Реферат за темою випускної роботи
Цей реферат використано у якості прикладу з дохволу його атвора, магістра ДонНТУ Євгена Татолова.
Оригінал: http://masters.donntu.ru/2011/fknt/tatolov/diss/
Зміст
- ВСТУП
- 1.МАТЕРІАЛИ І ТЕХНОЛОГІЇ ВИГОТОВЛЕННЯ ЩІЛИННИХ СИТ ДЛЯ ГРОХОЧЕННЯ І ЗНЕВОДНЕННЯ МІНЕРАЛЬНОЇ ТА ОРГАНІЧНОЇ СИРОВИНИ
- 2.ЗВАРЮВАННЯ НЕРЖАВІЮЧИХ СТАЛЕЙ
- 2.1. Вплив чистоти газу на зварювання
- 2.2. Режими зварювання
- 3.ОБРОБКА РЕЗУЛЬТАТІВ
- ВИСНОВОК
- Список джерел
ВСТУП
Щілинні сита використовуються, головним чином, в якості поверхонь для технологічного застосування в процесах згущення, зневоднення, пресування, висушування, ферментації в харчовій переробній промисловості, цукроварінні, солодоварінні і в багатьох інших галузях (пивоварінні,кондитерському виробництві, м'ясопереробній промисловості та ін.). А також вони застосовуються в хімічній, фармацевтичній переробної промисловості для схожої технології, при збагачувальних процесах вугільної та гірничорудної промисловості, при зневодненні різних суспензій і шламу на станціях очищення стічних вод і т. д.[1].
Щілинні поверхні сит витримують значне навантаження на одиницю площі (до декількох сот кг). Робоча поверхня гладко оброблена, вона володіє рівною, циліндричної або іншою формою (конуси, круглі, параболічні поверхні і т.п.). Для збільшених навантажень і для підвищення міцності поверхні сит в технологічному обладнанні необхідно застосувати зміцнюючі технології.
1. МАТЕРІАЛИ І ТЕХНОЛОГІЇ ВИГОТОВЛЕННЯ ЩІЛИННИХ СИТ ДЛЯ ГРОХОЧЕННЯ І ЗНЕВОДНЕННЯ МІНЕРАЛЬНОЇ ТА ОРГАНІЧНОЇ СИРОВИНИ
Шпальтові сита являють собою плоскі карти з гладкою поверхнею і збираються з окремих дротяних колосників фасонного профілю з вирізами, вушками або витками для несучих або сполучних рейок або шпильок, розташованих на певній відстані один від одного перпендикулярно до напрямку колосників [2]. Для виготовлення дротяних колосників сіток повинна застосовуватися:
- Дріт зі сталі марок 08Х18Н10, 12Х18Н9, 12Х18Н9Т, 12Х18Н10Т, 10х17н13м3т термічно оброблена світлого відпалу або травлена по НТД;
- Дріт зі сталі марки 12x13 термічно оброблена оксидована по ГОСТ 18143;
- Дріт низьковуглецевий зі сталей 08кп; 10; 15; 20 по НТД.
Для сіток з розміром щілини до 0,3 мм включно повинна застосовуватися сталевий дріт, термічно оброблена, світлого відпалу, підвищеної точності-низьковуглецевий по ТУ 14-4-1563, високолегований по ТУ 14-4-1571 і латунний напівтвердий або м'який підвищеної точності дріт по ГОСТ 1066[3].
2.ЗВАРЮВАННЯ НЕРЖАВІЮЧИХ СТАЛЕЙ
Хромисті стали схильні до під загартуванню на повітрі, яка в сильному ступені залежить від вмісту вуглецю. Найкраще зварюються стали з дуже низьким вмістом вуглецю (≤ 0,08% С), наприклад сталь 0х13. Сталь марки 1х13 сильніше подзакаливается, так як при нагріванні близько 1000°З вона стає повністю аустенітної і при охолодженні навіть на повітрі відбувається γ - м-перетворення.
