Реферат по теме выпускной работы
Содержание
- Введение
- 1. Актуальность темы
- 2. Цель и задачи исследования
- 3. Анализ средств и способов добычи шлама из шламонакопителей
- 4. Исходные данные для расчета эрлифта ЭЗК
- 5. Приготовление и сжигание водоугольного топлива
- Выводы
- Список источников
Введение
В ближайшей перспективе прогнозируется повышение роли угля в топливно-энергетическом балансе Украины, что обусловлено его крупными запасами. Однако экологические ограничения (особенно после ратификации Киотского протокола) требуют разработки и внедрения новых экологически чистых угольных технологий, обеспечивающих высокую полноту использования топлива при максимально низкой вредной нагрузке на окружающую среду. Для Украины это может быть колоссальным дополнительным энергоресурсом. Для угольной энергетики принципиально важен переход от прямого сжигания угля в топочных устройствах к приготовлению из углей различных качеств, в том числе и из отходов углеобогащения, водоугольного топлива (ВУТ) [1].
В угольных объединениях Донбасса и Луганщины шламоотстойники занимают гектары земли, а объемы отходов угольного производства достигают 5–11 млн. тонн на объекте. При этом шламоотстойники являются точечной зоной
экологического бедствия и головной болью для владельцев угольных предприятий.
Идея водоугольного топлива далеко не нова. С начала 70 х годов прошлого века в ряде стран, в том числе в США, Канаде, Италии и Китае, ведутся работы по разработке технологий для производства добычи шлама из шламонакопителей и производству ВУТ.
1. Актуальность темы
В результате многолетней эксплуатации угледобывающих предприятий образовалось множество отстойников–шламонакопителей с огромными запасами полужидкой массы угольного шлама. На сегодняшний день возможности предприятий по организации расчистки шламонакопителей ограничены. В то же время эту проблему можно решить при наличии механизма быстрого изъятия большого количества угольного шлама и его дальнейшего эффективного использования. Проведенный в магистерской работе расчет ЭЗК с целью отыскания оптимальных параметров работы комплекса для добычи шлама из шламонакопителей может быть использован с целью более рационального использования энергетических, материальных и человеческих ресурсов. Поэтому разработка оптимальных параметров ЭЗК и дальнейшее ее совершенствование являются актуальными.
2. Цель и задачи исследования
Целью работы является определение рациональных параметров работы комплекса для добычи шлама из шламонакопителей и расчет методики ЭЗК с целью получения оптимальных параметров. Разработка технологии полного цикла добычи шлама, для приготовления и сжигания водоугольного толива на базе этих шламов. Для достижения указанной цели поставлены следующие задачи:
- Анализ литературы по данному вопросу.
- Составление математической модели для расчета ЭЗК.
- Разработка технологии добычи шламов из шламонакопителей.
- Исследование энергозатрат для данной технологии.
3. Анализ средств и способов добычи шлама из шламонакопителей
В результате длительной эксплуатации этих предприятий (десятки лет) на территории угольных районов Украины образовывались сотни отстойников, наполненных тонкозернистым шламом, запасы которого составляют более 100 миллионов тонн, содержащих примерно 15–20 % горючей массы.
Технология выемки из шламонакопителей может осуществляться различными способами.
Однако существует ряд объективных естественных, технических и организационных проблем, которые влияют на освоение ресурсов вторичного топлива.
На некоторых предприятиях уже ведется выемка и отгрузка потребителям забалансовых углесодержащих шламов.
В УкрНИИуглеобогащении разработана адаптивная схема технологического комплекса переработки шламов из илонакопителей с полной утилизацией продуктов, рассчитанная на производительность до 120 т/ч по исходному шламу (рис. 1).

Рисунок 1 – Адаптивная схема технологического комплекса для безотходной переработки шламов из илонакопителей
Ее основные особенности: универсальность, адаптивность, безотходность и замкнутость технологического цикла, что исключает потребность в дополнительной подпитке технической водой и сброс неочищенной шламовой воды во внешние водоемы.
