Реферат за темою випускної роботи
Зміст
- Вступ
- 1. Актуальність теми
- 2. Мета і задачі дослідження
- 3. Огляд досліджень та розробок
- 3.1 Аналіз існуючих математичних моделей
- 3.2 Аналіз існуючих фізичних моделей
- 4. Розробка математичної моделі валкової розливки-прокатки
- Висновки
- Перелік посилань
Вступ
В умовах зростання цін на енергоносії і поступового наближення їх до рівня середньоєвропейських, пріоритетним напрямом розвитку металургії України є впровадження сучасних енергозбережних технологій, які дозволяють понизити відповідну долю витрат в собівартості прокату і підвищать конкурентоспроможність вітчизняної металопродукції на зовнішніх ринках. Однією з найбільш перспективних технологій виробництва листа з точки зору економії енергії і екологічності є процес валкової розливки-прокатки. Незважаючи на 150-ти літній вік ідеї сера Генрі Бесемера про отримання листа шляхом формування його безпосередньо з розплаву між двома валками, що обертаються, промислове застосування цього способу кристалізації при виготовленні плоского прокату досить обмежене. Це пов'язано з вищими поточними виробничими витратами при переході з класичною на нову технологію, багато в чому із-за її інноваційної складової, а також більшою собівартістю тонни продукції в порівнянні з лініями обладнаними машинами безперервного лиття тонких, завтовшки від 50 до 90 мм, слябів при виконанні великих замовлень по одному марочному сортаменту. Останнє пояснюється меншою продуктивністю ливарно-прокатних агрегатів з машинами безперервного валкового лиття-прокатки, що робить їх конкурентоздатними при дрібносерійному виготовленні листів з нерядових марок сталей і сплавів в об'ємі 300–700 тис. т. в рік. Проте, завдяки можливості зниження енергоспоживання на 90% в порівнянні з традиційною схемою, що включає безперервне розливання слябів, а також зменшенню викидів в атмосферу вуглекислого газу в сім разів і вдесятеро менше капітальних витрат на будівництво і установку ЛПА з двохвалковими кристалі заторами. Тому ця технологія вважається однією з найперспективніших напрямів розвитку листопрокатного виробництва і потребує подальшого поліпшення.
1. Актуальність теми
Валкова розливка-прокатка є однією з найбільш перспективних і енергозбережних технологій виробництва тонких штаб. Отримання тонкого і особливо тонкого плоского прокату полягає у формуванні смуги безпосередньо з рідкого металу шляхом кристалізації і деформації його між двома валяннями, що обертаються. Тому найпривабливішим є питання вивчення гідродинаміки струменя розплаву з метою гарантованого отримання профілю смуги(особливо бічної кромки). Актуальним завданням є розвиток теоретичних і технологічних основ процесу валкового лиття-прокатки з метою отримання базових залежностей, що визначають взаємний вплив параметрів розливання, деформації і охолодження, які дозволять розробити енергозбережну технологію виробництва з розплаву листів з потрібним рівнем точності і механічних властивостей.
2. Мета і задачі дослідження
Магістерська робота присвячена розробці математичної моделі валкового лиття-прокатки, яке дозволить отримати дані про поля температури і швидкостях в зоні кристалізації-деформації, особливо на бічній кромці смуги і враховувала б вплив обертання валків і інших технологічних параметрів валкового лиття-прокатки, а також її реалізація в середовищі Ansys.
3. Огляд досліджень та розробок
Суть цього способу виробництва тонкого і особливо тонкого плоского прокату полягає у формуванні листа безпосередньо з рідкого металу шляхом кристалізації і наступної деформації його між двома валками що обертаються Після машини безперервного валкового лиття-прокатки матеріал без проміжного підігрівання поступає в прокатну кліть, де обтискається до необхідної товщини, а потім поступає на ділянку контрольованого охолодження, покликаного забезпечувати необхідну, мікроструктуру і рівень механічних властивостей листа. Після охолодження штаба змотується в рулони, готові для відвантаження споживачам. Нині діапазон товщини сталевих листів, що отримуються на агрегатах безперервного валкового лиття-прокатки, складає для промислових установок від 1 до 5 мм, в лабораторних умовах - 0,1...3 мм[1].
