Abstract
Content
- Introduction
- 1. Theme urgency
- 2. Goal and tasks of the research
- 3. A review of research and development
- 3.1 Review of international sources
- 3.2 Review of national sources
- 3.3 Review of local sources
- 4. Development of technology for production of protection combined method with high load-bearing capacity and the establishment of its optimal parameters
- Conclusion
- References
Introduction
The constant increase in the Donbass mining depth is accompanied by increase in difficulty of mining and increasing the total length of mine workings. Since the second half of the 90s. only Donetsk and Makeevka regions of Donbass coal average depth of mining reached the mark of 850 m., and the total length of supported excavation workings was about 2000 km.
Unsatisfactory state mining complicates the mine transport, cleaning and airing development faces leads to an increase in the number of workers employed in jobs keeping workings, which ultimately reduces the technical and economic performance of the mine. Especially acute resilience reservoir excavation workings, supported in weak surrounding rocks in the zone of influence of intensive treatment works. Therefore, the problem of maintaining mining is highly relevant and more attention is paid to the development of effective ways and means to protect the development workings.
1. Theme urgency
The cheapest on the material costs are methods involving the use of an ordinary rock. And, despite the fact that they are one of the most labor-intensive with the greatest ductility, and they are the most common.The most famous construction of the ordinary rock band is rubble. For its facilities used to conduct excavation rock drifts or specially conducted after the longwall face rubble drifts. Limited scope, high complexity, significant shrinkage — are the main disadvantages of the rubble strip. In addition, after shrinking to 30–45% rubble band begins to work as pillar, squeezing rocks in production [16,19-21].
In my opinion, these methods should be used and developed, developing technological solutions to reduce compliance and security installations to increase their carrying capacity.
2. Goal and tasks of the research
The most famous construction of the ordinary rock band is rubble. For its facilities used to conduct excavation rock drifts or specially conducted after the longwall face rubble drifts. Limited scope, high complexity, significant shrinkage — are the main disadvantages of the rubble strip. In addition, after shrinking to 30–45% rubble band begins to work as pillar, squeezing rocks in production [16].
3. A review of research and development
Currently increasing use is being made of solid design and system development based on solid. This is primarily due to the fact that continuous development system is used most often on very thin and thin layers, and therefore its scope is about 95% of coal reserves [1]. However, the most common system — long poles with the shortest period of the strike, insurrection or fall.
One of the main advantages of the pillar system development is the complete separation of time and space clearing and preparatory work, which creates favorable conditions for the application of high — performance clearing mechanized complexes providing large load on longwall face. This is confirmed by the fact that almost all the longwall face — tysyachnitsy fulfill coal seams long poles.
Despite the advantages pillar continuous development systems before, statistics show outlined the second half of the 80s the reverse trend. Analysis shows that with increasing depth development has been steadily declining equity stake system development (68% at a depth of 600 m. and 39% at a depth of 1000 m.). The share of the combined system remains at the same level (19–20%), and solid increases significantly — from 13 to 37% [1].
Not pleading merits pillar system, this system design, despite the obvious advantages that it is on the main mines of Donbass, has significant drawbacks:
• Almost all the mines there is a break in time between the end of mining excavation and preparation of new posts. Of the lack of highly efficient and reliable tunnel combines the pace of excavation of drifts very low. To prepare column length 1200–1500 m. with average faces motion tunnel conveyor and ventilation drifts 80 m. requires up to 1.5 years. Conducting split furnace cleaning and installation of mechanized complex even more increases the gap in time. Result — reducing the number of stopes. Consequence — the decline in production and deterioration of all technical and economic indicators of mines;
• In the current economic conditions in the mines are no funds for the purchase of high — clearing mechanized complexes. Namely, when mining excavation pillars such complexes are shown the main advantages pillar system;
• In developing the reserves at a depth of 500–600 m. increasing confining pressure, temperature, gas content, the danger of sudden coal and gas, and mining strikes. In the long term recess seams less than 0.8 m. will be conducted in 50% with stopes are unstable roof on seams over 0.8 m. 70% of longwall face will operate at very unstable and fragile roofs [2]. It is difficult to pre-contouring stocks preparatory development and complicates maintenance. Ultimately the cost of human and financial resources to carry out the maintenance and excavation at pillar system drifts higher than the solid;
• Virtually all of the excavation of rock drifts issued on the surface, which leads not only to the cost of transporting it, but also pollute the environment. When solid rock system is laid in rubble bands;
• In order to increase the pace of their drifts excavation excavation is usually performed without separate slaughter narrow excavation of coal and rock.
