Реферат по теме выпускной работы
Содержание
- Введение
- 1. Актуальность темы
- 2. Цель и задачи исследования
- 3. Обзор исследований и разработок
- 3.1 Анализ существующих математических моделей
- 3.2 Анализ существующих физических моделей
- 4. Разработка математической модели валковой разливки-прокатки
- Выводы
- Список источников
Введение
В условиях роста цен на энергоносители и постепенного приближения их к уровню среднеевропейских, приоритетным направлением развития металлургии Украины является внедрение современных энергосберегающих технологий, которые позволяют снизить соответствующую долю затрат в себестоимости проката и повысят конкурентоспособность отечественной металлопродукции на внешних рынках. Одной из наиболее перспективных технологий производства листа с точки зрения экономии энергии и экологичности является процесс валковой разливки-прокатки. Несмотря на 150-ти летний возраст идеи сэра Генри Бессемера о получении листа путем формирования его непосредственно из расплава между двумя вращающимися валками, промышленное применение этого способа кристаллизации при изготовлении плоского проката достаточно ограничено. Это связано с более высокими текущими производственными расходами при переходе с классической на новую технологию, во многом из-за ее инновационной составляющей, а также большей себестоимостью тонны продукции по сравнению с линиями оборудованными машинами непрерывного литья тонких, толщиной от 50 до 90 мм, слябов при выполнении крупных заказов по одному марочному сортаменту . Последнее объясняется меньшей производительностью литейно-прокатных агрегатов с машинами непрерывной валковой разливки-прокатки, что делает их конкурентоспособными при мелкосерийном изготовлении листов из нерядовых марок сталей и сплавов в объеме 300-700 тыс. т. в год. Тем не менее, благодаря возможности снижения энергопотребления на 90% по сравнению с традиционной схемой, включающей в себя непрерывную разливку слябов, а также уменьшению выбросов в атмосферу углекислого газа в семь раз и в десять раз меньше капитальных затрат на строительство и установку ЛПА с двухвалковыми кристаллизаторами. Поэтому данная технология считается одним из перспективнейших направлений развития листопрокатного производства и нуждается в дальнейшем улучшении.
1. Актуальность темы
Валковая разливка-прокатка является одной из наиболее перспективных и энергосберегающих технологий производства тонких полос. Получение тонкого и особо тонкого плоского проката заключается в формировании полосы непосредственно из жидкого металла путём кристаллизации и деформации его между двумя вращающимися валками. Поэтому наиболее привлекательным является вопрос изучения гидродинамики струи расплава с целью гарантированного получения профиля полосы (особенно боковой кромки).
2. Цель и задачи исследования
Магистерская работа посвящена разработке математической модели валковой разливки-прокатки, которая позволит получить данные о полях температуры и скоростях в зоне кристаллизации-деформации, особенно на боковой кромке полосы и учитывала бы влияние вращения валков и других технологических параметров валковой разливки-прокатки, а также её реализация в среде Ansys.
3. Обзор исследований и разработок
Суть данного способа производства тонкого и особо тонкого плоского проката заключается в формировании листа непосредственно из жидкого металла путем кристаллизации и последующей деформации его между двумя вращающимися валками. После машины непрерывной валковой разливки-прокатки материал без промежуточного подогрева поступает в прокатную клеть, где обжимается до требуемой толщины, а затем поступает на участок контролируемого охлаждения, призванного обеспечивать необходимую, микроструктуру и уровень механических свойств листа. После охлаждения полоса сматывается в рулоны, готовые для отгрузки потребителям. В настоящее время диапазон толщин стальных листов, получаемых на агрегатах непрерывной валковой разливки-прокатки, составляет для промышленных установок от 1 до 5 мм, в лабораторных условиях -0,1...3 мм [1].
3.1 Анализ существующих математических моделей
Из работ, посвященных теоретическому описанию процессов, протекаю¬щих между вращающимися валками-кристаллизаторами можно выделить труды В. Клосса К. А.[2], Сантоса [3], К М. Жанга [4], а также коллектива российских ученых из МГИ-СиС [5]. Одной из основных работ посвященных моделированию процесса течения металла в валковом кристаллизаторе является работа Р. Гутри и Р. Тавареса [6].Также известны работы бразильских ученых по созданию модели течения металла [7],в которой методом конечных разностей решается лишь температурная задача.
