The articles formed layer increased imperfection is the glass based materials mechanical treatment characteristics. The imperfection degree, which depends on the cutting forces level, can be a treatment technology processes design efficiency criterion Grin ling process force characteristics can be defined by the treatment scheme and conditions.
Как известно, для хрупких неметаллических материалов глубина и структура нарушенного обработкой слоя определяется уровнем силового воздействия на формируемую поверхность. Поэтому при обработке крупногабаритных тонкостенных изделий сложной пространственной формы из ситаллов рациональной может быть признана схема шлифования, позволяющая, из-за особенностей контактирования инструмента и изделия, снизить напряженность в микрообъемах материала под обработанной поверхностью. Для исследования напряженно-деформированного состояния (НДС) зоны резания был использован разработанный ранее принцип компьютерного моделирования [1], базирующийся на вероятностных положениях теории разрушения и реализуемый с использованием методов конечных и граничных элементов.
Названный принцип моделирования был апробирован в опытно-промышленныx условиях для разработки рациональной схемы внутреннего шлифования тонкостенных крупногабаритных изделий сложной пространственной формы из ситаллов (см. рис. 1). Основные размеры изделия: длина до 1,0 м; максимальный диаметр 450-500 мм; толщина стенки заготовки 20 мм при толщине готового изделия 5 мм. Технологический процесс обработки включает многооперационную обработку шлифованием как наружного, так и внутреннего контуров изделий. Наибольшие трудности связаны с операциями внутреннего шлифования, на которых снимается основной припуск.
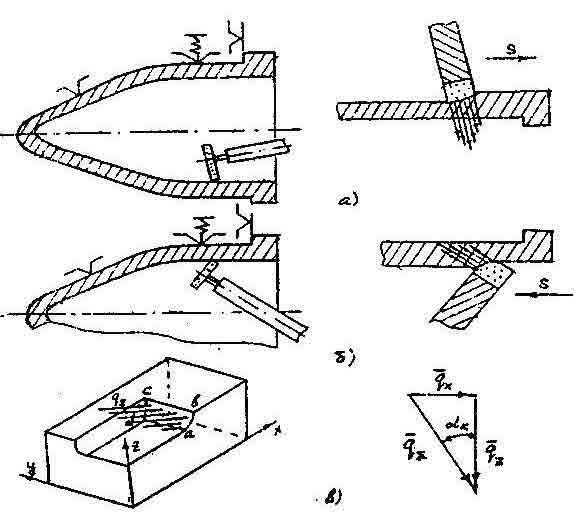
Рисунок 1 – Схемы обработки внутренней поверхности изделия при шлифовании с подачей: а - «к фланцу» изделия, традиционная схема; б - «к носку» изделия, предлагаемая схема; в - моделирование схемы взаимодействия изделия и инструмента
Выбору схемы предшествовал этап теоретического анализа напряженного состояния обрабатываемого материала при различных вариантах приложения нагрузки. Моделью зоны резания служил трехмерный образец, мысленно вырезанный из заготовки в месте ее контакта с инструментом (см. рис. 1, в). Ширина образца соответствовала толщине обрабатываемой заготовки, длина и высота выбраны таким образом, чтобы, учитывая соотношение кривизны изделия и образца, с целью упрощения решения задачи иметь возможность с достаточной степенью точности заменить криволинейные наружные поверхности прямоугольными. Для обеспечения адекватности модели реальная деформационная обстановка в образце, как в части изделия, учтена путем наложения связей на его соответствующие грани. Затем с помощью разработанных методик, определялся уровень НДС зоны резания при вариации величины и направления нагрузки, имитирующей усилия шлифования. К уступу «a-b-c-d», в модели - к зоне контакта инструмента и заготовки, под разными углами
ak
к вертикали, определяющими соотношение между нормальной и тангенциальной составляющими усилий резания, прикладывалась суммарная распределенная нагрузка
qсум, равная
qсум=
qx+
qz, где векторы qx и qz - соответственно учитывают действие тангенциальной и нормальной составляющих усилий резания.