3.1 Аналіз існуючих математичних моделей
З останніх робіт, присвячених теоретичному опису процесів, які протікають між валками-кристалізаторами, що обертаються, можна виділити праці В. Клосса. А.[2], Сантоса [3], К М. Жанга [4], а також колективу російських вчених з МГІ-СіС [5].Однією з основних робіт присвячених моделюванню процесу течії металу у валковом кристалізаторі є робота Р. Гутри і Р. Тавареса [6].Також відомі роботи бразильських вчених із створення моделі течії металу [7],у якій методом кінцевих різниць вирішується лише температурне завдання.
Cпівробітниками Шанхайського університету і дослідницького інституту фірми "Baoshan Iron & Steel", Шанхай, Китай [8]була виконана розробка моделі температурно-гідродинамічного режиму, придатною для аналізу течії і теплопередачі в двофазній зоні методом кінцевих різниць. Було також проаналізовано вплив коефіцієнта теплопередачі в контакті метал/валок на течію і кристалізацію розплаву.
Робота Грідіна [9] включає опис і верифікацію математичної моделі в частини опису теплового стану литого металу, а також результати моделювання еволюції температурних полів валків, що обертаються, в часі. З урахуванням відмічених вище недоліків методу кінцевих різниць, в якості ма-тематичного інструменту для чисельного вирішення завдань теплопереноса і течії металу безперервного валкового лиття-прокатки вибраний метод кінцевих елементів.
Наступна публікація [10] розглядає роботи К.-Д. Ху і Д.-Й. Жу [11], в яких використовується програмний пакет Аnsys Flotran американській компанії Аnsys Inc. При цьому в цій гідродинамічній моделі закристалізувавшийся метал розглядається як в'язка рідина. Раніше на кафедрі обробки металів тиском НМетАУ була розроблена модель [12] валкового лиття-прокатки, в якому метал розглядався як жорстко пластичне тіло. У публікації за допомогою Аnsys Flotran було проведено пробне моделювання течії металу через двохвалковий кристалізатор. Результати моделювання показали можливість створення математичної моделі процесу валкового лиття-прокатки за допомогою модуля Аnsys Flotran.
3.2 Аналіз існуючих фізичних моделей
Первинна ідея безпосереднього отримання листа з розплаву належить серові Г. Бессемерові, була висловлена ним в 1857 і запатентована у вигляді машини в 1865 році [13]. Перша промислова установка для розливання-прокатки алюмінію з кристалізатором валкового типу була сконструйована в 1950 році Дж. Л. Хантером, засновником відомої нині фірми-виробника металургійного устаткування FATA Hunter [14].
Незважаючи на успішне освоєння в середині минулого століття процесу валкового лиття-прокатки для виготовлення листів з алюмінію, припоїв і чавуну, промислове застосування цієї технології на сталях веде свій відлік лише з 1991 року, коли в результаті спільного проекту австралійської компанії ВНР і японської фірми IHI в місті Порт Кембла (Австралія) була запущена перша установка з двохвалковим кристалізатором, що дозволяє формувати безпосередньо з розплаву лист з низько вуглецевих або легованих сталей товщиною до 1,9 мм і ширина до 1300 мм [15]. В результаті цього досягнення відразу декілька великих світових виробників сталі звернули увагу на цей перспективний спосіб отримання плоского прокату, що привело до незалежного створення ряду комерційних, з елементами know-how, технологій, виробництва сталевого листа і устаткування для його здійснення, велика частина з яких до теперішнього часу реалізована в промислових умовах. До таких комерційних проектів можна віднести програми Eurostrip (ThyssenKrupp Stahl, Німеччина; Usinor, Франція; AST, Італія: VAI, Австрія) [16], Castrip® (Nucor, США і ВНР, Австралія) [15], POSCO/RIST (POSCO, Південна Корея і Nippon Steel, Японія) [17],ВНІІМЕТМАШ (Росія) [18] та ін.
Для проведення досліджень, у рамках спільної наукової роботи між кафедрою обробки металів тиском Національної металургійної академії України і Інститутом матеріалознавства Гановерського університету ім. Лейбніца(ФРН), була створена експериментальна машина валкового лиття-прокатки тонких смуг [19].
