Тимошенко Ніна Вікторівна

Фізико-металургійний факультет
Кафедра обробки металів тиском
Спеціальність: обробка металів тиском
Тема випускної роботи : Дослідження параметрів гарячої прокатки особливо тонких смуг
Науковий керівник: професор кафедри ОМД Руденко Євгеній Олексійович
Дослідження параметрів гарячої прокатки особливо тонких смуг
Нині в Японії, США, Мексиці, Іспанії освоєно гаряча прокатка смуг завтовшки 0,8- 1 мм, практично не поступливих по точності і механічним властивостям холоднокатаному металу. Прогнозовані обсяги виробництва гарячекатаних особливо-тонких смуг щорічно збільшуються на 8,3 % в США, 6,7% в ЄС і 6,6% в Японії [ 1 ].
Заміна холоднокатаних листів на гарячекатані, собівартість яких нижча, як мінімум, на 20 доларів США на тонні прокату, а також тенденція зростання цін на холоднокатаний лист обумовлюють доцільність освоєння виробництва особливо тонкого гарячекатаного листа в Україні. Нині освоєно виробництво гарячекатаних смуг завтовшки 1,5 мм на стані 1700 ВАТ "МарМК" ім. Ілліча і 1680 меткомбінату "Запорожсталь". Умови прокатки особливо тонкої гарячекатаної смуги 1,5 мм на стані 1680 характеризуються низькою температурою кінця прокатки (770-810°С), що не забезпечує потрібні механічних властивості гарячекатаних смуг [2,3].Технічні і технологічні можливості отримання на цих станах смуг завтовшки менше 1,5 мм відсутні.
Особливо тонкі смуги з низьковуглецевої сталі можуть мати широкі діапазони зміни механічних властивостей. Отримати необхідних механічних властивості можна, реалізовуючи конкретні деформаційні і температурні режими прокатки смуг в чистовій групі клітей широкосмугового стану, а також правильним вибором товщини і температури підкату. Тільки певний комплекс вхідних параметрів підкату, обтискань по чистових клітях і швидкості кінця прокатки забезпечує необхідну температуру кінця прокатки і як наслідок необхідні механічні характеристики сталі.
Для отримання пластичної сталі з низькими тимчасовим опором (межею міцності) і межею плинності, а також з високим відносним подовженням необхідно температуру кінця прокатки (за останньою чистовою кліттю) тримати в межах 860 - 900 °С, а температуру змотування смуги в рулон - 680-740 °С. У цьому діапазоні температур кінця прокатки відбувається повна рекристалізація аустеніту. Нижче в діапазоні температур 820- 860 °С в металі починається фазове перетворення аустеніту на ферритно-перлитную суміш. Закінчення деформації в цьому діапазоні веде до здрібніння зерна, збільшення міцності і зменшення пластичних характеристик стали.
Якщо температура кінця прокатки знаходиться нижче 820 °С, то процес деформації протікає в двофазній області структури сталі. В цьому випадку смуга після прокатки має дрібнозернисту структуру, високі прочностні і низькі пластичні властивості.
По чистових клітях широкосмугового стану температура зменшується. У перших клітях деформація сталі здійснюється в аустенітній області, а в останніх - найчастіше в двофазній феррито-перлитной області. Для отримання особливо тонких гарячекатаних смуг, що мають високі пластичні властивості, відповідних холоднокатаним смугам після відпалу, необхідно забезпечити температуру кінця прокатки вище 860 °С.
В зв'язку з цим розробка ефективних технологічних режимів гарячї прокатки пластичних особливо тонких смуг заснована на різних варіантах технічних і технологічних рішень по реалізації вказаних вище вимог.
Метою роботи є визначення параметрів гарячої прокатки особливо тонких смуг в п'яти - семи клітьових чистових групах необхідних для забезпечення потрібної якості металу .
