Реферат за темою випускної роботи
Зміст
- Вступ
- 1. Актуальність теми
- 2. Мета і задачі роботи та заплановані результати
- 3. Технологія мембранного розділення газів
- 3.1 Принцип розділення газів
- 3.2 Класифікація мембранних повітророздільних установок
- 3.3 Аналіз мембранної установки отримання азоту
- 4. Порівняльний аналіз адсорбційного і мембранного способів промислового виробництва азоту
- Висновки
- Перелік посилань
Вступ
Впровадженню мембранного методу розділення газів у промисловості сприяли результати вивчення явищ, пов'язаних з селективним перенесенням молекул газів через суцільні (гомогенні) і мікропористі мембрани, які мають неорганічну або полімерну природу; успіхи в синтезі полімерів з газороздільними властивостями; розробка методів отримання високопродуктивних (асиметричних, композиційних, напилених і т. д.) полімерних, металевих і керамічних мембран, створення конструкцій та й методів розрахунку мембранних апаратів і установок.
Перспективи застосування мембранного розділення газів в хімічній промисловості визначаються, перш за все, простотою апаратурного оформлення процесу, безреагентністью, економічністю, тривалою роботою газороздільних мембран при незмінних їх характеристиках, можливістю повної автоматизації установок і т. п.
Мембранне розділення газів використовують в технології переробки природних газів, збагачення повітря киснем, концентрування водню продувних газів синтезу аміаку, для створення регульованого газового середовища при зберіганні сільськогосподарської продукції та багатьох інших цілей. Також перспективним є використання мембранного газорозділення для очищення вихідних газів.
1. Актуальність теми
Атмосферне повітря являється сировиною для отримання таких промислових газів, як кисень, азот, аргон, неон, криптон, ксенон. Темпи щорічного приросту виробництва цих газів в світі в 1,2–1,4 рази перевищують приріст будь-яких інших видів продукції. Промислове виробництво цих газів здійснюється на повітророздільних установках (ПРУ). Існує три основних способи розділення повітря: кріогенний, адсорбційний та мембранний [1].
На відміну від мембранних повітророздільних установок, криогенні і адсорбційні ПРУ представляють собою складні технічні системи, що включають в собі: обладнання для стиснення атмосферного повітря, його очищення від вологи, двоокису вуглецю, вибухонебезпечних домішок; теплообмінні апарати для охолодження повітря до кріогенних температур і нагрівання продуктів розділення; ректифікаційні колони і конденсатори-випарники; криогенні насоси тощо [2].
Мембранні процеси розділення газових сумішей відносяться до нових технологічних процесів, які в даний час знаходять все більш широке застосування в різних галузях промисловості. У технологічному відношенні організація процесу розділення на мембранах відрізняється простотою і широко застосовується на практиці.
2. Мета і задачі роботи та заплановані результати
Мета роботи полягає в обґрунтуванні раціонального апаратурного оформлення мембранної установки, що забезпечує при заданій продуктивності досягнення необхідної чистоти кінцевих продуктів розділення повітря (азоту і кисню) при мінімізації енерго-, і матеріалоспоживання.
Задачі, які вирішуються для досягнення зазначеної мети:
- Аналіз теоретичних основ розділення газів в мембранному елементі.
- Обгрунтування конструкції мембранного модуля, типу і матеріалу використовуваних мембран.
- Розробка математичної моделі, яка описує роботу мембранного модуля.
- Аналіз впливу різних факторів на ефективність мембранного процесу розділеня повітря і використання цього аналізу для обґрунтування вибору допоміжного обладнання.
- Техніко-економічне обґрунтування технічних рішень.
Об'єкт дослідження: процес мембранного розділення повітря.
Предмет дослідження: аппаратурне оформлення процесу мембранного розділення повітря.
Можливі результати, які очікуються при виконанні роботи, їх новизна та значення:
Наукова новизна роботи полягає в розробці алгоритму обґрунтування апаратурного оформлення процесу мембранного розділення повітря на основі аналізу різних схем взаємодії мембранних модулей і аналізу впливу різних чинників на ефективність процесу.
Практичне значення роботи полягає у використанні результатів роботи для зниження енерго-, і матеріалоспоживання при прийнятті проектних рішень і промисловому впровадженню установок для розділення повітря.
