Реферат за темою випускної роботи
Зміст
- Вступ
- 1. Актуальність теми
- 2. Мета і задачі дослідження
- 3. Автоматичний газовий захист в структурі АСУ ТП гірничого підприємства
- 4. Моделювання події
Вибух метаноповітряної суміші
- 5. Оптимізація систем автоматичного газового захисту
- 6. Робота АГЗ при нестаціонарних процессах метаноутворення
- 7. Боротьба з шаровими скупченнями метану
- Висновки
- Перелік посилань
Вступ
Вибухи газу та вугільного пилу відносяться до аварій з найбільш тяжкими наслідками в соціальному і економічному плані. Вибух метаноповітряної суміші і вугільного пилу в шахті, який супроводжується формуванням і поширенням по мережі гірничих виробок ударних хвиль – дуже небезпечний вид підземної аварії. Погрожуючи життю і здоровʼю гірників, вибух завжди призводить до руйнування виробок і пошкодження розташованого в них гірничого обладнання. При цьому соціальні, матеріальні і фінансові втрати можуть досягати катастрофічних розмірів.
Незважаючи на те, що автоматичні системи газового захисту не один десяток років експлуатуються в умовах шахт, вони не можуть забезпечити гарантованої безпеки, а тому питання їх вдосконалення залишаються актуальними. Сучасні тенденція розвитку систем автоматичного газового захисту полягають у перетворенні даних систем в системи моніторингу, прогнозування складу та захисту рудничної атмосфери, для чого необхідний комплексний контроль ряду параметрів. Також важливим напрямком розвитку даних систем є підвищення їх надійності, закордонні виробники пропонують повністю дубльовані системи автоматичного газового захисту видобувних дільниць.
Зрозуміло, що потрібно застосувати на гірничих підприємствах України системи нового покоління, зі схемотехническими рішеннями підвищеної надійності, можливістю збору і обробки більшої кількості параметрів рудничної атмосфери, можливістю захисту від небезпечних ситуацій, що виникають при нестаціонарних процесах метаноутворення.
1. Актуальність теми
У ході розслідування причин виникнення аварій на вугільних шахтах України [1], було встановлено, що в переважній більшості випадків контроль вмісту метану в атмосфері гірничих виробок здійснювався незадовільно. Причинами вибухів на шахтах обладнаних системами автоматичного газовогу захисту є газодинамічні явища або виникнення шарових скупчень метану в неконтрольованих просторах. Дані факти вказують на необхідність подальшого вдосконалення систем автоматичного газового захисту.
2. Мета і задачі дослідження
Метою наукової роботи є підвищення надійності функціонування та виконання захисних функцій системою автоматичного газового захисту при стаціонарних і нестаціонарних процесах метаноутворення, за рахунок зміни структури та архітектури системи автоматичного газового захисту. Для досягнення поставленої мети необхідно вирішити наступні задачі:
- провести аналіз сучасних систем АГЗ;
- розробити математичну модель, що зв'язуює структуру і архітектуру системи АГЗ з імовірністю виникнення події
Вибух метаноповітряної суміші
; - базуючись на результатах моделювання розробити оптимальну архітектуру системи автоматичного газового захисту;
- дослідити роботу системи автоматичного газового захисту при нестаціонарних процесах метановиділення;
- на підставі дослідження розробити вдосконалену структуру системи АГЗ.
3. Автоматичний газовий захист в структурі АСУ ТП гірничого підприємства
Автоматичний газовий захист – забезпечення захисних заходів, що виключають можливість загазування гірничих виробок понад допустимої концентрації метану
і вибуху метаноповітряної суміші на шахтах [2]. Газовий захист заснований на безперервному контролі вмісту метану в гірничих виробках шахт,
фіксуванні моменту досягнення гранично допустимої концентрації газу і автоматичній видачі захисних команд на знеструмлення всього електрообладнання,
що потрапило в небезпечну зону, ввімкнені аварійної сигналізації, введення в дію додаткових засобів для інтенсивного провітрювання і розгазування аварійної
ділянки. Газовий захист поширюється на окремі технологічні дільниці, їх частини, камери або обмежується районом дії гірничої машини. Газовий захист
реалізується на шахтах за допомогою окремих засобів і систем. Дані системи можуть бути незалежними, або входити в якості підсистем в АСУ ТП Провітрювання
або Видобуток вугілля
(див. рис. 1 ), або як складова частина уніфікованих телекомунікаційних автоматизованих систем диспетчерського контролю та управління.
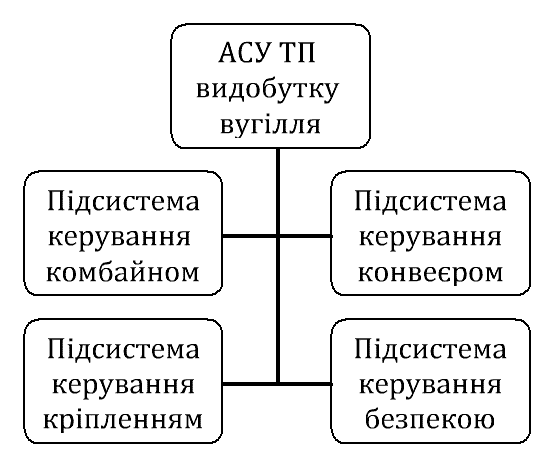
Рисунок 1 – Структура АСУ ТП видобутку вугілля
Структурно АГЗ являє собою розподілену в просторі систему, що складається з первинних перетворювачів (датчиків), ліній звʼязку та телемеханіки, пристроїв обробки вимірювальної інформації (аналізаторів та реєстраторів, сигналізаторів, пристроїв захисного відключення). До конструктивних особливостей АГЗ слід віднести значну віддаленість елементів системи, іскробезпечне виконання ланцюгів живлення, сигнальних і вимірювальних ланцюгів. Режим роботи АГЗ безперервний. Умови експлуатації характеризуються вибухонебезпечною оточуючою середою, її підвищеною вологістю, температурою, атмосферним тиском; наявністю в атмосфері струмопровідного пилу, механічними вібраціями, низькою кваліфікацією обслуговуючого персоналу [3].
