Реферат по теме выпускной работы
Содержание
- Введение
- 1. Актуальность темы
- 2. Цель и задачи работы, планируемые результаты
- 3. Технология мембранного разделения газов
- 3.1 Принцип разделения газов
- 3.2 Классификация мембранных воздухоразделительных установок
- 3.3 Анализ мембранной установки получения азота
- 4. Сравнительный анализ адсорбционного и мембранного способов промышленного производства азота
- Выводы
- Список источников
Введение
Внедрению мембранного метода разделения газов в промышленность способствовали результаты изучения явлений, связанных с селективным переносом молекул газов через сплошные (гомогенные) и микропористые мембраны, имеющие неорганическую или полимерную природу, успехи в синтезе полимеров с газоразделительными свойствами, разработка методов получения высокопроизводительных (асимметричных, композиционных, напыленных и т. д.) полимерных, металлических и керамических мембран, создание конструкций и методов расчета мембранных аппаратов и установок.
Перспективы применения мембранного разделения газов в химической промышленности определяются, прежде всего, простотой аппаратурного оформления процесса, безреагентностью, экономичностью, длительной работой газоразделительных мембран при неизменных их характеристиках, возможностью полной автоматизации установок и т. п.
Мембранное разделение газов используют в технологии переработки природных газов, обогащения воздуха кислородом, концентрирования водорода продувочных газов синтеза аммиака, для создания регулируемой газовой среды при хранении сельскохозяйственной продукции и многих других целей. Также перспективно применение мембранного газоразделения для очистки отходящих газов.
1. Актуальность темы
Атмосферный воздух является сырьем для получения таких промышленных газов, как кислород, азот, аргон, неон, криптон, ксенон. Темпы ежегодного прироста производства этих газов в мире в 1,2–1,4 раза превышают прирост любых других видов продукции. Промышленное производство этих газов осуществляется на воздухоразделительных установках (ВРУ). Существует три основных способа разделения воздуха: криогенный, адсорбционный и мембранный [1].
В отличие от мембранных воздухоразделительных установок, криогенные и адсорбционные ВРУ представляют собой сложные технические системы, включающие: оборудование для сжатия атмосферного воздуха, его очистки от влаги, двуокиси углерода, взрывоопасных примесей; теплообменные аппараты для охлаждения воздуха до криогенных температур и нагрева продуктов разделения; ректификационные колонны и конденсаторы-испарители; криогенные насосы и т. п [2].
Мембранные процессы разделения газовых смесей относятся к новым технологическим процессам, которые в настоящее время находят все более широкое применение в различных отраслях промышленности. В технологическом отношении организация процесса разделения на мембранах отличается простотой и широко применяется на практике.
2. Цель и задачи работы, планируемые результаты
Цель работы заключается в обосновании рационального аппаратурного оформления мембранной установки, обеспечивающей при заданной производительности достижение требуемой чистоты конечных продуктов разделения воздуха (азота и кислорода) при минимизации энерго-, и материалопотребления.
Задачи, решаемые для достижения указанной цели:
- Анализ теоретических основ разделения газов в мембранном элементе.
- Обоснование конструкции мембранного модуля, типа и материла используемых мембран.
- Разработка математической модели, описывающей работу мембранного модуля.
- Анализ влияния различных факторов на эффективность мембранного процесса разделения воздуха и использования этого анализа для обоснования выбора вспомогательного оборудования.
- Технико-экономическое обоснование технических решений.
Объект исследования: процесс мембранного разделения воздуха.
Предмет исследования: аппаратурное оформление процесса мембранного разделения воздуха.
Научная новизна работы заключается в разработке алгоритма обоснования аппаратурного оформления процесса мембранного разделения воздуха на основе анализа различных схем взаимодействия мембранных модулей и анализа влияния различных факторов на эффективность процесса.
Практическое значение работы заключается в использовании результатов работы для снижения энерго-, и материалопотребления при принятии проектных решений и промышленном внедрении установок для разделения воздуха.
3. Технология мембранного разделения газов
3.1 Принцип разделения газов
Разделение воздуха на мембране может происходить как без химических превращений, так и с химическими превращениями с помощью введенных в мембрану катализаторов и ферментов. В качестве мембран используют полимерные пленки, тонкие металлические или керамические пластины, слой жидкости и т. д. Мембранный модуль (рис. 3.1) обеспечивает разделение исходного потока F на два: пермеат V проходит через мембрану, а сбрасываемый поток (ретант) L уносится на следующую ступень разделения или сбрасывается. В технологическом отношении организация процесса разделения на мембранах отличается простотой и широко применяется на практике, например при получении из воздуха азота и кислорода [3].
