ELECTRONIC LIBRARY
Karakuts Irene Sergeevna
LUDMILA KALAFATOVA
The influence of grinding conditions of engineering cetalls-made products on the formed surface defects presence are examined in the paper. The level of the defects presence is stated to depends on the cutting forces and is defined by such technological process input parameters as grinding mode, diamond tool state and characteristics, the performed operations order and technological environment features.
The manufacturing technology of large complicated shape products made of pyroceramics can be referred to complex hierarchy system with good reason, which can be presented as an aggregate of well designed interrelated objects [1]. The technology transformations N, when the products made of the above mentioned material are manufactured, is presented in Fig. 1.
The operators of technology transformations system are as follows: H - human factor (depending on the system details studying degree; the products designers, technologists, machine operators etc. can be referred to this group), TS - technology systems under which the technology processes are implemented, M - medium which influences state of all the system objects which are under consideration. The TS system include the following technology effect stages: N1 - before mechanical treatment (the billet is obtained), N2 - when mechanical treatment is taking place, N3 - after mechanical treatment. When all technology transformations are implemented, the system operators are influenced by the external flows of material Mvi , energy Evi, and information Ivi. Thus the technology transformations system can be presented as
N=N1U N2U N3=M(m1,m2,...,ms) U E(e1,e 2,…,et) U I(i1, i2,…,iv). (1)
Obtaining of a high-quality products with minimum expenses covering its manufacturing is the main task to be solved at each technology stage. To solve the technology transformations optimization task, the complex control system at each technology cycle stages, based on application of some criterion of optimization Ô, is needed when the products are manufactured. The technological cost CTñóì of the products can serve as the criterion.
The mechanical treatment stages are the most time consuming, and have maximum effect on the CTñóì level. The physical and mechanical features of treated material make the accurate billets obtaining practically impossible. The common allowance which has to be removed at the mechanical treatment stage is 10-12 mm for a side. Besides, the examined materials based products are highly requested to be accurate in form and of high quality. That is why a number of operations, such as rough and finish grinding, polishing or diamond lapping, are supposed to be done at the second effect stage of technology N2.
But as a result of force effect made on the machined surface during grinding the defects in the state of microcracks penetrate to a certain depth what have negative influence on the surface quality. The force effect depend upon the operations input parameters. All the defected layer with the depth of hd has to be removed at the third, final stage of technology with the help of expensive and ecologically harmful operations of etching and ion strengthening of the products. The work input level is determined by the defected surface layer depth and structure.
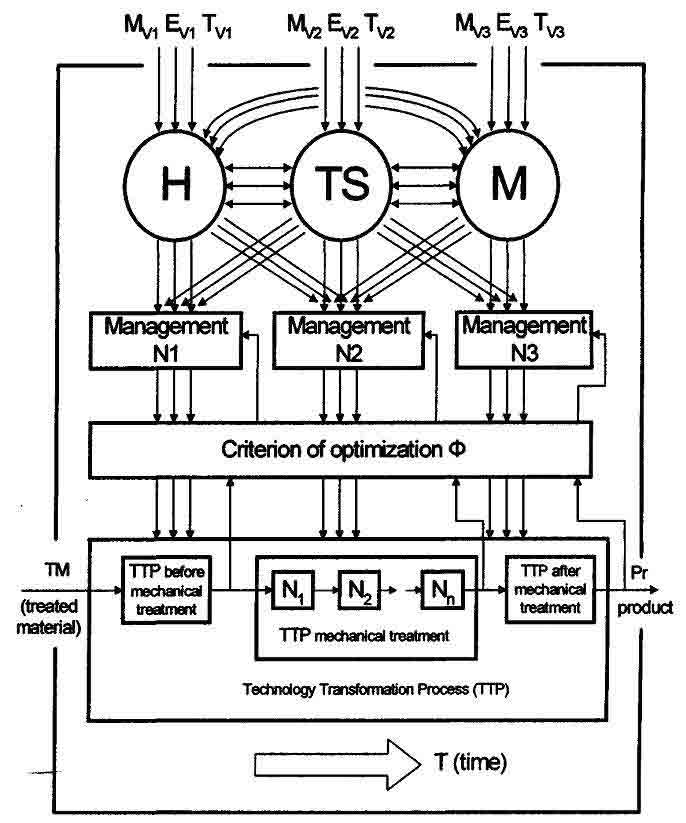
Fig. 1. System of technology transformations when the cetalls based products are manufactured
The technological cost CTñóì of getting of completed part is composed of cost of the blank CTI, machining CTII and the product hardening CTIII.
CTñóì = CTI+CTII+ CTIII. (2)
If CTI is constant for all versions of the product manufacturing, changing of the CTII level is of great interest. Therefore CTñóì could be considerably reduced at the expense of the machining time which is defined by value of the minimal removed material Zmin during a certain operation and by the machining modes. The value of Zmin depends on the depth of the defected layer forming under the previous operation which is influenced by the technological factors defining the energy expenses to implement machining process.