У більшості існуючих систем АГЗ можна виділити такі недоліки:
- релейний принцип дії, що не враховує динаміки процесу метаноутворення;
- контроль недостатньої кількості параметрів рудничної атмосфери;
- недостатньо висока надійність;
- неможливість ідентифікації шарових скупчень метану;
- неефективна робота при виникненні ГДЯ.
4. Моделювання події Вибух метаноповітряної суміші
Для того, щоб відбулася подія вибух метаноповітряної суміші
необхідно виконання ряду умов, кожна з яких є необхідною, але не достатньою.
Використовуючи елементи теорії графів і алгебри логіки, наведемо спрощену структуру події Вибух
(рис. 2 ).
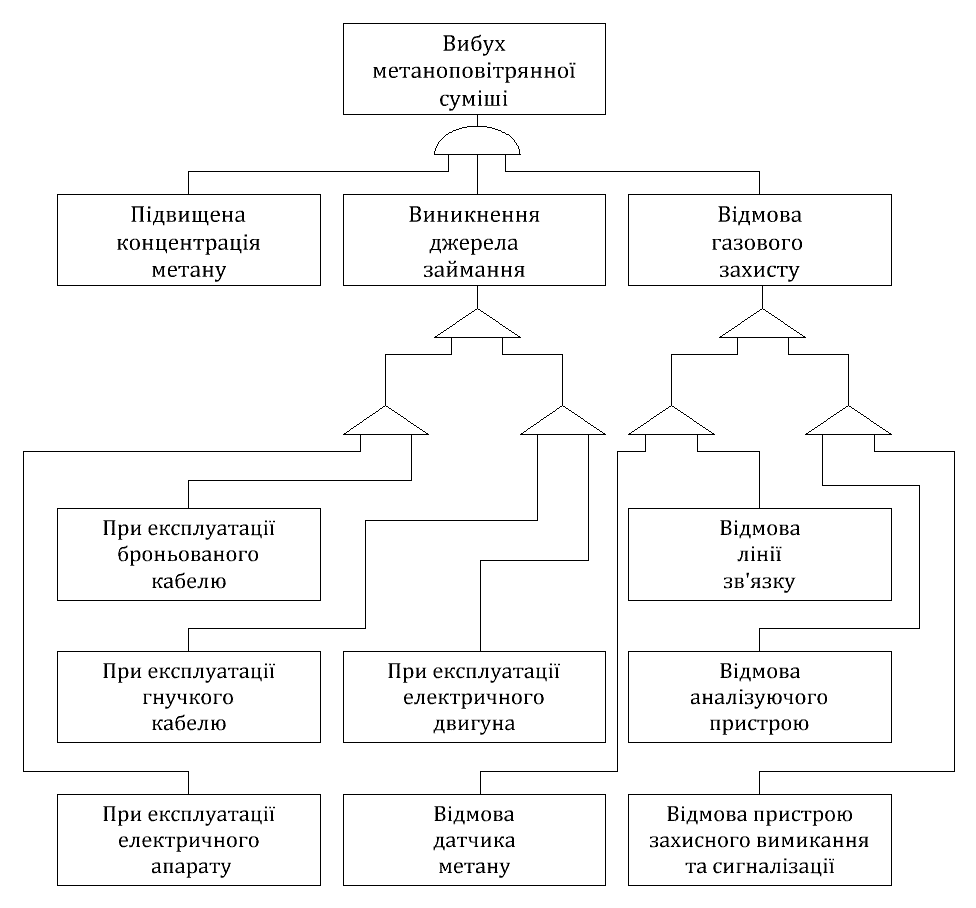
Рисунок 2 – Дерево події Вибух метаноповітряної суміші
Подія вибух є конʼюнкцією таких станів: підвищена концентрація метану
, наявність джерела займання
, відмова АГЗ
[4]. Всі дані умови є
необхідними, але жодна з них не є достатньою. Так для вибуху необхідна строго певна концентрація метану. При концентрації метану менше 5 %
(за обʼємом) метан не вибухає, а горить, згораючи повністю з утворенням СО2 і Н2О; при концентрації вище 16 % він також горить, але при цьому
можливе неповне згоряння з утворенням Н2О і отруйного СО. Таким чином вибухонебезпечна концентрація метану С[СН4]∈(5,15) %.
Однак наявність
вибухонебезпечної концентрації не є достатньою для виникнення події вибух. Необхідний фактор, яким є джерело займання електричного,
механічного або хімічного роду. При цьому джерело займання повине мати достатню для детонації метаноповітряної суміші потужність. Так як
виникнення джерела займання механічного або хімічного характеру в шахтах небезпечних по газу і пилу організаційними заходами зводиться
нанівець, то основним фактором, що ініціює вибух є електрична дуга або іскра критичної (достатньої) потужності. Джерелом розряду необхідної
потужності в підземній виробці може служити пошкодження броньованого або гнучкого кабелю, електричного двигуна, електричного апарату. Сигнальні
ланцюги і ланцюги управління за умови їх іскробезпечного виконання не можуть служити джерелом іскри достатньої потужності. Третім необхідним
чинником є відмова системи АГЗ. Це пояснюється тим, що за своїм функціональним
призначенням АГЗ повинна нейтралізувати можливість вибуху. Виходячи
з різноманіття відмов АГЗ, їх можна розділити по теріторіальній ознаці:
відмова датчика, відмова в лінії звʼязку, відмова аналізуючого пристрою,
відмова схеми (пристрою) захисного відключення.
