Реферат за темою випускної роботи
При написанні даного реферату магістерська робота ще не завершена. Остаточне завершення: січень 2015 року. Повний текст роботи та матеріали по темі можуть бути отримані у автора або його керівника після зазначеної дати.
Зміст
- Вступ
- 1. Мета, ідея і завдання дослідження
- 2. Переваги та недоліки способів і технологій брикетування металургійних матеріалів
- 3. Коротка характеристика використовуваної сировини
- 4. Традиційні зв’язуючі, використовувані при брикетуванні
- 5. Якість вихідної сировини і брикетованих матеріалів
- 6. Особливості вибору параметрів технології брикетування
- 6.1 Критерії вибору технології та її параметрів
- 6.2 Вибір способу отримання міцних брикетів
- 6.3 Масштабний ефект
- 6.4 Визначення основних параметрів технології брикетування
- 7. Принципова технологічна схема процесу брикетування
- Висновки
- Список використаної літератури
Вступ
З кожним роком запаси рудної сировини з достатньою кількістю заліза безперервно виснажуються. Незабаром, технології які широко використовуються в металургії в даний час, стануть непридатними для переробки низькосортної сировини. У зв'язку з цим актуальною стає задача розробки технологій виготовлення металопродукції з вторинної сировини, яка у величезних кількостях накопичується на кожному металургійному підприємстві.
Не дивлячись на сучасні досягнення в сфері захисту навколишнього середовища, металургійне виробництво робить значний вплив на біосферу. Чорна металургія є однією з матеріалоємних та енергоємних, а також екологічно шкідливих галузей промисловості. Так, загальна витрата матеріально-сировинних ресурсів по циклу від видобутку руди і вугілля до прокатки складає до 7 т на 1 т готового прокату [1].
Металургійні заводи і комбінати для того щоб зменшити власні витрати на виробництво, утилізують ці відходи шляхом захоронення їх на спеціальних полігонах. В основному через відсутність технології їх переробки або їх недостатньої ефективності.
Альтернативні методи отримання металу, металургія тонкоподрібнених матеріалів та ресурсозберігаючі технології в недалекому майбутньому отримають все більш широке розповсюдження. При цьому наявність великої кількості тонкофракційних матеріалів та концентратів глибокого збагачення, а також шламів і пилу призводить до погіршення процесів агломерації, ускладнює окатування.
Виробництво окатишів і брикетів, які включають тонкодисперсні компоненти залізовмісних відходів металургії, пов'язано з деякими труднощами, зумовленими низкою суперечливих вимог до технологічних режимів огрудкування і значною нестабільністю характеристик одержуваної сировини.
Тому розробка і впровадження передових, енергозберігаючих, ефективних технологій огрудкування залізовмісних відходів металургійного виробництва є перспективною й актуальною науково-практичною задачею.
1. Мета, ідея і завдання дослідження
Мета роботи — розробка технологічних режимів виробництва композиційних окатишів і брикетів, які включають залізовмісні відходи металургійного виробництва.
Ідея роботи — Використання сучасних технологій і техніки огрудкування та брикетування для виробництва композиційних матеріалів на основі вторинних залізовмісних продуктів металургії.
Завдання дослідження:
- Теоретичний аналіз механізму формування композиційних окатишів і брикетів;
- Експериментальні дослідження можливих технологій виробництва окатишів і брикетів;
- Розробка рекомендацій для промислових технологічних схем огрудкування.
2. Переваги та недоліки способів і технологій брикетування металургійних матеріалів
За кордоном з початку ХХ століття широко використовують брикетування, яке вважають досить ефективним способом огрудкування відходів. Найбільшого поширення брикетування отримало в Німеччині, США та Японії [3].
У Росії та інших країнах СНД останнім часом різко зріс інтерес до брикетування як екологічно чистого та економічно вигідного методу огрудкування металургійних відходів [4,5].
У кольоровій металургії брикетування нерідко застосовують в якості основного методу огрудкування сировини в тих випадках, коли інші методи огрудкування не дають бажаного результату: сировина погано огрудковується і спікається, а при спіканні видаляються потрібні компоненти (вуглець, сірка тощо).
Брикетування має ряд істотних переваг, які в умовах розвитку металургії дозволяють вважати його перспективним методом огрудкування. До їх числа відносяться наступні [3]:
- Брикетування пред'являє менш жорсткі вимоги до якості сировини, дозволяє огрудковувати матеріали широких класів крупністю менше 10 мм, практично в будь-яких пропорціях і складах;
- Процес брикетування технологічно простий; деяку складність представляє лише дозування зв’язуючих і їх змішування з матеріалом що брикетується;
- При брикетуванні зберігаються властивості компонентів, що входять у брикети;
- Брикетування є екологічно чистим способом огрудкування;
- Брикетування розширює сировинну і паливно-енергетичну базу металургії, дозволяє ширше впроваджувати позадоменні способи отримання заліза.
Ці переваги дозволяють ефективно вирішувати такі актуальні завдання, як отримання нових, комплексних видів сировини, що включають оксиди заліза, відновник і флюс, впровадження ефективних способів обробки сировини, наприклад, металізацією, зниження шкідливого впливу металургійних процесів на навколишнє середовище.
До основних недоліків брикетування зазвичай відносять наступні [3]:
- Недостатня міцність брикетів, особливо при високих температурах і в умовах відновлювальної атмосфери;
- Використання зв'язуючих, що містять шкідливі домішки і мають недостатні в'яжучі властивості;
- Висока вартість якісних зв'язуючих;
- Труднощі, пов'язані з рівномірним введенням зв'язуючих у шихту;
- Недостатня продуктивність пресового устаткування.
До теперішнього часу більшість цих проблем частково вирішені. За кордоном сформовані декілька напрямків отримання міцних брикетів, до числа яких відносять гаряче
брикетування, високотемпературну обробку брикетів, використання термостійких зв'язуючих.
3. Коротка характеристика використовуваної сировини
У металургійному виробництві використовують велику кількість матеріальних ресурсів, що мають загальну, термінологічно встановлену назву: сировина, сировина і матеріали або сировинні (сирі) матеріали. Технологічне паливо через його важливість, особливий вплив на металургійні процеси, а також високу вартість виділено в окрему групу [3].
