Реферат по теме выпускной работы
Содержание
- Введение
- 1. Актуальность темы
- 2. Цель и задачи исследования
- 3. Результаты исследования
- 3.1 Анализ процесса транспортировки горной массы технологического комплекса поверхности как объекта автоматизации
- 3.2 Критический анализ существующих технических решений
- 3.3 Разработка схемотехнического решения системы автоматического управления бункерно-транспортной цепью поверхности шахты
- Выводы
- Список источников
Введение
Горная масса из шахты скипом выдается на поверхность в приемный бункер, который расположен в надшахтном здании скипового ствола. Далее через распределительную воронку поступает в дробильно-сортировочное устройство, где горная масса распределяется на уголь и породу. Выданная на поверхность порода поступает на породный отвал.
Породный комплекс относится к технологическим объектам шахты с низким уровнем автоматизации. На данном объекте зачастую применяется малоэффективное ручное управление, которое приводит к существенным материальным затратам, и не исключает наличие аварийные ситуации. Таким образом, повышение уровня автоматизации породного комплекса является актуальной задачей.
1. Актуальность темы
Проблема транспортирования горной массы на породный отвал является комплексной, эффективность которой по большей части зависит от уровня применяемых технических решений.
Следует так же обратить внимание на ранее не принимавшееся во внимание изучение измерения массы породы в вагонетке при разгрузке бункера. Контроль этого параметра позволит снизить динамические нагрузки на электродвигатель лебедки; позволит обеспечить равномерное распределение породных масс в выработанном пространстве карьеров, зонах обрушения, ущельях, оврагах и т.п. с подветренной стороны населённых пунктов и промышленных площадок с целью уменьшения ущерба для окружающей среды.
Решить данные проблемы возможно при разработке системы автоматического управления бункерно-транспортной цепочки поверхности шахты.
2. Цель и задачи исследования
Целью исследования является повышение эффективности работы породного комплекса шахты за счет обоснования рациональных параметров и структуры системы автоматического управления бункерно-транспортной цепью поверхности шахты.
Для достижения поставленной цели необходимо решить следующие задачи:
- Анализ процесса транспортировки горной массы технологического комплекса поверхности как объекта автоматизации.
- Критический анализ существующих технических решений.
- Разработка схемотехнического решения системы автоматического управления бункерно-транспортной цепью поверхности шахты.
3. Результаты исследования
3.1 Анализ процесса транспортировки горной массы технологического комплекса поверхности как объекта автоматизации
Отвалы служат для складирования породы. Комплекс механизмов и сооружений, предназначенных для этой цели, именуются отвальным или хвостовым хозяйством. Отвалы различают:
1. По способу компоновки – высотные, образуемые на ровной местности, что загромождает поверхность, уничтожая пригодную для сельского хозяйства почву; глубинные, использующие овраги, балки, долины, заброшенные карьеры и другие углубления.
2. По виду оборудования – конвейерные; рельсовые; с подвесными канатными дорогами; с автомобильным транспортом; с гидротранспортом.
3. По форме штабеля – плоские; хребтовые; конические; коноидальные.
Уголь выдается на поверхность угольным скипом в приемный бункер, расположенный в надшахтном здании скипового ствола. Из бункера уголь подается через распределительную воронку в дробильно-сортировочное отделение, откуда через классификационный узел идет распределение на уголь и породу. Во всех угольных бассейнах страны порода складируется преимущественно в отвалы конической формы, оборудованные рельсовой канатной откаткой. Схема транспортирования породы на отвал приведена на рисунке 3.1
Для конических рельсовых отвалов (рис. 3.1) используют саморазгружающиеся вагонетки или скипы. В зависимости от производительности устраивают одно- и двухколейные рельсовые пути. Для перемещения сосудов применяют одно- и двухбарабанные лебедки. По мере заполнение отвала концевая ферма передвигается вперед при помощи домкрата или лебедки [1].
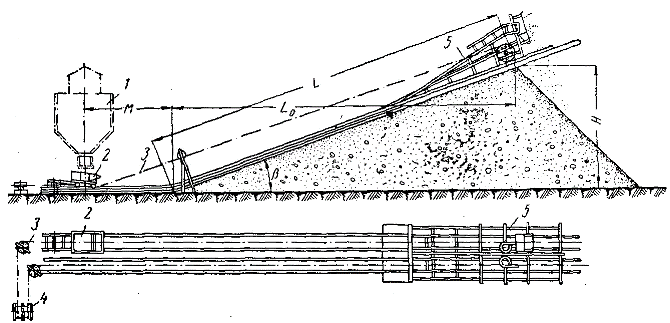
Рисунок 3.1 – Схема транспортирования породы на отвал: 1 – бункер, 2 – скип, 3 – канат, 4 – лебедка, 5 – разгрузочная ферма.