Позначимо подію вибух
– В, подію небезпечна концентрація метану
– С, подію джерело
займання – I,
подію відмова АГЗ – А̄, тоді формалізуємо подію вибух:
![]() | (1) |
Концентрація метаноповітряної суміші є випадковою величиною, залежить від газоносності пласта, гірничого тиску, швидкості повітря у виробці
(отже, і від загальношахтної депресії), конфігурації виробки, наявності заходів щодо дегазації і інше. При цьому процес метановиділення не стаціонарний,
а отже і не ергодичний. Подія джерело займання
також є не детермінованою. При цьому дана подія досліджена, і існують формули для розрахунку ймовірності
виникнення даної події [5].
Система АГЗ є відновлюваної системою без резервування при послідовному зʼєднанні пристроїв і за наявності їх профілактики [6]. Елементи пристрою прийняті послідовно зʼєднаними, оскільки при виході з ладу будь‑якого з них вся система виходить з ладу. Складемо граф станів системи (рис.ʼ3).
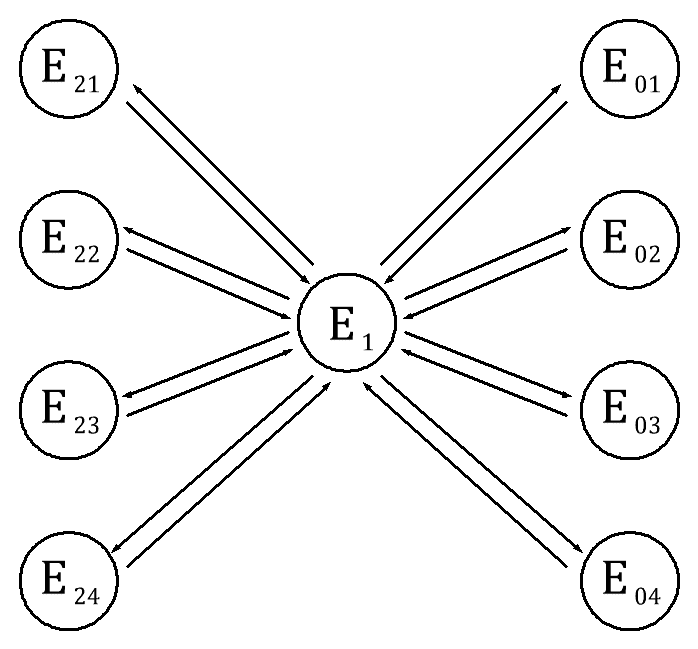
Рисунок 3 – Граф стану АГЗ
На даній схемі стан Е1 відповідає працездатному стану системи АГЗ, стан Е0i – аварійний простій з причини відмови i‑го елемента (i=1..n) і його відновлення, Е2j – профілактичне обслуговування і плановий простій j‑го елемента системи (j=1..k). λ – інтенсивність відмов, μ &ndash інтенсивність відновлення. Індекс 1 відповідає датчик метану, 2 – лінія звʼязку, 3 – аналізатор, 4 – пристрій захисного відключення. Інтенсивність відмови λ – умовна щільність ймовірності виникнення відмови обʼєкта, визначена за умови, що до розглянутого моменту відмова обʼєкта не виникає. Інтенсивність відновлення μ має той же математичний сенс.
При моделюванні імовірності відмови АГЗ використовуємо правило Колмогорова, для складання аналітичної моделі,
яка описує граф стану якоїсь системи. Згідно
даному правилу: система містить стільки диференціальних рівнянь, скільки станів містить граф; ліва частина всіх рівнянь містить похідну від імовірності
i‑го стану; права частина рівнянь містить стільки доданків, скільки гілок графа пов'язано з даними станом, якщо гілка спрямована в даний стан,
то перед
доданком ставитися +
, якщо з даного стану, то −
, кожний доданок правої частини являє собою добуток інтенсивності переходу з одного стану в
інший та
ймовірності того стану, з якого виходить стрілка.
Згідно з формулою (1) для здійснення події B (вибух), необхідно одночасне здійснення подій С, I, А̄. Оскільки дані події незалежні, тобто здійснення одного з них не змінює ймовірність здійснення іншого, то ймовірність виникнення події В дорівнює добутку ймовірностей виникнення подій С, I, А̄: PB = PC ⋅ PI ⋅ PĀ
Приймемо припущення про те, що в розглянутій нами виробці завжди вибухонебезпечна концентрація метану, тобто PC = 1, для того щоб змоделювати найгірший розвиток подій, тоді:PB = PI ⋅ PĀ
Відомо [6], що навіть при повній безвідмовності захисне обладнання (захист від витоків), не може запобігти появі вибухонебезпечного джерела від електроустаткування ділянки, таким чином PI≥0,036.
Під станом А̄ мається на увазі непрацездатний стан АГЗ, що може бути повʼязано не тільки з відмовою системи, а й з виконанням профілактичних робіт. Відповідно з графом стану АГЗ (рис. 7) стан А̄ відповідає будь‑якому стану за винятком стану E1. Так як всі стани, наведені на рис. 3 утворюють повну групу подій, то: PĀ = 1 − P1. Де P1 – ймовірність того, що система знаходиться в стані Е1.
Для вираження Р1 складемо рівняння відносних ймовірностей переходу системи з одного стійкого стану в інший, використовуючи правило Колмогорова.
