Реферат по теме выпускной работы
При написании данного реферата магистерская работа еще не завершена. Окончательное завершение: январь 2015 года. Полный текст работы и материалы по теме могут быть получены у автора или его руководителя после указанной даты.
Содержание
- Введение
- 1. Цель, идея и задачи исследования
- 2. Преимущества и недостатки способов и технологий брикетирования металлургических материалов
- 3. Краткая характеристика используемого сырья
- 4. Традиционные связующие, используемые при брикетировании
- 5. Качество исходного сырья и брикетированных материалов
- 6. Особенности выбора параметров технологии брикетирования
- 6.1 Критерии выбора технологии и её параметров
- 6.2 Выбор способа получения прочных брикетов
- 6.3 Масштабный эффект
- 6.4 Определение основных параметров технологии брикетирования
- 7. Принципиальная технологическая схема процесса брикетировани
- Выводы
- Список источников
Введение
С каждым годом запасы рудного сырья с достаточным количеством железа беспрерывно истощаются. В скором времени, технологии которые широко используются в металлургии в настоящее время, станут непригодными для переработки низкосортного сырья. В связи с этим актуальной становится задача разработки технологий изготовления металлопродукции из вторичного сырья, которое в огромных количествах накапливается на каждом металлургическом предприятии.
Не смотря на современные достижения в сфере защиты окружающей среды, металлургическое производство оказывает значительное влияние на биосферу. Чёрная металлургия является одной из материалоемких и энергоёмких, а также экологически вредных отраслей промышленности. Так, общий расход материально-сырьевых ресурсов по циклу от добычи руды и угля до прокатки составляет до 7 т на 1 т готового проката [1].
Металлургические заводы и комбинаты для того чтобы уменьшить собственные затраты на производство, утилизируют эти отходы путем захоронения их на специальных полигонах. В основном из-за отсутствия технологии их переработки либо их недостаточной эффективности.
Альтернативные методы получения металла, металлургия тонкоизмельчённых материалов и ресурсосберегающие технологии в скором будущем получат всё более широкое распространение. При этом наличие большого количества тонкофракционных материалов и концентратов глубокого обогащения, а также шламов и пылей приводит к ухудшению процессов агломерации, усложняет окатывание.
Производство окатышей и брикетов, которые включают тонкодисперсные компоненты железосодержащих отходов металлургии, связано с некоторыми затруднениями, обусловленными рядом противоречивых требований к технологическим режимам окускования и значительной нестабильностью характеристик получаемого сырья.
Поэтому разработка и внедрение передовых, энергосберегающих, эффективных технологий окускования железосодержащих отходов металлургического производства является перспективной и актуальной научно-практической задачей.
1. Цель, идея и задачи исследования
Цель работы — разработка технологических режимов производства композиционных окатышей и брикетов, которые включают железосодержащие отходы металлургического производства.
Идея работы — использование современных технологий и техники окускования и брикетирования для производства композиционных материалов на основе вторичных железосодержащих продуктов металлургии.
Задачи исследования:
- Теоретический анализ механизма формирования композиционных окатышей и брикетов;
- Экспериментальные исследования возможных технологий производства окатышей и брикетов;
- Разработка рекомендаций для промышленных технологических схем окускования.
2. Преимущества и недостатки способов и технологий брикетирования металлургических материалов
За рубежом с начала ХХ века широко используют брикетирование, которое считают весьма эффективным способом окускования отходов. Наибольшее распространение брикетирование получило в Германии, США и Японии [3].
В России и других странах СНГ в последнее время резко возрос интерес к брикетированию как экологически чистому и экономически выгодному методу окускования металлургических отходов [4,5].
В цветной металлургии брикетирование нередко применяют в качестве основного метода окускования сырья в тех случаях, когда другие методы окускования не дают желаемого результата: сырьё плохо окомковывается и спекается, а при спекании удаляются нужные компоненты (углерод, сера и др.).
Брикетирование имеет ряд существенных преимуществ, которые в создавшихся условиях развития металлургии позволяют считать его перспективным методом окускования. К их числу относятся следующие [3]:
- Брикетирование предъявляет менее жёсткие требования к качеству сырья, позволяет окусковывать материалы широких классов крупностью менее 10 мм, практически в любых пропорциях и составах;
- Процесс брикетирования технологически прост; некоторую трудность представляет лишь дозирование связующих и их смешивание с брикетируемым материалом;
- При брикетировании сохраняются свойства компонентов, входящих в брикеты;
- Брикетирование является экологически чистым способом окускования;
- Брикетирование расширяет сырьевую и топливно-энергетическую базу металлургии, позволяет шире внедрять внедоменные способы получения железа.
Эти преимущества позволяют эффективно решать такие актуальные задачи, как получение новых, комплексных видов сырья, включающих оксиды железа, восстановитель и флюс, внедрение эффективных способов обработки сырья, например, металлизацией, снижение вредного влияния металлургических процессов на окружающую среду.
К основным недостаткам брикетирования обычно относят следующие[3]:
- Недостаточная прочность брикетов, особенно при высоких температурах и в условиях восстановительной атмосферы;
- Использование связующих, содержащих вредные примеси и имеющих недостаточные вяжущие свойства;
- Высокая стоимость качественных связующих;
- Трудности, связанные с равномерным введением связующих в шихту;
- Недостаточная производительность прессового оборудования.
К настоящему времени большинство этих проблем частично решены. За рубежом сформированы несколько направлений получения прочных брикетов, к числу которых относят «горячее» брикетирование, высокотемпературную обработку брикетов, использование термостойких связующих.
3. Краткая характеристика используемого сырья
В металлургическом производстве используют большое количество материальных ресурсов, имеющих общее, терминологически установившееся название: сырьё, сырьё и материалы или сырьевые (сырые) материалы. Технологическое топливо в виду его важности, особого влияния на металлургические процессы, а также высокой стоимости выделено в отдельную группу [3].
