Реферат за темою випускної роботи
Зміст
- Вступ
- 1. Актуальнiсть теми
- 2. Мета і завдання дослідження
- 3. Аналіз засобів і способів видобутку шламу з шламонакопичувачів
- 4. Вихідні дані для розрахунку ерліфта ЕЗК
- 5. Приготування і спалювання водовугільного палива
- Висновки
- Перелiк посилань
Вступ
У найближчій перспективі прогнозується підвищення ролі вугілля в паливно-енергетичному балансі України, що зумовлено його великими запасами. Однак екологічні обмеження (особливо після ратифікації Кіотського протоколу) вимагають розробки і впровадження нових екологічно чистих вугільних технологій, що забезпечують високу повноту використання палива при максимально низькому шкідливому ??навантаженнюю на навколишнє середовище. Для України це може бути колосальним додатковим енергоресурсом. Для вугільної енергетики принципово важливий перехід від прямого спалювання вугілля в топкових пристроях до приготування з вугілля різних якостей, у тому числі і з відходів вуглезбагачення, водовугільного палива (ВВП) [1].
У вугільних об’єднаннях Донбасу і Луганщини шламовідстійники займають гектари землі, а обсяги відходів вугільного виробництва досягають 5–11 млн. тонн на об’єкті. При цьому шламовідстійники є точковою зоною
екологічного лиха і головним болем для власників вугільних підприємств.
Ідея водовугільного палива далеко не нова. З початку 70 х років минулого століття в ряді країн, у тому числі в США, Канаді, Італії та Китаї, ведуться роботи по розробці технологій для виробництва, видобутку шламу з шламонакопичувачів та виробництва ВВП.
1. Актуальність теми
В результаті багаторічної експлуатації вугледобувних підприємств утворилося безліч відстійників – шламонакопичувачів з величезними запасами напiврiдкої маси вугільного шламу. На сьогоднішній день можливості підприємств щодо організації розчищення шламонакопичувачів обмежені. У той же час цю проблему можна вирішити за наявності механізму швидкого вилучення великої кількості вугільного шламу та його подальшого ефективного використання. Проведений в магістерській роботі розрахунок ЕЗК з метою відшукання оптимальних параметрів роботи комплексу для видобутку шламу з шламонакопичувачів може бути використаний з метою більш раціонального використання енергетичних, матеріальних та людських ресурсів. Тому розробка оптимальних параметрів ЕЗК і подальше її вдосконалення є актуальними.
2. Мета і завдання дослідження
Метою роботи є визначення раціональних параметрів роботи комплексу для видобутку шламу з шламонакопичувачів і розрахунок методики ЕЗК з метою отримання оптимальних параметрів. Розробка технології повного циклу видобутку шламу, для приготування та спалювання водовугільного толіва на базі цих шламів. Для досягнення зазначеної мети поставлені наступні завдання:
- Аналіз літератури з даного питання.
- Складання математичної моделі для розрахунку ЕЗК.
- Розробка технології видобутку шламів з шламонакопичувачів.
- Дослідження енерговитрат для даної технології.
3. Аналіз засобів і способів видобутку шламу з шламонакопичувачів
В результаті тривалої експлуатації цих підприємств (десятки років) на території вугільних районів України утворювалися сотні відстійників, наповнених тонкозернистим шламом, запаси якого становлять понад 100 мільйонів тонн, що містять приблизно 15-20 % горючої маси.
Технологія виїмки з шламонакопичувачів може здійснюватися різними способами.
Однак існує ряд об’єктивних природних, технічних і організаційних проблем, які впливають на освоєння ресурсів вторинного палива.
На деяких підприємствах вже ведеться виїмка і відвантаження споживачам позабалансових углевмістких шламів.
У УкрНДІвуглезбагачення розроблена адаптивна схема технологічного комплексу переробки шламів з мулонакопичувачів з повною утилізацією продуктів, розрахована на продуктивність до 120 т/год по вихідному шламу (рис. 1).

Рисунок 1 – Адаптивна схема технологічного комплексу для безвідходної переробки шламів з мулонакопичувачів
Її основні особливості: універсальність, адаптивність, безвідходність і замкнутість технологічного циклу, що виключає потребу додаткового підживлення технічною водою і скидання неочищеної шламової води в зовнішні водойми.