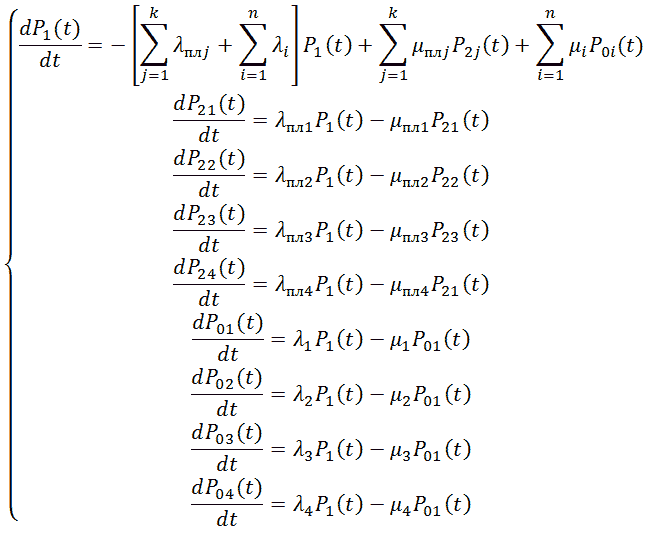
Інтенсивність відмови λ в загальному випадку є функцією часу, тобто λ = f(t), за визначенням – умовна щільність ймовірності виникнення відмови обʼєкта, визначена за умови, що до розглянутого моменту відмова обʼєкта не виникне. Однак, при практичних розрахунках приймається розрахункове значення, отримане на підставі випробувань та експлуатації обладнання, що є константою. При цьому введенням поправочних коефіцієнтів враховуються умови експлуатації. Інтенсивність відмов залежить від наявного устаткування, його елементної бази, способу зʼєднання елементів і т. д. і є унікальним для кожної конфігурації системи. Нами розглядається типова сучасна система АГЗ видобувної дільниці.
Після параметричної ідентифікації розробленої моделі, і вирішення рівнянь моделі чисельними методами для інтервалу часу в 1 рік, були отримані наступні
результати: ймовірність появи події вибух
як функція часу швидко досягає сталого значення РB = 6,6 ⋅ 10-4.
Динаміка зміни ймовірності незначна і
представлена на рис. 4, де час виражено в днях.

Рисунок 4 – Імовірність події Вибух метаноповітряної суміші
як функція часу
Згідно з результатами моделювання ймовірність виникнення події вибух
в гірничій виробці перевищує допустиму ймовірність події вибух
(згідно ГОСТ 12.1.010–76 Вибухобезпека. Загальні вимоги
, ймовірність виникнення вибуху на будь‑якій вибухонебезпечній ділянці на протязі
року не вище 10-6) на 2 порядки.
5. Оптимізація систем автоматичного газового захисту
Підвищення надійності системи можна досягти двома шляхами: зниженням інтенсивності відмов, зниженням інтенсивності профілактичних простоїв. При моделюванні системи без виконання профілактичних робіт отримані результати на 1 порядок перевершують допустимі (рис. 5), отже, даний шлях не достатній.
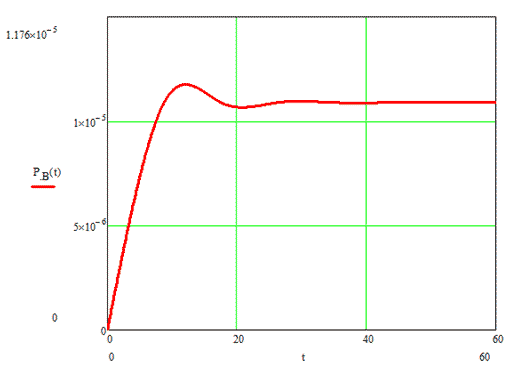
Рисунок 5 – Імовірність події Вибух метаноповітряної суміші
як функція часу для системи без профілактики
Розробка принципово нової системи з повним дублюванням датчиків та ліній звʼязку недоцільна, так як її застосування важко обгрунтувати економічно. Для відповідності ймовірності вибуху необхідним значенням необхідно знизити на порядок ймовірність відмови елементів системи, що можливо при застосуванні резерву з автоматичним пристроєм перемикання. Для того, щоб відмови пристрою відключення, датчика та лінії звʼязку не створювали небезпечних станів пропонується: живити котушку контактора, що подає напругу на ділянку, через нормально розімкнутий контакт системи АГЗ; використовувати такі інтерфейси передачі даних від датчика до аналізатора що дозволяють організувати функцію самодіагностики, наприклад аналогова струмова петля 4..20 мА або передачу даних у вигляді цифрового коду.
Наявність резервного контролера дозволяє не переривати технологічний процес для заміни апаратури що відмовила [7]. Резервний мікроконтролер повинен виконувати той же набір інструкцій, що і основний, однак мати іншу адресу в промисловій мережі, щоб перемикання на резервний МК фіксувалося концентратором інформації вищого рівня АСУ ТП. Доцільно застосувати ненавантажений резерв. Найбільш відповідальним вузлом в такій структурі є пристрій, що здійснює автоматичне перемикання живлення з основного на резервний МК. На вхід даної схеми надходять контрольні імпульси від основного МК, наявність яких свідчить про штатний режим роботи пристрою. Відсутність зазначених імпульсів свідчить про відмову основного МК і необхідность включення в роботу резервного контролера. Періодичність контрольних імпульсів задається сторожовим таймером основного МК.
На принциповій схемі пристрою перемикання (рис. 6) генератор G являє собою зовнішній вихід сторожового таймера основного МК.