3. Технологія мембранного розділення газів
3.1 Принцип розділення газів
Розділення повітря на мембрані може відбуватися як без хімічних перетворень, так і з хімічними перетвореннями за допомогою введених в мембрану каталізаторів і ферментів. У якості мембран використовують полімерні плівки, тонкі металеві або керамічні пластини, шар рідини і т. д. Мембранний модуль (рис. 3.1) забезпечує розділення вихідного потоку F на два: пермеат V проходить через мембрану, а відхідний потік (ретант) L подається на наступну ступінь розділення або скидається. У технологічному відношенні організація процесу розділення на мембранах характеризується простотою і широко застосовується на практиці, наприклад при отриманні з повітря азоту та кисню [3].
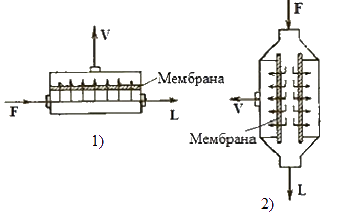
1 — плоскокамерний; 2 — трубчатий
Рисунок 3.1 — Схеми мембранних модулей
Перенесення речовини через мембрану здійснюється під дією полей потенціалів різної природи (полей тиску, температури, концентрації, гравітації, електромагнітної природи та ін.). Потоки речовини через мембрану бувають дифузійними, осмотичними, іонними, електрофоретичний і т. п. Масовий потік в мембрані орієнтований по нормалі до розділяємої поверхні. Рушійна сила перенесення компонента визначається різницею хімічних потенціалів в напірному і дренажному каналах, розділених мембраною. Швидкість масопереносу через мембрану змінюється по довжині мембранного елемента і залежить від термо- і гідродинамічних параметрів в даній точці напірного або дренажного каналу [3].
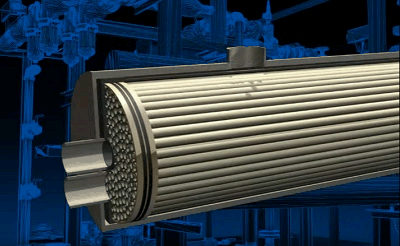
Рисунок 3.2 — Процес розділення повітря у трубчатому модулі
анімація: 4 кадра, 6 циклів повторення, 143 кілобайт
Під час опису процесів масопереносу через пористу мембрану часто використовують різні моделі течій як вузького, так і молекулярного потоку. Структура пір мембрани складна, а часто й невідома, тому для правильного застосування рівнянь течії газів при розрахунку процесів мембранного розділення необхідно враховувати структуру та розмір пор (еквівалентний діаметр, довжину каналу, питому площу поверхні, розподіл пор за розмірами та ін.). Для вузького потоку розмір пор повинен бути досить великий у порівнянні з довжиною вільного шляху молекул газу [4].
3.2 Класифікація мембранних повітророздільних установок
На рис. 3.3 подані схеми організації потоків до мембранних елементів, що утворюють у зборці мембранний апарат. Газ в напірному і дренажному каналах може рухатися: 1 — прямотоком. 2 — противотоком, 3 — перехресним потоком. За конструктивною ознакою виділяють два основних типи мембранних модулів: плоско камерні та трубчасті (див. рис. 3.1). У модулях плоскокамерного типу форма перетину напірного і дренажного каналів близька до прямокутної, та якщо відсутня вільна конвекція, співвідношення геометричних розмірів каналів дозволяють моделювати процеси в ньому як двовимірні течії газу з селективним відсосом або вдувом. У модулях з трубчастими елементами один з каналів має круглий перетин, і течію газу в ньому можна вважати осесиметричною; другий канал утворений зовнішніми циліндричними поверхнями сусідніх мембранних елементів і корпусом модуля, в ньому реалізуються більш складні моделі обтікання пучка циліндрів з різними кутами атаки [3].
