Abstract
Content
- Introduction
- 1. Classification of thermal furnaces
- 2. Thermal bell furnace
- 2.1 Design of the bell furnace
- 2.2 Technological process of the bell furnace
- List of sources used
Introduction
Heat treatment of metals is performed to improve their structure and impart properties necessary for these specific conditions: strength, hardness, wear resistance, viscosity, etc. Heat treatment includes a number of operations: heating to a certain temperature, holding it for a certain time and cooling at a given speed. The most common heat treatment operations are: annealing, normalizing, quenching, tempering and carburizing.
Annealing - heating to a certain temperature, holding at it and slow cooling in the furnace - is performed to obtain steel with a uniform structure free from internal stresses. During annealing, the steel is heated to a temperature of 750-1150°C, depending on its composition. Normalization used to eliminate internal stresses in steel. It differs from annealing in that after holding, the metal is immediately released from the furnace and air-cooled. Quenching - heating, holding and rapid cooling (in water, oil, etc.) -is done to harden the steel. When quenching ordinary steel is heated to a temperature of 850-900°С, and special alloyed steels - up to 1250°С.
Tempering is used to eliminate or reduce stresses resulting from hardening. When tempered, the metal goes through the same operations as during annealing or normalization, but at the same time heats up to lower temperatures - from 150 to 600°C.
1. Classification of thermal furnaces
Thermal furnace - a furnace for heat treatment of metal products.
Thermal ovens are classified:
- according to technological characteristics and purpose (quenching, annealing, carburizing, etc.);
- by the heating method (electric, flame, indirect heating), by the environment of the working space (air, gaseous controlled medium, liquid medium);
- by design (chamber, bell, bathroom, etc.);
- according to the mode of operation (periodic and continuous action).
In the process of heat treatment, the quality of products is increased or additional properties are reported, which ensures a reduction in metal consumption during operation. All types of hot-rolled and cold-rolled steel are subjected to heat treatment: sheet, angle, wire, rail, pipe, channel, tape, etc.
Types of heat treatment:
• long products - full and isothermal annealing, normalization, hardening (patenting);
• hot-rolled sheet;
• normalization or hardening followed by tempering;
• annealing or high tempering;
• rails - normalization, isothermal holding, tempering;
• cold rolled sheet and strip - recrystallization annealing.
All types of heat treatment can be divided into two large groups:
1) simple heating to a certain temperature with subsequent delivery to air (normalization) or to liquid media (quenching).
2) heating to a certain temperature, followed by a long isothermal holding and, finally, regulated cooling or cooling together with the furnace (annealing).
For heating for normalization and hardening, continuous heating furnaces of all types are used. In addition to these furnaces, specialized pass-through and chamber furnaces designed for heat treatment of specific types of products.
For heating for annealing, chamber furnaces are used and for certain types of products - continuous continuous-flow furnaces (annealing tape, strip, wire).
A furnace specialized in heat treatment must ensure the temperature-time mode of processing the product specified by the technology and high uniformity of product heating. Conventional heating furnaces are not always able to provide the necessary uniformity in heat treatment and heating accuracy. So, when heating ingots under pressure treatment, the specific temperature difference at the end of heating should be no more than 100-300°C per 1 meter of thickness, and when heating blanks - no more than 1000°C per 1 meter of thickness. Both when heating ingots and billets, the absolute value of the difference temperature is 50-70°C.
During the heat treatment of metal products, the temperature drop across the cross section at the end of the heat treatment mode should most often be absent altogether or be no more than 5-10°C. When they talk about temperature changes, in thermal furnaces they mean a difference not over the section, but over the volume of the metal cage. In fact, this is the temperature spread over the cage volume. Its value is usually 5-10°C, while in heating furnaces the temperature range can be 80-100°C and more. Therefore, they say that during heat treatment there are very strict requirements for the uniformity of heating.
Compilation of material and heat balances of thermal furnaces has a feature associated with the almost complete absence of metal oxidation in the heating process due to the low temperature level. In fact, the material balance can be reduced to the material balance of fuel combustion, calculated or 1 kg of fuel, or 1 m3 of fuel, or 1 J of fuel chemical energy.