Ланцюжок R1, C1 згладжує
імпульсний сигнал. В якості перемикаючих елементів використовуються MOSFET‑транзистори з каналом n‑типу, які в сталому режимі споживають досить малу
потужність. Оскільки MOSFET‑транзистори мають паразитне ємність по каналу затвор‑сток, то на їх вході включений повторювач на операційному підсилювачі,
що виключає вплив ємності транзистора на даний ланцюг [8]. Сигнал з виходу операційного підсилювача надходить на затвори транзисторів VT1 і VT2.
VT1 використовується в якості вимикача, через який подається живлення на основний МК. До тих пір, поки на затворі транзистора
VT1 напруга вище потенціалу
землі – він відкритий. Транзистор VТ2 і резистор R2 утворюють логічний елемент НЕ. Поки сигнал подається на затвор VТ2 – VТ3 закритий. У разі,
якщо
основний МК перестає подавати контрольні імпульси, потенціал затвора VТ2 дорівнює 0
, він закривається і через резистор
R2 відкривається транзистор VT3,
що створює ланцюг живлення резервного МК. Кнопка S1 служить для запуску основного МК,
замикаючись, вона шунтує VТ1, утворюючи ланцюг живлення основного
МК. Параметри R1 і C1 розраховуються виходячи з амплітуди і прогальності контрольного сигналу, які визначаються
напругою живлення і частотою тактового
генератора МК.

Рисунок 6 – Принципова схема пристрою перемикання
Робота розглянутої схеми моделювалася з використанням пакета MicroCAP. На рис. 7 представлені графіки перехідного процесу в схемі при подачі живлення.
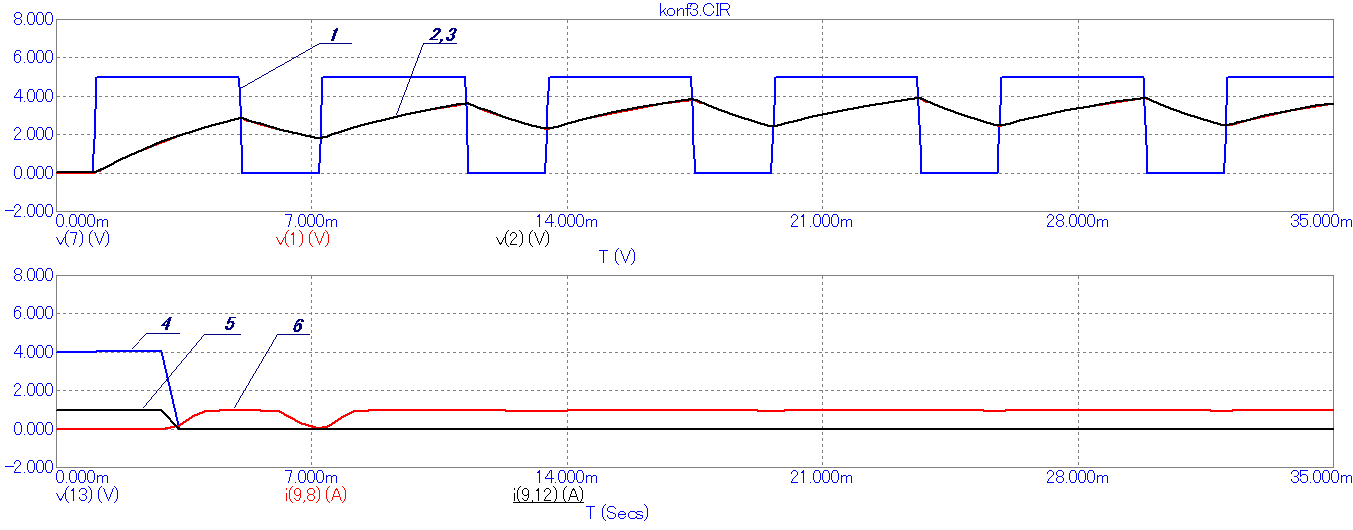
Рисунок 7 – Графіки перехідного процесу в схемі при подачі живлення: 1 – контрольний імпульс, 2 – напруга на виході RC‑ланцюга, 3 – напруга на виході повторювача на операційному підсилювачі, 4 – напруга на затворі транзистора VT3, 5 – струм по каналу виток‑сток транзистора VT3, 6 – струм по каналу виток‑сток транзистора VT1
При подачі живлення транзистор VT1 закритий, VT3 – відкритий. Після першого контрольного імпульсу VТ3 замикається, після другого – VТ1 повністю відкритий. Таким чином, тривалість перехідного процесу відмикання VT1 становить 12 мс. Після третього контрольного імпульсу RC‑ланцюжок переходить в квазісталий режим. Слід зазначити, що збільшення прогальності контрольних імпульсів і зниження їх амплітуди призводить до збільшення тривалості перехідного процесу.
На рис. 8 представлені графіки перехідного процесу в схемі при відмові основного мікроконтролера.
За відсутності контрольного імпульсу RC‑ланцюг розряджається, потенціал на виході повторювача стає рівним нулю, VT1 і VТ2 замикаються, зʼявляється позитивний потенціал на затворі VТ3 і починає протікати струм в ланцюзі живлення резервного МК. Тривалість перехідного процесу складає 16 мс.