У ДонДТУ була розроблена технологія видобутку і гідротранспорту шламу з далекого шламонакопичувача ГЗФ Червоноармійська
із застосуванням ЕЗК, який був спроектований на базі серійного земснаряду типу 180-60, а так само ГЗФ Жовтнева
, на базі спеціально спроектованого ЕЗК. На рис. 2 наведена гідравлічна схема ЕЗК, принцип дії якого полягає в наступному. Стисле повітря від компресора 1 через повітропровід 17 поступає в змішувач, поєднаний в загальний вузол 22 зі всмоктуючим пристроєм спеціальної конструкції (є відповідні авторські свідоцтва) для видобутку шламу високої концентрації, який переміщується як в одному, так і в іншому напрямку (без неодружених переміщень). Гідросуміш (пульпа і повітря) по підйомному трубопроводу 16 надходить в воздуховiддiльник 9 оригінальної конструкції, де відбувається виділення повітря в атмосферу, а пульпа по зливнiй труби 10 опускається в проміжну ємність 14, куди додається заборна вода і далі за допомогою грунтонасоса 12 пульпа подається по пульповодах 13 на берег, а з берега вуглесосами транспортується до збагачувальної фабрики.
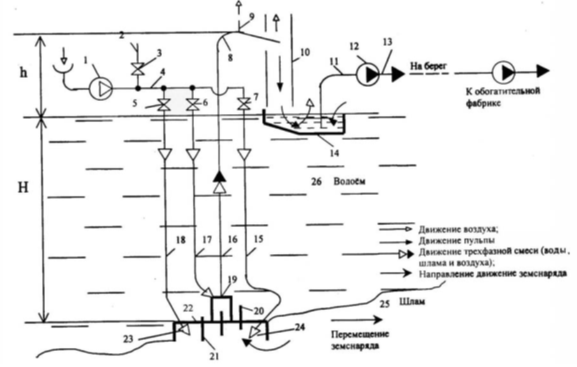
Рисунок 2 – Гідравлічна схема ЕЗК
Розрахунок і проектування ерліфтів для ЕЗК наведено в монографіях [ 2 , 3 ]. Висока зольність дрібного вугілля з шламонакопичувачів обумовлює в ряді випадків необхідність його збагачення. Якщо збагачувальна установка споруджується в безпосередній близькості від шламонакопичувача, то, враховуючи обмеженість кількості заскладованого в ньому матеріалу, вiн повинен легко демонтуватися і переміщатися до іншого місця.
4. Вхідні дані для розрахунку ерліфта ЕЗК
Конструктивні елементи ерліфтів ЕЗК істотно відрізняються від звичайних стаціонарних ерліфтів, відрізняються і умови роботи, а, отже, розрахунок ерліфтів необхідно уточнити. Принцип роботи ерліфта наведено на рис. 3.
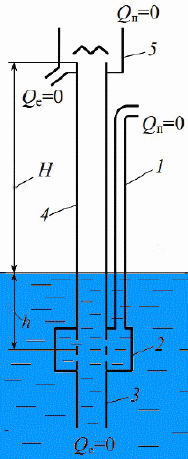
Рисунок 3 – Принцип роботи ерліфта: 1 – повітроподавальна труба; 2 – змішувач; 3 – труба, що підводить; 4 – підйомна труба; 5 – воздуховiддiльник (анімація: 9 кадрів, 5 циклів повторення, 150 кілобайт)
Нижче наведені відмінні риси розрахунку ерліфта ЕЗК для умов роботи в шламонакопичувачах [4–7].
Основними параметрами ерліфта є: подача Qe, обрахована від декількох м3/ч, до декількох тисяч м3/ч, витрата стисненого повітря QВ, питома витрата повітря

і діаметр підйомного трубопроводу D. Між розмірами q і α існує функціональна залежність q = f(α) (рис. 4), експериментально отримана в Донецькому Політехнічному Інституті (ДПІ) і використовується для розрахунку ерліфтів.
