Abstract
This master's work is not completed yet. Final completion: January 2015. Full text of the work and materials on the topic can be obtained from the author or his adviser after that date.
Contents
- Introduction
- 1. The purpose of the idea and problem of the study
- 2. Advantages and disadvantages of methods and technologies for briquetting of metallurgical materials
- 3. Features choice of parameters briquetting technology
- 3.1 Criteria for selection of the technology and its parameters
- 3.2 Selecting a method for producing durable briquettes
- 3.3 Scale effect
- 3.4 Determination of the main parameters of briquetting technology
- 4. Process flow diagram of the process briquetting
- Conclusion
- References
Introduction
Every year stocks of crude ore with sufficient iron continuously depleted. In a short time, the technologies that are widely used in metallurgy will become unsuitable for processing low-grade raw materials. In this regard, priority is the task of developing manufacture technologies of metal products from recycled materials that accumulate in large quantities on each metallurgical works.
Despite the recent advances in the field of environmental protection, metallurgical production has a significant impact on the biosphere. Ferrous metallurgy is one of the materially and energetically expensive and polluting industries. Thus, the total consumption of raw material resources in a cycle from mining and coal before rolling up to 7 tons per 1 ton of finished rolled products [1].
Steel mills and factories, reducing their costs of production, utilization of these wastes by burying them in special landfills. Mainly because of the lack of technology of their processing or their lack of effectiveness.
Alternative methods for the preparation of metal, metallurgy fine materials and energy saving technologies in the near future will have more widespread. The presence of a large amount of fines in the raw materials, as well as sludge and dust leads to deterioration processes of agglomeration and complicates clumping.
Production of lumps and briquettes, which include components of fine iron metallurgy waste associated with some difficulties occasioned by a number of conflicting claims to the technological modes of agglomeration and significant volatility characteristics of the resulting materials.
1. The purpose of the idea and problem of the study
Objective — development of technological modes of production of the composite pellets and briquettes from waste metals that contain iron.
The idea of work — use of modern technologies and equipment for briquetting and pelletizing production of composite materials based on secondary products of iron and steel industry.
Research objectives:
- Theoretical analysis of the formation mechanism of the composite pellets and briquettes;
- Experimental investigations of possible technologies pellets and briquettes;
- Develop recommendations for industrial agglomeration process flowsheets.
2. Advantages and disadvantages of methods and technologies for briquetting of metallurgical materials
Abroad since the beginning of the twentieth century is widely used briquetting, which is considered a very effective way agglomeration waste. The most widespread briquetting received in Germany, USA and Japan [3].
In Russia and other CIS countries has recently sharply increased interest in briquetting as environmentally safe and economically advantageous method of agglomeration metallurgical waste [2,4].
In nonferrous metallurgy, briquetting is often used as the main method in cases where other methods do not give the desired result.
Briquetting has some significant advantages, which in the current situation of development of metallurgy suggest it a promising method of agglomeration. Among them are the following [3]:
- Briquetting imposes less stringent requirements for quality of raw materials, enables the production of briquettes materials broad classes of size less than 10 mm, almost all proportions and compositions;
- The briquetting process is technologically simple; some difficulty is - dosing and mixing binder to the base material;
- During briquetting properties of the components do not change;
- Briquetting is an environmentally friendly way of agglomeration;
- Briquetting enables greater use of raw materials, fuel and energy base, to introduce alternative sources of iron.
These benefits can effectively solve such pressing problems:
- getting new, complex raw materials, including iron oxides and other reductant;
- The introduction of effective ways of processing of raw materials, such as metallization;
- Reducing the harmful effects of metallurgical processes on the environment.
The main disadvantages of briquetting process [3]:
- Insufficient strength of the briquettes, especially at high temperatures and in a reducing atmosphere;
- Using binders containing harmful impurities and having insufficient astringent properties;
- The high cost of high-quality binders;
- Difficulties associated with the introduction of uniformly binder in the charge;
- Insufficient capacity forging equipment.
To date, most of these problems partially solved. Abroad formed several directions receiving durable briquettes, which include a hot
briquetting, briquettes high temperature treatment, the use of heat-resistant resins.
