Abstract
Maintenance
- Introduction
- 1. The rocking mechanism. Production requirements.
- 2. Roller-screw pair.
- 3. Review of researches on a subject
- Conclusion
- References
Introduction
Work of the master is devoted to research of possibility of improvement of quality of regulation by increasing accuracy of working of harmonious entrance influence by the electric drive of the rocking mechanism of a crystallizer of the machine of continuous molding of preparations (MCMP).
The urgency of a subject consists in research of possibility of improvement of quality of work of installation that in turn can lead to improvement of quality of produced production.
The scientific importance of work consists in research of methods of management of system by the crystallizer electric drive as drive operated on speed and situation, and introduction of the roller-screw mechanism which will allow realizing effective management of technological process. Researches concern sections of the theory of automatic control, control systems of the electric drive and mathematical modeling of electromechanical systems.
Practical value of results of work consists in possibility of use of the received results for introduction on technological lines of metallurgical branch for the purpose of increase of efficiency of productions.
1. The rocking mechanism. Production requirements.
Modern MCMP are equipped with hydraulic system of a drive of the rocking mechanism of a crystallizer. Wide use of hydraulic rocking mechanisms became possible thanks to rapid development of systems of automatic control in the 80-90th years of the XX century and their input on production Wednesday. It is considered to be the most important functional element of the car of continuous molding of preparations a crystallizer. Its work substantially defines quality of preparation. The crystallizer carries out function of reception of the liquid metal getting to it from an intermediate ladle, and also transfers of a part of liquid steel to a firm condition by means of heat removal by cooling water. During stay of metal in a crystallizer from preparation it is taken away from 10 % to 30 % of all heat which is accumulated by metal. Thus formed crust should on an exit from a crystallizer maintain ferrostatic of a liquid phase. Besides, the internal form of a crystallizer defines a preparation form.
At a rupture of a firm crust owing to sticking its part located near a mirror of liquid steel, is linked to a wall of a crystallizer and separates from a crust moving down. To the place of the formed gap liquid metal which when hardening doesn't manage to form any more a crust of sufficient thickness and durability gets. Turning-out connection is rather fragile and can collapse both at ingot movement in a crystallizer and at an exit from it.
Minimization of the phenomenon of sticking of a firm crust manage to be reached in that case when the effort of a friction between a surface of preparation and walls of a crystallizer appears below a certain critical level which is defined depending on durability of a crust.
In the analysis of process of a friction between preparation and a crystallizer it is established that level of size of force of a friction depends on a number of factors, including from brand of spilled steel. This dependence can be presented through factor of a friction in function from the content of carbon.
Other things being equal level of force of a friction when molding steel, containing less than 0,06 % With, turns out very high. The minimum force of a friction turns out at the content of carbon within 0,08 - 0,12 %. At further increase of the content of carbon in steel level of forces of a friction again raises a little. The content of silicon and manganese in steel also influences level of forces of a friction. So, silicon strengthens a friction, and manganese reduces it.
For reduction of forces of a friction, in the course of a continuous pouring of steel technological greasing has great value. Greasing reduces effort of resistance to a preparation pulling in 1,5-2,5 times. The method of a supply and uniformity of supply of greasing in a crystallizer thus matters. Force of a friction also depends on size of an active surface of a friction, thickness of a film of greasing between components of a friction and from viscosity of lubricant.
Decrease in probability of sticking of a crust to walls of a crystallizer is reached by giving to a crystallizer of back and forth motions with a certain frequency and amplitude. Thus in a gap between a crust and a crystallizer the greasing substance moves: slag-forming mix or liquid oil. At temperatures of a continuous pouring a slag-forming mix in a place of contact to metal melting, and oil burns down. The liquid mix or the remains of products of combustion of oil fill a gap between a crust of an ingot and a crystallizer wall that reduces size of forces of a friction.