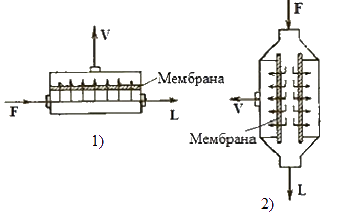
1 — плоскокамерный; 2 — трубчатый
Рисунок 3.1 — Схемы мембранных модулей
Перенос вещества через мембрану осуществляется под действием полей потенциалов различной природы (полей давления, температуры, концентрации, гравитации, электромагнитной природы и др.). Потоки вещества через мембрану бывают диффузионными, осмотическими, ионными, электрофоретическими и т. п. Массовый поток в мембране ориентирован по нормали к разделяющей поверхности. Движущая сила переноса компонента определяется разностью химических потенциалов в напорном и дренажном каналах, разделенных мембраной. Скорость массопереноса через мембрану изменяется по длине мембранного элемента и зависит от термо- и гидродинамических параметров в рассматриваемой точке напорного или дренажного канала [3].
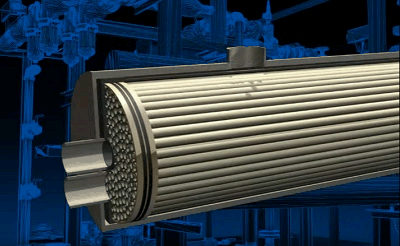
Рисунок 3.2 — Процесс разделения воздуха в трубчатом модуле
анимация: 4 кадра, 6 циклов повторения, 143 килобайт
При описании процессов массопереноса через пористую мембрану часто используют различные модели течения как вязкого, так и молекулярного потока. Структура пор мембраны сложна, а часто и неизвестна, поэтому для правильного применения уравнений течения газов при расчете процессов мембранного разделения необходимо учитывать структуру и размер пор (эквивалентный диаметр, длину канала, удельную площадь поверхности, распределение пор по размерам и др.). Для вязкого потока размер пор должен быть достаточно велик по сравнению с длиной свободного пути молекул газа [4].
3.2 Классификация мембранных воздухоразделительных установок
На рис. 3.3 даны схемы организации потоков в мембранных элементах, образующих в сборке мембранный аппарат. Газ в напорном и дренажном каналах может двигаться: 1 — прямотоком. 2 — противотоком, 3 — перекрестным током. По конструктивному признаку выделяют два основных типа мембранных модулей: плоскокамерные и трубчатые (см. рис. 3.1). В модулях плоскокамерного типа форма сечения напорного и дренажного каналов близка к прямоугольной, причем если отсутствует свободная конвекция, соотношения геометрических размеров каналов позволяют моделировать процессы в нем как двумерные течения газа с селективным отсосом или вдувом. В модулях с трубчатыми элементами один из каналов имеет круглое сечение, и течение газа в нем можно считать осесимметричным; второй канал образован наружными цилиндрическими поверхностями соседних мембранных элементов и корпусом модуля, в нем реализуются более сложные модели обтекания пучка цилиндров с различными углами атаки [3].