По назначению и характеру потребления сырые металлургические материалы делятся на основные и вспомогательные. Основные материалы составляют главное содержание продукта, например, руды, концентраты. Вспомогательные материалы используют в процессе производства как добавочные и прочие материалы, улучшающие технологический процесс и качество продукции, в частности, флюсы, легирующие добавки и др. [3].
По источникам образования все материалы подразделяют на первичные, свежие материалы и оборотные, вторичные материалы или отходы. К оборотным материалам относят используемые отходы, прoсыпи, возвраты, побочные и попутные продукты. Под отходами металлургического производства в широком смысле слова следует понимать сырьё, материалы и энергоресурсы, в силу тех или иных причин не использованные для получения основной продукции. Отходы являются неизбежным элементом существующей технологии производства металлов.
В случае окускования отходов брикетированием первичное сырьё, материалы и отходы классифицируют [6, 7]:
- по месту производства, возникновения или источникам образования;
- по характеру образования и удаления;
- по способу добычи, извлечения или улавливания;
- по химическому (вещественному) составу;
- по физическим свойствам;
- по другим (в т.ч. технологическим) критериям.
По месту производства первичное сырьё и материалы подразделяют на поставляемые со стороны и собственные [7].
В качестве классификации отходов по месту возникновения может служить номенклатура шламов, представленная в [6,7].
По характеру образования и удаления все отходы подразделяют на уносы с отходящими газами (пыли); просыпи, осыпи, смывы (шламы); сливы, натёки, остатки (шлаки, сварочный шлак, скардовины).
По химическому (вещественному) составу отходы группируют по двум уровням – виду (наличию) и содержанию основного компонента. По виду основного компонента отходы классифицируют на железосодержащие, марганецсодержащие и др., а также отходы, детерминируемые по вредному компоненту [7].
По содержанию основного компонента отходы классифицируют на богатые, относительно-богатые и бедные. Уровень богатства определяют сопоставлением с аналогичным первичным сырьем.
По вещественному (компонентному) составу шламы представляют собой смеси остатков сырья и материалов, частично подвергшихся обработке, уносы, возгоны и вторичные оксиды.
К физическим свойствам, определяющим пригодность шламов к окускованию гранулированием, относят плотность, дисперсность, адгезионную способность и другие свойства [8].
Плотность является важным свойством материалов, от которого зависит эффективность того или иного способа окускования. Так, при агломерации желательно, чтобы объёмная плотность шихты принимала максимальное значение при некотором оптимальном значении насыпной плотности, обеспечивающей нужную газопроницаемость. При брикетировании, наоборот, следует стремиться к увеличению насыпной плотности, что уменьшает усадку материала и позволяет получать более прочные брикеты.
К основным свойствам, характеризующим брикетируемость материалов, относится дисперсность (измельчённость). Для полидисперсных материалов характеристикой дисперсности является фракционный состав. По фракционному составу брикетируемые материалы подразделяют на:
- кусковые — 80–90% размером более 10 мм;
- крупнозернистые и зернистые — 40–60% размером 1–10 мм;
- мелкие — 60–80% размером 3,0–0,074 мм;
- пылевидные — 60–80% размером 0,5–0,01 мм;
- тонкие — более 50% размером менее 0,05 мм [6].
Многие виды металлургического сырья и отходов имеют мелкий и пылевидный состав, а также разнообразные физические свойства [10,11].
По физическим свойствам и химическому составу эти материалы обладают целым рядом особенностей. Это — неоднородность химического состава, низкая смачиваемость и плохая влагоудаляемость [12].
По слипаемости все материалы и пыли можно условно подразделить на три группы [9]:
- первая группа — неслипающиеся и слабослипающиеся; как правило, это сухие материалы, фракция +0,063 мм которых составляет более 80%;
- вторая группа — среднеслипающиеся, 80% которых имеют размер 0,063–0,01 мм;
- третья группа — сильнослипающиеся; это пыли с частицами —0,01 мм.
По влажности измельчённое сырьё и шламы подразделяют на пылевидные (до 3% влаги), сухие (3–6%), нормальные (6–12%), влажные (12–18%) и переувлажненные (более 18%). Влагоемкость данных материалов в значительной степени зависит от удельной поверхности частиц, т.е. чем сильнее измельчён материал, тем больше влаги он удерживает.
Важной металлургической характеристикой сырья является его способность образовывать легкоплавкие и жидкоподвижные соединения, хорошо смачивающие и скрепляющие частицы шихты при спекании, что повышает прочность агломерата [13].
4. Традиционные связующие, используемые при брикетировании
При брикетировании многих видов измельчённого сырья, обладающего недостаточными аутогезионными свойствами, даже при высоких давлениях (180 МПа и более) обычным холодным прессованием получать прочные брикеты без их спекания не представляется возможным. В таких случаях используют связующие — вспомогательные материалы, улучшающие слипаемость частиц и повышающие прочность брикетов до заданного уровня 3].
Поскольку добавки таких материалов могут составлять от нескольких до 10% и более, они должны соответствовать следующим требованиям [2,14]:
- Обладать высокими аутогезионными свойствами, т.е. обеспечивать высокую холодную и горячую прочность при минимальном расходе связующего;
- Обеспечивать быструю схватываемость;
- Вносить минимальное количество вредных, балластных и других примесей, небезопасных для обслуживающего персонала и снижающих качество конечного продукта;
- Не ухудшать условий плавки брикетов;
- Быть распространёнными и обладать невысокой стоимостью;
- Не требовать сложных приёмов и операций по их использованию;
- Обеспечивать минимальную влагостойкость.
Связующее является определяющим условием прочности и в значительной мере — восстановимости брикетов. Увеличение расхода связующего, повышая прочность, приводит не только к снижению полезных компонентов в брикетах, но и к значительному их удорожанию.
Связующие подразделяют на три типа: минеральные (неорганические), органические и комбинированные [3].
К распространённым неорганическим связующим следует отнести гашёную известь, жидкое стекло, глинозёмистый и портландский цементы. Однако многие из них обладают существенными недостатками. Так, гашёная известь и портландцемент при нагревании отдают гидратную влагу и теряют прочность, жидкое стекло содержит значительное количество щелочей и двуокись кремния, а глинозёмистый цемент к тому же чрезвычайно дорог. При этом лучшие вяжущие характеристики обнаруживает жидкое стекло и глинозёмистый цемент[3].