За призначенням і характером споживання сирі металургійні матеріали поділяються на основні і допоміжні. Основні матеріали складають головний зміст продукту, наприклад, рyди, концентрати. Допоміжні матеріали використовують у процесі виробництва як додаткові та інші матеріали, що покращують технологічний процес і якість продукції, зокрема, флюси, легуючі добавки та ін. [3].
За джерелами утворення всі матеріали підрозділяють на первинні, свіжі матеріали та оборотні, вторинні матеріали або відходи. До оборотних матеріалів відносять використовувані відходи, просипи, повернення, побічні і попутні продукти. Під відходами металургійного виробництва в широкому сенсі слова слід розуміти сировину, матеріали та енергоресурси, в силу тих чи інших причин не використані для отримання основної продукції. Відходи є неминучим елементом існуючої технології виробництва металів.
У разі огрудкування відходів брикетуванням первинну сировину, матеріали та відходи класифікують [6, 7]:
- за місцем виробництва, виникнення або джерел утворення;
- за характером утворення та видалення;
- за способом видобутку, вилучення або уловлювання;
- за хімічним (речовинним) складом;
- за фізичними властивостями;
- за іншими (в т.ч. технологічними) критеріями.
За місцем виробництва первинну сировину і матеріали поділяють на ті, що поставляються з боку і власні [7].
В якості класифікації відходів за місцем виникнення може служити номенклатура шламів, представлена в [6,7].
За характером утворення та видалення всі відходи поділяють на: ті, що уносяться та відходять з газами (пилу); просипи, осипи, змиви (шлами); сливи, натікання, залишки (шлаки, зварювальний шлак, скардовіни).
За хімічним (речовинним) складом відходи групують за двома рівнями - виду (наявності) та змістом основного компонента. За видом основного компонента відходи класифікують на залізовмісні, марганцевмісні та ін., а також відходи, що детермінуються по шкідливому компоненту [7].
За змістом основного компонента відходи класифікують на багаті, відносно-багаті і бідні. Рівень багатства визначають співставленням з аналогічною первинною сировиною.
За речовинним (компонентним) складом шлами представляють собою суміші залишків сировини і матеріалів, що частково зазнали обробки, уноси, возгони і вторинні оксиди.
До фізичних властивостей, що визначають придатність шламів до огрудкування гранулюванням, відносять щільність, дисперсність, адгезійну здатність та інші властивості [8].
Щільність є важливою властивістю матеріалів, від якої залежить ефективність того чи іншого способу огрудкування. Так, при агломерації бажано, щоб об'ємна щільність шихти приймала максимальне значення при певному оптимальному значенні насипної щільності, що забезпечує потрібну газопроникність. При брикетуванні, навпаки, слід прагнути до збільшення насипної щільності, що зменшує усадку матеріалу і дозволяє отримувати більш міцні брикети.
До основних властивостей, що характеризують брикетуемість матеріалів, відноситься дисперсність (подрібненість). Для полідисперсних матеріалів характеристикою дисперсності є фракційний склад. За фракційним складом брикетуемі матеріали поділяють на:
- кускові — 80–90% розміром більше 10 мм;
- крупнозернисті і зернисті — 40–60% розміром 1–10 мм;
- дрібні — 60–80% розміром 3,0–0,074 мм;
- пилоподібні — 60–80% розміром 0,5–0,01 мм;
- тонкі — понад 50% розміром менше 0,05 мм [6].
Багато видів металургійної сировини і відходів мають дрібний і пилоподібний склад, а також різноманітні фізичні властивості [10,11].
За фізичними властивостями та хімічним складом ці матеріали мають цілу низку особливостей. Це - неоднорідність хімічного складу, низька змочуваність і погане вологовидалення [12].
За злипанням всі матеріали і пил можна умовно поділити на три групи [9]:
- Перша група — ті, що не злипаються і слабо злипаються; як правило, це сухі матеріали, фракція +0,063 мм яких складає більше 80%;
- Друга група — ті, що середньо злипаються, 80% яких мають розмір 0,063–0,01 мм;
- Третя група — ті, що сильно злипаються; це пил з частками -0,01 мм.
За вологості подрібнену сировину і шлами поділяють на пилоподібні (до 3% вологи), сухі (3–6%), нормальні (6–12%), вологі (12–18%) і перезволожені (більше 18%). Вологоємність даних матеріалів в значній мірі залежить від питомої поверхні частинок, тобто чим сильніше подрібнений матеріал, тим більше вологи він утримує.
Важливою металургійною характеристикою сировини є його здатність утворювати легкоплавкі і рідкорухомі з'єднання, що добре зволожують і скріплюють частки шихти при спіканні, що підвищує міцність агломерату [13].
4. Традиційні зв'язуючі, використовувані при брикетуванні
При брикетуванні багатьох видів подрібненої сировини, що володіє недостатніми аутогезійними властивостями, навіть при високих тисках (180 МПа і більше) звичайним холодним пресуванням отримувати міцні брикети без їх спікання не представляється можливим. У таких випадках використовують зв'язуючі - допоміжні матеріали, що покращують злипання частинок і підвищують міцність брикетів до заданого рівня 3].
Оскільки добавки таких матеріалів можуть становити від кількох до 10% і більше, вони повинні відповідати наступним вимогам [2,14]:
- Володіти високими аутогезійними властивостями, тобто забезпечувати високу холодну і гарячу міцність при мінімальній витраті зв'язуючего;
- Забезпечувати швидку схоплюваність;
- Вносити мінімальну кількість шкідливих, баластних та інших домішок, які небезпечні для обслуговуючого персоналу і знижують якість кінцевого продукту;
- Не погіршувати умов плавки брикетів;
- Бути розповсюдженими і мати невисоку вартість;
- Не вимагати складних прийомів і операцій з їх використання;
- Забезпечувати мінімальну вологостійкість.
Зв'язуюче є визначальною умовою міцності і значною мірою — відновлюваності брикетів. Збільшення витрат зв'язуючого, підвищуючи міцність, призводить не тільки до зниження корисних компонентів в брикетах, а й до значного їх подорожчання.