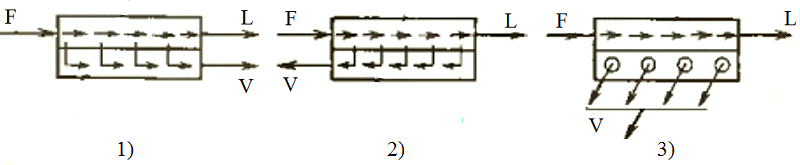
1 — прямоток; 2 — противоток; 3 — перекрестный ток
Рисунок 3.3 — Схемы организации потоков в мембранных аппаратах
Мембранные газоразделительные установки делятся на одно-, и многоступенчатые. Разделение газовых смесей в одноступенчатых мембранных установках применяется в тех случаях, когда мембрана обладает очень высокой селективностью по отношению к извлекаемому компоненту. Одноступенчатая установка может включать один или несколько мембранных модулей, соединенных параллельно, последовательно или комбинированно. При параллельном соединении в каждый из мембранных модулей подается примерно одинаковое количество исходной смеси одного и того же состава. Получаемые в каждом из модулей потоки ретентата и пермеата отводятся в общие коллекторы (рис. 3.4, 1). Достоинством такой схемы является возможность отключения части модулей при уменьшении расхода исходной смеси, что позволяет сохранить неизменными концентрации получаемых продуктов. Такие установки легко масштабировать, т. е. переносить результаты полупромышленных испытаний на крупномасштабные промышленные установки. Основной недостаток этой схемы — необходимость тщательного контроля над равномерным распределением исходной смеси на модули. Применение данной схемы наиболее целесообразно в случае сравнительно небольших значений коэффициента деления потока и использования мембран, обладающих большими проницаемостями и высокой селективностью. [4]
При последовательном соединении мембранных модулей (рис. 3.4, 2) расходы газа в напорных каналах отдельных модулей уменьшаются по направлению движения газа. Для того чтобы обеспечить одинаковую скорость газа в напорных каналах всех модулей, необходимо устанавливать модули с уменьшающимися по ходу движения газа размерами. В установках этого типа возможно получение пермеатов различного состава. В принципе они могут использоваться для разделения многокомпонентных газовых смесей. Пермеат первых по ходу движения газа модулей будет обогащен компонентами, имеющим наибольшую проницаемость, пермеат последних модулей — компонентами с промежуточными значениями проницаемостей, ретентат – компонентами с наименьшей проницаемостью. Недостатком рассматриваемой схемы является сравнительно большое гидравлическое сопротивление [4].
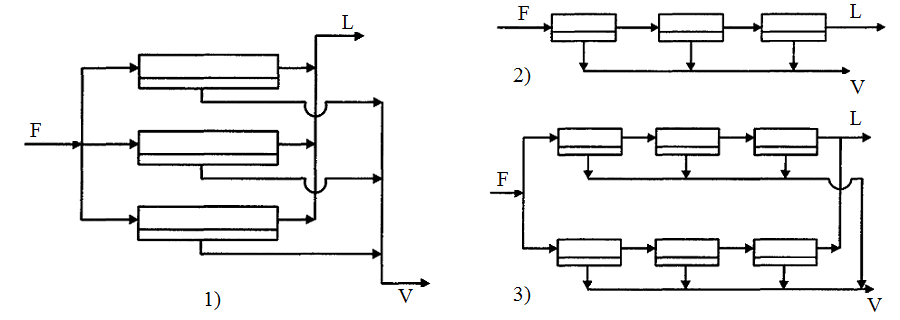
1 — параллельное; 2 — последовательное; 3 — комбинированное
Рисунок 3.4 — Схемы установок с различным расположением мембранных модулей
Из числа одноступенчатых установок в промышленной практике наиболее часто применяются установки с комбинированным (параллельно-последовательным) расположением мембранных модулей. Схема такой установки показана на рис. 3.4, 3. В этом случае сочетается возможность работы установки при изменяющейся нагрузке по исходной газовой смеси с возможностью разделения многокомпонентных смесей.
Чем больше поверхность мембран в одном модуле и, соответственно, чем меньше модулей объединено в одну установку, тем меньшими будут габаритные размеры и стоимость всей установки и более простой и надежной ее эксплуатация. В то же время применение большого числа модулей одинакового типоразмера обеспечивает большую гибкость в работе установки [4].
3.3 Анализ мембранной установки получения азота
В России и странах СНГ развитие мембранного аппаратостроения связано с созданием асимметричной поливинилтриметилсилановой (ПВТМС) мембраны в Институте нефтехимического синтеза им. A. B. Топчиева, а также полых полимерных волокон в ПО «Химволокно» (г. Мытищи). [2]
Асимметричная мембрана состоит из активного гомогенного слоя толщиной несколько микрометров и пористой подложки толщиной 100–200 мкм. Благодаря тому, что практически все сопротивление потоку проникающего газа сосредоточено в тонком гомогенном слое, газопроницаемость асимметричной мембраны значительно выше, чем у гомогенной, имеющей обычно минимальную бездефектную толщину несколько десятков микрометров. Это позволяет наряду с сохранением селективности полимера уменьшить площадь поверхности мембраны в аппарате, т.е. габариты и капитальные затраты, а процесс разделения сделать экономически эффективным [5].