Continuous and continuous furnaces are most widely used for heat treatment of rolled products in the metallurgical industry. Hardening, normalization and tempering of hot-rolled sheets is carried out in roller hearth furnaces. Cold-rolled steel strip in coils is annealed as in broaching, and in bell-type furnaces. Broaching furnaces carry out heat treatment of carbon and stainless steel and non-ferrous metal strips, as well as chemical heat treatment of a strip of electrical steel and preparation of the strip for applying various coatings on it (galvanizing, aluminizing, etc.).
Long products are processed in roller hearth furnaces and in conveyor furnaces. Roller hearth furnaces, sectional furnaces are used for pipe processing high-speed heating, walking hearth furnaces and conveyor furnaces. Wire in coils and rods are processed in roller-hearth furnaces, and with a small volume production - in bell-type furnaces. Wire hardening in lead or galvanizing is carried out in patent furnaces. Heat treatment of wheels and wheel rims for railway transport is carried out in vertical furnaces, and sometimes in ring furnaces[1].
2. Thermal bell furnace
Bell-type furnaces for metal processing with hot gas were developed specifically for the needs of the metallurgical industry and first appeared in the 1920s last century. Somewhat later, bell-type furnaces for heat treatment of products in vacuum appeared. The design of this type of furnace provides for heating products in a gas or in a vacuum environment under a portable hood and allows for a full cycle of heat treatment: heating, cooling, holding. Products are placed on a stationary stand with one or, in some cases, several stops.
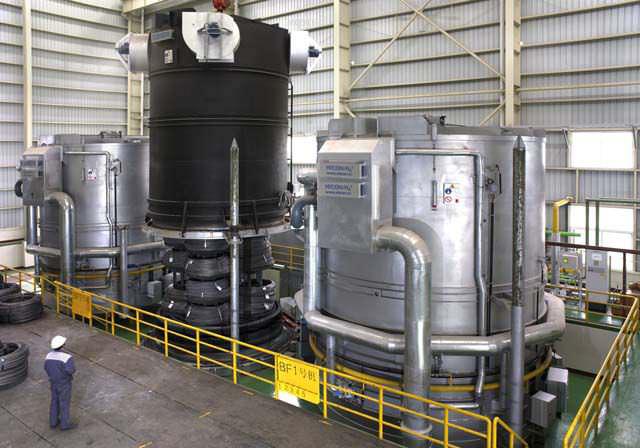
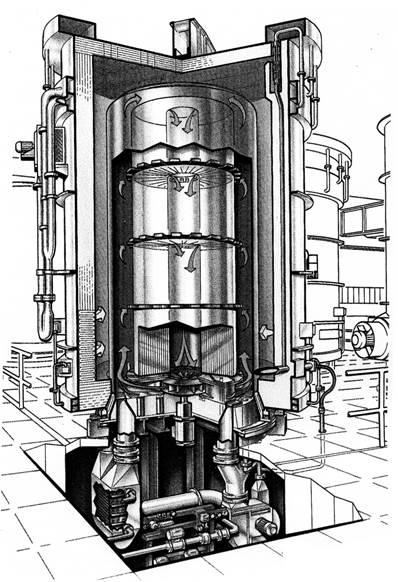
Figure 1 - Bell furnace
Bell-type furnaces are designed for heat treatment of large-sized items and are widely used at metallurgical enterprises, in nuclear, electronic, aviation and many other industries where there is a need to perform thermochemical operations with large metal workpieces. They are used for austenitizing, coking, cyanidation, nitriding, nitrocarburizing, oxynitriding, quenching, annealing, tempering, brazing, blackening, sintering and other operations of metal heat treatment.
Bell-type furnaces can be gas or electric and are classified according to the type of processed products, for processing tape coils, wire, rods, sheets and other rolled metal.
Main technical characteristics of bell-type furnaces:
- heating temperature;
- cage weight;
- overall dimensions of the processed products;
- number of processing stands.
2.1 Bell furnace design
Bell-type furnace is a batch furnace for heat treatment of rolls of tape, sheets and wire bundles.