3. Features choice of parameters briquetting technology
3.1 Criteria for selection of the technology and its parameters
In developing the technology briquetting of metallurgical raw materials use the following selection criteria of factors, operations and parameters:
- Indicators of economic efficiency (general and comparative);
- The conditions of necessity and sufficiency of the required operation of technological process and its the parameter values [3].
Applying these general criteria can in principle provide a representative selection of the technology and its parameters. If necessary, one may be selected and other criteria, such as:
- Compliance with processing methods and equipment quality raw materials processed;
- The technical complexity of the process;
- Cost criteria, etc. [3].
The main process parameters referred quality of the briquetting of burden preparation (crushing components of the charge the homogeneity, moisture level etc.) mode pressing (pressing pressure, capacity, etc.), as well as thermal and chemical indicators briquette hardening (drying temperature, duration hardening process, etc.), the quality of the briquettes (strength, chemical composition, moisture resistance, etc.) [3].
Need to be assigned the raw material processing methods and type of equipment the quality of the processed material derived from the process capability and processing equipment.
Criteria of technical complexity allows you to choose the least intensive process with reasonable parameters.
Cost criteria of at similar technical characteristics of the allow you to choose cheaper, therefore, the most advantageous option. These include the the cost of capital, operating costs and reduced the amount of ecological losses, etc.
Most justified this problem is solved by VEA associated with certain conditions, one of which included the need for the valuation of the impact of each factor on the cost of briquetting process.
If there are multiple factors or alternative of operations, expenses for their realization is compared with the saving of improving the strength of briquettes, simplification or cheapening technology. And choose the option with maximum efficiency [3].
In practice, such computations are complicated by the presence of a significant number of factors and operations that implement these factors. So will restrict the choice of the minimum required amount, which will provide the required mechanical strength of the briquettes without using extreme values of the parameters that significantly complicate and increase the cost of briquetting process.
3.2 Selecting a method for producing durable briquettes
A method for producing durable briquettes should be chosen almost the same criteria as in the choice of technology and its parameters, but before the development of the technology chosen method by comparing it with known alternatives, and then on its basis are developing technology and determine its parameters corresponding to this method and allowing to to reach a predetermined level of product quality. [3].
To date, developed several ways to get strong briquettes. The most famous Options include briquetting using binders, as well as "hot" briquetting. These options allow you to give briquettes high strength, however a number of disadvantages (high cost, the introduction of harmful impurities and ballast with binders, depreciated equipment, etc.) that do not allow to achieve high efficiency briquetting process.
The component composition of the briquettes is not determined only by the requirements of mechanical strength and chemical composition, including content of alumina of components, but also the condition of maximal volumes of sludge disposal of.
Depending on the availability of various investment opportunities in the enterprise, there are two ways to obtain briquettes.
The first method requires a significant operational cost. Includes the preparation of material, briquetting, the drying rate and shipping. Warehouse of finished products can be absent as dry briquettes are ready for use. This method is used in excess cheap heat transfer fluids, such as of blast furnace gas or coke oven gas.
The first method requires a significant operational cost. Includes the preparation of material, briquetting, the drying rate and shipping. Warehouse of finished products can be absent as dry briquettes are ready for use. This method is used in excess cheap heat transfer fluids, such as of blast furnace gas or coke oven gas.
The second method requires lower operating costs, but more capital because of the need to build capacity of warehouses, where there is a natural drying, hardening and protection from rain briquettes. When the drying time of 14 to 28 days, the capacity of the warehouse for the annual production of 300 tons of briquettes per year should be 15–35 tons.
In general, the second mentioned method has smaller cost, but must be chosen as the basic first embodiment to ensure the independence of the weather conditions.
3.3 Scale effect
When embedded in a production laboratory results will inevitably have to deal with the phenomenon of inconsistency obtained industrial designs and parameters of their production experimental samples and parameters. This phenomenon is called scale effect.
Scale effect — this physical modeling error arising due to violation of similarity (geometric, chemical, thermal, etc.) processes in laboratory and industrial applications [3].
For of briquettes are the parameters — the size, shape, density, strength, pressure pressing, strength parameters, etc. The results obtained in laboratory conditions (compaction pressure, humidity, drying time) in an industrial environment can not to provide the required strength of the briquettes.
The difference in properties of briquettes obtained in laboratory and pilot-scale conditions allows us to estimate scale effect and to develop the necessary changes to the adopted briquetting technology and the need to revise the parameters briquetting.