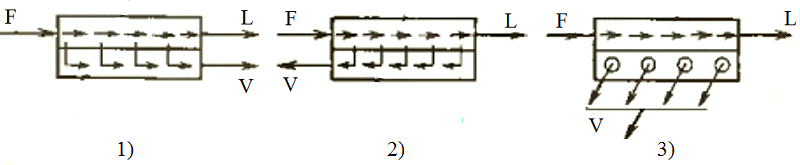
1 — прямоток; 2 — противоток; 3 — перехресний потік
Рисунок 3.3 — Схеми организації потоків у мембранних апаратах
Мембранні газороздільні установки поділяються на одно-, і багатоступеневі. Розділення газових сумішей в одноступеневих мембранних установках застосовується в тих випадках, коли мембрана має дуже високу селективність по відношенню до виділяємого компоненту. Одноступенева установка може включати в собі один або кілька мембранних модулей, з'єднаних паралельно, послідовно або комбіновано. При паралельному з'єднанні у кожний з мембранних модулей подається приблизно однакова кількість вихідної суміші одного і того ж складу. Отримані в кожному модулі потоки ретентата і пермеата відводяться в загальні колектори (рис. 3.4, 1). Перевагою такої схеми є можливість вимкнення частини модулів при зменшенні витрат вихідної суміші, що дозволяє зберегти незмінними концентрації отриманих продуктів. Такі установки легко масштабувати, тобто переносити результати напівпромислових випробувань на великомасштабні промислові установки. Основний недолік цієї схеми — необхідність ретельного контролю над рівномірним розділенням вихідної суміші на модулі. Застосування даної схеми найбільш доцільно в разі порівняно невеликих значень коефіцієнта розділу потоку і використання мембран, що мають велику проникність та селективність [4].
При послідовному з'єднанні мембранних модулей (рис. 3.4, 2) витрати газу в напірних каналах окремих модулей зменшуються у напрямку руху газу. Для того щоб забезпечити однакову швидкість газу в напірних каналах всіх модулей, необхідно встановлювати модулі, в яких розміри по ходу руху газу зменшуються. В установках цього типу є можливість отримання пермеата різного складу. В принципі, вони можуть використовуватися для розділення багатокомпонентних газових сумішей. Пермеат перших модулей буде збагачений компонентами, які мають найбільшу проникність, пермеат останніх — компонентами з проміжними значеннями проникності, ретентат — компонентами з найменшою проникністю. Недоліком розглянутої схеми є порівняно великий гідравлічний опір [4].
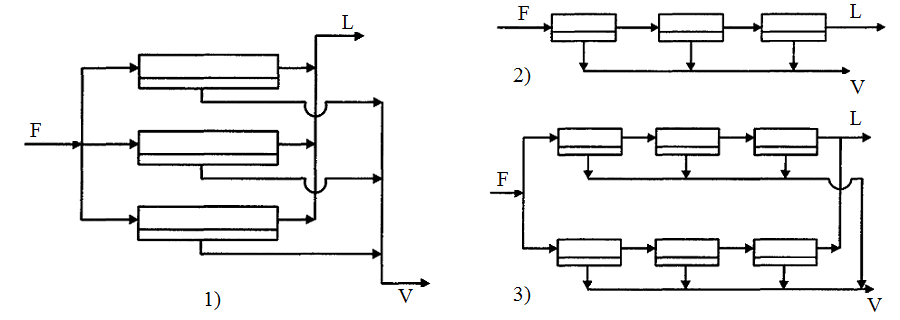
1 — паралельне; 2 — послідовне; 3 — комбіноване
Рисунок 3.4 — Схеми установок з різноманітним розташуванням мембранних модулей
Серед різноманіття одноступеневих установок у промисловій практиці найбільш часто застосовуються установки з комбінованим (паралельно-послідовним) розташуванням мембранних модулей. Схема такої установки показана на рис. 3.4, 3. В цьому випадку поєднується можливість роботи установки при навантаженні, що змінюється по вихідній газової суміші з можливістю розділу багатокомпонентних сумішей.
Чим більше поверхня мембран в одному модулі і, відповідно, чим менше модулів об'єднано в одну установку, тим меншими будуть габаритні розміри, вартість всієї установки, а також буде більш простою і надійною її експлуатація. У той же час застосування великого числа модулів однакового типорозміру забезпечує більшу гнучкість в роботі установки [4].
3.3 Аналіз мембранної установки отримання азоту
У Росії та країнах СНД розвиток мембранного апаратобудування пов'язаний зі створенням асиметричної полівінілтріметілсілановой (ПВТМС) мембрани в Інституті нафтохімічного синтезу ім. A. B. Топчієва, а також порожніх полімерних волокон в ПО «Хімволокно» (м. Митищі) [2].
Асиметрична мембрана складається з активного гомогенного шару завтовшки кілька мікрометрів і пористої підкладки товщиною 100–200 мкм. Завдяки тому, що практично увесь опір потоку проникаючого газу зосереджений в тонкому однорідному шарі, газопроникність асиметричної мембрани значно вище, ніж у гомогенної, що має звичайно мінімальну бездефектну товщину кілька десятків мікрометрів. Це дозволяє поряд зі збереженням селективності полімеру зменшити площу поверхні мембрани в апараті, тобто габарити і капітальні витрати, а процес поділу зробити економічно ефективним [5].
