Коксованием называется метод термической переработки преимущественно каменных углей, заключающийся в их нагревании без доступа воздуха до 1000—1100°С, в результате чего топливо разлагается с образованием летучих продуктов и твердого остатка — кокса.
Целевым продуктом этого процесса является кокс, используемый главным образом в металлургической промышленности. По этой причине установки по производству кокса (коксовые батареи) часто включают в состав металлургических заводов, а для обогрева коксовых печей применяют низкокалорийный доменный газ, получаемый в качестве побочного продукта в доменном процессе. Расход кокса достигает 0,8 т на 1 т чугуна. В этом процессе кокс выполняет функцию топлива и одновременно является источником оксида углерода, который восстанавливает железо из руды. Наряду с этим кокс можно использовать в качестве генераторного топлива для получения горючих газов методом газификации.
Кокс характеризуется следующими основными показателями: истинная плотность 1800—1950 кг/м3, насыпная плотность 400—500 кг/м3, пористость 49—53%, выход летучих (на горючую массу) 0,7—1,2%, содержание углерода не менее 96,5%, влажность не более 5%, зольность 10—11%, содержание серы 1—2%, теплота сгорания 32 000 кДж/кг.
Наряду с коксом, выход которого составляет 70—80%, образуются летучие продукты. При их охлаждении и разделении получают надсмольную аммиачную воду (или сульфат аммония), смолу, обогащенную ароматическими углеводородами, и высококалорийный топливный газ. Большие масштабы металлургической промышленности и соответствующие мощности по выработке кокса, обуславливают получение значительных количеств побочных продуктов коксования, исчисляемых сотнями тысяч тонн в год. Вследствие этого приблизительно до середи-дины XX в. коксохимия была основным поставщиком сырья для крупнотоннажного тяжелого и тонкого органического синтеза. В настоящее время коксохимия в этом отношении заметно уступает нефтеперерабатывающей и нефтехимической промышленности, но тем не менее вклад коксохимических продуктов в сырьевую базу производства пластмасс, химических волокон, синтетических каучуков, красителей и других продуктов достаточно велик.
Следует подчеркнуть, что полукоксование и коксование — практически единственные процессы, позволяющие получать такое остродефицитное сырье, как крезолы, ксиленолы, резорцин и пирокатехин, производство которых на основе нефти пока не организовано в промышленных масштабах.
Теоретические основы процесса
При нагревании без доступа воздуха любые твердые топлива претерпевают примерно одни и те же изменения. Для молодых топлив с низкой степенью углефикации (торф, бурые угли) наибольшие превращения протекают при температурах ниже 550—600°С, поэтому они подвергаются только полукоксованию. Динамика происходящих при этом явлений рассмотрена выше (см. разд. 3 1.2). Каменный уголь направляют на высокотемпературную переработку — коксование. Из-за более низкого содержания кислорода в каменных углях количества продуктов, выделяющиеся из них на начальной стадии процесса, меньше, чем из торфа или бурого угля. Кроме того, отличительной особенностью многих каменных углей является переход их органической массы (ОМУ) в пластическое состояние при 350—450°С.
Коксование обычно осуществляют с внешним подводом тепла, поэтому все описываемые ниже процессы, начинаясь у стенок коксовой камеры, постепенно захватывают и зоны у ее центра. При нагревании угля до 200°С вначале происходит испарение влаги и удаление растворенных в угле газов, состоящих в основном из метана и азота За счет отщепления гидроксильных и карбоксильных групп в газовой фазе появляется некоторое количество оксида и диоксида углерода, а также пары пирогенетической воды. При последующем нагревании до 300°С разложение угольного вещества несколько интенсифицируется (о чем свидетельствует образование небольших количеств водорода и метана), однако существенной потери массы еще не наблюдается.
Температурный диапазон 350—450°С характеризуется изменением агрегатного состояния угля: из сыпучего он переходит в пластическое (тестоподобное) за счет того, что начинается выделение смолы. В результате термической деструкции органической массы спекающихся углей вначале образуется жидкая пленка на поверхности угольных частичек, которые как бы оплавляются. Затем происходит размягчение зерен, появляется пластический слой, толщина которого определяется свойствами угля и равна 15—30 мм Пластическая масса представляет собой сложную гетерогенную систему, состоящую из газообразной, жидкой и твердой фаз. Вначале она имеет высокую вязкость и достаточно хорошую газопроницаемость. По мере повышения температуры возрастает количество жидкой фазы, уменьшается вязкость пластической массы, а свободные промежутки между твердыми частицами сокращаются, в результате чего увеличивается сопротивление эвакуации газообразных продуктов. Вследствие этого возникает внутреннее давление, приводящее к вспучиванию среды.