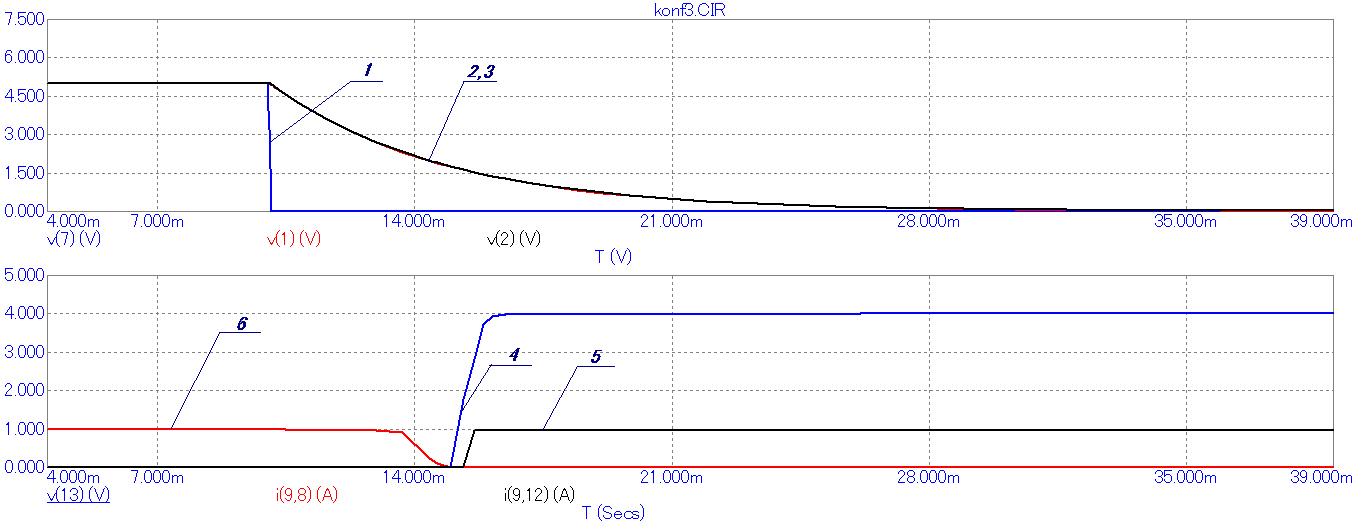
Рисунок 8 – Графіки перехідного процесу в схемі при відмові основного мікроконтролера: 1 – контрольний імпульс, 2 – напруга на виході RC‑ланцюга, 3 – напруга на виході повторювача на операційному підсилювачі, 4 – напруга на затворі транзистора VT3, 5 – струм по каналу витік‑стік транзистора VT3, 6 – струм по каналу витік‑стік транзистора VT1
Таким чином, підвищити надійність моніторингу стану рудничної атмосфери можливо за рахунок пасивного резервування мікропроцесорного пристрою захисту.
6. Робота АГЗ при нестаціонарних процессах метаноутворення
При розрахунках витрати повітря на провітрювання виробок, приймається допущення, що кожна одиниця площі вугільного масиву виділяє рівну обʼємну кількість метану, тобто вважається, що метановиділення стаціонарне. У такому випадку концентрація метану в рудниковому повітрі, у міру його просування по виробках, збільшується наростаючим підсумком. Однак, існує ряд процесів – газодинамічних явищ, при яких з незначної площі вугільного масиву, за короткий проміжок часу, виділяється кількість метану достатня для утворення вибухонебезпечних концентрацій. Як правило, ГДЯ призводять до вибухів метаноповітряної суміші на ділянках обладнаних автоматичним газовим захистом.
Складність захисту від ГДЯ, полягає в наявності транспортної затримки, яка визначається швидкістю руху повітря і довжиною виробки. Згідно Правил безпеки [9], допустима швидкість руху повітря по виробках vдоп = 0,25..4 м/с. При довжині очисного вибою від 200 до 250 м, транспортна складова затримки може становити від 50 до 1000 с (рис. 9), що є неприпустимим.
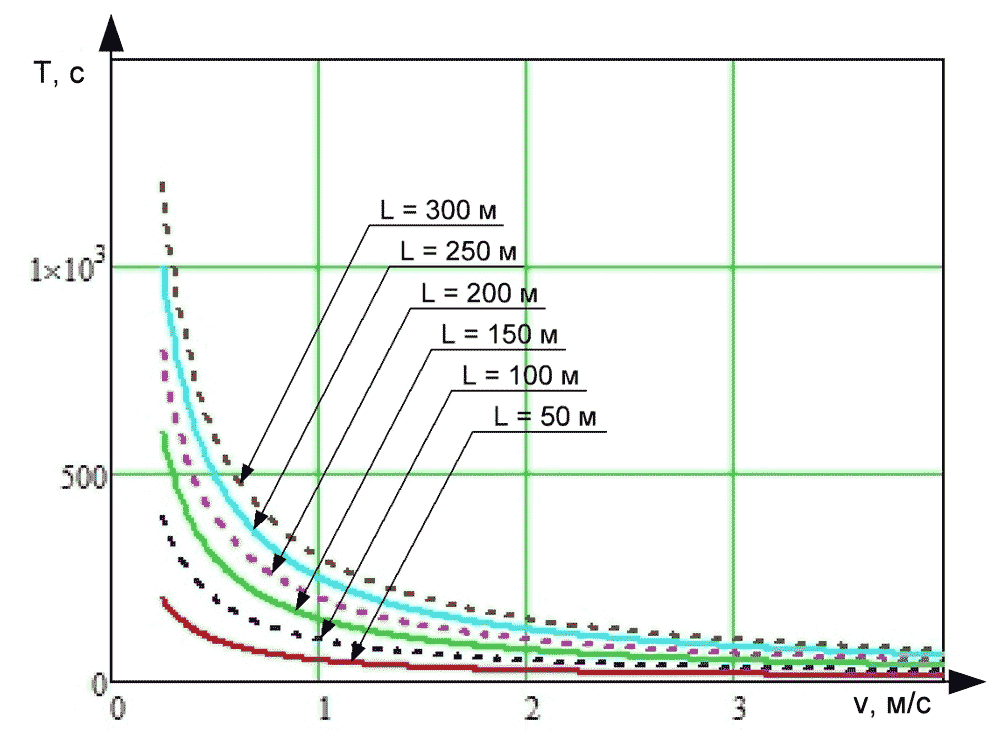
Рисунок 9 – Графіки залежностей транспортної затримки виміру концентрації метану від швидкості повітря і довжини очисної виробки для датчика, розташованого на вентиляційному штреку
Наявні методи поточного прогнозу різних типів ГДЯ були, в основному, запропоновані і обгрунтовані кілька десятиліть тому, і
засновані на використанні
первинних фізичних величин, що характеризують руйнування газонасиченого вугільного масиву: діючих механічних напруг, характеристик міцності вугілля і порід,
тиску газу в пласті, газоносності вугілля, його вологості і т. п. [10]. Ці величини вимірювалися,
так званими, інструментальними
методами,
що полягають в експрес‑аналізі проб газу і вугілля, взятих при бурінні передових розвідувальних свердловин. З метою забезпечення
безпеки необхідний безперервний контроль фактора розвʼязування ГДЯ. Окремі методи безперервного моніторингу:
спектрально‑акустичний, акустичної
емісії, по температурі забою та інші, крім низької точності вимагають проектування, створення, монтажу та експлуатації принципово нових систем в
умовах очисного вибою. При цьому, інформацію про початок ГДЯ можна мати, обробляючи показники датчиків існуючих систем.
