ABSTRACT OF THE MASTER WORK'S THEME
Table of contents:
Table of contents:
1. Actuality of theme
2. Analysis of publications
3. Aim and research tasks
4. A physical model of resonator is with a branch
5. Mathematical model of new hydraulic of oscillation contour
Conclusions
List of literature
1. Actuality of theme
Further development and technical level of hydraulic apparatuses are indissolubly related to the improvement of them dynamic descriptions. Application of existent hydraulic apparatuses is in technological machines, does not allow to provide permanent reliability of work of hydraulic driver of vcelom.
The known lacks of hydraulic apparatuses with valvular or slide-valve distributive elements are a presence of hydrodynamic forces, nonlinear friction, possibility of the hydrostatical jamming.
One of effective ways of fight against the noted defects there is application of hydraulic apparatuses with oscillation which registers in works of Т.М. Bashta, Г.А. Nikitina, other researchers. However, working processes which take place in hydraulic apparatuses with a hydraulic management and with hydraulic oscillation are not investigational and a simple and effective hydraulic oscillation contour is not worked out.
Hydroelectric generators which are used in industry are characterized by the variety of elements which are included in their composition, presence of difficult working processes which take place in the process of their functioning. The methods of their calculation and planning have a row of features from the account of which it is possible to improve them dynamic descriptions: complex account at mathematical description of hydraulic apparatuses of unstationarity of hydraulic mechanic processes and descriptions of working liquid, which change in the process of his functioning; improvement of schematics of гідроапаратури and томпоновки of his elements; an increase of exactness of calculation of sources is in the mobile elements of гідроапаратури; forces of friction are on the осцилюючому slide-valve of гідророзподільиика, which promote exactness of mathematical model of hydraulic apparatuses.
Taking into account transferred, count the theme of master's degree work, sent to the decision scientifically, - practical task, related to the increase of technical level of hydroelectric generators by the use of pulsation of pressure of working liquid for revealing to of oscillation motion the mobile elements of hydraulic apparatuses is timely and actual.
Table of contents
2. Analysis of publications
To the methods of planning of resonator with a branch, which to it was used as гасник, the small amount of works is devoted. Yes, in [3, 4] they over are brought fundamental charts and dependences for determination of volume of chamber and sizes of channels. In [5] a design technique over, which is based on an electro-analogy at the use of which the row of limitations is laid on, is brought, tying up with the sizes of resonator with a branch and sometimes passing of hydrodynamic transients. In addition, the use of this methodology requires realization of previous experimental researches, that complicates her use considerably. In [6] the brought mathematical models over of resonator with a branch, built with the use of method of Euler, but in them absent recommendations in relation to determination of them rational, structural and working parameters. In addition, the use of these mathematical models is labour intensive enough. More complete reflection of this problem found in [7], where mathematical models over of such devices, built with the use of transformations of Fourier, which can be used for certain them rational, structural and working parameters, are brought. However in her more attention is spared гасникам pulsations of pressure. Thus, determination of structural and working parameters of resonator with a branch on the basis of realization of comprehensive analytical researches is an actual scientific and technical task.
Table of contents
3. Aim and research tasks
The aim of work is a construction of mathematical model resonator with a branch, analysis of influence of him structural and working parameters on a transmitivity.
Table of contents
4. A physical model is a resonator with a branch
In a cylindrical corps 3(capacity element) the cylindrical narrowed union coupling is placed 2 (inertia element), which through the union coupling 1 it is connected to the highway of feed (sources of pulsations of pressure). It is realized shaking loose resonance contour. Union coupling 4 connects a resonator with a branch with the chamber of management of hydrodistributor. The pulsations of pressure of working liquid enter capacity through the union coupling 1 and 2. In case of presence of change of phases of pulsating stream of working liquid and eigenfrequency a resonator is with a branch, there is strengthening of pulsations of pressure which acts to the chamber of management of hydrodistributor. Gathering additionally corresponding capacities, crossing and length of the narrowed union coupling 2, it is possible to get different amplification factors.
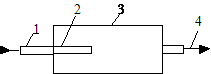
Picture 1 - Chart of resonator from by a branch: 1 - an entrance pipeline; 2 - the entrance narrowed union coupling; 3 - chamber of new hydraulic oscillation contour; 4 - chamber of hydrodistributor.
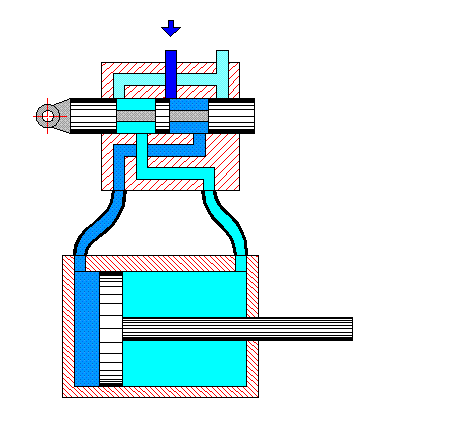
Picture 2 – Interaction of the hydrodistributor with the volume pump
(animation: volume - 254 Кб; size - 450х422; consists of a 22 shot; delay between shots - 1с; delay between the last and first shots - 7с; amount of cycles of reiteration - 25)
Table of contents
5. Mathematical model of new hydraulic of oscillation contour
At the stowage of mathematical model of new hydraulic oscillation contour will do such suppositions:
– consider that there are withstand hydrodynamic processes in a new hydraulic oscillation contour. Does not examine transients, related to the dramatic change of parameters on his entrance. Examine batch hydrodynamic processes, conditioned by the pulsation of pressure of working liquid on an exit from a pump;
– possibly, that the type of distribution of speed of working liquid on the cut of channels of new hydraulic oscillation contour is formed;
– consider that in hydraulic sistem, and thus and in a new hydraulic oscillation contour, absents resonance, kavitacion of working liquid and water-hammer;
– speed of sound of working liquid is a size permanent, considerably anymore from her speed in hydraulic system;
– a temperature of working liquid is permanent and is in a range 50-55?С. Permanent also there is газовміст of working liquid, which is taken into account at the calculation of the module of by volume resiliency of working liquid, which take permanent and expect taking into account resilient properties of pipeline;
– equalization of unbreak of working liquid is executed on all areas of hydraulic sistem;
– ignore mass forces of working liquid. Will notice that analogical supposition is taken by most researchers [14, 15];
– consider a working liquid newtonian, and flow isothermal;
– the flow of working liquid is unidimensional axisymmetrical.
Taking into account the accepted suppositions, motion of working liquid in hydraulic sistem can be described by means of wave equalization as a system of two differential equalizations of first-order, which taking into account hydraulic resistance of pipeline can write down as [8]
,(1)
where ; λ - is a coefficient of hydraulic resistance; dт – is a diameter of pipeline; ρ - it is a closeness of working liquid; V - - is speed of working liquid; а -is speed of sound in a works liquid; р -is pressure ; х -is distance from the beginning of pipeline to the cut, where pressure (speed) of working liquid is determined
As an expense absents through a new hydraulic oscillation contour, it is possible a member which takes into account the losses of pressure in equalization (1) to scorn. A ground over of this supposition is brought in [9,10].
A decision (1) will conduct the method of frequency analysis, namely by the method of standing waves, offered Lytcem for the calculation of wave processes. In accordance with this method, a decision (1) can be writtenin in a hyperbolical form [8]
,(2)
where - became distribution of wave process; φ - it is a wave-number; l - - it is length of area of pipeline (to the channel); |