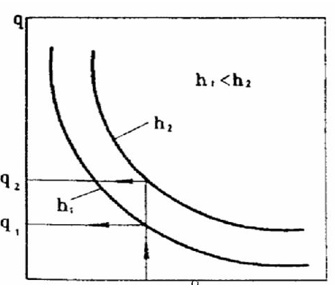
Рисунок 4 – Функціональна залежність
Залежність Qэ =f1(Qв) називається видатковою характеристикою ерліфта (рис. 5).
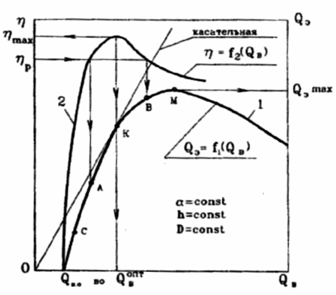
Рисунок 5 – Видаткова (1) та енергетична (2) характеристики ерліфта
Ця характеристика має кілька характерних точок. Початок подачі гідросуміші, при досягненні певного витрати повітря Qв.о – оптимальна точка К, знаходиться в місці зіткнення дотичної, проведеної з початку координат і відповідає максимальному ККД на енергетичній η=f2(Qв) характеристиці ерліфта. Точка М відповідає максимальній подачі (горбу), після якої йде зниження подачі ерліфта при збільшенні витрати повітря. Робоча зона АВ відповідає оптимальному ККД, тобто ηопт=0,85ηmax, де робота ерліфта економічно доцільна.
5. Приготування і спалювання водовугільного палива
Тематика по ВВП стала особливо популярною в 70-х роках минулого століття. Завдання полягало в розробці технологій приготування ВВП такої якості, щоб з найменшими витратами можна було замінити їм мазут в енергетичних агрегатах. Проектували також трубопровідне транспортування ВВП на далеку відстань. Розробляли технологію застосування ВВП в двигунах внутрішнього згоряння (ДВЗ) і замість вугілля в газогенераторах. Був також виконаний значний обсяг робіт по заміні вугілля на ВВП в теплових котелень. Припускали цим зменшити обсяг шкідливих викидів.
Нерентабельність ВВП для вугільних ТЕС і теплових котелень слід було вважати цілком очікуваною. Витрати на приготування і спалювання ВВП за рідинною схемою значно перевершують витрати при шаровому і пиловугільному спалюванні. У реальних умовах теплові котельні необхідно було дооснастити установками приготування, зберігання та паливоподачі суспензії. Для цього потрібні капітальні вкладення і додаткові виробничі площі. Паливні тракти і форсунки також необхідно модернізувати.
Промислова установка виробництва ВВП в оптимальному за витратами її варіанті являє собою помольний модуль, до якого входять: дробарка і млин з системою подачі і дозування вугілля, система знепилювання з рукавним фільтром і ексгаустером, циклони для готового вугільного пилу та змішувачі для приготування суспензії (рис. 4). Далі розташовані пристрій відбору готової суспензії з металлоуловітелем, пульповий насос зі змішувачем і проміжна ємність для готової суспензії, другий насос подачі суспензії в форсунки. Для забезпечення факельного горіння ВВП необхідні форсунки, які повинні бути істотно більш зносостійкими, ніж пальники, що працюють на сухому вугіллі.