В ДонГТУ была разработана технология добычи и гидротранспорта шлама из дальнего шламонакопителя ГОФ Красноармейская
с применением ЭЗК, который был спроектирован на базе серийного земснаряда типа 180–60, а так же ГОФ Октябрьская
, на базе специально спроектированного ЭЗК . На рис. 2 приведена гидравлическая схема ЭЗК, принцип действия которого заключается в следующем. Сжатый воздух от компрессора 1 через воздухопровод 17 поступает в смеситель, совмещенный в общий узел 22 со всасывающим устройством специальной конструкции (имеются соответствующие авторские свидетельства) для добычи шлама высокой концентрации, который перемещается как в одном, так и в другом направлении (без холостых перемещений). Гидросмесь (пульпа и воздух) по подъемному трубопроводу 16 поступает в воздухоотделитель 9 оригинальной конструкции, где происходит выделение воздуха в атмосферу, а пульпа по сливной трубе 10 опускается в промежуточную ёмкость 14, куда добавляется заборная вода и далее с помощью грунтонасоса 12 пульпа подается по пульповоду 13 на берег, а с берега углесосом транспортируется к обогатительной фабрике.
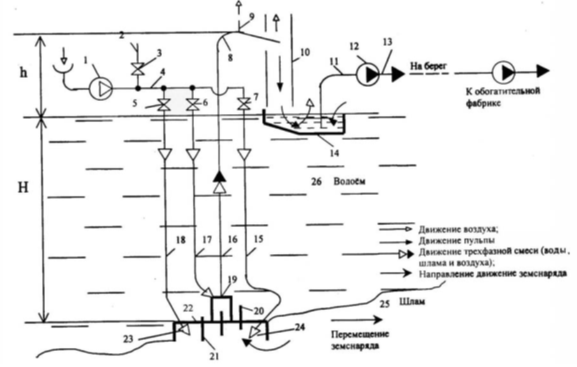
Рисунок 2 – Гидравлическая схема ЭЗК
Расчет и проектирование эрлифтов для ЭЗК приведен в монографиях [2, 3]. Высокая зольность мелкого угля из шламонакопителей обуславливает в ряде случаев необходимость его обогащения. Если обогатительная установка сооружается в непосредственной близости от шламонакопителя, то, учитывая ограниченность количества заскладированного в нем материала, она должна легко демонтироваться и перемещаться к другому месту.
4. Исходные данные для расчета эрлифта ЭЗК
Конструктивные элементы эрлифтов ЭЗК существенно отличаются от обычных стационарных эрлифтов, отличаются и условия работы, а, следовательно, расчет эрлифтов необходимо уточнить. Принцип работы эрлифта приведен на рис. 3.
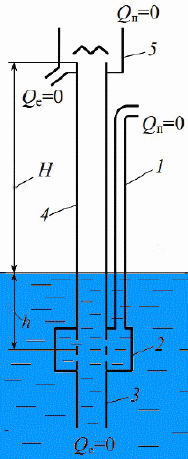
Рисунок 3 – Принцип работы эрлифта: 1 – воздухоподающая труба; 2 – смеситель; 3 – подводящая труба; 4 – подъёмная труба; 5 – воздухоотделитель (анимация: 9 кадров, 5 циклов повторения, 150 килобайт)
Ниже приведены отличительные особенности расчета эрлифта ЭЗК для условий работы в шламонакопителях [4–7].
Основными параметрами эрлифта являются: подача Qe, исчисляемая от нескольких м3/ч, до нескольких тысяч м3/ч, расход сжатого воздуха QВ, удельный расход воздуха

и диаметр подъемного трубопровода D. Между размерами q и α существует функциональная зависимость q =f(α) (рис. 4), экспериментально полученная в Донецком Политехническом Институте (ДПИ) и используемая для расчета эрлифтов.
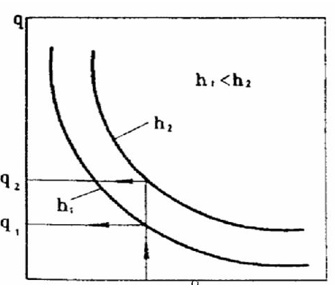
Рисунок 4 – Функциональная зависимость
Зависимость Qэ =f1(Qв) называется расходной характеристикой эрлифта (рис. 5).
