Abstract
Content
- Introduction
- 1 Heatphysical conditions of heat removal from nepreryvnolity preparation in a crystallizer
- 2 Review of researches and developments
- Conclusion
- List of sources
Introduction
The crystallizer represents a constructive element in which liquid metal is filled in and there is a formation of a firm crust on preparation section perimeter. For CCM used the barrel molds , the main element of which is a copper sleeve (fig. 1) [1].
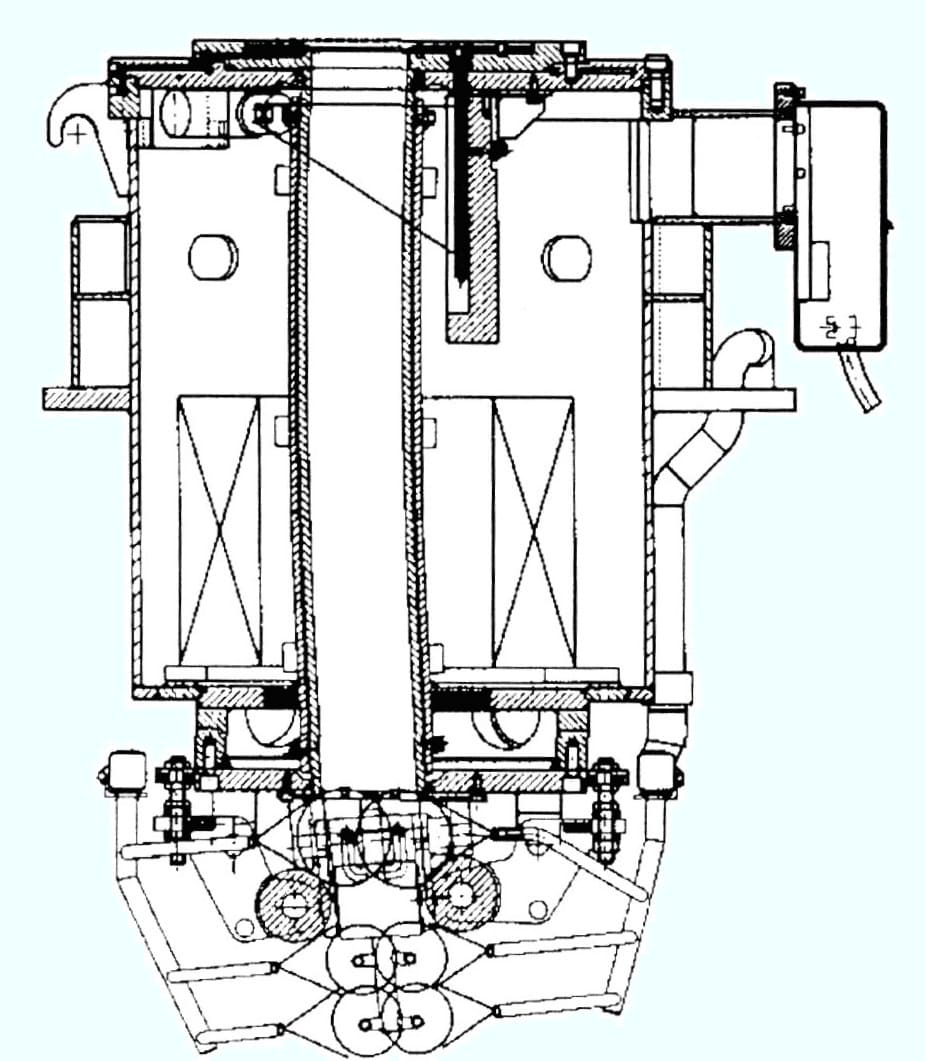
During stay in a crystallizer from liquid metal 20-30% of heat are taken away. In a crystallizer it is necessary to create such thickness of a firm crust that she after an exit from a crystallizer could sustain the ferrostatics pressure of liquid metal and mechanical loadings. For decrease in wear of sleeves of crystallizers the special sheeting from materials with high resistance for attrition about 100 microns thick is applied on their internal surface.
1. Heatphysical conditions of heat removal from nepreryvnolity preparation in a crystallizer
Warmly from the preparation which is formed in a crystallizer sleeve it is transmitted to the cooling water through a row "the thermal resistance which are consistently included": from liquid metal to an internal surface of the formed firm crust > through a firm crust > from an external surface of a firm crust to an internal surface of a sleeve of a crystallizer > through a copper wall of a sleeve of a crystallizer > from an external surface of a sleeve of a crystallizer to the cooling water (fig. 2) [2].
Among the called thermal resistance resistance to transfer of heat from a preparation crust to an internal surface of a sleeve of a crystallizer dominates and and according to laws of heat exchange determines heat removal size in a crystallizer. Distinguish two possible mechanisms of transfer of heat through this resistance: through a gas gap and on the contact mechanism. The greatest value gets the considered resistance in the presence of a steady gas gap thickness from several honeycombs microns and is in range 1•10-3 .. 2,5•10-3 sq.m • To/W. On the contrary, in the presence of the contact mechanism this resistance is much lower (5•10-4 .. 6•10-4 sq.m • To/W).
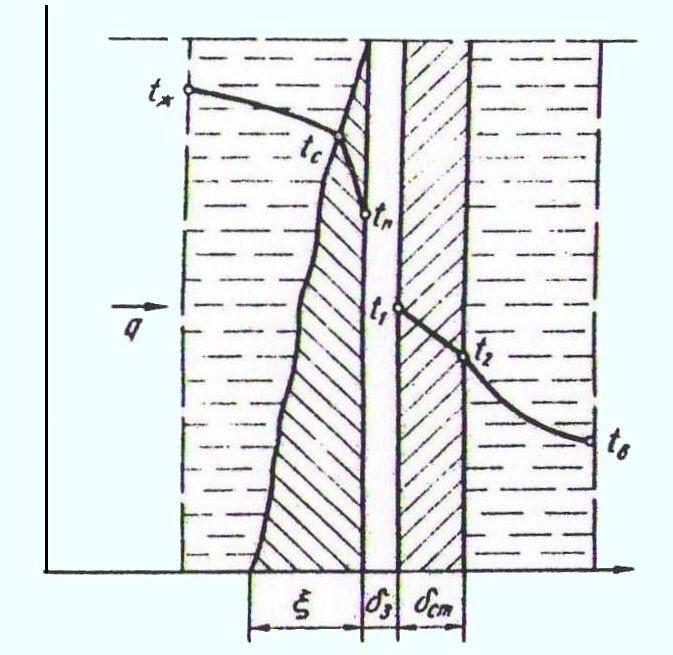
tж, tс, tп, t1, t2, tв – temperatures of liquid steel, solidus, external surface of a crust of metal, internal temperature of a wall of a crystallizer, external temperature of a wall of a crystallizer and the cooling water respectively, °С; ξ – thickness of a crust of metal, m; δз, δст – In continuous caster’s mouldthe heat from melted steel is transferred to cooling water through the placed in series range of thermal resistances
Formation of a gas gap is explained by shrinkage of steel upon transition from liquid to a firm state. At the same time contact of a surface of preparation with a crystallizer sleeve worsens [1, 2, 3]. In the top part of a crystallizer contact of preparation is maximum as the thin crust of preparation is insufficiently strong here to sustain the ferrostatics pressure of metal. Further at the movement of preparation between a sleeve and a crust the gas gap which considerably reduces intensity of cooling of preparation is formed. Under certain conditions it can lead to submelting of a crust of preparation and its break at an exit from a crystallizer.
2. Review of researches and developments
In practice for control of a thermal stream in a crystallizer difference of temperatures of the cooling water on an entrance and at the exit from a crystallizer is used. This size characterizes heat exchange between a crust of preparation and an internal surface of a crystallizer. Tells increase in difference of temperatures of the cooling water in a crystallizer about increase in amount of heat which is taken away from a preparation surface [4].
Change in time of the sizes characterizing thermal work of a crystallizer (for conditions of one of the metallurgical enterprises of Donbass), is shown on fig. 3. It is visible that for the temporary interval considered on a trend conditionally constant can accept a consumption of the cooling water (1700 л/мин). For the analysis of thermal work of a crystallizer it is offered to consider sizes, more informative than temperature drop of the cooling water. In the role of such values it makes sense to use heat flow average density from the surface of billet in the mould (q), heat-transfer coefficient average value in the mould (k), average ratio of heat transfer from billet shell to inner surface of the mould tube (α), effective gas gap thickness (δэф). The methodology of determination of these sizes offered in work [5], it can be adapted in actual practice. Settlement determination of average values of the called sizes for basic data has been carried out, showned on fig. 3. Section of the spilled preparation makes 120х120 mm, and crystallizer length – 750 mm.
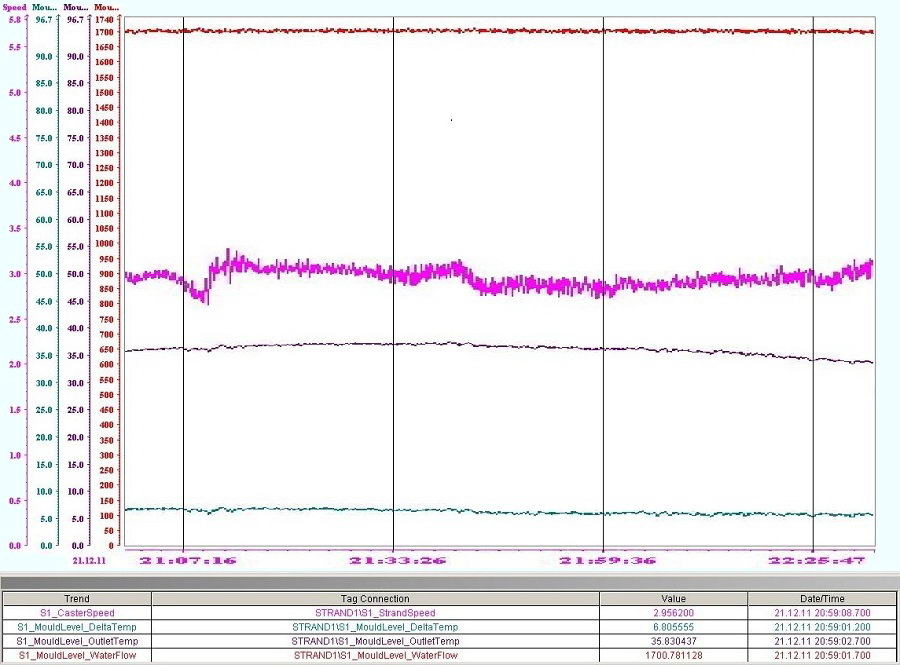
So it is in number shown that on the basis of the offered dependences (1-7) within system of industrial control system in real time it is possible to define change of values of all declared sizes (q,k,α ,δэф) depending on such parameters as differential temperature of cooling water in the mould, usage of primary water, thermal and physical characteristics of the poured steel, geometrical parameters of the mould tube [5].
Выводы
1. Approaches to diagnostics of thermal processes in a crystallizer are analysed. As sizes on the basis of which diagnostics is conducted it is offered to allocate: heat flow average density from the surface of billet in the mould, heat-transfer coefficient average value in the mould, average ratio of heat transfer from billet shell to inner surface of the mould tube, effective gas gap thickness.
2. For the settled modes of pouring quantitative values of the offered sizes are defined. So, the total coefficient of a heat transfer k has made 1387,1 W / (sq.m • J) , and the effective thickness of a gas gap δэф=2,72•10-5 m.
Список Источников
1. Смирнов А.Н. Непрерывная разливка стали: Учебник / А.Н. Смирнов, С.В. Куберский, Е.В. Штепан. - Донецк: ДонНТУ, 2011. - 482 с.
2. Огурцов А.П. Непрерывное литье стали / А.П. Огурцов, А.В. Гресс. - Днепропетровск: Системные технологии, 2002. - 675 с.
3. Смирнов А.Н. Непрерывная разливка сортовой заготовки / А.Н. Смирнов, С.В. Куберский, А.Л. Подкорытов и др. - Донецк: Цифровая типография, 2012. - 417 с.
4. Бирюков А.Б. Совершенствование теплотехнических параметров систем производства непрерывнолитой заготовки и ее тепловой обработки: Монография / А.Б. Бирюков. - Донецк: Изд-во «Ноулидж» (донецкое отделение), 2013. - 471 с.
5. Birukov A.B. Billet CC’s mould heat engineering parameters monitoring system / A.B. Birukov // Metallurgical and mining industry. – 2014. – №1. – Р. 44-48.