Основні переваги мембранних газороздільних установок:
- розділення газових сумішей без фазових переходів при нормальній температурі;
- екологічна чистота мембрани і продуктів поділу;
- гнучкість характеристик і плавність регулювання режимів;
- короткий час пуску (1–2 хв) і простота в обслуговуванні;
- багаторічний термін служби (більше 10 років).
Мембранні установки отримання азоту застосовують для створення інертного середовища при зберіганні і транспортуванні легкозаймистих рідин і палива, зберіганні спецтехніки, виплавці кольорових металів, проведенні процесів полімеризації в автоклавах, продування охолоджуючих сорочок турбогенераторів ТЕЦ, післязбиральної обробки і зберігання зерна, упаковці харчових продуктів, проведенні бурових робіт в нафтогазовидобувній промисловості, проведенні гіпоксітерапії в медицині і т. п.
В основі конструкції — модульність побудови, що дозволяє тиражуванням уніфікованих модулів створювати установки будь-якої продуктивності від 1 до 500 м3/год з вмістом азоту в продукті 98-99%. Існує можливість плавного зниження вмісту азоту з одночасним збільшенням продуктивності (наприклад, перехід установки в режим отримання 95% -вого азоту підвищує продуктивність в 2 рази) [2].
Повітря (F), що входить в апарат (ступінь розділення) для отримання азоту (рис. 3.5), розділяється на два потоки, які, пройшовши складний шлях і збагатившись пермеатом — азотом (V), видаляються через штуцер 1. Відхідний потік (L) потрапляє в перфоровану трубу 5. Перегородки 2 встановлюють через різне число мембранних елементів: більше — на початку, менше — в кінці по ходу газу [2].
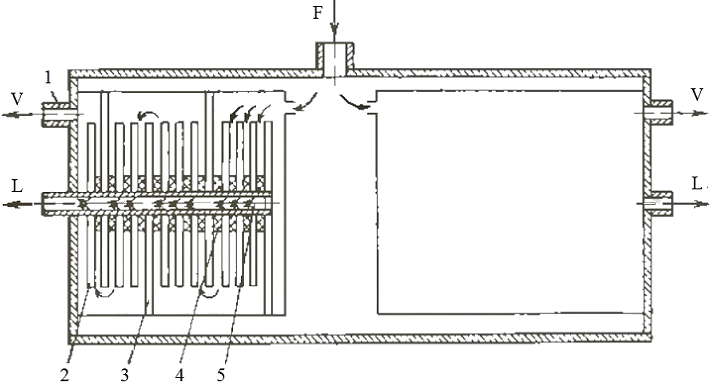
1 — штуцер; 2 — мембранний елемент; 3 — перегородка; 4 — прокладка; 5 — перфорована труба
Рисунок 3.5 — Принципова схема апарата для отримання азоту
4. Порівняльний аналіз адсорбційного і мембранного способів промислового виробництва азоту
Азот широко використовується в різних галузях промисловості, зокрема при: створенні інертного середовища в ємностях з вогне- та вибухонебезпечними рідинами; продування і випробування трубопроводів нафти і газу; азотному пожежогасінні в вугледобувних шахтах; освоєнні свердловин нафти і газу та ін. Існує три основних промислових способів роділення повітря з метою виробництва азоту: кріогенний (ректифікація зрідженого повітря), адсорбційний (затримування молекул кисню в порах молекулярних сит, з подальшою їх регенерацією в адсорбційних установках) і мембранний. Кріогенний спосіб має наступні недоліки: висока вартість; складність апаратурного оформлення; складність експлуатації; вибухо- і пожежонебезпека; наявність шкідливих викидів, що забруднюють навколишнє середовище і тому цей спосіб в подальшому аналізі не розглядається [6]. Порівняння за різними показниками плюсів і мінусів адсорбційних і мембранних установок виробництва азоту приведено у таблиці 4.1 [8].