Зв'язуючі підрозділяють на три типи: мінеральні (неорганічні), органічні і комбіновані [3].
До поширених неорганічних зв'язуючих слід віднести гашене вапно, рідке скло, глиноземистий і портландский цементи. Однак багато з них мають істотні недоліки. Так, гашене вапно і портландцемент при нагріванні віддають гідратну вологу і втрачають міцність, рідке скло містить значну кількість лугів і двоокис кремнію, а глиноземистий цемент до того ж надзвичайно дорогий. При цьому кращі в'яжучі характеристики виявляє рідке скло і глиноземистий цемент [3].
До поширених органічних зв'язуючих відносять кам'яновугільні і нафтові смоли, меляса, відходи гідролізної і целюлозної промисловості, тощо. Загальним недоліком органічних зв'язуючих є їх піроліз чи вигоряння при високих температурах з втратою міцності, а також внос до брикетів значної кількості сірки [3].
Більшість органічних зв'язуючих можуть використовуватися для отримання брикетів з високими показниками холодної міцності. При нагріванні таких брикетів зв'язка руйнується або згорає, в результаті чого вони втрачають більшу частину міцності, розсипаються під тиском верхніх шарів матеріалу і виносяться потоком газів з агрегату. Більш стійкі зв'язуючі при згорянні утворюють спечений шлак, який скріплює частинки брикетів, перешкоджаючи їх руйнування [3].
Зв'язуючі неорганічного походження, поміщаючись між частинками оксидів заліза і відновника, погіршують відновлюваність. Органічні зв'язуючі, частково замінюючи відновник, зазвичай вносять небажані домішки, в т.ч. сірку. Поряд з цим деякі види зв'язуючих при нагріванні можуть сприяти утворенню легкорухомих фаз, наприклад, фаяліта, що бажано для усадки брикетів які відновлюються [3].
До комбінованих зв'язуючих відносять суміші різних зв'язуючих. Ці суміші дозволяють поліпшити позитивні і знизити негативні властивості. Наприклад, суміш, що містить рідке скло і лігносульфонат, вносить знижену кількість лугів, кремнезему або сірки, ніж кожне зв'язуюче окремо, при одночасному забезпеченні високої механічної міцності брикетів [3].
5. Якість вихідної сировини і брикетованих матеріалів
Якість матеріалу — це сукупність його властивостей, які відповідають певним потребам у відповідності з його призначенням [15]. Якість брикетів, як і будь-якої металургійної сировини і матеріалів, має відповідати умовам споживаючого процесу.
Сучасний технічний рівень металургійного виробництва дозволяє використовувати матеріали різноманітної якості з досить широким розкидом за змістом корисних компонентів і шкідливих домішок. Однак для економічно ефективної переробки потрібна сировина певної якості. Брикети ж, що виготовляються з відходів, мають знижений вміст корисних компонентів і підвищений — шкідливих [3].
Для посилення зацікавленості у використанні брикетів, в т.ч. і з відходів, вимоги, що пред'являються до них, повинні бути дещо знижені. Економічно це зниження забезпечується зменшенням впливу на навколишнє середовище шляхом використання більш дешевого та екологічно безпечного методу огрудкування, ніж агломерація або окатування, зниження платежів, що вносяться підприємствами за розміщення відходів у навколишньому середовищі, а також більш низькою вартістю відходів у порівнянні з первинною сировиною [3].
На даний час для оцінки якості металургійної сировини — мономатеріалов (руди, концентрату, флюсів, тощо) і матеріалів, що з них виготовляються (агломерату, окатишів), сформована система одиничних показників, представлених у відповідних ГОСТах, ДСТУ, СТП, технічних умовах та інших нормативно-технічних документах, що дозволяють оцінювати відповідність того чи іншого матеріалу тому чи іншому металургійному процесу. Вони регламентують хімічний склад, фізичні та металургійні властивості, а також механічну міцність, див. рис. 5.1.
Так, відповідно до [7,16] шлами, використовувані при огрудкуванні, повинні відповідати наступним вимогам:
– вологість шламу не більше 8-12%;
– крупність грудок шламу після сушіння не більше 6 мм;
– мінімальний наведений вміст заліза не менше 45%;
– вміст шкідливих домішок визначається можливостями споживаючих технологій;
– вміст цинку не більше 1%;
– загальний вміст корисних компонентів не менше 45%.
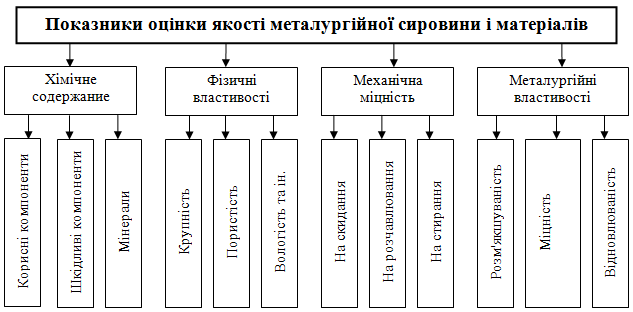
Рисунок 5.1 — Система оцінки якості металургійної сировини і матеріалів
Вміст шкідливих домішок з урахуванням тих, що надходять в піч з усією шихтою, в брикетах не повинно перевищувати деяких граничних кількостей: для цинку — 0,3 кг/т чавуну, лугів — 4–7 кг/т [17] и т.п.
Більшість з цих показників є бракувальними, тобто, якщо значення будь-якого показника не відповідає вимогам нормативного документа, то матеріал не підлягає використанню у даному процесі.
Для агломерату та окатишів, виготовлених з добавками шламів, зберігаються практично ті ж вимоги, що і для звичайних матеріалів [18].
Однак для брикетів з первинної сировини і відходів, що є полікомпонентною сировиною, слід використовувати інші методи оцінки, такі, як оцінка за наведеним вмістом заліза, по металургійній цінності або за методом академіка М.А. Павлова, який висунув ідею укрупненої вартісної оцінки якості [7,19].
Для більш точної оцінки слід використовувати складні системи [20-25].
