Abstract
Содержание
- Introduction
- 1. Goal, objectives and research facility
- 2. Effect of sulfur dioxide on human, plant and animal life
- 3. Review of dry and wet flue gas cleaning methods containing sulfur dioxide
- 3.1 Methods based on suspensions of natural sorbents
- 3.2 Methods based on the use of solutions of sodium and ammonium
- 3.3 The absorption of sulfur dioxide by solid
- 3.4 Dry desulphurization methods
- 4. Methods of experimentation
- Conclusion
- References
Introduction
1. Goal, objectives and research facility
The purpose and objectives of research activation oxide and calcium carbonate is:
- Determination of the Alloy activator and calcium carbonate, an activator and calcium oxide;
- Temperatures start interacting with sulfur dioxide systems МеNO3 – CaCO3 и МеNO3 – CaO;
- Determination of the efficiency of absorption of sulfur dioxide and oxides of calcium carbonate with various activators.
The object of study: the interaction of systems МеNO3 – CaCO3 и МеNO3 – CaO с SO2.
2. Effect of sulfur dioxide on human, plant and animal life
Sulfur dioxide is one of the largest and most difficult-to-clean outdoor air pollutants. It adversely affects human health: causes irritation of the mucous membranes of the eyes, respiratory tract, bronchospasm and increased airway resistance.
In addition to effects on human health, sulfur dioxide has an adverse effect on the environment, in particular to vegetation on buildings.
In addition to effects on human health, sulfur dioxide has an adverse effect on the environment, in particular to vegetation on buildings. Repeatedly researchers studied the effect of emissions of power plants on the health of people living in areas with different intensity of air pollution, causing established the presence of the adverse impact of emissions on the sanitary conditions and public health in the area of smoke with a maximum concentration in the atmosphere S02 3.3 -4.0 and dust 2,5-4,6 mg/m3. The total number and frequency of complaints of respiratory diseases in certain forms in this zone was two times higher than in the relatively clean region. In the main group of students (zone smoke) most children noted reduced hemoglobin, revealed the presence of SO2 in the blood (from traces up to 0.02 mg), high incidence of conjunctivitis (13.3% compared with 3.8% in the control area) .
Results of research on the effects on the human organism S02 are shown in Table. 1
Тhe concentration S02 in the air, mg/m3 | The concentration of dust in the air, mg/m3 | Duration of exposure, h | The effects |
2600 | - | - | Instantaneously leads to death |
1400–1600 | - | 0.5–1 | Leads to death |
400–500 | - | 0.5–1 | Causes life-threatening disease |
40–60 | - | 0.5–1 | Causes irritation of the mucous membranes, sneezing, coughing |
20 | - | - | The threshold of irritation |
8–10 | - | - | Causes olfactory sensations |
2–3 | - | - | There is a faint smell |
0.72 | 0.75 | 24 | Partial death |
0.5 | Slight | 24 | Increased mortality among persons of a certain category |
0.1–0.27 | 0.185 (smoke) | Annual | The increase in diseases of the upper respiratory tract and bronchitis |
0.115 | 0.16 (smoke) | - | Increased mortality of persons with asthma and bronchitis |
The average concentration of SO2 in air varies depending on the amount of combustible fuel and its sulfur content. Typically ambient air contains sulfur dioxide in high concentration. The content of SO2 in the atmosphere naturally increases significantly with the onset of the heating season and the period of adverse weather conditions.
If there are individual cases of the maximum permissible concentration in the air is not generally characterized by extreme levels of sulfur dioxide pollution in relation to man, at the same time, these levels are harmful to vegetation, as MPC forest is 3 times lower limit values for air in populated areas. However, many ingredients, including SO2, under the joint finding can create effects summation or potentiation, and therefore the environmental situation can be dangerous. It is therefore necessary to conduct regular monitoring of the content of sulfur dioxide in the atmosphere and to develop methods of cleaning [1].
There are many methods for neutralization of gas emissions of SO2, but all of them can be divided into "dry" and "wet."
Each of them can be divided into three groups:
- The first provides only sanitary cleaning of the gas;
- The second group involves the cyclical processes, to produce SO2, or sulfur;
- The third group includes the processes by which the absorber is not returned to the process, and is used to produce new chemicals. Below is a closer look at some of them [2].