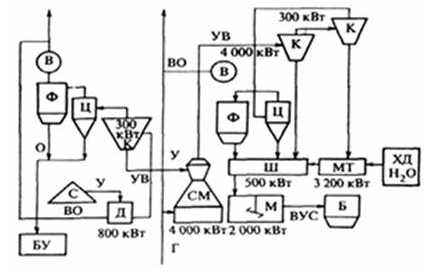
Рисунок 4 – Схема технологічної лінії приготування ВВП з частковим збагаченням вугілля. Розрахункова продуктивність лінії 400 ... 500 т / год. З – склад вугілля; Д – молоткова дробарка; До – класифікатор; Ц – циклон; Ф – фільтр; В – вентилятор; СМ – середньоходовими млин; МТ – трубна млин; ХД – резервуар для хімічної добавки; Ш – шнековий змішувач; М – лопатевий змішувач; Б – сховище суспензії; Про – відходи вуглезбагачення; УВ – углевоздушний потік; У – вугілля; ВО – повітряний потік; Г – топковий газ; БО – блок утилізації відходів
На сухе подрібнення вугілля до крупності, яка характеризується залишком на ситі з осередками розміром 250 мкм менше 5 %, в сучасних молоткових і середньоходовими млинах витрачається електроенергії 12...15 кВт*год/т. Витрати, обумовлені зносом металу мелють тел, не перевищують витрати на електроенергію. Відновлювальна атмосфера практично виключає хімічну корозію. Витрати електроенергії на приготування ВВП за найбільш примітивною (і тому найбільш вживаною) схемою (подрібнення вугілля в складі суспензії) значно перевищують відповідні витрати на сухе пилепріготовленія до рівної дисперсності. Вони становлять не менше 25 кВт*год/т. Обумовлено це високою в’язкістю суспензії, в якій утруднені рухи тіл, що мелють і руйнування часток вугілля. Механічний і корозійний знос тіл, що мелють в 3...5 разів (залежно від марки сталі) перевищують такі при сухому подрібненні. Наведені витрати електроенергії і металу відносяться до технології, в якій не передбачено транспортування ВВП по трубах. Для оптимізації в’язкості і концентрації ВВП, призначеного для транспортування, необхідно приблизно третина вугілля подрібнювати до часток менше 60 мкм, що в 3 рази підвищує витрати на його приготування. Для стабілізації застосовують ПАВ, вартість яких по питомій витраті порівнянна з вартістю вугілля. При прямому приготуванні суспензій затрачиваемая млином електроенергія (25 кВт*год/т) трансформується в тепло і витрачається в основному на випаровування міститься в ВВП води. Згідно з розрахунками і експериментальними даними, в процесі приготування на 1 т ВВП випаровується приблизно 15 кг води. При продуктивності млина, наприклад, 3 т/год за 1 год її роботи випаровується 45 кг води, за 1 добу – 1 т. Для запобігання конденсації пари в приміщенні помольну установку необхідно обладнати паровідвідна системою. На противагу цьому в машинах сухого пилепріготовленія механічна енергія подрібнення разом з теплом підводяться до них топкових газів корисно використовується для підсушування вугілля. Парвіддаляється системою аспірації помольної установки. Витрати на приготування ВВП за примітивною схемою (не рахуючи вартості входить до нього води) кілька разів перевищують витрати на пилепріготовленія вугілля рівній дисперсності (млини сухого подрібнення працюють з повітряної сепарацией частин за розмірами, що майже в 2 рази знижує витрати енергії; знос млинів сухого помелу в кілька разів менше). Вони становлять не менше 12 % вартості вугілля і істотну частку вартості одержуваної електроенергії. Якщо ВВП призначено для транспортування по трубах, витрати на його приготування значно збільшуються. Процесу горіння неминуче передує повне випаровування води. Згідно теплотехнічних розрахунках при спалюванні ВВП на випаровування води витрачається приблизно 5 % вхідного ВВП вугілля (1 % на кожні 10 % води). Відповідно до отриманих під ОТІ експериментальними даними при спалюванні ВВП температура горіння приблизно 150 °С нижче, механічний і хімічний недожог мінімум на 2...3 % більше, ККД котла на 2...5 % менше, ніж при спалюванні пиловугільного палива.
Відомі способи і пристрої спалювання рідкого палива, включаючи водовугільне паливо, що забезпечують його розпил та вдув в топку за рахунок атмосферного повітря, або гарячого повітря, або повітря і гарячих димових газів, займання і стабілізацію горіння з використанням тангенциальной закрутки потоків [7]. Зазначені пристрої мають той недолік, що поєднання окремих вузлів не оптимізоване. В результаті, режим роботи котла недостатньо стійкий.
Висновки
В даний час при незначній видобутку вугілля та у зв’язку з його низькою якістю виникає дефіцит енергетичного і коксівного вугілля. У зв’язку з цим за останні кілька років в Україні різко зріс інтерес до переробки вторинної сировини, що міститься в шламовідстійниках і мулонакопичувачах, які, по суті, є техногенними родовищами. Це обумовлено рядом причин:
- Високий вміст горючої маси – до 20 % і навіть більше.
- Нескладність видобутку сировини та її невисока собівартість.
- Критичний стан більшості діючих мулонакопичувачів, що значно ускладнюють роботу ОФ.
