BIOGRAPHY
LIBRARY
LINKS
REPORT ABOUT THE SEARCH
IRAQ IS MY MOTHERLAND
|
ABSTRACT
CONTEMPORARY STATE OF A QUESTION, PURPOSE AND THE TASKS OF THE STUDY
The need for the assembly-line processes appeared in extreme antiquity, when man began to create the first implements of labor, capable of facilitating, the confronting it tasks in the viability, and also to partially or completely replace for the function of man. In the process of evolution assembly-line processes continuously were complicated and were improved, which was basis at the creation of the automatic machines of assembling. The first automatic machines of assembling articles appeared in the past century.
At present the automation of assembly-line processes reached higher level; however, the analysis of contemporary state shows delay in the development of assembly-line processes from the stockpiling and machining operations. The requirements of an increase in the productivity of the production of articles assume the automation of all entering in them elements, including the operation of assembling. The level of the operations of the automation of assembling does not exceed 6%. Taking into account the high specific
weight of the operations of assembling in the total volume of production (25-40% in general machine building), an increase in the level of their automation remains urgent at present.
The work of the scientists are dedicated to a question of the automation of assembly-line processes: [M].[S]. Of [lebedevskogo], [A].[I]. of Fedotov, [T].[E]. treasure, [K].[YA]. Of [mutseneka], [L].[I]. Of [belovskogo], [A].[A]. of Gusev, [V].[V]. Of [kosilova], [N].[V]. of Zakharov, [I].[A]. Of [klusova], [N].[P]. of Novikov, [P].[I]. of Alekseyev, [L].[N]. Of [koshkina], [A].[N]. of Rabinovich, [N].[I]. Of [shereshevskogo], [V].[A]. Of [yakhimovicha]; the foreign scientists: [U].[B]. Of [kheginbotama], J.
Of [khollingama], J. Of [mortimera] Of [b]. [Raks], [M]. Guinness, [I].[K]. Of [boyadzhieva]… On the base of studies of the authors indicated are obtained automatic assembly-line systems. However, contemporary requirements for the productivity of assembly-line processes and increased requirements for the assemblies of machines require passage to qualitatively the higher level of the automatic technological assembly-line systems of continuous action. To this question is dedicated this work.
1.1. Analysis of the structure of the technological processes of the automatic assembling
The technological process of the automatic assembling of article consists of the following passages:
1) the load of mating parts into bunker or other loaders and their supply into the gripping, intercepting, and card-take devices in the preliminarily or finally oriented position;
2) Seizure, cutting and the supply of mating parts into the orienting and basing devices assembly jigs;
3) Orientation with the required accuracy of the relative attitude of the surfaces of mating parts on the basing assembly-line devices;
4) Connection and the fixation of conjugate parts with the required accuracy;
5) the checking of the required accuracy of relative attitude of conjugate parts or assembly unit;
6) load and the transport of finished assembly unit.
With the fulfillment of the automatic assembling of articles the most important elements of assembly-line production are the orientation of the gathered components in the space and their supply to the positions of assembling, achieved with the aid of the loaders. Under the conditions for automatic assembling the loaders are carried out in the form the independent units, organically-bound with the assembly equipment. In the flexible production systems of assembling the use of the bunker- orienting cassette and
magazine loaders in proportion to decrease is most effective. The orientation of components with the required accuracy of the relative attitude of the surfaces of mating parts on the basing assembly-line devices is one of the most important stages of automatic assembling. In this case the components must be arranged so that it would be easy to carry out their joining with the established tolerances in size and relative turnings of the mating surfaces. This stage appears by the most critical and on it depends
the fitness for work of assembly equipment and the quality of assembling. The structure and the content of the components of the stage of the orientation of the gathered components in the space and their supply to the position of assembling is determined by the type of the loader used. The content of the components of the stages of the orientation of components with the use of the bunker- orienting devices they compose the displacement of the gathered components from the specially diverted area of the work site
of assembling to the loader; the filling in bulk of components into the bunker ([predbunker]); the inspection of the minimum and maximum filling of bunker ([predbunker]) with components; capturing and the by the piece department of components made of the overall mass (with the aid of the mechanism of seizure); the primary orientation of components in the space (transfer from the chaotic state into any that determined and steady); the second orientation of components in the space (transfer into the specific assigned
position); the control of the correctness of the orientation of components; reorientation or the discharge of the incorrectly oriented components; the receiving inspection of components; the supply of components into the receiving chutes, the control of the minimum and maximum levels of the filling of store (accumulator) with components; separation of one (or group) component from the general flow of components, which are located in the store (accumulator); supply to the position of seizure; seizure and the displacement
of one (or group) component to the position of assembling; the checking of presence and correctness of position in the seizure.