Таблица 4.1 — Плюси та мінуси адсорбційного і мембранного способів виробництва азоту
Адсорбційні установки | Мембранні установки |
1.Отримувана чистота азоту | |
Плюс: Легко забезпечується стабільна чистота азоту на рівні до 99,999%, що забезпечує можливість використання практично в будь-яких галузях виробництва і невиробничої діяльності. | Мінус: У більшості випадків досягнута чистота азоту не перевищує 99,5%. Для досягнення чистоти вище 99,5% споживання стисненого повітря і, отже, енергетичні витрати перевищують ці показники адсорбційних установок. Тому мембранні генератори азоту можуть бути економічно вигідним варіантом тільки при необхідному рівні чистоти газу на рівні 99,0 ... 99,5% або нижче. |
2. Чутливість до парів компресорного масла | |
Мінус: Адсорбент потребує захисту від парів компресорного масла. | Мінус: Мембрани схильні до пошкодження парами компресорного масла, тому в компресорі необхідно використовувати синтетичні масла, які втрачають менше важких вуглеводневих сполук. |
3. Чутливість до вологості повітря | |
Мінус: Наявність в стисненому повітрі парообразной вологи викликає зниження ефективності роботи адсорбенту, в зв'язку з чим обов'язково установка потребує осушувача стисненого повітря. | Плюс: Наявність в стисненому повітрі парообразной вологи не регламентується і помітно не впливає на функціонування мембран більшості виробників. |
4. Чутливість до температури стисненого повітря | |
Плюс: Малочутливі до температури стисненого повітря як з точки зору ефективності роботи, так і з точки зору зносу. Підігрів стисненого повітря не використовується. | Мінус: Мембрани більшості виробників вкрай чутливі до температури стисненого повітря. Для ефективної роботи потрібен підігрів стисненого повітря до +40 ... + 55 ° C. |
5. Складність регулювання чистоти азоту і продуктивності | |
Мінус: Змінити розрахункову чистоту азоту і продуктивність - складно. Для цього потрібується ретельне регулювання як налаштувань регуляторів витрати і тиску, так і зміна програмованих параметрів. | Плюс: Чистота азоту і продуктивність піддається максимально простому регулюванню за допомогою одного встановленого регулятора витрати на виході з мембран. |
6. Стійкість технологічного процесу | |
Плюс: Неполадки в роботі регуляторів малоймовірні, і навіть у разі виникнення зазвичай не призводять до стрибків чистоти газу. Мінус: Коливання тиску або витрати більш вірогідні і цілком можуть привести до падіння чистоти. | Мінус: Коливання тиску або витрати більш вірогідні та цілком можуть привести до падіння чистоти. |
7. Термін служби адсорбенту | |
Плюс: При належному очищенню стисненого повітря, термін служби адсорбенту становить 10 ... 15 років або більше. | Мінус: Навіть при належному очищенню стисненого повітря, мембрани не довговічні і досить швидко зношуються. Термін служби мембран зазвичай становить близько 5 років. |
8. Вартість робочого матеріалу (адсорбенту і мембран) | |
Плюс: Адсорбент коштує дешевше, ніж мембрани, як у відносному вираженні в порівнянні з вартістю всієї установки, так і в абсолютному грошовому вираженні. | Мінус: Вартість мембран становить більшу частину ціни мембранної азотної установки, а в абсолютному вираженні мембранні модулі також коштують дорожче, ніж адсорбційні модулі при однаковій продуктивності. |
9. Складність апаратурного оформлення | |
Мінус: Конструкція адсорбційних установок складніше, ніж мембранних, що означає велику ймовірність відмов. | Плюс: Простота конструкції з мінімумом рухомих частин. |
10. Складність монтажу | |
Мінус: Мала пристосованість до монтажу в складі контейнерних мобільних азотних станцій. | Плюс: Мембранні модулі добре підходять для монтажу в контейнерах та експлуатації в складі мобільних азотних станцій. |
Дані, наведені в таблиці 4.1, показують, що переваги і недоліки існують як у адсорбційних, так і у мембранних систем виробництва азоту. Однак сучасні мембранні установки служать основою створення безвідходних технологій. Їх застосування здатне вирішити одне з головних технічних протиріч «зростання промислового потенціалу» — «чистота навколишнього середовища», так як вони «безреагентні», а точніше сказати «малореагентні». У зв'язку з цим за мембранними технологіями — майбутнє [8].
Мембранне розділення повітря засновано на різній проникності (швидкості проникнення) кисню, азоту та інших компонентів повітря через речовину мембрани. Об'еми кисню та азоту (приведені до нормальних умов), які проходять через мембрану відповідно визначається за формулами [7]:
Vк=Кк·S·ΔP·τ;
Va=Кa·S·ΔP·τ;
де Кк і Кa — коэфіціенти проникності кислороду та азоту відповідно;
S — площа робочої поверхні мембрани;
ΔP — різниця тисків до і після мембрани;
τ — час.