Вторинна переробка відходів вуглезбагачення важлива не тільки для збільшення резервів палива, але і для скорочення нераціонального відчуження земельних ресурсів, зниження експлуатаційних витрат на утримання відстійників, для захисту від забруднень водного і повітряного басейну.
До даного питання проявляють підвищену увагу не тільки підприємства вугільної промисловості – істинні власники ресурсів, але і різні комерційні структури, індивідуальні підприємці.
Ерліфтної-земснаряднi комплекси (ЕЗК), в порівнянні з традиційними земснарядами, мають більш високу продуктивність, меншу трудомісткість і вартість видобутку, забезпечують можливість розробки копалин на глибині декількох сотень метрів, у тому числі і з-під шару порід, і роботу грунтового насоса з постійною високою концентрацією пульпи.
Ерліфт не має рухомих або швидко зношуючихся частин, не вимагає постійного спостереження і обслуговування, як того вимагає грунтовий відцентровий насос, простий і недорогий у виготовленні.
Досвід експлуатації ерліфтно-земснарядних комплексів з видобутку піску з річок і водойм Західного Сибіру (Росія), розроблених на кафедрі ЕМС ДонНТУ, показав їх виняткові переваги перед звичайними землесосними снарядами. Незважаючи на кілька (близько 20 %) більшу витрату електроенергії або дизпалива, собівартість видобутого ними матеріалу нижче, ніж для земснаряду, за рахунок більш високої концентрації одержуваної гідросуміші, стабільної та безаварійної роботи комплексу. Крім цього, комплекс має у багато разів більшу глибину розробки – до 120 м, що дозволяє вести розробку в таких умовах, в яких звичайний земснаряд працювати не здатний. Є досвід експлуатації ерліфтної-земснарядного комплексу в зимових умовах, а також при розташуванні його в гранично малому по глибині і просторі водойму (у болотних умовах). У ерліфтно-земснарядному комплексі забезпечуються сприятливі умови роботи для роботи грунтонасоса, до якого подається підготовлена ??гідросуміш з постійно високою концентрацією, яка не містить великі шматки твердого матурiалу; насос працює з невеликим розрідженням у всмоктуючому патрубку, що значно знижує ймовірність роботи в кавітаційному режимі.
Враховуючи переваги ерліфтно-земснарядного комплексу, доцільно використовувати його для очищення від мулу дна внутрішніх водойм, замість земснаряда.
При написанні даного реферату магістерська робота ще не завершена. Остаточне завершення: грудень 2015 року. Повний текст роботи та матеріали по темі можуть бути отримані у автора або його керівника після зазначеної дати.
Список источников
- Бойко М. Г., Козиряцький Л. М., Кононенко А. П. Землесосні та ерліфтно–землесосні снаряди: Навч. посібник / М. Г. Бойко, Л. М. Козиряцький, А. П. Кононенко. – Донецьк: ДонНТУ, 2005. – 296 с.
- Антонов Я. К., Козыряцкий Л. Н., Малашкина В. А. и др. Гидроподъем полезных ископаемых / Я. К. Антонов, Л. Н. Козыряцкий. – М: Недра, 1995. – 225 с.
- Гидроподъем полезных ископаемых /Антонов Я. К., Козыряцкий Л. Н., Пащенко B. C., Малашкина В. А. и др. – М.: Недра, 1995. – 173 с.
- Эрлифтные установки /Гейер В. Г., Козыряцкий Л. Н., Пащенко B. C., Антонов Я. К. – Донецк: ДПИ, 1982. – 64 с.
- Эрлифтно-земснарядные комплексы для добычи песка / Холмогоров А. П., Козыряцкий Л. Н., Антонов Я. К. // Строительство трубопроводов. – 1988. – № 5
- Эксплуатация Эрлифтно-земснарядных комплексов в Западной Сибири / Холмогоров А. П., Козьряцкий Л. Н. и др. // Строительство трубопроводов. – 1990. – № 4.
- Зайденварг В. Е., Трубецкой К. Н., Мурко В. И., Нехороший И. Х. Производство и использование водоугольного топлива / В. Е. Зайденварг. – М.: Изд-во Акад. Горных наук, 2001. – 176 с.