При зварюванні феритних сталей з 14-28% Cr зварні шви виходять крихкими і часто розтріскуються. Тому зварювання сталей слід проводити у підігрітому стані при & asymp;200 & deg; C, на розігрів металу під час зварювання повинен бути мінімальним. Кращі результати виходять при електродугової, чим при газовому зварюванні. Після зварювання зварне з'єднання рекомендується нагріти до 720-780 & deg;C і швидко охолодити.
Стали з 15-17% Cr іноді при зварюванні підколюються. Щоб це уникнути, рекомендується застосовувати сталі з присадкою титану або ніобію, а в разі сталі з 13% Cr-з присадкою 1% Al [4< / a>].
[4].
Аустенітні стали володіють зниженою температурою плавлення(1400 & deg;С), більш низькою теплопровідністю і високим коефіцієнтом лінійного розширення, ніж вуглецеві сталі. Тому при зварюванні цих сталей розплавлення йде швидше з великим перепадом температури від зварного шва до основного металу. Стабілізовані титаном або ніобієм стали типу 00Х18Н10, 0Х18Н10, Х18Н9 при зварюванні набувають схильність до межкристаллитной корозії і тим більше, чим вище вміст вуглецю[4]
2.1.Вплив чистоти газу на зварювання
Зазвичай зварювання вольфрамовим електродом в середовищі інертного газу (TIG) доцільно використовувати при зварюванні металів товщиною до 7,0 мм. Якщо товщина не перевищує 1,5 мм, застосування інших способів дугового зварювання недоцільно через ризик утворення прожогов. При аргонодугового зварювання в середовищі аргону або гелію спостерігається мінімальний Чад легуючих елементів і підвищується стабільність дуги.
Зварювання аустенітних нержавіючих сталей можна виконувати безперервно палаючої, або імпульсної дугою. Завдяки особливостям теплового впливу імпульсна дуга дозволяє зменшити ширину околошовной зони і викривлення деталей, що зварюються, а також зварити метал малої товщини і забезпечити хороше формування шва.Чим нижче вміст Н2О в складі захисного середовища, тим вище показник теплопровідності дуги, за рахунок чого забезпечується більш висока температура зварювальної ванни. Таким чином застосування аргону високої чистоти сприяє більш повному газовиділенню з розплаву в зоні зварювання, отже, знижується ймовірність утворення пор[5].
Режим подачі аргону і його кількість в пальнику повинні бути оптимальними і стабільними. Необхідно особливо відзначити, що збільшення швидкості подачі газу часто не покращує, а іноді і погіршує якість захисного середовища. При високому тиску і великій швидкості газу в пальнику виникає турбулентний потік, що викликає змішування аргону з повітрям в зоні зварювання [5].
2.2 Режими зварювання
Режим автоматичного і механізованого зварювання плавиться електродом в захисних газах характеризується діаметром дроту, напругою на дузі, швидкістю подачі дроту і пов'язаної з нею силою струму, витратою захисного газу.Орієнтовні режими автоматичного і механізованого зварювання електродом, що плавиться, наведені на малюнку 2.1.
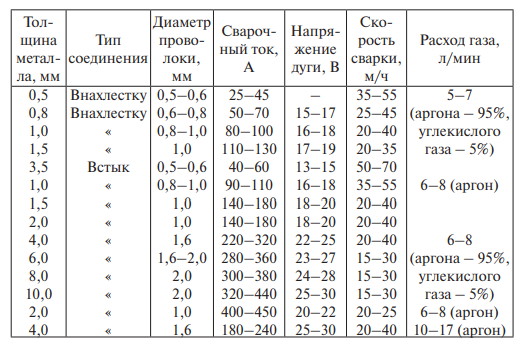
Малюнок 2.1-Режими автоматичного зварювання стикових з'єднань з аустенітних хромонікелевих сталей електродом, що плавиться (дріт Св-04Х19Н11М3[5]
Незалежно від розмірів зварюваного виробу оптимальною швидкістю подачі дроту діаметром 0,8 - 1,2 мм можна вважати 400 м/ч. Сила зварювального струму при цьому буде близько 120-140 А[6].
