Реферат за темою випускної роботи
Зміст
- Вступ
- 1 Актуальність теми
- 2 Мета, задачі дослідження та заплановані результати
- 3 Технологический процесс непрерывной разливки стали
- 4 Огляд досліджень та розробок
- 4.1 Огляд міжнародних джерел
- 4.2 Огляд національних джерел
- 4.3 Огляд локальних джерел
- 5 Розробка автоматизованої системи управління процесом безперервного розливання сталі
- 6 Розробка структурної схеми електроприводу ТПМ
- 7 Моделювання електроприводу
- 7.1 Обгрунтування прийнятих допущень
- 7.2 Математична модель АД в осях
α, β, 0
- 7.3 Математична модель автономного інвертора
- 7.4 Розрахунок моменту навантаження
- 7.5 Результати моделювання
- 8 Розробка SCADA-системи машини безперервного розливання сталі
- Висновки
- Перелік посилань
Вступ
Підприємства чорної металургії України є одними з найбільших постачальників сортової заготовки і довгомірного прокату на світовий ринок, динаміка розвитку якого характеризується помітним підвищенням конкуренції і вимог до якості продукції [1].
Безперервне розливання сталі є одним з найважливіших технологічних етапів у виробництві металопродукції, оскільки вона забезпечує переклад стали з рідкого стану в твердий і надання їй певної геометричної форми. Крім цього умови охолодження і затвердіння стали під час безперервного розливання значною мірою обумовлюють високу якість металопродукції в порівнянні з консервативною системою розливання у злитки.
Використання безперервного розливання в сталеплавильному виробництві [2]:
1 Актуальність теми
Сучасні вимоги ринку металургійної продукції спрямовані на підвищення якості, збільшення виробництва і зниження витрат. У свою чергу ці вимоги викликають необхідність модернізації діючих та створення нових машин, що відрізняються високим ступенем автоматизації технологічних процесів, підвищеним коефіцієнтом корисної дії, зниженими витратами енергоресурсів, здатністю гнучко налаштовуватися на випуск продукції тієї якості, якої вимагає споживач.
Особливостями металургійних машин є: високі навантаження і важкі режими, агресивна навколишнє середу, безвідмовність роботи, легкодоступний і нетрудомісткий ремонт. Непланова зупинка машини в безперервному металургійному процесі викликає значні втрати через недоотриманої продукції, витрат на ремонт [3].
Актуальність даної тематики обумовлена використанням безперервного розливання в індустріально розвинених країнах і необхідністю запуску досить великої кількості машин безперервного розливання стали на металургійних заводах України найближчим часом. Завдання підтримки конкурентоспроможності вітчизняної продукції вирішуються за рахунок створення комплексної автоматизованої системи контролю та управління технологічним процесом (АСУ ТП), яка забезпечує необхідну якість металопродукції на кожному етапі її виробництва [8].
2 Мета, задачі дослідження та заплановані результати
Метою даної роботи є підвищення ефективності процесу безперервного розливання сталі шляхом створення комплексної системи автоматизованого управління.
Для контролю та управління всім комплексом обладнання, що забезпечує технологічний процес розливання сталі, до системи автоматизованого управління висувають такі вимоги:
В роботі планується виконати:
3 Технологічний процес безперервного розливання сталі
Схема машини безперервного лиття заготовок (МБЛЗ) наведена на рисунку 1.
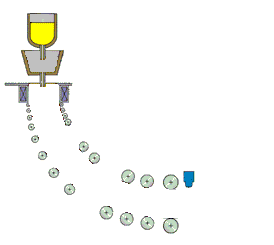
Рисунок
1 – Технологічна схема МБЛЗ
(анімація: 17 кадрів, 6 циклів повторення, 90,5 кілобайта)
Стальковш, наповнений рідкою сталлю, виробленої в конверторі за допомогою спеціального сталерозливного крана піднімають на робочу площадку МБЛЗ і встановлюють на стенд. Відкривають шибер і наповнюють промковш до заданого рівня, після чого шиберну заслінку закривають, відкривають стопор промковша і подають метал у кристалізатор.
В началі дно кристалізатора закрито головкою затравки, що представляє собою довгий стержень, що складається з ланок, з’єднаних між собою шарнірами. Хвостова частина затравки утримується в валках тягнуче-правильної машини.
Після заповнення кристалізатора металом до заданого рівня запускається тягнуче-правильна машина на витягування затравки і одночасно включається механізм гойдання, який повідомляє кристалізатору рух по технологічній лінії машини з малим ходом і великою частотою, що дозволяє знизити тертя між стінками кристалізатора і скоринкою твердіє заготовки.
