Актуальність темы
Поверхні прокату піддаються зачистці. Залежно від групи поверхні заготівку піддається вибірковій або суцільній зачистці. Зовнішній шар знімають рівними борозенками уздовж циліндричної частини прутка в місцях, що мають дефекти. Обдиранню піддаються заготівки, поставка яких за технічних умов і стандартів повинна проводитися в обідраному стані, а також заготівки, які вимагають переточування на менший діаметр через поверхневі дефекти. Обдирання прокату проводиться на бесцентрово-токарних верстатах 9А340Ф1 і КЖ9340.
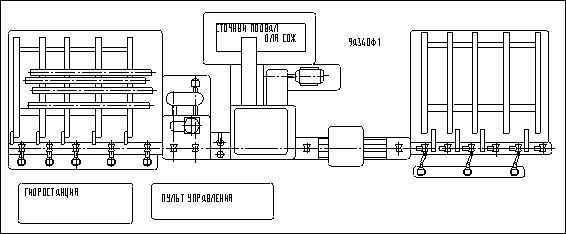
Малюнок 1 - Обдирний верстат 9А340Ф1
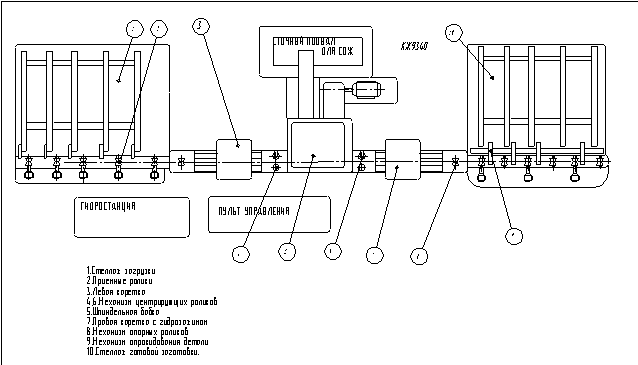
Малюнок 2 - Обдирний верстат КЖ9340
Безцентрово-токарні обдирні верстати працюють у порівняно тяжких умовах, в умовах більших динамічних навантажень. Тому часто відбуваються поломки, що приводить до простою. Для успішної експлуатації верстатів в умовах перебудови народного господарства нашої країни використаються нові принципи й підходи для рішення завдань технічного обслуговування й ремонтів. До таких нових підходів на сучасному етапі в першу чергу ставиться широке використання стаціонарних засобів технічної діагностики, що дозволяють скоротити витрати праці на обслуговування й ремонт.

|
Мета й завдання
Ціль роботи полягає в пошуку найбільше часто вихідних з ладу вузлів верстатів для встановлення на них датчиків. Для цього необхідно:
- зробити аналіз відмов;
- вибрати метод діагностування;
- визначити крапки установки датчиків;
- розробити стаціонарну систему діагностування.

|
Наукова новизна
Ціль роботи: розробити 32-канальну стаціонарну систему діагностування для безцентрово-токарних верстатів 9А340Ф1 і КЖ9340.До цього цим питанням мало хто займався. Саме тому вона представляє наукову новизну як для кафедри «МОЗЧМ», так і для персоналу обслуговуюче дане встаткування.
|
|
Практична цінність
Планований практичний результат: система діагностування дозволить стежити за працездатністю верстатів автоматично за допомогою приладів й у випадку критичного стану одного з вузлів, сповістить операторові на пульт керування верстатом про несправності.

|
Огляд існуючих досліджень
Проблеми:
Безцентрово-токарні обдирні верстати працюють у порівняно тяжких умовах, в умовах більших динамічних навантажень. Основними відмовами таких верстатів є :
- Неполадки подачі змащення в шпиндельний вузол. Це приводить до дострокового зношування ущільнюючих манжет. Така поломка найчастіше відбувається через малу подачу масла, і подачі великої кількості повітря до підшипників шпинделя (у цих верстатах застосовують систему змазування “Масло-повітря”). .