Therefore serious alternative pillar system design is solid. In the last three or four years, she again began to be widely used at various depths especially when removing layers of outburst. In modern conditions clearly manifested dignity continuous development system [3]:
• Longwall drifts are unloaded zone, feeling less pressure from the surrounding rocks Statistics show that at a depth of 600–650 m. the cost of maintaining drifts lower than the pillar;
• Speed of drifts less than the pillar system, so a permanent deficit mounting frames less noticeable;
• Creates good prospects for drifts wide slaughter, thus increasing the amount of coal produced and post rock in the mine;
• Virtually all of the breed by laying open drifts goes to rubble bands and stowing, which is particularly important from an environmental point of view;
• Concentration clearing and preparatory work within the horizon, panels, floors higher than the pillar system.
But pillar system development more favorable conditions for treatment mechanized complexes than in the solid. This is particularly evident in normal geological conditions and good stability of excavation of drifts. If these conditions are unfavorable, the complexes do not work well, as evidenced by the statistics for the last ten years. For example, it is proved [2], that the system is competitive with solid pillar using mechanized complexes, and rightly draws attention to the fact that "in the calculation of the relative cost–effectiveness of different complexes are often neglected costs preconditioned pillars, thereby artificially high efficiency pillar system. "Confirmation of this is the experience of countries where the law prohibits the extradition of rocks at the surface in the German mechanized complexes operate in a continuous system with full goaf, issuing of stope up to 2000 tons of coal per day.
Thus, analysis of current trends in the development of underground coal seams of Ukraine to the following conclusions: in complex geological conditions, characterized by considerable depth, unstable rock walls, high rock pressure, gas content and outburst, lack of road headers, clearing mechanized complexes economically feasible and environmentally sound further extension of the scope of continuous development. With the economic crisis, this system not only competitive with pillar, but in many cases is preferable.
As a result, a brief analysis of strengths and weaknesses and areas of application of existing systems development can be concluded that it is necessary to design systems development, combining the advantages of pole and solid systems combined systems, and providing reuse workings.
Recently pressing issue reuse workings progressive way of keeping the workings for the lava to reuse a small volume of use compared with other methods, despite the fact that experience has revealed a number of its advantages — the decline in development workings, increase load on the sewage treatment, improvement of ventilation in production areas [4-8]. Along with this, as experience has shown , increases dramatically the complexity of maintaining the roadway, caused by the need of repeated perekrepleniya Bomb rocks with soil. In most cases, existing methods of maintaining the workings to keep them in working condition fails.
Expandarea and volume of use of progressive technologies pillarless reuse excavation workings may address issues of location, protection and maintenance of workings.
3.1 Overview of international sources
Abroad this method of protection is not investigated .
3.2 Overview of national sources
Today at coal mines some experience with the protection of development workings artificial constructions. Analysis of the results of their application reveals their strengths and weaknesses, as well as area of effective application.
cheapest on material costs are methods involving the use of an ordinary rock. And, despite the fact that they are among the most labor-intensive, and are the most common. The most famous construction of the ordinary rock band is rubble. For its facilities used to conduct excavation rock drifts or specially conducted after the lava rubble drifts. Limited scope, high complexity, significant shrinkage — these are the main disadvantages rubble strip. In addition, after shrinking to 30–45% rubble band begins to work as pillar, squeezing rocks in the production of [ 16 , 19-21].