3. Review of dry and wet flue gas cleaning methods containing sulfur dioxide
3.1 Methods based on suspensions of natural sorbents
The limestone (calcareous) method
The purification is based on the neutralization of sulfuric acid, which is obtained by dissolving sulfur dioxide contained in flue gases, alkaline reagents: calcium hydroxide (lime) or calcium carbonate (limestone). Thus the following reactions:
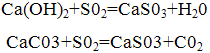
As a result of these reactions is obtained calcium sulfite partially oxidized to sulphate. In most cases the products of neutralization are not used and are sent to the blade.
The advantages of limestone (lime) method are simplicity of the technological scheme, the availability of a low cost sorbent, relatively low capital costs for cleaning the gas without pre-cooling and dedusting.
The disadvantages of the method include low utilization of limestone, depending on the type of mineral and reaching typically 40-50%, obtaining as a product of sludge disposal of unused, the relatively low efficiency of cleaning, exposure to crystalline deposits clogging the absorption apparatus and fluid communication.
Мagnesite method
The binding of sulfur dioxide occurs in its interaction with magnesite by reacting:

Magnesium sulfite formed again reacts with sulfur dioxide and water to form magnesium bisulfite:

The resulting neutralized by the addition of bisulfite magnesite:

Magnesium sulfite formed in the firing process at a temperature of 800-900 °C undergoes thermal decomposition to form the initial reaction products:

Magnesium oxide is returned to the process, concentrated and S02 may be processed into sulfuric acid or elemental sulfur.
Gas is cleaned from sulfur oxides at a concentration of 0.03% in the scrubber (Fig. 2), and the resulting solution with magnesium bisulfite concentration 50-70 g/l of circulating flows in the collection, where part of the solution is fed into the pressure tank and returns to irrigation scrubber and another part of the neutralizer to isolate magnesium sulfite. A solution of the catalyst in gidrotsikloiy displayed, then the pulp is directed to a vacuum belt filter and then to the kiln, where the sulfur dioxide formed and magnesite, reused in the loop.
The mother liquor and the wash water after the filter media enters the collection of clarified solution magnesite is added to the kiln. The solution is fed from the collection into the pressure tank, where it is mixed with an acidic solution of the circulating collection and goes to irrigation scrubber. The degree of purification of gases from SO2 is 90 -92%.
The advantage of the method of magnesite is possible to achieve a high degree of purification of gases without cooling. Firing magnesium sulfite can be done at a chemical plant outside the TPP, as the dried and dehydrated crystals can quite comfortably transported.
The main disadvantage of this method is the presence of magnesite numerous operations with solids (crystals sulfite, magnesium oxide, ash), which is due to abrasion and sawing equipment. For drying the crystals and remove the hydrate water requires a considerable amount of heat.
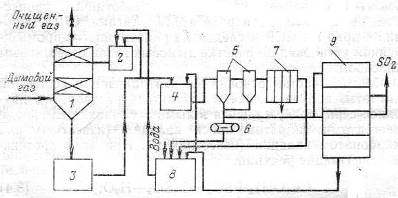
Figure 1 – The scheme of the flue gases from SO2 by magnesite: 1 – скруббер; 2 – напорный бак; 3 – циркуляционный сборник; 4 – нейтрализатор; 5 – гидроциклоны; 6 – ленточный вакуум-фильтр; 7 – фильтр-пресс; 8 – сборник осветленного раствора; 9 – обжиговая печь [3].
3.2 Methods based on the use of solutions of sodium and ammonium
Ammonia methods
Ammonia-cyclical cleaning method allows to obtain liquefied gas 100% iy sulfur dioxide and ammonium sulfate – products that can be widely used in the national economy. The amount of waste in this purification process is small.
The disadvantages of the method is the need to pre-deep cooling the flue gas before absorption of sulfur. Deep cooling is water that comes into direct contact with the hot gases and thus to 40-50 ° C. This water can not be discharged into public waterways, and recirculation of the cooling system requires the neutralization of the acid with lime and cooling tower. In the neutralization of the calcium salt form, which may crystallize in the cooling system. Cleaned the cooled gases require a significant amount of heat to warm them before release into the atmosphere.
Emissions of air from the cooling towers, cooling liquid flowing from scrubbers contain a certain amount of ammonia that can pollute the atmosphere. Additional consumption associated with the consumption of steam for regeneration of the solution, evaporation and drying of ammonium sulfate, the power consumption for the installation and fuel for heating the treated lawn make up about 10% of the fuel consumed by power plants. Seroulavlivayuschey equipment installation is pretty bulky and has a high cost.