У кристалізаторі здійснюється первинне, закрите охолодження злитка через контакт з холодною мідної стінкою, інтенсивно омивається водою за передбаченими в ній каналам. Поступово швидкість витягування доводять до номінальної. Заготовка в двофазному стані (рідка серцевина) потрапляє в зону вторинного охолодження, де охолоджується в розрахунковому режимі відкритою подачею води за допомогою форсунок.
Коли місце стику головки затравки і заготовки виходить за вісь останнього валка тягнуче-правильного механізму, запал відокремлюється від заготовки за допомогою механізму відділення затравки і далі заготовка рухається в зону ріжучого пристрою, де здійснюється порізка на мірні довжини [3].
4 Огляд досліджень і розробок
Машина безперервного лиття заготовок є однією з основних складових всього металургійного виробництва, тому в сучасному світі постійно ведуться розробки на вдосконалення як технології і конструкції, так і систем автоматизації, покликаних убезпечити і полегшити роботу персоналу.
4.1 Огляд міжнародних джерел
Ідея безперервного лиття була висунута в середині XIX в. Г. Бессемером, який пропонував розливати рідку сталь між двома водоохолоджуваних валками [4].
В роботах Бровмана М.Я. розглянуті основні особливості технології та запропоновано деякі вдосконалення [5, 6].
Проектуванням систем контролю й автоматичного регулювання металургійних процесів займався Глинков Г.М. [7]. Крім того, серед уже сучасних розробок є роботи зі створення адаптивних автоматизованих систем управління (Батраева А.Е. [8], Саліхов К.З. [9]).
Принцип оптимізації охолодження сляба в зоні вторинного охолодження криволінійної машини безперервного лиття за критерієм мінімуму експлуатаційних витрат розглядаються в роботах Лукіна С.В., Гофмана А.В. [10, 11]. Моделювання процесів формування заготовки в кристалізаторі представлено у Повітухіна С.А. [12].
Питаннями стабілізації технологічних параметрів витягування зливка електроприводом тягнучих роликів займався Лук’янов С.І. [13].
4.2 Огляд національних джерел
В Україні дослідження і розробки в металургійній сфері ведуться в містах Київ, Днепропетровськ, Донецьк и Запоріжжя. Це пов’язано з вимогами постійного підвищення якості готового продукту.
Питанням модернізації металургійних об’єктів займався Арист Л.М. [14]. Теплотехнічні процеси представлені в роботах Свінолобова Н.П. [15].
Основні положення моделювання в літійному виробництві розглядається в книгах Чорного А.А. [16, 17].
4.3 Огляд локальних джерел
У Донецькому національному технічному університеті досить активно ведуться розробки систем автоматизації машин безперервного лиття заготовок, а також займаються дослідженням теплових процесів.
Комплексна автоматизована система локального управління розглянута в роботі Боярова Д.В.[18]. Питаннями автоматизації також займалися Бобіта Т.Ю., Маренич К.М., Терещук Р.С., Новикова Ю.С., Гавриленко Б.В. [19–21]. Системою діагностики процесу хитання кристалізатора займалися Цупрун А.Ю., Кубкін Д.А., Антикуз О.В., Дзвонів А.В., Пільгаев В.М. [22]. Шептура А.А., Турченко Е.А. розробили структуру системи підтримки прийняття рішень при управлінні [23]. Система автоматичного управління рівнем металу і швидкості витягування заготовки з кристалізатора розглянута в роботі Жукова Н.В., Волуева О.С., Корчака В.В. [24]. Метод контролю геометричних параметрів машини безперервного лиття заготовок представлений в роботі Шоломицького А.А., Сотнікова А.Л., Адаменко В.І. [25].
Питаннями регулювання швидкості тягнуче-правильного механізму займався Стіблій А.В., Мінтус А.Н. [26].
Моделювання та оптимізація теплової роботи розглядаються в роботах Гинкула С.І., Струка С.В., Парахіна Н.Ф., Дробишевської І.П., Кононенко А.В., Смирнова А.Н., Ухіна В.Є. [27–29].
5 Розробка автоматизованої системи управління процесом безперервного розливання сталі
На рисунку 2 наведена структурна схема системи автоматизації.
