Понятие готовности кокса можно отождествить с моментом завершения образования его тонкой структуры при достижении температуры около 9009. Последующее нагревание на 300—500° уже не приводит к каким-либо существенным изменениям.
Тонкая структура кокса может характеризоваться сорбционной
способностью, теплотами смачивания и электропроводностью. Стадию процесса коксования удобнее всего определять, измеряя электрическое сопротивление в монолитном слое кокса.
Изучение изменения электрического сопротивления слоя шихты и кокса в различных участках по ширине камеры коксовой печи, проведенное нами с помощью гребенки электродов, показало, как постепенно слой за слоем достигался постоянный минимум сопротивления кокса.
Куски кокса, отобранные из участков печи (1 м над подом), где процесс коксования не только был закончен, но кокс еще был выдержан дополнительно 3 часа, при достигнутой высокой температуре, обладали по всей своей длине почти одинаковыми характеристиками их тонкой структуры. Сопротивление кусков у «капусты» и у «шва» имело одинаковую величину, не превышавшую 0,5 Ома.
Таким образом, на образцах производственного кокса подтвердились данные лабораторных исследований, согласно которым завершение образования тонкой структуры кокса должно выражаться в достижении постоянного минимума сопротивления, а на кусках производственного кокса — определяться неизменной минимальной величиной сопротивления отдельных участков по всей длине куска. Все это относится к сопротивлению монолитного слот куска, а не кокса, измельченного в порошок.
Замеры, на кусках кокса, полученных из заведомо не готовых печей, показали постепенный, а затем резкий рост сопротивления при продвижении от середины куска кокса ко шву коксового пирога.
Следовательно, если определить сопротивление монолитного слоя кокса на отдельных участках по всей длине куска и сопоставить полученные данные с динамикой изменения сопротивления в камере печи при данном режиме коксования, можно установить, на какой стадии процесса был выдан кокс, т. е. тем самым определить степень его готовности.
Описанные наблюдения и выводы из них послужили основой для разработки специального прибора и метода определения готовности кокса.
Прибор (рис. 1) состоит из контактных подвижных штекеров и омметра с питающим элементом на 1,4 в. В текстолитовом блоке высверлены два цилиндрических углубления, где помещаются штекеры с возвратными пружинами. Концы каждого штекера выходят наружу через текстолитовую стенку прибора и дно блока. К наружным заостренным концам штекеров прижимается испытуемый образец кокса. Оба штекера, преодолевая упругость пружин, вдвигаются внутрь прибора, причем внутренние готы штекеров замыкают цепь питания омметра. На шкале последнего в этот момент делается отсчет. Как только кусок кокса убирается с прибора, пружины возвращают штекеры в исходное положение. Таким образом, устройство гарантирует
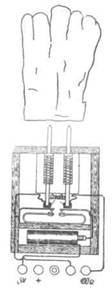
Рис. 1. Схема прибора
от повышенных, неверных показаний при недостаточно плотном контакте между штекером и коксом. В качестве выключателя цепи питания нами использованы контакты. телефонного реле, поставленные на ребро. Такое положение контактов исключает осаждение на них пыли. Цени измеряемого сопротивления составлена из клеммы омметра, штекера, образца кокса, другого штекера и клеммы омметра. Соединения подвижного штекера осуществлены гибким проводом на пайке. Весь прибор вместе с элементом питания заключен в деревянный или текстолитовый кожух, укрепленный на доске. Снаружи остаются лишь концы штекеров и омметр. Для удобства отсчетов шкала омметра градуирована непосредственно з «степенях готовности» кокса, т. е. разделена на зоны, окрашенные в различные цвета.
Производительность работы на приборе равна 400 кускам (или 120 кг) кокса в час.
Метод проверялся на многочисленных образцах кокса, полученных из разнообразных шихт. При этом было установлено, что на показатель готовности ни трещиноватость, ни влажность, ни даже его макроструктура (губка, капуста, наличие трещин) не оказывают никакого влияния.
Точность метода зависит от величины пробы и точности настройки омметра. При пробе в 200 кг ошибка составляет 1—2%.