К распространённым органическим связующим относят каменноугольные и нефтяные смолы, меласса, отходы гидролизной и целлюлозной промышленности и т.п. Общим недостатком органических связующих является их пиролиз или выгорание при высоких температурах с потерей прочности, а также внос в брикеты значительного количества серы [3].
Большинство органических связующих могут использоваться для получения брикетов с высокими показателями холодной прочности. При нагреве таких брикетов связка разрушается или сгорает, в результате чего они теряют бoльшую часть прочности, рассыпаются под давлением верхних слоёв материала и выносятся потоком газов из агрегата. Более стойкие связующие при сгорании образуют спёкшийся шлак, который скрепляет частицы брикетов, препятствуя их разрушению [3].
Связующие неорганического происхождения, помещаясь между частицами оксидов железа и восстановителя, ухудшают восстановимость. Органические связующие, частично заменяя восстановитель, обычно вносят нежелательные примеси, в т.ч. серу. Наряду с этим некоторые виды связующих при нагреве могут способствовать образованию легкоподвижных фаз, например, фаялита, что желательно для усадки восстанавливающихся брикетов [3].
К комбинированным связующим относят смеси различных связующих. Эти смеси позволяют улучшить положительные и снизить негативные свойства. Например, смесь, содержащая жидкое стекло и лигносульфонат, вносит пониженное количество щелочей, кремнезёма или серы, чем каждое связующее в отдельности, при одновременном обеспечении высокой механической прочности брикетов [3].
5. Качество исходного сырья и брикетированных материалов
Качество материала — это совокупность его свойств, удовлетворяющих определённым потребностям в соответствии с его назначением [15]. Качество брикетов, как и любого металлургического сырья и материалов, должно соответствовать условиям потребляющего процесса
Современный технический уровень металлургического производства позволяет использовать материалы разнообразного качества с достаточно широким разбросом по содержанию полезных компонентов и вредных примесей. Однако для экономически эффективной переработки требуется сырьё определенного качества. Брикеты же, изготовляемые из отходов, имеют пониженное содержание полезных компонентов и повышенное — вредных [3].
Для усиления заинтересованности в использовании брикетов, в т.ч. и из отходов, требования, предъявляемые к ним, должны быть несколько снижены. Экономически это снижение обеспечивается уменьшением воздействия на окружающую среду путём использования более дешёвого и экологически безопасного метода окускования, чем агломерация или окатывание, снижение платежей, вносимых предприятиями за размещение отходов в окружающей среде, а также более низкой стоимостью отходов по сравнению с первичным сырьём [3].
В настоящее время для оценки качества металлургического сырья — мономатериалов (руды, концентрата, флюсов и др.) и материалов, из них изготавливаемых (агломерата, окатышей), сформирована система единичных показателей, представленных в соответствующих ГОСТах, ДСТУ, СТП, технических условиях и иных нормативно-технических документах, позволяющих оценивать соответствие того, или иного материала тому, или иному металлургическому процессу. Они регламентируют химический состав, физические и металлургические свойства, а также механическую прочность, см. рис. 5.1.
Так, в соответствии с [7,16] шламы, используемые при окусковании, должны отвечать следующим требованиям:
– влажность шлама не более 8–12%;
– крупность комков шлама после сушки не более 6 мм;
– минимальное приведенное содержание железа не менее 45%;
– содержание вредных примесей определяется возможностями потребляющих технологий;
– содержание цинка не более 1%;
– общее содержание полезных компонентов не менее 45%.
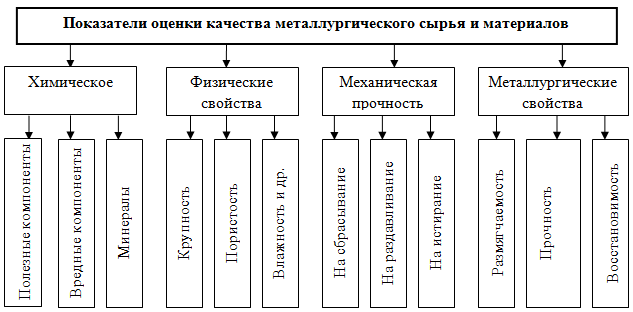
Рисунок 5.1 — Система оценки качества металлургического сырья и материалов
Содержание вредных примесей с учётом поступающих в печь со всей шихтой, в брикетах не должно превышать некоторых предельных количеств: для цинка – 0,3 кг/т чугуна, щелочей — 4–7 кг/т [17] и т.п.
Большинство из этих показателей являются браковочными, т.е., если значение какого-либо показателя не соответствует требованиям нормативного документа, то материал не подлежит использованию в данном процессе.
Для агломерата и окатышей, изготовленных с добавками шламов, сохраняются практически те же требования, что и для обычных материалов [18].
Однако для брикетов из первичного сырья и отходов, являющихся поликомпонентным сырьём, следует использовать другие методы оценки, такие, как оценка по приведенному содержанию железа, по металлургической ценности или по методу академика М.А. Павлова, выдвинувшего идею укрупнённой стоимостной оценки качества [7,19].
Для более точной оценки следует использовать сложные системы [20–25].
Прочность — это свойство материалов в определённых условиях и пределах, не разрушаясь, воспринимать те или иные воздействия (нагрузки, неравномерный температурный нагрев, высыхание, набухание, неравномерное протекание физико-химических процессов в разных частях тела и др.)[15].
В металлургии прочность является важной характеристикой окускованного материала. В сущности, она является браковочным критерием, по которому оценивают материал на пригодность к металлургической обработке. Недостаточная механическая прочность приводит к преждевременному измельчению материала и изменению условий, при которых процесс металлургической обработки является оптимальным, в частности, ухудшается газопроницаемость, увеличиваются потери материала с выносами и т.п.
