Abstract
Content
- Introduction
- 1. Purpose and object of development research
- 2. Analysis of the state of the issue of automation of the process of dissolution of dry waste
- 2.1 Analysis of TP for dissolving dry waste in a pulper as a control object
- 2.2 Analysis of existing ACS TP for processing dry waste in a pulper
- 3. Synthesis of ACS for dissolving dry waste
- 4. Analysis of the dynamics of the ACS processing dry waste
- Conclusion
- References
Introduction
One of the important problems of the papermaking industry is the search for raw materials. This problem has acquired particular urgency in connection with the forecast that appeared at the end of the last century about the growth of the world population and the corresponding possible increase in the need for paper. Therefore, the necessary actions were taken to explore the possibility of increasing the production of wood fiber materials. On the one hand, these measures concerned the development of the most modern methods of providing enterprises with these products, and on the other hand, the use of recycled fibers by obtaining them from waste paper. In addition, the use of waste paper contributes to the preservation and improvement of the environment, which is important. Of great importance in the production of paper and cardboard is the quality of the water used in the paper production. Efforts have been made to improve the degree of its purification, which has led to the introduction of a closed cycle of water use in paper mills and allowed to save water resources.
One of the possible ways to improve the quality of dissolving dry waste in the production of paper and cardboard is to provide a given concentration of the loose mass in the pulper bath, taking into account the productivity of dry waste and fulfillment the material balance condition.
1. Purpose and object of development research
The goal is to increase the efficiency and quality of dissolving dry waste through the development of an automatic control system for the technological process of processing dry waste, which provides a given concentration of the dissolved mass in pulper.
To achieve this goal, it is a necessary to solve the following tasks:
- Review of the technological scheme for dissolving dry waste in a pulper.
- To analyze the technological process of dissolving dry waste in a pulper as a control object.
- Substantiate the selected method of controlling the technological process of processing dry waste in a paper-making and board-making machine.
- Perform the synthesis of the Automatic control system (ACS). Analyze the dynamics of the ACS.
- Check the system performance using mathematical modeling methods.
The object of research is a system for automatic control of the technological process of processing dry waste in a pulper.
2. Analysis of the state of the issue of automation of the process of dissolution of dry waste
The paper and board production process consists of preparing paper pulp to ebb and papermaking on a paper machine (PM) or cardboard machine (CM). Preparation of paper pulp generally consists of dissolving dry waste (waste paper), semi-finished product, grinding the mass and composing. The quality of the finished product is determined by the efficiency of the process processing of dry waste in machines for breaking up fibrous semi-finished products. Such machines are called - pulper. Hydropulders are available in open and closed types, one-rotor, two-rotor and multi-rotor (up to four rotors). These machines can be used to dissolve pure and dirty materials (waste paper). Dissolution refers to the process of separating a fibrous material in an aquatic environment into individual fibers [1-4].
Open type pulper is a machine for breaking up fibrous sheet materials. In the pulp and paper industry, pulper is used for breaking up and wet purification waste paper, breaking up semi-finished cellulose and wood pulp, dry and wet waste from paper machines (PM) and cardboard machines (CM).
The pulper consists of a bath 1 with an overflow box 2, a rotor with blades 3 and an electric motor for driving the rotor 4. The principle of operation of the pulper is as follows: water and the fibrous material to be pulverized are fed into the bath, As a result of the mechanical action of the rotor blades and the hydrodynamic action of the moving, the materials is separated into separate fibers. The resulting pulp passes through the openings of the sieve 5 and then goes to the overflow box 2, which serves to adjust the level of the pulp in the pulper bath. A pump is usually installed behind the overflow box for further transportation of the loose mass. In some designs, there is no overflow box, and the pump is connected to the outlet of the pulper 10. There are fixed guide vanes on the bottom or walls of the tank to guide the mass movement 6. The pulper rotor 3 is a massive disk, on the surface of which there are blades that circulate the mass in the bath and dissolve the fibrous material.
