Реферат по теме выпускной работы
Содержание
- Введение
- 1. Актуальность темы
- 2. Цель и задачи исследования
- 3.Результаты исследования
- 3.1 Анализ технологического процесса работы очистного комбайна, как обьекта автоматизации
- 3.2 Критический анализ существующих технических решений
- 3.3 Разработка схемотехнического решения системы автоматического управления очистным комбайном
- Выводы
- Список источников
Введение
Основным технологическим процессом в шахте является процесс выемки угля (очистные работы). Поэтому ему уделяется множество разработок и исследований, направленных на контроль и управление данным процессом. Очистные работы – совокупность работ, выполняемых в подземной очистной выработке c целью добычи полезного ископаемого. Ha современных угольных шахтах очистные работы – комплекс процессов и операций: очистная выемка (разрушение полезной толщи c отделением полезного ископаемого от массива и навалкой его на транспортирующее устройство); доставка полезного ископаемого к транспортной выработке; перемещение в очистной выработке транспорта и выемочного оборудования; крепление горной выработки (очистной), управление горным давлением в очистной выработке. Ha современных рудных шахтах очистные работы обычно включают: отбойку – отделение руды от массива и дробление при этом на куски; доставку рудной массы до транспортной выработки; вторичное дробление руды, т.e. измельчение негабаритных кусков в выемочном блоке; иногда закладку или крепление очистного пространства [12].
В роли устройства выполняющего непосредственно отделение горной массы выступает очистной комбайн. Он требует большого внимания в плане автоматизации и постоянной модернизации.
1. Актуальность темы
На современном рынке угольной промышленности наблюдается тенденция к повышению качества добываемой горной массы и минимизация затрат. Это в свою очередь вызывает необходимость в модернизации существующих очистных комплексов, создания различных систем автоматизации, осуществляющих управление основными процессами очистных работ. Для управления все этими процессами необходимо совершать сбор, контроль и управление основными параметрами данных процессов.
Контроль существующих параметров ведет к дальнейшему управлению основными функциями очистных работ, и в последующем, работу добычного участка без человека. Безлюдная выемка угля является перспективной и продуктивной отраслью развития автоматизации. Это связано с тем, что безлюдная выемка угля сводит работу человека к минимуму и практически исключает из процесса работы забоя человеческий фактор.
Кроме того, актуальной проблемой является повышение качества добываемой горной массы. Как известно, на сегодняшний день добываемый на шахтах Украины уголь характеризуется существенной зольностью. Это снижает энергетические параметры добываемого угля, вызывает необходимость в обогащении. Актуальной задачей, является разработка аппаратуры, способной повысить экономический эффект добываемой горной массы, а именно увеличить удельный вес угля в ней.
2. Цель и задачи исследования
Основной целью данного исследования является повышение эффективности работы очистной машины (комбайна) за счет разработки автоматической системы сбора основных технологических параметров работы очистного комбайна, и на основании данных параметров, осуществление управляющих воздействий на составные части горной машины.
В результате анализа данной задачи выдвинут следующий ряд задач:
1. Автоматическое поддержание оптимального режима работы; оптимизация процесса разрушения угля по критерию минимальной интенсивности исчерпания механического ресурса; минимизации удельной энергоемкости резанья угля; снижение амплитуд колебания моментов; ограничение медленных и защита от опасных экстренных механических перегрузок; выравнивание нагрузок между приводами.
2. Автоматический выбор и оптимально направленное движение машины вдоль забоя с учетом изменения мощности и гипсометрии пласта.
3. Автоматическое выполнение операций, заданных программой цикла работы, а также последующее выполнение повторных циклов.
3. Результаты исследования
3.1 Анализ технологического процесса очистных работ, как обьекта автоматизации
Для достижения поставленной цели система автоматизации технологического процесса очистных работ предполагает наличие следующих подсистем автоматизации:
– подсистема управления добычной машиной;
– подсистема управления транспортными средствами;
– подсистема управления креплением выработанного пространства;
– подсистема контроля и управления аэрологической средой и безопасным ведением работ.