Прочность металлургических материалов в значительной мере зависит от степени нагрева и химических воздействий, имеющих место в металлургическом агрегате и изменяющих их прочностные характеристики. При этом многие материалы в естественном состоянии имеют высокую прочность, а при нагреве и восстановлении быстро её теряют и разрушаются.
По данным [2,14,27,28] браковочные пределы механической прочности брикетов составляют следующие значения, см. табл. 5.1.
Наиболее эффективным оказывается брикетирование измельчённых материалов. При этом весьма сложной, трудно решаемой проблемой продолжает оставаться недостаточная механическая прочность брикетов.
Брикет | Размер брикета, мм | Пористость, % | Прочность | |||
---|---|---|---|---|---|---|
по ГОСТ 15137–77 | На сжатие, МПа | По ГОСТ 19575–84 | ||||
На сбрасывание | На истирание | |||||
Доменный | 40 | >10 | >70 | 5 | >18 | >40 |
Конвертерный | 30 | <10 | <70 | <10 | 10 | – |
Электропечной | 100 | – | <70 | 10 | >7,5 | – |
Сформировавшимся направлением повышения прочности, ставшим традиционным, является разработка и использование высокопрочных связующих. В принципе оно может обеспечить нужную прочность, но на практике пока ещё не даёт удовлетворительного решения поставленной задачи в основном из-за высокой стоимости связующего или ухудшения металлургических свойств брикетов.
Временной альтернативой этому направлению является более широкое использование брикетов в тех производствах, где требования к прочности менее высокие, например, в сталеплавильном производстве. В долговременной перспективе получение высокопрочных брикетов может осуществиться лишь комплексным сочетанием, как известных методов упрочнения, так и находящихся в настоящее время в стадии изучения и становления.
Важным фактором, определяющим работу доменных печей, является процесс шлакообразования, которому предшествует размягчение и плавление шихтовых материалов. Оптимальной работы доменной печи можно достичь лишь при использовании материалов с относительно высокой температурой начала размягчения и достаточно узким интервалом температур размягчения.
К показателям, характеризующим металлургические свойства сырья, относят температуру начала и температурный интервал размягчения, восстановимость и прочность железорудных материалов при восстановлении. Для сталеплавильных материалов, подвергающихся интенсивным температурным воздействиям при загрузке в сталеплавильный агрегат, испытание на термоудар является обязательным.
Металлургические свойства брикетов также определяют по горячей прочности (прочности при восстановлении), определяемой в барабане Линдера (для доменных брикетов) и способности выдерживать термоудар (для сталеплавильных брикетов). При отсутствии барабана Линдера металлургические свойства брикетов оценивают по размягчаемости и восстановимости. Совокупность этих показателей даёт возможность с достаточной степенью точности определить металлургические свойства брикетов [26].
В частности, брикеты, удовлетворяющие требованиям доменной плавки, должны быть устойчивы при температуре 900–1000 °С, а также в атмосфере перегретого до 150 °С пара, быть пористыми, газопроницаемыми и вместе с тем водоустойчивыми. Размягчение материалов, предназначенных для доменной плавки, должно осуществляться в интервале температур от 1050 до 1200 °С.
Брикеты для сталеплавильного производства должны выдерживать нагревание до 1500 °С в течение трёх минут и при этом не разваливаться на куски, а также иметь пористость не более 5–10 % [2].
6. Особенности выбора параметров технологии брикетирования
6.1 Критерии выбора технологии и её параметров
При разработке технологии брикетирования металлургического сырья используют следующие критерии выбора факторов, операций и параметров:
- показатели экономической эффективности (общей и сравнительной);
- условия необходимости и достаточности той или иной операции технологического процесса и величины её параметра[3].
Применение этих общих критериев в принципе может обеспечить репрезентативный выбор технологии и её параметров. При необходимости из них могут быть вычленены и другие критерии, такие как:
- соответствие способов обработки сырья и оборудования качеству обрабатываемого сырья;
- техническая сложность процесса;
- стоимостные критерии и др.[3].
Критерием (от греч. kriterion) — называют признак или мерило, на основании которого производится оценка или выбор чего-нибудь [30].
Технологическим параметром ((от греч. parametron — отмеривающий, соразмеряющий) процесса называют величину, характеризующую этот процесс либо отличающую его от какого-либо другого процесса [15,30].
К основным технологическим параметрам процесса брикетирования относят качество подготовки шихты (степень измельчения компонентов, однородность шихты, уровень влажности и др.), режимы прессования (давление прессования, производительность и др.), а также показатели термического и химического упрочнения брикетов (температура сушки, длительность процесса упрочнения и др.), качество брикетов (прочность, химический состав, влагостойкость и др.)[3].
Необходимость соответствия способов обработки сырья и типа оборудования качеству обрабатываемого материала вытекает из возможностей процесса и обрабатывающего оборудования.
Критерий технической сложности позволяет выбрать наименее интенсивный процесс с умеренными параметрами.
Стоимостные критерии при близких технических характеристиках позволяет выбирать более дешёвый, следовательно, и наиболее выгодный вариант. К их числу относят стоимость капитальных, эксплуатационных и приведенных затрат, сумма экологических потерь и др.
Рассмотренные критерии пригодны для выбора любых технических параметров оборудования или параметров технологических процессов.
Наиболее обосновано данная задача решается методом функционально-стоимостного анализа, т.к. относится к классу задач технико-экономического характера, связанных с определёнными условиями, в число которых включается необходимость стоимостной оценки влияния каждого учтённого фактора на себестоимость брикетирования. При наличии нескольких альтернативных факторов или операций, затраты на их реализацию сопоставляются с экономией от повышения прочности брикетов, упрощения или удешевления технологии. При этом выбирают вариант с максимальной эффективностью[3].
На практике такие расчёты усложнены наличием значительного количества факторов и операций, реализующих эти факторы. Поэтому в дальнейшем ограничимся выбором минимально необходимого их количества, которое обеспечит брикетам требуемую механическую прочность без использования экстремальных значений параметров, значительно усложняющих и удорожающих процесс брикетирования.
