Реферат по теме выпускной работы
Содержание
- Введение
- 1. Актуальность темы
- 2. Цель и задачи исследования
- 3. Существующие способы сушки
- Выводы
- Список источников
Введение
Согласно Энергетической стратегии Украины, объем внутреннего потребления угля к 2015 году должен увеличиться до 98,7 млн т. Такие же тенденции проявляются в энергетически развитых экономиках Германии, США, ЮАР, Китая, Англии и даже «газовой империи» – России. Потому что, в отличие от нефти и газа, запасы угля распределены по странам и регионам более равномерно и поставки угля менее подвержены геополитической конъюнктуре. На тепловых электрических станциях Украины в основном используют в качестве топлива уголь, причем не лучшего качества, поэтому целесообразно правильно организовать подготовку топлива перед сжиганием, для более надежной работы электростанций.
1. Актуальность темы
Подсушка топлива перед размолом благоприятно сказывается на работе мельниц. Производительность молотковых мельниц увеличивается на 20% по сравнению с мельницами, работающими на сыром топливе, приблизительно в 2 раза увеличился ресурс бил.; Снижение размольной производительности мельниц при увеличении влажности топлива можно объяснить тем, что размол влажного топлива осуществляется при наличии большого количества пластических деформаций, затрудняющих получение готовой угольной пыли. По данным ВТИ установлено, что чем больше отличие влажности размалываемого топлива от величины гигроскопической влажности, тем больше снижение размольной производительности мельниц. Предварительная подсушка топлива со снятием части внешней влаги всего на 3-5 % резко улучшает его сыпучие свойства, устраняются трудности транспортирования угля на трактах топливоподачи и его движения в бункерах, увеличивается теплота сгорания топлива. Таким образом, предварительная подсушка угля является составной частью его обогащения и решения вопросов, повышения надежности работы оборудования топливоподачи, пылесистем и в конечном итоге всей котельной установки. Сжигание в кипящем слое — одна из технологий сжигания твёрдых топлив в энергетических котлах. Топки с кипящем слоем не чувствительны к качеству топлива, поэтому в них сжигают шлам – отходы продуктов обогащения. Шлам имеет большую влажность, поэтому перед сжиганием его необходимо просушить до влажности не более 10%. Подсушка топлива является одной из основных энергоемких операций по облагораживанию угля. В связи с этим разработка рациональных схем подсушки является важным направлением повышения экономичности современных энергоблоков.
2. Цель и задачи исследования
Цель: Оптимизации управления сушкой для снижения энергозатрат. Разработка математической модели процесса сушки в барабанной сушилке для выявления условий энергоэффективного использования оборудования. Разработка мероприятий, обеспечивающих безопасность сушки.
Для решения данной цели необходимо решить следующие задачи:
- Провести анализ состояния вопроса сушки сыпучих материалов;
- Выбрать метод исследования;
- Разработать рекомендации по улучшению процессов сушки;
- Рассмотреть меры безопасности при сушки, способы тушения пожаров.
3.Существующие способы сушки
Сушкой называется термический процесс удаления из твердых материалов содержащейся в них влаги. Сушка – сложный технологический процесс, зависящий от большого числа факторов, знание которых существенно для анализа и расчета процесса. Интенсивность сушки зависит от ряда факторов, свидетельствующих о сложности реального процесса сушки, о трудности получения для него адекватного математического описания. Наибольшее влияние на процесс сушки оказывают факторы, определяющие высушиваемый материал как объект сушки. Они характеризуют сопротивляемость материала переносу влаги внутри него и сего поверхности в окружающую среду, способность материала воспринимать подводимое к нему тепло. К таким факторам относятся его внутренняя структура, теплофизические свойства, форма, размер. Наиболее сильное влияние оказыает внутренняя структура материала.
По способу подвода тепла различают следующие типы сушилок:
а) конвективные, когда тепло, необходимое для испарения влаги передается от воздуха, топочных газов или перегретого пара сушимому материалу путем непосредственного соприкосновения (конвекции)
б) кондуктивные, когда тепло передается к сушимому материалу через стенку.
в) радиационная сушка – влага удаляется путем воздействия электромагнитных волн.
г) сушка в поле токов высокой частоты – благодаря повышению температуры внутри материала влага испаряется.
