовку транспортной системы к работе и выгрузку полезного ископаемого из бункеров до минимально допустимой высоты загрузки. Перед началом работы система автоматизированного управления проверяет условие на запрет работы в часы максимума энергосистемы tmax с последующей инициализацией отдельных элементов.
При успешной инициализации оцениваются текущие значения грузопотоков из участковых бункеров Xj и уровни твердого материала в бункерах Hiб.
На основании полученных данных определяются рациональные уровни загрузки бункеров полезным ископаемым Hрацб. Если фактические значения уровня твердого материала в бункерах превышают расчетные значения – выполняется подпрограмма выгрузки твердого материала (рис. 10) в следующей последовательности:
- производится условная нумерация бункеров по критерию транспортного запаздывания Tзп, нумерация осуществляется от бункера с наибольшим транспортным запаздыванием и далее – по мере его уменьшения;
- включается питатель бункера с наибольшим отклонением текущего значения уровня загрузки Hiб от расчетного значения Hрацб;
- включается задержка на время работы питателя бункера tцбп;
- по завершении рабочего цикла питатель бункера отключается.
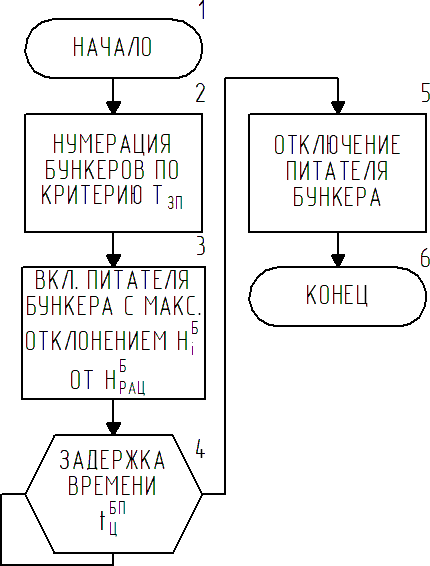
Рисунок 10 – Блок-схема подпрограммы выгрузки твердого материала
По обновленным данным производится определение следующего бункера с наибольшим отклонением текущего уровня загрузки Hiб от расчетного, рационального значения Hрацб. Подготовка транспортной системы к работе продолжается до момента, пока фактические уровни загрузки бункеров твердым материалом не станут меньше или равны расчетным значениям. Если инициализация системы не произошла – осуществляется остановка процедуры запуска оборудования. Одновременно с этим осуществляется передача информации о характере неисправности оператору системы.
Далее осуществляется выгрузка полезного ископаемого из бункеров до минимальных значений загрузки Hminб. При этом отслеживаются текущие значения грузопотоков из очистных забоев Xj и уровни твердого материала в бункерах Hiб. Если фактические значения уровней твердого материала в бункерах превышают минимальные высоты загрузки – инициируется выполнение подпрограммы выгрузки твердого материала (рис. 10).
После достижения в бункерах-питателях минимальных высот загрузки Hminб магистральный конвейерный транспорт принудительно останавливается. Возобновление работы магистрального конвейерного транспорта происходит при достижении средней высоты загрузки Hсредб отдельного бункера, входящего в транспортную цепочку.
6. Практическая реализация системы автоматического управления магистральным конвейерным транспортом шахты
Структура системы мониторинга и автоматического управления работой подземного конвейерного транспорта шахты представляет собой компьютерно-интегрированную двухуровневую систему управления, элементы которой связаны между собой промышленной информационной сетью.
Верхний уровень представляет собой систему централизованного автоматизированного мониторинга и управления подземным транспортом шахты, который выполняет следующие функции:
- диагностирование и отображение в графическом виде состояния каждого конвейера;
- расшифровка причины аварийных и оперативных остановок в графической (изменение цвета на схеме) и в подробной текстовой форме (комментарии);
- протоколирование параметров технологического процесса и истории процесса управления;
- формирование советов по оперативному управлению конвейерным транспортом в зависимости от грузопотока.
На нижнем уровне система представлена двумя подсистемами: подсистема управления конвейерным транспортом и подсистема управления аккумулирующими бункерами. Обобщенная структурная схема приведена на рисунке 11.
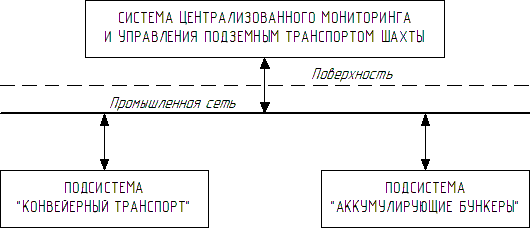
Рисунок 11 – Структурная схема системы автоматического управления работой подземного конвейерного транспорта шахты
Подсистема Конвейерный транспорт
обеспечивает выполнение следующих функций:
- функции базовой аппаратуры автоматизации АУК.3 в режиме управления конвейерными линиями;
- автоматическое измерение массы твердого материала, транспортируемого ленточными конвейерами;
- автоматический контроль тепловых режимов работы отдельных элементов конвейера (приводной барабан, конвейерная лента, роликоопоры);
- синхронизация работы конвейерного оборудования с аккумулирующими бункерами в условиях неравномерности поступающих грузопотоков;
- прогнозирование возникновения аварийных ситуаций.