Основные преимущества мембранных газоразделительных установок:
- разделение газовых смесей без фазовых переходов при нормальной температуре;
- экологическая чистота мембраны и продуктов разделения;
- гибкость характеристик и плавность регулирования режимов;
- короткое время пуска (1–2 мин) и простота в обслуживании;
- многолетний срок службы (более 10 лет).
Мембранные установки для получения азота применяют для создания инертной среды при хранении и транспортировании легковоспламеняющихся жидкостей и топлива, хранении спецтехники, выплавке цветных металлов, проведении процессов полимеризации в автоклавах, продувке охлаждающих рубашек турбогенераторов ТЭЦ, послеуборочной обработке и хранении зерна, упаковке пищевых продуктов, проведении буровых работ в нефтегазодобывающей промышленности, проведении гипокситерапии в медицине и т. п.
В основе конструкции — модульность построения, что позволяет тиражированием унифицированных модулей создавать установки любой производительности от 1 до 500 м3/ч с содержанием азота в продукте 98-99%. Имеется возможность плавного снижения содержания азота с одновременным увеличением производительности (например, перевод установки в режим получения 95%-ного азота повышает производительность в 2 раза) [2].
Воздух (F), входящий в аппарат (ступень разделения) для получения азота (рис. 3.5), разделяется на два потока, которые, пройдя сложный путь и обогатившись труднопроникающим компонентом — азотом (V), удаляются через штуцер 1. Отбросной поток (L) попадает в перфорированную трубу 5. Перегородки 2 устанавливают через различное число мембранных элементов: большее — в начале, меньшее — в конце по ходу газа [2].
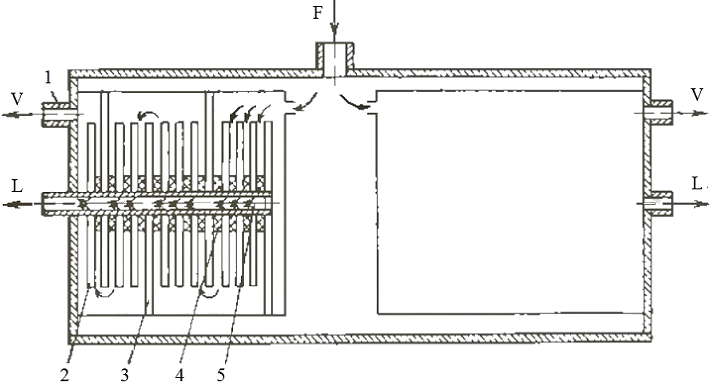
1 — штуцер; 2 — мембранный элемент; 3 — перегородка; 4 — прокладка; 5 — перфорированная труба
Рисунок 3.5 — Принципиальная схема аппарата для получения азота
4. Сравнительный анализ адсорбционного и мембранного способов промышленного производства азота
Азот широко используется в различных отраслях промышленности, в частности при: создании инертной среды в емкостях с огне- и взрывоопасными жидкостями; продувке и испытании трубопроводов нефти и газа; азотном пожаротушении в угледобывающих шахтах; освоении скважин нефти и газа и др. Существует три основных промышленных способов разделения воздуха с целью производства азота: криогенный (ректификация сжиженного воздуха), адсорбционный (задерживание молекул кислорода в порах молекулярных сит, с последующей их регенерацией в адсорбционных установках) и мембранный. Криогенный способ имеет следующие недостатки: высокая стоимость; сложность аппаратурного оформления; сложность эксплуатации; взрыво- и пожароопасность; наличие вредных выбросов, загрязняющих окружающую среду и поэтому этот способ в дальнейшем анализе не рассматривается [6]. Сравнение по различным показателям плюсов и минусов адсорбционных и мембранных установок производства азота приведено в таблице 4.1 [8].
