Abstract
Contents
- Introduction
- 1. Purpose and objectives of the study
- 2. Justification themes and brief analysis of the issue
- 2.1. General characteristics of the binders
- 2.2. Description of the hydraulic press for RUF briquettes
- 2.3. Advantages of briquettes
- Conclusion
- References
Introduction
In recent years, more and more clear is the energy crisis, especially in the hydrocarbon fuel. Traditional fuels derived from oil, gas and coal. It is believed that these resources are not enough for more than 100 years, with the cost of their production is growing.
All of the above makes us look for alternative clean fuel. Therefore, in this report we draw attention to this type of fuel, the fuel from biomass.
The raw material for this fuel is vegetable waste, which are in abundance in Ukraine: sunflower husks, buckwheat, millet, straw, sawdust, soft and hard wood, and other plant waste.
Bioenergy in Ukraine – one of the youngest, perhaps, the fastest growing and one of the most promising sectors of the industry at the time [1].
Briquettes are divided on two principles:
First – for raw materials from which they are made.
Here distinguished:
– Briquettes from wood waste (chips and sawdust bark, waste with bark, bark, waste production MDF shlifpyl, waste veneer, lignin, briquettes from agricultural waste);
– Briquettes agrobiomassy (straw, sunflower hulls, husks of cereals, cotton waste, straw, reeds);
– Briquettes of other materials (paper, cardboard, pulp, polymers, peat) [2].
Second – the method and form of compression.
Currently, there are three main types of fuel briquettes. They are different in shape, which depends on the method of production. "The people" caught three names that originated from the names of companies that manufacture equipment for the production of a briquette.
Thus isolated:
1 – briquettes RUF (produced on a hydraulic press at a pressure of 300-400 bar);
2 – briquettes NESTRO (radial hole or without him, produced by hydraulic or mechanical presses shock at pressures of 400-600 bar);
3 – briquettes Pini-Kay (4- or 6- point bricks with a radial hole made on the mechanical (screw) presses through a combination of very high pressure - 1000-1100 bar - and heat treatment) [2].
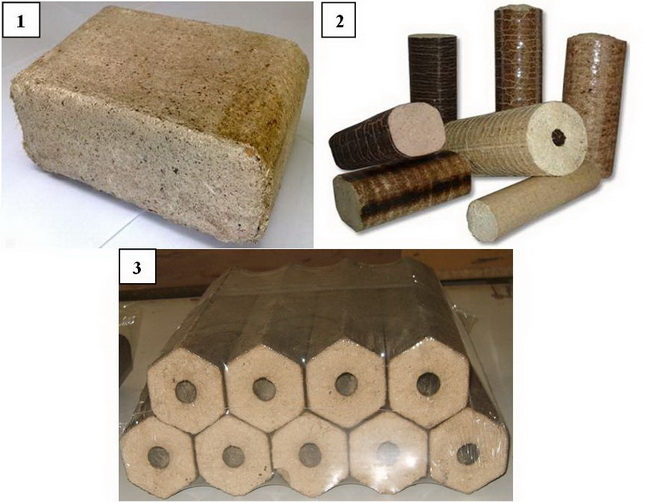
1. Purpose and objectives of the study
Development of technological modes of production of composite briquettes include coal and waste vegetable origin, with different binders.
Research objectives:
1. Theoretical analysis of the formation mechanism of composite briquettes;
2. Experimental studies of the possible technologies for composite briquettes;
3. Develop recommendations for industrial circuits briquetting.
2. Justification themes and brief analysis of the issue
Briquetting of coal – one of the conversion of coal into smaller classes, domestic fuel and power for stratified combustion. Briquetting of coal and anthracite size (0-6) mm, as a rule, in roller presses with different binders [3].
In recent years, became widespread production of fuel briquettes and pellets (granules) from plant wastes (sawdust, straw, lnokostra, sunflower husks, cobs, etc.).
Briquetting plant matter waste produced in the extruder by forming a rigid system of cut dies with supply feedstock conical rotating screw, creating a pressure sufficient to sinter the material into a solid mass in a continuous sleeve without adding binders. The binder serves lignin contained in the feedstock. The sintering process is continuous at 170-220° C. The extrusion is set depending on the characteristics of the feedstock and is achieved by forced heat pressing zone, and through the process.
This way of preforming a number of requirements for raw materials (grain size – up to 3 mm, humidity 8-12%) and is used in the production of relatively small amounts (no more than 300 grams per month for a single installation), but it is easy to use, operates in simple terms and provides high-quality products is highly demanded in the international market [4].
Production of composite sticks, including coal and vegetable waste component in various ratios are associated with some difficulties. There are a number of conflicting claims to technological regimes briquetting of coal and crop residues (Table 1).
Object briquetting | Type of press | Compaction pressure | The presence of a binder | Moisture raw, % | Curing |
Hard coal and anthracite | Roller | Up to 40 MPa | Yes | To 4% for bituminous binder, and more than 8% with a water-soluble | Cooling with bituminous binder; 150-200° C with a water-soluble |
Vegetable waste | Screw, stamp | More than 50 MPa | No | 8-12 | None |
Key Financial Ratios of fuel briquettes are reduced to the following parameters:
– Heat of combustion;
– Mechanical strength;
– Water resistance.
The heat of combustion of briquettes is determined only by the quality and composition of the components of the charge briketiruemoy that can purposefully change.
Mechanical properties of the composite briquette depend on the composition of the charge, and on a number of process parameters of briquetting, including:
– Material composition briketiruemoy charge;
– Sieve of charge;
– Moisture content of the charge;
– The type and flow of binder;
– Compaction pressure;
– Heat treatment briquettes;
One of the main technological parameters of briquetting composite charge is the type used binder.