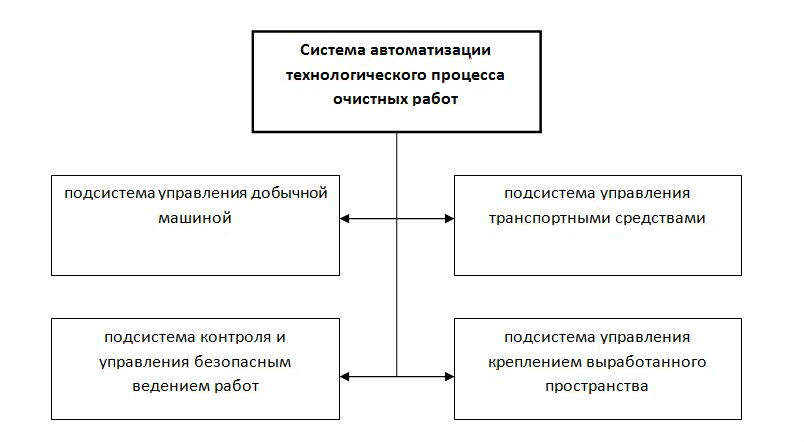
Рис. 3.1 – Структурная схема автоматизации очистного забоя
В данном случае, рассматривается только подсистема управления добычной машиной.Подсистема управления добычной машиной выполняет следующие функции:
– местный и дистанционный контроль очистным комбайном, а именно вынесенной системой подачи (ВСП) и исполнительными органами резания;
– автоматическое управление перемещением комбайна вдоль забоя с учётом изменения мощности и гипсометрии пласта.
Сама добычная машина, в данном случае очистной комбайн имеет следующий вид, указанный на рисунке 3.2.
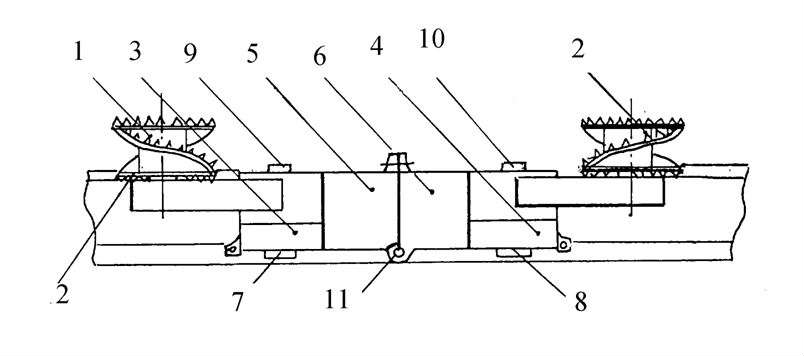
Рис. 3.2 – Горный комбайн УКД 200–250
Очистной комбайн – это горная машина, производящая отделение горной массы (полезного ископаемого) от массива пласта и выполняющая погрузку ее на транспортную машину.
На данном рисунке 3.2 указанно: 1, 2 – шнеки, 3, 4 – механизмы подачи 5, 6 – электродвигатели, 7, 8 – завальные лыжи, 9, 10 – убойные лыжи, 11 – шарнир.
Комбайны, как правило, работают с рамы забойного конвейера, имеющегося у забоя (за исключением комбайнов для выемки пластов мощностью менее 0,8 м).Процесс добычи угля очистным комбайном представлен на рисунке 3.3.
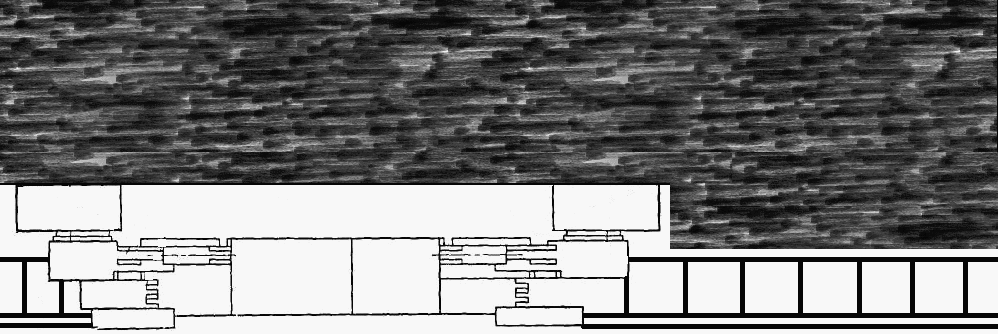
Рис. 3.3 – Процесс добычи угля очистным комбайном (анимация: 6 кадров, 3 цикла повторения, 206 килобайт)
Структурная схема аппаратуры автоматизации очистного комбайна приведена на рисунке 3.4.