In the production association "Ukrzapadugol" when reusing precinct workings widely spread way of protection Butovo stripes. But this method is time — consuming because of the large shrinkage and rubble bands (50–60%) does not provide a satisfactory condition workings. Along with rubble strip widespread in the pool was way protection workings with one — two rows of wooden pyres. The complexity of this method is considerably less than in the protection of Butovo stripes. But high compliance fires also cause degradation of the workings. Therefore, many mines began to apply Rolling fires in conjunction with organ bolting. The rigidity of such structures is considerably higher, resulting in a decrease and lowering of the roof of the roof there is no fault on the array.
On mine "Velikomostovskaya" instead of fires applied duplex organ lining, installed at a distance of 1 m from the contour of the roadway. The high rigidity of the lining also permits effective collapse of the roof over the roadway loop and reduce the size of consoles rocks, hovering over elaboration. Observations have shown that with this method of protection status workings no worse than in protecting knurled bonfires. This dramatically reduces the complexity and expense of the forest protection workings.
On mine "Velikomostovskaya number 3" developed passport mounting couplings, which allowed to exclude roof collapse at pairings, as well as passport protection drifts, ensuring their maintenance for re–use with virtually no maintenance. Passports provides for the protection of openings used mutually perpendicular organ wall. Application mutually perpendicular rows organ lying on the presence of weak rocks soil allows you to maintain and reuse drift without repair. The presence of "pockets" on the part of developed space provides remission rocks in a mine in the production of ripping the soil [22].
On mine "Novovolynska number 9" drift after passage guarded by longwall face artificial barriers variable stiffness, consisting of wood fires and organ series. Near the roadway were laid — row strip of fires spaced 0.5 — Next 1 m. from the roadway installed duplex organ lining. Rigidity of the support elements increases from the roadway to the goaf of density calculations and setting fires organ series. Knurled fire with two rows of two — row organ lining support breed console and serves as a hard—cutting support along which the mold and close the main roof of the exhaust space. As a result of applying the method of protection drift has been saved for reuse [23].
On mine it. Kostenko reuse drift became possible after the application of three — row instead organki pliable strip rubble. Increase rows organki not led to a noticeable improvement of production, decrease — its failure [24].
construction analysis, constructed of wood, showed that these structures may be amenable (fires) and rigid (Rolling bonfires, organ lining).
Engineers mine "Jubilee" was proposed by way of protection, which included the following: rubble drift with organ bolting trim array besieging roof; using a large amount of shrinkage rubble strip discharge at the maximum allowable distance of the roof, creating the possibility of its shrinkage; provide maximum resistance precipitating roof by installing staggered concrete pedestals.
Experience adopting this method of protection showed that rubble drift in conjunction with organ bolting really contributed circumcision roof. By the rubble of the strip is soft squeeze, but 5–8 m. distance was not enough for the desired precipitation. In the formation of the load entered as a direct and main roof, capturing a significant bearing pressure distribution area. Load on w/w thumbs significantly exceeded their carrying capacity.
Using this method, the protection of the roof was cut off from the main body and formed with rubble drift console, which relied on an array of untouched, the lower excavation column. The maximum of the stresses due to the cut line formed rubble drift comes to Butovo strip. Perceiving this load rubble band precipitated by 40–55%, occurred at the same time the gap of the active part of the roof of the overlying layers.
On mine "Orehovskaya" laboratory rock mechanics KSMI protection is provided a method of development workings retained after passing longwall face, rubble strips with pre — disposal and simultaneous unloading of the marginal zone of the coal seam from stress cracks using variable stiffness.
to protect workings at the mine. Bazhanov used method of construction of the bands and sparse concrete blocks. At the same time from the goaf publishing two series of solid wood fires, and from the vehicle drift — wall of blocks BZHBT. Nether laid breed derived from ripping drift. The method has shown good results for keeping generation [27].
3.3 Overview of local sources
On the basis of the location
methods are divided into the workings of the ways:
• For coal seam with the bottom, top or bottom and the top ripping;
• On the rocks at some distance from mineral deposits;
• In areas of low stress (or underworked in nadrabotannoy thicker, and tumbled on compacted rocks, close to the out space or vprisechku to it).