A distinctive feature of the bell-type furnace is the presence of two bells: the inner one, which protects the metal from oxidation (muffle), and the outer one, lined with refractory brick on which burners or electric heaters are mounted. The muffle is made of heat-resistant steel. The sealing of the bell-type furnace is achieved by using sand gates. Usually, to speed up the heating of the metal, an intensive circulation of the shielding gas under the muffle is created using an internal circulation fan.
Bell-type furnaces for annealing stacked sheets have fundamental differences; one-stop bell-type furnaces, three-stop bell-type furnaces and bell-type furnaces for annealing fluff rolls. Of this variety of designs, the single-foot oven is the most common. It fits into line production better than others, heats the metal quite evenly and quickly, gives a low heating cost and a fairly low fuel consumption[2].
The bell furnace consists of several main parts:
1. The stand is the main part of the bell furnace
The stand is the main one for installing the bales, muffle and hood. A circular fan is installed on the bottom side, the impeller of which is located in the central part of the stand.
The casing of the stand, consisting of steel sheets in a gas-tight welded design, is intended for fastening the metal frame and the circular shielding gas fan.
A water-cooled (indirectly) special flange seal is required for the tightness of the muffle, inlet and outlet connections for the shielding and purge gas and cooling water.
A circulating fan circulates the shielding gas under the muffle. Made of chromium-nickel steel, water-cooled, gas-tight air box with standard motor attached.
In the stand, flush with the lower and upper surfaces of the guide vane plate, two thermocouples are installed: a regulating (RT) - for fixing the metal heating temperature during annealing, and a contact (AT) - for measuring the metal temperature during cooling.
2. Heating hood:
The heating hood is a welded structure made of steel sheet and profiles for the hood casing with holes for installing burners. The heating hood has overall dimensions: height 6134 mm and outer diameter 3640 mm. The installation level of the bell thermocouple is 2800 mm from the bottom edge of the bell and 1300 mm from the horizontal band.
The working surface of the hood for wall and vault insulation is made of fiber mats, including heat-resistant anchors. Total wall thickness 250 mm, vault 225 mm.
3. Bell furnace heating system
The furnace heating system consists of recuperators and 12 gas burners installed tangentially, divided into two burner belts, and the N01 burner in the lower burner belt is designed for hydrogen afterburning. The N01 burner is equipped with a by-pass valve to reduce the gas fuel consumption during the hydrogen post-combustion period. Each burner is equipped with an electric ignition and UV and ionization control.
Total consumption per heating hood: natural gas - 140m3/h. Hydrogen for afterburning: the maximum flow rate for the N01 burner is 30m3/h.
A fan with a capacity of 1500 m3/h, a fan power of 5,5 kW, and an engine speed of 3000 rpm are used to supply combustion air. The fan is used with a silencer and sound insulation.
4. Muffle
The muffle of the furnace is made of chromium-nickel steel 20Х20Н14С2 and is designed to separate the working space of the heating hood and the loading of rolls with a protective atmosphere. The muffle is made in the form of a cylinder with a diameter of 2520 mm. The lower part of the muffle in the area of ??the burner belts is made of 7,5 mm thick sheet, the upper part of the muffle is made of 6 mm thick sheet.
5. Cooling hood
The hood is made of steel sheets with profiled steel ribs. There is a supporting structure for crane transportation and guide holes for centering the hood on the stand.
The cooling hood has overall dimensions: height 6075 mm and outer diameter 2760 mm.
The cooling hood has two maximum fans with motors located at the bottom of the hood.
6. Convector rings
Convector rings are installed between the rolls and are designed to evenly distribute the flow of shielding gas along the height of the foot and accelerate heating of the rolls by intensive convection heat transfer between the circulating gas and the ends of the rolls. Each convector ring consists of a sheet ring on which convective ribs and swirl strips are welded on. The rings are transported by an electric bridge crane using an electromagnet with a load capacity of 50 kN (5 tons).