Згідно з температурним балансом смуги при прокатці в чистовій групі клітей температура кінця прокатки tк залежить від температури підкату перед першою чистовою кліттю tп, втрат тепла шляхом випромінювання і конвекції в міжклітьових проміжках, втрат тепла внаслідок контакту гарячого металу з холодними валками у вогнищах деформації клітей і підвищення температури за рахунок роботи деформації і сил тертя у вогнищах деформації клітей. У цьому балансі підвищити температуру можна шляхом підвищення роботи деформації і зниження усіх складових втрат. Температура підкату tп безпосередньо і однозначно впливає на температуру готової смуги на виході з чистової групи tк. Отже, при інших постійних параметрах для збільшення tк необхідно збільшити tп. Проте діапазон збільшення tп обмежений. Температура підкату, отриманого шляхом прокатки товстих слябів в чорновій групі клітей широкосмугового стану і на виході з печі ливарно-прокатного модуля, що підігріває, складає 1000-1100 °С. Підвищити нижню межу можна шляхом підвищення обтискань в останніх чорнових клітях, екрануванням підкату або його підігріванням перед чистовою групою клітей. Можливе збільшення температури складає лише 20-50 °0С, що дозволяє підвищити t к лише на 7-12 °С. Отже, єдиним ефективним шляхом підвищення tк є підвищення швидкості прокатки. При цьому збільшується робота деформації і скорочуються усі статті втрат тепла в балансі.
Дослідження температурно-швидкісних, енергосилових і деформаційних режимів прокатки особливо тонких смуг виконали в п'яти, шести, і семи клітьових чистових групах клітей широкосмугового стану з використанням математичних моделей і пакету програм "Універсал", розробленого в НВО "Доникс" [ 4 ].
Дослідження показало, що реалізувати прокатку особливо тонких смуг можливо тільки з високими відносними обтисканнями в перших чистових клітях (50-65%), залежно від числа чистових клітей і товщини підкату. При таких обтисканнях момент прокатки М досягає 3 і більше МНм, а сила прокатки Р 30 МН і більше. Передати такі моменти можуть шийки робочих валків діаметром 900 мм і більше. В зв'язку з цим діаметри робочих валків перших двох чистових клітей вибрали рівними 900-950 мм. В наступних чистових клітях моменти прокатки різко зменшуються, тому діаметри валків зменшували по парах клітей до 750 мм. Діаметри зменшували також з метою зниження сили прокатки. Так, для п'ятиклітьової чистової групи діаметри робочих валків першої і другої кліті прийняті 900 мм, третьою і четвертою 850 мм і пятой- 800 мм. В шести - і семи клітьових групах діаметри останніх клітей вибрали 800-750 мм.
При діаметрах опорних валків в два рази великих валкові вузли чистових клітей забезпечують силу прокатки до 40 МН і більше. Для забезпечення великих швидкостей прокатки (20 м/с і більше), потужність електродвигунів має бути не менше 20 МВт.
Температурно-швидкісні режими моделювали для умов прокатки особливо тонких смуг з підкатів завтовшки 10-60 мм, шириною 1000 мм, завдовжки 50 м із сталі Ст3сп. Температуру підкату приймали рівною 900, 1000 і 1100 °С. Швидкість прокатки варіювали в діапазоні 10-20 м/с. На кожному рівні швидкості (10, 15, 20 м/с) визначали прискорення чистової групи клітей, яке забезпечує стабільність температуру смуги по довжині (компенсацію температурного клину підкату, що утворюється за час руху його заднього кінця до першої кліті).
Такий температурний клин на підкаті завтовшки 50 мм, завдовжки 50 м, при прокатці смуги завтовшки 0,8 мм із швидкістю 10 м/з досягає 200 °С.
За планом дослідження підкат кожної товщини з температурою 900, 1000 і 1100 °С прокатували на смуги завтовшки 0,8; 1,1 і 1,4 мм на швидкості 10, 15 і 20 м/с в п'яти, шести і семиклітьовий групах клітей.
З використанням розробленої програми розрахунку визначали температури переднього tп і заднього tк кінця розкату на вході і виході кожної кліті, а також значення вирівнюючого по довжині готової смуги прискорення ау і температуру кінців розкату при прокатці з прискоренням в кожній кліті tзу.
Розрахунки показали, що оптимальний діапазон температури кінця прокатки 860- 890 °С при прокатці особливо тонких смуг забезпечується режимом прокатки з підкату завтовшки 50 мм на швидкості 10 м/с як в шести так і в семиклітьовій чистовій групі, а також з підкату завтовшки 20-40 мм в п'ятиклітьовій чистовій групі.