The technology of a pouring of metal with use of rocking (back and forth motions) of a crystallizer is offered Z.Yungkhansom (Germany) in the early thirties last century. However the main effect from a rocking of a crystallizer was reached only in the 50th years of the last century at the expense of a choice of such parameters of an oscillation at which during certain periods of time a crystallizer, moving in the same direction, as preparation, overtakes it. This interval of time is called as the period of a negative undressing of an ingot (negative strip time) or advancing time.
Other important step of updating of parameters of a rocking was transition to the sinusoidal law of movement of a crystallizer. It is considered that for the first time in world practice the sinusoidal law of fluctuations applied on two Russian MCMP of Novolipetsk Steel to a pouring of slabs in 1959. The scheme of implementation of the sinusoidal law of a rocking of a crystallizer is presented in drawing 3.40. For implementation of this law of a rocking of a crystallizer the electric drive is used.
Up to the last 10-15 years the sinusoidal mode of fluctuations was considered as the standard mode which is applying practically on all MCMP. This results from the fact that its model is rather simple in realization and has advantages of the smaller moments of inertia and smaller breakthroughs of acceleration (size of change of acceleration in time).
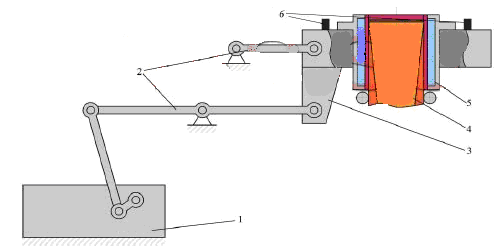
Drawing 1 – the Scheme of an electromechanical drive of the rocking mechanism of a crystallizer (sinusoidal movements): 1–drive of the rocking mechanism; 2–system of levers; 3– rocking table of a crystallizer; 4–unstoppable preparation; 5–crystallizer; 6–installation sites of accelerometers for control of parameters of a rocking
Recently the main share of new and modernized MCMP is equipped with crystallizers with hydraulic actuators which allow carrying out not sinusoidal mode rocking (drawing 1). It is considered that not sinusoidal modes of a rocking allow to increase essentially speed of a pouring and to improve quality of a surface and upper layers of preparation.
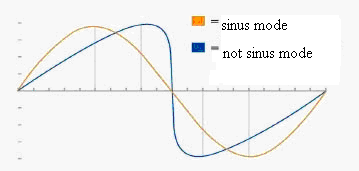
Drawing 2 Schedules of change of speed of movement of a crystallizer for the sinusoidal and not sinusoidal law with frequency of a cycle of 2 Hz
Important parameter of optimization of the law of a rocking of a crystallizer is depth of penetration of traces of a rocking which can fluctuate from the several tenth shares millimeters to 1,5-2,0 mm and more. It is represented very important factor already because in a crystallizer the crust is fragile and rather thin. Therefore, rocking traces reduce its durability that can lead to cross-section cracks and breaks even more. Usually maximum depth of penetration of traces of a rocking is observed in the field of preparation corners that is caused by lower temperature of liquid steel on these sites. The smallest depth of traces of a rocking is observed, as a rule, in the middle of a side that is especially well shown when molding slabs
Depth of traces of a rocking depends on a way of a pouring: at low frequency of rocking (<130 cycles/mines) the pouring with a slag-forming mix (SFM) leads to formation of deeper labels, than when molding by an open stream. At increase in frequency of rocking this ratio practically doesn't change. In other important parameter influencing depth of traces of a rocking, speed of a pouring is: higher speed of a pouring leads to education less rocking scars. Therefore, if it is required to minimize depth of penetration of traces of a rocking, first of all, it is necessary to increase speed of a pouring to the level allowed by other technological parameters.