Масса влаги, которую может принять сушильный агент, зависит от содержания в нем водяного пара, его температуры и давления. Выбор сушильного агента имеет большое значение, так как стоимость расходуемого тепла значительно сказывается на экономичности сушильных установок. По конструктивному исполнению различают сушилки барабанные, трубы-сушилки, сушилки кипящего слоя, распылительные и другие.Таблица 1
Классификация сушилок
Признак классификации | Типы сушилок |
Способы подвода тепла к материалу | Конвективные, контактные, радиационные, электрические |
Давление в рабочем пространстве | Атмосферные, вакуумные |
Способ действия | Периодического или непрерывного действия |
Сушильный агент | Воздух, топочные газы, смесь воздуха с топочными газами, перегретый пар и инертные газы |
Направление движения сушильного агента относительно материала | С прямотоком, противотоком, перекресным током и реверсные |
Характер циркуляции сушильного агента | С естественной и принудительной циркуляцией |
Способ нагрева сушильного агента | С паровыми воздухоподогревателями, огневыми воздухоподогревателями, путем смешения с топочными газами, с электронагревом |
Схема нагрева сушильного агента | С центральным подогревом, с подогревом индивидуальными агрегатами и с промежуточным подогревом |
Кратность использования сушильного агента | Однократные и с рециркуляцией |
Способ удаления влаги из сушилки | С воздухообменом, конденсационные, с химическим поглощением влаги |
Конструкции сушилки | Коридорная, камерная, шахтная, ленточная, конвейерная, барабанная, трубчатая и т.п. |
Чаще всего при сушке различного минерального сырья используют барабанные сушилки.
Различают барабанные сушилки с прямым, косвенным и комбинированным теплообменом. В сушилках с прямым теплообменом обеспечивается непосредственный контакт влажного материала с нагретыми газами. Сушилки работают по прямоточной и противоточной схемам движения материала и нагретых газов. В сушилках с косвенным теплообменом тепло передается сушимому продукту через нагретую металлическую поверхность, а в сушилках с комбинированным теплообменом — при контакте с нагретыми газами и через нагретую металлическую поверхность.
Барабанная сушилка (рис. 1) состоит из сварного барабана 1 с укрепленными на его внешней поверхности двумя бандажами 2 и венцовой шестерни 3. Барабан устанавливают бандажами на опорные ролики 5 под углом 1—5° в сторону разгрузки. Для устранения продольного перемещения барабана предусмотрены упорные ролики. Вращение барабану передается от привода 6, состоящего из электродвигателя, редуктора и приводной шестерни, находящейся в зацеплении с венцовой шестерней. К верхнему торцу барабана примыкают топка 7 со смесительной камерой и загрузочное устройство 8, а к нижнему — разгрузочная камера 4 для выгрузки высушенного материала и отвода дымовых газов.
Внутри барабана укреплены насадки для обеспечения максимального контакта материала с горячими газами, равномерного распределения и перемешивания материала по всему внутреннему объему барабана. Форма и размеры внутренних насадок определяются диаметром барабана и характеристикой подвергаемого сушке материала (крупность, влажность, способность к слипанию, спеканию и пылеобразованию). Насадки выполняют в виде приемно-винтовых лопастей (рис. 1, б), подъемно-лопастными (рис. 2, в), секторными (рис. 3, г) и цепными (рис. 4, д). Приемно-винтовые лопасти обычно укрепляют в загрузочной части барабана, с их помощью увеличивают скорость перемещения материала и уменьшают время контактирования с дымовыми газами. Иногда винтовые лопасти укрепляют на разгрузочном конце барабана.
Подъемно-лопастную систему насадок применяют для сушки крупно-кусковых материалов, обладающих значительной плотностью, насадки остальных типов применяют при сушке мелкозернистых материалов, способных к слипанию и пылеобразованию. По длине барабана могут быть укреплены насадки трех различных типов.