4. Розробка математичної моделі валкової розливки-прокатки
Для математичного моделювання процесів валкового лиття-прокатки був вибраний універсальний пакет застосовних програм ANSYS Int., який використовується для вирішення завдань, пов'язаних з багатьма розділами науки і техніки, такими, як електротехніка, електромагнетизм, гідродинаміка, газова динаміка і т. д.
Створення математичної моделі для дослідження процесів перемішування металевого розплаву і твердіння смуги при валковом литті-прокатці
здійснювалося в середовищі ANSYS CFX, що має наступні можливості :
–моделювання нев'язких, ламінарних і турбулентних потоків;
–моделювання теплопереноса, включаючи різні види конвекції, зв'язаний теплообмін і випромінювання і т. д.
У основі розробленої математичної моделі лежить рішення за допомогою методу кінцевих елементів основного рівняння нестаціонарної теплопровідності і
рівнянь Навьє-Стокса, що включають:
– рівняння нерозривності(закон збереження маси);
– рівняння імпульсу(закон збереження імпульсу);
– рівняння енергії(закон збереження енергії).
Рішення поставлених завдань гідродинаміки і твердіння було реалізоване в тривимірній інтерпретації, з наступними допущеннями: валяння не деформуються, течія розплаву турбулентна, на контакті між валком і металом виконується умова постійного прилипання.
В В якості розливаємого металу був вибраний свинець. Граничні умови: теплопровідність - 23,2 Вт(м•К), питома теплоємність розливаємого металу - 138,84 Дж(кг•К), щільність розливаємого металу - 10641 кг/м3. Технологічні характеристики узяті максимально наближеними до можливостей лабораторної установки : зовнішній діаметр валка - 76 мм, довжина зони кристалізації-деформації - 40 мм, товщина смуги - 3,25 мм, початкова температура рідкого металу - 327°З, температура розливаємого металу постійна.
На першому етапі моделювання, вирішувалося завдання способу подання розплаву в кристалізатор. Проведені дослідження показали значний вплив розподілу потоків розплаву в кристалізаторі(рисунок 1) на процеси твердіння.
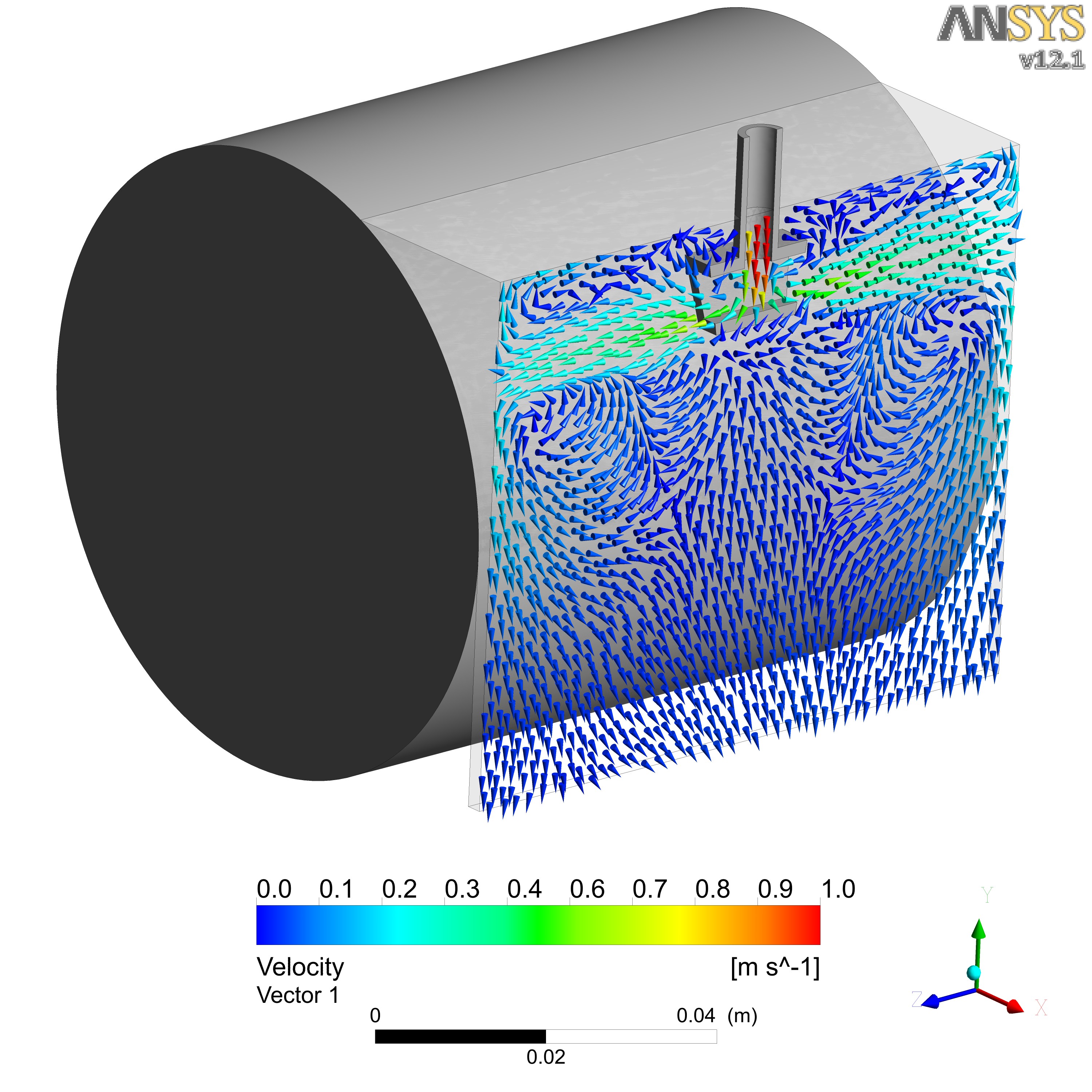
Рисунок 1 - Швидкість руху розплаву(векторна картина) в подовжній площині двохвалкового кристалізатора
