Реферат по теме выпускной работы
Содержание
- Введение
- 1. Класификация термических печей
- 2. Термическая колпаковая печь
- 2.1 Конструкция колпаковой печи
- 2.2 Технологический процесс колпаковой печи
- Список использованых источников
Введение
Термическая обработка металлов производится для улучшения их структуры и придания свойств, необходимых для данных конкретных условий: прочности, твердости, износоустойчивости, вязкости и т. п. Термическая обработка включает в себя ряд операций: нагрев до определенной температуры, выдержку при ней определенное время и охлаждение с заданной скоростью. Наиболее распространенными операциями термической обработки являются: отжиг, нормализация, закалка, отпуск и цементация.
Отжиг - нагрев до определенной температуры, выдержку при ней и медленное охлаждение в печи - производят для получения стали с равномерной структурой, свободной от внутренних напряжений. При отжиге сталь нагревают до температуры 750-1150°С в зависимости от ее состава. Нормализацию применяют для устранения внутренних напряжений в стали. Она отличается от отжига тем, что после выдержки металл сразу выдается из печи и охлаждается на воздухе. Закалку - нагрев, выдержку и быстрое охлаждение (в воде, масле и пр.) - производят для придания стали твердости. При закалке обыкновенную сталь нагревают до температуры 850-900°С, а специальные легированные стали - до 1250°С.
Отпуск применяют для устранения или уменьшения напряжений, полученных в результате закалки. При отпуске металл проходит те же операции, что и при отжиге или нормализации, но при этом нагревается до более низких температур - от 150 до 600°С.
1. Класификация термических печей
Термическая печь - печь для термической обработки металлических изделий.
Термические печи классифицируются:
- по технологическим признакам и назначению (закалочные, отжигательные, цементационные и др.);
- по способу нагрева (электрические, пламенные, косвенного нагрева), по среде рабочего пространства (воздух, газовая контролируемая среда, жидкая среда);
- по конструкции (камерные, колпаковые, ванные и т.д.);
- по режиму работы (периодического и непрерывного действия).
В процессе термической обработки повышается качество изделий или сообщаются дополнительные свойства, что обеспечивает сокращение расхода металла в процессе эксплуатации. Термической обработке подвергаются все виды горячекатаного и холоднокатаного проката: лист, уголок, проволока, рельс, труба, швеллер, лента и др.
Виды термической обработки:
• сортовой прокат – полный и изотермический отжиг, нормализация, закалка (патентирование);
• горячекатаный лист;
• нормализация или закалка с последующим отпуском;
• отжиг или высокий отпуск;
• рельсы – нормализация, изотермическая выдержка, отпуск;
• холоднокатаный лист и лента – рекристаллизационный отжиг.
Все виды термообработки можно разделить на две большие группы:
1) Простой нагрев до определённой температуры с последующей выдачей на воздух (нормализация) или в жидкие среды (закалка).
2) Нагрев до определённой температуры с последующей длительной изотермической выдержкой и, в завершение, регламентированным охлаждением или охлаждением вместе с печью (отжиг).
Для нагрева под нормализацию и закалку применяют нагревательные проходные печи всех типов. Кроме этих печей применяют специализированные проходные и камерные печи, предназначенные для термической обработки конкретных видов продукции.
Для нагрева под отжиг применяют камерные печи и для отдельных видов продукции – протяжные печи непрерывного действия (отжиг ленты, полосы, проволоки).
Специализированная на термической обработке печь должна обеспечивать заданный технологией температурно-временной режим обработки изделия и высокую равномерность нагрева изделия. Обычные нагревательные печи не всегда в состоянии обеспечить необходимую в термообработке равномерность и точность нагрева. Так, при нагреве слитков под обработку давлением удельный перепад температуры в конце нагрева должен быть не более 100-300°С на 1 метр толщины, а при нагреве заготовок – не более 1000°С на 1 метр толщины. Как при нагреве слитков, так и заготовок абсолютное значение перепада температуры составляет 50-70°С.