Фізичний сенс коефіцієнтів Кк і Кa полягає в тому, що вони, відповідно, показують скільки об'eму чистого кисню та азоту проходить в одиницю часу через 1,0 м2 мембрани при різниці тисків 1,0 МПа. Чисельні значення коефіцієнтів і визначаються експериментально. Значення коефіцієнтів проникності кисню, азоту та інших газів (гелію — Не, неону — Ne, аргону — Ar, криптону — Kr, ксенону — Xe), що входять до складу повітря, показані з використанням логарифмічної шкали на рисунку 4.1. З рисунка 4.1 видно, що проникність кисню приблизно в два рази вище проникності азоту. Ці властивості кисню та азоту покладені в основу мембранної технології поділу повітря [7].
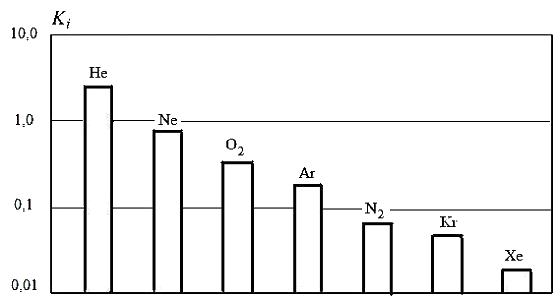
Рисунок 4.1 — Коэффіціенти проникності компонентів повітря
Висновки
Мембранні процеси розділення газових сумішей відносяться до нових технологічних процесів, які сьогодні знаходять все більш широке застосування в різних галузях промисловості. Принцип роботи установок заснований на селективної проникності компонентів газових сумішей через полімерні мембрани.
Поява асиметричних мембран стало проривом в промисловому застосуванні мембран. Ці мембрани складаються з дуже щільного поверхневого шару або покриття товщиною від 0,1 до 5 мкм, що лежить на пористої підкладці товщиною від 50 до 150 мкм. Такі мембрани поєднують високу селективність щільною мембрани з високою швидкістю масопереносу дуже тонкої мембрани.
Перспективи застосування мембранного розділення газів в хімічній промисловості визначаються, перш за все, простотою апаратурного оформлення процесу, безреагентністю, економічністю, тривалою роботою газороздільних мембран при незмінних їх характеристиках, можливістю повної автоматизації установок і т. п.
Мембранні газорозділювальні установки застосовують для отримання азоту і створення інертного середовища, збагачення повітря киснем, створення регульованого газового середовища в холодильних камерах при зберіганні продуктів харчування, концентрування водню в азотоводородной сумішах.
Під час написання даного реферату магістерська робота ще не завершена. Остаточна дата завершення: червень 2017 року. Повний текст роботи і матеріали по темі можуть бути отримані у автора або його керівника після зазначеної дати.
Перелік посилань
- Архаров А. М. Криогенные системы. В 2 т. Т.1. Основы теории и расчета / А. М. Архаров — М.: Машиностроение, 1996. — 576 с.
- Архаров А. М. Криогенные системы. В 2 т. Т.2. Основы проектирования аппаратов, установок и систем / А. М. Архаров — М.: Машиностроение, 1999. — 720 с.
- Дытнерский Ю. И., Брыков В. П., Каграманов Г. Г. Мембранное разделение газов / Ю. И. Дытнерский, В .П. Брыков, Г. Г. Каграманов — М.: Химия, 1991. — 344 с.
- Новый справочник химика и технолога. Процессы и аппараты химических технологий. Ч. II. — СПб.: НПО «Профессионал», 2006. — 916 с.
- Мулдер М. Введение в мембранную технологию / Мулдер М. — Пер. с англ. — М.: Мир, 1999. — 513 с.
- Кельцев Н. В. Основы адсорбционной техники / Н. В. Кельцев — М.: Химия, 1984. — 592 с.
- Бондаренко В. Л., Лосяков Н. П., Симоненко Ю. М. и др. Мембранное разделение газовых смесей на основе компонентов воздуха / В. Л. Бондаренко, Н. П. Лосяков , Ю. М. Симоненко // Вестник МГТУ им. Н.Э Баумана. Сер. «Машиностроение», 2012. с. 20–40.
- Мартынов В. В., Остапенко М. А. Сравнительный анализ адсорбционного и мембранного способов промышленного производства азота / В. В. Мартынов, М. А. Остапенко // Материалы X Международной научной конференции аспирантов и студентов «Охрана окружающей среды и рациональное использование природных ресурсов» — Донецк, ДонНТУ — 2016.