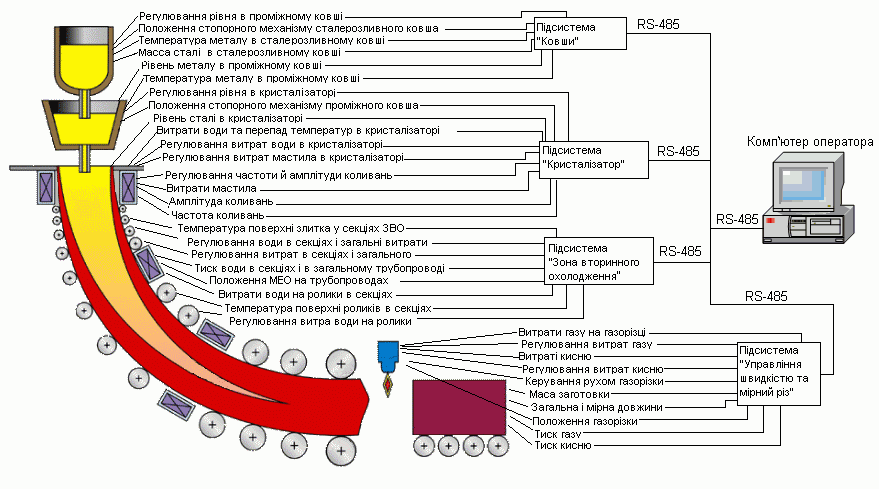
Рисунок 2 – Структурна схема автоматизированої системи управління МБЛЗ
Уся система ділиться на функціональні підсистеми управління окремими
механізмами МБЛЗ (Ковши
,
Кристалізатор
,
ЗВО
та Управління швидкістю і мірний рез
). Для передачі значень
контрольованих параметрів і прийому керуючий впливів пропонується
використовувати один з найбільш поширених стандартів передачі фізичного
рівня зв’язку – RS-485.
Особливістю розробленої системи автоматизації є розподілена
структура на основі широкого використання мікроконтролерів фірми
ATmega. При цьому підході модулі підсистем для обробки сигналів можуть
встановлюватися максимально близько до механізмів МБЛЗ і замінюватися в
гарячому
режимі. Така архітектура дозволяє знизити витрати на кабельну
продукцію, підвищити перешкодозахищеність обладнання, а також при
необхідності оперативно здійснювати модернізацію з мінімальними
витратами, не переробляючи, а замінюючи конфігурацію системи управління
[30].
Функції підсистеми Ковши
[18]:
Функції підсистеми Кристалізатор
:
Функції підсистеми ЗВО
:
Функції підсистеми Управління швидкістю і мірний різ
:
6 Розробка структурної схеми електроприводу ТПМ
Технологія безперервного розливання сталі і конструкція машин постійно удосконалюються в напрямку підвищення якості отримуваної продукції та продуктивності. Збільшення продуктивності МБЛЗ прямо пов’язано зі збільшенням лінійної швидкості розливання.
Основними причинами обмеження швидкості є: якість внутрішньої структури заготовки і частота пориву металу. Це пов’язано з тим, що зі збільшенням швидкості розливання зростає інтенсивність охолодження заготовки та швидкість її деформації, що призводить до зниження якості внутрішньої структури заготовки і збільшення ймовірності пориву скоринки злитка.
У більшості вітчизняних та зарубіжних МБЛЗ застосовується електропривод постійного струму з силовим живленням всіх електродвигунів від одного або двох тиристорних перетворювачів [13].
Проте основний недолік машин постійного струму – наявність щітково-колекторного вузла, який вимагає ретельного догляду в експлуатації і знижує надійність роботи машини. У зв’язку з цим пропонується технічне рішення (рисунок 3) реалізовано з використанням асинхронних електродвигунів з частотним регулюванням.
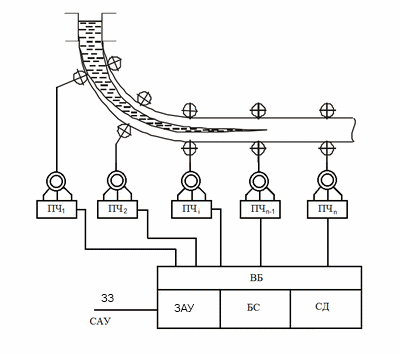
Рисунок 3 – Схема электропривода ТПМ
Поточний стан струму і швидкості двигунів передаються у вхідний блок (ВБ) по секціях МНЛЗ. З нього також передаються сигнали управління, як різниця між заданим (ЗЗ) і поточним значеннями. Загальний алгоритм управління електроприводом тягнуче-правильного пристрою (ЗАУ) відповідає за плавне регулювання швидкості протяжки по секціях. Блок стабілізації (БС) забезпечує розрахунок і підтримання необхідного за технологією відносного розподілу загального моменту витягування зливка [13]. До складу системи управління також включена система діагностики (СД), що дозволяє відстежити можливі несправності використовуваного обладнання.
7 Моделювання електроприводу
Принцип частотного методу регулювання швидкості двигуна полягає в тому, що, змінюючи частоту напруги живлення, можна змінювати кутову швидкість магнітного поля статора. Цей спосіб забезпечує плавне регулювання швидкості в широкому діапазоні, а механічні характеристики мають високу жорсткість.
Регулювання швидкості при цьому не супроводжується збільшенням ковзання асинхронного двигуна, тому втрати потужності при регулюванні невеликі.