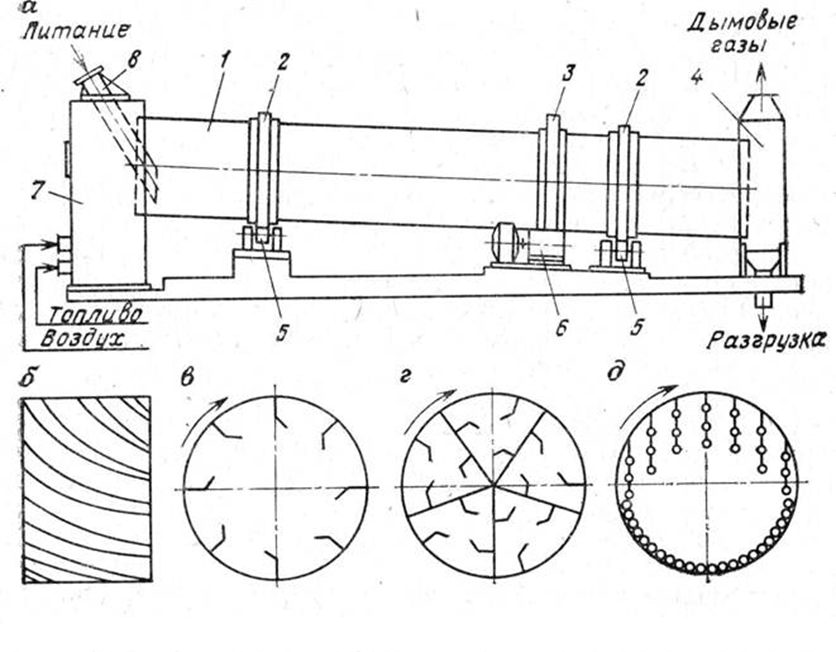
Рисунок 1 - Барабанная газовая сушилка
На концах сушильного барабана устанавливают уплотнительные устройства с целью предотвращения подсосов воздуха. Вследствие присоса воздуха увеличиваются потери тепла с отходящими газами, вытяжные вентиляторы работают с перегрузкой, уменьшается подача дымовых газов из топок. Подача воздуха в сушилку вследствие присосов не должна превышать 20—25 % расхода сушильного агента.
Преимущество барабанных сушилок — возможность сушки продуктов при высоких температурах нагретых газов (700—800 °С) и значительной крупности исходного материала до 250 мм. К недостаткам барабанной сушилки относят: значительную массу сушилки, большие габариты, налипание влажного материала на внутреннюю поверхность и насадки барабана.
Продолжительность пребывания материала в барабане зависит от характеристики сушимого продукта, его начальной и конечной влажности и составляет от 15 до 40 мин. Влажность высушенного материала составляет 4—6 %, а в некоторых случаях — 0,5—1,5 %. Барабанные сушилки имеют высокую производительность по испаряемой влаге.
Трубы-сушилки применяют также для сушки мелких продуктов в цветной металлургии и химической промышленности.
Труба-сушилка состоит из устройства подачи горячих газов , компенсатора , загрузочного устройства , прямолинейного участка трубы постоянного сечения и разгрузочных аппаратов. Внутренняя часть трубы-сушилки от загрузочного устройства до провальной части футеруется огнеупорным кирпичом, чтобы температура металлического кожуха не превышала 45 °С. Для восприятия температурных перепадов по длине сушилки предусмотрены компенсаторы.
Длина рабочего участка трубы-сушилки колеблется в пределах 15—25 м. Для увеличения срока службы этот участок трубы обычно изготовляют из нержавеющей стали с толщиной стенки 6—8 мм.
Горячие дымовые газы из топки подают в трубу-сушилку вентилятором-дымососом. На расстояние h от точки подачи газов в трубу-сушилку подают сырой материал, который подхватывается восходящим потоком дымовых газов и перемещается по трубе вверх. При движении материала по трубе с его поверхности испаряется влага. Высушенный материал поступает в циклон или гравитационный аппарат, в котором твердая фаза отделяется от газообразной. Отработанные газы из циклона или гравитационного аппарата поступают на вторую стадию их очистки.
При сушке в трубе-сушилке часть материала иногда падает в нижнюю часть сушилки (провал). Такие частицы выводят из сушилки через специальный затвор.
Для уменьшения прососов воздуха через провальную часть сушилки ее герметизируют с помощью установки в нижней части трубы-сушилки шнековых затворов, мигалок, скребковых питателей, шлюзовых гидрозатворов.
Схемы компоновки сушилок разнообразны, они определяются формой и размерами труб-сушилок, типами топок и размерами дымососов.