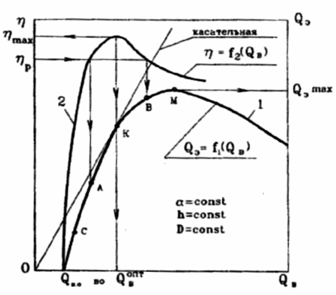
Рисунок 5 – Расходная (1) и энергетическая (2) характеристики эрлифта
Эта характеристика имеет несколько характерных точек. Начало подачи гидросмеси, при достижении определенного расхода воздуха Qв.о – оптимальная точка К, находится в месте соприкосновения касательной, проведенной из начала координат и соответствует максимальному КПД на энергетической η=f2(Qв) характеристике эрлифта. Точка М соответствует максимальной подаче (горбу), после которой идет снижение подачи эрлифта при увеличении расхода воздуха. Рабочая зона АВ соответствует оптимальному КПД, т. е. ηопт=0,85ηmax, где работа эрлифта экономически целесообразна.
5. Приготовление и сжигание водоугольного топлива
Тематика по ВУТ стала особенно популярной в 70-х годах прошлого века. Задача состояла в разработке технологий приготовления ВУТ такого качества, чтобы с наименьшими издержками можно было заменить им мазут в энергетических агрегатах. Проектировали также трубопроводное транспортирование ВУТ на дальнее расстояние. Разрабатывали технологию применения ВУТ в двигателях внутреннего сгорания (ДВС) и вместо угля в газогенераторах. Был также выполнен значительный объем работ по замене угля на ВУТ в тепловых котельных. Предполагали этим уменьшить объем вредных выбросов.
Нерентабельность ВУТ для угольных ТЭС и тепловых котельных следовало считать вполне ожидаемой. Затраты на приготовление и сжигание ВУТ по жидкостной схеме значительно превосходят затраты при слоевом и пылеугольном сжигании. В реальных условиях тепловые котельные необходимо было дооснастить установками приготовления, хранения и топливоподачи суспензии. Для этого нужны капитальные вложения и дополнительные производственные площади. Топливные тракты и форсунки также необходимо модернизировать.
Промышленная установка производства ВУТ в оптимальном по затратам ее варианте представляет собой помольный модуль, в который входят: дробилка и мельница с системой подачи и дозирования угля, система обеспыливания с рукавным фильтром и эксгаустером, циклоны для готовой угольной пыли и смесители для приготовления суспензии (рис. 4). Далее расположены устройство отбора готовой суспензии с металлоуловителем, пульповые насосы со смесителем и промежуточная емкость для готовой суспензии, второй насос подачи суспензии в форсунки. Для обеспечения факельного горения ВУТ необходимы форсунки, которые должны быть существенно более износостойкими, чем горелки, работающие на сухом угле.