Вибір марки дроту визначається маркою зварюваної сталі, способом зварювання і Умовами, в яких працює зварна конструкція.Дріт діаметром до 1,6 мм, призначена для автоматичного аргонодугового зварювання, нагартовується розтягуванням з метою надання їй більшої жорсткості для кращого проходження між роликами і в мундштуці. Дуже важливо отримати нагартовку постійну по довжині і певною мірою[6].
3.ОБРОБКА РЕЗУЛЬТАТІВ
Зварений шов при зварюванні плавленням утворюється в місці з'єднання металевих заготовок в результаті сплаву присадочного матеріалу зі зварюваним. В одержуваних зварних з'єднаннях можна виділити три зони, що відрізняються один від одного структурною будовою: зона наплавленого металу (шов) – I, зона термічного впливу (околошовная) – II, зона основного металу – III. Структура і властивості металу останньої зони в процесі зварювання не змінюються. Метал же шва і околошовной зони зазнає фазові перетворення внаслідок нагріву і подальшого охолодження. Отже, якість зварного з'єднання в основному визначається властивостями металу цих двох зон.
Вивчення мікроструктури починають з розгляду мікрошліфа під мікроскопом до травлення. Це дозволяє виявити мікродефекти: пори, тріщини, неметалеві включення.
Зварюванні піддавали колосники зі сталі 20Х13 до якої приварювалися ребра жорсткості з різних дротів. Обробку вели методом TIG і MIG на установці, що включає газобалонне обладнання, вольфрамовий електрод і пристрій його переміщення.
На одній з граней зразків наносили одну або кілька зміцнених доріжок. Макроструктуру вивчали неозброєним оком і за допомогою мікроскопа МБС-9.
На малюнку 3.1 показано щілинне сито з якого вирізалося 18 зразків.
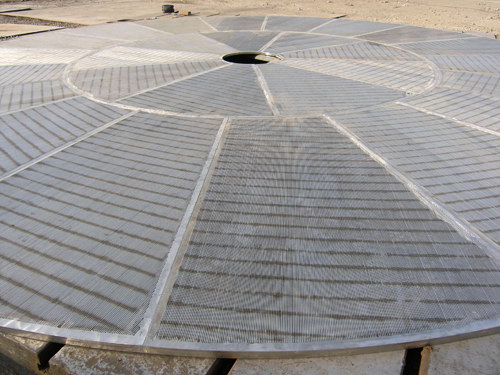
Малюнок 3.1 – Сито щілинне зварне для фільтр-чана
На зразках виготовляли поперечні шліфи за звичайною методикою. Підготовку поверхні, шліфування та полірування зразків ведуть за допомогою абразивних матеріалів та інструментів. Абразивні матеріали являють собою наждачний папір від великого до дрібного абразиву.Приготування мікрошліфів складається з декількох послідовних процесів: підготовки плоскої поверхні, шліфування та полірування.Плоску поверхню готують на торцевій поверхні зразка. Зразки обробляли на обертовому шліфувальному колі.
При ручному способі шліфування на жорстку плоску підкладку (товсте скло), розташовану горизонтально, кладуть шліфувальну шкурку. Зразок ставлять на папір заторцованной площиною і шліфують послідовно у взаємно перпендикулярних напрямках з легким натиском до повного знищення рисок, що залишилися після торцювання. Закінчивши шліфування на шкірці з найдрібнішим зерном, зразок промивають проточною водою і полірують.Щоб остаточно вирівняти поверхню, шліф полірують до дзеркального блиску. Полірування шліфу механічним способом проводиться на полірувальному верстаті. При поліруванні шліф періодично повертають для більш рівномірної обробки всієї поверхні.
На шліфах досліджували мікроструктуру на мікроскопі "Neophot-21". Структуру виявляли травителем №14 по Коваленко.На малюнку 3.2 і 3.3 показана мікроструктура реберного зразка № 2.