And their supplies to the position of assembling with the use of cassette loaders enter in the content of the components of the stage of the orientation of the gathered components in the space: the displacement of the gathered components from the specially diverted area of the work site of assembling to the loader; the filling in of components in bulk into the bunker; the inspection of minimum and maximum fillings of bunker by components; the preliminary orientation of components in the space;
the filling with the components of the nests of cassette; the checking of the presence of components in the nests and the correctness of their position; reorientation or the removal of the incorrectly oriented components in the nests; the control of the assigned level of the load of the nests of cassette; fixation and the retention of components in the nests of cassette; the removal of the remained excess components; additional load by the components of the free nests of cassette; the removal of the loaded cassette
from the installation of cassetting; the displacement of the filled cassette to the position of seizure; seizure of the cassette and displacement of one (or group) component to the position of assembling; the checking of presence and correctness of the position of one component (or group) in the seizure.
The nests of cassette are filled with the components (they [kassetiruyut]) with the aid of the vibration, pneumatic, magnetic and [lentomagnitnykh] systems of cassetting and cassetting with the application of electric field and others in the cassette loaders for the accumulation of the gathered components oriented in the space it serves the cassette, from which the components are seized and fall on the position of assembling. Depending on construction, sizes, mass and material of components the load of cassettes
can be achieved by hand or with the aid of the mechanized or automatic devices. In the magazine loaders for the accumulation of the gathered components oriented in the space is intended the store (to the accumulator), from which the components will be given to the position of seizure. Depending on construction, sizes, mass and material of components the load of stores can be achieved by hand or with the aid of the mechanized or automated devices The content of the components of the stage of the orientation of
the gathered components in the space and their supplies to the position of assembling with the use of magazine loaders appear: the displacement of the gathered components from the specially diverted area of the work site of assembling to the loader; capturing and the by the piece department of components made of the overall mass; the preliminary orientation of components in the space; piling components to the orienting surfaces of store; the final orientation of components in the space; the control of the correctness
of the orientation of components; reorientation or the removal of the incorrectly oriented components; the control of the minimum and maximum levels of filling of store by components; separation of one or (group) component from the general flow of components, which are located in the store (accumulator); the supply of component to the position of assembling; the checking of presence and correctness of one (or group) component in the seizure. Load with the aid of the adaptive devices makes it possible to ensure
seizure by the robot of the gathered components from the loading; the orientation of components in the space and their supply to the position of assembling in the automatic cycle.
The content of the components of the stage of the orientation of the gathered components in the space and their supplies to the position of assembling with the aid of the adaptive loaders comprise: the displacement of the gathered components from the specially diverted area of work site to the loader; the filling in bulk of components in the place of their seizure; the supply of the seizure of adaptive device to the components; determination with the aid of the sensors (visual, tactile and other) of attitude
of one of the components; the corresponding orientation of the seizure of the relatively this component; capturing and the department of one component of the overall mass; the preliminary orientation of component in the space due to the appropriate displacements of seizure; the final orientation of component in the space due to the appropriate displacements of kinematic it is sectional device and seizure; the supply of component to the position of assembling; the checking of presence and correctness of the position
of component in the seizure. The basing of the gathered objects depends on the technology of automatic assembling, constructing of assembly-line article and requirements of those presented to it, and also from the accuracy of equipment. Basing of the gathered components during the automatic assembling - this the continuously changing process, beginning from the loaders and concluding by the direct joining of assembly-line components. The task of basing is the presence and the application of the simplest and reliable
diagrams of the basing of the gathered components, with which is ensured the fulfillment of conditions of the collectability of components.
Depending on the construction of the assembly equipment the basing of components on the position of assembling can be produced with the vertical, horizontal and inclined position of the axis of the gathered components. The selection of the method of basing depends on the construction of the gathered components and of the assembly equipment of the necessary effort of closing component after basing, nature and accuracy of joining. During the assembling base component in the majority of the cases remains fixed relative
to the mobile joined components.