При дальнейшем повышении температуры до 500—550°С происходит резкое уменьшение массы угля и бурное выделение газа и смолы При этом одновременно протекают вторичные реакции термического разложения компонентов смолы, за счет которых конечные продукты обогащаются наиболее термически стабильными соединениями (водородом, метаном, ароматическими углеводородами). В результате реакций полимеризации и поликонденсации продуктов разложения происходит накопление твердой фазы в пластической массе, вновь возрастают ее вязкость и газопроницаемость, и начинает формироваться жесткая структура полукокса. Постепенно жидкая фаза исчезает, а твердый остаток представляет собой полукокс.
При последующем увеличении температуры до 900—1000°С протекают термохимические превращения в твердой фазе, соответствующие переходу полукоксовой структуры в коксовую. Твердый остаток уплотняется, увеличивается его прочность и уменьшается объем — происходит усадка. Благодаря этому «коксовый пирог» отделяется от стенок камеры, что облегчает его выгрузку.
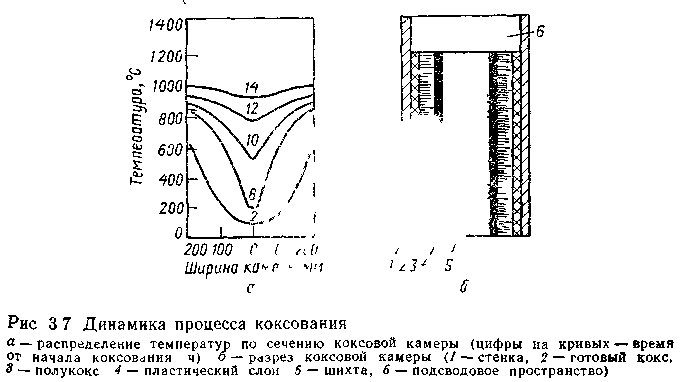
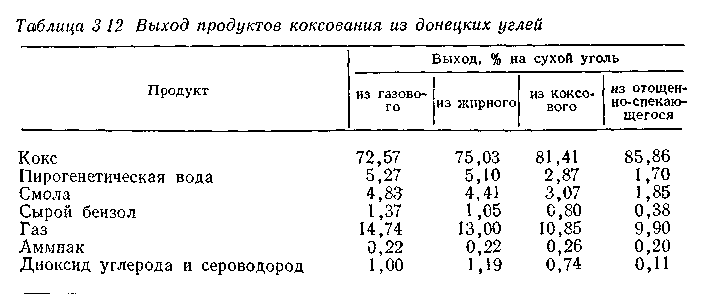
На рис. 3.7 показан разрез коксовой камеры и даны кривые распределения температуры по ее ширине в различные периоды коксования. Вследствие небольшой теплопроводности угольной шихты [от 0,75 до 0,8 Дж/(м·ч·К) или ~2·l0-4 Вт/(м·К)] температура в центре камеры заметно ниже, чем у стенок. Она выравнивается лишь через 13—14 ч. В соответствии с динамикой прогрева шихты в ней протекают описанные выше процессы. К концу коксования оба пластических слоя, перемещающиеся от стенок, соединяются в центре камеры, образуя шов, по которому «коксовый пирог» при выгрузке из печи распадается на две примерно равные части.
Большинство реакций вторичного превращения паров смолы происходит в подсводовом пространстве, над поверхностью раскаленного кокса. Оптимальные условия образования ценных побочных продуктов, получаемых при коксовании: температура 700—720°С, время пребывания паров смолы в подсводовом пространстве ~40 с.
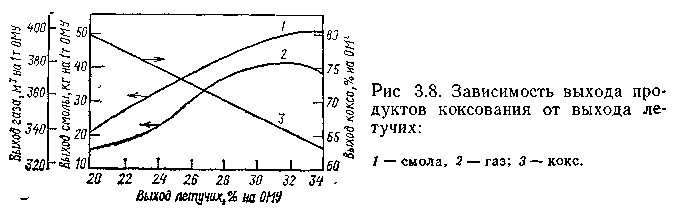
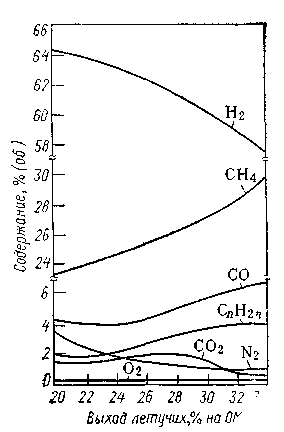 |
Рис. 3.9. Зависимость состава коксового газа от выхода летучих. |
К числу основных факторов, влияющих на выходы продуктов коксования, относятся свойства перерабатываемого угля. В качестве примера в табл. 3.12 приведены данные, полученные при коксовании донецких углей различных марок. Видно, что при переходе от газового угля к отощенно-спекающемуся (т. е. по мере уменьшения выхода летучих) нарастает выход кокса при соответствующем снижении количеств смолы, бензола, газа и пирогенетической воды.