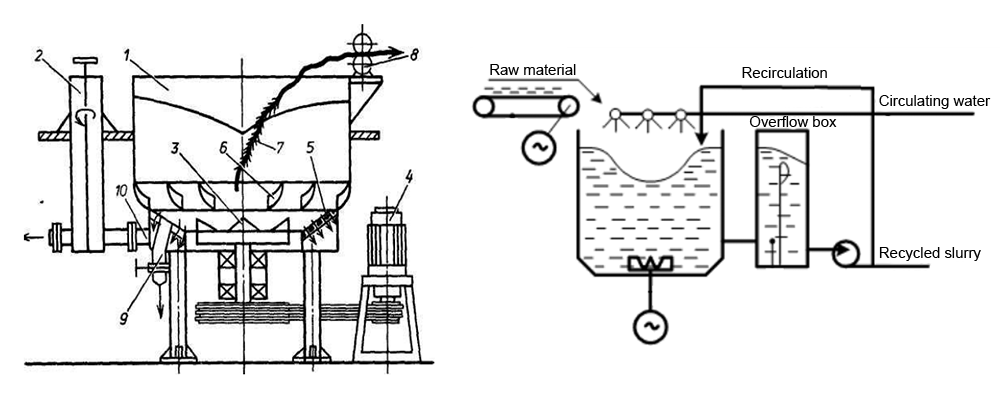
Figure 1 – Open type pulper diagram
When dissolving waste paper containing various contaminants, the pulper performs the function of wet purification of the material. For this purpose, various devices are used. For cleaning the mass of curly dirt from wires, ropes, etc. harness is applied 7. The principle of the harness is as follows. Before the start of dissolution, the end of the rope with the pieces of wire fixed in it is lowered into the tub of the pulverizer, and the other end is fixed between the rollers of the harness extractor winch 8. As a result of the rotational movement, the mass of contamination is wound on the lowered end of the rope, forming a tightly twisted tourniquet, which is periodically or continuously pulled out of the bath and cut off.
Heavy dirt (stones, metal objects, etc.) are thrown away by the rotor blades and, moving along the bottom, fall into the sump 9, from which they are periodically removed. Sometimes an elevator is used to continuously remove heavy dirt. The elevator is connected to a sump, from which mud sludge is continuously taken by buckets and sent to a sieve, where fiber and dirt are separated and the fibers are returned to the pulper.
The considered devices do not solve the problem of removing light impurities from the breaker that have a density lower than or close to that of water [2]. Such contamination in the form of scraps of plastic films, pieces of wood, cork, etc. accumulate in the bath, increase the power consumption and clog the surface of the screens, disrupting the normal operation of the pulper. To remove these inclusions, some designs use a rotary grille. The rotary grate is periodically lowered into the pulper bath and retains contaminants on its surface, then the grate is removed from the bath by turning, pollution is dumped and removed from the workshop.
The disadvantage of a rotary lattice is the impossibility of removing bundles from the pulper, which can form when curly dirt gets into the bath. There are other devices available for cleaning the pulper bath from various contaminants. The breakers can be operated continuously and intermittently. During continuous operation, the concentration of the loose mass is usually 1.5 - 6%, with intermittent operation - 6 - 30%.
2.1 Analysis of TP for dissolving dry waste in a pulper as a control object
The pulping process is characterized by the following parameters: mass consumption of raw materials (dry waste), dryness of raw materials, consumption of circulating water, concentration of circulating water, rotor speed, power consumed from the network by the electric drive of the rotor in the process of dissolution, the concentration of the pulp in the pulper bath, the level of the pulp in the pulper bath.
One of the most important parameters characterizing the quality of the pulping process is the concentration of the pulp in the pulper bath.
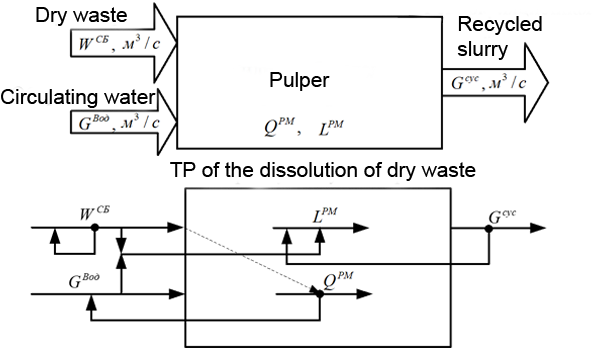
Figure 2 – Analysis of the technological process of dissolving dry waste in a pulper as a control object
The main adjustable variables of the dissolution technological process are:
- concentration of the loose mass in the pulper;
is the level of pulp in the pulper.