The collected components can be based both over the mating surfaces and on the auxiliary. In this case the greatest application with the basing find the cylindrical, flat, threaded, conical and combined surfaces. Spherical, core and knife surfaces more rarely are used. The design forms of the basing surfaces of the gathered components have a direct effect on the selection of the schematic of the basing devices. As the adjusting elements of the basing devices are used the plates,
prisms, supports, centers, cylindrical or conical fingers and mounts, squares other base component usually is pressed in the basing device with the aid of the clamp elements for purposes of the guarantee of its necessary resistance to the appearing in the process of assembling forces and the moments, which are attempted to displace it. In a number of cases base component can freely be established in the basing device,
which makes it possible to simplify the construction of the basing device due to the exception of clamp elements and drive to them. The calculation of the clamping pressures of base component should be conducted taking into account the greatest values of moments. The basing devices for the joined components must ensure the possibility of its displacement in the direction of base component. The content of the components of the stage of the basing of the gathered components on the position of assembling is the
following: the installation of base component in the basing device (adaptation), centering of base component in the adaptation; the fixation of base component in the adaptation; the inspection of the accuracy of the installation of base component in the adaptation; the installation of the joined component in the basing device (adaptation), centering of the joined component in the adaptation; the fixation of the gathered component in the adaptation, the inspection of the accuracy of the installation of the joined
component in the adaptation.
To the selection of constructing the basing devices render influence geometric form, sizes, the mass, the physicomechanical properties of the material of the gathered components, the methods of their supply into the zone of assembling, the required accuracy of basing, the type of the equipment used, the type of the assembly equipment used and the conveying appliance. The programmed universal readjusted basing devices are most effective in the flexible production systems of assembling. The technological similarity
of the gathered components in the flexible production systems of assembling in the stage the basing and fulfilling of the process of assembling are determined by the generality of the methods of basing, installation and fixation of components, and also programming and readjustment of the basing devices used. The accuracy of the relative orientation of the gathered components, established into the basing devices, frequently can be insufficient for fulfilling the process of automatic assembling. In this case, when
the stiffening of admittances for the production of equipment and gathered components economically does not justify, the devices of relative orientation adapt, with the aid of which it is possible to ensure the necessary accuracy of the relative orientation of component on the assembly-line position and their automatic assembling.
For purposes of an increase in the relative orientation of the gathered components it is necessary to use principle of the combination of bases. The programmed universal readjusted and specialized readjusted orienting devices with the guides are most effective in the flexible production systems of assembling. The technological similarity of the gathered components in the flexible production systems of assembling in the stage of their relative orientation with the necessary accuracy on the position of assembling
is determined by the generality of the methods of relative orientation, installation and fixation of components, and also programming and readjustment of the orienting devices used. With following stage in the structure
the technological process of automatic assembling appears the stage of joining and fastening of the gathered components with each other. To the requirements of technological effectiveness of design of the gathered components in connection with to the conditions of their automatic joining and fastening can be attributed the technological effectiveness of connections; the free access of erecting tool to junction; the presence of the structural elements, which ensure the assigned accuracy of the alignment of components
in the article; the presence of guides, that facilitate assembling, substantiated roughness of the mating surfaces of components, sufficient strength of materials and of protective coatings of components, that prevents their damages; the substantiated accuracy of the dimensions of components and object of assembling.
The selection of constructing the actuating assembly-line mechanisms (devices) influence geometric form and sizes (diameter, length, width, area) of the mating surfaces, case of fit in the joining, the forms of the motion of operating unit and so forth most effective in the flexible production systems of assembling are the programmed readjusted assembly-line devices of modular construction and assembly-line robots. The technological similarity of the gathered components in the flexible production systems of assembling
in the stage of their joining and fastening with each other with the assigned parameters is determined by the region of the methods of programming and adjustment of assembly-line devices and their operating units.
The checking of the presence of the gathered components on the assembly-line basing devices and the checking of the required accuracy of relative attitude of conjugate parts or assembly unit are the necessary elements of the assembly-line devices, on which depends the quality of assembling and the fitness for work of assembly-line devices. In more detail the structure of the technological process of automatic assembling it is possible to examine based on the example of the existing technological processes of
automatic collection.
As the example to automation line with the continuous transport of object let us examine the production of battery “change”.
The element of battery contains six components and other components. Element is manufactured on two rotary- chain lines. On the first line they make and gather the housing, to which join two components. On the second line completes the production of element this line, as the first, consists of a number of the rotary automatic weapons of those connected together by chain conveyer.