Сотрудниками Шанхайского университета и исследовательского института фирмы "Baoshan Iron & Steel", Шанхай, Китай [8] была выполнена разработка модели температурно-гидродинамического режима, пригодной для анализа течения и теплопередачи в двухфазной зоне методом конечных разностей. Было также проанализировано влияние коэффициента теплопередачи в контакте металл/валок на течение и кристаллизацию расплава.
В работе Гридина [9] включающей в себя описание и верификацию математической модели в части описания теплового состояния разливаемого металла, а также результаты моделирования эволюции температурных полей вращающихся валков во времени. С учетом отмеченных выше недостатков метода конечных разностей, в качестве математического инструмента для численного решения задач теплопереноса и течения металла при непрерывной валковой разливке-прокатке выбран метод конечных элементов.
Следующая публикация [10] рассматривает работы К. - Д. Ху и Д. - Й. Жу [11], в которых используется программный пакет Аnsys Flotran американской компании Аnsys Inc. При этом в этой гидродинамической модели закристаллизовавшийся металл рассматривается как вязкая жидкость. Раньше на кафедре обработки металлов давлением НМетАУ была разработанная модель [12] валковой разливки-прокатки, в которой металл рассматривался как жесткое пластичное тело. В публикации с помощью Аnsys Flotran было проведено пробное моделирование течения металла через двухвалковый кристаллизатор. Результаты моделирования показали возможность создания математической модели процесса валковой разливки-прокатки с помощью модуля Аnsys Flotran.
3.2 Анализ существующих физических моделей
Первоначальная идея непосредственного получения листа из расплава принадлежит сэру Г. Бессемеру, была высказана им в 1857 и запатентована в виде машины в 1865 году [13]. Первая промышленная установка для разливки-прокатки алюминия с кристаллизатором валкового типа была сконструирована в 1950 году Дж. Л. Хантером, основателем известной ныне фирмы-производителя металлургического оборудования FATA Hunter[14].
Несмотря на успешное освоение в середине прошлого века процесса валковой разливки-прокатки для изготовления листов из алюминия, припоев и чугуна, промышленное применение этой технологии на сталях ведет свой отсчет лишь с 1991 года, когда в результате совместного проекта австралийской компании ВНР и японской фирмы 1HI в городе Порт Кембла (Австралия) была запущена первая установка с двухвалковым кристаллизатором, позволяющая формировать непосредственно из расплава лист из низкоуглеродистых или легированных сталей толщиной до 1,9 мм и шириной до 1300 мм [15]. В результате этого достижения сразу несколько крупных мировых производителей стали обратили внимание на этот перспективный способ получения плоского проката, что привело к независимому созданию ряда коммерческих, с элементами know-how, технологий, производства стального листа и оборудования для его осуществления, большая часть из которых к настоящему времени реализована в промышленных условиях. К таким коммерческим проектам можно отнести программы Eurostrip (ThyssenKrupp Stahl, Германия; Usinor, Франция; AST, Италия: VAI, Австрия) [16], Castrip® (Nucor, США и ВНР, Австралия) [15], POSCO/RIST (POSCO, Южная Корея и Nippon Steel, Япония) [17], ВНИИМЕТМАШ (Россия) [18] и др.
Для проведения исследований, в рамках совместной научной работы между кафедрой обработки металлов давлением Национальной металлургической академии Украины и Институтом материаловедения Ганноверского университета им. Лейбница (ФРГ), была создана экспериментальная машина валковой разливки-прокатки тонких полос [19].
4. Разработка математической модели валковой разливки-прокатки
Для математического моделирования процессов валковой разливки-прокатки был выбран универсальный пакет прикладных программ ANSYS Int., который используется для решения задач, связанных со многими разделами науки и техники, такими, как электротехника, электромагнетизм, гидродинамика, газовая динамика и т. д.