Control actions:
- consumption of diluting circulating water;
- consumption of the removed (suspension) and recirculated mass.
The main disturbing influence is:
is the mass consumption of raw materials (dry waste) coming from the conveyor belt.
2.2 Analysis of existing ACS TP for processing dry waste in a pulper
Consider the existing automatic process control systems processing of dry waste in a pulper, the analysis of which will justify the selected the concept of building an ACS, which ensures an increase in the efficiency and quality of dissolving dry material.
There is an automatic dissolution control system that can be used for the dissolution of semi-finished products and dry waste from PM and CM [5]. The essence of this control method is that the concentration of the loose mass is measured indirectly by measuring the level in the center of the bath (or vertically above the edge of the rotor disk) and on the periphery, and depending on their difference, change the flow rate of raw materials and adjust the flow rate of circulating water.
When the pulper is in operation, a "funnel" is formed as a result of the rotation of the mass and the bath. The level difference in the bath in the center and at the periphery characterizes the shape of the free surface of the "funnel". The shape of the free surface of the "funnel" or the level difference is an indicator of concentration.
It is known that the quality of raw material dissolution at a constant rotor speed depends on the degree pulper loading or bath concentration. With an increase in the pulper load, the level difference decreases, those. concentration increases. Here the difference in levels, i.e., the concentration, is controlled by changing the flow rate of the diluting circulating water according to the proportional-integral law.
There is also a bath level control loop by changing the flow rate of the discharged and recirculated mass by proportional law. Simultaneously signal of the level difference through the positional regulator and the magnetic the starter controls the switching on and off of the feed conveyor electric drive. This also provides turning off the supply of raw materials for dissolution when reaching the minimum allowable level difference (maximum allowable concentration in the bath).
If the sieve is clogged and the level at the periphery of the maximum value is exceeded, another positional regulating device switches off automatic level control and signals the operator about the emergency situation at the facility.
The process of dissolving waste paper arriving in bales or in bulk is controlled according to the scheme, shown in Figure 3. Here, the mass flow rates of raw materials and circulating water are measured, their ratio is determined (pos. 2) and the flow rate of the discharged (suspension) and recirculating mass is changed depending on their ratio and level in the damper (overflow box) (pos. 1). Such a control system makes it possible to improve the quality of the dissolution of raw materials, since it provides a given concentration during dissolution, indirectly determined by the ratio of raw materials and water consumption.
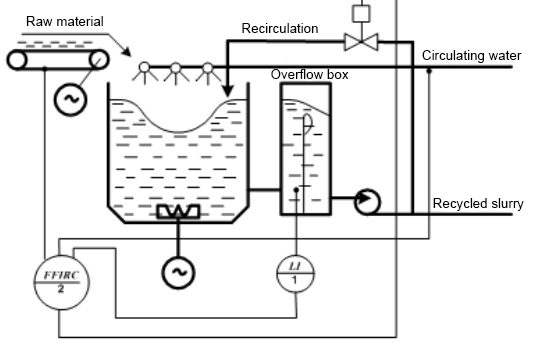
Figure 3 – Functional diagram of the automation of the dissolution of a circulating waste in a pulper
(animation: 7 frames, 10 cycles of repetition, 80 kilobytes)
Having analyzed the existing control methods, the following disadvantages can be identified:
- indirect regulation of the concentration of the loose mass in the bath by the difference in mass levels in the center of the funnel and at the periphery is not a very accurate method for determining this value, which characterizes the quality of the dissolution and its effectiveness;
- the dry waste feeding conveyor belt does not work continuously. It is turned off when the difference in levels of the permissible value decreases, i.e. upon reaching the maximum concentration of the loose mass in the bath;
- the performance of dry waste is not regulated, only controlled;
- the level of the mass in the overflow box is not regulated, only controlled.
- there is no interconnected regulation of the loose mass concentration system, with a dry waste capacity system and a stock level system in the overflow box.