3.4 Determination of the main parameters of briquetting technology
In determining the briquetting technology should take such basic technological parameters that provide strength of briquettes:
- type of press — valtsevyj providing compaction pressure: Operating — 50 MPa, maximum — 90 MPa; pressing nature — both sides on valtsevyj press to preset parameters; regulation of the strength of briquettes may be increasing pressure up to 90 MPa;
- faction of briquettes — 50–60 mm for the sample cells shape briquettes — Pillow or selliform, providing maximum performance;
- order of mixing the components as follows: at the beginning of mixed lime-alumina components, then fed the rest;
- cells treated with oil-graphite suspension;
- returning to the use of 2% is equal to the number of dropouts and cracked briquettes, produced in an industrial briquetting recompression the same amount of briquettes [5];
- moisture content should be maintained at an optimum level determined experimentally;
- provides two modes of drying: intense — at a drying temperature of 250–500 °C, a natural — at 20–25 °C; drying option determined desired final moisture briquettes (0.5% and 1.2%).
Since the net effect of selected factors to mechanical strength of the briquettes is generally not equal to the sum of the effects of each of them, conducted briquetting display for the selected technological factors.
Experience briquetting fine material shows that a mandatory condition for obtaining the required quality of the briquettes is strict observance of technological regulations, including:
- unconditional fulfillment of the established regime of of preparation material;
- the ratio of the material and a binder, and humidity;
- conditions of mixing material with a binder;
- respective performance of valtsevyj the press and of the dispenser;
- of optimal compacting pressure;
- ripening and warehousing of briquettes [6].
4. Process flow diagram of the process briquetting
Criteria for the need this or that operation and their classification to one or another production stage is requirement to achieve of certain indicators, characteristics and parameters of of the processed material. So, when preparing materials for baling, the main parameters are — moisture, fractional composition, a homogeneous mixture, etc. When compacting such characteristics are the density and strength of raw briquettes, the amount of returnable material, the withdrawability of briquettes from the mold, etc. During strengthening of briquettes - the strength of briquettes, their the residual moisture, the presence of volatile substances, etc.
Besides the main, directly manufacturing operations, briquetting includes preparatory and final operations, in particular, such as the acceptance of raw materials and shipment of finished products.
The briquetting process of metallurgical raw materials comprises several elements, components, operations, similar to other methods — by agglomeration and pelletizing. These components, primarily relates the preparation of raw materials and elements shipment finished products which can be used in the briquetting. Have similarities and some agglomeration processes, which are based on the same processes of adhesion and bonding of particles in a solid monolith. [3].
This similarity is largely determined by similar types and characteristics of feedstock, component composition of the material, of formation patterns of pieces of, the presence of heat treatment, the requirements for finished products, its shipment etc. These operations largely determine conditions of preparation of of raw materials and can be used for the production of briquettes practically unchanged [3].
Using the maximum possible number of known processes allows the use of standard equipment and typical operations, which greatly simplifies the briquetting technology, as well as cheapens of capital costs and ongoing costs for the construction the installation and its operation.
Thus, the briquetting process generally consists of three phases (phases associated technology, operations groups):
- Preparation of raw materials for briquetting;
- Pressing (molding) briquettes (figure 4.1) ;
- Hardening (drying) of briquettes.
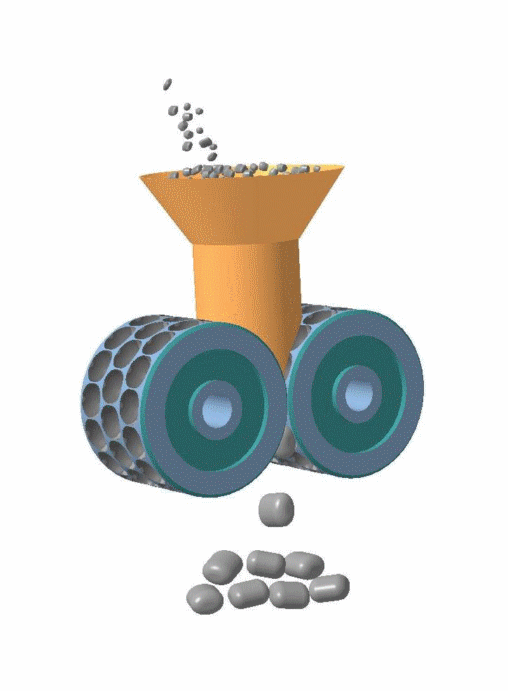
Figure 4.1 — Animation example of briquetting press
(9 image's,5 frames/sec, size - 290kb)
Preparation of raw materials for briquetting involves the following steps:
- Receipt and storage of raw materials;
- Preparation of raw materials for processing;
- Dosing, mixing and homogenization of raw materials;
- Preparation and putting into raw material binders.