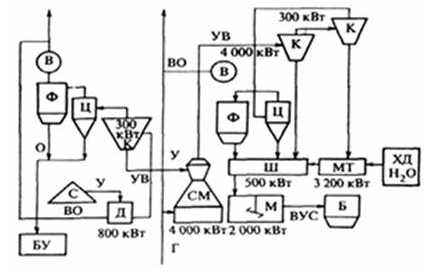
Рисунок 4 – Схема технологической линии приготовления ВУС с частичным обогащением угля. Расчетная производительность линии 400...500 т/ч. С – склад угля; Д – молотковая дробилка; К – классификатор; Ц – циклон; Ф – фильтр; В – вентилятор; СМ – среднеходная мельница; МТ – трубная мельница; ХД – резервуар для химической добавки; Ш – шнековый смеситель; М – лопастный смеситель; Б – хранилище суспензии; О – отходы углеобогащения; УВ – углевоздушный поток; У – уголь; ВО – воздушный поток; Г – топочный газ; БУ – блок утилизации отходов
На сухое измельчение угля до крупности, характеризуемой остатком на сите с ячейками размером 250 мкм менее 5 %, в современных молотковых и среднеходных мельницах затрачивается электроэнергии 12...15 кВт*ч/т. Затраты, обусловленные износом металла мелющих тел, не превышают затраты на электроэнергию. Восстановительная атмосфера практически исключает химическую коррозию. Затраты электроэнергии на приготовление ВУТ по наиболее примитивной (и потому наиболее применяемой) схеме (измельчение угля в составе суспензии) значительно превышают соответствующие затраты на сухое пылеприготовление до равной дисперсности. Они составляют не менее 25 кВт*ч/т. Обусловлено это высокой вязкостью суспензии, в которой затруднены движения мелющих тел и разрушение частиц угля. Механический и коррозионный износы мелющих тел в 3...5 раз (в зависимости от марки стали) превышают таковые при сухом измельчении. Приведенные затраты электроэнергии и металла относятся к технологии, в которой не предусмотрено транспортирования ВУТ по трубам. Для оптимизации вязкости и концентрации ВУТ, предназначенного для транспортирования, необходимо примерно треть угля измельчать до частиц менее 60 мкм, что в 3 раза повышает затраты на его приготовление. Для стабилизации применяют ПАВ, стоимость которых по удельному расходу сопоставима со стоимостью угля. При прямом приготовлении суспензий затрачиваемая мельницей электроэнергия (25 кВт*ч/т) трансформируется в тепло и расходуется в основном на испарение содержащейся в ВУТ воды. Согласно расчетам и экспериментальным данным, в процессе приготовления на 1 т ВУТ испаряется примерно 15 кг воды. При производительности мельницы, например, 3 т/ч за 1 ч ее работы испаряется 45 кг воды, за 1 сут – 1 т. Для предотвращения конденсации пара в помещении помольную установку необходимо оборудовать пароотводящей системой. В противоположность этому в машинах сухого пылеприготовления механическая энергия измельчения вместе с теплом подводимых к ним топочных газов полезно используется для подсушки угля. Пар удаляется системой аспирации помольной установки. Расходы на приготовление ВУТ по примитивной схеме (не считая стоимости входящей в него воды) несколько раз превышают расходы на пылеприготовление угля равной дисперсности (мельницы сухого измельчения работают с воздушной сепарацией частей по размерам, что почти в 2 раза снижает затраты энергии; износ мельниц сухого помола в несколько раз меньше). Они составляют не менее 12 % стоимости угля и существенную долю стоимости получаемой электроэнергии. Если ВУТ предназначено для транспортирования по трубам, затраты на его приготовление значительно увеличиваются. Процессу горения неизбежно предшествует полное испарение воды. Согласно теплотехническим расчетам при сжигании ВУТ на испарение воды затрачивается примерно 5 % входящего ВУТ угля (1 % на каждые 10 % воды). В соответствии с полученными во ВТИ экспериментальными данным при сжигании ВУТ температура горения примерно 150 °С ниже, механический и химический недожог минимум на 2...3 % больше, КПД котла на 2...5 меньше, чем при сжигании пылеугольного топлива.
Известны способы и устройства сжигания жидкого топлива, включая водоугольное топливо, обеспечивающие его распыл и вдув в топку за счет атмосферного воздуха, либо горячего воздуха, либо воздуха и горячих дымовых газов, воспламенение и стабилизацию горения с использованием тангенциальной закрутки потоков [7]. Указанные устройства имеют тот недостаток, что сочетания отдельных узлов не оптимизированы. В результате, режим работы котла недостаточно устойчив.
Выводы
В настоящее время при незначительной добыче угля и в связи с его низким качеством возникает дефицит энергетических и коксующихся углей. В связи с этим за последние несколько лет в Украине резко возрос интерес к переработке вторичного сырья, содержащегося в шламоотстойниках и илонакопителях, которые, по сути, являются техногенными месторождениями. Это обусловлено рядом причин:
- Высокое содержание горючей массы – до 20 % и даже более.
- Несложность добычи сырья и его невысокая себестоимость.
- Критическое состояние большинства действующих илонакопителей, что значительно усложняют работу ОФ.