Паралельно із створенням математичної моделі була розроблена фізична модель процесу. При проектуванні експериментальної установки використали вертикальну схему ведення процесу, коли рідкий метал подається від печі до розливної ванни, а після в межвалковий простір в зону кристалізації металу під дією сил тяжіння. Валяння-кристалізатори складаються з водо охолоджуваної мідної гільзи і двох осьових вставок, що забезпечують потрібні характер теплоотбора з внутрішньої поверхні бандажів. Кожен валок має індивідуальний привід постійного струму, який забезпечує реалізацію високих моментів, що крутять, і можливість ведення процесу з необхідними пластичними деформаціями. Крім того, передбачена можливість регулювання відстані між валяннями, що дозволяє розширити діапазон досліджуваної товщини кінцевої смуги : максимальне до 4,0 мм. Дані, отримані в умовах малої лабораторної установки, можуть служити критерієм і джерелом натурних досліджень.
Надалі планується виконання наступних етапів моделювання і проведення досліджень по модернізації погружного стакану.
Висновки
Таким чином, проведений аналіз досліджень, присвячених математичному моделюванню валковойї розливки-прокатки дозволяє зробити наступні висновки:
- Більшість існуючих моделей спрямована на вивчення явищ гідродинаміки разом з тепло- і масопереносом.
- Основу моделей представляють рівняння нерозривності, рівняння імпульсу і рівняння енергії. Рішення систем рівнянь і моделювання виконується методом кінцевих елементів із застосуванням прикладних пакетів FLOW, CFX, Fluent, ANSYS.
Розроблені теоретичні моделі процесу валкової розливки-прокатки, виконані у вигляді призначеної для користувача програми ANSYS, вона показала адекватність і достатню міру точності отримуваних результатів прогнозу температурних полів металу і бандажів. Цей математичний інструмент може служити надалі для ведення множинних розрахунків з метою отримання базовых залежностей, які визначають взаємний вплив параметрів розливання, деформації і охолодження, який дозволить створити енергозбережні технології виробництва листів з необхідним рівнем точності і механічних властивостей. Подальше удосконалення моделі дозволить широко використати це для визначення оптимальних параметрів процесу і враховувати більшу кількість чинників, які впливають на валкову розливку-прокатку.
Перелік посилань
- Zapuskalov N. Comparison of continuous strip casting with conventional technology / N. Zapuskalov //ISI J International. – 2003. – Vol. 43 (№ 8). – P. 1115–1127.
- Kloss W. Duenbandgiessen mit variable Giasspalt. Umformtechnische Schriften / W. Kloss .– Aachemn: Shaker Verlag, 2005. Band 144. –180s.