If you receive briquettes any other way than pressing, use a generic term — molding.
Hardening briquettes involves the following steps:
- Maturing;
- Drying and aging briquettes;
- Strengthening processing active media and materials.
Hardening of briquettes can be done in different ways, of which the drying due to its high efficiency occupies a privileged position.
Shipment briquettes not formally refers to the process of briquetting, but its correct organization helps to reduce losses briquettes from destruction during loading and unloading and transportation, so this stage is subject to regulation.
Briquetting process flowsheet is shown in Figure 4.2 Dispensing components.
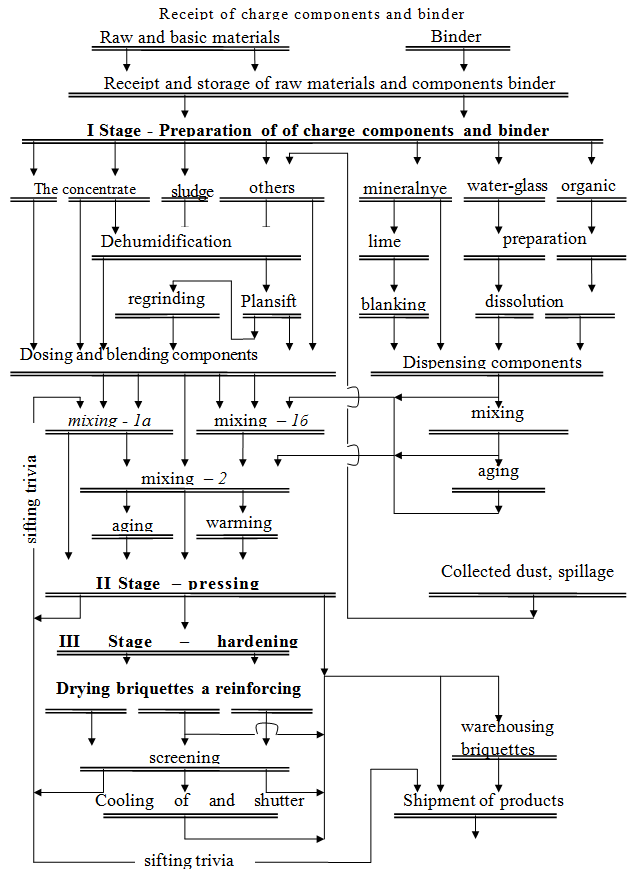
Figure 4.2 — The technological scheme of raw of briquetting
A simplified circuit diagram of the installation of briquetting machines corresponding to the shown in Fig. 4.2 technological scheme of briquetting of metallurgical raw materials is shown in Fig.4.3
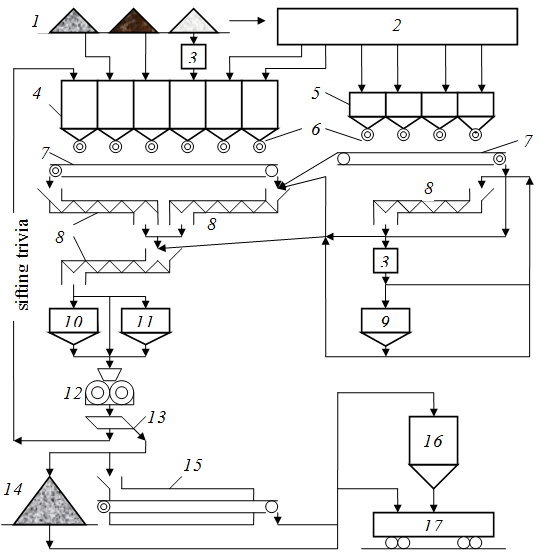
1 - outdoor storage of raw; 2 - closed storage of raw materials and binder; 3 - crushers; 4 - silos for of charge components; 5 - silos for communication components; 6 - dispensers; 7 - conveyor assembly; 8 - taps; 9 - a device for slaking; 10 - hopper shutter charge; 11 - heater apparatus; 12 - briquette press; 13 - roar; 14 - Playground for cooling and exposure briquettes; 15 - tape sushilo; 16 - bunker finished products; 17 - railway carriage.
