Timoshenko Nina

Faculty Physical-Metallurgical
Department of treatment of metals pressure
Speciality: treatment of metals pressure
Theme of final work:Research of pearameters of hot rolling of especially thin stripes
Scientific leader: professor Yevgeny Rudenko
RESEARCH OF PARAMETERS OF HOT ROLLING OF ESPECIALLY THIN STRIPES
Presently in Japan, USA, Mexico, Spain the hot rolling of stripes is mastered in a 0,8-1 mm thick, practically not yieldings on exactness and mechanical properties to the холоднокатаному metal. The forecast production of hot-rolled especially-thin strips volumes annually increase on 8,3 % in the USA, 6,7% in ЕС and 6,6% in Japan [ 1 ].
Substituting folias by hot-rolled, the prime price of which below, at least, on 20 dollars of the USA on the ton of rent, and also tendency of price advance on a kholodnokatany sheet stipulate expediency mastering of production of especially thin hot-rolled sheet in Ukraine. The production of hot-rolled strips is presently mastered in a 1,5 mm thick on a figure 1700 ОАО of "МарМК" the name of Ilich and 1680 combine of "Zaporozhstal'". Terms of rolling of especially thin hot-rolled strip a 1,5 mm on a figure 1680 characterized by the subzero temperature of end of rolling (770-810оС), not providing required mechanical properties of hot-rolled strips [2,3].Economic and technological feasibilities of receipt on these figures of stripes in a less than 1,5 mm thick absent.
Especially thin stripes from low-carbon steel can have wide turn-downs of mechanical properties. Getting the required mechanical properties is possible, realizing the concrete deformation and temperature modes of rolling of stripes in the clean group of cages of shirokopolosnogo figure, and also by the correct choice of thickness and temperature of podkat. Only certain complex of entry parameters of podkat, wringing out on clean cages and speed of end of rolling provides the required temperature of end of rolling and mechanical descriptions required as a result became.
For the receipt of plastic steel with subzero temporal resistance (by tensile strength) and limit of fluidity, and also with the high relative lengthening it is necessary to hold the temperature of end of rolling (after the last clean cage) within the limits of 860 - 900 оС, and temperature of winding up of stripe in a roll - 680-740 оС. There is complete rekristallizaciya of austenite in this range of temperatures of end of rolling. Below in the range of temperatures of 820- 860 оС in a metal the phase converting of austenite begins into ferritic-pearlitic mixture. Completion of deformation in this range conduces to growing of grain, increase of durability and diminishing of plastic descriptions shallow became.
If a temperature of end of rolling is below 820 оС, then the process of deformation flows in the diphasic area of structure became. In this case a stripe after rolling has a fine-grained structure, high прочностные and subzero plastic properties.
On the clean cages of shirokopolosnogo figure a temperature diminishes. In the first cages deformation of steel is carried out in an austenitic range, and in the last - mostly in a diphasic феррито-перлитной area. For the receipt of especially thin hot-rolled strips, being high plastic characteristics, corresponding to the холоднокатаным stripes after annealing, it is necessary to provide the temperature of end of rolling higher 860 оС.
In this connection development of the effective technological modes of the hot rolling of plastic especially thin stripes is based on the different variants of technical and technological decisions on realization of the requirements indicated higher.
The purpose of work is determination of parameters of the hot rolling of especially thin stripes in five - seven cage clean groups necessary for providing required quality of metal .