The solving of task of glass based materials technology treatment optimization is stated to be connected with minimum by depth and favorable structure of treated surface defects.
If more the force influence machined surface, more defects has the product surface [4]. This is demonstrated by such parametres of the defected machined surface as the defects size, form, concentration, and depth of penetration. In its term the defects presence determines the products operation characteristics and the treatment work input and cost.
The database on changes of defects presence level of glass based materials under the system objects inner parameters variations occurred at technology stages was formed as a result of the presented investigations.
Influence of physical and mechanical properties of treated material, cutting conditions, the applied tool characteristics abrasive tool wear level and properties of the technological medium on the depth and defects presence of the products surface layers was studied. The obtained information based on the data on implemented technology transformations were used for design of optimal technology process which is distinctive by its low costs and required products quality.
The influence of grinding conditions on the cutting process energy parameters and the products surface layer defects were investigated and modeled in laboratories and at the plants. To investigate the depth and structure of the material layer broken by treatment testing fluorescent dye penetrant in combination with the samples layer by layer etching was applied [5].
The cutting force components under the grinding process are known to depend on grinding condition parameters. To achieve the grinding high productivity it is rational to intensify the cutting mode parameters, the depth t and feed s in particular. However, it was stated that the grinding force components - radial Fr and tangential F, - are increased. Under the work with dressed 1À1-200õ6õ3õ76 AC20-250/200-4-Ì1 wheel when flat infeed grinding of the AC-418 cetall is implemented, the dependence of the components of the grinding force on the cutting modes are as follows
Ft =Ct*v-0.87 *s0.68 *t1.37; Fr =Cr*v-0.55 *s0.62 *t0.92. (3)
Where Ft, Fr - are correspondingly the tangential and radial components of the grinding force [N] under the work made by the dressed wheel; v - speed of grinding [m/s]; t - depth of grinding [mm]; s - line feed [m/min]; Ct, Cr - coefficients defined by physical and mechanical characteristics of the work material and the diamond grains. For the conditions under discussion Ct = 54, Cr = 75.
The radial component Fr of the grinding force, which is directed to the machined surface itself, generally, defines structure and depth of the defected layer. Regardless of the machining scheme increase of feed and cutting depth is influenced negatively the defects presence in the forming surface. Thus, when the feed is changed from s = 0.109 mm/rev to s = 0.256 mm/rev (for internal grinding) at the level of etching h = 150*10-6 m the size of the defects made by machining is 3.5 times as much and reaches 300*10-6m and even more. The treatment productivity raises at the expense of the grinding conditions intensification.
When the glass material is grinded the level of forces which appear in the zone of contact between the tool and workpiece is increased when the wheel wears. It is connected with the change of the areas of contact of grains with the treated surface and redistribution of nominal pressure at these areas. The wheels wear depends on the grinding conditions, the tool technology characteristics, and the chosen dressing method. For all treatment methods under discussion there is a tendency of defects decrease when not glazed wheel is used. It is seen most vividly when the wheels with finer graininess and the diamonds with smaller density are used. It is illustrated in the Fig. 2 for the internal grinding of the AC – 418 cetall. The nomenclature is as follows: W - specific volume of the co-grinding material [mm3], equal to the ratio of the volume of co-grinding material to the square of wheel working surface.
Decrease of the defects presence is observed practically at all etching levels and, what is especially important, when hd > 300*10-6 m. Thus, the application of wheels with fine graininess (100/80 against 250/200) under the glass ceramic treatment was stated to provide the decrease of introduced defects size, practically independent on the tool wear degree on all levels of defects occurrence (up to 600*10-6m). At the depth of 300*10-6m this decrease is 8 times as much. The application of fine grain wheels will decrease two times the surface layer volume removed under the article forming. The data which demonstrate that application of abrasive tool with stronger structure (AC20 if compared to AC6) leads to significant increase of the surface defects volume. At the etching depth equal to 420-500*10-6m the size of defects increases 12 times as much. The application of progressive wheels dressing methods allows to increase the tool durability to a considerable extent and to decrease the defects level up to 3 times just after the dressing and up to 5-7 times by the end of the tool durability period.