Слід зазначити, що швидкість прокатки 10 м/с являється максимальною по умові заправки стану, транспортування смуги по рольгангу, що відводить, і заправки в моталку. На практиці вона нижча (8-9 м/с). Температура кінця прокатки смуг завтовшки 0,8 мм з підкату завтовшки 10 мм на швидкості 10 м/с в 5,6 і 7-клітьовій чистовій групі складає відповідно до 786, 719 і 674 °С. При швидкості прокатки 15 м/с температура підвищується на 70-80 °С, а при 20 м/с ще на 40-50 °С і складає відповідно до 904, 842 і 786 °С.
Аналіз результатів розрахунків показав, що для забезпечення заданої температури смуги на виході з чистової групи може бути досягнутий тільки шляхом підвищення швидкості прокатки. Чим вище прискорення, тим більша частина довжини смуги матиме задану температуру. Зазвичай прискорення починають після заправки переднього кінця смуги в моталку. Смуги завтовшки 0,8-1,4 мм з підкату завтовшки 10 мм слід катати на швидкості 20 м/с; з підкату 30 мм - на швидкості 15 м/с, а з підкату завтовшки 50-60 мм - на швидкості 10 м/с.
Встановили, що температура кінця прокатки із збільшенням числа клітей зменшується на 60-90 °С при збільшенні товщини підкату з 10 до 60 мм відповідно.
Температурний клин підкату зменшується по чистових клітях в 2-6 разів (при швидкості плющення 10 м/с) із зменшенням товщини підкату.
Зміну коефіцієнта передачі температурного клину (вирівнювання температури по довжині смуги) К&Deltat розраховували як відношення

где Δtk - зменшення температури по довжині готової смуги, мм; де
Δtn- зменшення температури по довжині підкату, мм..
Значення КΔt змінюється в діапазоні 0,14-0,5 для товщини смуги 0,8-1,4 мм відповідно. Із збільшенням товщини підкату значення КΔt зменшуються, а із збільшенням температури підкату збільшується.
Швидкість плющення неоднозначно впливає на коефіцієнт КΔt . При плрокатці смуг завтовшки 0,8 мм із збільшенням швидкості прокатки КΔt зменшується, а при прокатці смуг завтовшки 1,1 і 1,4 мм в 6-клітьовій чистовій групі зменшується, а 7-клітьовий - збільшується.
Зниження температури гуркоту від першої до останньої кліті чистової групи характеризує коефіцієнт передачі Кt

Як видно з рисунків, коефіцієнт Кt збільшується з підвищенням швидкості прокатки і товщини підкату і навпаки зменшується із збільшенням температури підкату. Із збільшенням товщини смуги з 0,8 до 1,1 мм Кt падає, а на товщині 1,4 мм зростає. При температурі підкату 900 °С і високій швидкості прокатки (15-20 м/с) Кt збільшується до 1,0-1,15. При цьому температура кінця прокатки стає більше температури підкату.
Зниження температурного клину по довжині готової смуги можна досягти двома шляхами. Перший шлях полягає в усуненні температурного клину підкату на вході в першу чистову кліть.чистову кліть. Другий - прокатка з компенсуючим прискоренням. Значення прискорень y залежать від усіх основних параметрів прокатки

Hп , tп - товщина і температура підкату; де
hk ,Vk - товщина і швидкість прокатки смуги.
Встановили. Що компенсуюче прискорення змінюється в межах 0,005-0,6 м/с?. Чим вище швидкість прокатки і товщина смуги, менше температура і товщина підкату, тим вище величина компенсуючого прискорення прокатки.
Для опису залежності температури кінця пркатки tк, температурних показників Кt і КΔt і прискорення ay були побудовані моделі виду

где Кt , КΔt – де коефіцієнти передачі чистової групи клітей по температурі підкату і перепаду температур по довжині смуги відповідно..
Залежності tк , Кt, КΔt прийняли у виді

Залежність ay прийняли у виді

звідки

де A0 , A1 , A2 ... - коефіцієнти моделі.
Отримані коефіцієнти для 6-клітьової і 7-клітьової чистових груп ШСГП приведені в таблиці.
Значення коефіцієнтів для залежностей tк, КΔt, aу
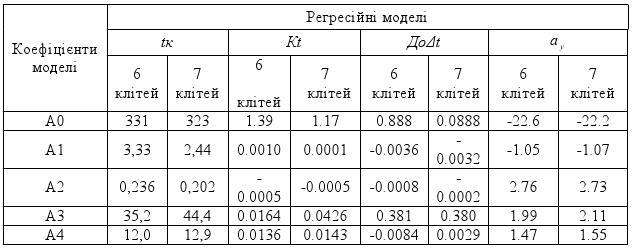
Основне завдання при розробці режиму обтискань - визначення оптимальних значень t товщини hп і температури п підкату, розподілів відносних обтискань по чистових клітях, а також швидкості прокатки vk , що забезпечують задані завантаження робочих клітей по силі P, моменту прокатки M і температури кінця прокатки tk .