Покажемо, що за
допомогою апаратури АГЗ можна контролювати газовий фактор викидонебезпечності, що характеризує тиск газу в пласті
і його газофільтраціонную
здатність. Відомо [11], що тиск вільного газу Р, спрямований у бік виробки, на відстані х
від оголеної поверхні виробки може бути описаний
наступною напівемпіричної формулою:
![]() | (2) |
де m – константа, що характеризує вплив на тиск газу пористості вугілля; G – витрата газу з вибою виробки, м3/с; k0 – коефіцієнт, що характеризує газопроникність пласта, м-3; ψ = 1/xст – константа, обумовлена відстанню xст від вибою до ділянки масиву, де тиск газу стабілізується, м-1;
![]() | (3) |
Sз – площа поверхні вибою виробки, м2; η – коефіцієнт динамічної вʼязкості метану, Па⋅с; Pат – тиск газу на площині забою, Па.
Потрапляючи у виробку, газ змішується з повітрям, у результаті чого концентрація метану знижується. Газовиділення у вироблення Хв складається з газовиділення з поверхні забою, бортів вироблення і відбитого вугілля:
![]() | (4) |
де Gб і Gо.у. – витрата газу з поверхні відповідно бортів вироблення і відбитого вугілля, м3/с⋅м2; Sб і Sо.у. – відповідно, поверхня бортів вироблення і відбитого вугілля на ділянці від вибою до місця установки датчика метану (наприклад, ДМТ‑4) апаратури автоматичного газового захисту, м2.
Це газовиділення можна визначити через поточне значення Cт концентрації метану в атмосфері виробки:
![]() | (5) |
де Q – витрата повітря вентилятора місцевого провітрювання (ВМП), м3/с; Cт – поточне значення концентрації метану, заміряне датчиком метану, %; C0 – концентрація метану в свіжому струмені повітря, що надходить у виробку.
Тоді витрата газу з вибою виробки:
![]() | (6) |
де Cф – фонова концентрація метану, до початку роботи комбайна, що характеризує газовиділення з бортів виробки і відбитого, але не відвантаженого вугілля, %, за умови, що C0 = 0 в момент виміру фонової концентрації.
Шуканий тиск газу на деякій критичній
відстані від вибою виробки хкр, де починається викидонебезпечного зона, визначиться
підстановкою (6) в (2):
![]() | (7) |
Таким чином, концентрація метану у виробці, контрольована апаратурою контролю метану, характеризує тиск вільного газу в привибійній зоні вугільного пласта і його газофільтраціонную здатність – параметри, що визначають газовий фактор викидонебезпечності.
Для підвищення швидкодії АГЗ пропонується установка стаціонарних датчиків на секціях кріплення вибою. Дане рішення дозволить скоротити час транспортної затримки при виникненні газодинамічних явищ. Кількість додаткових датчиків визначає час транспортного запізнювання:
![]() | (8) |
де L – довжина вироблення між датчиками метану, v – швидкість повітря у виробці.
Так як швидкість повітря в очисному вибої величина нерегульована, то для зниження величини затримки необхідно зменшити відстань між сусідніми датчиками. Якщо прийняти оптимальне значення величини транспортного запізнюванн, то необхідна кількість датчиків метану в очисному забої становить:
![]() | (9) |
7. Боротьба з шаровими скупченнями метану
Апаратура автоматичного газового захисту контролює концентрацію метану в місцях регламентованих правилами безпеки у вугільних шахтах. Однак з огляду на те що швидкість і витрата повітря не рівномірна для всіх виробок можливі шарові скупчення метану у вибухонебезпечних концентраціях в місцях не контрольованих апаратурою АГЗ. Зрозуміло, що неможливо встановити датчики у всіх місцях можливого скупчення метану. Тому пропонується інтеграція мобільного компонента в систему автоматичного газового захисту. В даний час поширені шахтні головні світильники з вбудованим датчиком концентрації метану, зокрема СМГВ.1А.Р.05, KLW4LMX і ін. Перспективним напрямком у розвитку шахтних інформаційно керуючих систем є системи позиціонування гірників, типу СПГТ‑41. Цілком логічним є обʼєднання цих технологій в одну.