Field production held steady on the rocks in the soil reservoir to improve conditions. They are connected with the formation or workings with treatment staple, stingrays, crosscuts. Apply field training stands at slaboustoychivyh host reservoir rocks and with a significant term of operation [6].
Zborschik [7, 8] has been proposed to use a method of protection workings based on conducting them caving roof. Experience of using the method indicates that it is effective only when a continuous system development.
In most cases, existing methods of maintaining the workings to keep them in working condition fails, and to serve the next column shall be a new — vprisechku to old [5]. Conducting workings vprisechku to goaf is a promising way. This technology development is carried out in a pre — weakened array under rocks immediate collapse consoles and the main roof. The main reasons hindering the application of this method are: the need to change the order of fields and training excavation difficulties in implementing complex hypsometry formation and low efficiency when used in difficult geological conditions.
Holding reservoir openings is most common in comparison with other methods. Location relative to production of coal seam is taken depending on the physico — mechanical properties of the host rocks and the type of lining. Develop adjacent to the working face, it is advisable to conduct a Bomb rocks soil formation, without violating the integrity of the roof rocks. At low power Puig rocks (up to 2 m.) production with the lower recommended ripping with full notch Puig layer [15]. When applying arch support allowed Bomb roof rocks on the value of 0.5–1.0 m. Large Bomb possible when hard rock roof.
Just the Donetsk National Technical University (Department of mineral development) method was developed using an ordinary rock rock pillars under the leadership Negrei S. [35]. At present the project is under development.
4. 4. Development of technology for production of protection combined method with high load-bearing capacity and the establishment of its optimal parameters
The analysis methods of protecting openings using an ordinary breed has been proposed combined security structures (Fig. 1)[3], in which as the main limiting elements will apply breed rack mounted along the production, to be concluded between the rubble band of small width[20].
In general, at this stage of the research planned:
- Structural test computation with two spaced rock pillars of the two bags in a row, and oriented perpendicular an upper, which will be backfilled between species (Fig. 2)[29];
- Test construction described with No. 1, but with different fractional composition of the rocks in the free coating (Fig. 3);
Fig. 1 – Flowsheet mounting end portion of lava and construction combined security structures of ordinary rock.
Fig. 2 – General view of the test design combined pedigree.
- Structural test computation with two rock pillars spaced from one bag in the series, which will be backfilled between breed (Fig. 4);
- Test construction described with paragraph 3, but at different distances between the breed stands in width (Fig. 4);
- Free bags of rock laying on the side face of the breed Dumping natural inclination angle to the horizontal plane (Fig. 5).
Testing of trained models yielded an array of data to support optimal parameters combined rock supports increased carrying capacity.
By measuring the height shrinkage designs at their various parameters under the influence Surcharging were obtained depending on whose study is possible to establish the type of design with high load capacity (Fig. 6-9)[27].
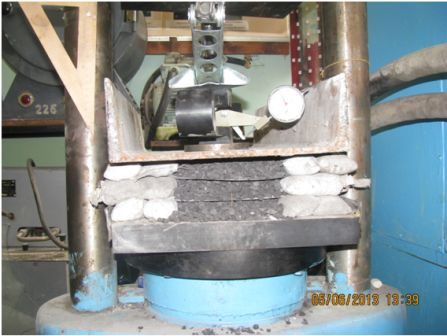
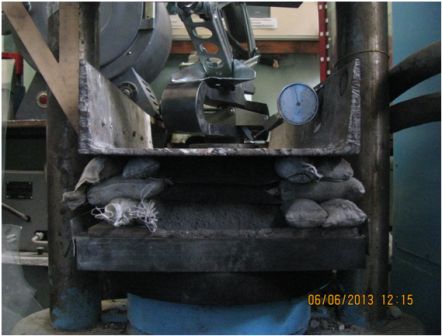
Fig. 3 – General view of the test combined with bulk rock structures of rocks of different fractions.