6.2 Выбор способа получения прочных брикетов
Способ получения прочных брикетов необходимо выбирать практически по тем же критериям, что и выбор технологии и её параметров, однако с тем отличием, что перед разработкой технологии выбирают способ, сравнивая его с известными альтернативами, а затем на его основе разрабатывают технологию и определяют её параметры, соответствующие данному способу и позволяющие достичь заданный уровень качества продукции.
К настоящему времени сложились несколько способов получения прочных брикетов. К наиболее известным вариантам относят брикетирование с использованием связующих, а также «горячее» брикетирование. Эти варианты позволяют придать брикетам высокую прочность, однако обладают рядом недостатков (высокая стоимость, ввод со связующими вредных и балластных примесей, высокий износ оборудования и т.п.), не позволяющих достичь высокой эффективности процесса брикетирования.
Компонентный состав брикетов определяется не только требованиями по механической прочности и химическому составу, в т.ч. содержанию глинозёмистых компонентов, но и условием утилизации максимальных объёмов шламов.
В зависимости от наличия тех или иных инвестиционных возможностей предприятия имеют место два способа получения брикетов.
Первый способ менее капиталоёмок, но требует более значительных эксплуатационных затрат. Он включает подготовку шихты, брикетирование, интенсивную сушку и отгрузку. Склад готовой продукции может отсутствовать, поскольку сухие брикеты готовы к употреблению. Этот способ применяют при избытке дешёвых теплоносителей, например, доменного или коксового газа.
Второй способ требует меньших эксплуатационных затрат, но более капиталоёмкий из-за необходимости строительства крытых складов, в которых происходит естественная сушка, упрочнение и защита брикетов от осадков. При длительности сушки от 14 до 28 суток ёмкость такого склада для годового объема производства 300 тыс. т. брикетов в год должна составлять 15–35 тыс. т.
В целом второй способ имеет меньшие приведенные затраты, однако в качестве основного следует выбирать первый вариант, обеспечивающий независимость от погодных условий.
6.3 Масштабный эффект
При внедрении в производство результатов лабораторных исследований неизбежно приходится сталкиваться с явлением несоответствия получаемых промышленных образцов и параметров их производства с экспериментальными образцами и параметрами. Это явление носит название масштабного эффекта.
Масштабный эффект — это погрешность физического моделирования, возникающая вследствие нарушения подобия (геометрического, химического, термического и др.) процессов в лабораторных и промышленных условиях [3].
Для брикетов это касается, размеров, формы, плотности, прочности, давления прессования, параметров упрочнения и др. Механический перенос достигнутых в лабораторных условиях давлений, влажности, времени сушки в промышленных условиях может не обеспечить брикетам требуемой прочности.
Различие свойств брикетов, полученных в результате прессования в лабораторных и опытно-промышленных условиях позволяет оценить величину масштабного эффекта и разработать необходимые изменения к принятой технологии брикетирования и при необходимости пересмотра параметров брикетирования.
6.4 Определение основных параметров технологии брикетирования
При определении технологии брикетирования следует принять такие основные технологические параметры, которые приемлемы для получения прочных брикетов:
- тип пресса — вальцовый, обеспечивающий давление прессования: рабочее — 50 МПа, максимальное — 90 МПа; характер прессования — двусторонний, на вальцовом прессе должна быть предусмотрена подпрессовка; регулирование прочности брикетов может осуществляться повышением давления до 90 МПа;
- фракция брикетов — 50–60 мм для типовой ячейки, форма брикетов — седловидная или подушкообразная, обеспечивающая максимум производительности;
- очерёдность смешивания шихты следующая: в начале смешивают известково-глинозёмистые компоненты, затем подают остальные;
- предпочтительно обрызгивание ячеек масляно-графитовой суспензией;
- предусматривается использование возврата в количестве 2 %, равном количеству отсева и боя брикетов, образующихся при промышленном брикетировании, что равносильно повторному прессованию такого же количества брикетов; при наличии аглофабрики предпочтителен ввод этой мелочи в аглошихту, что существенно увеличивает производительность агломашин и улучшает качество агломерата [29];
- влажность брикетируемой шихты должна выдерживаться на оптимальном уровне, определяемом экспериментально;
- предусматривается два режима сушки: интенсивный — при температуре сушки 250–500 °С, естественный — при 20–25 °С; вариант сушки определяется заданной конечной влажностью брикетов (0,5% и 1–2%).
Поскольку результирующее воздействие выбранных факторов на механическую прочность брикетов в общем случае не равно сумме влияний каждого из них, проводят пробное брикетирование с учётом выбранных технологических факторов.
Опыт брикетирования мелкозернистых материалов показывает, что обязательным условием получения брикетов требуемого качества является строгое соблюдение технологического регламента, в том числе:
- безусловное выполнение установленного режима подготовки материала;
- соотношения количества материала и связующего, а также влажности;
- условий смешивания материала со связующим;
- соответствия производительностей дозатора материала и пресса;
- оптимального давления прессования;
- условий дозревания брикетов и их складирования [32].
7. Принципиальная технологическая схема процесса брикетирования
Критериями необходимости той или иной операции и отнесение её к той или иной стадии производства является требование достижения заданных показателей, характеристик и параметров обрабатываемого материала. Так, при подготовке сырья к прессованию, в качестве этих характеристик выступают влажность, фракционный состав, однородность смеси и др. При прессовании такими характеристиками служат плотность и прочность сырых брикетов, количество образующегося возврата, извлекаемость брикетов из пресс-формы и др. При упрочнении брикетов — прочность готовых брикетов, их остаточная влажность, наличие летучих веществ и др.
Кроме основных, непосредственно производственных операций, брикетирование включает подготовительно-заключительные операции, в частности, такие, как приёмка исходного сырья и отгрузка готовой продукции.
Процесс брикетирования металлургического сырья содержит ряд составляющих, элементов, операций, в той, или иной степени схожих с другими методами окускования — агломерацией и окатыванием. К таким составляющим, в первую очередь, относится подготовка сырья и элементы отгрузки готовой продукции, которые могут быть использованы и в брикетировании. Имеют сходство и отдельные процессы окускования, в основе которых лежат одни и те же процессы слипания и связывания частиц в прочный монолит[3].