The main requirement for the binder – its universality, ie high adhesive strength to all components of the briquette.
2.1 General characteristics of the binders
From existing practice briquetting binders are the following groups:
– Neftesvyazuyuschie (bitumen, tar). Provide a very strong and water-resistant bricks at a cost of 6-7%. But the need for pre-drying material, sophisticated technology charge preparation for briquetting and significant operational costs for briquetting results in low profitability for small briquetting plant productivity [5 c.22].
– Inorganic binders (cement, lime). Provide sufficient strength and water resistance of briquettes without heat treatment, but requires optimal screen composition charge and long set optimum strength. The main disadvantage of a significant increase in ash content of the briquette [5 c.29].
– Water-soluble binders. These include waste paper industry (lignosulfonates, sulfate soap), sugar production (molasses), waste milling industry (starchy substance). The main drawback of these binders – insufficient water resistance received briquettes, which requires waterproofing additives or packaging of products, and the need for heat treatment of the briquettes.
In accordance with the terms of reference in the present study we investigated the following links – lignosulfonate, molasses and additionally – Waste milling industry and bitumen emulsion.
Lignosulfonate technical (LST). LST is the waste paper industry and is available in powder and liquid form, solid matter content of not less than 47%. The products are mainly salts lignosulphonic acid – sodium, calcium, magnesium or ammonium. Ash content in dry matter LST is 10 ... 22% and a sulfur content of up to 5 ... 10%. Liquid lignosulfonates have a dark brown color, the density of not less than 1230 kg/m3 and highly soluble in water. By drying them, a solid brittle product which, after grinding can be used as a powdered binder. Tensile stretching dried samples reaches 0.4 ... 0.6 MPa.
The advantage of LST is fire and explosion, and low toxicity [7].
Molasses. Molasses, a product of sugar beet processing, syrupy liquid dark brown color and odor.
During the drying process occurs dilution of molasses, which can contribute to spreading it on the surface of the solid particles. The disadvantage of this binder is more hygroscopic.
Starchy substance. This is a waste of flour and starch, rice polishing and processing of rye, spoiled grain, etc., which are available in Ukraine. These products are eco-friendly material, no harmful effects during processing. The starch content in them is 80%. Binding properties of starch based on the fact that in the presence of water at elevated temperatures, it is gelatinized to form viscous dispersions (gels), which, when the pressure and the associated carbon particles. Positive point – possibility to dose dry binder, which improves the moisture content of raw materials for briquetting.
Cationic bitumen emulsion. Cationic bitumen emulsion. Has been applied in recent years in the manufacture of asphalt-road. The emulsion is prepared by intensive mixing in Table. 2.
Component | Content,% |
1. Bitumen | 67,0 |
2. Water | 31,45 |
3. Emulsifier "Dinoramsl" | 0,25 |
4. Hydrochloric acid | 0,21 |
5. Butanol NS 198 | 1,09 |
The advantage of the binder – water resistant bricks, lack of heat treatment operations finished briquettes. The disadvantage – the need for heating briketiruemoy charge up to 80-85° C, a small watering source material [8].
2.2 Description of the hydraulic press for RUF briquettes
The principle of action of the press to give the RUF briquettes based on the cold, 2-fold hydraulic pressing a certain portion of the material without the addition of binders. In the beginning, at a low pressure is outer seal material due to the voids between the particles. Then compacted and deformed particles themselves - among them there is a molecular bond. High pressure at the end of compression results in a transition of the elastic deformation to plastic particles, whereby the structure of the briquette hardens and stored predetermined shape. The nature of the deformation greatly influence properties of the starting material (moisture fraction homogeneity, etc.).
When the briquette press at each cycle there is a briquette formation and simultaneous extraction of the preform formed in the previous cycle [9].
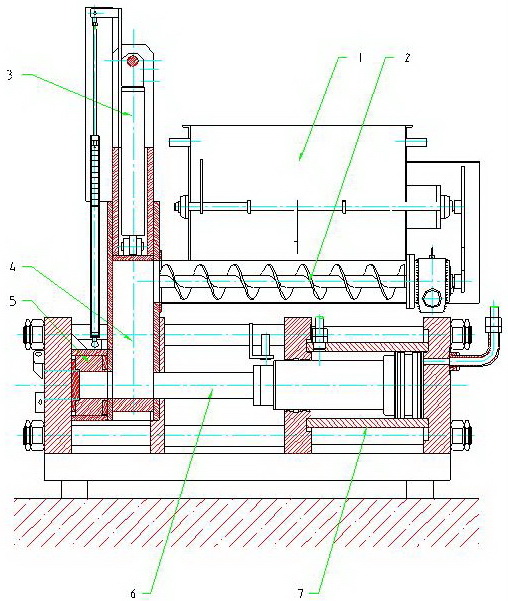
Description of the press
– Filling auger (2) delivers the material present in the hopper (1), the precompression chamber (4). The duration of the auger is calculated using a special feedback system.
– After the download is pre-compression chamber and stop the auger, pre-compression cylinder (3) perform initial compaction of the material in the chamber (4).
– Master cylinder (7) by the punch (6) presses the pre-compressed in one of the two chambers of the mold (5) and compresses the material into a tight unit. During this stage, ejectors in parallel with the master cylinder push finished preform produced in the previous cycle from the second mold cavity through the holes in the front plate.
– The cylinder pre-compression (3) goes up. The master cylinder (7) is returned to its original position.
– Filling auger (2) begins to feed the next batch of material.
– The mold (5) changes its position to the opposite.
– The cycle repeats[9].