Результати вимірювання з вбудованого в головний світильник датчика будуть використовуватися не тільки для сигналізації аерогазової обстановки гірнику, а й разом з персональним ідентифікатором будуть транслюватися в систему позиціонування. Структурна схема пропонованого портативного блоку вимірювання концентрації метану і позиціонування приведена на рис. 10. Датчик метану, через блок узгодження подає результати вимірювань на вхід вбудованого в мікроконтролер аналого‑цифрового перетворювача. Вибірка результатів вимірювань зберігається у внутрішній памʼяті МК. Якщо мікроконтролер через приймач отримує сигнал від мітки системи позиціонування, він передає в систему позиціонування не тільки ідентифікатор, а й усереднене і максимально зареєстроване з моменту останнього звернення значення концентрації метану. При цьому функція оповіщення гірника мерехтінням світильника збережена (блок сигналізації). Таким чином, є можливість контролювати значення концентрації метану у всіх виробках, в яких знаходиться персонал. Дана технологія дозволить доповнити стаціонарні системи газового захисту на видобувних і підготовчих ділянках, а також контролювати значний простір гірських виробок, без впровадження дорогої інфраструктури стаціонарних систем.
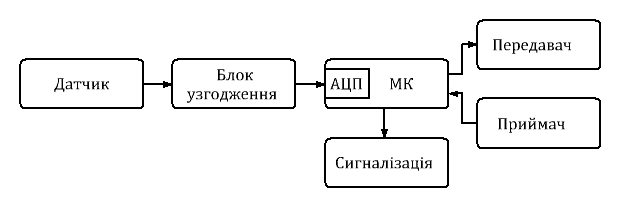
Рисунок 10 – Структурна схема портативного блоку вимірювання концентрації метану і позиціонування
Висновки
Дана робота присвячена підвищенню надійності автоматичного газового захисту шахти. У ній розглянуті сучасні тенденції розвитку систем
АГЗ, і перспективи
їх вдосконалення. У роботі розглянуті причини виникнення такого стану як Вибух метаноповітряної суміші
і складена імовірнісна модель даної події.
У результаті моделювання найгіршого
стану була виявлена недостатня надійність газоаналізаторів систем АГЗ.
Для усунення виявленого недоліку була розроблена
і досліджена схема пасивного резервування мікроконтролера газоаналізатора.
При розгляді роботи АГЗ при виникненні ГДЯ, а також шарових скупчень метану, зазначено, що АГЗ не в змозі нівелювати дані небезпечні стани, зважаючи на особливості структури побудови даних систем. Для усунення даних недоліків:
- вказано на можливість контролювати параметри, що визначають газовий фактор викидонебезпечності за допомогою даних про концентрацію метану;
- запропонована інтеграція мобільного компонента в структуру АГЗ;
- запропоновано спосіб скорочення часу транспортного запізнювання.
Важливо! При написанні даного реферату магістерська робота ще не завершена. Остаточне завершення: грудень 2014 року. Повний текст роботи та матеріали по темі можуть бути отримані у автора після зазначеної дати.
Перелік посилань
- Кашуба И. О. Оценка эффективности контроля содержания метана в рудничной атмосфере при крупных авариях в угольных шахтах / О. И. Кашуба, В. Н. Медведев, О. А. Демченко // Науковий вісник УкрНДІПБ, 2012, № (25). – с. 68‑78.
- Басовский Б. И. Автоматическая газовая защита и контроль рудничной атмосферы / Басовский Б.И., Биренберг И.Э., Карпов Е.Ф.; – М.: Недра, 1984 – 284 с.
- Курносов В. Г. Научные основы автоматизации в угольной промышленности: опыт и перспективы развития: монография / Курносов В. Г., Силаев В. И.; Международный институт независимых педагогических исследований МИНПИ – ЮНЕСКО, ОАО
Автоматгормаш им. В.А. Антипова
. – Донецк: изд‑воВебер
(Донецкое отделение), 2009. – 422 с. - Федорченко А. А. Микропроцессорное устройство прогнозирования опасности взрыва метановоздушной смеси в шахте / А. А. Федорченко, С. В. Василец // Автоматизація технологічних об’єктів та процесів. Пошук молодих. Збірник наукових праць ХІII науково‑технічної конференції аспірантів та студентів в м. Донецьку 14‑17 травня 2013 р. – Донецьк, ДонНТУ, 2013. – с. 369–371
- Надежность электрооборудования угольных шахт / Б. Н. Ванеев, В. М. Гостищев, В. С. Дзюбан и др.; Под ред. А. И. Пархоменко. – М.: Недра, 1994. – 255 с.
- Колосюк В.П. Защитное отключение рудничных электроустановок / Колосюк В. П. – М: Недра, 1980 – 334 с.
- Федорченко А.А. Повышение надежности мониторинга состояния рудничной атмосферы за счет резервирования микропроцессорного устройства защиты / А.А. Федорченко // Севергеоэкотех‑2013. Сборник научных работ XIV международной молодежной научной конференции в г. Ухте 20‑22 марта 2013 г. – Ухта, УГТУ, 2013. – с. 117–120.
- Хилл У. Искусство схемотехники / Хилл У., Хоровиц П. – М.: Мир, 1998. – 704 с.
- НПАОП 10.0‑1.01‑10. Правила безпеки у вугільних шахтах. Наказ Державного комітету України з промислової безпеки, охорони праці та гірничого нагляду № 62 від 23.03.2010. – 150 с.
- Шадрин А. В., Шадрина О.Я. Сравнительный анализ известных критериев текущего прогноза выбросоопасности угольных пластов // Информационные недра Кузбасса: Труды IV Всероссийской научно‑практической конференции. ‑ Кемерово: ООО
ИНТ
, 2005. – с. 84–86. - Глушко В. Т. Геофизический контроль в угольных шахтах. / Глушко В. Т., Ямщиков В. С., Яланский А. А.; Киев: Наукова думка, 1978. – 224 с.