При термической же обработке металлопродукции перепад температуры по сечению в конце режима термообработки чаще всего должен вообще отсутствовать или составлять не более 5-10°С. Когда говорят о перепадах температур, то в термических печах подразумевают перепад не по сечению, а по объему садки металла. Фактически – это разброс температуры по объему садки. Его величина обычно составляет 5-10°С, в то время как в нагревательных печах разброс температур может быть 80-100°С и больше. Поэтому и говорят, что при термообработке очень жесткие требования по равномерности нагрева.
Составление материального и теплового балансов термических печей имеет особенность, связанную с почти полным отсутствием окисления металла в процессе нагрева из-за малого уровня температур. Фактически материальный баланс можно свести к материальному балансу горения топлива, рассчитанному или на 1 кг топлива, или на 1 м3 топлива, или на 1 Дж химической энергии топлива.
Для термической обработки прокатной продукции в металлургической промышленности наиболее широко применяют проходные и протяжные печи. Закалку, нормализацию и отпуск горячекатаных листов проводят в печах с роликовым подом. Холоднокатаную стальную полосу в рулонах отжигают как в протяжных, так и в колпаковых печах. В протяжных печах проводят термическую обработку полосы из углеродистой и нержавеющей стали и цветных металлов, а также химико-термическую обработку полосы из электротехнических сталей и подготовку полосы к нанесению на неё различных покрытий (оцинкование, алюминирование и т. д.).
Сортовой прокат обрабатывают в печах с роликовым подом и в конвейерных печах. Для обработки труб применяют печи с роликовым подом, секционные печи скоростного нагрева, печи с шагающим подом и конвейерные печи. Проволоку в мотках и прутки обрабатывают в печах с роликовым подом, а при небольшом объёме производства - в колпаковых печах. Закалку проволоки в свинце или оцинкование её ведут в патентировочных печах. Термическую обработку колёс и колёсных бандажей для ж.д. транспорта проводят в вертикальных печах, а иногда в кольцевых печах[1].
2. Термическая колпаковая печь
Колпаковые печи для обработки металла горячим газом были разработаны специально для нужд металлургической промышленности и впервые появились в 20-е годы прошлого века. Несколько позже появились колпаковые печи для термообработки изделий в вакууме. Конструкция этого типа печей предусматривает нагрев изделий в газовой или вакуумной среде под переносным колпаком и позволяет производить полный цикл термообработки: нагрев, охлаждение, выдержка. Изделия располагаются на неподвижном стенде с одной или в некоторых случаях, несколькими стопами.
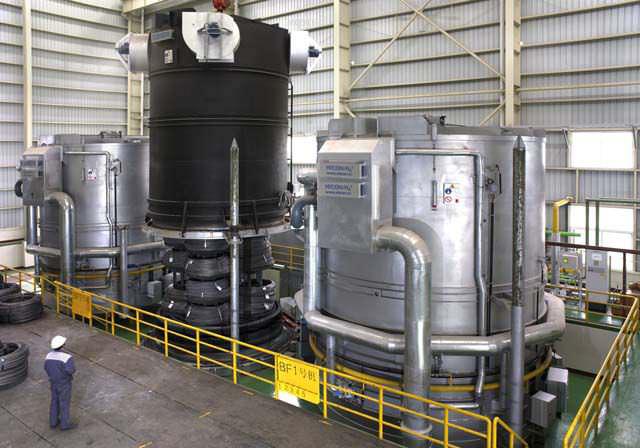
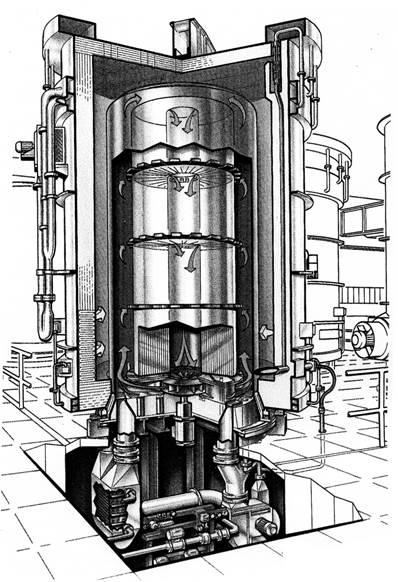
Рисунок 1 – Колпаковая печь
Колпаковые печи предназначены для термообработки крупно-габаритных изделий и широко применяются на предприятиях металлургии, в атомной, электронной, авиационной и многих других отраслях промышленности, где есть необходимость выполнения термохимических операций с металлическими заготовками больших размеров. Они применяются для аустенизации, коксования, цианирования, азотирования, нитроцементации, оксиазотирования, закалки, отжига, отпуска, пайки, чернения, спекания и других операций термообработки металла.
