Abstract
Contents
- Introduction
- 1. Analysis of existing mathematical models
- 2. Analysis of existing physical models
- 3. Mathematical modeling of solidification in twin-roll strip casting
- Conclusion
- References
Introduction
Twin-roll thin strip casting is a new technology which can produce a thin strip with a thickness of 1.0-6.0 mm directly from the liquidus steel. Twin-roll strip casting changes the traditional thin strip rolling significantly, making some production procedures, such as the continuous casting, heating and hot rolling be unnecessary, and enabling the metal solidification and rolling deformation to occur simultaneously. Liquid metal experiences hot working and plastic deformation simultaneously during the solidification of twin-roll casting, and forms a solid strip in a short time. Compared with the conventional thin strip casting, the twin-roll strip casting simplifies production process. It can save up to 70 % equipment investment and 30-40 % production cost. This technique can improve the microstructure of products, develop new materials and produce the metallic products which have a hard formability and cannot be produced by a traditional method. Twin-roll strip casting is very complicated, in which the heat transfer, solidification and plastic deformation can be completed in less than one second. It is hard to find its formability just through several experiments. However, the effects of the processing parameters can be obtained conveniently through the computer simulation. The obtained relationship can improve the quality of thin strip in practical application. There are many reports about the influences of the processing parameters on the casting and rolling processes. However, most simulations are carried out through 2D model and only few focuses on 3D model based on a lot of simplifications. In the conventional continuous casting process, the protective slag and suitable shape of nozzle can prevent the solidification of liquid steel. But the protective slag cannot keep warm in twin-roll strip casting, the submerged nozzle depth is a very important factor. This paper conducts a 3D coupling temperature-flow simulation of twin-roll strip casting. The outlet angle and the submerged nozzle depth are investigated. According to the metal flow in the molten pool and the temperature distribution in the casting process, the ranges of the processing parameters are discussed. Simulation can optimise the twin-roll strip casting process and improve the quality of products in practice.
1. Analysis of existing mathematical models
Currently, the range of thickness of steel sheets obtained in units of continuous roll casting-rolling is for industrial plants from 1 to 5 mm in the laboratory ... 3 -0.1 mm [1].
Of the papers devoted to the theoretical description of processes, flowing between rotating rollers, molds can be distinguished works of B. Kloss, KA [2] and Santos [3], K M. Zhang [4], as well as the team of Russian scientists from MHI -SIS [5]. One of the major works on modeling of metal flow in the roller mold is the work of R. Guthrie and R. Tavares [6] is also known for the work of Brazilian scientists to create a flow model of the metal [7], in which the finite difference method solved a thermal problem.
2. Analysis of existing physical models
The remainder are either single-roll casters or, far more commonly, twin-roll casters, as first proposed by Sir Henry Bessemer in an 1857 patent [13]. This ``holy grail'' has been pursued for some 140 years.The first commercial plant for casting-rolling aluminum roll-type mold was designed in 1950 by James L. Hunter, founder of the now well-known manufacturer of metallurgical equipment FATA Hunter [14]. Programs Eurostrip (ThyssenKrupp Stahl, Germany; Usinor, France; AST, Italy: VAI, Austria) [16], Castrip ® (Nucor, the U.S. and BHP, Australia) [15], POSCO / RIST (POSCO, South Korea and Nippon Steel , Japan) [17], VNIIMETMASH (Russia) [18], etc.
3. Mathematical modeling of solidification in twin-roll strip casting
The aim of this paper is to develop a 3D coupling temperature-flow mathematical model, which would be able to analyse the flow and heat transfer in the mushy zone, using a finite difference technique. The effect of the metal/roll heat transfer coefficient on flow and solidification was also studied. The simulation results can help to control the twin-roll strip casting process and improve the quality of the final products in industrial practice.
For the mathematical modeling of rtwin-roll casters was selected generic software package ANSYS Int., Which is used to solve the problems associated with many branches of science and technology, such as electrical engineering, electromagnetism, hydrodynamics, gas dynamics, etc.
A steady-state three-dimensional fluid flow, heat transfer and solidification model has been developed and applied to the twin-roll casting process for steel. In this model, the turbulent form of the Navier Stokes equation is fully coupled with a differential energy balance equation that takes solidification into account..
Creating a mathematical model to study the processes of mixing and solidification of molten metal strip at the twin-roll casting process was carried out in an environment ANSYS CFX.
As the spilled metal was chosen as lead. The boundary conditions are: thermal conductivity - 23.2 W / (m • K), specific heat capacity of spilled metal - 138.84 J / (kg • K), the density of the spilled metal - 10 641 kg/m3. The technological characteristics are taken as close to the capabilities of the laboratory setup: external rotor diameter - 76 mm, the length of the zone of crystallization-deformation - 40 mm, strip thickness - 3.25 mm, the initial temperature of the molten metal - 327 ° C, constant spilled metal.
In the first stage of modeling, the problem was solved in the way of feeding the melt crystallizer. Studies have shown a significant effect of melt flow distribution in the mold (Figure 1) on the solidification processes.