Pursuant to temperature balance of stripe at rolling in the clean group of cages the temperature of end of rolling of tк depends on the temperature of podkat before the first clean cage of tп, defervescences by a radiation and convection in intercage intervals, defervescences because of contact of hot metal with the cold felling in the hearths of deformation of cages and increase of temperature due to work of deformation and forces of friction in the hearths of deformation of cages. In this balance, promoting a temperature is possible by the increase of work of deformation and decline of all making losses. Temperature of podkata of tп directly and simply influences on the temperature of the prepared stripe on an exit from the clean group of tк. Consequently, at other permanent parameters for the increase of tк it is necessary to increase tп. However the range of increase of tп is limited. Temperature of подката, got by rolling of thick слябов in the draft group of cages of широкополосного figure and on an exit 1000-1100 оС makes from a warm up stove of the casting-rental module. Promoting a bottom limit is possible by the increase of wringing out in the last draft cages, screening of podkat or his heating before the clean group of cages. The possible increase of temperature makes only 20-50 0С, that allows to promote only on 7-12 0С. Consequently, the only effective way of increase of tк is a rev-up of rolling. Thus work of deformation increases and all articles of defervescences grow short in balance.
Research of the temperature-speed, energypower and deformation modes of rolling of especially thin stripes was executed in five, six, and seven cage clean groups of cages of широкополосного figure with the use of mathematical models and package of softwares "Универсал", worked out in НПО of "Доникс" [ 4 ].
Research showed that to realize rolling of especially thin stripes possibly only with the high relative wringing out in the first clean cages (50-65%), depending on the number of clean cages and thickness of podkata. At such wringing out the moment of rolling of M arrives at 3 and more МНм, and force of rolling of Р 30 МН and more. Transmission of such moments the necks of working rollers can by a diameter a 900 mm and more. In this connection diameters of working rollers first two clean cages chose equal 900-950 мм. In next clean cages the moments of rolling diminish sharply, therefore the diameters of rollers diminished on the pair of cages to 750 мм. Diameters diminished also with the purpose of decline of force of rolling. So, for a fivecage clean group the diameters of working rollers of the first and second cage are accepted a 900 mm, third and fourth a 850 mm and пятой- 800 мм. In six - and seven cage groups the diameters of the last cages chose 800-750 мм.
At the diameters of supporting rollers in two times large the rolling knots of clean cages provide force of rolling to 40 МН and more. For providing of high speeds of rolling (20 m/ with and more), power of electric motors must be no less than 20 МВт.
The Temperature-speed modes designed for terms rolling of especially thin stripes from podkat in a 10-60 mm thick, breadthways a 1000 mm, long a 50 m from steel of Ст3сп. The temperature of podkat was accepted by equal 900, 1000 and 1100 С. Speed of rolling a 10-20 m/ varied in a range p. At every level of speed (10, 15, 20 m/of с) determined the acceleration of clean group of cages, which provides stability temperature of stripe on length (indemnification of temperature wedge of podkat, appearing in times of motion of his back-end to the first cage).
Such temperature wedge on podkat in a 50 mm thick, long a 50 m, at rolling of stripe in a 0,8 mm thick at a speed of a 10 m/with 200 0С arrives at.
According to plan of research подкат of every thickness with a temperature 900, 1000 and 1100 0С rolled on stripes in 0,8 thick; 1,1 and a 1,4 mm on speed 10, 15 and a 20 m/with in five, six and sevencage groups of cages.
With the use of the worked out program of calculation the temperatures of front tп and tк back-end of roll determined on an entrance and output of every cage, and also value leveler on length of the prepared stripe of acceleration halloo and temperature of ends of roll at rolling with an acceleration in every cage of tзу.
Calculations showed that the optimal range of temperature of end of rolling of 860-890 0С at rolling of especially thin stripes was provided by the mode of rolling from podkat in a 50 mm thick on speed a 10 m/with as in six so in a sevencage clean group, and also from подката in a 20- 40 mm thick in a fivecage clean group.
It should be noted that speed of rolling a 10 m/with is maximal on a condition priming of figure, transporting of stripe on taking рольгангу and priming in a coiler. She below (8-9 m/of с) in practice. Temperature of end of rolling of stripes in a 0,8 mm thick from подката in a 10 mm thick on speed a 10 m/with in 5,6 and makes a 7-cage clean group according to 786, 719 and 674 0С. At speed of rolling a 15 m/with a temperature rises on 70-80 0С, and at a 20 m/with yet on 40-50 0С and makes according to 904, 842 and 786 0С.