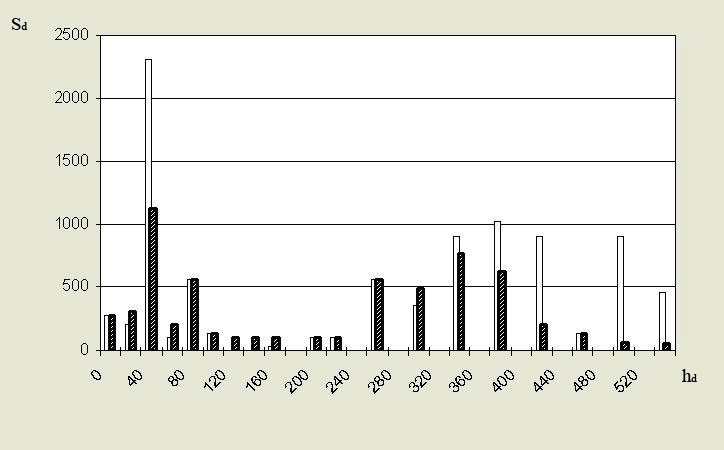
Fig. 2. Diagram of dependence of the square of the unit maximal microdefect Sd on the
depth of etching hd
The mentioned data allow to drive to the conclusion that the tool with stronger structure and harder grains should be preferably applied at the stage of rough grinding when decreasing of machining time is a very important factor that must be provided at the expense of the operations. Under the operations of finish grinding fine grain diamond wheels in combination with the tool periodic dressing should be applied because of great importance on depth and structure of the forming defects layer.
The investigations were carried out suggest the necessity to divide grinding operation of large products made of cetalls into several stages (not less than three) in accordance with the number of cuts when the billet allowance is removed. The stages can be differentiated by the applied tool graininess and brand. At the basic version all allowance was removed within two cuts and the treatment was held by one and the same tool under the same cutting conditions. The example is given below illustrates the results were obtained. Let's suggest the necessity in removal of the allowance equal to 3.5 mm. In accordance with the first version (the basic one) grinding is held within two cuts with the wheel of characteristic A 315/250 and with cutting depths of h = 2 mm, t2 = 1.5 mm, and feeds of s1 = s2 = 0.256 mm/rev. In accordance with the second version (supposed) the grinding is held within 3 cuts with the A 315/250 wheel at the first two cuts and the conditions of t1 = 2 mm, t2 = 1 mm, s1 = s2 = 0.256 mm/rev and the wheel AC6-100/80 at the finishing cut with the t3 = 0.5 mm, s3 = 0.083 mm/rev regime.
The technology medium (TM) with purposeful properties is one of the effective methods of influence on the cutting processes under the glass based material treatment. In this case the TM make considerable dispersion influence besides such traditional functions as cooling, lubrication and washing. This allows to make the cutting processes more intensive and, therefore, to raise the treatment productivity and the tool serviceability at the expense of the material surface layers strength loss because of the media influence. The energy expenses decrease falling at the volume unit of the removed allowance tells favorably on the depth and structure of the layer broken by the treatment.
The TM used to treat the glass material is related to the physical and chemical structure of treated material. That means that it is polar, surface-active, easily penetrate into the cutting zone, has lubrication properties, and facilitate both the tool and the grinding process. The efficient composition of the TM was found, on the formed requirements, to be water based surface-active substances [3]. The operations of rough and semifair grinding of glass and glass ceramic material is the area of the TM rational application. The developed medium provides fine defective structure of deeper layers at the expense of increased disperse ability. It also allows to reduce considerably the treatment time at the succeeding technology transitions. The recommended medium application allows to 1.4-3.5 times reduction of isolated defects size, reduction of the defective layer depth being 30% as average. It makes possible to achieve the 30-50% increase of feed under the grinding process without bringing any harm to the treatment quality and the articles strength.
The obtained results allowed to develop and implement the technology processes of mechanical treatment of products made of glass and glass ceramics which are notable by their rational grinding operations, applied TM components and tools with pre-arranged characteristics. The enumerated actions made possible to achieve the 20-30% raise of treatment productivity when the requirements as to the formed surface quality are met.
CONCLUSIONS
Taking into account the technological heredity of the working affect of the tool on the cetall-made products formed surface and having information on the depth and structure of the layer broken by machining which is formed during every operation of the technological process that differ by characteristics of the applied tool, machining modes, type of the applied technological medium etc. the design of rational technological processes becomes possible. Valid inter-operational machining tolerances are their main characteristics. They allow to reduce the products manufacturing time and cost.
REFERENCES
[[1] Kalafatova L., Diagnostics of qualitative performances of products from engineering cetalls. Archives of Mechanical Technology and Automation, 1997, vol. 17, nr 2, s. 107-116.
[2] Kalafatova L., Tekhnologicheskie sredy kak faktor povyshenija gicheskikh sistemakh, NTU "KHPI", 2003, Vyp. 64, p. 119-126.
[3] Kalafatova L., Vozmognosti upravlenija defektnostju shlifovannojj poverkhnosti materialov na osnove stekla za schet izmenenija parametrov tekhnologicheskogo processa obrobotki, Progressivnye tekhnologii i sistemy mashinostroenija, DonGTU, 1999, Vyp. 8, p. 100-108.
[4] Khubka V., Teorija tekhnicheskih sistem, Moskva, Mir 1987.
[5] Mikhajlov A., Kalafatova L., Osobennosti formirovanija defektnogo sloja pri abrazivnoj obrabotke konstrukcionnykh izdelijj iz materialov na osnove stekla, Progressivnye tekhnologii i sistemy mashinostroenija, DonGTU, 2001, Vyp. 17, p. 90-93.