Температура кінця прокатки, що визначає якість металу, має бути в діапазоні 860- 900 °С. Якщо tk нижче за цей діапазон, то гарячекатані смуги мають вищі прочностные і низькі пластичні характеристики, не відповідні механічним характеристикам холоднокатаних смуг, що відпалюють.
Температура кінця прокатки tk найбільшою мірою залежить від температури підкату t п і швидкості прокатки. У меншій мірі k залежить від перерозподілу обтискань по чистових клітях. Розрахунки показали, що збільшенням обтискань в останніх клітях можна збільшити tk на 15-20 °С. При цьому значно збільшується сила прокатки в останніх клітях, що затруднює роботу систем регулювання товщини, поперечної разнотолщинности і площинної смуги. t
Температура підкату на виході з останньої чорнової кліті широкосмугового стану залежно від товщини складає 1100-1150 °С. На вході до чистової групи клітей - біля 1070- 1100 °С. У зв'язку з тим, що на проміжному рольгангу підкат знаходиться протягом 2- 4 мін, підігріти його практично неможливо. Проте можна зменшити втрату температури на декілька десятків градусів шляхом екранування проміжного рольганга, сверткой його в рулон на установці типу "койл-бокс". Основний ефект від цих заходів - зниження температурного клину на підкаті.
При виробництві смуг на ливарно-прокатних модулях (ЛПМ) непреривноліті сляби завтовшки 50-70 мм підігрівають в прохідній нагрівальній печі до температури 1100-1150 °С. Якщо на виході з машини безперервного розливання слябів встановлені обтискові кліті, то розкат завтовшки 20-40 мм змотують в рулон в буферній печі, що підігріває. Таким чином, температура підкату на усіх смугових станах знаходиться в межі 1000-1150 °С. Найвищу температуру мають підкати завтовшки 50-70 мм.
Найбільш ефективний вплив на температуру смуги швидкості прокатки. Проте процес заповнення чистової групи клітей смугою (прокаткаа переднього кінця) не можна забезпечити за умовами захоплення валками, транспортування по рольгангу, що відводить, і заправки переднього кінця смуги в моталки на швидкості вище 10-11 м/с. Цей рівень швидкості при тонких (10-20 мм) підкатах найчастіше не забезпечують необхідну температуру кінця прокатки смуг завтовшки 0,8-1,5 мм.
Так, значення коефіцієнта К?t для особливо тонких смуг завтовшки 0,6-1,0 мм при швидкості прокатки 10 м/с складає в середньому 0,2. Тому підвищення температури підкату завтовшки 10-20 мм на 100 °С збільшує температуру кінця прокатки лише на 10-25 °С.
Із збільшенням товщини підкату до 40-60 мм і зменшенням числа робочих клітей з 7 до 6 або до 5 навіть при температурі підкату 1000 °С забезпечується необхідна температура кінця прокатки. При цьому різко зростає навантаження клітей при швидкості проктки 20 м/с (для смуг шириною 1000 мм сила прокатки зростає до 50 МН, момент - до 4,3 МНм, потужності - до 27 МВт).
Встановлено, що прокатка переднього кінця смуги завтовшки 0,6 мм на швидкості 10 м/с не забезпечує необхідну температуру кінця прокатки при товщині підкатів 10, 20 і 30 мм і при числі клітей 5, 6 і 7. Найбільша температура 833 °С отримана при прокатці смуги з підкату завтовшки 20 мм в п'ятиклітьовій чистовій групі. Сила прокатки по клітях склала 26-32 МН, момент - до 1,2 МНм, потужність - до 12 МВт. Підвищення температури підкату до 1100°С забезпечує необхідну температуру кінця прокатки і дещо знижує силові навантаження. При прокатці смуг завтовшки 0,6 мм в 6-7 клітьових чистових групах клітей температура складає 670-780 °С при швидкості 10 м/с і 840-930°С при швидкості 20 м/с.