Технологическая схема доставки горной массы на отвал, приведена на рисунке 3.2.
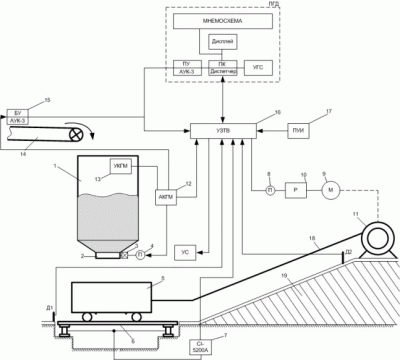
Рисунок 3.2 – Технологическая схема транспортировки горной массы на отвал
(анимация: 8 кадров, 7 циклов, 162 килобайт)
Горная масса в бункер 1 поступает с конвейера 14, который оборудован блоком управления 15 аппаратуры АУК-3 . При достижении верхнего уровня в бункере 1 порода поступает в вагонетку 5 через затвор 2, который оборудован приводом 3 и пусковой аппаратурой 4, и при достижении установленной максимальной массы, которая определяется весоизмерительной платформой 6, вагонетка направляется на отвал 18 за счет лебедки 11, которая оборудована приводным электродвигателем 9, пусковой аппаратурой 8 и регулятором скорости 10. С тензодатчиков весоизмерительной платформы [3] сигналы поступают на весовой индикатор типа CI-5200A [8], где сигналы усредняются, и далее поступают на устройство автоматической загрузки и транспортирования вагонеток УЗТВ 16. Контроль уровня горной массы в бункере осуществляется аппаратурой контроля горной массы АКГМ [9] с устройством контроля уровня горной массы УКГМ, которое устанавливается в специальное отверстие на верхнем перекрытии бункера. Также предусмотрены концевые датчики: датчик наличия вагонетки на загрузочной площадке Д1 и датчик положения вагонетки Д2, который предназначен для исключения переподъема вагонетки. Информация со всех датчиков поступает в устройство УЗТВ, которое обрабатывает полученную информация, вырабатывает управляющие воздействия, а также передает информацию на ПГД.
Пульт горного диспетчера включает в себя мнемосхему, промышленный компьютер ПК, пульт управления аппаратуры АУК-3, устройство оперативной связи УОС.
Процесс транспортирования породы может осуществляться как автоматически с учетом всех параметров и формированием команд автоматического управления затвором бункера, работы конвейера и движением вагонетки к местам погрузки и разгрузки, так и дистанционно оператором посредством пульта управления и индикации ПУИ 16, либо с пульта горного диспетчера
3.2 Критический анализ существующих технических решений
Проблема комплексной автоматизации работ породного комплекса в целом еще не решена, частично разработаны системы автоматизации и дистанционного управления отдельными механизмами и узлами породного комплекса.
Так, на некоторых шахтах переведены на дистанционное автоматизированное управление лебедки породных отвалов.
На шахтных террикониках обычно занято три и более рабочих в смену.
Автоматизация управления лебедкой позволяет сократить обслуживающий персонал до 1 человека в смену. При этом улучшается работа установки и повышается ее производительность.
Тип лебедки БЛ-1200 [10] с электродвигателем 75 кВт, 730 об/мин, 380 В. Электрическая схема автоматизированного управления лебедкой показана на рисунке 3.3.
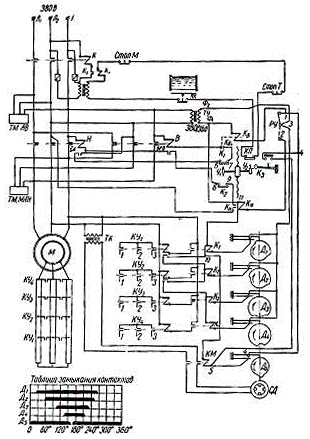
Рисунок 3.3 – Электрическая схема автоматизированного управления одноконцевой лебедкой террикона
Пускатель К установлен на главном вводе и служит общим пускателем установки. Пускатель В служит для включения электродвигателя установки при подъеме вагонетки, а пускатель Н – для включения электродвигателя установки при спуске вагонетки. Контакторная панель, состоящая из четырех пускателей ПМВ-1365 (КУ1, КУ2, КУЗ, КУ4), применяется для шунтирования пусковых сопротивлений в цепи ротора электродвигателя лебедки. Аварийный электромагнит ТМАВ удерживает груз аварийного тормоза, а электромагнит ТММАН – груз рабочего тормоза. Моторный коммутатор производит последовательное включение и выключение пускателей контакторной панели.