Метод оценки степени готовности отдельных кусков кокса дает возможность разделить всю пробу на части по степеням готовности, количественно определить выход каждой части и испытывать их раздельно.
Таким образом, можно установить влияние степени готовности на механические свойства кокса.
Металлургический кокс (после коксосортировки) имеет небольшой процент по весу мелких классов (5—6%). Поэтому, чтобы не занимать время сортировкой мелких кусков, в пробу отбирался кокс только крупнее 40 мм.
Деление кокса по степеням готовности проводилось -следующим образом. В каждом куске кокса определялось сопротивление в части, наиболее удаленной от «капусты», а в кусках, где ясно был заметен шов коксования, — непосредствен-• но на нем. В сомнительных случаях, когда на куске не было видно ни «капусты», ни «шва», сопротивление измерялось на обоих концах. Кусок относился к той или иной группе готовности по наибольшему сопротивлению.
Только в кусках первой степени готовности сопротивление во всех частях могло быть одинаковым.
Для данной шихты степень готовности была установлена в следующих пределах сопротивлений:
I — от 0 до 0,7 ом — полностью готовый кокс, включая перекал;
II — от 0,7 до 5,0 ом— нормально готовый (с точки зрения структурных преобразований).
III — от 5,0 ом до бесконечности — недопал.
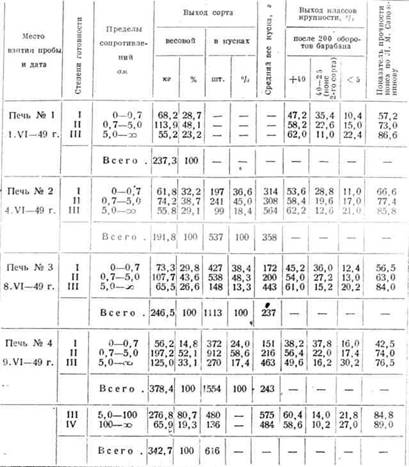
Для опытов были выбраны отстающие по температурам печи, которые, как правило, давали кокс с недопалом. Части пробы, разделенной по степеням готовности, подвергались испытаниям в малом барабане. Вычислялись показатели прочности по методу Л. М. Сапожникова и по методу Кузнецкого металлургического комбината для каждой части отдельно. Результаты приводятся в таблице.
Вес проб составлял 192—378 кг. Как видно из таблицы, процент готовых и неготовых кусков каждой печи меняется в широких пределах. Наибольший процент в этих печах составляет вторая степень готовности. Колебания в цифрах вполне понятны, так как все выбранные печи имели фактически различные режимы коксования. Из графы, где показан средний вес куска, можно видеть его возрастание от I к III степени готовности. Куски становятся крупнее.
Прочность кокса по показателям Сапожникова и КМК сильно возрастает при переходе от кокса I степени к коксу III степени готовности. Показатель Сапожникова достигает величины 86,6.
Вместе с ростом показателей прочности уменьшается также и выход класса 40—25 (кокс второго сорта), что также улучшает качество кокса. Однако количество мусора (класс меньше 5) возрастает при понижении готовности кокса. Нетрудно заметить, что уменьшение выхода класса 40—25 происходит в большей степени, чем возрастание доли мусора. Следовательно, благоприятный эффект преобладает.
Если принять, что величина остатка на сите 40 мм характеризует прочность кокса «а раскалывание, а выход мусора — на истирание, то можно утверждать, что по мере снижения степени готовности (от I до III) прочность его на раскалывание возрастает, а истираемость увеличивается. Не следует отсюда делать вывод, что сырой кокс лучше готового, ибо прочность может возрастать только до определенного предела, а мусористость беспредельно.
Нужно обратить внимание на незначительные расхождения всех показателей прочности для кокса II степени готовности. Несмотря на то, что кокс отбирался за разные дни из различных печей, все же сходимость результатов гораздо большая, чем при параллельных испытаниях кокса из одной и той же партии с пробами точно одинакового ситового состава, но не разделенными по степеням готовности. Как известно, расхождение показателя на 8-10единиц вполне допустимо. Напрашивается вывод, что сходимость параллельных испытаний в большой степени зависит от одинакового соотношения фракций каждой степени готовности, чем от постоянства гранулометрического состава.