The analysis of results of calculations showed that for providing of the set temperature of stripe on an exit from a clean group can be attained only by the rev-up of rolling. What higher acceleration, the greater part of length of stripe will have the set temperature. Usually an acceleration is begun after priming of front end of stripe in a coiler. Stripes in a 0,8-1,4 mm thick from подката in a 10 mm thick it is necessary to take for a ride on speed a 20 m/with; from подката there is a 30 mm - on speed a 15 m/with, and from подката in a 50-60 mm thick - on speed a 10 m/p.
Set that the temperature of end of rolling with the increase of number of cages diminished on 60-90 0С at the increase of thickness of podkat from 10 a to 60 mm accordingly.
The temperature wedge of podkat diminishes on clean cages in 2-6 times (there is a 10 m/of с) at speed of rolling with diminishing of thickness of подката..
The change of transmitivity of temperature wedge (smoothing of temperature on length of
stripe) ToΔt was expected as a relation
where is diminishing of temperature on length of the prepared stripe, mm;
Δtn- it is diminishing of temperature on length of подката, мм.
A value To&Deltat changes in a range 0,14-0,5 for the thickness of stripe a 0,8-1,4 mm accordingly. With the increase of thickness of подката of value To&Deltat diminish, and with the increase of temperature of подката increases.
Speed of rolling ambiguously influences on a coefficient To Δt . At rolling of stripes in a 0,8 mm thick with the increase of speed of rolling To Δt diminishes, and at rolling of stripes in 1,1 thick and a 1,4 mm diminishes in a 6-cage clean group, and 7-cage - increases.
The decline of temperature of roll from the first to the last cage clean group is characterized by the transmitivity of Кt

As be obvious from pictures, the coefficient of Кt increases with the rev-up of rolling and thickness of подката and vice versa diminishes with the increase of temperature of подката. With the increase of thickness of stripe from 0,8 a to 1,1 mm of Кt falls, and on a thickness a 1,4 mm increases. At the temperature of podkat of 900 0С and high-rate of rolling (15-20 m/of с) of Кt increases to 1,0-1,15. Thus the temperature of end of rolling becomes more temperature of podkat.
Decline of temperature wedge on length of the prepared stripe it is possible to attain in two ways. The first way consists in the removal of temperature wedge of podkat on included in the first clean cage. Second is rolling with a compensating acceleration. The values of accelerations depend on all basic parameters of rolling

Hn,Tn - where is a thickness and temperature of podkat;;
hk ,Vk - it is a thickness and speed of rolling of stripe.
Set. That a compensating acceleration changes within the limits of a 0,005-0,6 m/of с2. What higher speed of rolling and thickness of stripe, less than temperature and thickness of podkat, the higher size of compensating acceleration of rolling.
For description of dependence of temperature of end of rolling of tк, temperature indexes of Кt and ToΔt and accelerations were built to the model of kind

где Кt , КΔt – are transmitivities of clean group of cages on to the temperature of подката and overfall of temperatures on length of stripe accordingly.
Dependences tк , К , КΔt accepted in a kind

Dependence was accepted in a kind

from where

A0 , A1 , A2 ... - where are model coefficients..
Got coefficients for a 6-cage and 7-cage clean groups of ШСГП resulted in a table.
tк Values of coefficients for dependences , , Кt , КΔt, aу
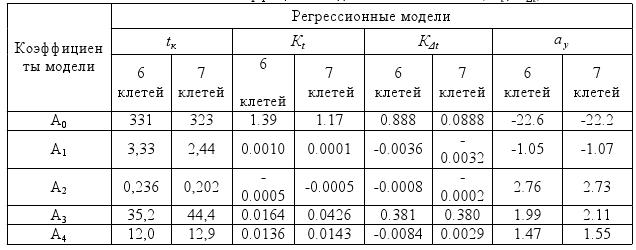
A basic task at development of the mode of wringing out is determinations of optimal values of thickness and temperature of podkat, distributions of the relative wringing out on clean cages, and also speed of rolling , providing the set loading of working cages on force of P, moment of rolling of M and temperatures of end of rolling .