Более наглядно взаимосвязь между свойствами угля, характеризуемыми выходом летучих, количествами кокса, смолы и газа, а также его составом, показана на рис. 3.8 и 3.9, на которых приведены данные для углей Рурского бассейна (ФРГ). Как видно из сопоставления рис. 3.8 и табл. 3.12, независимо от места добычи угля между содержанием в нем летучих и выходом продуктов коксования прослеживаются практически одни и те же зависимости. Что касается состава получаемого газа, то, как показано на рис 3.9, увеличение количества летучих в угле приводит к нарастанию в газе концентраций метана, оксида углерода и олефинов, тогда как содержание водорода и азота снижается, а объемная доля диоксида углерода проходит через максимум, равный ~2% (об.) при выходе летучих из угля ~28%.
Шихта, подвергаемая коксованию, как правило, состоит из смеси углей различных марок в следующих примерных соотношениях: 20% газовые, 40% жирные, 20% коксовые и 20% отощенно-спекающиеся. При этом учитываются следующие свойства отдельных технологических марок. Газовые угли характеризуются сравнительно небольшой толщиной пластического слоя, высоким выходом летучих и повышенной усадкой. Кокс из газовых углей обладает высокой реакционной способностью. Присутствие в шихте таких углей усиливает усадку «коксового пирога» и облегчает выдачу его из печи, а также увеличивает выход газа и химических продуктов коксования. При повышенном содержании газовых углей выход кокса уменьшается. Жирные угли являются главным компонентом шихты. Они обеспечивают ей хорошую спекаемость и придают коксу прочность. Однако при их повышенном содержании кокс получается трещиноватый и мелкокусковой. Жирные угли обусловливают вы В процессе приготовления шихты для коксования угли подвергают обогащению для снижения их зольности до 5—7%, многократному дроблению и рассеиванию. В итоге получают однородную смесь, на 90—95% состоящую из частиц размером менее 3 мм
Еще одним фактором, влияющим на выходы и состав продуктов коксования, является температура В табл. 3.13 приведены соответствущие данные, полученные при коксовании рурского угля с выходом летучих ~25% Видно, что по мере увеличения конечной температуры коксования возрастает объем получаемого прямого газа, а его плотность и теплота сгорания уменьшаются. Это объясняется изменением состава газа, который обогащается водородом за счет уменьшения доли метана и более тяжелых углеводородов. Небольшое повышение концентрации оксида углерода недостаточно для компенсации уменьшения калорийности газа вследствие сокращения содержания метана и этилена. Тем не менее теплота сгорания коксового газа, полученного при любой из указанных температур, весьма велика, и он может быть использован как эффективное газообразное топливо.