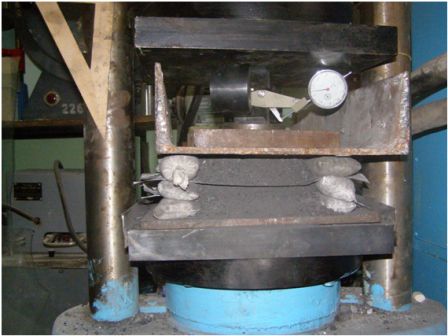
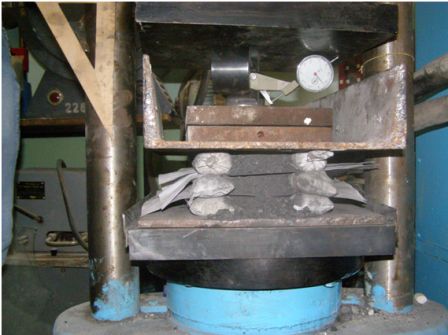
Fig. 4 – General view of the test combined rock structures with single-row racks pedigree.
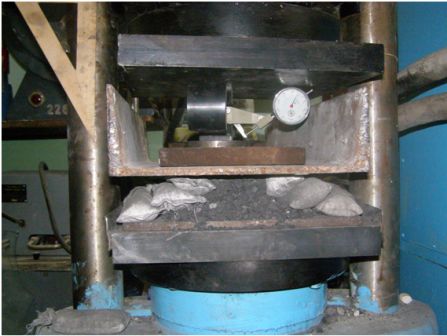
Fig. 5 – General view of the test combined rock structures with a free bag of rock laying on the side face of the breed dumping.
From these dependences that increase fractional composition composing a security design pedigree individually significant effect on reducing its compliance, and increase the size of individual from 0.02 to 0.1 times the height of the security structures leads to a decrease in compliance 1.55 times (Fig. 6).
In unexamined in rock walls of the bag 2 in a row with their laying perpendicular to each other protective structures adjustment structure yielding generally varies from 6.5 to 10.1% depending on the size separately in a bulk amount (Fig. 6).
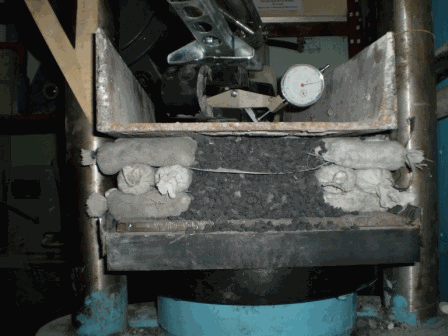
Animation. Behavior of the model during execution.
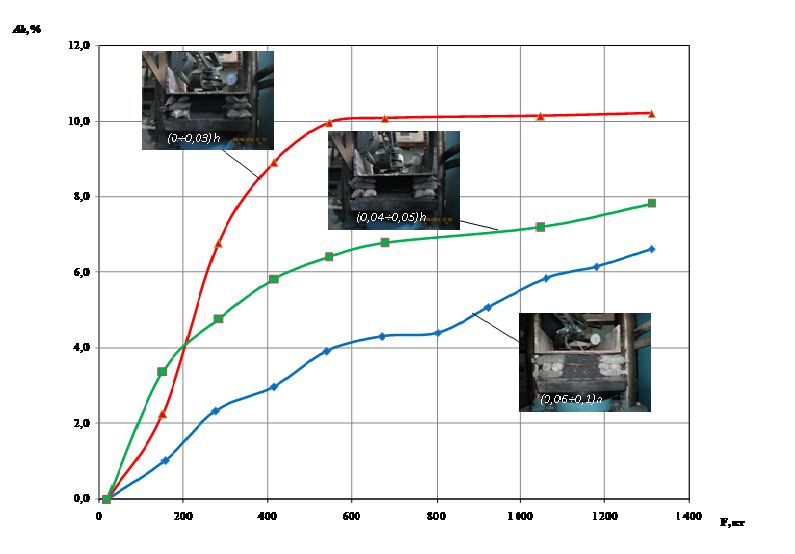
Fig. 6 – Dependence of shrinkage security installations on the load at various fractions breed dumping.