Создание математической модели для исследования процессов перемешивания металлического расплава и затвердевания полосы при валковой
разливке-прокатке осуществлялось в среде ANSYS CFX, обладающей следующими возможностями:
–моделирование невязких, ламинарных и турбулентных потоков;
–моделирование теплопереноса, включая различные виды конвекции, сопряженный теплообмен и излучение и т. д.
В основе разработанной математической модели лежит решение с помощью метода конечных элементов основного уравнения нестационарной теплопроводности и
уравнений Навье–Стокса, включающие:
– уравнение неразрывности (закон сохранения массы);
– уравнение импульса (закон сохранения импульса);
– уравнение энергии (закон сохранения энергии).
Решение поставленных задач гидродинамики и затвердевания было реализовано в трехмерной интерпретации, со следующими допущениями: валки недеформируемые, течение расплава турбулентное, на контакте между валком и металлом выполняется условие постоянного прилипания.
В качестве разливаемого металла был выбран свинец. Граничные условия: теплопроводность – 23,2 Вт/(м•К), удельная теплоемкость разливаемого металла – 138,84 Дж/(кг•К), плотность разливаемого металла – 10641 кг/м3. Технологические характеристики взяты максимально приближенными к возможностям лабораторной установки: внешний диаметр валка – 76 мм, длина зоны кристаллизации-деформации – 40 мм, толщина полосы – 3,25 мм, начальная температура жидкого металла – 327°С, температура разливаемого металла постоянна.
На первом этапе моделирования, решалась задача способа подачи расплава в кристаллизатор. Проведенные исследования показали значительное влияние распределения потоков расплава в кристаллизаторе (рисунок 1) на процессы затвердевания.
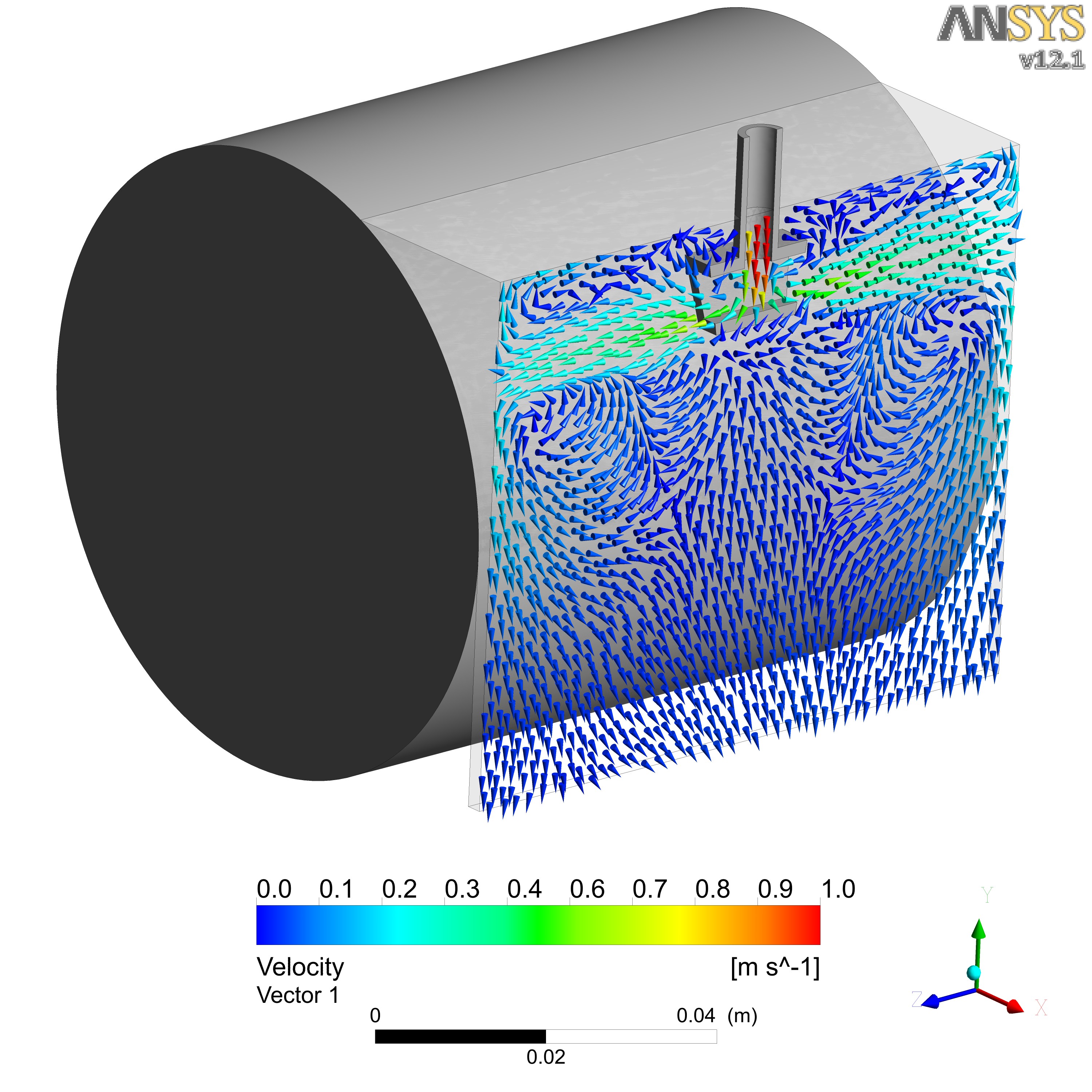
Рисунок 1 – Результирующая скорость движения расплава (векторная картина) в продольной плоскости двухвалкового кристаллизатора
Параллельно с созданием математической модели была разработана физическая модель процесса. При проектировании экспериментальной установки использовали вертикальную схему ведения процесса, когда жидкий металл подаётся от печи к разливочной ванне, а после в межвалковое пространство в зону кристаллизации металла под действием сил тяжести. Валки-кристаллизаторы состоят из водоохлаждаемой медной гильзы и двух осевых вставок, обеспечивающих