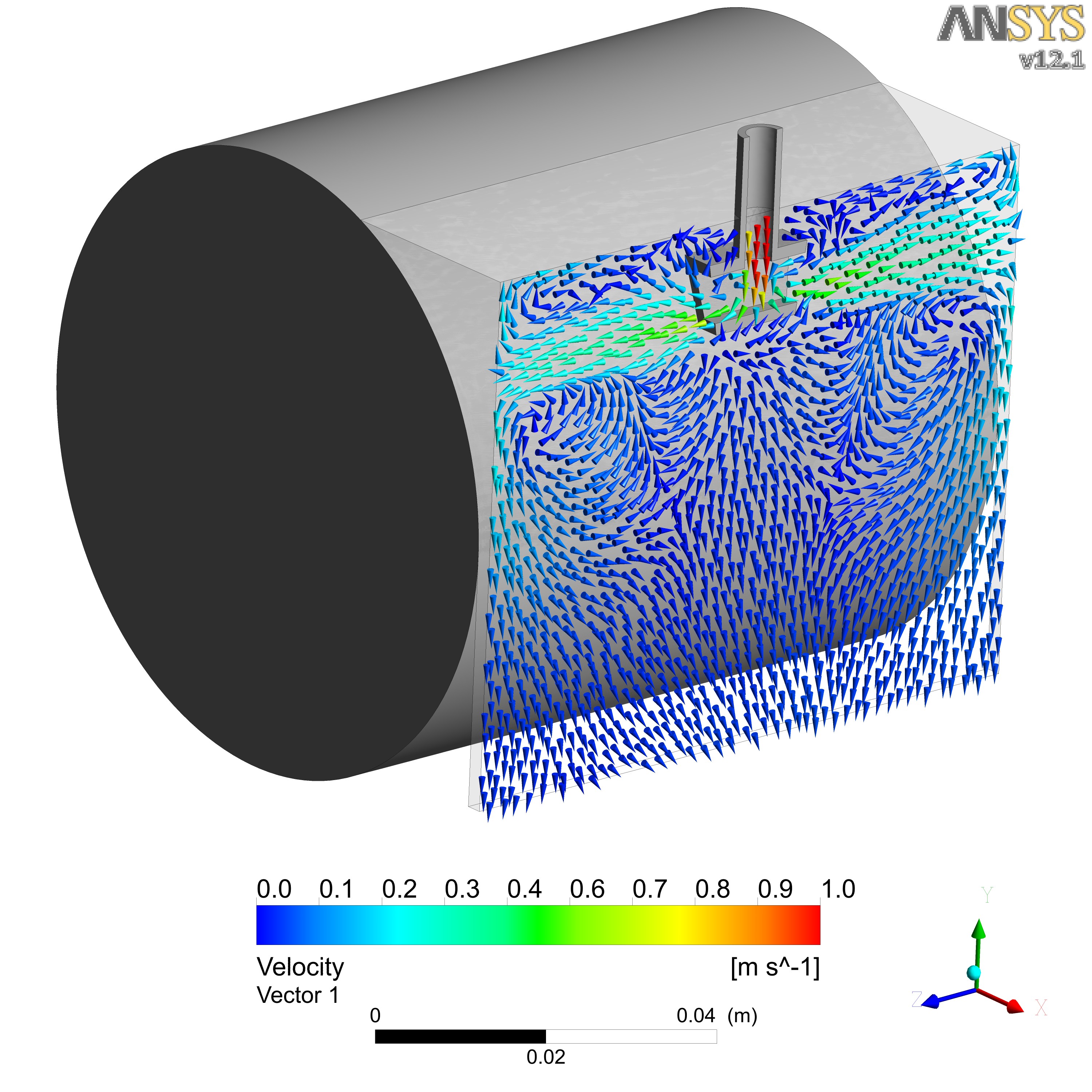
Figure 1 – The resultant velocity of the melt (vector pattern) in the longitudinal plane of the double roller crystallizer
In parallel with the creation of a mathematical model was developed by a physical model of the process. The data obtained in a small laboratory setting, can serve as a criterion and a source of field studies. In the future we plan to perform the following steps of modeling and research on the modernization of the submerged nozzle.
Conclusion
Thus, the analysis of research on mathematical modeling of roll casting-rolling to the following conclusions.
- Most existing models aimed at studying the phenomena of hydrodynamics with heat and mass transfer.
- The basis of the model are the continuity equation, momentum equation and energy equation. Solving systems of equations and modeling is performed by finite element method with application software packages FLOW, CFX, Fluent, ANSYS.
The developed theoretical model of the process of casting-rolling roller, in the form intended for the user program ANSYS, it showed sufficient measure of the adequacy and accuracy of prediction of the results of temperature fields of metal and tires. This mathematical tool can serve in the future to maintain multiple accounts with the purpose of obtaining ba-zovyh relationships that determine the relative influence of parameters of the casting, deformation and cooling, which will create an energy-saving technology of sheets with the necessary level of accuracy and mechanical properties.Further refinement of the model will use it extensively to determine the optimum process parameters and to consider more factors that influence the rwin roll strip casting.