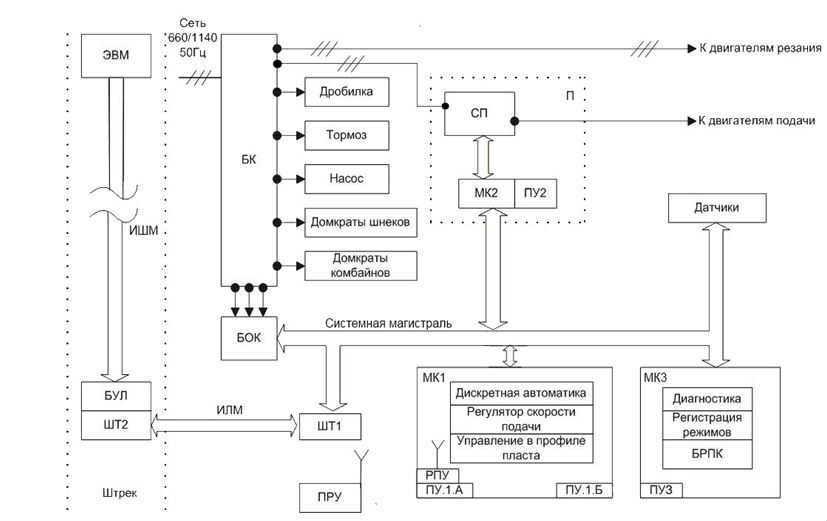
Рис. 3.4 – Структурная схема автоматизации очистного комбайна
Она включает в себя три контроллера, связанные между собой магистральной линией, блок коммутации, преобразователь частоты привода подачи очистного комбайна, шинные терминалы, блок управления, искробезопасную шахтную и лавную магистраль (ИШМ), центральную диспетчерскую ЭВМ на поверхности шахты.
Контроллер МК1 выполняет функцию включения и выключения оборудования добычного комбайна, регулирование скорости комбайна в зависимости от нагрузки электродвигателей резания, управление шнеками комбайна в профиле пласта.
Контроллер МК2 осуществляет управление преобразователем (СП) двигателей подачи по командам поступающим с контроллера МК1.
Контроллер МКЗ осуществляет диагностику оборудования комбайна.
В МК3 осуществляется обработка данных и их последующий анализ [3].
3.2 Критический анализ существующих технических решений
Далее рассмотрим более детально существующую аппаратуру автоматизации комбайна для очистного комбайна УКД-200 (рис. 3.2), а именно автоматическое регулирование скорости подачи и нагрузки режущих органов.
Регулятор Уран-1М
Наиболее распространенной системой автоматического регулирования нагрузки резания очистного комбайна является регулятор УРАН-1М. Регулятор имеет два канала: скорости и нагрузки, которые совместно работают на устройства выхода. К каналу нагрузки относятся: датчик тока, программа тока и импульсное устройство. В блоке канала нагрузки сравниваются напряжение пропорциональное фактическому току двигателя Iд и напряжение программы токовой уставки. При разности этих значений пределах ± 5% Iу регулятор по каналу нагрузки не работает (зона нечувствительности). При разности значения в пределах 5–25% больше Iу из блока контроля нагрузки в блок контроля скорости выдается напряжение Uн на импульсное уменьшение скорости подачи до значения установления тока Iд в пределах ±5% Iу. Если рассогласование тока Iд больше 25% тока Iу, то блок БКН выдает непрерывный сигнал на уменьшение скорости подачи. При недогрузе двигателя комбайна, т.е. когда Iу >> Iд, блоком БКН выдается напряжение на увеличение скорости подачи до значения, установленного программой скорости.
К основным недостаткам данного технического решения относится отсутствие учета гипсометрии пласта и осуществление регулирования за счет изменения скорости подачи, а не непосредственно изменения положения рабочих органов.