Количество образующейся смолы при повышении конечной температуры кокса до 1085°С достигает максимума (37,8 кг/т), а затем начинает уменьшаться за счет вторичных процессов разложения ее компонентов Это отражается на плотности смолы, которая непрерывно возрастает, и фракционном составе. Последний характеризуется уменьшением количества легких фракций (за исключением ароматизированной фракции 230—270°С) и повышением доли пека. В смоле увеличивается содержание нафталина при некотором сокращении количества его гомологов, а также фенолов
Выход бензола и его гомологов (так называемого сырого бензола), извлекаемых из коксового газа, достигает максимума (~10,57 кг на 1 т угля) при температуре 1132°С, а содержание в газе сырого нафталина непрерывно возрастает от 0,2 до 0,5 г/м? Количество аммиака, сероводорода и пирогенетической воды (конденсат) изменяется в небольших пределах при различных температурах коксования
Приведенные данные свидетельствуют о том, что газообразные и жидкие продукты, получаемые при коксовании, содержат большое число ценных компонентов, представляющих значительный интерес для осуществления на их основе многочисленных синтезов полимерных соединений, лакокрасочных материалов, химических средств защиты растений, лекарственных препаратов и т д
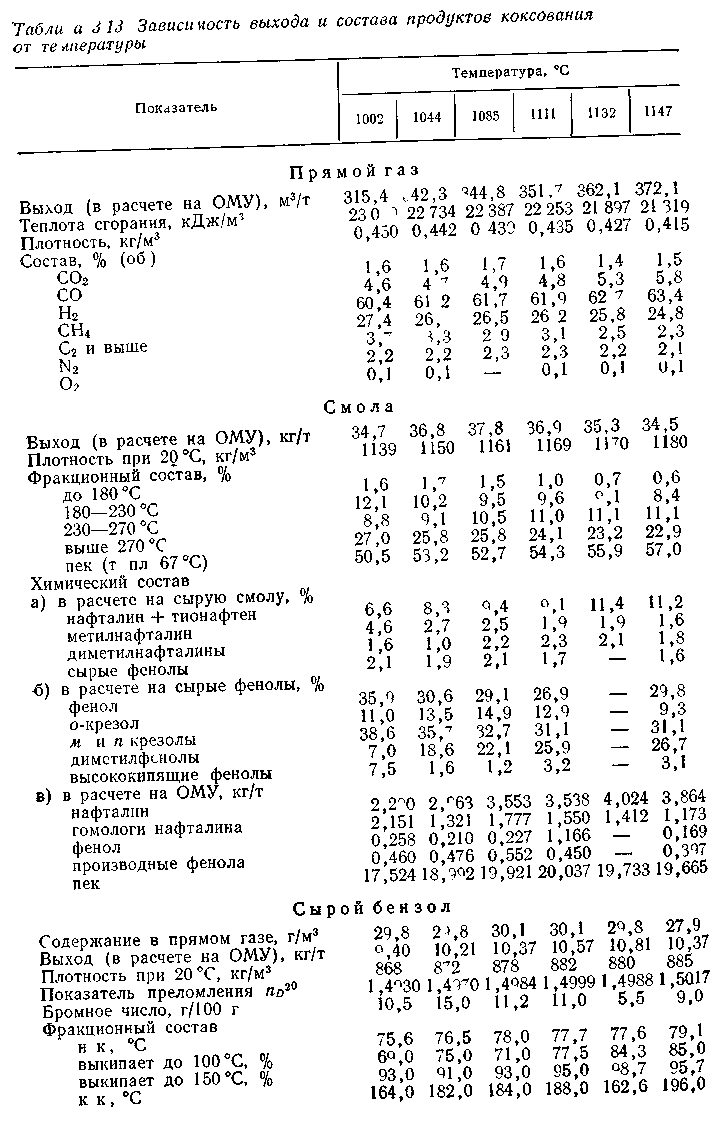
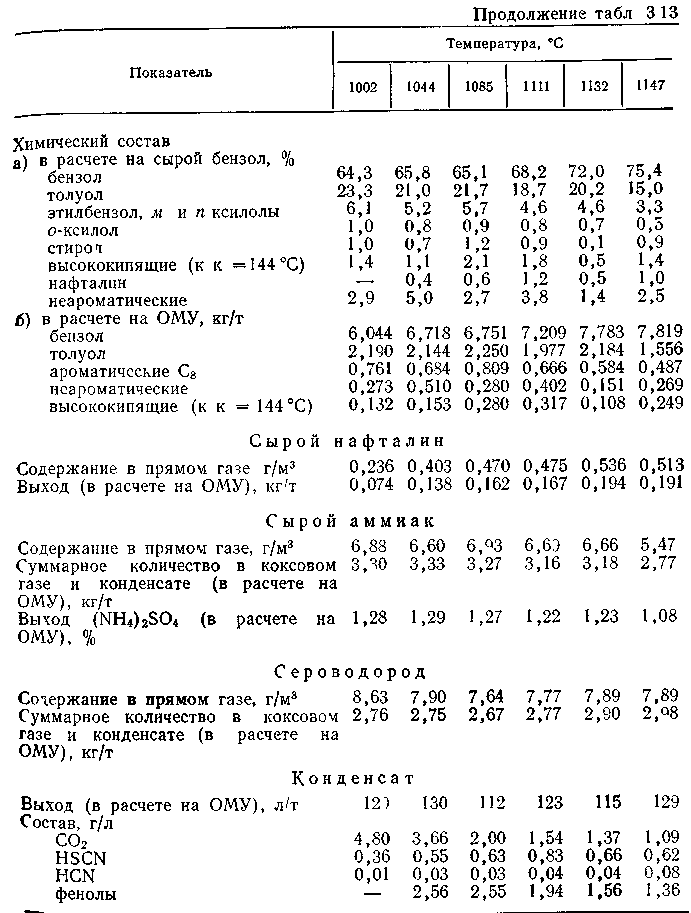
3.2.3. Аппаратурно-технологическое оформление процесса
В настоящее время существует несколько разновидностей коксовых печей, различающихся некоторыми деталями в системе обогрева, хотя принцип работы и основные узлы остаются без изменений на протяжении многих десятилетий В печах любой конструкции коксование угольной шихты ведут в узкой камере из огнеупорного кирпича Необходимое тепло подводят через боковые стенки камеры за счет сжигания газообразного топлива. Ввиду крайне низкой теплопроводности огнеупорных материалов и самой шихты процесс коксования требует длительного времени (12—14 ч) Камера коксовой печи имеет следующие размеры высота 5—6 м, длина 15—16 м, ширина 420—450 мм с коксовой (Коксовой называют ту сторону печи, откуда выводят кокс На противоположной стороне — машинной — находится специальная машина (коксовыталкиватель), которая с помощью штанги выталкивает кокс из камеры) стороны и 370—400 мм с машинной. Камера выполняется расширяющейся от машинной стороны к коксовой для облегчения выдачи «коксового пирога».
