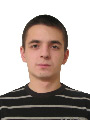 |
   Teriaiev Ievgen |
   Faculty: |
Engineering mechanics and mechanical engineering |
   Speciality: |
Technology of mechanical engineering |
   Theme of master's work: |
Technological support to improve the quality of surfaces revolution by finishing treatment |
   Scientific adviser: |
associate professor Kovalenko Valeriy |
Abstract |
Important remark! |
When I wrote this abstract, master's project work is not yet completed. Final completion will be
December 2010. Full text of work and materials on the subject can be obtained from the author or his adviser
after that date. |
|
Objective of work
To improve the stability of a manufacturing process based on an analysis of factors influencing the accuracy
of machined surfaces.
In a mass production factory called Compressor which is a subsidiary of the NORD Company. I did experimental
studies of couplings: shaft-casing and the piston-casing. Both of these couplings are used in compressor of
refrigerator and are the most important parts. Figure 1 shows the working processes of the main unit compressor.
|
Figure 1. Animation working processes of the main unit compressor
(size of animation 79 Kb; frame count 12; repeat count 5)
|
Searching and analyzing of factors influencing the accuracy of the machined surfaces based on finishing
treatment operation of these mating parts.
It may give some factors that have great impact on the analyzable manufacturing process:
- element displacement of the technological system under the action of cutting forces;
- geometric inaccuracy of machine tool;
- debugging and corrective adjustment of technological system on size;
- error of measurement;
- dimensional deterioration of process tool;
- microstructure;
- distribution of internal stresses;
- different hardness of work pieces;
- temperature deformations.
Object of study — finishing operations couplings shaft-casing and the piston-casing.
Item of study — samples with measurements of the shaft, piston and two matching bores in the casing.
Method of study — is based on statistical analysis of data obtained by measuring.
|
Aim and scope of work
In the study of accuracy of manufacturing processes and identifying patterns of production errors, analytical
and statistical methods are used to analyze manufacturing of parts.
The analytical method is based on establishing a functional relationship between the values of each primary
error and the final accuracy of the finished product.
In fact, defining the model does not reflect in its entire manufacturing processes, because it is impossible
to analytically determine all collection of the factors and their influence on the accuracy of the output
parameters of the process. Therefore, this method is applicable only to assess the impact of individual factors
on the accuracy of manufacturing of the individual parts.
In a more wide application, the estimated accuracy of manufacturing processes had received a statistical
method. The method is based on the theory of probability and mathematical statistics. The statistical method is
based on receiving and processing a large number of observations, providing the necessary body of information.
The statistical method used to investigate the accuracy of the manufacturing processes of serial and mass
production using the distribution curves, correlation and dispersion analysis, the accuracy of diagrams.
The statistical method differ is not only for its low cost and complexity, but also because it makes it
possible to find the conditions for optimal functioning of the process under investigation.
|
Scientific novelty
In the future, I will be able to innovate a method of estimating the precision manufacturing process based
on dispersion and correlation analysis.
|
Practical value
To obtain an experimental data that characterize the work couplings shaft-casing and the piston-casing with
point of view, their accuracy and identification of factors affecting the stability of the manufacturing process,
the appearance of defective parts; method clearing of wastage.
|
Review of research
Globally, a major contribution to the development of statistical methods of experimental design made by
Ronald Fisher, who first demonstrated the feasibility of simultaneous variation of all factors, as opposed to
common single-factor experiment, as well as Box and Wilson, who proposed a method of steep ascent.
On a scale of Donetsk National Technical University in similar work Masters engaged department "Technology of
mechanical engineering" Kudryavtsev A. on the subject "Investigation of processing roller of mill on a machine
with CNC" and Lobko A. on the subject "Technological maintenance of improvement of quality of details of the
hydraulic cylinder"
|
Summary of own results
At the present point in time do exploration of coupling shaft-casing. Fig. 2 shows a scheme of crank
mechanism.
|
Figure 2. Scheme of crank mechanism
Where dв1 - diameter of short section of shaft, dв2 - diameter of long section of shaft,
Dmin - minimal diameter of bore, Dmax - maximal diameter of bore.