Эта схожесть во многом определяется одинаковыми видами и свойствами исходного сырья, компонентным составом шихты, закономерностями формирования куска, наличием термообработки, требованиями к готовой продукции, её отгрузке и т.п. Эти операции во многом предопределяют условия подготовки сырья и могут быть использованы для производства брикетов практически в неизменном виде[3].
Использование максимально возможного количества известных процессов позволяет применять стандартное оборудование и типовые операции, что значительно упрощает технологию брикетирования, а также удешевляет капитальные и текущие затраты на строительство установки и её эксплуатацию.
Таким образом, технологический процесс брикетирования в общем виде состоит из трёх стадий (технологически связанных этапов, групп операций):
- подготовка сырья к брикетированию;
- прессование (формование) брикетов;
- упрочнение (сушка) брикетов.
Подготовка сырья к брикетированию включает следующие этапы:
- приёмка и складирование сырья;
- подготовка сырья к обработке;
- дозирование, смешивание и усреднение сырья;
- подготовка и ввод в шихту связующих.
Стадия прессования брикетов состоит из одного этапа — прессования брикетов (рис 7.1). В случае получения брикетов иным способом, чем прессование, применяют обобщающий термин — формование.
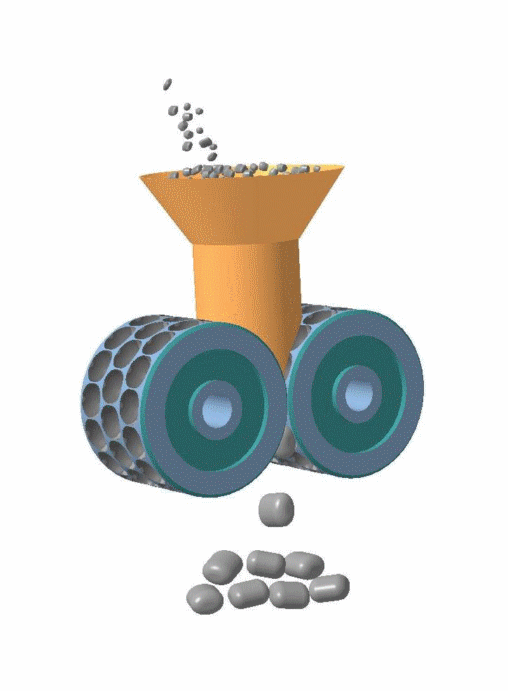
Рисунок 7.1 — Пример работы брикетного пресса
(8 картинок, 5 кадров/с, объем – 290кб)
Упрочнение брикетов включает следующие этапы:
- вылёживание;
- сушка и выдержка брикетов;
- упрочняющая обработка активными средами и материалами.
Упрочнение брикетов может осуществляться различными способами, из которых сушка вследствие своей высокой эффективности занимает превалирующее положение.
Отгрузка брикетов формально не относится к процессу брикетирования, однако правильная её организация способствует уменьшению потерь брикетов от разрушения при погрузочно-разгрузочных работах и транспортировке, поэтому данный этап подлежит регламентации.
Технологическая схема процесса брикетирования представлена на рис. 7.2.
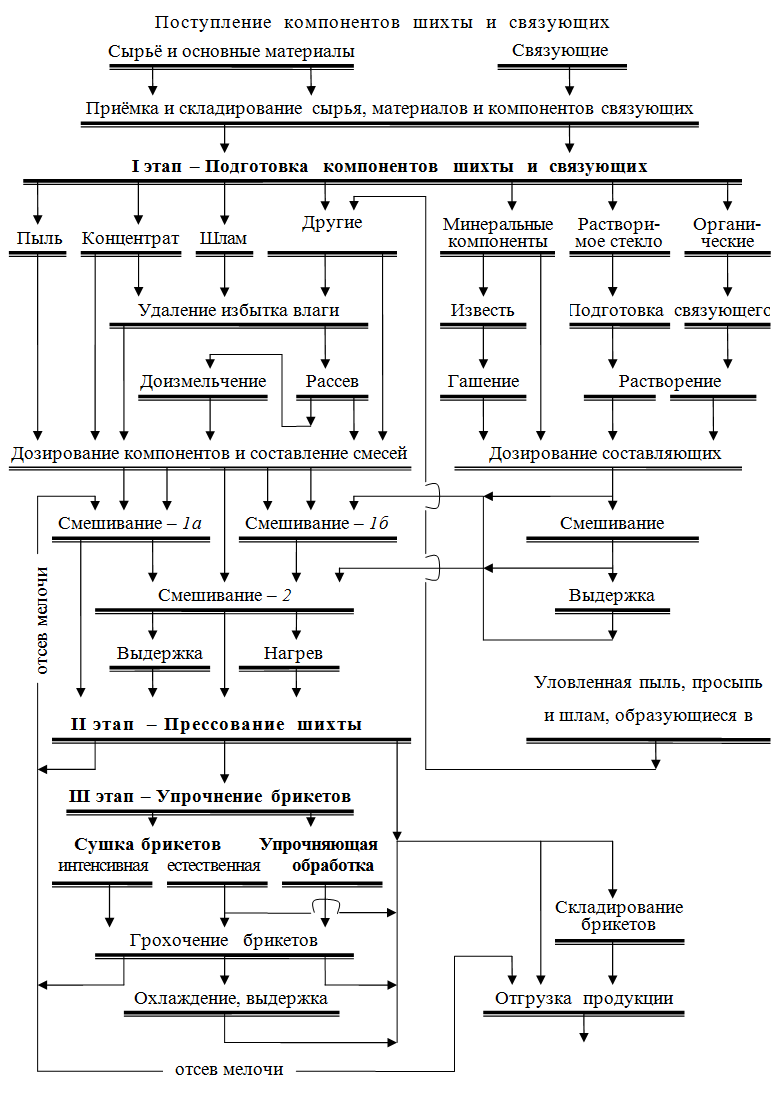
Рисунок 7.2 — Технологическая схема брикетирования сырья
Упрощённая схема цепи аппаратов установки брикетирования, соответствующая представленной на рис. 7.2 технологической схеме брикетирования металлургического сырья, изображена на рис. 7.3.