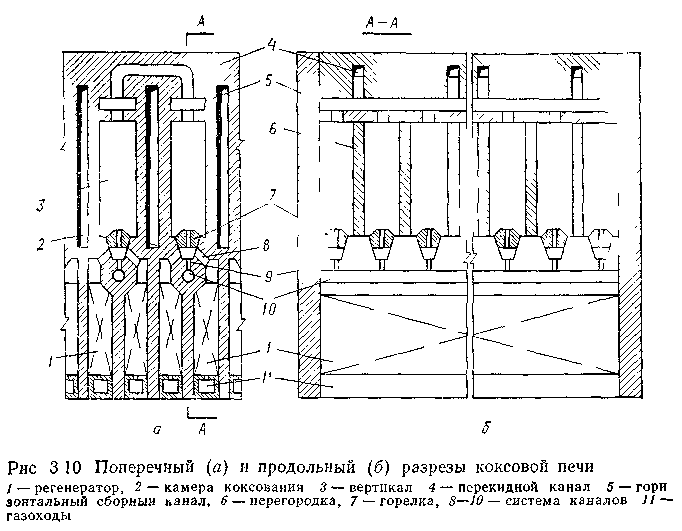
Основными элементами коксовой печи (рис. 3 10) являются: камеры коксования 2, обогревательные простенки, расположенные по обе стороны каждой камеры и разделенные вертикальными перегородками на отопительные каналы (вертикалы) 3, в которых происходит горение топливного газа; система каналов 8, 9 и 10, обеспечивающих подачу воздуха и топливного газа в горелки 7 вертикалов 3; регенераторы 1 для нагревания воздуха и топливного газа (если это необходимо). В качестве топлива чаще всего используется обратный коксовый газ (выводимый из системы очистки и разделения и содержащий в основном водород и метан). Этот газ подают в коллектор (корнюр) 10, а из него распределяют по горелкам каждого вертикала. В последнее время для отопления коксовых печей применяют также низкокалорийный доменный газ. В этом случае его, как и воздух, предварительно подогревают в регенераторах.
В своде каждой коксовой камеры имеются отверстия для загрузки шихты и вывода летучих продуктов коксования (на рисунке не показаны). По обе стороны коксовой камеры располагаются обогревательные простенки шириной 700—760 мм, разделенные перегородками 6 на вертикалы 5, представляющие собой узкие колодцы. Число вертикалов в каждом простенке велико — около 30, чтобы обеспечить равномерный обогрев коксовой камеры. В каждом вертикале имеется регулируемая горелка 7, в которую подают отопительный газ и воздух. Последний предварительно подогревается, проходя через регенераторы 1, соединенные каналами (косыми ходами) 8 с каждым вертикалом. Регенераторы заполнены огнеупорной фасонной насадкой, аккумулирующей тепло дымовых газов, а затем отдающей его нагреваемому воздуху. С помощью перекидных каналов 4, соединенных с горизонтальными каналами 5, обогревательные простенки попарно связаны друг с другом.
В вертикалах одного простенка происходит сгорание топливного газа. Образующиеся дымовые газы нагревают боковые стенки соседних коксовых камер, затем газы через горизонтальные и перекидные каналы попадают в вертикалы второго простенка, где тоже нагревают боковые стенки коксовых камер, а потом по косым ходам 8 направляются в регенераторы, нагревают насадку и через газоходы 11 выводятся в дымовую трубу. Для равномерного обогрева коксовых камер через каждые 20—30 мин проводится кантовка — изменение направления подачи отопительного газа, воздуха и отбора дымовых газов.
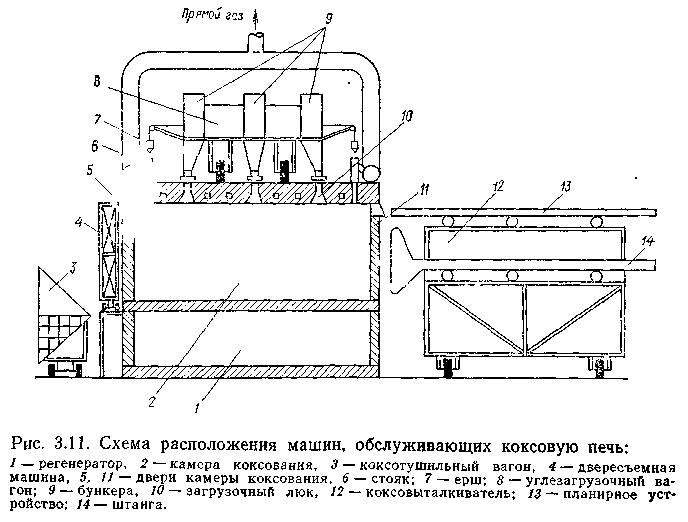
Современные коксовые печи объединяют в батареи по 50—60 камер; две-три батареи образуют блок коксовых печей, обслуживаемый одним комплектом машин и механизмов. Эти машины могут перемещаться вдоль батареи, обслуживая каждую коксовую камеру.