требуемые характер теплоотбора с внутренней поверхности бандажей. Каждый валок имеет индивидуальный привод постоянного тока, который обеспечивает реализацию высоких крутящих моментов и возможность ведения процесса с требуемыми пластическими деформациями. Кроме того, предусмотрена возможность регулирования расстояния между валками, что позволяет расширить диапазон исследуемых толщин конечной полосы: максимально до 4,0 мм. Данные, полученные в условиях малой лабораторной установки, могут служить критерием и источником натурных исследований.
В дальнейшем планируется выполнение следующих этапов моделирования и проведение исследований по модернизации погружного стакана.
Выводы
Таким образом, проведенный анализ исследований, посвященных математическому моделированию валковой разливки-прокатки позволяет сделать следующие выводы:
- Большинство существующих моделей направлено на изучение явлений гидродинамики вместе с тепло- и массопереносом.
- Основу моделей представляют уравнения неразрывности, уравнения импульса и уравнения энергии. Решение систем уравнений и моделирования выполняется методом конечных элементов с применением прикладных пакетов FLOW, CFX, Fluent, ANSYS.
Разработанные теоретические модели процесса валковой разливки-прокатки, выполнены в виде предназначенной для пользователя программы ANSYS, она показала адекватность и достаточную меру точности получаемых результатов прогноза температурных полей металла и бандажей. Этот математический инструмент может служить в дальнейшем для ведения множественных расчетов с целью получения ба-зовых зависимостей, которые определяют взаимное влияние параметров разливки, деформации и охлаждения, который позволит создать энергосберегающие технологии производства листов с необходимым уровнем точности и механических свойств. Дальнейшее усовершенствование модели позволит широко использовать это для определения оптимальных параметров процесса и учитывать большее количество факторов, которые влияют на валковую разливку-прокатку.
Список источников
- Zapuskalov N. Comparison of continuous strip casting with conventional technology / N. Zapuskalov //ISI J International. – 2003. – Vol. 43 (№ 8). – P. 1115–1127.
- Kloss W. Duenbandgiessen mit variable Giasspalt. Umformtechnische Schriften / W. Kloss .– Aachemn: Shaker Verlag, 2005. Band 144. –180s.