The advantages include the presence of an automatic control system for regulating the recirculation mass, depending on the level in the overflow box and the ratio of the productivity of dry waste and the consumption of circulating water.
So, the analysis of existing ACS from the point of view of the concept of construction leads to the choice a control method that takes into account the merits of the existing automation solution which includes the regulation of the recirculated mass according to the level of the loose mass in the overflow box and the ratio of the costs of dry waste with recycled water. It will also provide interconnected loop control the concentration of the loose mass and the productivity of dry waste. In addition, an indirect way follows replace the concentration regulation with a direct one by means of appropriate sensors.
3. Synthesis of ACS for dissolving dry waste
Before the synthesis procedure for the concentration control loop, it is necessary to set the requirements for the control quality indicators of the ACS concentration of the loose mass, which are presented to objects of this class.
The main indicators of the quality of regulation meet the specified requirements:
- the aperiodic nature of the transient process with a permissible overshoot when the reference signal is processed no more than 3%;
- the settling (regulation) time does not exceed 5-7 minutes;
- the time for working out the load on dry waste is not more than 2 minutes.
- the processing time for changing the reference signal is not more than 3 minutes.
The main task of the ACS synthesis is to choose the regulation law and determination of the tuning parameters of the regulator. From the practice of using regulators for objects of this class [5] we accept the PI control law:
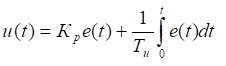
Kp - proportional component; 1 / Tu - integral component; e(t) - regulation error.
The settings of values that are close enough to the optimal. can be obtained as a result of studying the dynamics of a closed system. As a method for finding the tuning parameters of the regulator, we will choose the method of automatic tuning of the PID-control block the Matlab modeling package, since automatic optimization methods are a powerful tool for modern industrial controllers. The automatic tuning method is based on three stages: identifying the object model, determining the parameters of the regulator and setting the parameters [6].
The choice of the above method is due to the fact that the parameters of the regulator, determined by the existing and widespread methods of Ziegler and Nichols, as well as CHR (Chien, Hrones and Reswick) are then manually or automatically adjusted during the analysis of the ATS dynamics [6].
Modeling of ACS with concentration will be carried out under the conditions of the modeling scheme shown in Figure 4.
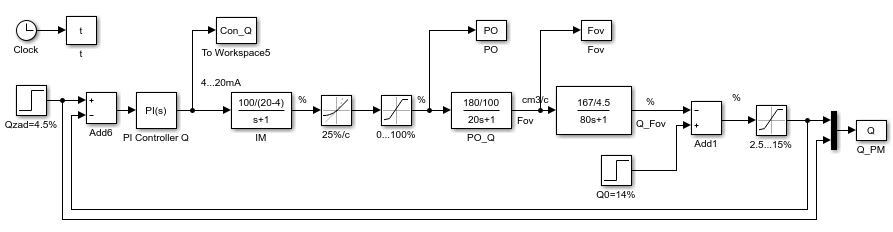
Figure 4 – Simulation scheme of the ACS of the concentration of the loose mass in the pulper
The simulation will be carried out at the nominal parameters of the dissolution process, typical for the production of paper and cardboard:
- the initial concentration of dry waste is 14 - 18%;
- concentration of loose mass 6 - 3%;
- supply of dry waste 1.2 - 1.4 m³ / h = 333 - 398 cm³ / s;
- area of the layer of dry waste 16 - 19 cm²
- speed of movement of the conveyor belt 20 cm / s;
- flow rate of circulating water 0.4 - 0.6 m / h = 111 - 167 cm³ / s.
The transient response of the loose mass concentration is shown in Figure 5.