Methods of using soda solution
The essence of this method consists of washing exhaust gases with aqueous solutions of soda ash. Thus reactions occur:
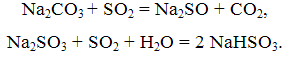
The process of absorption of SO2 soda solution is carried out in the apparatus or bubble packing types. The gas passes successively two towers, the first of which is irrigated with a solution of NaHSO3, the second – a solution of Na2SO3. Soda method provides a good cleaning of exhaust gases from SO2 while obtaining marketable salt NaHSO3 and Na2SO3.
The advantages of the techniques based on the use of aqueous solutions of sodium, are high cleaning efficiency, the lack of a solid absorbent component obtained as a waste product of the national economy substances.
The disadvantages of these methods include increased oxidation of salts in the cycle of sorption and regeneration, which leads to additional costs of the sorbent, the relative scarcity of the sorbent, the complexity of the technological scheme, higher steam consumption for regeneration in cyclic processes, increased corrosivity absorbent.
The acid-catalytic methods
The acid catalyst based on the method of delivery to the absorption zone of weak sulfuric acid (10-15 wt.%) Finding limited use.
Disadvantages of the method, an obstacle to its widespread distribution in the industry, refers slow oxidation of SO2 to sulfuric acid solutions, despite the use of different catalysts, as well as a sharp decrease in the activity of catalysts under the action of inhibiting organic impurities such as are present in gases FCS [5].
3.3 The absorption of sulfur dioxide by solid
Disadvantages of the wet waste gas cleaning methods of SO2 (temperature decrease and the gas stream discharged hydration, corrosion of equipment, the complexity and high installation cost) necessitated the development process based on the absorption of SO2 from gas streams and chemically active adsorbents sinks at a temperature above the dew point of the gas . Such works have been recently widely held in all industrialized countries. Many researchers believe the dry processes are very promising for cleaning waste gas, especially in the energy industry and non-ferrous metallurgy.
Capital costs for the construction of facilities for dry gas cleaning methods are generally lower, and operating costs are often significant. The terms of the regeneration of sorbents and cleaning exhaust gases of dust absorbing material associated with the appearance of mixed processes, which are used along with dry wet cycles.
3.4 Dry desulphurization methods
From dry desulfurization methods considered only processes using natural agents. There are also other dry methods such as the processes developed by "Bergbau Forshung," "OPS-Shell", etc. However, some of these technologies are complicated and unpromising in plants [6].
Dry additive method
The method consists in that the finely ground limestone is introduced into the boiler furnace. In this case, the limestone is burned (calcined) to form calcium oxide and carbon dioxide:

When the flue gas temperature 500 ... OS 900 interacts with the calcium oxide with sulfur dioxide to form calcium sulfite

Then, by the oxygen contained in the flue gases, part of the calcium sulfite to sulfate dookislyaetsya

After the boiler mixture of sulfite and calcium sulfate together with ash and unreacted lime is captured in the ash collectors.
This method was tested in many countries various modifications as posters, and industrial plants. Enter the additive into the furnace was carried out by different schemes:
- by addition to the fuel;
- nadfakelnoe blown into space;
- through the burners in the peripheral region of the flare.
Dry additive method technologically the simplest of all presently known methods for flue gas desulfurization. Compared with other methods, it requires the least capital and operating costs, is easy to implement in existing power plants. Deterrent to the use of the method is its low efficiency, accounting on average for 30 ... 40%. In addition, the possibility of applying the method are limited to the terms of bezshlakovochnoy screens and high-temperature furnace heating surfaces.
Due to the fact that the final product contains reactive sulfite waste disposal problem.
At the same time, on the basis of this method is the technology «SONOX» (Canada) in the power system «ONTARIO HYDRO», to simultaneously reduce emissions of oxides of sulfur and nitrogen. In it, the use of limestone as a reactant desulfurization efficiency is 70%, and 90% nitrogen removal level. When added to a slurry of limestone 5-percent additive dolomite stone seroochistnki efficiency was increased to 80% [7].
The method of «Lifaki»
The process of «Lifaki», developed by the Finnish company «Tampella» is essentially a combination of dry and semi-additive method seroulavlivaniya.
Schematic flow diagram of «Lifaki» is shown in Figure 2.