Схема коксовой батареи, на которой показаны основные машины, изображена на рис. 3.11. Машины и механизмы, обслуживающие коксовую батарею, выполняют следующие операции. Углезагрузочный вагон 8, перемещающийся с помощью электродвигателей по рельсам, уложенным над сводом коксовой батареи, имеет три бункера 9 для шихты. По мере необходимости бункера заполняют шихтой (из угольной башни). При загрузке очередной коксовой камеры 2 углезагрузочный вагон располагается над нею. С помощью специальных устройств открываются загрузочные люки 10 камеры, находящиеся под каждым бункером, и шихта пересыпается в коксовую камеру. Углезагрузочный вагон оборудован также механизмами для очистки от отложений графита стояков 6, по которым из камеры 2 отводится прямой коксовый газ. Очистка осуществляется при помощи специального ерша 7, подвешенного на цепи.
Коксовыталкиватель 12 перемещается по рельсам, уложенным с машинной стороны коксовой батареи. Этот агрегат имеет механизм ?? для открывания и закрывания дверей с машинной стороны и передвижную штангу 14, которая вводится в коксовую камеру и выталкивает готовый кокс наружу. Одновременно с выталкиванием кокса удаляются графитовые отложения с поверхности свода камеры сжатым воздухом, подаваемым в сопла, укрепленные на штанге коксовыталкивателя. Кроме того, на коксовыталкивателе имеется планирное устройство 13 — штанга прямоугольного сечения, предназначенная для разравнивания шихты после загрузки ее в коксовую камеру.
На коксовой стороне батареи находится двересъемная машина 4, предназначенная для открывания и закрывания дверей 5 коксовых камер. Эта машина оборудована направляющей, по которой выгружаемый из печи кокс передается в коксотушильный вагон 3. Последний выполнен из жаропрочной стали и служит для транспортирования раскаленного кокса в тушильную башню, где его охлаждают путем орошения водой («мокрое тушение»). Охлажденный кокс опрокидывают на специальную рампу, откуда его направляют на сортировку и подают потребителям.
В комплект механизмов, обслуживающих коксовую батарею, входит также не показанная на рисунке кантовочная лебедка, предназначенная для переключения подачи отопительного газа и воздуха в обогревательные простенки.
Из изложенного следует, что современное коксовое производство характеризуется высоким уровнем механизации и автоматизации.
В табл. 3.14 и 3.15 в качестве примера приведены тепловой и материальный балансы коксования кемеровского каменного угля. Анализ этих данных позволяет установить, что с коксом и летучими продуктами выносится 60—70% тепла, полученного от сжигания топливного газа. Поэтому использование этого тепла представляет важную народнохозяйственную задачу вследствие больших масштабов коксохимической промышленности. В связи с этим одним из путей совершенствования процесса коксования является утилизация тепла кокса («сухое тушение»), газа и паров смолы.
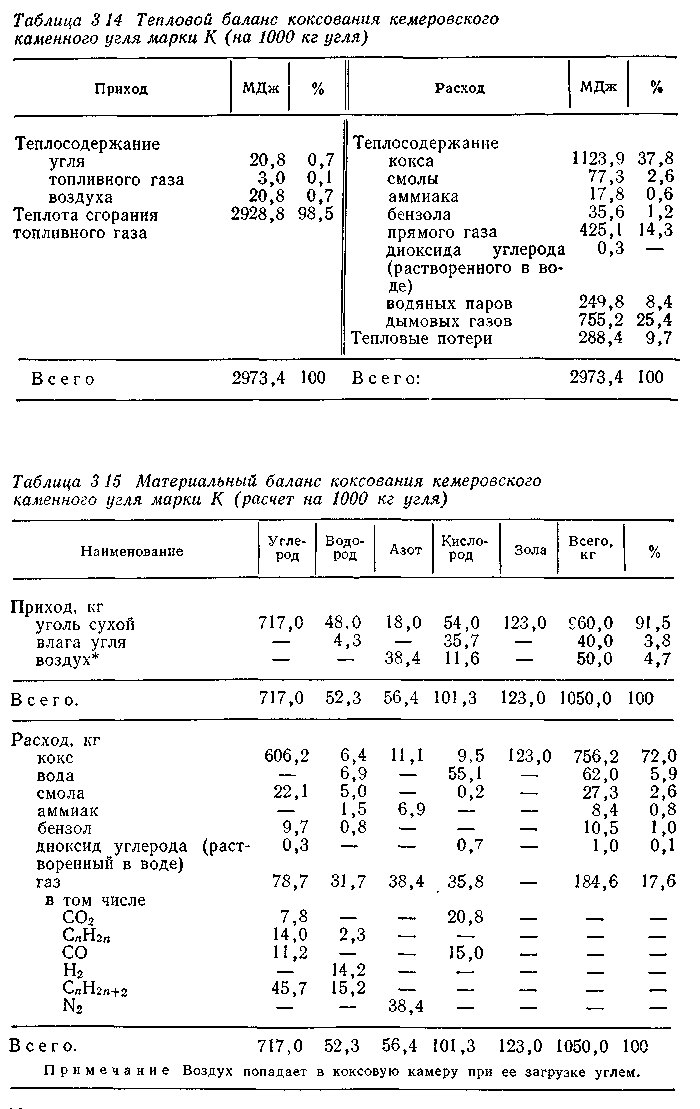
3.2.4. Улавливание химических продуктов
Выводимый из коксовых печей прямой коксовый газ, состав которого приведен в табл. 3.13, содержит большое количество ценных продуктов, подлежащих извлечению и последующей переработке. В частности, в 1 м3 прямого коксового газа присутствуют (в г):
Водяные пары (влага шихты и пирогенетическая вода) |
250—450 |
Пары смолы |
80—150 |
Ароматические углеводороды |
30—40 |
Аммиак |
8—13 |
Нафталин |
До 10 |
Сероводород |
6—40 |
Цианид водорода |
0,5—2,5 |
Пиридиновые основания |
0,4—0,6 |
Кроме перечисленных соединений в газе содержится небольшое количество сероуглерода, органических соединений серы, фенолов и некоторых других веществ.