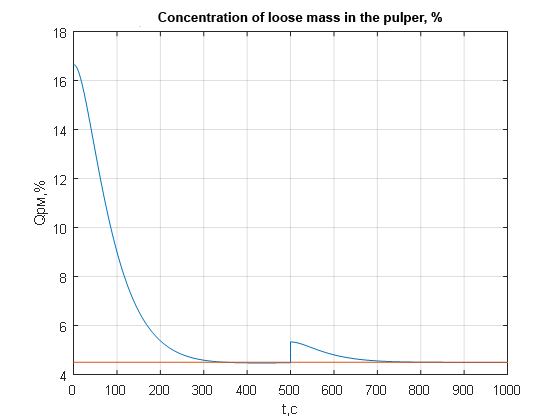
Figure 5 – Transient response of the concentration of the loose mass in the pulper
The transient response of concentration (Fig. 5) is aperiodic without overshoot, regulation time tp = 5 min. These indicators are satisfactory and meet the specified requirements.
Let's analyze the dynamics of the system to work out the disturbing effect. The graph shows that at the moment of time 8 min an increase in the concentration of loose mass from 4.5% to 5.5%. This is a reaction to an increase in dry waste productivity from 330 to 350 cm³/ s, served in the pulper. The concentration regulator fulfills the disturbance in no more than 2 minutes, which also meets the requirements for objects of this class. Figure 6 shows the transient characteristics of the main elements of the ACS, confirming the adequacy of its work.
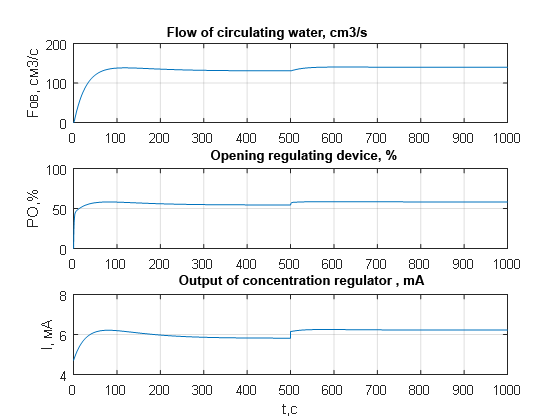
Figure 6 –Transient characteristics of the main elements of the ACS for the concentration of the loose mass in the pulper
Compensation for the consumption of dry waste occurs by increasing the consumption of excess circulating water (Fig. 6) due to an increase in the control signal at the output of the concentration regulator. In this case, the opening of the control valve by 10% increased the flow rate of circulating water from 130 cm ³ / s to 140 cm ³ / s.
When processing the disturbance, the concentration regulator does not go beyond the 4 ... 20mA limitation zone, determined by the conditions of technical implementation.
4. Analysis of the dynamics of the ACS processing dry waste
The scheme for modeling a complex ACS by the process of dissolving dry waste is shown in Figure 7. Transient processes in the system were also obtained from it.
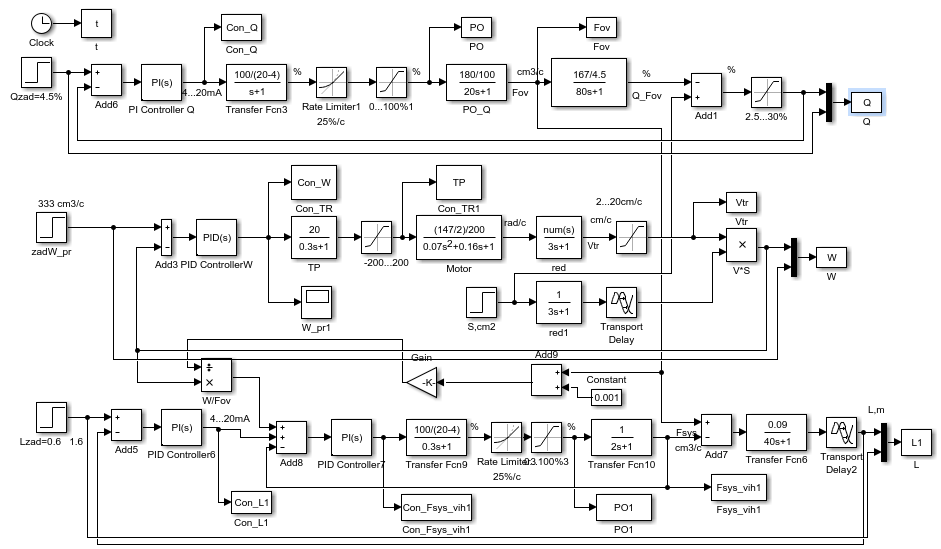
Figure 7 – Scheme for modeling a complex ACS by the process of dissolving dry waste
Consider the transition processes in the dissolution process control system. Simulation of the ACS dynamics without correcting the controller parameters the external contour of the suspension level in the overflow box led to unsatisfactory indicators of the quality of regulation and the type of the transition process, therefore, it was decided to adjust the parameters of the level controllers. The transient response of the slurry level in the overflow box is shown in Figure 8.