- Santos C. A. Modelling of solidification in twin-roll strip casting/ C. A. Santos, J. A. Spim, A. Garcia// Journal of Materials Processing Technology. – 2000. – №102(1–3). – P. 33–39.
- Zgang X. M. Modelling of the micro-segregation of twin-roll thin strip casting/ X. M. Zgang, Z. Y. Jiang, X. H. Liu, G. D. Wang//Journal of Materials Processing Technology. – 2005. №162–163. – P. 591–595.
- Зиновьев А. В. Моделирование процесса непрерывного литья тонких полос в валковом кристаллизаторе / А. В. Зиновьев, В. С. Савченко, А. А. Бондаренко. – Дніпропетровськ: «Системні технології», 2005. – T.8: Сучасні проблеми металургії. Наукові вісті. Пластична деформація металів. – C. 32–36.
- Guthrie R.I.L. Mathematical and physical modeling of steel flow and solidification in twin roll (horizontal belt thin strip casting machines)/R.I.L. Guthrie, R.P. Tavares // Inter Conf on CFD in Mineral & Metal Processing and Power Generation. CSIRO. -1997. –P. 41-54.
- Santos C.A. Modeling of solidification in twin-roll strip casting / C.A. Santos, J.A. Spim Jr., A.Garcia // Journal of Materials Processing Technology. -2000.- №102.-P. 33-39.
- Wang B. Modelling of Melt Flow and Solidification in the Twin-Roll Strip Casting Process / B. Wang, J.–Y. Zhang, J.–F. Fan et al. // Steel Research International. –2009. 80. –№ 3. – P. 218–222.
- Гридин А. Ю. Математическое моделирование температурного поля металла и валков в процессе валковой разливки-прокатки/ А. Ю Гридин// Обработка материалов давлением. – 2009. – №1(20). – С. 75–83.
- Столбченко М. Ю. Применение модуля Ansys Flotran для моделирования процесса валковой разливки-прокатки полос/ М. Ю. Столбченко, О. Ю. Гридін// Обработка материалов давленим. – 2011. – №3(28). – С. 41–44.
- Hu- X.-D. Simulation of Inelastic Deformation and Thermal Mechanical Stresses in Twin-roll Casting Process of Mg Alloy / X.-D. Hu, D.-Y.Ju// Key engineering materials. – 2007. – №340–341. – P. 877–882.
- Гридін О. Ю. Математичне моделюванне процесу валкової розливки прокатки за допомогою програми Ansys/ О. Ю. Гридін, В. М. Данченко// Металлургическая и горнорудная промышленность. – 2008. – №5. – С. 90–94.
- US Patent №49053. H. Bessemer. July 25, 1865.–10p.
- Zapuskalov N. Comparison of continuous strip casting with conventional technology / N. Zapuskalov //1 SI J International. - 2003. - Vol. 43 (M 8). - P. 1115-1127.
- Wechsler R. The status of twin-roll casting technology / R. Wechsler // Scandinavian Journal of Metallurgy. –2003.–Vol. 32 (Ns 1). – P. 58–63.
- Legrand H. Stainless steel direct strip casting – brief summary of current status of Eurostrip/ H. Legrand, U. Albrecht–Frueh, G. Stebner et cetera// Proceedings of Dr. Wolf Memorial Symposium. –Zurich,2002.–P.80–89.
- Moon H.-K. The statuse of twin roll strip casting process for steel strip is POSCO/RIST/ H.-K. Moon, D. -K. Choo, T. Kang,K.-S. Kim//Proceeding of 60th Electric Furnace Conference.–San Antonio,2002.–P.499–510.
- Бровман М. Я. Валковые литейно-прокатные агрегаты для производства тонких стальных полос / М. Я. Бровман, В. А. Николаев, В. П. Полухин, Н. В. Нижник//Удосконалення процесів і обладнання обробки тиском в металургії і машинобудуванні:зб.наук.пр. – Краматорськ, 2006. – С. 395–398.
- Гридин, А.Ю. Экспериментальная установка валковой разливки-прокатки тонких полос / А.Ю. Гридин, И. К. Огинский, В. Н. Данченко, Фр.-В. Бах // Металлургическая и горнорудная промышленность. – 2010. - №5.