A temperature of end of rolling, qualificatory quality of metal, must be in the range of 860- 900 0С. If below than this range, then hot-rolled strips have higher прочностные and subzero plastic descriptions, falling short of to mechanical descriptions of холоднокатаных anneal stripes.
The temperature of end of rolling in a most degree depends on the temperature of podkat and speed of rolling. In less degree depends on the redistribution of wringing out on clean cages. Calculations showed that in the last cages it is possible the increase of wringing out to increase on 15-20 0С. Thus considerably force of rolling increases in the last cages, that hampers work of the systems of adjusting of thickness, transversal разнотолщинности and flatness of stripe.
The temperature of podkat on an exit from the last draft cage of широкополосного figure depending on a thickness makes 1100-1150 0С. On included in the clean group of cages - near 1070-1100 0С. In connection with that on intermediate рольганге podkat is during 2-4 mines, to warm it is practically impossible up him. However it is possible to decrease the loss of temperature on a few ten of degrees by screening of intermediate рольганга, сверткой of him in a roll on setting of type "coil-dox". A basic effect from these measures is a decline of temperature wedge on podkat.
At the production of stripes on the casting-rental modules (ЛПМ) непрерывнолитые слябы in a 50-70 mm thick warm up in a communicating heater stove to the temperature of 1100-1150 0С. If on an exit from the machine of continuous teem of слябов обжимные cages are set, then a roll in a 20-40 mm thick is winded up in a roll in a buffer warm up stove. Thus, a temperature of подката on all полосовых figures is in the limit of 1000-1150 0С. The highest temperature is had podkat in 50-70 мм. thick
Influence on the temperature of stripe of speed of rolling is most effective. However process of filling of clean group of cages it is impossible to provide a stripe (rolling of front end) on the terms of capture felling, portages on taking рольгангу and priming of front end of stripe in coilers on speed higher a 10-11 m/p. This level of speed at thin (10-20 mm) подкатах mostly is not provided the required temperature of end of rolling of stripes in 0,8-1,5 мм. thick
So, values of coefficient To?t for especially thin stripes in a 0,6-1,0 mm thick at speed of rolling a 10 m/with averages 0,2. Therefore the increase of temperature ofpodkat in a 10-20 mm thick on 100 0С increases the temperature of end of rolling only on 10-25 0С.
With the increase of thickness of podkat a to 40-60 mm and diminishing of number of working cages from 7 to 6 or to 5 even at the temperature of podkat of 1000 0С the required temperature of end of rolling is provided. Thus sharply loading of cages increases at speed of rolling a 20 m/with (for stripes breadthways a 1000 mm force of rolling increases to 50 МН, moment - to 4,3 МНм, powers - to 27 МВт).
It is set. that rolling of front end of stripe in a 0,6 mm thick on speed a 10 m/with does not provide the required temperature of end of rolling at the thicknesses of podkat 10, 20 and a 30 mm and at the number of cages 5, 6 and 7. The most temperature of 833 0С is got at rolling of stripe from podkat in a 20 mm thick in a fivecage clean group. Force of rolling on cages made 26-32 МН, moment - to 1,2 МНм, power - to 12 МВт. The increase of temperature of podkat to 1100 0С provides the required temperature of end of rolling and some reduces the power loading. At rolling of stripes in a 0,6 mm thick in 6-7 cage clean groups of cages a temperature makes 670-780 0С at speed a 10 m/with and 840-9300С at speed a 20 m/p.