Аппаратура управления и автоматизации КДА очистного комбайна типа УКД200
Аппаратура предназначена для управления механизмами очистных комплексов КД-80, КМ-103 и вынесенной системы подачи (ВСП) комбайнов КА-80, К-103М, 1К101УД, ГШ200В, УКД3, УКД-200 по вспомогательным жилах силового кабеля комбайна или с использованием дополнительного кабеля, проложенного по лаве от комбайна на штрек, обеспечение заданных режимов работы (нагрузки и скорости подачи) комбайна с ВСП и защиты их электродвигателей.
Аппаратура рассчитана на эксплуатацию в макроклиматических районах с холодным, умеренным и тропическим климатом и изготавливается в климатических исполнениях "УХЛ" и "Т" категории 5. Может применяться в шахтах, опасных по газу или пыли, в составе электрооборудования очистного участка и работать совместно с магнитными пускателями или станциями управления с различными типами аппаратуры сигнализации и громкоговорящей связи (КУЗ) [11].
К недостаткам данной аппаратуры можно отнести малую надежность, связанную с использованием старых интегральных микросхем.
3.3 Разработка схемотехнического решения системы автоматического управления очистным комбайном
Основой разрабатываемой системы автоматизации очистного комбайна является принцип автоматического контроля всех основных параметров очистного комбайна, обработка и передача данных, для дальнейшей визуализации на пульте диспетчера, необходимых для нормальной работы очистного комбайна. А также, в случае автоматического управления, выдачи устройством управляющих команд на основные технологические объекты.
Разрабатываемая система предполагает два режима работы:
1) «Автоматический контроль» – этот режим предполагает автоматический опрос датчиков, установленных на очистном комбайне, и передачу данных на разрабатываемое устройство, а также автоматическую выдачу управляющих команд на регуляторы;
2) «Дистанционный контроль» – данный режим предполагает автоматический опрос датчиков установленных на очистном комбайне, передачу и обработку данных, и выдачу визуального состояния объекта, а также в случае аварийного состояния работы, подачу предупредительной и аварийной звуковой и световой сигнализации.
В основу регулирования системы, положена система регулирования частоты питающей сети, посредством которого, будут регулироваться основные параметры работы технологических установок, такие как скорость, ток, температура двигателей. Кроме того, предполагается автоматическое регулирование положения органов резания по профиля пласта.
Была создана модель в среде Matlab, которая моделирует работу всей вынесенной системы подачи очистного комбайна с преобразователем частоты в цепи приводного асинхронного двигателя с короткозамкнутым ротором. Асинхронный двигатель в фазных координатах описан следующей системой дифференциальных уравнений:
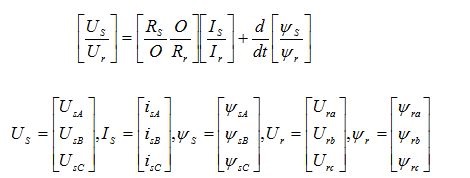
Модель реализована несколькими подсистемами, указанными на рисунке 3.5. Подсистема 1 моделирует питающую сеть асинхронного двигателя с преобразователем частоты; подсистема 2 представляет собой непосредственно асинхронный двигатель с к.з. ротором. При моделировании учитывался рабочий орган комбайна (подсистема 3). Для его имитации Мс изменялся случайным образом, что позволило моделировать прохождение рабочего органа комбайна через породу или уголь. Для этого был рассчитан момент сопротивления двигателя при прохождении рабочего органа через уголь или породу и при работе модели происходило случайное переключение между указанными значениями с определенной временной задержкой.