- Заклинювання підшипників на роликах, що подають. Заклинювання походить від удару заготівлі при влученні її на ролики. Також однієї із причин заклинювання може бути й недостача змащення в підшипниках роликів.
- Прокручування заготівлі в тисах Відмова походить від малого зусилля на притискному гідроциліндрі. Причин поломок гідроциліндра дуже багато: зношування ущільнень, забруднення трубопроводу, що підводить, неполадки в насосній установці й т.д. Тиса (ролики) мають рифлену поверхню. Ушкодження цієї поверхні приводить до зменшення сили тертя між заготівлею й поверхнею. Цей фактор також впливає на притискне зусилля й навіть при нормальному робочому тиску гідроциліндра заготівля може прокручуватися. Ушкодження поверхні тисів може відбуватися й через малу твердість матеріалу, що грає дуже більшу роль при експлуатації механізму.
- Нерівномірна подача заготівлі. Однієї із причин несправності може бути проблеми із приводом, другою причиною може бути поверхня, що зносилася, напрямних верстатів. Напрямні мають не ідеально рівну форму, і саме через перепади нерівностей привод переміщається нерівномірно.
- Перегрів маслостанції. Перегрів говорить про те що, несправна система змащення, або з'явилися деталі, між поверхнями яких підвищене тертя [7,стр.56]. Якщо вчасно не звернути увагу, то це може привести до аварійної ситуації.
Усе вище наведені відмови можуть привести до зупинки встаткування, і тому вимагають додаткової уваги. Дуже немаловажно за ними стежити, тому що навіть заклинювання підшипників може привести до значних матеріальних втрат для підприємства.
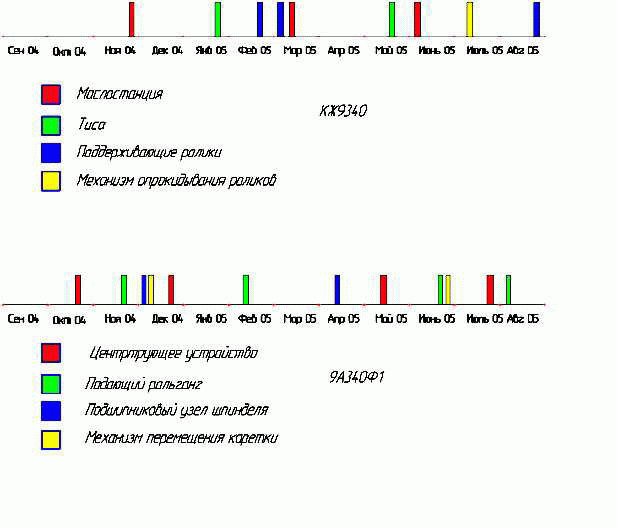
Малюнок 3 - Тимчасовий аналіз відмов верстатів
Рішення:
Для діагностики деталей, що входять у характерні вузли, виберемо наступні діагностичні параметри:
1. Рівень шуму;
2. Рівень вібрацій ;
3. Температура;
4. Деформації.
Для фіксації й контролю перерахованих вище параметрів можна застосувати наступні види засобів діагностування:
1. Ручний або електронний стетоскоп;
2. Віброметр ВШВ-003-1М;
3. Зубомір, індикаторний щуп Г112-5-0ММ11;
4. Температурні датчики.