Концевые выключатели К1, К2 и КЗ, установленные на указателе глубины, имеют свои контакты 6-7 в цепи включающей катушки пускателя В; 8-9 – в цепи включающей катушки пускателя Н; 4-5 – в цепи пускателя КМ и срабатывают в зависимости от положения гайки указателя глубины. Кнопка КП установлена на индикаторе глубины и имеет свои контакты в цепи общего пускателя К. Трехполюсный рубильник РУ служит для ручного пуска установки. Кнопки «Стоп», Т и М служат для аварийного торможения установки при отказе средств управления тормозными устройствами. Контакторное устройство, предcтавляющее собой металлическую пластинку, размещается под барабаном лебедки и укрепляется на кронштейнах таким образом, что при восприятии нагрузки от провисающего каната пластинка опускается. При опускании пластины размыкаются контакты ПК, которые включены в цепь управления пускателя К.
Пускатель КМ, служащий для включения моторного коммутатора, срабатывает вначале хода вагонетки при замыкании рубильников РУ (положение I) и концевого выключателя К3 – в конце рабочего хода [2].
Взрывобезопасное реле с искробезопасными цепями управления типа ИКС-1 предназначено для автоматического контроля заполнения угольных и породных бункеров. Это реле может применяться также для автоматического управления шахтными установками в качестве путевого или конечного выключателя со щеточными датчиками.
Реле типа ИКС-1 представляет собой панель, на которой смонтированы следующие элементы
1. Поляризованное реле типа РП-5. Катушка реле имеет две обмотки, из которых одна 4600 витков с омическим сопротивлением 700 Ом.
2. Исполнительное реле типа РПТ-100М2 с катушкой на 36 В. Подвижные контакты исполнительного реле выполнены в виде мостиков со сферическими контактами из серебра и имеют моментное переключение. Неподвижные контакты представляют собой латунные пластинки с плоскими цилиндрическими контактами из серебра.
3. Трансформатор питания с первичной обмоткой на 127 В и двумя вторичными обмотками.
4. Селеновый выпрямитель собранный из четырех столбиков типа АВС-7-4 с 18 шайбами диаметром 7 мм в каждом.
5. Селеновый шунт, состоящий из двух плеч, с 4 шайбами диаметром 18 мм в каждом плече
6. Конденсатор металлобумажный емкостью 2 мкФ 250 В.
7. Выключатель, служащий для переключения катушек реле РП-7 при контроле больших или малых сопротивлений.
8. Переключатель напряжения питания искробезопасной цепи.
9. Два предохранителя.
10. Пакетный выключатель.
Электрическая схема реле ИКС-1 представлена на рисунке 3.4.
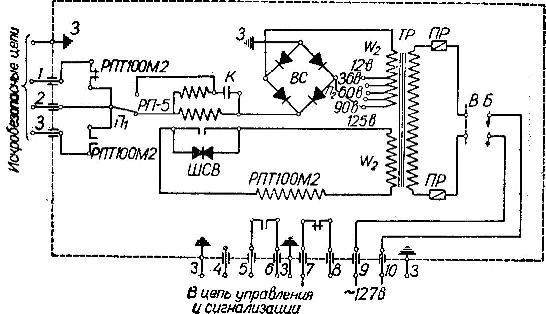
Рисунок 3.4 – Принципиальная схема реле типа ИКС-1
Через переключатель на высокоомную обмотку трансформатора включены обмотки высокочувствительного поляризованного реле РП-5. Параллельно обмоткам реле РП-5 включен конденсатор К емкостью 2 мкф, выполняющий роль фильтра. При помощи выключателя П1 можно включать в цепь управления одну обмотку реле РП-5 для контроля малых сопротивлений либо две обмотки последовательно – для контроля больших сопротивлений. Контакт реле РП-5 включен в цепь питания исполнительного реле РПТ-100М2. Параллельно контактам реле РП-5 включен встречный селеновый шунт, защищающий контакты от чрезмерного электрического износа.