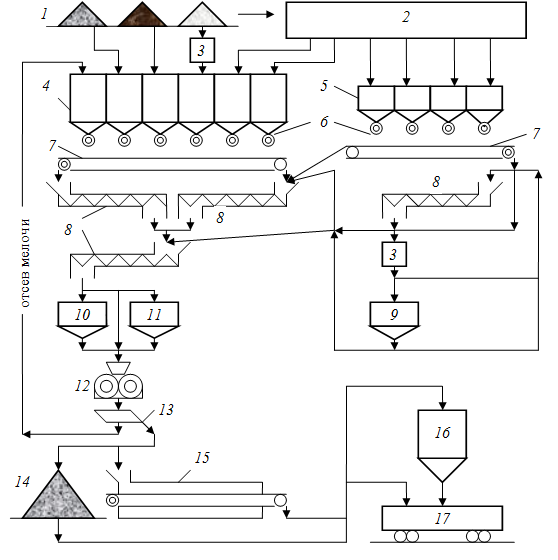
1 – открытый склад сырья; 2 – закрытый склад сырья, материалов и связующих; 3 – дробилки; 4 – бункеры для компонентов шихты; 5 – бункеры для компонентов связующих; 6 – дозаторы; 7 – сборный конвейер; 8 – смесители; 9 – устройство для гашения извести; 10 – бункер для выдержки шихты; 11 – нагревательное устройство; 12 – брикетный пресс; 13 – грохот; 14 – площадка для охлаждения и выдержки брикетов; 15 – ленточное сушило; 16 – бункер готовой продукции; 17 – железнодорожный вагон.
Рисунок 7.3 — Схема цепи аппаратов технологической линии для производства брикетов
Для проектирования установки брикетирования необходим подбор оборудования, выполняющего соответствующие технологические операции или группы операций, которое устанавливают в соответствии с технологической схемой в единый цикл. Так, операцию смешивания выполняют смесители различных типов, дозирование — дозаторы, прессование — брикетные прессы, сушку — сушильные печи и т.д.
Выбор того, или иного типа оборудования должен производиться по следующим критериям:
- пропускной способности (производительности) оборудования с учётом резерва мощности, позволяющей его эксплуатацию в щадящем режиме;
- обеспечения заданных характеристик и качества обработки сырья;
- минимизации капитальных и эксплуатационных затрат;
- минимальных габаритов, «вписывающихся» в здание;
- обеспечения экологических норм, нормативов охраны труда и др.
Окончательный выбор того или иного вида оборудования производят путём сопоставления его технических характеристик с соответствующими требованиями данной операции. Если эффективность работы выбранного типового оборудования вызывает сомнение, необходимо проведение опытного опробования и внесение необходимых изменений в конструкцию в процессе его изготовления у производителя.
Выводы
Повышенный интерес к брикетированию в настоящее время объясняется кризисным развитием экологической обстановки, в которую существенный негативный вклад вносит агломерация, постепенной выработкой месторождений качественной аглоруды, повышением доли тонкоизмельчённых концентратов, негативно влияющих на интенсивность агломерации. Уменьшение запасов коксующихся углей заставляет уделять всё большее внимание внедоменным методам получения железа, для которых брикетирование, наряду с окатыванием, может оказаться основным методом окускования [3].
Литературный и эксперементальный анализ отечественного и зарубежного опыта, показывает высокую эффективность брикетирования при его использовании не только в качестве основного, но и, особенно, в качестве вспомогательного метода окускования измельчённого металлургического сырья. Существенно увеличивается производительность металлургических агрегатов, экономится первичное сырьё, снижается расход энергоресурсов, повышается выход годного, улучшается качество металла. Снижается вредное воздействие на окружающую среду, отмечается рост и других технико–экономических показателей.
Изучение отечественного и зарубежного опыта получения и использования брикетов показывает, что в чёрной металлургии Украины, несмотря на рост потребности в новых материалах, брикетирование не находит должного внимания, которое оно по праву заслуживает.
Производственники и некоторые учёные-металлурги объясняют создавшееся положение различными объективными причинами, в т.ч. неудовлетворительной прочностью брикетов, недостаточным научным и производственным опытом их получения, отсутствием требуемого оборудования, низкой его эффективностью, нехваткой необходимой информации и т.п. Однако успешный зарубежный опыт использования брикетирования и полученные результаты, опровергают эти утверждения.
Поэтому разработка и внедрение передовых, энергосберегающих, эффективных технологий окускования железосодержащих отходов металлургического производства является перспективной и актуальной научно-практической задачей.
Список источников
- Банный Н.П. Экономика чёрной металлургии СССР / Н.П. Банный, А.А. Федотов, П.А. Ширяев и др. – М.: Металлургия, 1978. – 344 с.
- Равич Б.М. Брикетирование в цветной и чёрной металлургии / Б.М. Равич. – М.: Металлургия, 1975. – 232 с.
- Ожогин В.В. Основы теории и технологии брикетирования измельчённого металлургического сырья: Монография. – Мариуполь, ПГТУ, 2010. – 442 с
- Динельт В.М. Малооперационная технология получения брикетов из тонкодисперсных углеродистых материалов и отходов / В.М. Динельт, В.М. Левинец, М.С. Никишанин и др. // Изв. вузов: Чёрная металлургия. – 2007. – № 6. – С. 61-63.
- Фоменко А.И. Утилизация шламов металлургических производств / А.И. Фоменко // Изв. вузов: Чёрная металлургия. – 2001. – № 11. – С. 70-71.
- Барышников В.Г. Вторичные материальные ресурсы чёрной металлургии: Справочник. В 2-х т. Т. 2: Шлаки, шламы, отходы обогащения железных и марганцевых руд, отходы коксохимической промышленности, железный купорос / В.Г. Барышников, А.М. Горелов, Г.И. Папков и др. – М.: Экономика, 1986. – 344 с.