У верстатах використаються підшипники кочення, зубчасті передачі, а так само можливі зачіпання й кавітація, то необхідно стежити за високочастотної складової вібрації. Підшипники кочення зручно діагностувати по вібрації, зосередженої на частотах порядку кілогерц (50-70 гармоніки від оборотної частоти). Дефекти зубчастих передач локалізуються на частотах «зачеплення», рівних добутку частоти обертання шестірні на число зубів, що перебувають на ній. Контрольована смуга повинна містити в собі частоту зачеплення. При ймовірності виникнення зачіпань, вібрація, так само як і при дефектах підшипників коченні має сплеск на декількох кілогерцах. У системі моніторингу для виміру вібрації можуть використатися як автономні датчики, установлювані в крапки виміри з використанням магніту або гвинтової шпильки або утримувані вручну при використанні вимірювального щупа, так і стаціонарно встановлені штатні датчики системи безперервного контролю вібрації. П'єзоелектричні акселерометри - самі універсальні й найбільше часто використовувані датчики на сьогоднішній день. Акселерометр є перетворювачем механічних коливань об'єкта в електричний сигнал пропорційний виброприскоренню. У результаті п'єзоелектричного ефекту на поверхні п”єзоелемента виникає електричний сигнал пропорційний силі, що впливає, і прискоренню механічних коливань. Частотний діапазон від 0 до 1/3 резонансної частоти акселерометра (звичайно 30 кгц). Акселерометри мають в основному лінійну амплітудну чутливість, стабільно працюють тривалий час, бідують тільки в періодичному калібруванні. Перегрів маслостанції можна контролювати термодатчиком, який би передавав сигнал про перегрів на пульт програмістові.
Ефективність:
Ефективність металургійних підприємств значною мірою буде визначатися надійністю встаткування. Для успішної експлуатації металургійних верстатів використаються нові принципи й підходи для рішення завдань технічного обслуговування й ремонтів. До таких нових підходів на сучасному етапі в першу чергу ставиться широке використання обчислювальної техніки й засобів технічної діагностики, що дозволяють скоротити витрати праці на обслуговування й ремонт. Відносно невисока вартість переносних систем (в 2-3 рази нижче вартості систем провідних західних виробників) і підвищена ремонтопридатність властиво стаціонарних систем діагностики, що дозволяє швидко відновлювати їх після ушкоджень при проведенні ремонтів машин, що діагностуються дозволяють вигравати конкурентну боротьбу в західних виробників. Цьому сприяє й діяльність вітчизняних фірм по навчанню й підтримці користувачів діагностичних систем. Як правило, багато підприємств починають впровадження систем моніторингу й діагностики з переносних систем, що не вимагають тривалої підготовки фахівців. Такі системи окупаються в 2-3 місяця, особливо на великих виробництвах. І лише на другому етапі, у процесі модернізації машин й устаткування, починають монтуватися й уводитися в дію невеликі стаціонарні системи моніторингу й діагностики, розраховані на 50-100 точок контролю.

|
Основні результати роботи
1. Визначення коефіцієнта запасу міцності колеса редуктора:
Для зубчастих коліс коефіцієнт запасу міцності розраховують по двох показниках:
- По згибу:
nизгибающее=(G изгиб.факт.*K напр)/[G]изгиб.допуск.
где Кнапр.-коефіцієнт який враховує зміну напруг вигину (Кнапр=1,2 тому що передача реверсивна),
[G]изгиба-допускаєме значення напруги вигину:
[G]изгиб.допуск.=(0,8...0,9)Gтеор.
где где Gтекучести-предел плинності
(для Ст40Х = 700 МПа) [1,табл.2,4, стр 43-44]
[G]изгиб.допуск.=0,8*700=560 МПа
G изгиба фактическое –фактична напруга вигину,
Gизгиба фактическое=10HRC+300=10*50+300=800 МПа
nизгиба=(800*1,2)/560=1,71
- По контактній міцності:
nконтактное=G конт.факт.*Zдолговечности)/[G]конт.допуск.
где Zдолговеч.-коефіцієнт довговічності (Zдовговічності=1,8) [1,рис. 2,6, стр. 40],
,
[G]контакт допускаемоедопускаемоедопускаєме значення напруги по контактній міцності:
[G]конт.допуск.=1,8Gтекуч.