Величина напряжения, необходимая для контроля заданного сопротивления, определяется из таблицы, укрепленной на верхней панели аппарата. Требуемое напряжение устанавливается при помощи переключателя П2.
К зажимам 1 и 2 искробезопасной цепи контроля подводится провод от трубчатого датчика (рис. 3.5), укрепляемого непосредственно в бункере. Электрод может быть расположен в 500-600 м от места установки реле ИКС-1. К зажимам цепи управления и сигнализации реле могут подключаться катушки пусковых устройств конвейеров или других механизмов, производящих загрузку бункера, и сигнальные устройства (сирены, лампы).
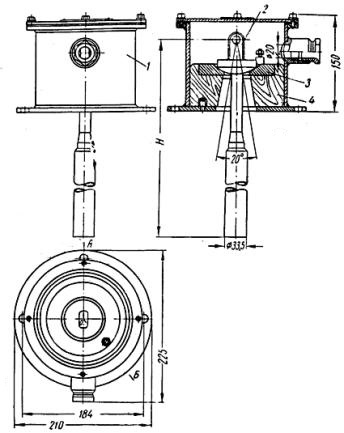
Рисунок 3.5 – Датчик трубчатый электродный: 1 – корпус; 2 – электрод; 3 – подпятник; 4 – изолятор.
При использовании реле ИКС-1 для контроля подвижного состава применяется щеточный датчик типа ДЩ-1, общий вид которого показан на рисунке 3.6 [3].
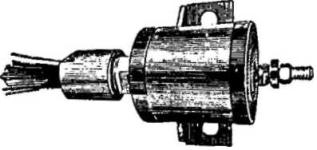
Рисунок 3.6 – Щеточный датчик типа ДЩ-1
К достоинствам можно отнести: дешевизну и простоту исполнения.
К недостаткам данного реле можно отнести: не высокую надежность при контроле подвижного состава , т.к. материал «щетки» имеет свойство стираться и выгибаться, что может привести к неточным показаниям; датчик трубчатый электродный под действием агрессивной окружающей среды может деформироваться, исходя из конструкции датчика при попадании в корпус пыли или мелких частиц породы может происходить залипание чувствительного элемента, что может привести к переполнению бункера и недостоверным показаниям датчика.
3.3 Разработка схемотехнического решения системы автоматического управления бункерно-транспортной цепью поверхности шахты
В соответствии с технологической схемой транспортировки горной массы на отвал была составлена структурная схема системы автоматического управления бункерно-транспортной цепью поверхности шахты, которая приведена на рисунке 3.7
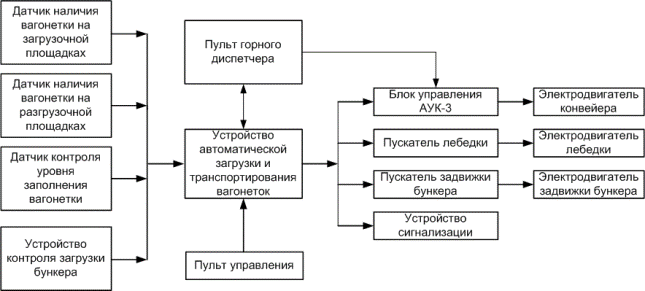
Рисунок 3.7 – Структурная схема системы автоматического управления бункерно-транспортной цепью поверхности шахты
Согласно структурной схеме системы автоматического управления бункерно-транспортной цепью поверхности шахты разработано устройство автоматической загрузки и транспортирования вагонеток, структурная схема которого приведена на рисунке 3.9
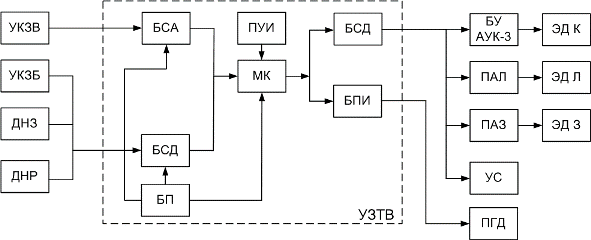
Рисунок 3.8 – Структурная схема устройства автоматической загрузки и транспортирования вагонеток
Данное устройство работает следующим образом: информация с аппаратуры контроля горной массы (АКГМ), датчиков наличия вагонетки на загрузочной (ДНЗ) и разгрузочной (ДНР) площадках, через блок согласования дискретных сигналов (БСД), а информация с устройства контроля загрузки вагонетки (УКЗВ) через блок согласования аналоговых сигналов (БСА) поступает на микроконтроллер (МК). В МК обрабатывается поступившая информация и вырабатывается управляющее воздействие. Информация о текущем состоянии процессов объекта передается через блок передачи информации (БПИ) на пульт горного диспетчера (ПГД). В случае достижения верхнего уровня в бункере отключается конвейер, оборудованный блоком управления аппаратуры АУК-3 и опрашивается ДНЗ: если вагонетка отсутствует на загрузочной площадке, тогда через пусковую аппаратуру привода лебедки (ПАЛ) включается лебедка и доставляет вагонетку на загрузочную площадку, затем подается сигнал на пусковую аппаратуру привода задвижки бункера (ПАЗ), задвижка открывается и вагонетка наполняется до тех пор, пока УКЗВ не выдаст сигнал о том, что достигнута уставка массы. Затем на ПАЗ подается сигнал на закрытие бункер. Включается лебедка и поднимает вагонетку на отвал. Для того, чтобы вагонетка не проехала место разгрузки, в конце подъема устанавливается ДНР, который при срабатывании будет свидетельствовать о прибытии вагонетки. Данным процессом можно управлять как непосредственно с пульта управления (ПУИ), так и удаленно с пульта диспетчера (ПГД).