At the set speed of a pouring and scope of rocking of a crystallizer depth of traces of a rocking decreases at increase of frequency of rocking. In other words, depth of traces of a rocking decreases with reduction of size of an interval between rocking traces. Optimum it is considered a mode of a pouring which other things being equal (MCMP type, brand of cast metal, cross-section section of preparation and its sizes, a cooling mode in a crystallizer, speed of a pulling of an ingot, etc.) in the best way meets requirements of stability of molding and quality of a surface of preparation, that is provides necessary time of an advancing at the maximum frequency and the minimum amplitude of a rocking of a crystallizer. Respectively and parameters of a rocking of a crystallizer (frequency and amplitude) in an optimum mode too are considered as the optimum.
2. Roller-screw pair.
Back and forth motion of the mechanism of a rocking can be realized on the basis of roller-screw gear use. The Roller-screw gear represents the mechanism of transformation of a rotary motion in forward, how it occurs in traditional transfers such as a ball-screw gear or to a trapezium carving. However unlike these devices, the roller-screw pair can maintain big loadings during thousand hours of operation in the most severe constraints. In this regard the roller-screw pair is ideally suited for responsible applications with a continuous operating mode.
The difference consists in how the roller running screw transfers efforts. Some carving spiral rollers are located round a carving shaft according to the planetary scheme that allows transforming a rotary motion of the electric motor to linear moving of a shaft or a nut. But, engineers went further, and, as though turned out the running screw on a wrong side (it is shown in the bottom drawing from below). Thus, the planetary mechanism of rollers rotates in the hollow cylinder with a carving. It provides possibility of high-quality consolidation of a smooth rod that isn't possible when using BSP.
The shaft of the electric motor is rigidly connected to carving shaft of a ball-screw gear. Owing to shaft rotation, the carriage being on a shaft starts to move is forward. The carriage, in turn, is fixed so that not to be turned. On end faces of the carriage loading is enclosed. For reduction of forces of a friction, between the carriage and carving shaft metal balls are started up to avoid a sliding friction.
Design shortcomings:
1) At carriage movement, the moment of the electric motor is transferred by means of contact of balls to carving shaft and the carriage. The less maximum loading and durability less than contact points. Example of the appendix of loading:
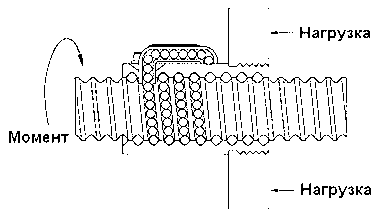
For comparison, we will give roller-screw pair of similar dimension:
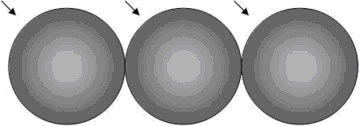
This drawing shows us that in similar dimensions, BSP and a roller-screw gear (RSG), contact points it is much more at the last. So much more loading ability and resource.
2) Lower efficiency and the maximum speed at ball-screw pair it is caused by the following factors:
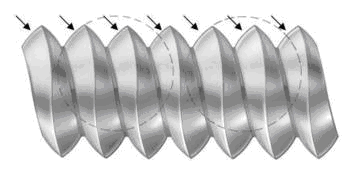
The more speed, the is more friction and wear of balls that reduces efficiency.
At speed of a shaft more than 1000 rpm arise strong impacts and vibrations of balls therefore, everything, even the most exact and expensive BSP aren't calculated on speeds over 2000 rpm.
The design of RGP is initially deprived of similar shortcomings. All rollers are rigidly fixed from each other and can't adjoin. Special cloves are applied to mechanical synchronization of rotation of each roller on the end of rollers that allows avoiding unnecessary slippage.
3. Review of researches on a subject
Researches in on studying of new methods of operation of the mechanism of a rocking of a crystallizer of the electric drive allow increasing efficiency and quality, to lower costs of repair. As a rule, researches are carried out for a design and parameters of concrete installation of some metallurgical enterprise on purpose to increase efficiency of installation or to modernize production.
As a basis for this work methods of the classical theory of management and in particular creation of systems of regulation by situation which were also repeatedly considered on chair of electrotechnical faculty are used.