Преимущества сушки материалов во взвешенном состоянии — простота конструкции сушилки, сравнительно невысокие капитальные затраты и большая скорость сушки, обусловленная интенсивной передачей тепла от газов к взвешенным частицам материала.
Продолжительность сушки в трубах-сушилках очень мала. Увеличить ее можно, только удлинив сушилку, что не всегда оправдано. При необходимости увеличить продолжительность сушки в несколько раз применяют режим сушки в кипящем слое.
Обычно сушку в кипящем слое используют для мелкозернистого материала. Сущность этого способа заключается в том, что материал, подлежащий сушке, подается на распределительную решетку и приводится в псевдоожиженное состояние потоками газа, подаваемого под решетку. Скорость потока газов через решетку подбирают такой, чтобы материал находился на решетке во взвешенном «кипящем» состоянии. По своим свойствам псевдоожиженный слой напоминает маловязкую жидкость. Частицы, перемещаемые в таком слое, почти не встречают сопротивления.
Печь сушилки кипящего слоя (рис. 2) состоит из двух камер: нижней топливосмесительной 1 и верхней сушильной 4. Камеры разделены между собой решеткой 2. Отверстия в решетке выполнены таким образом, чтобы обеспечить равномерное распределение воздуха по всей ее площади. В нижней камере осуществляется сжигание жидкого или газообразного топлива, поэтому она оборудована топливо- и воздухоподачей и средствами контроля работы топки. Верхняя камера снабжена загрузочным 3 и разгрузочным 5 устройствами и приборами контроля температуры. Материал подается питателем в сушильную камеру в надрешетное пространство. Благодаря подаче воздуха через решетку, на ней образуется кипящий слой высотой 0,3—0,45 м. При прохождении нагретого воздуха или дымовых газов через кипящий слой с поверхности частиц испаряется влага. Высушенный продукт разгружается через патрубок, расположенный над решеткой, высота которого может регулироваться. Отработанный сушильный агент вместе с испаренной влагой после прохождения через пылеулавливающие устройства выбрасывается в атмосферу.
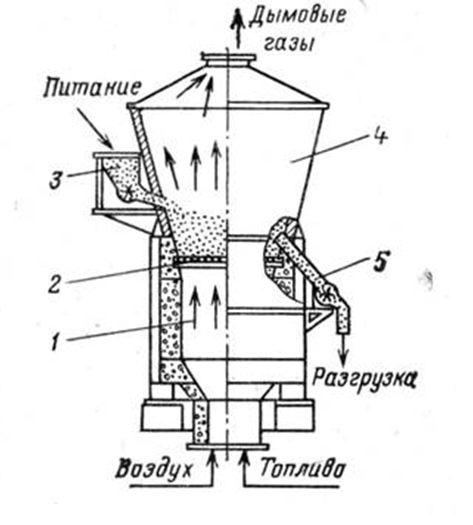
Рисунок 2 - Сушилка кипящего слоя
Сушилки кипящего слоя могут работать как под давлением, так и под разрежением. В настоящее время большое распространение получили сушилки с подачей теплоносителя под давлением.
Преимущества сушки материала в кипящем слое — высокая интенсивность сушки и возможность регулирования времени пребывания материала в сушилке.
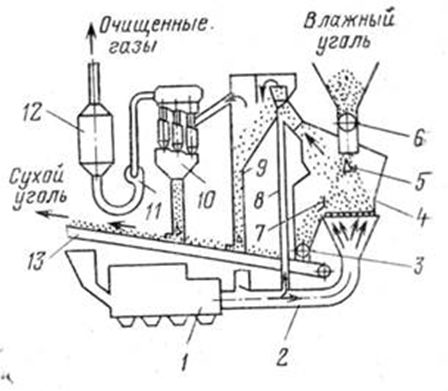
Рисунок 3 – Установка для сушки угля в кипящем слое
Установка для сушки продуктов обогащения угля — флотационного и мелкого концентратов — (рис. 3) состоит из топки 1, работающей на твердом топливе, газохода 2, сушильной камеры 4, питателей сухого 3 и влажного 6 угля, разбрасывателя 5, шибера донной разгрузки 7, обводного газохода 8, разгрузочной камеры 9, сухого 10 и мокрого 12 пылеуловителей, дымососа и конвейера высушенного угля 13.
Влажный уголь из бункера питателем подается на конусный разбрасыватель, который равномерно распределяет уголь по поверхности газораспределительной решетки сушильной камеры. Камера представляет собой сварную конструкцию круглого сечения, футерованную под решеткой огнеупорным кирпичом. Над газораспределительной решеткой стенки камеры футерованы плитами из жаростойкого металла.
При сжигании угля в топке получают дымовые газы с температурой 800—850 °С, которые подаются по газоходу под газораспределительную решетку со скоростью, обеспечивающей перевод угля, находящегося на решетке, в псевдоожиженное состояние. В таком состоянии сушимого угля обеспечивается интенсивный тепло- и влагообмен с дымовыми газами. Высушенный материал пересыпается через порог и питателем подается на ленточный конвейер. Часть высушенного угля потоком газов уносится в разгрузочную камеру, в которой, благодаря перепаду скоростей движения газов, частицы осаждаются и разгружаются на конвейер. Окончательно газы очищаются в сухом и мокром пылеуловителях.
Обводной газоход предназначен для предотвращения налипания пыли в газоходах и сухом пылеуловителе. По обводному газоходу подают часть дымовых газов.
Производительность сушилки по влажному материалу 120— 130 т/ч и по испаренной влаге 10—12 т/ч. Температура запыленных газов 60—70°С.
Интенсифицировать процесс сушки и повысить эффективность работы сушильных аппаратов можно в результате повышения температур и скоростей движения подаваемого в сушилку сушильного агента, максимальной герметизации сушильных трактов с целью исключения подсосов воздуха и комплексной механизации процесса сушки.
В результате исследований и практической эксплуатации труб-сушилок установлена возможность подачи в сушилки сушильного агента со скоростью 80—100 м/с и температурой до 1500°С. При увеличении скорости движения и температуры сушильного агента значительно интенсифицируется тепло- и массообмен, снижаются эксплуатационные затраты на сушку минерального сырья.
Для совершенствования сушильных аппаратов целесообразно использовать процесс сушки в виброкипящем слое. Реализовать виброкипящее состояние материала можно не только пропуская газ через слой материала, но и воздействуя на слой механически. Установлено, что эффективность сушки в виброкипящем слое в 2— 3 раза выше, чем в кипящем слое. Скорость сушки возрастает с увеличением частоты и амплитуды вибрации слоя сушимого материала.
Сушка продуктов обогащения перегретым паром — более эффективный процесс по сравнению с сушкой дымовыми газами или нагретым воздухом. Установлено, что скорость сушки перегретым паром в 2—3 раза выше, чем при сушке дымовыми газами.
Выводы
В данной работе планируется провести оптимизацию управления сушильной установкой для снижения энергозатрат. Для того чтобы иметь на выходе определенное значение содержания влаги в материале достаточно варьировать температуру и поток (расход) сушащего воздуха. То есть, максимально снижая, например, температуру газа, на выходе иметь удовлетворительно высушенный материал. Уменьшать температуру и расход газа, уменьшая тем самым затраты, можно лишь до определенного предела, критерием в данном случае служит влажность материала на выходе барабана. При осуществлении любого технологического процесса прежде всего необходимо обеспечить его безопасность.
Список источников
1.Михайлов Н.М. Вопросы сушки топлива на электростанциях/ М.,Л: - 1957 - 153 с.
2.Лыков А.В. Теория сушки/ М.: Энергия, 1968 - 472 с.
3.Сажин Б.С. Основы техники сушки/ М.: Химия 1984 - 320 с.
4.Лебедев П.Д. Расчет и проектирование сушильных установок / М.: Госэнергоиздат, 1962- 320 с.
5.Пюшнер Г. Нагрев энергии сверхвысоких частот/ М.:Энергия, 1968 - 320 с.
6.Диденко А.Н. СВЧ-энергетика/ М.: Наука, 2003 - 446 с.
7.Лебедев Б.В. Технология сжигания органического топлива/ Томск: Изд-во Томского политехнического университете, 2012 - 148 с.
8.Коузов П.А., Скрябин Л.Я. Методы определения физико-химических свойств промышленных пылей/ Л.: Химия 1983 - 143 с.
9.Белоусов В.Н., Смородин С.Н., Смирнова О.С. Топливо и теория горения/СПб., 2011 - 84 с.