Таблица 4.1 — Плюсы и минусы адсорбционного и мембранного способов производства азота
Адсорбционные установки | Мембранные установки |
1. Достигаемая чистота азота | |
Плюс: Легко обеспечивается стабильная чистота азота на уровне до 99,999%, что обеспечивает возможность использования практически в любых областях производства и непроизводственной деятельности. | Минус: В большинстве случаев достигаемая чистота азота не превышает 99,5%. Для достижения чистоты выше 99,5% потребление сжатого воздуха и, следовательно, энергетические затраты превышают эти показатели адсорбционных установок. Поэтому мембранные генераторы азота могут являться экономически выгодным вариантом только при необходимом уровне чистоты газа на уровне 99,0...99,5% или ниже. |
2. Чувствительность к парам компрессорного масла | |
Минус: Адсорбент нуждается в защите от паров компрессорного масла. | Минус: Мембраны подвержены повреждению парами компрессорного масла, поэтому в компрессоре необходимо использовать синтетические масла, теряющие меньше тяжелых углеводородных соединений. |
3. Чувствительность к влажности воздуха | |
Минус: Наличие в сжатом воздухе парообразной влаги вызывает снижение эффективности работы адсорбента, в связи с чем обязательно требуется установка осушителя сжатого воздуха. | Плюс: Наличие в сжатом воздухе парообразной влаги не регламентируется и не оказывает заметного влияния на функционирование мембран большинства производителей. |
4. Чувствительность к температуре сжатого воздуха | |
Плюс: Малочувствительны к температуре сжатого воздуха как с точки зрения эффективности работы, так и с точки зрения износа. Подогрев сжатого воздуха не используется. | Минус: Мембраны большинства производителей крайне чувствительны к температуре сжатого воздуха. Для эффективной работы требуется подогрев сжатого воздуха до +40...+55°C. |
5. Сложность регулирования чистоты азота и производительности | |
Минус: Изменить расчетную чистоту азота и производительность — сложно. Для этого требуется тщательная регулировка как настроек регуляторов расхода и давления, так и изменение программируемых параметров. | Плюс: Чистота азота и производительность поддается максимально простой регулировке с помощью одного установленного на выходе из мембран регулятора расхода. |
6. Устойчивость технологического процесса | |
Плюс: Неполадки в работе регуляторов маловероятны, и даже в случае возникновения обычно не приводят к скачкам чистоты газа. | Минус: Колебания давления или расхода более вероятны и вполне могут привести к падению чистоты. |
7. Срок службы адсорбента | |
Плюс: При надлежащей очистке сжатого воздуха, срок службы адсорбента составляет 10...15 лет или больше. | Минус: даже при надлежащей очистке сжатого воздуха, мембраны неизбежно и довольно быстро изнашиваются. Срок службы мембран обычно составляет порядка 5 лет. |
8. Стоимость рабочего материала (адсорбента и мембран) | |
Плюс: Адсорбент стоит дешевле, чем мембраны, как в относительном выражении по сравнению со стоимостью всей установки, так и в абсолютном денежном выражении. | Минус: Стоимость мембран составляет большую часть цены мембранной азотной установки, а в абсолютном выражении мембранные модули также дороже, чем адсорбционные модули при одинаковой производительности. |
9. Сложность аппаратурного оформления | |
Минус: Конструкция адсорбционных установок сложнее, чем мембранных, что означает и большую вероятность отказов. | Плюс: Простота конструкции с минимумом движущихся частей. |
10. Сложность монтажа | |
Минус: Малая приспособленность к монтажу в составе контейнерных мобильных азотных станций. | Плюс: Мембранные модули хорошо подходят для монтажа в контейнерах и эксплуатации в составе мобильных азотных станций. |
Данные, приведенные в таблице 4.1, показывают, что преимущества и недостатки имеются как у адсорбционных, так и у мембранных систем производства азота. Однако современные мембранные установки служат основой создания безотходных технологий, Их применение способно разрешить одно из главных технических противоречий «рост промышленного потенциала» — «чистота окружающей среды», так как они «безреагентны», а точнее сказать «малореагентны». В связи с этим за мембранными технологиями — будущее [8].
Мембранное разделение воздуха основано на различной проницаемости (скорости проникновения) кислорода, азота и других компонентов воздуха через вещество мембраны. Объемы кислорода и азота (приведенные к нормальным условиям), которые проходят через мембрану соответственно определяется по формулам [7]:
Vк=Кк·S·ΔP·τ;
Va=Кa·S·ΔP·τ;
где Кк и Кa — коэффициенты проницаемости кислорода и азота соответственно;
S — площадь рабочей поверхности мембраны;
ΔP — разность давлений до и после мембраны;
τ — время.