Выводы
Таким образом, предложенное устройство позволяет существенно повысить уровень автоматизации объектов, участвующих в процессе транспортирования горной массы на отвал, обеспечить контроль количества горной массы, загружаемой в вагонетку, что позволяет стабилизировать усилия на приводном двигателе и подъемном канате. Это обеспечивает снижение энергозатрат на транспортирование, равномерность распределения горной массы на отвале и снижение вероятности аварийных ситуаций.
Новым в предложенной системе является наличие автоматического измерения массы породы в вагонетке при разгрузке бункера. Измерение массы породы в вагонетках позволит снизить динамические нагрузки на электродвигатели лебедки (так как при превышении нормы загрузки вагонеток возникает повышенная нагрузка на систему подъема, что приводит к перерасходу электроэнергии, к излишним экономическим затратам в случае выхода из строя элементов, входящих в состав лебедки).
Принцип работы данной автоматизированной системы заключается в минимизации человеческого фактора на погрузочные и транспортные работы, ускорить процесс погрузки, увеличить точность показаний веса транспортируемой горной массы и осуществлять ее подсчёт.
завершение: декабрь 2013 года. Полный текст работы и материалы по теме могут
быть получены у автора или его руководителя после указанной даты.
Список источников
- Кузнецов Б.А., Ренгевич А.А., Шорин В.Г. Транспорт на горных предприятиях. Изд. 2–е, перераб. и доп. М., «Недра», 1976. – 552 с.
- Авласенко Ю.Г., Ковалевский М.М. Автоматизация шахтных установок. Государственное издательство технической литературы УССР, Киев 1958. – 296 с.
- Вагонные весы [Электронный ресурс] – Режим доступа: http:www.etalon–ves.ru
- Евстифеев А.В. Микроконтроллеры AVR семейств Tiny и Mega фирмы ATMEL, 5–е изд., стер. – М.: Издательский дом «Додэка–XXI», 2008. – 560 с.
- Автоматизація технологічних об’єктів та процесів. Пошук молодих. Збірник наукових праць ХІІ науково–технічної конференції аспірантів та студентів в м. Донецьку 17–20 травня 2012 р. – Донецьк, ДонНТУ, 2012. – 300 с. Статья Ананичев В.В., студент; Жовтобрух С.А. Автоматизация процесса транспортирования породы на отвал.
- Горлова А.А. Исследование динамических процессов пуска электропривода одноконцевой откатки и разработка устройства автоматического управления его разгоном. Автореф. магистерской работы. [Электронный ресурс] – Режим доступа: Портал магистров ДонНТУ, Факультет КИТА, 2011 г.
- Коваленко Е.А. Разработка автоматизированной системы управления углепогрузочным комплексом поверхности шахты. Автореф. магистерской работы. [Электронный ресурс] – Режим доступа: Портал магистров ДонНТУ, Факультет ЭМА, 2004 г.
- Основные характеристики весового терминала с функцией дозирования CAS CI–5200A. [Электронный ресурс] – Режим доступа: СI–5200A
- Научно–технический центр проблем энергосбережения. [Электронный ресурс] – Режим доступа: АКГМ
- Техническая характеристика лебедки БЛ–1200. [Электронный ресурс] – Режим доступа: БЛ–1200