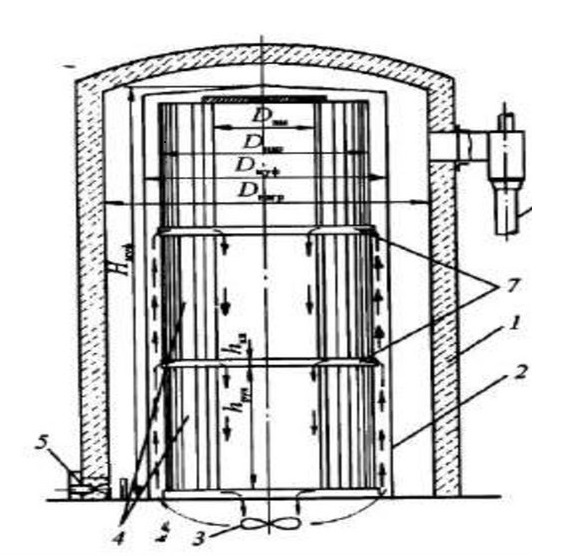
Figure 2 - Scheme of a bell-type furnace: 1-heating bell; 2-muffle; 3-circulating fan; 4-strip rolls; 5-burners; 6-recuperative ejector device; 7-convector rings.
The heating time in the bell-type furnace is the main factor affecting fuel consumption. The time depends on the conditions of heat transfer at the ends and lateral surfaces of the metal rolls. It is known that it takes several times more time to warm up tightly wound coils in the radial direction than to warm up in the axial direction. This is due to the fact that the coefficient of thermal conductivity in the radial direction for steel is only 1,5-4 W/(m×K), and in the axial direction about 30 W/(m×K). Low values of the thermal conductivity coefficient in the radial direction are associated with the presence of air between the turns of the coil. To ensure the supply of the required amount of heat to the ends of the rolls, special devices called convector rings and placed between the rolls are used. They are a set of narrow parallel spiral channels between flat plates. Hot shielding gas passes through the channels and gives off its heat. The height of the convector rings is 50-120 mm.
The uniformity of metal heating is determined by the type of guide vane located at the very bottom of the muffle. The impeller of the circulating fan is located inside the apparatus. The protective atmosphere is sucked into the apparatus from top to bottom and is distributed around the periphery.
2.2 Technological process of bell furnace
The technological process is divided into approximately three identical stages: heating up to 650-800°С, cooling under a muffle up to 150°С and without it, and the last stage - unloading and loading of the stand. Equality of time by stages allows using three stands with one heating hood and two muffles. Loading of metal ends with lowering onto the stand over the stack of rolls of the muffle and the heating cap. After that, a protective gas (usually a mixture of 95% N2 and 5% H2) is supplied and circulated by means of a circulating fan. Then the burners turn on. The combustion products pass between the heating hood and the muffle and are removed with the help of an injector (injection medium - compressor air) into the chimneys and into the chimney. The smoke temperature in front of the injector is about 630-660°C. In bell-type furnaces, the physical heat of smoke is usually not utilized, which can be considered one of the disadvantages of furnaces.
Shielding gas is supplied by a circulation fan into the gap between the muffle and the rolls of the foot. Gas is evenly distributed over the convector rings and through them enters the inner cavities of the rolls, washing them. Dropping along the inner cavity of the foot, the gas returns to the circulating fan. The rings receive heat from the shielding gas by convection and heat the rolls. The muffle radiates to the side surface of the metal, but the heat flux is insignificant for heating the rolls due to the previously noted low thermal conductivity coefficient in the radial direction. An exception is made for the top roll, which receives heat at its end. Therefore, the top roll always heats up faster than others. The bottom roll is in the worst heating and cooling conditions. The problem is the low coefficient of heat transfer from the muffle to the shielding gas, as a result of which the muffle temperature and the temperature of the smoke under the heating hood are forced to be kept high. This leads to higher flue gas temperatures and high fuel consumption[3].
When writing this abstract, the master's work is not yet completed. Final completion: November 2021.
List of sources used
- Тымчака В.М Справочник конструктора печей прокатного производства/ под ред./ В.М. Тымчака – Москва: Металлургия, 1970. - 991 с.
- Кривандин В.А.Теплотехника металлургического производства. Т. 1. Теоретические основы: Учебное пособие для вузов / В.А. Кривандин, В.В. Белоусов, Г.С. Сборщиков и др.- Москва: МИСиС, 2001. - 736 с.
- Монид А.Г Совершенствование колпаковых печей для светлого отжига рулона Сталь /А.Г. Монид, A.C. Кожевников, В.В. Петрик - 1971.- №2.- С.180-182.