The housings, assembled on the first line and which already present unit in the composition of three components, enter on chute 1 loading
rotor 2, which plots them to chain conveyer 3. on rotor 4 they make the negative electrode, which is formed made of the mass, which enters through chute 5. on rotor 7 it fills electrolyte. Rotors 6 serve for the control of the operations, performed on rotors 4 and 7 respectively. Further chain conveyer passes heating chamber 8, where the process of ripening electrolyte proceeds. The positive electrode is obtained on rotor 9,material for which enters on chute 10. further it follows control on rotor 11, and from
rotor 12 assembled elements reveal to chute 13. The branch of chain conveyer 14 is unmarried.
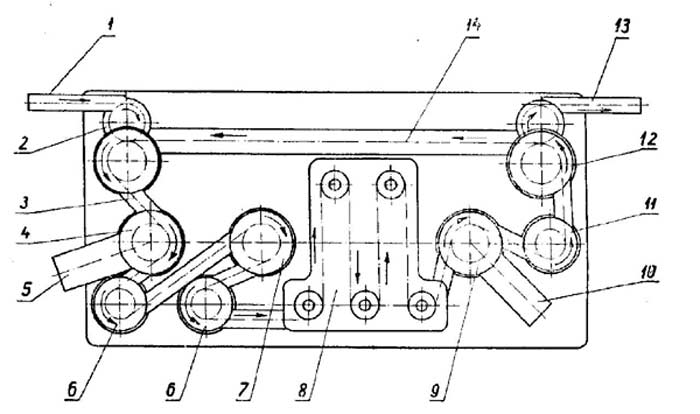
Fig. 1.1 schematic diagram of automation line for preparing the battery “change”
By such means, realized a complex automation of production of the elements, all components and materials of which manufacture into one whole in the united production line. As the second example let us examine automatic assembly line the unit of the crankcase of traction motor [SMD]-14. Assembling block with the pins, the crankshaft bearing caps, the washers and the nuts under the boring for the subsequent installation of crankshaft with the inserts is the labor-consuming work, which requires the high expenditures
of
manual labor for the delay of pins, nuts and the press-fitting of covers. The components enter in the block- crankcase in the collection: block, five crankshaft bearing caps, ten
the pins Of [m]18, ten special and ten locking washers. Automatic assembly line the unit of crankcase (Fig. 1.2) consists of two sections, connected together with main conveyer. The first section has two branches with the independent conveyers, each branch (right and leftist) consists of two aggregates: the hydraulic pressing of water jacket and oil passages and tilter. The second section consists of the automatic weapons: 1) the laying out of tapped holes into the groups; 2) healing and the delay of ten pins;
3) the inspection of pins on the height and the rejection; 4) the installation of five bearing caps; 5) healing and tightening of ten nuts; 6) marking. The enumerated automatic weapons are connected together by main conveyer for the transfer of the gathered article from one automatic weapon to another. The displacement of all actuating mechanisms of line is produced by means of one hydraulic drive with electrical control according to the specific cyclogram with time of the work T = of 1,04 min. line it has one
central control panel, and each automatic weapon - its automatic-adjustment independent panel, which is used for
Fig. 1.2 - the schematic diagram of automatic assembly line the block of the crankcase of engine [SMD]-14:
1 distributor; the hydraulic test bench of testing water jacket is 2nd; 3- tilter; 4 hydraulic test bench of testing oil valves; packer is 5th; 6 conveyer; 7 automatic weapon of the laying out of tapped holes into the groups; the automatic weapon of healing and delay of pins is eighth; 9 automatic weapon of the inspection of pins on the height; 10 automatic weapon of the installation of crankshaft bearing caps; 11- magazine attachment; 12- automatic weapon of healing and tightening of nuts; 13- automatic weapon
of the marking of the pins the pins Of [m]18, ten special and ten locking washers.