Після заправки смуги в моталку чистову групу клітей розганяють. Якщо температура переднього кінця відповідає потрібною, то прискорення забезпечує компенсацію температурного клину. Якщо температура нижча за потрібну, то чистову групу прискорюють до швидкості прокатки, що забезпечує необхідну температуру. В цьому випадку з метою зменшення довжини смуги з низькою температурою швидкість прокатки підвищують з максимальним прискоренням (0,5-2 м/с?), а потім за наявності температурного клину підкату прискорення знижують для його компенсації.
Високі швидкості мало впливають на силові умови прокатки. У перших чистових клітях сила і момент прокатки підвищуються, а в наступних знижуються. Потужність прокатки в перших клітях збільшується пропорційно швидкості, а в останніх змінюється мало ( ± 10 %). При прокатці смуг завтовшки 0,6-0,8 мм шириною 1000 мм із сталі Ст3сп з відносно тонкого підкату (10-30 мм) сила, момент і потужність прокатки на передньому кінці смуги складає в п'ятиклітьовій групі 28-32 МН; 0,3-1,75МНм і 3,8-26 МВт відповідно; на задньому кінці з нижчою температурою підкату 20-45 МН; 0,2-4 МНм і 9-27 МВт відповідно. У 6 і 7 клітьових групах клітей рівень енергосилових параметрів в перших клітях знижується, а в останніх збільшується за рахунок зниження температури. При використанні підкату завтовшки 40-60 мм рівень енергосилових параметрів прокатки в 6 і 7 клітьових групах збільшується. Особливо момент прокатки в першій чистовій кліті, де обтискання досягає до 63%.
З приведеного вище аналізу виходить, що прокатка особливо тонких смуг шириною 1000 мм з необхідною температурою кінця прокатки можна реалізувати в потужних чистових клітях, що забезпечують силу прокатки до 40 МН, момент прокатки (у перших клітях) - до 3,5 МНм, швидкість прокатки 20 м/с і більше, прискорення - до 2 м/с2, потужність двигунів до 25 МВт.
ВИСНОВКИ
На підставі результатів дослідження процесу прокатки особливо тонких смуг встановили:
Робочі кліті широкосмугових станів різних типів повинні забезпечувати високі значення енергосилових і деформаційних параметрів прокатки (для смуг шириною 1000 мм сила до 40МН; момент до 3 МНм, швидкість понад 20 м/с, потужність до 25 МВт).
Прокатка повинна відбуватися за мінімальне число обтискань на максимально високій швидкості.
Для підвищення температури металу і розвантаження клітей в перших проходах довгий підкат завтовшки 10-20 мм доцільно перед прокаткою змотувати в рулон. Підкат завтовшки 30-40мм слід заздалегідь обтискати і змотувати в рулон, а завтовшки 50 мм і більше обтискати і змотувати в рулон послідовно двічі.
ЛІТЕРАТУРА
1.Дубина О. В. Виробництво надтонких гарячекатаних, у тому числі і оцинкованих смуг і листів з метою часткової заміни холоднокатаного листа на внутрішньому ринку України / О. В. Дубина, Ю.В. Коновалів // Сучасні проблеми металургії, том 5, с. 78-86.
2.Условия виробництва особотонкой гарячекатаної смугової сталі на комбінаті Запорожсталь" / А.И.Молчанов, С. П. Солтан, В. П. Яланский [та ін.] // Металургійна і гірничорудна промисловість. - 2002. -№ 10. - С. 11-14.
3.Разработка технології виробництва гарячекатаних смуг завтовшки 1,5 мм методом прямого транзитного плющення на станах слябинг-НТЛС 1680 / В. Т. Тилик, О. Н. Шахно, А.Ю. Путноки [та ін.] // Металургійна і гірничорудна промисловість. - 2002. - №10. - С. 84- 87.
4.Освоение технології виробництва тонких смуг і гнутих профілів / В. А. Сацкий, А.Ю. Путноки В. Т. Тилик [та ін.] // Сталь. - 2003. -№10.-С. С. 33-37.
5.Программное забезпечення проектування технології плющення / А.Л. Остапенко, Э.Е. Бейгельзимер, Н.В. Миненко [та ін.] // Сталь. - 2006.- №8. - С. 56-59.
Руденко Е.А.-доктор техн. наук, проф. ДонНТУ;
Курдюкова Л.А. – научн. сотр. ДонНТУ;
Тимошенко Н.В. – студент ДонНТУ.