Расчеты показали следующее. Наиболее деформированной для всех исследованных вариантов нагружения является зона дальней границы уступа на образце; изменение направления действия усилий резания определяет перераспределение уровня НДС в объеме образца и его качественные характеристики - локализацию областей деформирования, обусловленных преимущественно растягивающими или сжимающими напряжениями. Предположительно лучшим с точки зрения формирования дефектного слоя является вариант ориентации нагрузки по нормали к плоскости уступа
(ak=900), когда уровень сжимающих напряжений, направленных в обрабатываемую поверхность минимален. При этом основной градиент напряжений сосредоточен в объеме удаляемого припуска. Об этом же свидетельствуют наибольшие значения риска разрушения материала отдельных зон контакта инструмента и детали, также расположенные в области диспергирования припуска.
Учитывая полученные теоретические результаты, была разработана и внедрена схема шлифования, представленная на рис. 1, б, для которой, в отличие от применявшейся на производстве схемы (см. рис. 1, а), характерно перемещение инструмента по дальней от рабочего стороне детали с подачей его к носку изделия. В этом случае равнодействующая сил шлифования стремится прижать заготовку к установочным элементам приспособления при значительном уменьшении радиальной составляющей силы резания, вызванном сокращением площади контакта круга и детали. Равнодействующая сила в значительной степени направлена в удаляемый припуск, тогда как при реализации традиционной схемы шлифования (подача инструмента «к фланцу») доминирует радиальная составляющая сил резания, обеспечивающая направление результирующей силы резания непосредственно в обрабатываемый материал, что должно отрицательно сказаться на уровне его дефектности.
Были проведены исследования, позволившие установить влияние схемы шлифования и уровня НДС материала изделия на дефектность обработанной; поверхности изделий и их прочность. Для этого на образцах, вырезанных из деталей, обработанных по каждой из рассматриваемых схем, определялись глубина и структура дефектного поверхностного слоя с использованием метода люминесцентной капиллярной дефектоскопии [2] и прочность на изгиб при разрушении образцов по трехточечной схеме нагружения. Результаты испытаний показали, что применение предлагаемой схемы шлифования позволяет существенно снизить дефектность обработанной поверхности. Так до трех раз уменьшаются размеры дефектов в приповерхностном слое глубиной до 80 мкм, кроме этого сужается область развития трещиноватого слоя. Максимальная глубина проникновения крупных трещин (длиной до 300 мкм) составляет 140 мкм против 180 мкм при прежней схеме шлифования.
Следствием благоприятной структуры образующегося нарушенного обработкой слоя при предлагаемой схеме явилось повышение прочности изделий во всем исследованном диапазоне режимов обработки на 25-35 % (см. таблица).
Таблица - Результаты прочностных испытаний деталей
№
п/п |
Параметры режима обработки
|
Направление подачи
|
Параметры прочностных испытаний образцов
|
nд, об/мин
|
s, мм/об
|
t, мм
|
Прочность на изгиб
σи,МПа
|
Среднеквадротичное отклонениеS,МПа
|
Число испытуемых образцов n
|
1
2
3
4
|
80
80
80
80
|
0,11
0,11
0,34
0,34
|
1,0
1,0
1,0
1,0
|
"к носку"
"к фланцу"
"к носку"
"к фланцу"
|
131,5
89,3
69,9
50,8
|
22,4
11,6
15,7
12,4
|
23
21
22
20
|
Как следует из представленных данных, использование метода компьютерного моделирования НДС, возникающего при резании стекломатериалов, позволяет с минимальными затратами проектировать рациональные технологические процессы их обработки, в частности, обосновывать выбор схемы шлифования.
Список литературы: 1. Дашевский Е.М„ Калафатова Л.П. Компьютерное моделирование процесса разрушения образца из ситалла при алмазном шлифовании // Резание и инструмент в технологических системах. - Харьков: ХГПУ. - 1997. Вып. 51. С. 83-85. 2. Калафатова Л.П. Диагностика дефектности обработанной поверхности технических ситаллов // Прогрессивные технологии и системы машиностроения: Сб. науч. тр./ Донецк, гос. техн. ун-т. - Донецк, 1997. Вып. 4. С.66-74.