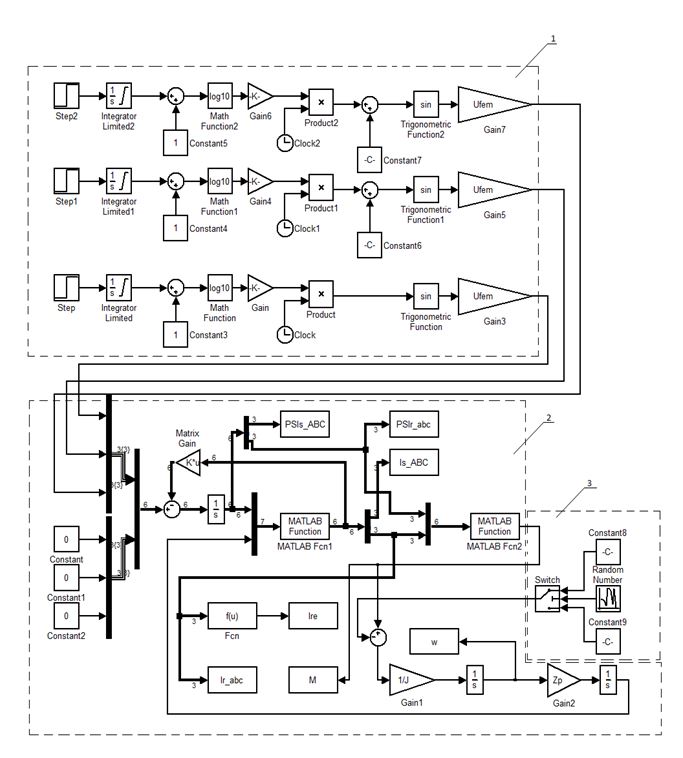
Рис. 3.5 – Модель ВСП комбайна с преобразователем частоты
Были получены следующие зависимости скорости, тока, электромагнитного момента и момента сопротивления от времени.
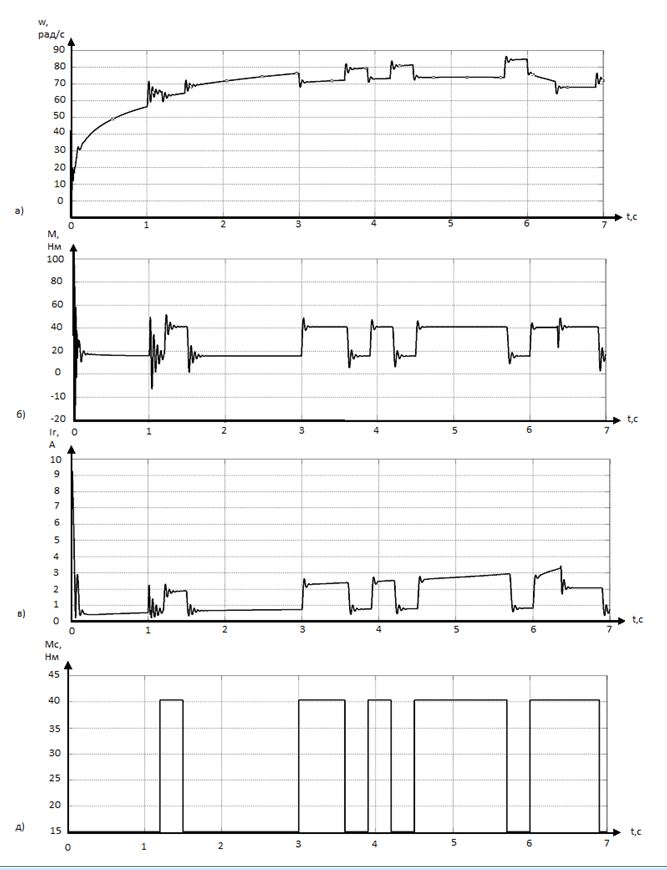
Рис. 3.6 – Зависимости скорости (а), электромагнитного момента (б), тока ротора (в) и момента сопротивления (д) от времени
График на рисунке 3.6 (д) отображает изменение гипсометрии пласта, т.е. прохождения рабочего органа комбайна через породу или уголь. На промежутке, когда момент равен 15Нм рабочий орган комбайна проходит через уголь, а при 40Нм – через породу. И в зависимости от этого изменяется величина электромагнитного момента, скорость и частота вращения двигателя.
Приведем функциональную схему разрабатываемого устройства автоматизации работ очистного комбайна на рисунке 3.6.