The initial data are measuring size drift dв1, dв2, Dmin,
Dmax for the three samples. Each sample consists of 50 measurements. Samples were selected during a
period of one-week intervals. Results obtained when measuring the samples are presented in table 1.
Diagram of the size distribution of the first sample for the parameters dв1, dв2
presented in figure 3.
Figure 3. Diagram of the size distribution dв1 and dв2
|
Table 1. Results of measuring inaccuracies of mating parts, mcm
№ | Sample №1 | Sample №2 | Sample №3 |
dв1 | dв2 | Dmin | Dmax | dв1 | dв2 | Dmin | Dmax | dв1 | dв2 | Dmin | Dmax |
1 | 14 | 13 | 5 | 7 | 15 | 14 | 5 | 7 | 16 | 14 | 1 | 4 |
2 | 14 | 12 | 8 | 11 | 14 | 13 | 7 | 8 | 11 | 12 | 8 | 9 |
3 | 14 | 12 | 3 | 6 | 12 | 11 | 3 | 5 | 11 | 12 | 5 | 5 |
4 | 14 | 13 | 1 | 4 | 16 | 15 | 5 | 7 | 13 | 12 | 4 | 6 |
5 | 12 | 12 | 5 | 7 | 14 | 13 | 0 | 3 | 10 | 12 | 4 | 6 |
6 | 14 | 14 | 6 | 9 | 14 | 15 | 3 | 6 | 12 | 12 | 5 | 8 |
7 | 13 | 13 | 5 | 8 | 14 | 13 | 4 | 6 | 13 | 13 | 5 | 7 |
8 | 12 | 11 | 4 | 7 | 15 | 15 | 1 | 6 | 13 | 11 | 6 | 8 |
9 | 14 | 14 | 6 | 9 | 16 | 15 | 1 | 3 | 11 | 12 | 4 | 6 |
10 | 13 | 13 | 5 | 7 | 13 | 15 | 5 | 6 | 11 | 11 | 6 | 8 |
11 | 15 | 14 | 4 | 7 | 13 | 16 | 5 | 8 | 9 | 10 | 6 | 8 |
12 | 14 | 13 | 6 | 8 | 13 | 15 | 5 | 6 | 11 | 11 | 9 | 10 |
13 | 13 | 13 | 4 | 5 | 13 | 16 | 9 | 10 | 16 | 13 | 1 | 4 |
14 | 10 | 10 | 2 | 5 | 12 | 15 | 5 | 6 | 11 | 11 | 1 | 3 |
15 | 13 | 13 | 7 | 9 | 13 | 12 | 5 | 7 | 13 | 13 | 4 | 7 |
16 | 12 | 12 | 9 | 11 | 13 | 15 | 0 | 2 | 12 | 13 | 5 | 8 |
17 | 14 | 12 | 4 | 6 | 16 | 14 | 7 | 9 | 13 | 13 | 7 | 9 |
18 | 13 | 13 | 9 | 10 | 14 | 15 | 6 | 9 | 10 | 11 | 4 | 7 |
19 | 14 | 13 | 5 | 8 | 14 | 16 | 4 | 6 | 11 | 11 | 3 | 6 |
20 | 15 | 13 | 4 | 6 | 13 | 14 | 3 | 6 | 12 | 12 | 7 | 8 |
21 | 13 | 13 | 7 | 10 | 14 | 15 | 2 | 3 | 11 | 11 | 5 | 7 |
22 | 13 | 13 | 7 | 9 | 16 | 15 | 4 | 7 | 13 | 11 | 7 | 9 |
23 | 13 | 12 | 7 | 9 | 13 | 14 | 6 | 9 | 11 | 11 | 0 | 3 |
24 | 11 | 12 | 6 | 9 | 11 | 12 | 4 | 6 | 10 | 9 | 8 | 9 |
25 | 11 | 12 | 7 | 9 | 15 | 16 | 8 | 9 | 14 | 13 | 3 | 4 |