Подсистема Аккумулирующие бункеры
обеспечивает выполнение следующих функций:
- местное автоматизированное и автоматическое управление исполнительным органом бункера по информации с технологических датчиков;
- передача информации о состоянии аккумулирующих бункеров на АРМ горного диспетчера и оператора конвейерного транспорта.
Сеть передачи данных верхнего уровня на физическом уровне представляет собой промышленный Ethernet, работающий по стандарту PROFINET, который использует протоколы TCP/IP, RT и IRT.
Сеть нижнего уровня на физическом уровне представляет собой электрическую сеть с шинной топологией RS-485, которая работает по стандарту Profibus с протоколом Profibus DP.
Для осуществления автоматического измерения массы твердого материала на конвейерах применяются весы конвейерные автоматические ВКАУ.
Автоматический контроль тепловых режимов работы элементов конвейера осуществляется аппаратурой АКТЛ-1.
Непрерывное измерение уровней заполнения аккумулирующих бункеров осуществляется аппаратурой контроля уровня горной массы АГКМ.
Предложенные средства отбора информации имеют рудничное взрывобезопасное исполнение и разработаны для применения на угольных шахтах, в том числе, опасных по газу, пыли и внезапным выбросам.
Выводы
В результате анализа режимов и особенностей технологического процесса работы магистрального конвейерного транспорта сформулированы требования к системе автоматического управления.
Анализ существующих технических решений в области автоматизации подземного конвейерного транспорта показал, что представленные на рынке системы и средства автоматизации обладают недостатками, к которым следует отнести невозможность энергоэффективной работы в условиях неравномерности поступающих грузопотоков, а также отсутствие контроля тепловых режимов работы элементов конвейера. В качестве базовой аппаратуры автоматизации принят комплекс автоматизированного управления конвейерными линиями АУК.3.
Разработана имитационная модель системы подземного транспорта шахты, которая позволяет: оценивать аккумулирующую способность магистральной конвейерной линии при возникновении аварийных ситуаций, производить прогноз грузопотоков в транспортных системах с различной топологией, определять оптимальные параметры аккумулирующих бункеров для сглаживания неравномерности грузопотоков.
Во время исследования режимов работы подземного конвейерного транспорта совместно с аккумулирующими бункерами разработан алгоритм системы автоматизированного управления конвейерным транспортом шахты, позволяющей снизить неравномерности поступающих грузопотоков, повысить энергоэффективность работы шахтного конвейерного транспорта благодаря уменьшению удельных затрат электроэнергии на транспортирование полезного ископаемого в часы максимумов энергосистемы, увеличить ресурс работы технологического оборудования.
Система автоматического управления магистральным конвейерным транспортом шахты реализована на двух уровнях с
применением промышленных сетей. В подсистеме верхнего уровня принят стандарт промышленного Ethernet с
использованием протоколов: TCP/IP, RT и IRT. Подсистемы нижнего уровня Конвейерный транспорт
и
Аккумулирующие бункеры
организованы при помощи промышленной сети стандарта Profibus с использованием
протокола Profibus DP. Для расширения функциональных возможностей системы автоматического управления
магистральным конвейерным транспортом шахты в состав включены дополнительные системы автоматизации и
средства отбора информации: ВКАУ, АКТЛ-1 и АГКМ.
При написании этого реферата магистерская работа еще не завершена. Окончательное завершение: июнь 2021 года.
Список литературы
- Шахмейстер, Л. Г. Вероятностные методы расчета транспортирующих машин [Текст] / Л. Г. Шахмейстер, В. Г. Дмитриев. – М.: Машиностроение, 1983. – С. 67–69.
- Петков, О. Н. Разработка и исследование системы автоматического управления скоростью
ленточного конвейера по входному грузопотоку: автореф. дис. на сосиск. уч. степени
канд. техн. наук: спец. 05.13.07
Автоматизация процессов управления
/ Петков О. Н. – Москва, 2007. – 20 с. - Заика, В. Т. Методы повышения эффективности электроснабжения и энергоиспользования подземных горных машин и установок угольных шахт: Дис. д-ра техн. наук: 05.09.03 / [Национальная горная академия Украины]. – Днепропетровск, 2001. – 350 c.
- Шахмейстер, Л. Г. Тяговые расчеты ленточных конвейеров / Шахмейстер Л. Г., Дмитриев В. Г. – М. [МГИ]. 1969. – 108 с.
- Разумный, Ю. Т. Энергосбережение / Разумный Ю. Т., Заика В. Т., Степаненко Ю. В. – Днепропетровск: [НГУ], 2008. – 164 с.
- Рудничный транспорт и механизация вспомогательных работ / Под ред. Б. Ф. Братченко. – М.: Недра, 1978. – 423 c.
- Шахмейстер, Л. Г. Подземные конвейерные установки / Л. Г. Шахмейстер, Г. И. Солод. – Москва: Недра, 1976. – 429 с.
- Васильев В. В., Кузьмук В. В. Сети Петри, параллельные алгоритмы и модели мультипроцессорных систем. – Киев.: Наук. Думка, 1990. – 212 с.