Міцність — це властивість матеріалів в певних умовах і межах, не руйнуючись, сприймати ті чи інші дії (навантаження, нерівномірний температурний нагрів, висихання, набухання, нерівномірне протікання фізико-хімічних процесів в різних частинах тіла та ін.) [15].
У металургії міцність є важливою характеристикою огрудкованного матеріалу. По суті, вона є бракувальним критерієм, за яким оцінюють матеріал на придатність до металургійної обробки. Недостатня механічна міцність призводить до передчасного подрібнення матеріалу і зміни умов, при яких процес металургійної обробки є оптимальним, зокрема, погіршується газопроникність, збільшуються втрати матеріалу з виносами і т.п.
Міцність металургійних матеріалів значною мірою залежить від ступеня нагріву і хімічних впливів, що мають місце в металургійному агрегаті і змінюють їх характеристики міцності. При цьому багато матеріалів в природному стані мають високу міцність, а при нагріванні і відновленні швидко її втрачають і руйнуються.
За даними [2,14,27,28] бракувальні межі механічної міцності брикетів складають наступні значення, див. табл. 5.1.
Найбільш ефективним виявляється брикетування подрібнених матеріалів. При цьому вельми складною, важко вирішуваною проблемою продовжує залишатися недостатня механічна міцність брикетів.
Брикет | Розмір брикету, мм | Пористість, % | Міцність | |||
---|---|---|---|---|---|---|
За ГОСТ 15137-77 | На стискання, МПа | За ГОСТ 19575-84 | ||||
На скидання | На стирання | |||||
Доменний | 40 | >10 | >70 | 5 | >18 | >40 |
Конвертерний | 30 | <10 | <70 | <10 | 10 | – |
Електропічний | 100 | – | <70 | 10 | >7,5 | – |
Сформованим напрямком підвищення міцності, який став традиційним, є розробка і використання високоміцних зв'язуючих. В принципі воно може забезпечити потрібну міцність, але на практиці поки ще не дає задовільного вирішення поставленого завдання в основному через високу вартість зв'язуючого або погіршення металургійних властивостей брикетів.
Тимчасовою альтернативою цьому напрямку є більш широке використання брикетів в тих виробництвах, де вимоги до міцності менш високі, наприклад, в сталеплавильному виробництві. У довготривалій перспективі отримання високоміцних брикетів може здійснитися лише комплексним поєднанням як відомих методів зміцнення, так і тих, що знаходяться наразі у стадії вивчення і становлення.
Важливим фактором, що визначає роботу доменних печей, є процес шлакоутворення, якому передує розм'якшення і плавлення шихтових матеріалів. Оптимальної роботи доменної печі можна досягти лише при використанні матеріалів з відносно високою температурою початку розм'якшення і досить вузьким інтервалом температур розм'якшення.
До показників, що характеризують металургійні властивості сировини, відносять температуру початку і температурний інтервал розм'якшення, відновлюваність і міцність залізорудних матеріалів при відновленні. Для сталеплавильних матеріалів, які зазнають інтенсивних температурних впливів при завантаженні в сталеплавильний агрегат, випробування на термоудар є обов'язковим.
Металургійні властивості брикетів також визначають по гарячій міцності (міцності при відновленні), яка визначається в барабані Ліндера (для доменних брикетів) і здатності витримувати термоудар (для сталеплавильних брикетів). За відсутності барабана Ліндера металургійні властивості брикетів оцінюють за показниками розм'якшування і відновлюваності. Сукупність цих показників дає можливість з достатнім ступенем точності визначити металургійні властивості брикетів [26].
Зокрема, брикети, що задовольняють вимогам доменної плавки, повинні бути стійкі при температурі 900-1000 °С, а також в атмосфері перегрітого до 150 °С пару, бути пористими, газопроникними і разом з тим водостійкими. Розм'якшення матеріалів, призначених для доменної плавки, має здійснюватися в інтервалі температур від 1050 до 1200 °С.
Брикети для сталеплавильного виробництва повинні витримувати нагрівання до 1500 °С протягом трьох хвилин і при цьому не розвалюватися на шматки, а також мати пористість не більше 5–10% [2].
6.Особливості вибору параметрів технології брикетування
6.1 Критерії вибору технології та її параметрів
При розробці технології брикетування металургійної сировини використовують наступні критерії вибору факторів, операцій і параметрів:
- показники економічної ефективності (загальної та порівняльної);
- умови необхідності і достатності тієї чи іншої операції технологічного процесу і величини її параметра [3].
Застосування цих загальних критеріїв у принципі може забезпечити репрезентативний вибір технології та її параметрів. При необхідності з них можуть бути виокремленні й інші критерії, такі як:
- відповідність способів обробки сировини та обладнання якості оброблюваної сировини;
- технічна складність процесу;
- вартісні критерії та ін. [3].
Критерієм (від греч. kriterion) — називають ознаку або мірило, на підставі якого проводиться оцінка або вибір чогось [30].
Технологічним параметром ((від греч. parametron — відмірюють, співмірний) процесу називають величину, що характеризує цей процес або відрізняє його від будь-якого іншого процесу [15,30].
До основних технологічних параметрів процесу брикетування відносять якість підготовки шихти (ступінь подрібнення компонентів, однорідність шихти, рівень вологості, тощо), режими пресування (тиск пресування, продуктивність та ін.), а також показники термічного та хімічного зміцнення брикетів (температура сушки, тривалість процесу зміцнення та ін.), якість брикетів (міцність, хімічний склад, вологостійкість та ін.) [3].
Необхідність відповідності способів обробки сировини і типу обладнання якості оброблюваного матеріалу випливає з можливостей процесу і обробного устаткування.
Критерій технічної складності дозволяє вибрати найменш інтенсивний процес з помірними параметрами.
Вартісні критерії при близьких технічних характеристиках дозволяють вибирати більш дешевий, отже, і найбільш вигідний варіант. До їх числа відносять вартість капітальних, експлуатаційних і приведених витрат, сума екологічних втрат і ін.
Розглянуті критерії придатні для вибору будь-яких технічних параметрів обладнання або параметрів технологічних процесів.