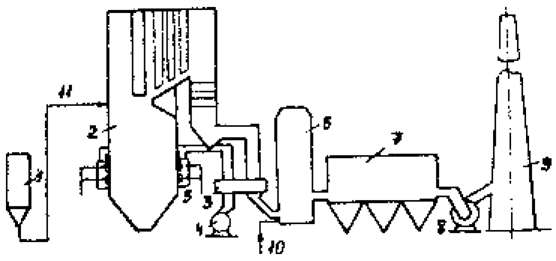
Figure 2 – Installation scheme «Lifaki»: 1 – limestone silo 2 – boiler, 3 – Regenerative Air 4 – The fan 5 – burners, 6 – activation reactor, 7 – electrostatic, 8 – ID fan, 9 – trumpet; 10 – a supply of water, 11 – Enter the limestone the furnace
Limestone and a fine dust fractions which 80% have a size less than 32 microns, is introduced via air nozzles in the flue gas stream at a temperature of 950 ... 1100 ° C. In this interval there are calcining limestone by reaction (1). Next to the binding path boiler of sulfur dioxide according to the reactions (2) and (3). Degree dioxide capture in this phase of the process is 30 ... 35%. At this stage, and does not aim to achieve the maximum degree of binding of SO2. It is equally important to ensure optimum calcination process - the maximum possible transition limestone, calcium oxide. With the change in the load zone of optimal calcination temperature gas moves. Therefore, the input nodes limestone advisable to carry at least two sections of the gas path.
After the boiler flue gas containing a mixture of solid substances in the form of ash, sulfite and calcium sulfate and unreacted lime fed to the activation reactor into which water is injected. Atomization of water to the optimum droplet size is provided by a system of nozzles, developed by Tampella.
In the reactor, burnt lime CaO due to contact with water to an active slaked, which connects with SO2 to form calcium sulfite:
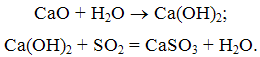
As the movement of the gas flow in the reactor liquid drops evaporate, the gas temperature decreases. At the outlet of the reactor is a mixture of dry ash sulphite and calcium sulphate, which is then trapped in an electrostatic precipitator or baghouse.
General purification reaches a molar ratio of Ca/S equal to 2 (Fig. 3). Cleaning efficiency is higher, the temperature of the stream close to the dew point.
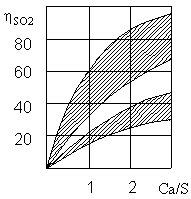
Figure 3 – The dependence of the degree of purification ηSО2 from flue gases of sulfur dioxide on the ratio of Ca/S [7]
The flue gas temperature in the reactor was maintained at 10 ... 15 °C above the dew point temperature that provides reaction products in dry form.
The composition of the final dry product during «Lifaki»:
- fly ash – 50...70;
- calcium sulphate – 10...15;
- calcium sulfite – 10...15;
The residue additive (СаО, СаСО3, Са(ОН)2) – 10...20.
The main objects of the automation of the process are as follows:
- enter the limestone adjusted depending on the amount of fuel delivered. Because the quality of the incoming fuel (sulfur content, moisture, ash, etc.) changes, the amount of limestone supplied is automatically adjusted by the concentration of SO2 in the flue gas after the boiler;
- the amount of water introduced into the reactor is regulated depending on the final temperature of the gases in the reactor in excess of 10 ... 15 °C dew point.
The high degree of automation of the unit, the remote control of equipment from the control panel reduces maintenance, carried out as a rule, only the crawler.
Additional space required are minimal, because the reactor is placed in a slightly modified flue boiler, which is especially important in the case of existing installations seroulavlivayuschimi equip thermal power plants. Capital and operating costs for installation "Lifaki" significantly lower costs desulphurization installation according to any other method [7].
4. Methods of experimentation
However, all the methods are not perfect in this connection there is a need for a universal absorber which could work in a wide range of temperatures and concentrations, and do not require further processing or disposal.
As such can act oxide absorber and calcium carbonate, the reaction process:
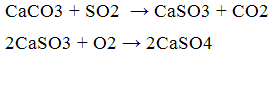
Also, use as an absorber carbonate and calcium oxide is rational for the following reasons:
- Presumably high reactivity with respect to the oxide of sulfur (IV);
- It does not require additional processing;
- Generation of heat, which can be used in the future.
Another important advantage of such sinks is its low cost, widespread in nature, as well as the ability to recycle waste production by getting soda. That, in turn, solves several problems, waste management, receipt of raw materials, absorbent, without extraction of natural resources. In this regard, this paper is very relevant and useful for a number of the above reasons.