Количества указанных продуктов сравнительно невелики, однако вследствие очень крупных масштабов коксохимических производств только в нашей стране на основе соединений, извлекаемых из коксового газа, вырабатывается более 200 видов продукции общим объемом около 6 млн. т в год для нужд химической промышленности, цветной металлургии, сельского хозяйства, строительной индустрии, железнодорожного транспорта и других отраслей народного хозяйства. Таким образом, коксохимия является важным источником сырья, и дальнейшее углубление переработки химических продуктов коксования представляет важную народнохозяйственную задачу.
На рис. 3.12 изображена принципиальная схема извлечения продуктов, содержащихся в коксовом газе. Выходящий из коксовых печей газ при 650—750°С подвергают первичному охлаждению, осуществляемому в две ступени.
Вначале он охлаждается до 85—90°С путем впрыскивания воды на входе в газосборник, в котором собирается газ из всех печей коксовой батареи. В газосборнике охлаждение потока происходит за счет частичного испарения подаваемой воды, поэтому применяют воду, подогретую до 70—75°С, так как при использовании холодной воды ее испарение протекает менее интенсивно. В результате охлаждения газа конденсируется примерно половина содержащейся в нем смолы, причем в первую очередь высококипящие фракции. При этом из газа одновременно выделяются фусы — смесь угольной и коксовой пыли со смолой — в виде пастообразной массы.
Неиспарившаяся часть охлаждающей воды, впрыскиваемой в газосборник, абсорбирует из газа некоторое количество аммиака, сероводорода, диоксида углерода, цианида водорода с образованием солей аммония. Жидкую фазу (смола, фусы, вода) отделяют от газа в сепараторе и направляют в отстойник, откуда воду возвращают в газосборник (на первую ступень охлаждения коксового газа). Фусы выводят скребковым транспортером и направляют в углеподготовительный цех, где их используют как добавки к шихте, идущей на коксование. Смолу подают в конечный холодильник для извлечения нафталина.
Газ, имеющий температуру 80—90°С, направляют на вторую ступень первичного охлаждения в трубчатые теплообменники (или холодильники смешения), где его температура понижается до 25—35°С. В этих аппаратах происходит конденсация основного количества паров воды и смолы. В смоле растворяется некоторая часть содержащегося в газе нафталина, а в водном конденсате — аммиак, сероводород, диоксид углерода, цианид водорода, фенолы и некоторые другие соединения. В газе, отводимом из холодильников второй ступени охлаждения, содержится (в г/м3):
Водяные пары |
26—30 |
Аммиак |
7—11 |
Пары смолы |
2—5 |
Нафталин |
2—3 |
Ароматические углеводороды |
32—36 |
Сероводород |
16—26 |
Пиридиновые основания |
0,4—0,6 |
|
|
При сравнении этих данных с содержанием примесей в прямом коксовом газе на выходе из печей видно, что в результате первичного охлаждения наиболее резко уменьшается количество водяных паров и смолы. Остающаяся смола находится в виде тумана. Чтобы избежать ее выделения в последующей аппаратуре, окончательную очистку газа от смолы осуществляют в электрофильтрах (обычно трубчатых), позволяющих обеспечить степень извлечения 98—99% при остаточном содержании смолы в газе 40—50 мг/м3.
Очищенный от смолы газ сжимается нагнетателем до избыточного давления 20—30 кПа, необходимого для транспортирования его через последующую аппаратуру. Следует отметить, что оборудование, находящееся до нагнетателя (по ходу газового потока), работает при небольшом разрежении (4—5 кПа), что обеспечивает полный отсос газа из коксовых печей.
Далее газ подогревают паром до 50—60°С и направляют на извлечение аммиака, осуществляемое путем взаимодействия его с серной кислотой (получаемый при этом сульфат аммония является удобрением). На эту же стадию подают аммиак, отгоняемый из воды, образующейся при первичном охлаждении коксового газа. Серная кислота одновременно связывает содержащиеся в газе пиридиновые основания в сульфат пиридина, из которого затем в отдельной установке выделяют пиридиновые основания.