26 | 14 | 14 | 8 | 9 | 16 | 15 | 5 | 6 | 13 | 13 | 2 | 4 |
27 | 14 | 13 | 6 | 8 | 14 | 13 | 2 | 6 | 12 | 10 | 2 | 4 |
28 | 14 | 13 | 0 | 3 | 16 | 15 | 1 | 3 | 12 | 13 | 1 | 3 |
29 | 12 | 14 | 6 | 8 | 15 | 16 | 2 | 6 | 13 | 13 | 2 | 3 |
30 | 14 | 14 | 5 | 7 | 13 | 15 | 4 | 6 | 12 | 11 | 4 | 6 |
31 | 14 | 12 | 6 | 9 | 14 | 15 | 6 | 9 | 12 | 12 | 3 | 4 |
32 | 13 | 13 | 6 | 8 | 14 | 13 | 1 | 3 | 12 | 11 | 4 | 5 |
33 | 13 | 14 | 10 | 11 | 12 | 13 | 6 | 9 | 13 | 12 | 5 | 7 |
34 | 15 | 13 | 4 | 5 | 16 | 15 | 4 | 5 | 13 | 12 | 8 | 9 |
35 | 15 | 14 | 10 | 11 | 14 | 15 | 7 | 8 | 12 | 11 | 0 | 3 |
36 | 12 | 11 | 8 | 11 | 13 | 14 | 7 | 8 | 11 | 10 | 5 | 6 |
37 | 14 | 14 | 4 | 7 | 13 | 14 | 5 | 7 | 13 | 13 | 7 | 9 |
38 | 12 | 13 | 4 | 6 | 18 | 16 | 6 | 9 | 13 | 13 | 3 | 4 |
39 | 13 | 13 | 6 | 7 | 13 | 14 | 4 | 5 | 12 | 12 | 7 | 8 |
40 | 14 | 13 | 4 | 6 | 16 | 18 | 4 | 6 | 10 | 9 | 8 | 9 |
41 | 15 | 13 | 8 | 9 | 16 | 17 | 5 | 6 | 10 | 10 | 2 | 3 |
42 | 15 | 14 | 4 | 6 | 16 | 15 | 8 | 9 | 12 | 11 | 4 | 6 |
43 | 14 | 12 | 3 | 5 | 16 | 15 | 5 | 8 | 11 | 10 | 4 | 7 |
44 | 15 | 13 | 5 | 7 | 15 | 14 | 4 | 6 | 11 | 10 | 0 | 3 |
45 | 14 | 12 | 10 | 11 | 17 | 15 | 4 | 6 | 12 | 12 | 8 | 9 |
46 | 15 | 13 | 7 | 8 | 13 | 14 | 5 | 8 | 13 | 14 | 9 | 11 |
47 | 13 | 15 | 10 | 11 | 18 | 19 | 3 | 5 | 16 | 15 | 5 | 7 |
48 | 13 | 12 | 9 | 10 | 15 | 14 | 7 | 8 | 15 | 14 | 3 | 5 |
49 | 13 | 13 | 10 | 11 | 15 | 13 | 6 | 9 | 14 | 13 | 3 | 5 |
50 | 10 | 11 | 7 | 9 | 16 | 12 | 4 | 7 | 10 | 10 | 0 | 3 |
|
In order to simplify the calculation formed mean bore diameter Dср on all the values in the samples:
|
Dср = (Dmin + Dmax) ⁄ 2 |
(1) |
Secure and heavy activity of compressor ensured optimal clearances in all movable joints. Therefore, for
each sample that was determined, clearance J1 and J2 have difference in the
size of mean bore diameter and the diameter of the corresponding surfaces of shaft.:
| J1 = Dср - dв1 | (2) |
| J2 = Dср - dв2 | (3) |
|
Diagram of distribution clearance J1 and J2 on the first sample is shown in fig. 4.