Колпаковые печи могут быть газовыми или электрическими и классифицируются по типу обрабатываемых изделий, для обработки ленточных рулонов, проволоки, прутков, листов и другого металлопроката.
Основные технические характеристики колпаковых печей:
- температура нагрева;
- вес садки;
- габаритные размеры обрабатываемых изделий;
- количество стендов обработки.
2.1 Конструкция колпаковой печи
Колпаковая печь – печь периодического действия для термообработки рулонов ленты, листов и бунтов проволоки.
Отличительная особенность колпаковой печи является наличие двух колпаков: внутреннего, предохраняющего металл от окисления (муфеля), и наружного, футерованного огнеупорным кирпичом, на котором монтируются горелки или электрические нагреватели. Муфель выполняется из жароупорной стали. Герметизация колпаковой печи достигается применением песочных затворов. Обычно для ускорения нагрева металла с помощью внутреннего циркуляционного вентилятора создают интенсивную циркуляцию защитного газа под муфелем.
Принципиальные отличия имеют колпаковые печи для отжига листов, уложенных в стопу; колпаковые печи одностопные, колпаковые печи трёхстопные и колпаковые печи для отжига распушенных рулонов. Из этого многообразия конструкций наиболее распространена одностопная печь. Она лучше других вписывается в поточное производство, нагревает металл достаточно равномерно и быстро, даёт низкую себестоимость нагрева и довольно низкий расход топлива[2].
Колпаковая печь состоит из нескольких основных частей:
1. Стенд - основная часть колпаковой печи
Стенд является основной для установки садки рулонов, муфеля и колпака. С нижней стороны установлен циркулярный вентилятор, крыльчатка которого расположена в центральной части стенда.
Кожух стенда, состоящий из стальных листов в газоплотном сварном исполнении, предназначен для крепления металлической станины и циркулярного вентилятора защитного газа.
Водоохлаждаемое (косвенно) специальное фланцевое уплотнение необходимо для герметичности муфеля, подводящие и отводящие патрубки - для защитного и продувочного газа и охлаждающей воды.
Циркулярный вентилятор осуществляет циркуляцию защитного газа под муфелем. Изготовлен из хромоникелевой стали, водоохлаждаемого газоплотного воздушного короба с присоединённым стандартным мотором.
В стенде, заподлицо нижней и верхней поверхностям плиты направляющего аппарата, установлены две термопары: регулирующая (RТ) - для фиксации температуры нагрева металла при отжиге, и контактная (АТ) - для измерения температуры металла при охлаждении.
2. Нагревательный колпак:
Нагревательный колпак представляет собой сварные конструкции из стального листа и профилей для кожуха колпака с отверстиями для установки горелок. Нагревательный колпак имеет габаритные размеры: по высоте 6134 мм и наружный диаметр 3640 мм. Уровень установки колпаковой термопары 2800 мм от нижнего среза колпака и 1300 мм от горизонтального пояса.