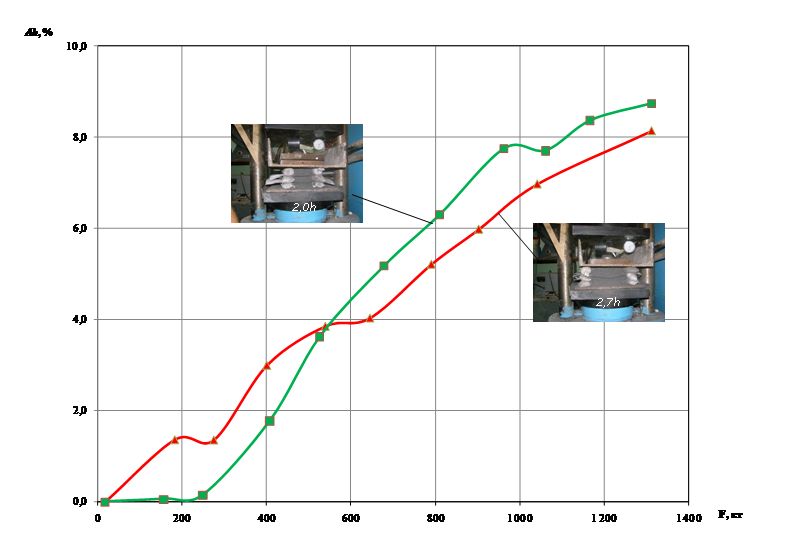
Fig. 7 – The dependence of the shrinkage of the protective structures with different load values of the width.
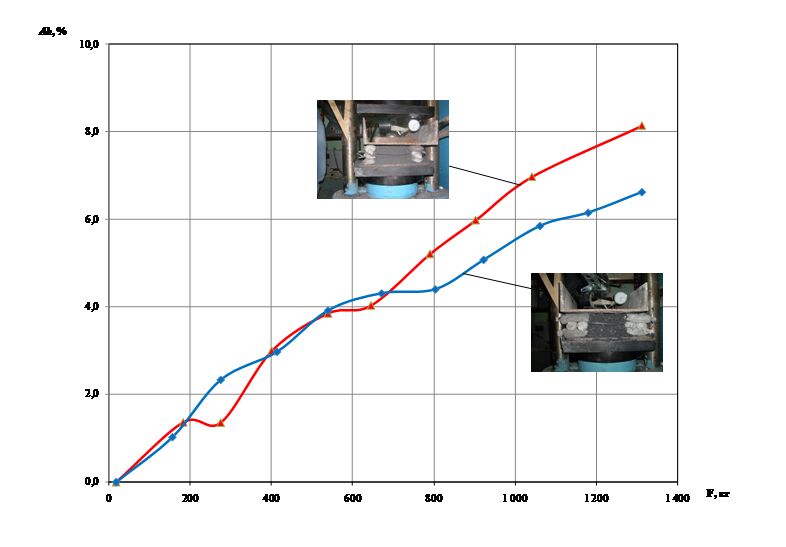
Fig. 8 – Dependence of shrinkage security installations on the load at different amounts of bags in rock walls./p>
Fig. 9 – Dependence of shrinkage security installations on the load at various circuits installation of rock walls.
Conclusion
Increasing the width of the combined security facilities under the same conditions from 2.0 to 2.7 structure height does not significantly affect its stability and decrease compliance observed within 0.5% (Fig. ). But it should be noted that the compliance of these structures is 8.0–8.5%, which is 5.7 times less than with conventional rubble strip which in turn is 3–4 times greater and thus requires more breeds.
Increasing the width of rock walls in the composite structure by increasing the number of bags entails a decrease in compliance (increase in carrying capacity) to 1.5%. It is also not a serious option for the conditions under consideration (Fig. 8).