В заключение разбора таблицы обратим внимание на сильное увеличение процента кокса III степени готовности в печи № 4. Результаты испытаний в барабане этого кокса показывают, что показатели прочности его ниже, чем во всех других печах, а процент мусора больше. Поскольку границы III степени готовности не были ограничены каким-либо пределом сопротивления, в этот класс мог попадать совсем сырой кокс, прочность которого весьма невелика, чтобы отделить кокс III степени готовности от совсем неготового,
III степень была ограничена пределом сопротивления в 100 ом и введена IV степень готовности, которая определялась сопротивлениями от 100 ом до бесконечности.
Остатки проб III степени готовности от всех печей (342,7 кг) были вновь рассортированы на III (в новых пределах сопротивления) к
IV степени готовности и испытаны в малом барабане. Результаты испытаний приведены в последних строках таблицы. Показатель прочности по Сапожникову продолжает возрастать и достигает величины 89,0 для кокса IV степени готовности. В то же время показатель КМК для того же кокса несколько уменьшается. В этих пробах значительна разница только по мусору, что подтверждает сделанный ранее вывод о росте мусористости кокса с ростом недопала.
При наблюдениях за коксом при его выдаче можно обнаружить, что недопал встречается обычно только в верхней части пирога и головке.
Определить, как распределяется готовность по пирогу, можно лишь при условии полной сохранности пирога, т. е. до выдачи его в тушильный вагон.
Такие пробы кокса, отобранные на различных уровнях, представляют и другой интерес. Всякая разница в свойствах кокса таких проб может быть отнесена только за счет положения загрузки в камере, так как состав шихты и все условия коксования для одной камеры, естественно, будут такими же. Техника отбора таких проб была следующей. Часть коксового пирога длиной 3 м (в нашем опыте конец пирога) оставалась не выданной из шита двересъемной лебедки. Лебедка с горячим коксом была отведена на путь контрфорсной площадки, где пирог был затушен водой из шлангов. Большие зазоры между решеткой щита и пирогом позволили быстро охладить «цветную капусту» пирога по всей длине и предохранить щит от разогревания.
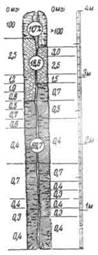
Рис. 2 Распределение готовности кокса в камере печи. Период коксования 14 ч. 30 м.
Готовность кокса по всей высоте пирога определялась, как обычно. Сопротивление каждого куска измерялось у шва. Прибор был снабжен длинным шнуром с вилкой на конце, которая прижималась к месту замера, что позволило установить прибор на площадке на безопасном расстоянии.
Результаты замеров готовности кокса в целом пироге приведены на рис. 2. Недопал целиком расположен в верхней части пирога и составляет 11,7% по объему. Ниже расположен готовый кокс (II степень готовности) 18,6% и дальше до самого пода печи - вполне готовый кокс с перекалом (69,7%).
Следует обратить внимание на постепенное повышение сопротивления (по пирогу снизу вверх) и на участок кокса с сопротивлением 0,7 ом на 1,5 м от пода. Такое распределение готовности бесспорно указывает «а значительную разницу температур по высоте камеры.
Следовательно, чтобы устранить «пестроту» кокса по готовности, нужно выравнивать температуру камер не только по контрольным вертикалам по длине всей батареи, как это делается обычно, но и по всей высоте камер.
Равномерный по степени готовности кокс будет иметь одинаковый минимум (в «капусте») и максимум (у «шва») сопротивления во всех частях пирога.
Изменяя температуру или время коксования, нужно будет ориентироваться, с одной стороны, на максимально допустимую величину сопротивления у шва, чтобы избежать большого количества недопала, образующего мелочь за счет истирания, с другой стороны — на минимально допустимую величину сопротивления во избежание излишнего перекала, приводящего к разрушению «капусты».
Метод определения готовности кокса по сопротивлению в монолитном слое был впервые применен на Кузнецком металлургическом комбинате имени И. В. Сталина при исследовании влияния режима коксования на качество кокса.
Новый метод определения готовности кокса позволяет количественно оценивать кокс по степени и равномерности его выжига и дает ориентировку для получения кокса желаемой степени готовности.