During twin roll strip casting the contact heat transfer between the rolls and solidifying metal has a significant influence on the size of the solidification end point in the pool. The permeability of the mushy zone is a key factor to understand and model the flow and solidification in the twin-roll strip casting process.
References
- Zapuskalov N. Comparison of continuous strip casting with conventional technology / N. Zapuskalov //ISI J International. – 2003. – Vol. 43 (№ 8). – P. 1115–1127.
- Kloss W. Duenbandgiessen mit variable Giasspalt. Umformtechnische Schriften / W. Kloss .– Aachemn: Shaker Verlag, 2005. Band 144. –180s.
- Santos C. A. Modelling of solidification in twin-roll strip casting/ C. A. Santos, J. A. Spim, A. Garcia// Journal of Materials Processing Technology. – 2000. – №102(1–3). – P. 33–39.
- Zgang X. M. Modelling of the micro-segregation of twin-roll thin strip casting/ X. M. Zgang, Z. Y. Jiang, X. H. Liu, G. D. Wang//Journal of Materials Processing Technology. – 2005. №162–163. – P. 591–595.
- Зиновьев А. В. Моделирование процесса непрерывного литья тонких полос в валковом кристаллизаторе / А. В. Зиновьев, В. С. Савченко, А. А. Бондаренко. – Дніпропетровськ: «Системні технології», 2005. – T.8: Сучасні проблеми металургії. Наукові вісті. Пластична деформація металів. – C. 32–36.
- Guthrie R.I.L. Mathematical and physical modeling of steel flow and solidification in twin roll (horizontal belt thin strip casting machines)/R.I.L. Guthrie, R.P. Tavares // Inter Conf on CFD in Mineral & Metal Processing and Power Generation. CSIRO. -1997. –P. 41-54.
- Santos C.A. Modeling of solidification in twin-roll strip casting / C.A. Santos, J.A. Spim Jr., A.Garcia // Journal of Materials Processing Technology. -2000.- №102.-P. 33-39.
- Wang B. Modelling of Melt Flow and Solidification in the Twin-Roll Strip Casting Process / B. Wang, J.–Y. Zhang, J.–F. Fan et al. // Steel Research International. –2009. 80. –№ 3. – P. 218–222.
- Гридин А. Ю. Математическое моделирование температурного поля металла и валков в процессе валковой разливки-прокатки/ А. Ю Гридин// Обработка материалов давлением. – 2009. – №1(20). – С. 75–83.
- Столбченко М. Ю. Применение модуля Ansys Flotran для моделирования процесса валковой разливки-прокатки полос/ М. Ю. Столбченко, О. Ю. Гридін// Обработка материалов давленим. – 2011. – №3(28). – С. 41–44.
- Hu- X.-D. Simulation of Inelastic Deformation and Thermal Mechanical Stresses in Twin-roll Casting Process of Mg Alloy / X.-D. Hu, D.-Y.Ju// Key engineering materials. – 2007. – №340–341. – P. 877–882.
- Гридін О. Ю. Математичне моделюванне процесу валкової розливки прокатки за допомогою програми Ansys/ О. Ю. Гридін, В. М. Данченко// Металлургическая и горнорудная промышленность. – 2008. – №5. – С. 90–94.
- US Patent №49053. H. Bessemer. July 25, 1865.–10p.
- Zapuskalov N. Comparison of continuous strip casting with conventional technology / N. Zapuskalov //1 SI J International. - 2003. - Vol. 43 (M 8). - P. 1115-1127.
- Wechsler R. The status of twin-roll casting technology / R. Wechsler // Scandinavian Journal of Metallurgy. –2003.–Vol. 32 (Ns 1). – P. 58–63.
- Legrand H. Stainless steel direct strip casting – brief summary of current status of Eurostrip/ H. Legrand, U. Albrecht–Frueh, G. Stebner et cetera// Proceedings of Dr. Wolf Memorial Symposium. –Zurich,2002.–P.80–89.
- Moon H.-K. The statuse of twin roll strip casting process for steel strip is POSCO/RIST/ H.-K. Moon, D. -K. Choo, T. Kang,K.-S. Kim//Proceeding of 60th Electric Furnace Conference.–San Antonio,2002.–P.499–510.
- Бровман М. Я. Валковые литейно-прокатные агрегаты для производства тонких стальных полос / М. Я. Бровман, В. А. Николаев, В. П. Полухин, Н. В. Нижник//Удосконалення процесів і обладнання обробки тиском в металургії і машинобудуванні:зб.наук.пр. – Краматорськ, 2006. – С. 395–398.
- Гридин, А.Ю. Экспериментальная установка валковой разливки-прокатки тонких полос / А.Ю. Гридин, И. К. Огинский, В. Н. Данченко, Фр.-В. Бах // Металлургическая и горнорудная промышленность. – 2010. - №5.