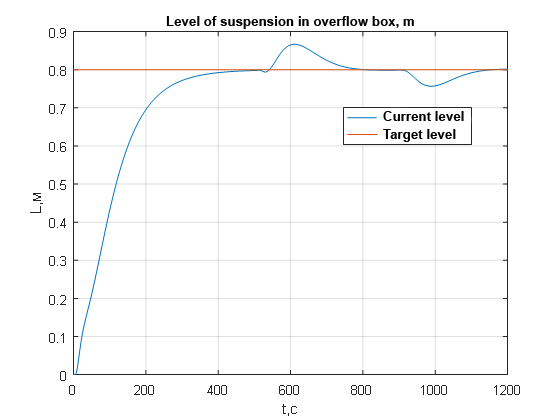
Figure 8 – Transient response of the slurry level in the overflow box
It can be seen from the graph that the transient process of the suspension level in the overflow box is aperiodic without overshoot, the regulation time does not exceed 10 minutes.
At the moment of time 500 s, the productivity of dry waste increases from 333 cm³ / s to 380 cm³ / s, which leads to an increase in the consumption of circulating water, supplied to the pulper, and as a consequence, an increase in the level of suspension in the box from 0.8 m to 0.87 m. In order to compensate for the perturbation in the performance of dry waste, the recirculating suspension flow controller, back to the pulper, taking into account the current ratio of dry waste and recycled water consumption, will open the regulating device (RD) up to 76% and will increase the supply of recirculated mass up to 48 cm³/ s (Fig. 9).
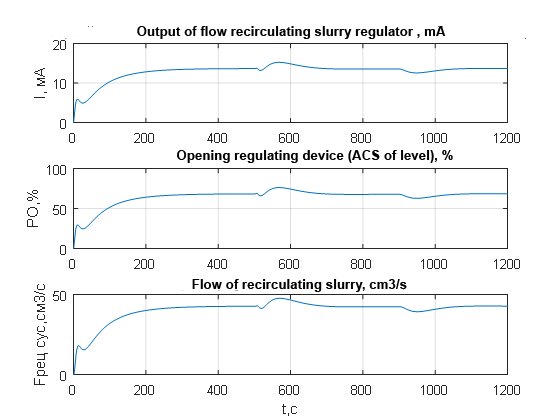
Figure 9 – Transient characteristics of the ACS elements of the suspension level in the overflow box
It can be seen from the graph that the system works out the disturbance in terms of current productivity (consumption of dry waste) up to 5 minutes, which meets the requirements presented to objects of this class.
An increase in the level of the task of the concentration of the loose mass in the pulper from 4.5% to 6% at the time of 900 s, leads to a decrease in the consumption of circulating water, fed into the pulper up to 140 cm³/ s (Fig. 10). This, in turn, affects the lowering of the suspension level in the overflow box (Fig. 8). At the same time, the ACS of the suspension level in order to restore the material balance, taking into account the ratio of current costs for the productivity of dry waste and the consumption of circulating water compensates for the change in the slurry level by changing the flow rate of the recirculated mass (Fig. 9).