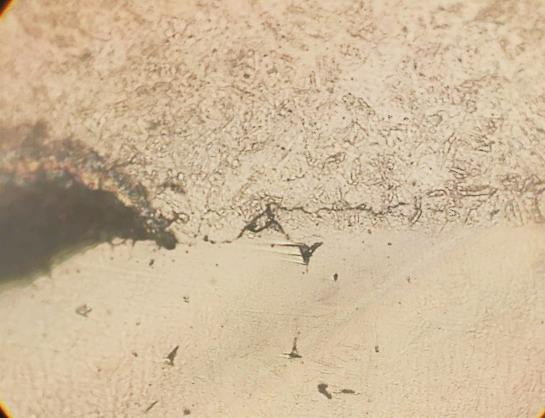
Малюнок 3.2 – Зразок № 2 (присадний дріт Св-08) х600
На малюнку 3.2 видно тріщину, яка з'явилася після зварювання.
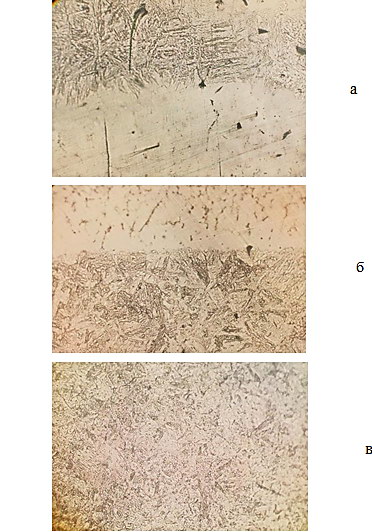
Малюнок 3.2-мікроструктура зразок № 2 (присадний дріт Св-08) Х600
З малюнка 3.3 а – межа ребро і зварений шов, б - зварний шов, який має мартенситну структуру, в-колосник зі сталі 20Х13, мартенситної структури.
Висновки
Підвищення вмісту вуглецю в сталях, з одного боку, дозволяє поліпшити властивості зварного з'єднання за рахунок термообробки, а з іншого – погіршує зварюваність через охрупчивания ЗТВ. Усунути зазначені труднощі дозволяє правильний вибір теплового режиму зварювання. Неприпустимими дефектами зварних з'єднань і швів, виявленими зовнішнім оглядом, є:
- Тріщини всіх розмірів і напрямків;
- Місцеві напливи загальною довжиною більше 10 мм на ділянці шва 1000 мм;
- Підрізи глибиною більше 0,5 мм при товщині найбільш тонкого з зварюваних елементів до 20 мм включно;
- Пори в кількості більше 4 штук на довжині шва 100 мм, при цьому максимальний розмір пір не повинен бути більше 1,0 мм, при товщині зварюваних елементів до 8,0 мм включно, і більше 1,5 мм при товщині зварюваних елементів понад 8,0 мм до 50,0 мм включно;
- Незаварені кратери .
Встановлено, що при використанні присадного дроту Св-08 на зразку № 2 виникла тріщина. З фотографій мікроструктури зразка № 2 структура колосника і зварного шва складається з мартенситу.
Перелік посилань
- Щелевые сита: Каталог продукта [Электронный ресурс]. – Режим доступа: http://www.ruseurositex.ru/docs/slotted_sieve.pdf
- Вайсберг, Л.А., Просеивающие поверхности грохотов. Конструкции, материалы, опыт применения /Л.А. Вайсберг, А.Н. Картавый, А.Н. Коровников // СПБ.: Изд-во ВСЕГЕИ. - 2005. — 252 с.
- ГОСТ 9074-85 Сетки щелевые на соединительных шпильках. Технические условия (с Изменениями N 1, 2). - Введ 1987-01-01.- М.: ИПК Издательство стандартов, 2003
- Химушин, Ф.Ф. Нержавеющие стали .- М: Металлургия, 1966. – 776 с.
- Белугин, К.Н. Преимущества использования продукта ARCAL 1 TM (99,998% Ar) для сварки аустенитных нержавеющих сталей / К.Н. Белугин, В.В. Бисин, И.М. Лозинский // Металлообработка. – 2012. - № 4. – С. 47-50.
- Масаков, В.В. Сварка нержавеющих сталей: учеб. пособие / В.В. Масаков, Н.И. Масакова, А.В. Мельзитдинова. – Тольятти: ТГУ, 2011. – 184 с.