Найбільш обґрунтовано дана задача вирішується методом функціонально-вартісного аналізу, тому що відноситься до класу задач техніко-економічного характеру, пов'язаних з певними умовами, в число яких включається необхідність вартісної оцінки впливу кожного врахованого фактора на собівартість брикетування. За наявності декількох альтернативних факторів або операцій, витрати на їх реалізацію зіставляються з економією від підвищення міцності брикетів, спрощення або здешевлення технології. При цьому вибирають варіант з максимальною ефективністю [3].
На практиці такі розрахунки ускладнені наявністю значної кількості факторів і операцій, що реалізують ці чинники. Тому надалі обмежимося вибором мінімально необхідної їх кількості, яка забезпечить брикетам необхідну механічну міцність без використання екстремальних значень параметрів, значно ускладнюючих і здорожуючих процес брикетування.
6.2 Вибір способу отримання міцних брикетів
Спосіб отримання міцних брикетів необхідно вибирати практично за тими ж критеріями, що і вибір технології та її параметрів, однак з тією відмінністю, що перед розробкою технології вибирають спосіб, порівнюючи його з відомими альтернативами, а потім на його основі розробляють технологію і визначають її параметри, відповідні даному способу і дозволяють досягти заданий рівень якості продукції.
До теперішнього часу склалися кілька способів отримання міцних брикетів. До найбільш відомих варіантів відносять брикетування з використанням зв’язуючих, а також гаряче
брикетування. Ці варіанти дозволяють додати брикетам високу міцність, однак мають ряд недоліків (висока вартість, введення зі зв’язуючими шкідливих і баластних домішок, високий знос устаткування і т.п.), що не дозволяють досягти високої ефективності процесу брикетування.
Компонентний склад брикетів визначається не тільки вимогами по механічній міцності і хімічному складу, в т.ч. вмісту глиноземистих компонентів, а й умовою утилізації максимальних обсягів шламів.
Залежно від наявності тих чи інших інвестиційних можливостей підприємства мають місце два способи отримання брикетів.
Перший спосіб менш капіталомісткий, але вимагає більш значних експлуатаційних витрат. Він включає підготовку шихти, брикетування, інтенсивне сушіння та відвантаження. Склад готової продукції може бути відсутнім, оскільки сухі брикети готові до вживання. Цей спосіб застосовують при надлишку дешевих теплоносіїв, наприклад, доменного або коксового газу.
Перший спосіб менш капіталомісткий, але вимагає більш значних експлуатаційних витрат. Він включає підготовку шихти, брикетування, інтенсивне сушіння та відвантаження. Склад готової продукції може бути відсутнім, оскільки сухі брикети готові до вживання. Цей спосіб застосовують при надлишку дешевих теплоносіїв, наприклад, доменного або коксового газу.
В цілому другий спосіб має менші наведені витрати, проте в якості основного слід вибирати перший варіант, що забезпечує незалежність від погодних умов.
6.3 Масштабний ефект
При впровадженні у виробництво результатів лабораторних досліджень неминуче доводиться стикатися з явищем невідповідності одержуваних промислових зразків і параметрів їх виробництва з експериментальними зразками і параметрами. Це явище носить назву масштабного ефекту.
Масштабний ефект — це похибка фізичного моделювання, яка виникає внаслідок порушення подібності (геометричного, хімічного, термічного та ін) процесів в лабораторних і промислових умовах [3].
Для брикетів це стосується розмірів, форми, щільності, міцності, тиску пресування, параметрів зміцнення та ін. Механічне перенесення досягнутих в лабораторних умовах тисків, вологості, часу сушіння в промислових умовах може не забезпечити брикетам необхідної міцності.
Відмінність властивостей брикетів, отриманих в результаті пресування в лабораторних і дослідно-промислових умовах, дозволяє оцінити величину масштабного ефекту і розробити необхідні зміни до прийнятої технології брикетування і при необхідності перегляду параметрів брикетування.
6.4 Визначення основних параметрів технології брикетування
При визначенні технології брикетування слід прийняти такі основні технологічні параметри, які прийнятні для отримання міцних брикетів:
- тип преса — вальцьовий, що забезпечує тиск пресування: робочий — 50 МПа, максимальний — 90 МПа; характер пресування — двосторонній, на вальцьовому пресі має бути передбачене підпресування; регулювання міцності брикетів може здійснюватися підвищенням тиску до 90 МПа;
- фракція брикетів — 50–60 мм для типового вічка, форма брикетів — сідлоподібна або подушкоподібна, що забезпечує максимум продуктивності;
- черговість змішування шихти наступна: на початку змішують вапняно-глиноземисті компоненти, потім подають інші;
- переважно оббризкування осередків олійно-графітовою суспензією;
- передбачається використання повернення в кількості 2%, що дорівнює кількості відсіву і бою брикетів, що утворюються при промисловому брикетуванні, що рівносильне повторному пресуванню такої ж кількості брикетів; при наявності аглофабрики переважнішим є введення цієї дрібниці в аглошихту, що істотно збільшує продуктивність агломашин і покращує якість агломерату [29];
- вологість бриктуємої шихти повинна витримуватися на оптимальному рівні, визначеному експериментально;
- передбачається два режими сушки: інтенсивний — при температурі сушіння 250–500 °С, природний — при 20–25 °С; варіант сушіння визначається заданою кінцевою вологістю брикетів (0,5% і 1–2%).
Оскільки результуючий вплив обраних факторів на механічну міцність брикетів в загальному випадку не дорівнює сумі впливів кожного з них, проводять пробне брикетування з урахуванням обраних технологічних факторів.
Досвід брикетування дрібнозернистих матеріалів показує, що обов'язковою умовою отримання брикетів необхідної якості є суворе дотримання технологічного регламенту, в тому числі:
- безумовне виконання встановленого режиму підготовки матеріалу;
- співвідношення кількості матеріалу і зв'язуючого, а також вологості;
- умов змішування матеріалу зі зв'язуючим;
- відповідності продуктивностей дозатора матеріалу і преса;
- оптимального тиску пресування;
- умов дозрівання брикетів і їх складування [32].