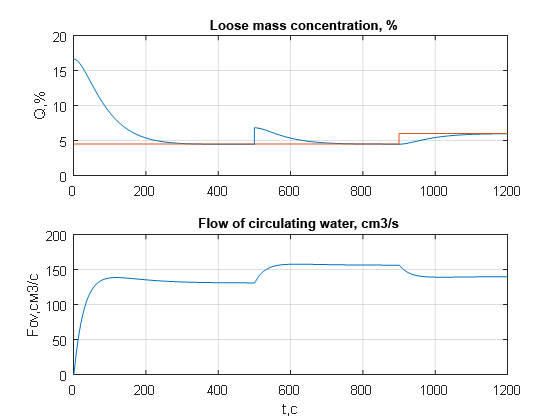
Figure 10 – Transient characteristics of the ACS elements for the concentration of the loose mass in the pulper
Thus, the graphs shown in fig. 8 - fig. 10 confirm the correct functioning of the complex ACS dissolution of dry waste. Transient characteristics of the main elements of the three subsystems that are part of the integrated ACS dissolution, do not go beyond the limits of technically and technologically permissible values. Based on the analysis of the dynamics of the integrated ACS for the dissolution dry waste, it is possible to recommend the use of the developed ACS in the automation of paper production technological schemes.
Conclusion
1. A block diagram of a complex ACS for dissolving dry waste in a paper machine has been developed, providing the required concentration of the loose mass while maintaining the material balance in the pulper by maintaining the level of the loose mass in the overflow box, taking into account the current consumption of dry waste and circulating water.
2. A theoretical synthesis of the automatic control system for dissolving dry waste was carried out, the parameters of the regulators of local control systems for concentration were adjusted loose mass, dry waste capacity and slurry level in the overflow box. The controller parameters were automatically optimized by means of the PID-control block. The developed system is robust, solves the problem of tracking and stabilization in the presence of interference in the measurement chain of the main controllable parameters of the dissolving system in PM conditions.
3. The simulation results proved the efficiency of the ACS and the possibility of using the developed system, the main indicators of the quality of which are: the absence of a static error; regulation time - about 10 minutes; aperiodic nature of transients without overshoot; satisfactory time of processing of signals of settings and disturbances; compensation of both controlled and uncontrolled disturbances due to the selected deviation control principle.
References
- Корда И., Либнар 3., Прокоп И. Размол бумажной массы. - М.: Лесная промышленность, 1967. - 421 с.
- Гаузе А. А., Гончаров В. Н. Оборудование для подготовки бумажной массы. - М.: Лесная промышленность, 1991. - 256 с.
- Технология целлюлозно-бумажного производства. В 3 т. Т. I. Сырье и производство полуфабрикатов. Ч. 2. Производство полуфабрикатов. — СПб.: Политехника, 2003. — 633 с.
- Смоляницкий Б. З. Переработка макулатуры. - М.: Лесная промыш-ленность, 1980. – 176 с. 5. Теоретические основы производства окускованного сырья: Учебное пособие для вузов. Ковалев Д.А., Ванюкова Н.Д., Иващенко В.П. и др.. – НметАУ. – Днепропетровск: ИМА-пресс. – 2011. – 476 с.
- Петровский, В. С. Автоматизация технологических процессов и производств лесопромышленного комплекса [Электронный ресурс] : учебник для студентов вузов, обучающихся по специальности «Автоматизация технологических процессов и производств (лесотехническая отрасль)» направления подготовки «Автоматизированные технологии и производства» / В. С. Петровский ; Издательство «Лань» (ЭБС). – Воронеж : ВГЛТА, 2011. – 400 с. – Режим доступа: . http://e.lanbook.com/view/book/....
- Денисенко В.В. Компьютерное управление технологическим процессом, экспериментом, оборудованием. –М.: Горячая линия – Телеком, 2009. – 608 с., ил.
- Казиев, В. М. Введение в анализ, синтез и моделирование систем : учебное пособие для вузов /В. М. Казиев. - 2-е изд.-: БИНОМ. Лаборатория знаний, 2007. - 244с. – 3 экз.
- Введение в математическое моделирование: учебное пособие для вузов / В. Н. Ашихмин [и др.]; под ред. П.В. Трусова. - М.: Логос. 2007. - 440с. – 2 экз.
- Бобков, С. П. Моделирование систем [Электронный ресурс] / С. П. Бобков. - 1 Мб. - 2008. - 1 файл. - Систем. требования: Acrobat Reader.
- Копылов И.П. Электрические машины: Учеб. для вузов. 4-е изд., испр.-М.: Высш. шк., 2004.-607с.
- Копылов И.П. Математическое моделирование электрических машин: Учеб. для вузов. 3-е изд., испр.-М.: Высш. шк., 2001.-327с.