The presence of security in age structure limiting elements, in particular rock walls, entails an increase in its load-bearing capacity, and, the stability of a wall, the more effective security structure. Compliance structure for vertical installation of single-row rock walls in Butovo band decreases by 1.5 times (Fig. 9). The variant of rock stacking bags on the plane side face rubble bands formed as a result of its application phase. But in this case the structure to decrease compliance of not more than 1.33 times (Fig. 9).
References
- Морозов И.Т., Пономаренко П.И. Перспективы применения сплошной системы разработки в Донбассе // Уголь Украины. – 1997.– №12. – С. 8-10.
- Тупиков Б.Т., Андриенко В.М. Оценка технологии поддержания участковых выработок, проводимых вслед за очистным забоем // Уголь Украины. – 1997.– №12. – С.10-13.
- Дорохов Д.В. и др. Технология подземной разработки пластовых месторождений полезных ископаемых. – ДонГТУ. – Донецк – 1997.– 368с.
- Баймухаметов С.К., Есмагамбетов Х.Б., Спроге А.О. Совершенствование способа поддержания выемочных выработок за лавой при бесцеликовой технологии отработки пластов в Карагандинском бассейне // Уголь. – 1989. – №12. – С. 14-15.
- Терентьев Б.Д., Кушнаренко Г.Л., Хамин И.А. Опыт сохранения выемочных штреков для повторного их использования // Уголь. – 1991. – №9. – С. 3-6.
- Фомин Е.В., Шапошников В.И., Цыплаков Б.В. Исследования проявлений горного давления при сохранении выработки для повторного использования // Уголь. – 1993. – №11. – С. 19-22.
- Егоров А.П., Середенко М.И., Жаров А.И. Управление горным давлением в сохраняемых для повторного использования выработках // Уголь. – 1993. – №10. – С. 11-14.
- Кириенко М.И. Повторное использование выемочных штреков // Уголь Украины. – 1980. – №2. – С. 13.
- Горное дело: Терминологический словарь / Г.Д. Лидин, Л.Д. Воронина, Д.Р. Каплунов и др. – 4-е изд., перераб. и доп. – М.: Недра, 1990. – 694 с.
- Зборщик М.П. Охрана и расположение выработок в обрушенных породах // Разработка месторождений полезных ископаемых. - Вып. 45. - К.: Техніка. – 1976. - С. 3-11.
- Зборщик М.П. Выбор времени проведения выработок в обрушенных породах вблизи неподвижных границ очистных работ // Уголь Украины. - 1975. - №12.- С. 8-10.
- Черняк И.Л. Предотвращение пучения почвы горных выработок. - М.: Недра, 1978. – 237 с.
- Борзых А.Ф., Радченко В.И. Устойчивость проводимых за лавой присечных выработок // Уголь. - 1990. - №9.- С. 53-57.
- Бажин Н.П., Райский В.Б., Волков Ю.В. и др. Охрана подготовительных выработок без целиков. - М.: Недра, 1975, 103 с.
- Белаенко Ф.А., Глушко В.Т. Исследование пучения горных пород в капитальных и подготовительных выработках на шахтах Донбасса // Труды Украинского научно-исследовательского института организации и механизации шахтного строительства. - Вып. XI. – М.: Госгортехиздат. – 1960. – С. 117-138.
- Указания по рациональному расположению, охране и поддержанию горных выработок на угольных шахтах СССР. – Л.: ВНИМИ, 1986. – 222 с.
- Ануфриев В.Е., Ремезов А.В., Тризно С.К., Дубровский В.И. Проявления горного давления в окрестности охраняемой для повторного использования выработки в зависимости от свойств опор и технологии их применения // Уголь. – 1992. - №9. - С. 20-23.
- Лурий В.Г., Романов Ю.Г., Лукин К.Д. Новый способ охраны и поддержания выработок при бесцеликовой технологии // Уголь. - 1989. - №10.- С. 20-21.