- Типовая технологическая инструкция о порядке учета образования и использования железосодержащих шламов (пылей) на металлургических предприятиях Минчермета СССР. ТТИ 2.2-08-02-81: Утв. Техн. упр. Минчермета СССР 26.06.81: Срок действия с 01.01.82 / Минчермет СССР. – Свердловск, 1982. – 32 с.
- Классен П.В. Гранулирование / П.В. Классен, И.Г. Гришаев, И.П. Шомин. – М.: Химия, 1991. – 320 с.
- Ефремов Г.И. Пылеочистка / Г.И. Ефремов, В.П Лукачевский. – М.: Химия, 1990. – 72 с.
- Гончаров Б.Ф. Технико-экономические расчеты по производству чугуна / Б.Ф. Гончаров, И.С. Соломахин. – Харьков: Вища школа, 1979. – 176 с.
- Вегман Е.Ф. Краткий справочник доменщика / Е.Ф. Вегман. – М.: Металлургия, 1981. – 240 с.
- Овчаренко Н.Л. Неполадки хода доменных печей / Н.Л. Овчаренко. – М.: Металлургия, 1972. – 192 с.
- Эсезобор Д.Э. Разработка малоотходной технологии аглодоменного производства: автореф. … дис. канд. техн. наук: 05.16.02. – Донецк, Донецкий госуд. техн. ун-т., 1994. – 20 с.
- Лурье Л.А. Брикетирование в чёрной и цветной металлургии / Л.А. Лурье. – М.: Металлургиздат, 1963. – 324 с.
- Политехнический словарь / Гл. ред. акад. А.Ю. Ишлинский. – 2-е изд. – М.: Советская энциклопедия, 1980. – 656 с
- Супрун Ю.М. Обезвоживание шламов металлургического производства на фильтр-прессах за рубежом / Ю.М. Супрун // Чёрная металлургия: Бюл. ин-та Черметинформация. – 1984. – № 5. – С. 14-23.
- Раджи О.И. Совершенствование технологии подготовки и утилизации металлургических шламов: автореф. дис. … канд. техн. наук: 05.16.02. – Донецк, ДНТУ, 2004. – 21 с.
- Волков Ю.П. Технолог-доменщик: Справочное и методическое руководство / Ю.П. Волков, Л.Я. Шпарбер, А.К. Гусаров. – М.: Металлургия, 1986. – 263 с.
- Воскобойников В.Г. Технология и экономика переработки железных руд / В.Г. Воскобойников, Л.П. Макаров. – М.: Металлургия, 1977. – 256 с.
- Ярхо Е.Н. Экономическая эффективность подготовки железных руд к плавке / Е.Н. Ярхо. – М.: Металлургия, 1974. – 96 с.
- Мироненко П.Ф. Методика металлургической оценки качества марганцевого сырья по его химическому составу / П.Ф. Мироненко, Ю.Б. Дедов, В.А. Гладких и др. // Сталь. – 2000. – № 8. – С. 29-31.
- Дударенко А.А. Концепция формализации управления качеством продукции по экономическому критерию / А.А. Дударенко, Т.А. Мазурова, А.Г. Чефранов // Теория и практика металлургии. – 1999. – № 6. – С. 60-64.
- Ожогин В.В. Комплексная оценка качества металлургического сырья / В.В. Ожогин, Н.С. Захаренко // Вестник Приазов. госуд. техн. ун-та: Сб. науч. тр. – Мариуполь. – 1999. – Вып. 8. – С. 254-256.
- Жак А.Р. Интегральные показатели металлургических свойств окускованного железорудного сырья / А.Р. Жак, Н.В. Ратников, Ю.С. Юсфин и др. // Сталь. – 1998. – № 3. – С. 10-13.
- Жак А.Р. Интегральные показатели химического состава окускованного железорудного сырья / А.Р. Жак, Н.В. Ратников, Ю.С. Юсфин и др. // Сталь. – 1998. – № 11. – С. 7-12
- Доменное производство: Справ. изд. В 2-х т. Т. 1. Подготовка руд и доменный процесс / Под ред. Вегмана Е.Ф. – М.: Металлургия. – 1989. – 496 с.
- Носков В.А. Перспектива подготовки и использования мелкофракционных железосодержащих отсевов сталеплавильных шлаков в доменной плавке / В.А. Носков, Н.М. Можаренко, Б.Н. Маймур // Металлург. и горноруд. пром-сть. – 2001. – № 1. – С. 119-121.
- Ожогин В.В. Брикетирование как полноправный метод окускования металлургического сырья / В.В. Ожогин, А.А. Томаш, И.А. Ковалевский и др. // Металлургические процессы и оборудование. – 2005. – Вып. 2. – С. 54-58.
- Ожогин В.В. Совершенствование ресурсосберегающей технологии получения и использования высокопрочных шламовых брикетов в аглодоменном производстве: дис. … канд. техн. наук: 05.16.02. – Мариуполь, ПГТУ, 2004. – 207 с.
- Словарь иностранных слов. – 18-е изд., стер. – М.: Рус. яз., 1989. – 624 с..
- Уманский Я.С. Рентгенография / Я.С. Уманский, А.К. Трапезников, А.И. Китайгородский и др. – М.: Машгиз, 1951. – 310 с.
- Бабанин В.И. Брикетирование мелкозернистых материалов в ферросплавном производстве: опыт и возможности / В.И. Бабанин, А.Я. Ерёмин // Металлург. – 2006. – 5. – С. 45-50.
- Большая Советская Энциклопедия. В 30 т. / Гл. ред. А.М. Прохоров. Изд. 3-е. – М.: Советская Энциклопедия, 1973 // Т. 8. Дебитор – Евкалипт. – 1972. – С. 172.
- Ожогин В.В. Дефекты брикетов и способы их устранения / В.В. Ожогин, И.А. Ковалевский, А.И. Ковалевский // Металург. процессы и оборудование. – 2008. – № 4. – С. 36-39.