Вторичная переработка отходов углеобогащения важна не только для увеличения резервов топлива, но и для сокращения нерационального отчуждения земельных ресурсов, снижения эксплуатационных затрат на содержание отстойников, для защиты от загрязнений водного и воздушного бассейна.
К данному вопросу проявляют повышенное внимание не только предприятия угольной промышленности – истинные владельцы ресурсов, но и различные коммерческие структуры, индивидуальные предприниматели.
Эрлифтно-земснарядные комплексы (ЭЗК), по сравнению с традиционными земснарядами, имеют более высокую производительность, меньшую трудоемкость и стоимость добычи, обеспечивают возможность разработки ископаемых на глубине нескольких сотен метров, в том числе и из-под слоя пород, и работу грунтового насоса с постоянной высокой концентрацией пульпы.
Эрлифт не имеет движущихся или быстро изнашивающихся частей, не требует постоянного наблюдения и обслуживания, как того требует грунтовой центробежный насос, простой и недорогой в изготовлении.
Опыт эксплуатации эрлифтно-земснарядных комплексов по добыче песка из рек и водоемов Западной Сибири (Россия), разработанных на кафедре ЭМС ДонНТУ, показал их исключительные преимущества перед обычными землесосными снарядами. Невзирая на несколько (около 20%) больший расход электроэнергии или дизтоплива, себестоимость добытого ими материала ниже, чем для земснаряда, за счет более высокой концентрации получаемой гидросмеси, стабильной и безаварийной работы комплекса. Кроме этого, комплекс имеет во много раз большую глубину разработки – до 120 м, что позволяет вести разработку в таких условиях, в которых обычный земснаряд работать не способен. Есть опыт эксплуатации эрлифтно-земснарядного комплекса в зимних условиях, а также при расположении его в предельно малом по глубине и пространстве водоеме (в болотных условиях). В эрлифтно-земснарядном комплексе обеспечиваются благоприятные условия работы для работы грунтонасоса, в который подается подготовленная гидросмесь с постоянно высокой концентрацией, которая не содержит большие куски твердого материала; насос работает с небольшим разрежением во всасывающем патрубке, что значительно снижает вероятность работы в кавитационном режиме.
Учитывая преимущества эрлифтно-земснарядного комплекса, целесообразно использовать его для очистки от ила дна внутренних водоемов, вместо земснаряда.
При написании данного реферата магистерская работа еще не завершена. Окончательное завершение: декабрь 2015 года. Полный текст работы и материалы по теме могут быть получены у автора или его руководителя после указанной даты.
Список источников
- Бойко М. Г., Козиряцький Л. М., Кононенко А. П. Землесосні та ерліфтно–землесосні снаряди: Навч. посібник / М. Г. Бойко, Л. М. Козиряцький, А. П. Кононенко. – Донецьк: ДонНТУ, 2005. – 296 с.
- Антонов Я. К., Козыряцкий Л. Н., Малашкина В. А. и др. Гидроподъем полезных ископаемых / Я. К. Антонов, Л. Н. Козыряцкий. – М: Недра, 1995. – 225 с.
- Гидроподъем полезных ископаемых /Антонов Я. К., Козыряцкий Л. Н., Пащенко B. C., Малашкина В. А. и др. – М.: Недра, 1995. – 173 с.
- Эрлифтные установки /Гейер В. Г., Козыряцкий Л. Н., Пащенко B. C., Антонов Я. К. – Донецк: ДПИ, 1982. – 64 с.
- Эрлифтно-земснарядные комплексы для добычи песка / Холмогоров А. П., Козыряцкий Л. Н., Антонов Я. К. // Строительство трубопроводов. – 1988. – № 5
- Эксплуатация Эрлифтно-земснарядных комплексов в Западной Сибири / Холмогоров А. П., Козьряцкий Л. Н. и др. // Строительство трубопроводов. – 1990. – № 4.
- Зайденварг В. Е., Трубецкой К. Н., Мурко В. И., Нехороший И. Х. Производство и использование водоугольного топлива / В. Е. Зайденварг. – М.: Изд-во Акад. Горных наук, 2001. – 176 с.