3.1 The review of researches on a subject in Ukraine and in the world
Universities which have automatic equipment or electric drive chair, as a rule, prosecute subjects of automation of metallurgical production of the nearby enterprises. The scope of works is directed on modernization of control systems and is considered, as a rule, for application on the concrete technological line of some enterprise.
4. Result
At the beginning of work the block diagram of system of regulation of situation (Rice … was developed.). For simplification of synthesis of system, real integration that establishes connection between speed and situation was replaced with discrete integration on a method of trapezes:
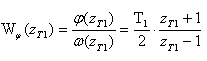
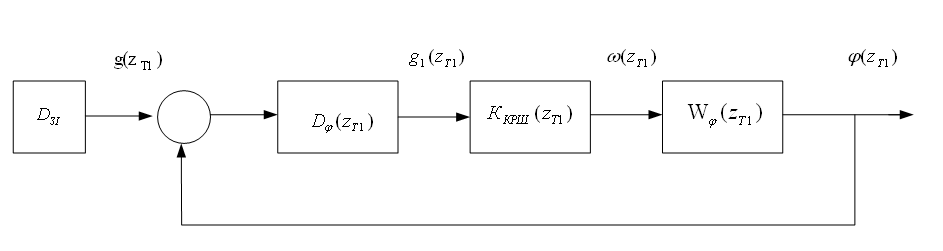
Drawing 3 - Settlement block diagram of a SRS.
The system is made with a linear regulator of situation which transfer function looks like .

where T - a constant of integration of opened SRS. Let's consider system where as an internal contour of SRS disposable integration of KRS is used. Let's define a constant of integration of opened SRS T which defines damping and a stock of firmness of digital SRS, with use of transfer function of the closed contour of situation:

Let's consider in more detail digital systems of regulation of speed. The settlement scheme repeated digital one time is provided by integrated SRS of speed on fig. 2.1. It includes two contours of regulation: current of an anchor and speed of the engine. SRC works with the period of quantization Т2 which coincides with the period of step-type behavior of VP, and SRS – with the period of quantization Т1 at what Т1 it is multiple Т2, i.e. Т1=kТ2 where k – the integer. Between regulators of speed and a current extrapolator Е of a zero order with fixing for period Т1 is established. Set-point device is presented to intensity by a linear part – an integrated element which forms the necessary law of change of speed on the basis of information on desirable acceleration Е. For convenience of a statement active resistance of an anchor chain, an engine constant with, and also factors of transfer of sensors of a current and speed are accepted equal to unit. It doesn't influence results of researches because the real system can be always brought by a respective choice of relative units to consider. Transfer function of the discrete sensor of speed looks like:
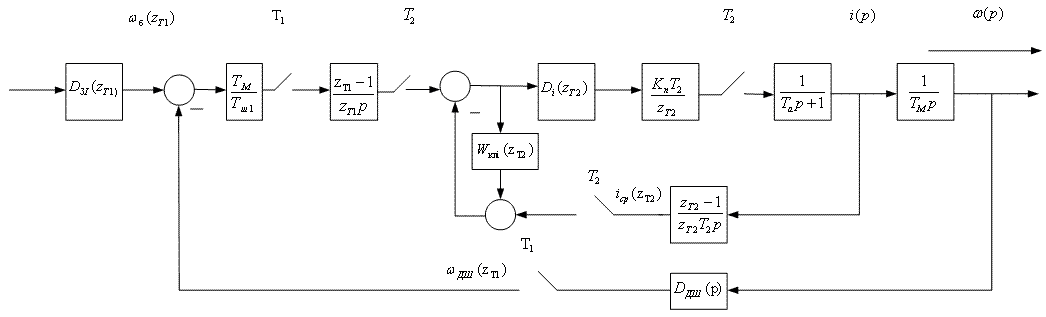
Drawing 4 - The settlement scheme of repeated digital integrated SPR of speed
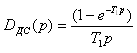
- in case of feedback use in an average for period Т1, value of speed;

- in case of feedback use on instant value of speed; Transfer function of a regulator of speed:

where Ts1 – a constant of integration of opened SRS. Transfer function of a regulator of a current looks like:
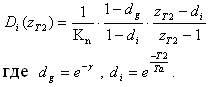
Transfer function of opened SRC looks like:

Transfer function of closed SRC looks like:

Transfer function of closed SRS looks like:
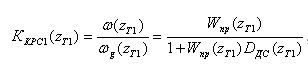
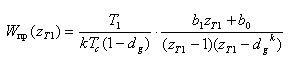
- transfer function of a direct part of SRS.