- Баймухаметов С.К., Новиков В.Я., Попов К.П. Опыт применения технологии выемки с повторным использованием выработок на шахтах Карагандинского бассейна // Уголь. - 1991. - №11. - С. 22-25.
- Литвинский Г.Г. Охрана подготовительных выработок бутовыми полосами с разгрузкой краевой части пласта / Литвинский Г.Г., Бабиюк Г.В. // Уголь. – 1976. №9. – С. 39.
- Черняк И.Л. Деформирование кровли при охране подготовительных выработок породными полосами / Черняк И.Л., Носко В.Ф. // Уголь Украины. – 1988. – С.11-13.
- Адонкин А.С. Опыт поддержания подготовительных выработок / Адонкин А.С. // Уголь. – 1975. – №5. – с. 34-37.
- Табаченко Н.М. Опыт охраны выемочных штреков в зоне влияния очистных работ / Табаченко Н.М. // Добыча угля подземным способом. – 1977. – №9. – с. 15-17.
- Сагинов А.С. Поддержание выемочных выработок за очистными забоями / Сагинов А.С., Векслер Ю.А., Эслингер Я.И. // Сб. научн. трудов «Крепление, поддержание и охрана горных выработок». – Новосибирск. – 1983. – с. 89-91.
- Литвинский Г.Г. Охрана подготовительных выработок бутовыми полосами с разгрузкой краевой части пласта / Литвинский Г.Г., Бабиюк Г.В. // Уголь. – 1976. №9. – С. 39.
- Литвинский Г.Г., Волошин В.Б., Горбунов И.А. Управление устойчивостью подготовительной выработки взорванной бутовой полосой // Уголь Украины.– 1989.– №2.– С. 19-21.
- Максфилд К. Проектирование на ПЛИС. Курс молодого бойца / К. Максфилд. – М.: Издательский дом «Додэка-XXI», 2007. – 408 с.
- Кузяра В.И. Сусло А.И., Афендиков В.С. Охрана выработок на шахтах объединения Макеевуголь // Уголь Украины. – 1984. – №10. – С. 10-11.
- Медяник В.Ю. Формування склепіння рівноваги над підготовчою виробкою за допомогою смуг змінної жорсткості – як спосіб її охорони і підтримки // Геотехнічна механіка: Міжвід. зб. наук. праць / Ін-т геотехнічної механіки, ім. М.С. Полякова НАН України: VII конференція молодих учених «Геотехнологічні проблеми розробки родовищ, 19 листопада 2009» – Д., 2009. – Вип. 81. – С. 173-183.
- Хазипов И.В. Разработка способов создания искусственных породных сооружений для охраны повторно используемых выработок. Дисс… канд. техн. наук: 05.15.02. – Д.: ДонНТУ, 2009. – 160с.
- Ильин А.И. Охрана подготовительных выработок / Ильин А.И., Николенко И.А., Теросипов В.М. // Изв. Вузов донецкого горного института. – 1998. – №2(8). – с.40-41.
- Ильин А.И. Шахтные специальные крепи из породных стоек / Ильин А.И., Теросипов В.М., Баранов С.А. // Уголь Украины. – 2003. – №3. – с.14-15.
- 32. Пат. 1488532 СССР, SU 1701920 A1 E 21 C 41/20 41/18. Способ возведения бутовой полосы / Бондаренко Ю.В., Макеев А.Ю., Теличко В.И., Сапицкий К.Ф. – 622.271(088.8); Заявл. 12.02.90 // Авторское свидетельство. – 1991. – №48.
- Ефименко А.А. Околштрековая охранная полоса из автомобильных шин / Ефименко А.А. // Уголь Украины. – 1998. – с. 13-14.
- Кузнецов Г.И. Технологические схемы охраны и поддержания выемочных выработок / Кузнецов Г.И., Леман А.А. // Москва: ЦНИЭИуголь. – 1983. – С. 27.
- Негрей С.Г. О возможности увеличения несущей способности бутовых полос // Вісті Донецького гірничого інституту. Донецьк, 2011, №1, С. 179-184.