Automatic assembly line the unit of crankcase (Fig. 1.2) consists of two sections, connected together with main conveyer. The first section has two branches with the independent conveyers, each branch (right and leftist) consists of two aggregates: the hydraulic pressing of water jacket and oil passages and tilter. The second section consists of the automatic weapons: 1) the laying out of tapped holes into the groups; 2) healing
and the delay of ten pins; 3) the inspection of pins on the height and the rejection; 4) the installation of five bearing caps; 5) healing and tightening of ten nuts; 6) marking. The enumerated automatic weapons are connected together by main conveyer for the transfer of the gathered article from one automatic weapon to another. The displacement of all actuating mechanisms of line is produced by means of one hydraulic drive with electrical control according to the specific cyclogram with time of the work T =
of 1,04 min. line it has one central control panel, and each automatic weapon - its automatic-adjustment independent panel, which is used for performing of starting and adjusting work. Base component - block- crankcase establishes on the distributor, that directs component to the right and the leftist of the branch of the first section alternately, and packer directs block to the place, which approaches the first conveyer of the second assembly-line section (Fig. 1.3). The operations of the hydrotest of water
jacket and oil passages on two branches are produced in two cycles of the work of automatic weapon. On all assembly-line operations base component - block- crankcase is fixed on the technological openings existing in it and is pressed. On the operations
hydro test block is established under the covers by technological openings downward, and after hydro test on the following position it is turned to relative to longitudinal axis. Further, for the elongation of the?180 subsequent control and assembly-line operations fundamental adjusting base is parting plane with the head of block. The entering the assembly line components are located in the accumulators, located near the assembly-line aggregates or in the cassettes of automatic weapons. A quantity of gathered
articles, which are simultaneously found on the line - 33. by integral part of this automation line appears transport system ([ris].1.3). With the automation of line after the installation of block to the position. But distributor r. by the pressure of starting button moves block- crankcase to the right, after which the conveyer of left branch L it is moved back, packer - to the left, right conveyer p. - forward. With the following installation of block and the pushing of the knob of the motion of distributor,
conveyers and packer it occurs in the reverse order. After each right and left end position of packer the main conveyer of main accomplishes back stroke and, after taking block, it moves it forward on the main branch of line. If as a result hydraulic pressing block proves to be rejected, then operator establishes in the opening the special mount, which with the approach of block to the packer presses the special limit switch, which includes the conveyer of ejector, and the latter, after taking the rejected block,
derives it from the general flow of the work of line.
The installation of crankshaft bearing caps is produced with the aid of the special automatic weapon.
Fig. 1.3 - the diagram of the layout of the conveyers of automatic assembly line the unit of the crankcase
Of the operations of installation to the ends of the pins the unit of the crankcase of ten special and ten locking washers is produced by operator by hand. Of the operations of automatic healing, screwing on and tightening of ten nuts Of [m]18 it is produced on two separate automatic weapons. Line ensures the productivity of 55 [izd]./[ch]. line they attend three workers. The analysis of the structure of the technological process of automatic assembling and examples of the existing automatic assembly lines given
above makes it possible to make the following conclusions:
1. For creating the technological systems of continuous action for the assembly-line processes the development of the general methodology of the design of such systems is necessary;
2. The structures of the assembly-line technological systems of continuous action must ensure the peak output of their functioning;
3. The development of the systems of continuous action for the assembly-line processes must be achieved on the basis of the elementary kinematics of the functioning of assembly-line modules;
4. With the development of the technological systems of continuous action a complete study of the motion of assembly-line components on positions and modules of assembly-line systems is necessary.
Enumeration of references
1. automation of discrete production/[B]. [E]. [Bonov], [G]. [Y]. [Bogachev], [I]. [K]. [Boyadzhiev] and other; Under it is general. ed. Of [e]. [I]. [Semenov], [L]. [I]. [Volchkevich]. - M.: Machine building, 1987, Sofia: Technology, 1987. - 376 s.
2. Automation of assembling miniature articles with the use of stochastic vibration action/Of [l]. [P]. [Sungurov]. - In the book: Automation of electronic machine building. - Transactions [LPI], 1982, ¹382, s. 60-63.
3. Rotary type automation lines: Constructions, calculation and design/[A]. [N]. [Koshkin], [I]. [A]. [Klausov], [V]. [F]. [Prey]-[s] and other; Edited by [V]. [F]. [Peys]. - Tula: [TSBTI], 1961. - 198 s.
4. Analysis of the basing of components under the conditions of automatic assembling/By [t]. [E]. [Klade], [K].[YA]. Of [mutsenek], [I].[A]. Of [oditis] and other // the automation of assembly-line processes. Riga: [RPI], 1977. - Bitterns. 5. - s. 45-52.
5. [A].[s]. of 774917 USSR, MCi in 23 Q 39/04. Rotary type automation line for assembling of units/[O]. [A]. [Larintsev]; It caused heaves. 30.10.80., ball. ¹40. - 4 s.
6. [B]. [S]. [Osnovy]'s [Balakin] the technology of machine building. - M.: Machine building, 1973. - 688 s.
7. Belov Yu. [S]., Vlasov e. [V]., [Yurevich] [E]. [I]. [Sostoyanie] and the trend of development of robot technology. - M.: [VNIITEMR], 1985. - 48 s.
8. [Berzh] k. the theory of graphs and its application. - M.: Illus., 1982. - 319 s.