7. Принципова технологічна схема процесу брикетування
Критеріями необхідності тієї чи іншої операції і віднесення її до тієї чи іншої стадії виробництва є вимога досягнення заданих показників, характеристик і параметрів оброблюваного матеріалу. Так, при підготовці сировини до пресування, у якості цих характеристик виступають вологість, фракційний склад, однорідність суміші та ін. При пресуванні такими характеристиками служать щільність і міцність сирих брикетів, кількість повернення що утворюється, чи витягаються брикети з прес-форми та ін. При зміцненні брикетів - міцність готових брикетів, їх залишкова вологість, наявність летких речовин і др.
Окрім основних, безпосередньо виробничих операцій, брикетування включає підготовчо-заключні операції, зокрема, такі, як приймання вихідної сировини і відвантаження готової продукції.
Процес брикетування металургійної сировини містить ряд складових, елементів, операцій, в тій, чи іншій мірі схожих з іншими методами огрудкування — агломерацією і окатування. До таких складових, в першу чергу, відноситься підготовка сировини і елементи відвантаження готової продукції, які можуть бути використані і в брикетуванні. Мають схожість і окремі процеси огрудкування, в основі яких лежать одні й ті ж процеси злипання і зв'язування частинок в міцний моноліт [3].
Ця схожість багато в чому визначається однаковими видами і властивостями вихідної сировини, компонентним складом шихти, закономірностями формування шматка, наявністю термообробки, вимогами до готової продукції, її відвантаження і т.п. Ці операції багато в чому зумовлюють умови підготовки сировини і можуть бути використані для виробництва брикетів практично в незмінному вигляді [3].
Використання максимально можливої кількості відомих процесів дозволяє застосовувати стандартне обладнання і типові операції, що значно спрощує технологію брикетування, а також здешевлює капітальні та поточні витрати на будівництво установки та її експлуатацію.
Таким чином, технологічний процес брикетування в загальному вигляді складається з трьох стадій (технологічно пов'язаних етапів, груп операцій):
- підготовка сировини до брикетування;
- пресування (формування) брикетів;
- зміцнення (сушіння) брикетів.
Підготовка сировини до брикетування включає наступні етапи:
- приймання та складування сировини;
- підготовка сировини до обробки;
- дозування, змішування і усереднення сировини;
- підготовка і введення в шихту зв'язуючих.
Стадія пресування брикетів складається з одного етапу — пресування брикетів (рис 7.1). У разі отримання брикетів іншим способом, ніж пресування, застосовують узагальнюючий термін — формування.
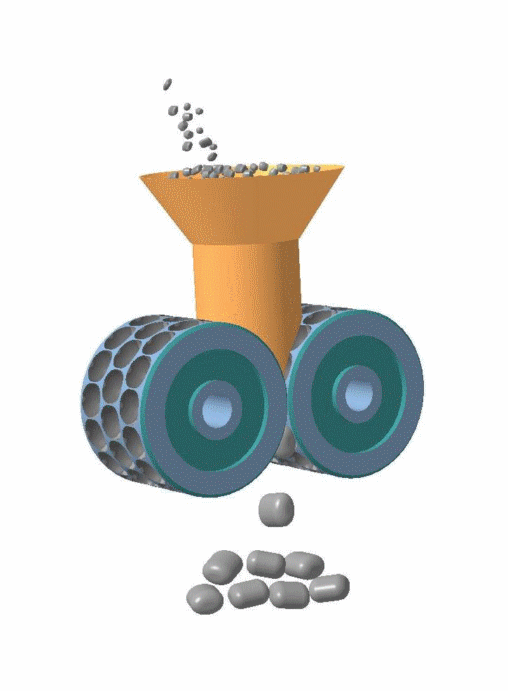
Рисунок 7.1 - Приклад роботи брикетного пресу
(8 картинок, 5 кадров/с, объем - 290кб)
Зміцнення брикетів включає наступні етапи:
- вилежування;
- сушіння й витримка брикетів;
- зміцнююча обробка активними середовищами і матеріалами.
Зміцнення брикетів може здійснюватися різними способами, з яких сушка внаслідок своєї високої ефективності займає превалююче становище.
Відвантаження брикетів формально не належить до процесу брикетування, однак правильна її організація сприяє зменшенню втрат брикетів від руйнування при вантажно-розвантажувальних роботах та транспортуванні, тому даний етап підлягає регламентації.
Технологічна схема процесу брикетування представлена на рис. 7.2.
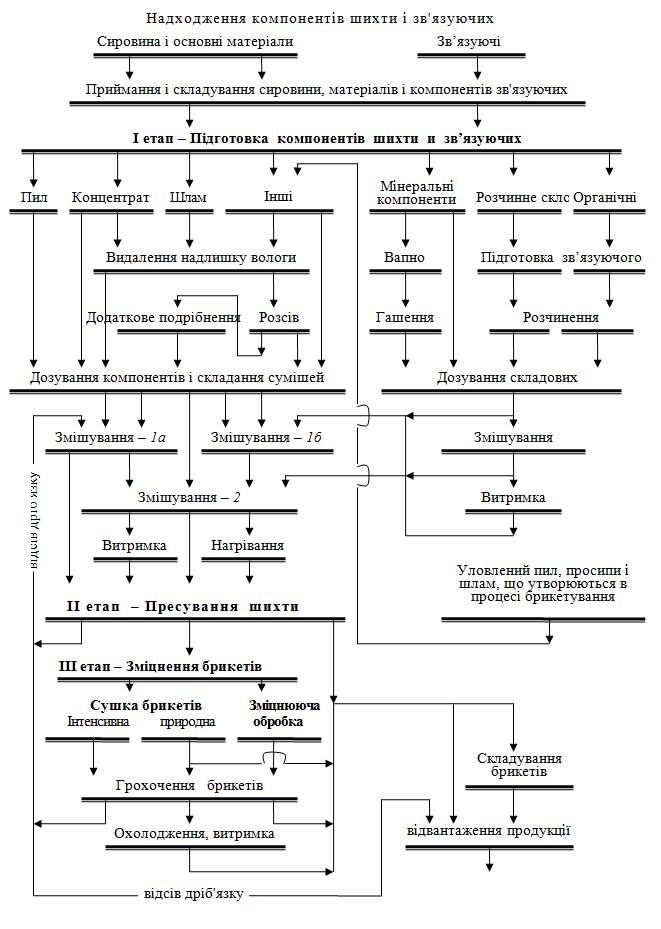
Рисунок 7.2 — Технологічна схема брикетування сировини
Спрощена схема ланцюга апаратів установки брикетування, відповідна до представленої на рис. 7.2 технологічної схеми брикетування металургійної сировини, зображена на рис. 7.3.