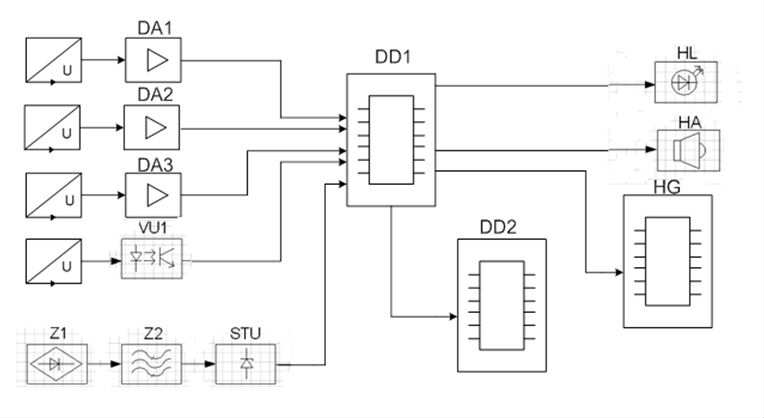
Рис. 3.7 – Функциональная схема разрабатываемой системы автоматизации очистного комбайна
На рисунке указаны: Z1, Z2, STU – соответственно выпрямитель, фильтр и стабилизатор напряжения(БП); DD2 – интерфейс RS–485, предназначен для передачи управляющих воздействий на соответствующие технологические цепочки; для выдачи аварийной сигнализации предусмотрена звуковая сигнализация НА; для визуального контроля предусмотрена индикация HL; VU1 – гальваническая развязка (оптопара); DA1–DA3 – операционные усилители, для аналоговых сигналов (напряжения, тока и усилия соответственно); DD1 – микроконтроллер; HG – жидко-кристаллический индикатор.
Выводы
Таким образом, в результате проведенной работы было выполнено проектирования комплекса контроля и управления состоянием системы добычных работ. Для устройства автоматизации объектом которого является очистной комбайн, были выдвинуты требования, описаны основные функции, которые он выполняет, а также существующие решения по его автоматизации, их достоинства и недостатки.
Основной целью данных исследований является разработка такой системы автоматизации, которая способна повысить эффективность ведения очистных работ и минимизировать затраты на их проведение и обслуживание.
При написании данного реферата магистерская работа еще не завершена. Окончательное завершение: январь 2013 года. Полный текст работы и материалы по теме могут быть получены у автора или его руководителя после указанной даты.
Список источников
- Квантович Л.И. Горные машины: Учебник для техникумов / Л.И. Квантович., В.Н. Гетопанов. – М.: Недра, 1989. – 304 с.
- Никулин Э.К. Методические указания к выполнению лабораторных работ по дисциплине технические средства автоматизации / Е.К.Никулин., А.С. Оголобченко. – Д.: ДонНТУ, 2005. – 81 с.
- Евстифеев А.В. Микроконтроллеры AVR семейств Tiny и Mega фирмы ATMEL / А.В. Ефтисеев. – М.: Издательский дом «Додэка-XXI», 2008. – 560 с.
- Кобус А.Д. Датчики Холла и Магниторезисторы / А.Д. Кобус, Я.В. Тушинский. – М.: Энергия, 1971. – 351 c.
- Опадчий Ю.Ф. Аналоговая и цифровая электроника / Ю.Ф. Опадчий, А.П. Глудкин. – М.: Недра, 2002. – 306 c.
- Морозов В.И. Очистные комбайны. Справочник / В.И. Морозов. – М.: Горная книга, 2006. – 650 с.
- Маренич К.Н. Асинхронный электропривод горных машин с тиристорными коммутаторами / К.Н. Маренич. – Д.: ДонГТУ, 1997. – 64 с. Li>
- Герман-Галкин С.Г. Matlab & Simulink. Проектирование мехатронный систем на ПК / С. Герман-Галкин. – СПб.: КОРОНА-Век, 2008. – 368 с.
- Черный А.П. Моделювння электромеханических систем: Учебник / А.П. Черный, А.В. Луговой, Д.И. Родькин, Г.Ю. Сисюк, А.В. Садовой. – Кременчуг: Энерго, 2001. – 410 с.
- Петров Л.П. Тиристорные преобразователи напряжения для асинхронного электропривода / Л.П. Петров, А.А. Андрющенко, В.И. Капинос. – М.: Энергоавтомиздат, 1986. – 200 с.
- ООО НПП Украинская Энергетическая компания [Электронный ресурс]. Режим доступа: http://ukrenergy.com.ua/ka-80 ...
- Горная эециклопедия [Электронный ресурс]. Режим доступа: http://www.mining-enc.ru ...