где где Gтекучести-предел плинності (для Ст40Х = 700 МПа)
[1,табл.2,4, стр 43-44]
[G]конт.допуск.=1,8*700=1260МПа
G конт.фактическое –фактична напруга по контактній міцності,
Gконт.фактическое=17HRC+200=17*50+200=1050 МПа
nконтакт.=(1050*1,8)/1200=1,5
2.Визначення зусилля різання:
P=CpTxSyVn
где Cp- - постійна, котра характеризує вид обробки (Cp=300).[2, табл.20, стр.429].
x, y, n –показники ступеня,
x=1,y=0.75, n=-0,13 [2, табл.20, стр.429].
t –довжина леза різця (t=15мм),
s –подача заготівки (s=1.3 мм/об),
v –швидкість різання, визначимо по формулі:
V=3.14*n*D/60
где n –частота обертання шпинделя (n=2,33 об/сек),
D –діаметр оброблюваної заготівки (D=200 мм),
V=3.14*2.33*0.2/60=0.0244 м/с
Зусилля різання:
P=300*151*1,30,75*24,4-0,13=3624,2 Н
3. Порушення врівноваженості валів - дисбаланс.
Вібрація неврівноваженого вала проявляється у вигляді синусоїдальних коливань із частотою обертання вала. У спектрі коливань при цьому є присутнім значний пік на частоті обертання: fповр = fвp, где fповр - частота прояву ушкодження; fвр - частота обертання вала. Тому що дисбаланс приводить до збільшення навантажень на опори, у більшої ступінь проявляються й інші ушкодження на частотах кратних частоті обертання (гармоніках).
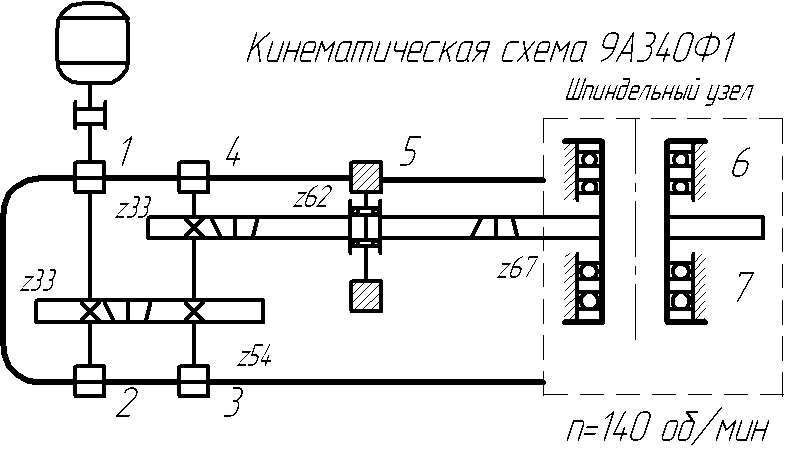
Малюнок 4 - Кінематична схема 9А340Ф1
fповр1=n*(67/33)*(54/33)=140*(67/33)*(54/33)=465.12 ГЦ
fповр2=n*(67/33)=140*(67/33)=284,24 Гц
fповр4=n=140 Гц
4. Ушкодження підшипників кочення шпиндельного вузла.
Поява великої кількості складових у спектрі виброприскорення в районі власних частот підшипників (1000...5000 Гц). У спектрі високочастотного сигналу або в спектрі коливань виникають одиночні або періодичні піки із частотою можливих ушкоджень підшипника :
- ушкодження зовнішнього кільця:
fнк0.5*Z*fвр=(1-d*cosβ/D)=0.5*30*140*(1-(52/740))=1952.4 Гц
- ушкодження внутрішнього кільця:
fвк0.5*Z*fвр=(1+d*cosβ/D)=0.5*30*140*(1+(52/740))=2247.6 Гц
- ушкодження тіл кочення:
fтк=(D*fвр/d)(1-(d*cosβ/D)2)=(740*140/52)(1-(52/740)2)=1982.5 Гц
- ушкодження сепаратора:
fc=0.5*fвр*(1-d*cosβ/D)=0,5*140(1-(52/740))=65.1 Гц
де fBP - частота обертання вала;
z - число тіл кочення;
d - діаметр тіл кочення;
; β- - кут контакту;
D - діаметр окружності, що проходить через центри тіл кочення.
5. Ушкодження зубчастих передач.