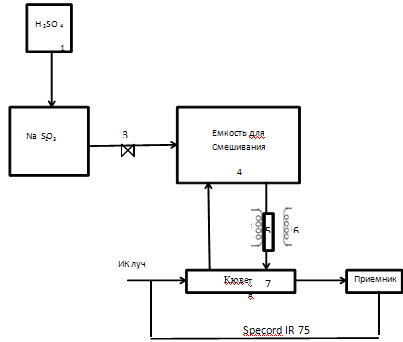
Figure 4 – Schematic diagram of the laboratory setup of the absorption of sulfur dioxide and oxides of calcium carbonate
In flask 2, which is a reaction vessel for obtaining sulfur dioxide filled weighed Na2SO3. The resulting SO2 through the dryer, which serves as Silicogel, pumped mixing container 3, which is 20 l. 4 cylinder needed to achieve a uniformly low concentrations of SO2 about 6 g/l. Further averaging gas passes through an absorption tube 5 placed in a tubular furnace 6, and the temperature of which varies over wide ranges. The gas passes through the cell 7, wherein the instrument (Specord IR 75) fixed SO2 content in the form of peaks on the spectrogram.
Next, the data are analyzed and the experiment is repeated.
Initially, the data held below.
For clarity, a table of temperatures interaction of calcium compounds and the activator.
Тable 2 – The temperature fusion activators and calcium compounds
The calcium compound | Аctivator | The reaction temperature of the activator and the calcium compound, оC |
СаСО3 | LiNO3 | 215 |
NaNO3 | 272 | |
СаО | LiNO3 | 210 |
NaNO3 | 260 |
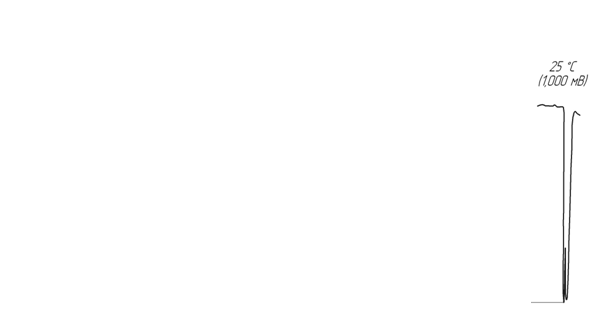
Figure 5 – IR spectra pogloschnniya SO2 activation LiNO3 – CaCO3 versus temperature
(Animation: 9 frames, 5 cycles of repetition, 16,3 kilobytes)
From these data, it is seen that the first and second portion the highest concentrations SO2 = 6 g/l. This suggests that the room temperature to 194 °C. No changes were observed, and at temperatures ranging from 194 ° C to + 210 ° C, an intense absorption of sulfur dioxide, as evidenced by reduction in peaks of SO2, and only the last portion E can watch the complete disappearance of the peak SO2. The completeness of absorption as evidenced by the fact that the sensitivity to IR spectroscopy SO2 is 0.09 mg/l.
Conclusion
References
- Ганз С.Н., Кузнецов И.Е. Очистка промышленных газов.– Киев, 1967
- Алиев Г.М.-А. Техника пылеулавливания и очистки промышленных газов. Справочник М.: Металлургия, 1986. – 544 с.
- Э.М. Соколов, В.М. Панарин, А.А. Зуйкова, Н.А. Криничная. Абсорбционно-каталитический способ очистки дымовых газов от диоксида серы [Электронный ресурс]. – Режим доступа: http://www.eco-oos.ru/biblio/konferencii/ekologiya-obrazovanie-i-zdorovyi-obraz-jizni/07/
- А.В. Гладкий «Абсорбционные методы очистки газов от двуокиси серы» / М. ЦИНТИХИМНЕФТЕМАШ, 1978.
- Абсорбционно-каталитический способ очистки дымовых газов от диоксида серы [Электронный ресурс]. – Режим доступа: http://works.tarefer.ru/94/100077/index.html
- Носков А.С., Пай З.П. Технологические методы защиты атмосферы от вредных выбросов на предприятиях энергетики. Аналит. обзор СО РАН, ГПНТБ, Институт катализа, Новосибирск, 1996. Вып.40.
- Кочетков А.Ю., Коваленко Н.А., Кочеткова Р.П. и др. Катализаторы жидкофазного каталитического окисления сернистых соелинений в сточных водах//Катализ в промышленности, 2003. № 4.
- В.И. Смола, Н.В. Кельцев «Защита атмосферы от двуокиси серы» / М. «Металлургия», 1976.