Figure 4.3 — Diagram of chains machines and apparatuses of technological line
Briquetting
For of briquetting installation design requires selection of the equipment performing appropriate technological operations or group of operations that are set in accordance with the technological scheme in a single cycle.
Thus, the mixing operation is performed different types of mixers, dosing - dosing, pressing - briquetting press, drying - drying ovens etc.
The choice of a particular type of equipment should be made on the following criteria:
- Bandwidth (capacity) of equipment subject power reserve, allowing its operation in power saving mode;
- Ensure the specified quality characteristics and processing of raw;
- Minimize capital and operating costs;
- Minimum size, "fit" into the building;
- Ensure environmental standards, occupational safety regulations, etc.
The final choice of a particular type of equipment produced by comparing the technical characteristics with the relevant requirements of the operation. If the efficiency of the selected standard equipment is in doubt, it is necessary to conduct pilot testing and making necessary changes to the design in the manufacturing process from the manufacturer.
Conclusion
Increased interest in briquetting now explained crisis development of ecological conditions in which significant negative contribution is agglomeration, gradual elaboration of quality sinter ore deposits, an increase in the proportion of fine concentrates, negatively affecting the intensity of agglomeration. Decrease in inventories of coking coal makes to focus increasingly on the methods of synthesis of iron outside the blast furnace, which briquetting, along with balling may be the primary method of agglomeration [3].
Literature and an experimental analysis of domestic and foreign experience shows high efficiency in its use briquetting not only as the core, but also, especially, as an auxiliary method of agglomeration of crushed steel raw materials. Significantly increases the performance of metallurgical equipment, saving raw materials, reduced energy consumption, increases the yield and improves the quality of the metal. Reduced adverse effects on the environment, on the rise and other technical and economic indicators.
Study of domestic and foreign experience in obtaining and using briquettes shows that the steel industry in Ukraine, despite the growing demand for new materials, briquetting is not widely used, which rightly deserves. [7].
The manufacturers and some scientists explain the situation metallurgists various objective reasons, including unsatisfactory strength briquettes, insufficient research and production experience for their preparation, lack of required equipment, its low efficiency, lack of necessary data, etc. However, successful use of foreign experience and briquetting results refute these allegations.
Therefore, the development and introduction of advanced, energy-saving, efficient technologies briquetting iron metallurgical waste is a promising and relevant scientific and practical task.
References
- Банный Н.П. Экономика чёрной металлургии СССР / Н.П. Банный, А.А. Федотов, П.А. Ширяев и др. – М.: Металлургия, 1978. – 344 с.
- Динельт В.М. Малооперационная технология получения брикетов из тонкодисперсных углеродистых материалов и отходов / В.М. Динельт, В.М. Левинец, М.С. Никишанин и др. // Изв. вузов: Чёрная металлургия. – 2007. – № 6. – С. 61-63.
- Ожогин В.В. Основы теории и технологии брикетирования измельчённого металлургического сырья: Монография. – Мариуполь, ПГТУ, 2010. – 442 с.
- Фоменко А.И. Утилизация шламов металлургических производств / А.И. Фоменко // Изв. вузов: Чёрная металлургия. – 2001. – № 11. – С. 70-71.
- Ожогин В.В. Совершенствование ресурсосберегающей технологии получения и использования высокопрочных шламовых брикетов в аглодоменном производстве: дис. … канд. техн. наук: 05.16.02. – Мариуполь, ПГТУ, 2004. – 207 с..
- Бабанин В.И. Брикетирование мелкозернистых материалов в ферросплавном производстве: опыт и возможности / В.И. Бабанин, А.Я. Ерёмин // Металлург. – 2006. – 5. – С. 45-50.
- Ожогин В.В. Брикетирование как полноправный метод окускования металлургического сырья / В.В. Ожогин, А.А. Томаш, И.А. Ковалевский и др. // Металлургические процессы и оборудование. – 2005. – Вып. 2. – С. 54-58.