After priming of stripe in a coiler the clean group of cages is dispersed. If the temperature of front end corresponds required, then an acceleration provides indemnification of temperature wedge. If a temperature below than required, then a clean group is accelerated to speed of rolling, providing the required temperature. In this case with the purpose of diminishing of length of stripe with a subzero temperature speed of rolling is promoted with a maximal acceleration (0,5-2 m/ of с2), and then at presence of temperature wedge of podkat an acceleration is reduced for his indemnification.
The high-rate small influence on the power terms of rolling. In the first clean cages force and moment of rolling rise, and in subsequent go down. Rolling in the first cages increased power proportionally speeds, and in the last changes small (10 %). At rolling of stripes in a 0,6-0,8 mm thick breadthways a 1000 mm from steel of Ст3сп from in relation to thin podkata (10-30 mm) force, a moment and power of rolling front-end stripe make 28-32 МН in a fivecage group; 0,3- 1,75МНм and 3,8-26 МВт accordingly; on a back-end with more subzero temperature of подката 20-45 МН; 0,2-4 МНм and 9-27 МВт accordingly. In 6 and 7 cage groups of cages the level of energypower parameters goes down in the first cages, and in the last increases due to the decline of temperature. At the use of подката in a 40-60 mm thick level of energypower parameters of rolling in 6 and 7 cage groups increases. Especially moment of rolling in the first clean cage, where wringing out arrives at to 63%.
It ensues from the analysis given above, that rolling of especially thin stripes breadthways a 1000 mm with the required temperature of end of rolling it is possible to realize in powerful clean cages, providing force of rolling to 40 МН, moment of rolling (in the first cages) - to 3,5 МНм, speed of rolling a 20 m/with and more, an acceleration is a to 2 m/of с2, power of engines to 25 МВт.
CONCLUSIONS
On the basis of results of research of process of rolling of especially thin stripes set:
The working cages of широкополосных figures of different types must provide the high values of energypower and deformation parameters of rolling (for the stripes of open space noy a 1000 mm force to 40МН; moment to 3 МНм, speed an over 20 m/with, power to 25 МВт).
Rolling must produced for the minimum number of wringing out on maximally high- rate.
For the increase of temperature of metal and unloading of cages in the first passage-ways long подкат in a 10-20 mm thick it is expedient before rolling to wind up in a roll. Подкат in thick 30-40мм it is necessary preliminary to wring out and wind up in a roll, and in a 50 mm thick and more to wring out and wind up in a roll consistently two times.
ЛИТЕРАТУРА
1.Дубина О.В. Производство сверхтонких горячекатаных, в том числе и оцинкованных полос и листов с целью частичной замены холоднокатаного листа на внутреннем рынке Украины / О.В. Дубина, Ю.В. Коновалов // Сучасні проблеми металургії, том 5, с. 78-86.
2.Условия производства особотонкой горячекатаной полосовой стали на комбинате Запорожсталь» / А.И.Молчанов, С.П. Солтан, В.П. Яланский [и др.] // Металлургическая и горнорудная промышленность. – 2002. –№ 10. -С. 11-14.
3.Разработка технологии производства горячекатаных полос толщиной 1,5 мм методом прямой транзитной прокатки на станах слябинг-НТЛС 1680 / В.Т. Тилик, О.Н. Шахно, А.Ю. Путноки [и др.] / / Металлургическая и горнорудная промышленность. – 2002. – №10. -С. 84- 87.
4.Освоение технологии производства тонких полос и гнутых профилей / В.А. Сацкий, А.Ю. Путноки, В.Т. Тилик [и др.] // Сталь. -2003. -№10.-С. С. 33-37.
5.Программное обеспечение проектирования технологии прокатки / А.Л. Остапенко, Э.Е. Бейгельзимер, Н.В. Миненко [и др.] // Сталь. – 2006.- №8. – С. 56-59.
Руденко Е.А.-доктор техн. наук, проф. ДонНТУ;
Курдюкова Л.А. – научн. сотр. ДонНТУ;
Тимошенко Н.В. – студент ДонНТУ.