Рабочая поверхность колпака для изоляции стен и свода выполнена из волокнистых матов, включая жаростойкие анкера. Общая толщина стены 250 мм, свода 225 мм.
3. Система отопления колпаковой печи
Система отопления печи состоит из рекуператоров и 12 газовых горелок, установленных тангенциально, разделенных на два горелочных пояса, причём горелка N01 в нижнем горелочном поясе предназначена для дожигания водорода. Горелка N01 оснащена байпасным вентилем для снижения расхода газового топлива в период дожигания водорода. Для каждой горелки предусмотрено электрическое зажигание и устройство ультрафиолетового и ионизационного контроля.
Суммарное потребление на нагревательный колпак: природный газ - 140 м3/ч. Водород на дожигание: максимальный расход на горелку N01 - 30 м3/ч.
Для подачи воздуха на горение используют вентилятор производительностью 1500 м3/ч, мощность вентилятора 5.5 кВт, число оборотов двигателя 3000 об/мин. Вентилятор используется с шумоглушителем и шумоизоляцией.
4. Муфель
Муфель печи выполнен из хромоникелевой стали 20Х20Н14С2 и предназначен для разделения рабочего пространства нагревательного колпака и садки рулонов с защитной атмосферой. Муфель выполнен в виде цилиндра диаметром 2520 мм. Нижняя часть муфеля в районе горелочных поясов выполнена из листа толщиной 7.5 мм, верхняя часть муфеля - из листа толщиной 6 мм.
5. Охлаждающий колпак
Колпак выполнен из стальных листов с рёбрами жесткости из профилированной стали. Имеется несущая конструкция для крановой транспортировки и направляющие отверстия для центровки колпака на стенде.
Охлаждающий колпак имеет габаритные размеры: по высоте 6075 мм и наружный диаметр 2760 мм.
Охлаждающий колпак имеет два максимальных вентилятора с моторами, расположенными внизу на колпаке.
6. Конвекторные кольца
Конвекторные кольца устанавливаются между рулонами и предназначены для равномерного распределения потока защитного газа по высоте стопы и ускоренного прогрева рулонов путём интенсивной теплопередачи конвекцией между циркулирующим газом и торцами рулонов. Каждое конвекторное кольцо состоит из листового кольца, на которое наварены конвективные ребра и завихрительные планки. Транспортировка колец производится электромостовым краном с помощью электромагнита грузоподьёмностьо 50 кН (5 т.).
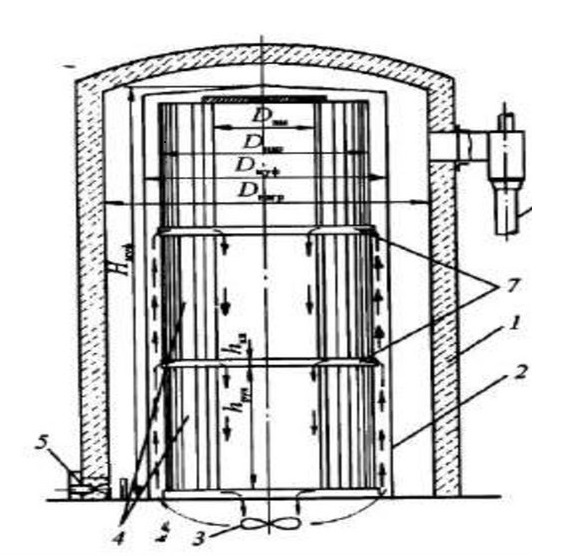
Рисунок 2 – Схема колпаковой печи: 1-нагревательный колпак; 2-муфель; 3-циркулирующий вентилятор; 4-рулоны полосы; 5-горелки; 6-рекуперативно-эжекторное устройство; 7-конвекторные колца.