- Santos C. A. Modelling of solidification in twin-roll strip casting/ C. A. Santos, J. A. Spim, A. Garcia// Journal of Materials Processing Technology. – 2000. – №102(1–3). – P. 33–39.
- Zgang X. M. Modelling of the micro-segregation of twin-roll thin strip casting/ X. M. Zgang, Z. Y. Jiang, X. H. Liu, G. D. Wang//Journal of Materials Processing Technology. – 2005. №162–163. – P. 591–595.
- Зиновьев А. В. Моделирование процесса непрерывного литья тонких полос в валковом кристаллизаторе / А. В. Зиновьев, В. С. Савченко, А. А. Бондаренко. – Дніпропетровськ: «Системні технології», 2005. – T.8: Сучасні проблеми металургії. Наукові вісті. Пластична деформація металів. – C. 32–36.
- Guthrie R.I.L. Mathematical and physical modeling of steel flow and solidification in twin roll (horizontal belt thin strip casting machines)/R.I.L. Guthrie, R.P. Tavares // Inter Conf on CFD in Mineral & Metal Processing and Power Generation. CSIRO. -1997. –P. 41-54.
- Santos C.A. Modeling of solidification in twin-roll strip casting / C.A. Santos, J.A. Spim Jr., A.Garcia // Journal of Materials Processing Technology. -2000.- №102.-P. 33-39.
- Wang B. Modelling of Melt Flow and Solidification in the Twin-Roll Strip Casting Process / B. Wang, J.–Y. Zhang, J.–F. Fan et al. // Steel Research International. –2009. 80. –№ 3. – P. 218–222.
- Гридин А. Ю. Математическое моделирование температурного поля металла и валков в процессе валковой разливки-прокатки/ А. Ю Гридин// Обработка материалов давлением. – 2009. – №1(20). – С. 75–83.
- Столбченко М. Ю. Применение модуля Ansys Flotran для моделирования процесса валковой разливки-прокатки полос/ М. Ю. Столбченко, О. Ю. Гридін// Обработка материалов давленим. – 2011. – №3(28). – С. 41–44.
- Hu- X.-D. Simulation of Inelastic Deformation and Thermal Mechanical Stresses in Twin-roll Casting Process of Mg Alloy / X.-D. Hu, D.-Y.Ju// Key engineering materials. – 2007. – №340–341. – P. 877–882.
- Гридін О. Ю. Математичне моделюванне процесу валкової розливки прокатки за допомогою програми Ansys/ О. Ю. Гридін, В. М. Данченко// Металлургическая и горнорудная промышленность. – 2008. – №5. – С. 90–94.
- US Patent №49053. H. Bessemer. July 25, 1865.–10p.
- Zapuskalov N. Comparison of continuous strip casting with conventional technology / N. Zapuskalov //1 SI J International. - 2003. - Vol. 43 (M 8). - P. 1115-1127.
- Wechsler R. The status of twin-roll casting technology / R. Wechsler // Scandinavian Journal of Metallurgy. –2003.–Vol. 32 (Ns 1). – P. 58–63.
- Legrand H. Stainless steel direct strip casting – brief summary of current status of Eurostrip/ H. Legrand, U. Albrecht–Frueh, G. Stebner et cetera// Proceedings of Dr. Wolf Memorial Symposium. –Zurich,2002.–P.80–89.
- Moon H.-K. The statuse of twin roll strip casting process for steel strip is POSCO/RIST/ H.-K. Moon, D. -K. Choo, T. Kang,K.-S. Kim//Proceeding of 60th Electric Furnace Conference.–San Antonio,2002.–P.499–510.
- Бровман М. Я. Валковые литейно-прокатные агрегаты для производства тонких стальных полос / М. Я. Бровман, В. А. Николаев, В. П. Полухин, Н. В. Нижник//Удосконалення процесів і обладнання обробки тиском в металургії і машинобудуванні:зб.наук.пр. – Краматорськ, 2006. – С. 395–398.
- Гридин, А.Ю. Экспериментальная установка валковой разливки-прокатки тонких полос / А.Ю. Гридин, И. К. Огинский, В. Н. Данченко, Фр.-В. Бах // Металлургическая и горнорудная промышленность. – 2010. - №5.