Следующим этапом обработки коксового газа является его конечное охлаждение до 25-30°С с одновременным извлечением нафталина. Для этой цели используют холодильники смешения (насадочные скрубберы) с водяным орошением. При охлаждении газа происходят конденсация содержащихся в нем водяных паров и вымывание кристаллов нафталина, которые накапливаются в нижней части холодильника. Сюда же подают смолу, отделяемую на стадии первичного охлаждения газа; смола растворяет нафталин. После отстаивания смолу направляют на переработку, а газ — на извлечение бензольных углеводородов. Этот процесс осуществляют абсорбционно-десорбционным методом; в качестве поглотителя используют каменноугольное или соляровое масло.
Далее газ очищают от цианида водорода, обрабатывая его раствором полисульфида натрия (или аммония), в результате образуются соответствующие тиоцианиды. Последним этапом является извлечение сернистых соединений с получением свободной серы или серной кислоты.
Очищенный газ (который называют «обратным коксовым газом», так как 40—45% его возвращают для обогрева коксовых печей) содержит [% (об.)]:
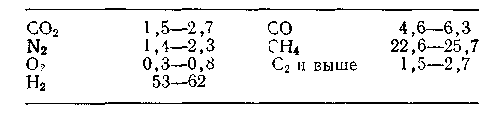
Отдельные стадии рассмотренной схемы более подробно описаны в гл. 4.
3.2.5. Перспективы развития процесса
Дальнейшее развитие и интенсификация процесса коксования осуществляется несколькими путями. Один из них — увеличение высоты коксовых камер до 7—8 м и длины до 17 м. Это позволяет повысить производительность коксовой батареи из 65 печей с 700 до 1000 тыс т валового кокса в год. Наряду с этим переход на изготовление печей из динаса, имеющего более высокую теплопроводность, чем шамот, дает возможность примерно на 15% увеличить производительность печей без изменения температуры в отопительных каналах.
Перспективным методом повышения качества кокса и улучшения технико-экономических показателей его производства является сухое тушение. Этот способ основан на охлаждении раскаленного кокса не водой, а циркулирующим инертным газом с последующим использованием аккумулированного им тепла в котле утилизаторе для получения водяного пара. Уже эксплуатируются промышленные установки производительностью до 50 т кокса в час, вырабатывающие пар под давлением ~3,9 МПа и при температуре ~450°С. Конечная температура охлажденного кокса ~250°С, количество вырабатываемого пара 0,4—0,5 т на 1 т кокса. При первоначальном запуске установки в качестве газа-теплоносителя используют воздух, который, взаимодействуя с раскаленным коксом, превращается в смесь диоксида углерода и азота. По мере циркуляции газа СО2, реагируя с коксом, восстанавливается в СО. Кроме того, в газовую фазу выделяется некоторое количество летучих продуктов из кокса. Поэтому в стационарном режиме средний состав циркулирующего в системе газа-теплоносителя следующий: 5% (об.) СО2, 18% (об.) СО, 10% (об.) Н2, 67% (об.) N2.
Преимущества метода сухого тушения кокса заключаются в том, что улучшается качество металлургического кокса, который не разрушается от резкого охлаждения; уменьшается расход технической воды и сокращается уровень загрязнений воздушного и водяного бассейнов; улучшаются технико-экономические показатели коксования за счет утилизации тепла кокса и получения водяного пара высоких параметров.
Одним из перспективных способов повышения эффективности коксования является производство формованного кокса, Этот вариант имеет ряд технологических преимуществ по сравнению с традиционной технологией. При его применении меньше загрязняется окружающая среда и, самое главное, расширяется ассортимент перерабатываемых углей (в сторону низкокачественных) без ухудшения качества получаемого металлургического кокса. Метод основан на том, что в диапазоне 400—450°С угли определенных типов способны размягчаться и переходить в пластическое состояние. Поэтому, используя подобный уголь как связующее, шихту, содержащую до 80% низкокачественных углей, нагревают до указанной температуры и в горячем состоянии подвергают прессованию в прочные брикеты. Их затем нагревают со скоростью 1,5—2°С/мин до 850°С. При этой температуре завершается образование прочной коксовой структуры. Применение полученного таким образом формованного кокса при выплавке чугуна позволяет на 2—5% повысить производительность доменной печи и сократить удельный расход кокса. Следовательно, формованный кокс не только является полноценной заменой обычного слоевого кокса, но и создает благоприятные условия для форсированного ведения доменного процесса.
Наряду с этим в Украинском углехимическом институте (г. Харьков) разработан способ получения формованного кокса с использованием в качестве связующего пеков и нефтяных остатков.
Помимо перечисленных методов ведутся разработки процесса коксования в печах непрерывного действия. Однако результаты этих исследований пока еще не получили широкого промышленного применения.