Conclusion
As entrances signal on a contour of regulation of situation the sinusoidal or not sinusoidal harmonious influence which quality of working off is supposed to be raised by realization on an entrance of system of the additional forcing influences which parameters it is necessary to define during further researches moves.
References
- А.Н. Смирнов, Развитие технологий и оборудования для непрерывной разливки в Украине / Смирнов А.Н. // Сборник научных трудов конференции. 50 лет непрерывной разливке стали в Украине. – Донецк: ДонНТУ. 2010. – С. 9-17.
- Brendzy J L, Bakshi I A, Samarasekara I V, Brimacombe J K 1993 Mouldstrand interaction in continuous casting of steel billets, part 2: Lubrication and oscillation mark formation. Ironmaking Steelmaking 20: 63-69.
- А.Ю. Цупрун, Системы диагностики процесса качания кристаллизатора машин непрерывного литья заготовок / Цупрун А.Ю., Кубкин Д.А., Антыкуз О.В., Колоколов А.В., Пильгаев В.М. // Сборник научных трудов конференции. 50 лет непрерывной разливке стали в Украине. – Донецк: ДонНТУ. 2010. – С. 247-253.
- Darle T, Mouchette A, Nadif M, Roscini M, Salvadori D 1993 Hydraulic oscillation of the CC slab mould at Soleac Florange: First industrial results, future development. Steelmaking Conference Proc. (Warrendale, PA: Iron & Steel Soc.) vol. 76, pp. 209-218.
- Еланский Г.Н. Оптимизация режимов работы кристаллизаторов МНЛЗ / Г.Н. Еланский, И.Ф. Гончаревич // Сталь. – 2006. - №10. – С. 18-21.
- Darle T. Hydraulic Oscillation of the CC Slab Mold at Sollac Florange: First Industrial Results, Future Developments / T. Darle, [et al] // Steelmaking Conference Proceedings. - 1993. – Warrendale: 1993. – P.209-218.
- Hydraulic drive technology for mold oscillation in continuous castings plant / Rexroth Bosh group
- Смиpнов А. Н. Некотоpые подходы к выбоpу pациональных паpаметpов качания кpисталлизатоpов МНЛЗ / А. Н. Смиpнов, О. В. Антыкуз, А. Ю. Цупpун, В. М. Пильгаев // Электрометаллургия. – 2008. - №5. – С. 22-30.
- Sahai Y., Emi T. Tundish Technology for Clean Steel Production. – New Jersey: World Scientific, 2008. – 316 p.
- Flow Dynamics and Inclusion Transport in Continuous Casting of Steel / B.G.Thomas, Q.Yuan, L.Zhang, S.P.Vanka // Proceedings of NSF Conference “Design, Service, and Manufacturing Grantees and Research” , Birmingham, Al, January 6-9, 2003. – University of Alabama: R.G.Reddy, ed., 2003. -P.2328 - 2362.
- Holdsworth B. Digital logic design / B. Holdsworth, C. Woods. – Prentice Hall, 2002. – 519 pp.
- Lala P. Principles of modern digital design / P. Lala. – Wiley, 2007. – 419 pp.
- Википедия [Электронный ресурс]. – Режим доступа: ru.wikipedia.org.
- Металлургический портал [Электронный ресурс]. – Режим доступа: uas.su/conferences/.
- Тематический портал[Электронный ресурс]. – Режим доступа: www.p-techno.ru/tehnologiya_roliko-vinto.