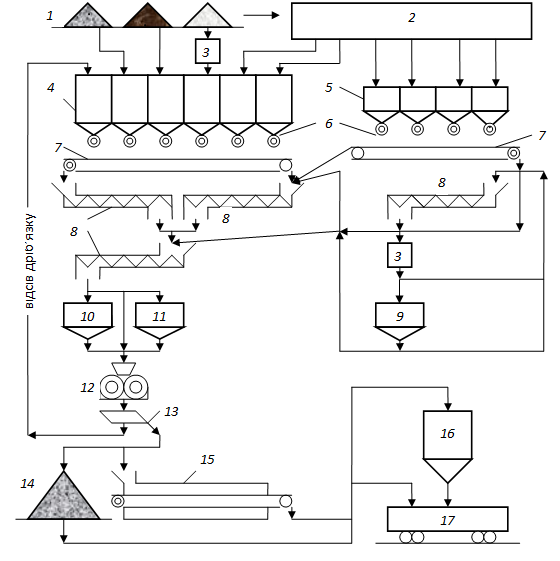
1 - відкритий склад сировини; 2 - закритий склад сировини, матеріалів і зв'язуючих; 3 - дробарки; 4 - бункери для компонентів шихти; 5 - бункери для компонентів зв'язуючих; 6 - дозатори; 7 - збірний конвеєр; 8 - змішувачі; 9 - пристрій для гасіння вапна; 10 - бункер для витримки шихти; 11 - нагрівальний пристрій; 12 - брикетний прес; 13 - грохот; 14 - майданчик для охолодження і витримки брикетів; 15 - стрічкове сушило; 16 - бункер готової продукції; 17 - залізничний вагон.
Рисунок 7.3 — Схема ланцюга апаратів технологічної лінії
для виробництва брикетів
Для проектування установки брикетування необхідний підбір устаткування, що виконує відповідні технологічні операції або групи операцій, яке встановлюють у відповідності з технологічною схемою в єдиний цикл. Так, операцію змішування виконують змішувачі різних типів, дозування — дозатори, пресування — брикетні преси, сушку — сушильні печі і т.д.
Вибір того, чи іншого типу обладнання повинен проводитися за наступними критеріями:
- пропускної здатності (продуктивності) обладнання з урахуванням резерву потужності, що дозволяє його експлуатацію в щадному режимі;
- забезпечення заданих характеристик і якості обробки сировини;
- мінімізації капітальних і експлуатаційних витрат;
- мінімальних габаритів, що вписуються
в будівлю;
- забезпечення екологічних норм, нормативів охорони праці та ін.
Остаточний вибір того чи іншого виду обладнання проводять шляхом зіставлення його технічних характеристик з відповідними вимогами даної операції. Якщо ефективність роботи обраного типового обладнання викликає сумніви, необхідно проведення дослідного опробування та внесення необхідних змін у конструкцію в процесі його виготовлення у виробника.
Висновки
Підвищений інтерес до брикетування в даний час пояснюється кризовим розвитком екологічної обстановки, в яку істотний негативний внесок вносить агломерація, поступовою виробкою родовищ якісної аглоруди, підвищенням частки тонкоподрібнених концентратів, що негативно впливають на інтенсивність агломерації. Зменшення запасів коксівного вугілля змушує приділяти все більшу увагу позадоменним методам отримання заліза, для яких брикетування, поряд з окотуванням, може виявитися основним методом огрудкування [3].
Літературний і експериментальний аналіз вітчизняного та зарубіжного досвіду, показує високу ефективність брикетування при його використанні не лише як основного, а й, особливо, в якості допоміжного методу огрудкування подрібненої металургійної сировини. Істотно збільшується продуктивність металургійних агрегатів, економиться первинна сировина, знижується витрата енергоресурсів, підвищується вихід придатного, поліпшується якість металу. Знижується шкідливий вплив на навколишнє середовище, відзначається зростання і інших техніко-економічних показників.
Вивчення вітчизняного і зарубіжного досвіду отримання та використання брикетів показує, що у чорній металургії України, незважаючи на зростання потреби в нових матеріалах, брикетування не знаходить належної уваги, якої воно по праву заслуговує.
Виробничники і деякі вчені-металурги пояснюють становище різними об'єктивними причинами, в т.ч. незадовільною міцністю брикетів, недостатнім науковим і виробничим досвідом їх отримання, відсутністю необхідного обладнання, низькою його ефективністю, недостачею необхідної інформації і т.п. Однак успішний закордонний досвід використання брикетування та отримані результати, спростовують ці твердження.
Тому розробка і впровадження передових, енергозберігаючих, ефективних технологій огрудкування залізовмісних відходів металургійного виробництва є перспективною й актуальною науково-практичною задачею.
Список використаної літератури
- Банный Н.П. Экономика чёрной металлургии СССР / Н.П. Банный, А.А. Федотов, П.А. Ширяев и др. – М.: Металлургия, 1978. – 344 с.
- Равич Б.М. Брикетирование в цветной и чёрной металлургии / Б.М. Равич. – М.: Металлургия, 1975. – 232 с.
- Ожогин В.В. Основы теории и технологии брикетирования измельчённого металлургического сырья: Монография. – Мариуполь, ПГТУ, 2010. – 442 с
- Динельт В.М. Малооперационная технология получения брикетов из тонкодисперсных углеродистых материалов и отходов / В.М. Динельт, В.М. Левинец, М.С. Никишанин и др. // Изв. вузов: Чёрная металлургия. – 2007. – № 6. – С. 61-63.
- Фоменко А.И. Утилизация шламов металлургических производств / А.И. Фоменко // Изв. вузов: Чёрная металлургия. – 2001. – № 11. – С. 70-71.