9. Birkhoff [G]. [Teoriya] structures. - M.: Illus., 1952. - 407 s.
10. [Blyakherov] i. s. and other automatic load of technological machines/- M.: Machine building, 1990, 346 s.
11. [Bonch]-[Osmolovskiy] M. a. selective assembly. - M.: Machine building, 1974. - 144 s.
12. Boolean p. [I]., Krylov g. [V]., [Lopukhin] [V]. [A]. [Avtomatizatsiya] the selective assembly of instruments. L.: Machine building, 1987. - 232 s.
13. Selection of equipment installation with the automation of fitters work/OF [A].[A]. Gusev. - In the book: Automation of assembly-line and welding process in machine building. M.: Science, 1974. - s. 116 - 123.
14. [Gavryush] [A].[P]. flexible robotic systems. - Kiev: Is prophetic school, 1989. - 406 s.
15. [Ganovski] v. [S]., [Boyadzhiev] [I]. [K]. [Avtomatizatsiya] and the overall mechanization of assembly-line processes in machine building. Sofia: Technology. 1982. - 236 s.
16. Flexible production systems of assembling/[P]. [I]. Alekseyev, [A]. [G]. Gerasim, [E]. [P]. [Davidenko] and other; [Pod]. it is general. ed. [A]. [I]. Fedotov. - L.: Machine building. Leningrad. return, 1989. - 349 s.
17.[Gibkoe] automatic production/[V]. [O]. Abel, [V]. [A]. Yegorov, [A]. [Yu]. [Zvonitskiy] and other; Edited by [S]. [A]. [Mayorov], [G]. [V]. [Orlovskogo], S.N. [Khalkiopova]. - L.: Machine building, 1985. - 454 s.
18. ALL-UNION STATE STAN. 14.320 - 81. Forms of assembling.
19. Gusev [A]. [A]. [Adaptivnye] are the device of assembly-line machines. M.: Machine building, 1979. - 266 s.
20. [Dvoryankin] a. M., the halves Of [a] [e], Sobolyev [A]. [N]. [Metody] the synthesis of the technical solutions. - M.: Science, 1977. - 253 s.
21. [Dovgan] s. [I]., [Litvinov] b. [Yu]., [Sbitne] [A]. [I]. [Personalnye] are THE COMPUTER(S): [TurboPaskal] 6.0, objective orientation, local networks. - Kiev: [Informsistema] service, 1993. - 440 s.
22. Zakharov [N]. [V]. [Sovershenstvovanie] are state and a trend in development of domestic and foreign production. /The contemporary problems of machine building and technical progress. Theses. Reports to internat. scientific-techn. conference. On September 10 to 13, 1996. - It is Donets: [DonGTU], 1996. - s. 85-86.
23. Zakharov M. [V]., [Timof]ºº[v] [Yu]. [V]. [Rozrobk] [tekhnolog]³[chnikh] [protses]³[v] of [skladannya]: [Nav]³[ch]. [pos]³[bnik]. K.: [NMK] INTO, 1992. - 152 c
24. Zakharov [M].[V]. Of [anal]³[z] that is the synthesis of the structures of the [avtomatizovanikh] [skladalnikh] [tekhnolog]³[chnikh] systems: Author's Abst. dis. … doctor of technical sciences. - [Khark]³[v], 1992, 38 c.
25. Zakharov n. [V]., [Rubets] n. [P]., Melnichenko a. [A]., [Nechiporenko] n. [V]., [Odnenko] g. i., Bondaryev of this year the perfection of technology in the machine-building production: - Sumy: [SumGU], 1994. - 98 s.
26. [Zamyatin] Of [v]. [K]. [Sbork] of mobile cylindrical and taper joints. M.: Machine building, 1980. - 145 s.
27. Winter p. [F]., Timoshenko [G]. [M]. [Teoriya] the engineering experiment: Studies. benefit - k.: [UMK] IN, 1991. - 124 s.
28. Study of the technological systems of automatic assembling by the method of theory of graphs/[M]. [S]. [Lebedevskiy], [A]. [I]. Fedotov. - In the book: Automation and overall mechanization in machine building. - Transactions [LPI], 1978, ¹360, s. 12-17.
29. [A]. [L]. [Zakonomernosti]'s [Ishchenko] the forming of the structures of the assembly-line automatic technological assembly-line systems of continuous action. /Advanced technologies and machine building system: Coll. of scientific works. - It is Donets: [DonGTU], 1997. Bitterns. 4 s. 61 - 66.
|