Figure 4. Diagram of distribution clearance J1 and J2
To study this coupling used dispersion analysis. To check the homogeneity of two dispersions in practice
most often used Fisher criterion (F-test), which lies in the fact that the taken relation of greater dispersion
(S12) to lower (S22) [1]:
|  | (4) |
Calculated value of the criterion is compared with the critical tabulated, defined for an accepted level of
significance and relevant S12 and S22 the degrees of freedom f1
and f2. If the calculated value F is greater than the table Fα,
then the dispersions are heterogeneous and there is need to compare other dispersions. When the calculated value
F is less than the table Fα, then they are homogeneous dispersions, in which case
you should use the weighted average value of the dispersion:
| 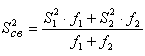 | (5) |
Characteristics of samples (sample size n, the degrees of freedom f, the arithmetic mean
X and dispersion estimation Sx2) are presented in table 2.
Table 2. Static characteristic of samples
№ of sample | Observable parameter | n | f | X, mcm | Sx2 |
1 | dв1 | 50 | 49 | 13,34 | 1,494 |
dв2 | 12,82 | 0,926 |
Dср | 6,95 | 4,716 |
J1 | 20,29 | 5,49 |
J2 | 19,77 | 6,073 |
2 | dв1 | 50 | 49 | 13,34 | 1,494 |
dв2 | 12,82 | 0,926 |
Dср | 6,95 | 4,716 |
J1 | 20,29 | 5,49 |
J2 | 19,77 | 6,073 |
3 | dв1 | 50 | 49 | 13,34 | 1,494 |
dв2 | 12,82 | 0,926 |
Dср | 6,95 | 4,716 |
J1 | 20,29 | 5,49 |
J2 | 19,77 | 6,073 |
|
|
|
Conclusion
In the future, I will engage in a research work on the dispersion and correlation analysis of couplings
shaft-casing and the piston-casing with a large number of samples. The interval between samples will be at least
one week, and this means that the properties of the material of work pieces and condition of the process tool.
And then it will be possible to determine the influence of various factors on the characteristics of the
manufacturing process.
|
|
Important remark! |
When I wrote this abstract, master's project work is not yet completed. Final completion will be
December 2010. Full text of work and materials on the subject can be obtained from the author or his adviser
after that date. |
References |
- Теория инженерного эксперимента: Учеб. пособие / Тимошенко Г.М., Зима П.Ф. – К.: УМК ВО, 1991.
- Справочник по теории вероятностей и математической статистике / Королюк В.С., Портенко Н.И., Скороход
А.В., Турбин А.Ф. – М.: Наука. Главная редакция физико-математической литературы, 1985.
- Кутай А.К., Кордонский X.Б. Анализ точности и контроль, качества в машиностроении с применением методов
математической статистики. М.- Л., Машгиз, 1958.
- Спиридонов А.А. Планирование эксперимента при исследовании технологических процессов. М.: Машиностроение,
1981.-184 с., ил.
- Адлер Ю.П., Маркова Е.В., Грановский Ю.В. Планирование эксперимента при поиске оптимальных условий. М.: Наука,
1976.-279 с.
- Вознесенский В. А. Статистические методы планирования эксперимента в технико-экономических исследованиях.
М., Статистика, 1974. 192 с.
- Вознесенский В. А. Статистические решения в технологических задачах. Кишинев, Картя молдовеняска, 1968. 232 с.
- Х. Шенк. Теория инженерного эксперимента.- Пер. с англ.- М.: Мир, 1972.
- Фишер Р.А. Статистические методы для исследователей. М.: Госстатиздат, 1958
- Феллер В. Введение в теорию вероятностей и ее приложения. Том 1. (2-е изд.). М.: Мир, 1964
- Феллер В. Введение в теорию вероятностей и ее приложения. Том 2. М.: Мир, 1967
- Математическая теория планирования эксперимента./Под редакцией С.М. Ермакова.-М.: Наука. Главная редакция
физико-математической литературы, 1983.-392 с.
- Xальд А. Математическая статистика с техническими приложениями. М.: ил, 1956
|
|