Поява в спектрі одиночних або періодичних зубцових частот:
fповр = z fBp, де z - число зубів колеса. Поява в спектрі бічних складових із частотою обертання. Можливі гармонійних складових даних ушкоджень:
fповр.Z67=Z67*fвр=67*140=9340 Гц
fповр.Z62=Z62*fвр=67*140=9340 Гц
fповр.Z33-2=Z33*fвр=33*(67/62)*(62/33)*140=9340 Гц
fповр.Z54=Z54*fвр=54*(67/62)*(62/33)*140=15349.1 Гц
fповр.Z33-1=Z33*fвр=33*(67/62)*(62/33)*(54/33)*140=15349.1 Гц

Висновки
Сучасні системи моніторингу й діагностики реально забезпечують перехід на обслуговування й ремонт машин по фактичному стані. У цей час жодне велике західне встаткування не поставляється без стаціонарних систем, і економічний ефект від її використання враховується при плануванні експлуатаційних витрат. Наша промисловість відрізняється від західної тем, що більшість машин й устаткування давно виробили ресурс і вимагають капітального ремонту або заміни. З огляду на цей факт, системи моніторингу й діагностики російського виробництва стали пристосовуватися до роботи з таким устаткуванням, і основну увагу приділяють глибокій діагностиці найбільше аварійнонебезпечних вузлів. Цей факт, а також відносно невисока вартість переносних систем (в 2-3 рази нижче вартості систем провідних західних виробників) і підвищена ремонтопридатність властиво стаціонарних систем діагностики, що дозволяє швидко відновлювати їх після ушкоджень при проведенні ремонтів машин, дозволяють вигравати конкурентну боротьбу в західних виробників. Цьому сприяє й діяльність вітчизняних фірм по навчанню й підтримці користувачів діагностичних систем. Як правило, багато підприємств починають впровадження систем моніторингу й діагностики з переносних систем, що не вимагають тривалої підготовки фахівців. Такі системи окупаються в 2-3 місяця, особливо на великих виробництвах. І лише на другому етапі, у процесі модернізації машин й устаткування, починають монтуватися й уводитися в дію невеликі стаціонарні системи моніторингу й діагностики, розраховані на 50-100 крапок контролю.

Література
1.Методическое указание к самостоятельной работе над курсовым про-ектом по деталям машин», раздел 3 «Эскизный проект. Технический проект» /сост. В.С.Горелик и др.- Донецк: ДПИ, 1992, 84с.
2.Справочник технолога машиностроителя» том 2, А.Н.Малов.М.: «Машиностроение», 1972, 568с.
3.Предупреждение разрушения деталей забойного оборудования / Н. Б. Шубина, Б. П. Грязнов, И. М. Шахтин и др. – М., Недра, 1985. - 215 с.
4. Сидоров В.А., Серебров Л.М. «Основы работы с виброметрами-анализаторами» // Конспект лекций семинара-практикума – Донецк,2003. – 113 с.
5. Марутов В.А. и Павловский С.А. Гидроцилиндры. Конструкция и расчет. – М "Машиностроение", 1966. – 315 с.
6. Производство блюмов, слябов и заготовок из углеродистых и легированных сталей в обжимном цехе. Технологическая инструкция. ТИ – 234 – П.03.01 – 95. Донецкий металлургический завод.: – Донецк, 1995. – 225 с.
7. Целиков А.И., Полухин П.И., Гребеник В.М. и др. Машины и агрегаты металлургических заводов. Том 3. Машины и агрегаты для производства и отделки проката. – М.: Металлургия, 1988. – 576 с.
8. Королев А.А. Конструкция и расчет машин и механизмов прокатных станов. Учеб. пособие для вузов. – М.: "Металлургия". 1985. – 367 с.
9. Анурьев В.И. Справочник конструктора-машиностроителя: В 3-х т. Т.1. – М.: Машиностроение, 1982. – 736 с.
10. Раздаточный материал к выполнению расчетов крюковвывх пдвесок по диссцмплине: "Подъемно-транспортные машины". П.И. Пузырьков. Днепропетровск ., 1991, 28 с.

| |