Время нагрева в колпаковой печи является главным фактором, влияющим на расход топлива. Время зависит от условий теплообмена на торцах и боковой поверхности рулонов металла. Известно, что для прогрева плотно смотанных рулонов в радиальном направлении требуется времени в несколько раз больше, чем для прогрева в аксиальном направлении. Это связано с тем, что коэффициент теплопроводности в радиальном направлении для стали составляет только 1,5-4 Вт/(м×К), а в аксиальном направлении около 30 Вт/(м×К). Низкие значения коэффициента теплопроводности в радиальном направлении связаны с наличием воздуха между витками рулона. Для обеспечения подвода необходимого количества теплоты к торцам рулонов служат специальные устройства, называемые конвекторными кольцами и размещаемые между рулонами. Они представляют собой набор узких параллельных спиралевидных каналов между плоскими пластинами. По каналам проходит горячий защитный газ, отдающий свою теплоту. Высота конвекторных колец – 50-120 мм.
Равномерность нагрева металла определяется типом направляющего аппарата, расположенного в самом низу муфеля. Внутри аппарата располагается рабочее колесо циркуляционного вентилятора. Защитная атмосфера подсасывается в аппарат сверху вниз и распределяется по периферии.
2.2 Технологический процесс колпаковой печи
Технологический процесс делится примерно на три одинаковые стадии: нагрев до 650-800°С, охлаждение под муфелем до 150°С и без него и последняя стадия – разгрузка и загрузка стенда. Равенство времени по стадиям позволяет использовать три стенда с одним нагревательным колпаком и двумя муфелями. Загрузка металла заканчивается опусканием на стенд поверх стопы рулонов муфеля и нагревательного колпака. После этого подаётся защитный газ (обычно смесь из 95 % N2 и 5 % Н2) и с помощью циркуляционного вентилятора осуществляется его циркуляция. Затем включаются горелки. Продукты горения проходят между нагревательным колпаком и муфелем и при помощи инжектора (инжектирующая среда – компрессорный воздух) удаляются в дымоотводы и в дымовой боров. Температура дыма перед инжектором около 630-660°С. В колпаковых печах физическая теплота дыма обычно не утилизируется, что можно считать одним из недостатков печей.
Защитный газ подается циркуляционным вентилятором в зазор между муфелем и рулонами стопы. Газ равномерно распределяется по конвекторным кольцам и через них попадает во внутренние полости рулонов, омывая их. Опускаясь по внутренней полости стопы газ, возвращается в циркуляционный вентилятор. Кольца получают теплоту от защитного газа конвекцией и нагревают рулоны. Муфель излучает на боковую поверхность металла, но тепловой поток несущественен для нагрева рулонов из-за отмеченного ранее низкого коэффициента теплопроводности в радиальном направлении. Исключение делается для верхнего рулона, который получает теплоту на свой торец. Поэтому верхний рулон всегда греется быстрее других. В наихудших условиях нагрева и охлаждения находится нижний рулон. Проблемой является низкий коэффициент теплоотдачи от муфеля к защитному газу, в результате чего вынужденно поддерживаются высокими температура муфеля и температура дыма под нагревательным колпаком. Это приводит к повышенной температуре уходящих газов и высокому расходу топлива [3].
При написании данного реферата магистерская работа еще не завершена. Окончательное завершение: ноябрь 2021 года.
Список использованых источников
- Тымчака В.М Справочник конструктора печей прокатного производства/ под ред./ В.М. Тымчака – Москва: Металлургия, 1970. - 991 с.
- Кривандин В.А.Теплотехника металлургического производства. Т. 1. Теоретические основы: Учебное пособие для вузов / В.А. Кривандин, В.В. Белоусов, Г.С. Сборщиков и др.- Москва: МИСиС, 2001 - 736 с.
- Монид А.Г Совершенствование колпаковых печей для светлого отжига рулона Сталь /А.Г. Монид, A.C. Кожевников, В.В. Петрик - 1971.- №2.- С.180-182.