Физический смысл коэффициентов Кк и Кa заключается в том, что они, соответственно, показывают объемы чистого кислорода и азота проходящие в единицу времени через 1,0 м2 мембраны при разности давлений 1,0 МПа. Численные значения коэффициентов определяются экспериментально. Значения коэффициентов проницаемости кислорода, азота и других газов (гелия — Не, неона — Ne, аргона — Ar, криптона — Kr, ксенона — Xe), входящих в состав воздуха, показаны с использованием логарифмической шкалы на рисунке 4.1. Из рисунка 4.1 видно, что проницаемость кислорода примерно в два раза выше проницаемости азота. Эти свойства кислорода и азота положены в основу мембранной технологии разделения воздуха [7].
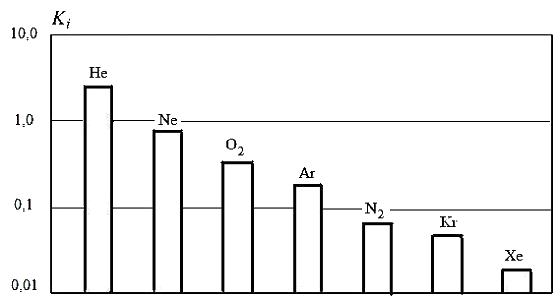
Рисунок 4.1 — Коэффициенты проникаемости компонентов воздуха
Выводы
Мембранные процессы разделения газовых смесей относятся к новым технологическим процессам, которые в настоящее время находят все более широкое применение в различных отраслях промышленности. Принцип работы установок основан на селективной проницаемости компонентов газовых смесей через полимерные мембраны.
Появление асимметричных мембран стало прорывом в промышленном применении мембран. Эти мембраны состоят из очень плотного поверхностного слоя или покрытия толщиной от 0,1 до 5 мкм, лежащего на пористой подложке толщиной от 50 до 150 мкм. Такие мембраны сочетают высокую селективность плотной мембраны с высокой скоростью массопереноса очень тонкой мембраны.
Перспективы применения мембранного разделения газов в химической промышленности определяются, прежде всего, простотой аппаратурного оформления процесса, безреагентностью, экономичностью, длительной работой газоразделительных мембран при неизменных их характеристиках, возможностью полной автоматизации установок и т. п.
Мембранные газоразделительные установки применяют для получения азота и создания инертной среды, обогащения воздуха кислородом, создания регулируемой газовой среды в холодильных камерах при хранении продуктов питания, концентрирования водорода в азотоводородных смесях.
При написании данного реферата магистерская работа еще не завершена. Окончательное завершение: июнь 2017 года. Полный текст работы и материалы по теме могут быть получены у автора или его руководителя после указанной даты.
Список источников
- Архаров А. М. Криогенные системы. В 2 т. Т.1. Основы теории и расчета / А. М. Архаров — М.: Машиностроение, 1996. — 576 с.
- Архаров А. М. Криогенные системы. В 2 т. Т.2. Основы проектирования аппаратов, установок и систем / А. М. Архаров — М.: Машиностроение, 1999. — 720 с.
- Дытнерский Ю. И., Брыков В. П., Каграманов Г. Г. Мембранное разделение газов / Ю. И. Дытнерский, В .П. Брыков, Г. Г. Каграманов — М.: Химия, 1991. — 344 с.
- Новый справочник химика и технолога. Процессы и аппараты химических технологий. Ч. II. — СПб.: НПО «Профессионал», 2006. — 916 с.
- Мулдер М. Введение в мембранную технологию / Мулдер М. — Пер. с англ. — М.: Мир, 1999. — 513 с.
- Кельцев Н. В. Основы адсорбционной техники / Н. В. Кельцев — М.: Химия, 1984. — 592 с.
- Бондаренко В. Л., Лосяков Н. П., Симоненко Ю. М. и др. Мембранное разделение газовых смесей на основе компонентов воздуха / В. Л. Бондаренко, Н. П. Лосяков , Ю. М. Симоненко // Вестник МГТУ им. Н.Э Баумана. Сер. «Машиностроение», 2012. с. 20–40.
- Мартынов В. В., Остапенко М. А. Сравнительный анализ адсорбционного и мембранного способов промышленного производства азота / В. В. Мартынов, М. А. Остапенко // Материалы X Международной научной конференции аспирантов и студентов «Охрана окружающей среды и рациональное использование природных ресурсов» — Донецк, ДонНТУ — 2016.