Для отримання високих енергетичних показників асинхронного двигуна – коефіцієнтів потужності, корисної дії, перевантажувальної здатності – необхідно одночасно з частотою змінювати й підводиму напругу.
Закон зміни напруги залежить від характеру моменту навантаження Mс. При постійному моменті навантаження Mс = const напруга на статорі повинно регулюватися пропорційно частоті.
7.1 Обгрунтування прийнятих допущень
З метою спрощення математичної моделі асинхронного двигуна (АД) приймається ряд припущень [31–33]:
зірка; якщо насправді якась обмотка з’єднана за схемою
трикутник, то розрахунки проводяться для еквівалентної обмотки зі схемою
зірка;
7.2 Математична модель АД в осях α, β, 0
Найбільш часто система диференційних рівнянь асинхроного двигуна записується відносно потокосчеплень. Така система має вигляд [35]:
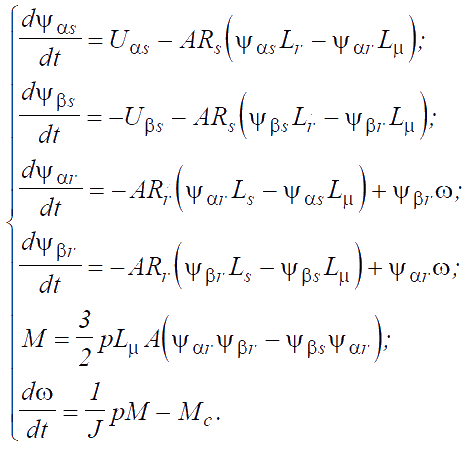
де A=1/(LsLr–Lμ2);
Rs, Rr – активний опір фази відносно статора і ротора відповідно;
Ls, Lr – повна індуктивність обмоток відповідно статора і ротора;
Lμ – ввзаємна індуктивність між обмотками ротора і статора.
Значення струмів пов’язані з потокозчепленням наступними рівняннями:
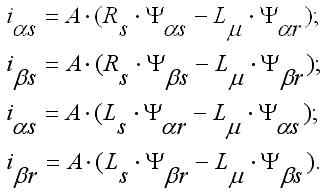
7.3 Математична модель автономного інвертора
Графік напруг після автономного інвертора на фазі А навантаження буде представляти собою знакозмінну функцію, приймаючу значення [34]:
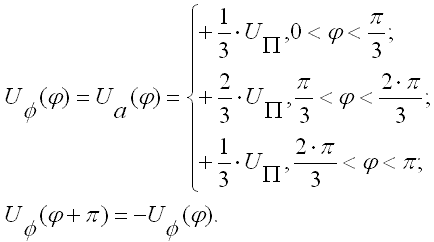
Аналогічно для фази В і С, тільки враховуючи відставання і випередження фаз на кут 2π⁄3 відповідно.
7.4 Розрахунок моменту навантаження
На початку визначаємо ферростатичний тиск рідкої серцевини злитку на широкі поверхні кристалізується оболонки за формулою [36]:

де γ = 70 кН⁄м2 – питома вага рідкої сталі;
b – ширина рідкої фази злитка, м;
R – радіус кривизни МБЛЗ, м;
φ0, φ1, φ2 – кутові координати, зазначені на рисунку 4.
Ширина рідкої фази злитка ,
де В – ширина злитка; δ – товщина його корки;
,
тут k – коефіцієнт, який дорівнює 2,6 для криволинійної зони
МБЛЗ; t – час кристалізації злитка.
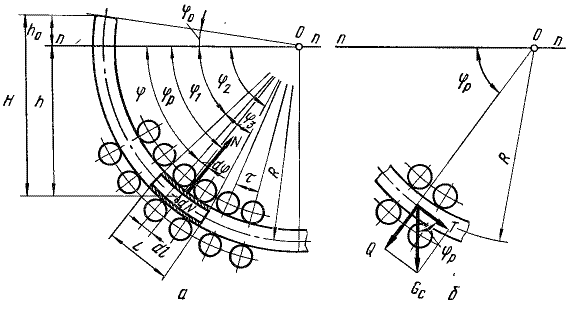
Рисунок
4 – Схеми дії сил в роликових секціях ТПМ:
а -
ферростатичний тиск на ролики; б - складові сили важкості
злитка.
Потім визначають вагу Gc частини злитка длиною L на участку розглянутої секції і розкладають на нормальну силу Q і тангенціальну T:

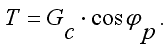
Результуючі сили тиску на опори нижніх і верхніх роликів відповідно:


де Gp – вага ролика; Gг – зусилля гідроциліндрів притиснення.
Крутні моменти на нижніх і верхніх роликах:


де μп = 0,015;
dcp – середній діаметр підшипника, м.
Сила Т створює момент в напрямку руху злитка: