Abstract
Contents
- 1. The relevance of the topic
- 2. Goal and objectives of the study
- 3. The existing methods of drying
- Conclusions
- List of sources
Introduction
According to the Energy strategy of Ukraine, the volume of internal consumption of coal by 2015 will increase up to 98.7 million tons. The same trends are evident in energetically advanced economies Germany, the USA, South Africa, China, England and even the «gas Empire - Russia. Because, unlike oil and gas, coal reserves distributed across countries and regions more evenly and coal supply is less susceptible to geopolitical situation. On thermal power stations of Ukraine are mainly used as fuel coal, and not of the best quality, so it is advisable correctly organize preparation of the fuel before combustion, for more reliable operation of power plants.
1. Topicality
Drying of fuel before grinding beneficial to the mills. Performance hammer mills increased on 20% in comparison with mills operating on cheese fuel, approximately in 2 times increased resource beat.; Reduction of the grinding mill production with increasing moisture content of the fuel can be explained by the fact that grinding wet fuel is subject to availability a large number of plastic deformations, impede ready coal dust. According to the VTI found that the greater the difference humidity the milled fuel from the value of hygroscopic moisture, the more the reduction of the grinding mill production. Preliminary drying of fuel with the removal of part of the external moisture only 3-5 % dramatically improves its loose properties, eliminated the difficulties of transportation coal on channels of fuel supply and its movement in the bunkers, increases heat of combustion of fuel. Thus, preliminary drying of coal is an integral part of its enrichment and the decision of questions of increase of reliability of work of the equipment a fuel supply, coal-pulverization systems and ultimately the entire boiler plant. Combustion in the fluidized bed - one of technologies of burning solid fuels in power boilers. A furnace with a boiling layer are not sensitive to fuel quality, so they burn sludge waste products of enrichment. The sludge has high humidity, so before burning it should be dried to a moisture content of not more than 10%. Drying of fuel is one of the major energy consuming operations on beautification of coal. In this regard, the development of rational schemes of drying is an important direction to increase the efficiency of power units.
2. Goal and objectives of the study
Objective: to Optimize the management of drying to reduce energy costs. Development of mathematical model of drying process in a drum for determining conditions the efficient usage of the equipment. Development of measures to ensure the safety of drying.
To solve this task it is necessary to solve the following tasks:
- Spend status analysis drying of bulk materials;
- Choose a method of research;
- Develop recommendations to improve the processes of drying;
- Consider the safety measures, drying, ways of fighting fires.
3.Existing types of drying
Drying is called thermal process for the removal of solid materials contained in them moisture. Drying is a complicated technological process which is dependent on a large a number of factors, knowledge of which is essential for the analysis and calculation process. The intensity of drying depends on a number of factors indicating the complexity of the real drying process, the difficulty of obtaining adequate for him mathematical description. The greatest influence on the drying process by factors that determine the dried material as the object of drying. They characterize the material's resistance to the transfer of moisture inside it and this surface into the environment, the ability of a material to perceive applied to him warmly. Such factors include its internal structure, thermophysical properties, shape, size. The most strong influence renders the internal structure of the material.
By the method of heat supply of the following types of dryers:
a) convective when the heat required to evaporate the moisture content is transferred from the air, flue gases or superheated steam material which dry by direct contact (convection)
b) electromagnetic when heat is transferred to the сушимому material through the wall.
in) radiation drying moisture is removed by the influence of electromagnetic waves.
g) drying in the field of high-frequency currents - by increasing the temperature inside the material moisture evaporates.
Moisture mass, which may take a drying agent depends on the content of water vapor, its temperature and pressure. The choice of drying agent is of great importance, as the cost of consumed heat significantly affects the efficiency of drying units. By design distinguish the dryer drum, pipe-dryer, fluidized bed dryers, spray and others.table 1
Classification of dryers
Symptom classification | Types of dryers |
Methods of heat supply to material | Convection, contact, radiation, electrical |
Pressure in the working space | Atmospheric, vacuum |
the mode of action | Periodic or continuous action |
Drying agent | Air flue gases mixture of air and flue gases, superheated steam and inert gases |
the Direction of movement of the drying agent with regard to the material | duecurrent, counterflow, crossshock and reverse |
Character of the circulation of drying agent | With natural and forced circulation |
heating Method of drying agent | steam heater air , fire heater air, by mixing with the flue gases, electrically heated |
Diagram of the heating drying agent | Central heated, heated individual units and with intermediate heated |
Multiplicity use a drying agent | one-time and recirculation |
a Way to remove moisture from the dryer | ventilation, condensing, with a chemical absorption moisture |
structure of the dryer | Corridor, chamber, shaft, belt, belt, drum, tubular etc. |
Most often, the drying of various mineral raw materials use drum dryers.
Distinguish drum driers, direct, indirect and combined heat exchange. In dryers with direct heat exchange is ensured by direct contact the wet material with hot gases. Dryers operate in direct-flow and counterflow schemes of the movement of material and greenhouse gas. In dryers with indirect heat exchange of a heat is transferred сушимому product through a heated metal surface, and driers combined heat exchange - contact with heated gases and through a heated metal surface.
Drum dryer (Fig. 1) consists of a welded drum (1) strengthened on its outer surface, two of the stiffening 2 and ring gear 3. Dryer set the tyres on the track rollers 5 angle 1-5 degrees toward the unloading. To eliminate the longitudinal movement of the drum are provided resistant rollers. Rotation of the drum is transmitted from the actuator 6, consisting of a motor, a reduction gearbox and drive gear is engaged with the notch the gear. The upper end face of the drum adjacent furnace 7 with mixing chamber and a device 8, and to the lower - unloading Luggage 4 for unloading dried material and the exhaust.
Inside the drum strengthened nozzle to ensure maximum contact of the material with hot gases, uniform distribution and mixing of material on around the inner volume of the drum. Shape and dimensions of internal nozzles are determined by the diameter of the drum and characteristic exposed to drying material (size, humidity, ability to stick together, sintering and dust). Nozzles are in the form of receiving screw blade (Fig. 1, b), hoisting-and-blade (Fig. 2), sector (Fig. 3, d) and chain (Fig. 4, d). Receiving helical blades typically strengthens in the boot of the drum, with their help increase the speed and reduce the time of contact with the flue gases. Sometimes helical blades strengthen dump the end of the drum.
Hoisting-and-blade system of nozzles used for drying of large-bulk materials possessing significant density of the tips of the other types used in drying of fine-grained materials, capable of sticking together and dust. The length of the drum can be strengthened tips of three different types.
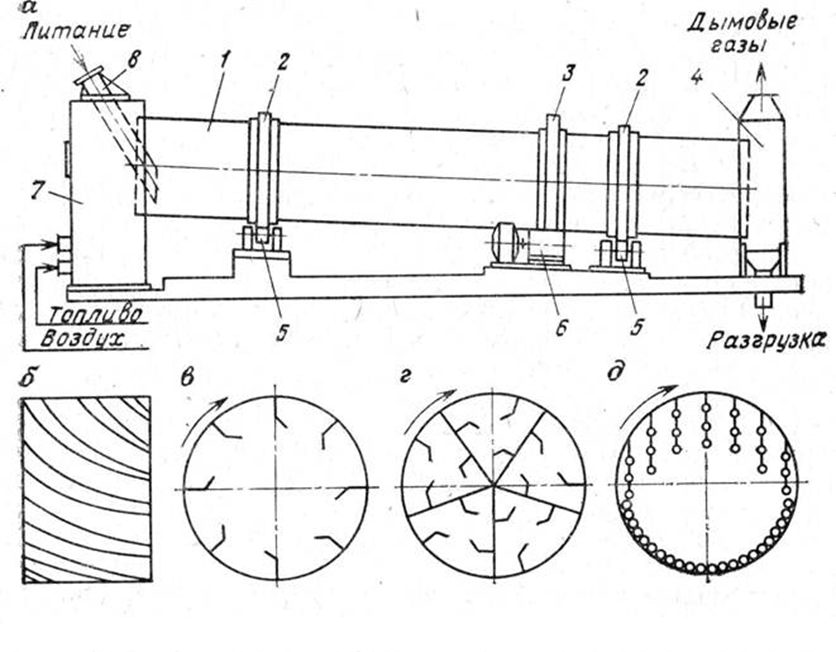
figure 1 - Drum gas dryer
At the ends of the drying drum set sealing device to prevent the intake of air. Due присоса air losses due heat from the flue gases, exhaust fans are overloaded, reduced supply of flue gases from the furnaces. Submission of air in the dryer due leakages must not exceed 20-25 % of the drying agent.
Advantage drum dryers - opportunity drying of products at high temperatures, greenhouse gas (700-800 C) large size of the original material up to 250 mm. The disadvantages of drum dryer include: significant mass dryer, large size, sticking of wet material on the inner surface and tips drum.
Duration of stay of the material in the drum depends on the characteristics of dry the product, its initial and final humidity and ranges from 15 to 40 min. Humidity dried material is 4-6 %, and in some cases - of 0.5-1.5 %. Drum driers have high performance the evaporated moisture.
Pipe-dryers are also used for drying of small products in non-ferrous metallurgy and chemical industry.
Pipe-dryer consists of the feeder hot gases , compensator , boot device , straight pipe with a constant cross section and unloading devices. The inner part of the tube dryers from the boot device to a failure of part of the футеруется a fire-resistant brick to temperature the metal casing does not exceed 45 Degrees. For the perception of temperature difference along the length of the dryer are provided compensators.
The length of the working section of pipe-dryer varies in the range of 15-25 meters. To increase the lifetime of this section of the pipe is usually produced from stainless steel with thickness of a the walls of 6-8 mm.
The hot flue gases from the furnace is served in the pipe-dryer blower-smoke exhauster. Distance h from the point of gas supply to the pipe-dryer served raw material, which embraces the upward flow of flue gas and is moving on a tube upwards. In goods movement through the pipe from its surface moisture evaporates. The dried material comes in a cyclone or gravity device where the solid phase is separated from the gaseous. The exhaust gases from a cyclone or gravitational apparatus arrive at the second stage of cleaning them.
When drying in the pipe-drier part of the material sometimes falls in the bottom part of the dryer (failure). Such particles are removed from the dryer through a special the shutter.
To reduce unmetered air through the failed part of the dryer its seal with the installation, in the bottom part of the pipe-dryer screw closures, flashing, scraper feeders, sluice valves.
Layout dryers are diverse, they are determined by the shape and size of pipe-dryers, types of furnaces and the size of the smoke exhausters.
Advantages of dry materials in suspension - simplicity of design dryer, relatively low capital costs and faster process, due to the intensive transfer of heat from gases to suspended particles the material.
the Duration of drying in pipes-dryers very small. Increase it can only extending the dryer, which is not always justified. If necessary, increase the duration of drying several times used mode of drying in a boiling layer.
Typically, a drying process in a boiling layer is used for fine material. The essence of this method is that the material to be dried, served the distribution grid, and is contained in a fluidized state flow of gas supplied under the grate. The speed of the flow of gases through the bars picked such that the material was on a lattice in suspension «boiling» state. According to its properties, fluidised reminds with small viscosity liquid. Particles transported in this layer, almost never see resistance.
Drying oven boiling layer (Fig. 2) consists of two chambers: the lower fuel mixer 1 and the top 4 drying. Camera divided between the 2 bars. Holes in the lattice performed in such a way as to ensure uniform air distribution throughout its area. In the lower chamber is burning the liquid or gaseous fuel, so it is equipped with a fuel - and supply air and means of the control of work of the furnace. The upper chamber is equipped bootable 3 and unloading 5 devices and devices of the control of temperature. The material is fed to a feeder into the drying chamber in space over a lettice. Thanks to the filing of air through the lattice, it formed a boiling layer height 0.3-0.45 m. With the passage of the heated air or flue gases through the boiling layer the surface of particles of moisture evaporates. The dried product is discharged through pipe, located above the grille, the height of which can be regulated. Exhaust drying agent, together with the evaporated moisture after passing through the de-dusting devices emitted into the atmosphere.
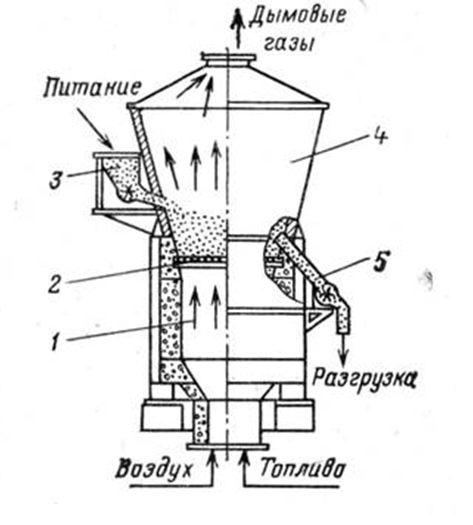
figure 2 - Dryer fluidized bed
Fluidized bed dryers can work under pressure and depression. Currently widespread were the dryer with the supply of heat carrier under pressure.
Advantages of the material drying in a fluidized bed - high drying rates and the possibility of regulating the residence time of the material in the dryer.
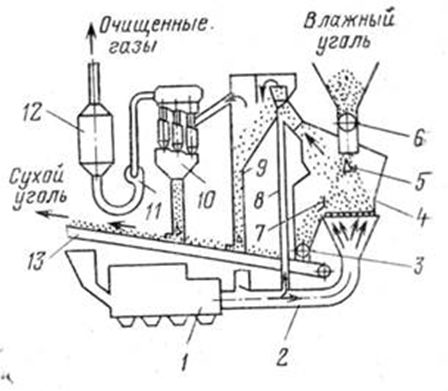
figure 3 - Drying plant for coal in fluidized bed
Installation for drying of products of enrichment of coal flotation and small concentrates (Fig. 3) consists of a combustion chamber 1 running on solid fuel, gas flue 2, drying chamber 4, feeders 3 dry and moist 6 coal, spreader 5, gate bottom discharge 7 Obvodny flue 8 handling the camera 9, dry 10 and wet 12 dust separators, exhaust fans and pipeline dried lignite 13.
Wet coal from the hopper feeder is served on the conical spreader evenly on the surface of coal gas-distributing grid the drying chamber. Luggage represents a welded construction of circular cross-section, lined behind a fire-resistant brick. Over gas distribution lattice walls lined plates of heat-resistant metal.
Coal combustion in the furnace receive flue gases with a temperature of 800-850 °served on gas flue under the gas distribution lattice with speed, providing a translation of the coal, located on a lattice in a fluidized state. In such a state of dry the coal is ensured by the intense heat and moisture with flue gases. The dried material is sprinkled over the threshold and the feeder is fed onto a belt conveyor. Part dried lignite gas flow blowin in the discharge chamber, in which, due to difference in velocities of motion of gases, particles settle and unloaded on the conveyor. Finally gases cleared the dry and wet dust catcher.
Bypass flue is intended to prevent buildup of dust flues and dry dust catcher. On Obvodny gas flue serves part of the flue gas.
The capacity of the dryer wet material 120 130 t/h and in the evaporated moisture 10-12 t/h. Temperature of dusty gases 60-70 Degrees.
To intensify the process of drying and improve the efficiency of drying apparatus can be a result of rising temperatures and velocities of motion of the supplied in the dryer drying agent, maximum sealing drying paths to exclude the intake of air and complex mechanization of process of drying.
As a result of research and practical operation of pipe-dryers provide for submission in the dryer drying agent with the speed of 80-100 m/s and temperature of up to 1,500 degrees. When you increase the speed and temperature of drying agent significantly intensifying heat and mass transfer, reduced operating costs for drying of mineral raw materials.
To improve the drying apparatus is advisable to use a drying process in vibro boiling layer. Implement vibro boiling state of the material can be not only gas flowing through a layer of material, but also influencing the layer mechanically. It is established that the efficiency of drying in vibro boiling layer in 2 - 3 times higher than in fluidized bed. Drying speed increases with the amplitude and frequency of vibration of a layer of dry material.
Drying of products of enrichment of superheated steam is a more efficient process in comparison with drying flue gases or heated air. Found that the rate superheated steam drying in 2-3 times above, than at drying flue gases.
Conclusions
In this work it is planned to conduct optimization of management of the drying unit for the decrease of energy consumption. To have the output of a certain the value of the moisture content of the material enough to vary the temperature and flow (flow) of drying air. That is, reducing, for example, temperature gas output have satisfactorily dried material. Decrease the temperature and flow rate of gas, thereby reducing costs, you can only to a certain limit criterion in this case is material humidity outlet drum. In the implementation of any technological process, the first thing you should secure.
List of sources
1.Михайлов Н.М. Вопросы сушки топлива на электростанциях/ М.,Л: - 1957 - 153 с.
2.Лыков А.В. Теория сушки/ М.: Энергия, 1968 - 472 с.
3.Сажин Б.С. Основы техники сушки/ М.: Химия 1984 - 320 с.
4.Лебедев П.Д. Расчет и проектирование сушильных установок / М.: Госэнергоиздат, 1962- 320 с.
5.Пюшнер Г. Нагрев энергии сверхвысоких частот/ М.:Энергия, 1968 - 320 с.
6.Диденко А.Н. СВЧ-энергетика/ М.: Наука, 2003 - 446 с.
7.Лебедев Б.В. Технология сжигания органического топлива/ Томск: Изд-во Томского политехнического университете, 2012 - 148 с.
8.Коузов П.А., Скрябин Л.Я. Методы определения физико-химических свойств промышленных пылей/ Л.: Химия 1983 - 143 с.
9.Белоусов В.Н., Смородин С.Н., Смирнова О.С. Топливо и теория горения/СПб., 2011 - 84 с.