- Барышников В.Г. Вторичные материальные ресурсы чёрной металлургии: Справочник. В 2-х т. Т. 2: Шлаки, шламы, отходы обогащения железных и марганцевых руд, отходы коксохимической промышленности, железный купорос / В.Г. Барышников, А.М. Горелов, Г.И. Папков и др. – М.: Экономика, 1986. – 344 с.
- Типовая технологическая инструкция о порядке учета образования и использования железосодержащих шламов (пылей) на металлургических предприятиях Минчермета СССР. ТТИ 2.2-08-02-81: Утв. Техн. упр. Минчермета СССР 26.06.81: Срок действия с 01.01.82 / Минчермет СССР. – Свердловск, 1982. – 32 с.
- Классен П.В. Гранулирование / П.В. Классен, И.Г. Гришаев, И.П. Шомин. – М.: Химия, 1991. – 320 с.
- Ефремов Г.И. Пылеочистка / Г.И. Ефремов, В.П Лукачевский. – М.: Химия, 1990. – 72 с.
- Гончаров Б.Ф. Технико-экономические расчеты по производству чугуна / Б.Ф. Гончаров, И.С. Соломахин. – Харьков: Вища школа, 1979. – 176 с.
- Вегман Е.Ф. Краткий справочник доменщика / Е.Ф. Вегман. – М.: Металлургия, 1981. – 240 с.
- Овчаренко Н.Л. Неполадки хода доменных печей / Н.Л. Овчаренко. – М.: Металлургия, 1972. – 192 с.
- Эсезобор Д.Э. Разработка малоотходной технологии аглодоменного производства: автореф. … дис. канд. техн. наук: 05.16.02. – Донецк, Донецкий госуд. техн. ун-т., 1994. – 20 с.
- Лурье Л.А. Брикетирование в чёрной и цветной металлургии / Л.А. Лурье. – М.: Металлургиздат, 1963. – 324 с.
- Политехнический словарь / Гл. ред. акад. А.Ю. Ишлинский. – 2-е изд. – М.: Советская энциклопедия, 1980. – 656 с
- Супрун Ю.М. Обезвоживание шламов металлургического производства на фильтр-прессах за рубежом / Ю.М. Супрун // Чёрная металлургия: Бюл. ин-та Черметинформация. – 1984. – № 5. – С. 14-23.
- Раджи О.И. Совершенствование технологии подготовки и утилизации металлургических шламов: автореф. дис. … канд. техн. наук: 05.16.02. – Донецк, ДНТУ, 2004. – 21 с.
- Волков Ю.П. Технолог-доменщик: Справочное и методическое руководство / Ю.П. Волков, Л.Я. Шпарбер, А.К. Гусаров. – М.: Металлургия, 1986. – 263 с.
- Воскобойников В.Г. Технология и экономика переработки железных руд / В.Г. Воскобойников, Л.П. Макаров. – М.: Металлургия, 1977. – 256 с.
- Ярхо Е.Н. Экономическая эффективность подготовки железных руд к плавке / Е.Н. Ярхо. – М.: Металлургия, 1974. – 96 с.
- Мироненко П.Ф. Методика металлургической оценки качества марганцевого сырья по его химическому составу / П.Ф. Мироненко, Ю.Б. Дедов, В.А. Гладких и др. // Сталь. – 2000. – № 8. – С. 29-31.
- Дударенко А.А. Концепция формализации управления качеством продукции по экономическому критерию / А.А. Дударенко, Т.А. Мазурова, А.Г. Чефранов // Теория и практика металлургии. – 1999. – № 6. – С. 60-64.
- Ожогин В.В. Комплексная оценка качества металлургического сырья / В.В. Ожогин, Н.С. Захаренко // Вестник Приазов. госуд. техн. ун-та: Сб. науч. тр. – Мариуполь. – 1999. – Вып. 8. – С. 254-256.
- Жак А.Р. Интегральные показатели металлургических свойств окускованного железорудного сырья / А.Р. Жак, Н.В. Ратников, Ю.С. Юсфин и др. // Сталь. – 1998. – № 3. – С. 10-13.
- Жак А.Р. Интегральные показатели химического состава окускованного железорудного сырья / А.Р. Жак, Н.В. Ратников, Ю.С. Юсфин и др. // Сталь. – 1998. – № 11. – С. 7-12
- Доменное производство: Справ. изд. В 2-х т. Т. 1. Подготовка руд и доменный процесс / Под ред. Вегмана Е.Ф. – М.: Металлургия. – 1989. – 496 с.
- Носков В.А. Перспектива подготовки и использования мелкофракционных железосодержащих отсевов сталеплавильных шлаков в доменной плавке / В.А. Носков, Н.М. Можаренко, Б.Н. Маймур // Металлург. и горноруд. пром-сть. – 2001. – № 1. – С. 119-121.
- Ожогин В.В. Брикетирование как полноправный метод окускования металлургического сырья / В.В. Ожогин, А.А. Томаш, И.А. Ковалевский и др. // Металлургические процессы и оборудование. – 2005. – Вып. 2. – С. 54-58.
- Ожогин В.В. Совершенствование ресурсосберегающей технологии получения и использования высокопрочных шламовых брикетов в аглодоменном производстве: дис. … канд. техн. наук: 05.16.02. – Мариуполь, ПГТУ, 2004. – 207 с.
- Словарь иностранных слов. – 18-е изд., стер. – М.: Рус. яз., 1989. – 624 с..
- Уманский Я.С. Рентгенография / Я.С. Уманский, А.К. Трапезников, А.И. Китайгородский и др. – М.: Машгиз, 1951. – 310 с.
- Бабанин В.И. Брикетирование мелкозернистых материалов в ферросплавном производстве: опыт и возможности / В.И. Бабанин, А.Я. Ерёмин // Металлург. – 2006. – 5. – С. 45-50.
- Большая Советская Энциклопедия. В 30 т. / Гл. ред. А.М. Прохоров. Изд. 3-е. – М.: Советская Энциклопедия, 1973 // Т. 8. Дебитор – Евкалипт. – 1972. – С. 172.
- Ожогин В.В. Дефекты брикетов и способы их устранения / В.В. Ожогин, И.А. Ковалевский, А.И. Ковалевский // Металург. процессы и оборудование. – 2008. – № 4. – С. 36-39.