Реферат по теме Исследование микропроцессорной системы управления для регулирования механических координат двигателя постоянного тока
Содержание
- Введение
- 1. Актуальность темы
- 2. Разработка аппаратной части лабораторного стенда
- 2.1 Выбор платы
- 2.2 Выбор драйвера
- 2.3 Выбор двигателя
- 3. Разработка аппаратной части лабораторного стенда
- 4. Способы вычисления угла поворота и скорости
- 5. Регулируемый электропривод
- Выводы
- Список источников
Введение
Данная работа посвящена исследованию микропроцессорной системы управления для регулирования механических координат двигателя постоянного тока. Особенностью работы является изучение основ управления двигателем при помощи лабораторного стенда на основе отладочной платы STM32F4.
Стенд является доработкой бакалаврского проекта по работе с инкрементальным датчиком положения.
Задачей является получение навыков по сбору и обработке научной и технической информации. Это важный навык для будущих специалистов по работ на производстве с приводами.
1. Актуальность темы
Актуальность данной работы является то, что данная разработка была собрана исключительно в обучающих целях, для подготовки студентов специальности Электромеханические системы автоматизации и электропривод
,
т.к. важно понимать и использовать информацию наиболее часто используемого – импульсного инкрементального датчика положения.
2. Разработка аппаратной части лабораторного стенда
2.1 Выбор платы
При разработке лабораторного стенда встал вопрос в выборе аппаратной платы, для реализации управления приводом. Для исполнения системы управления, необходим микроконтроллер, отвечающие следующим требованиям:
- Наличие не менее 5 аппаратных таймеров с возможностью формирования ШИМ сигнала;
- Наличие аппаратного интерфейса для связи с ПК;
- Наличие не менее 15 GPIO;
- Низкое энергопотребление;
- Возможность внутрисхемного программирования;
- Обеспечение выходного тока через порт не менее 20 мА;
- Поддержка бесплатными IDE;
- Возможность программирования, как на языках низкого уровня, так и на языках высокого уровня;
- Возможность быстрого выполнения математических операций, таких как умножение, деление, а также тригонометрических функций;
Выбор упал на 2 микроконтроллера:
- Arduino Uno
- STM32F4 Discovery
Таблица 1 – Таблица сравнения микроконтроллеров
Arduino Uno | STM32F4 Discovery | |
Рабочее напряжение | 5 В | 3-5 В |
Входное напряжение | 7-12 В | 5 В |
Цифровые входы/выходы | 14 (6 из которых могут использоваться как выходы ШИМ) | 46(16 из которых могут использоваться как выходы ШИМ) |
Аналоговые входы | 6 | 18 |
Постоянный ток через вход/выход | 50 мА | 25 мА |
Тактовая частота | 16 МГц | 168 МГц |
Габариты | 6.9х5.3 см | 9.7х6.6 см |
Цена | 186 руб | 1840 руб |
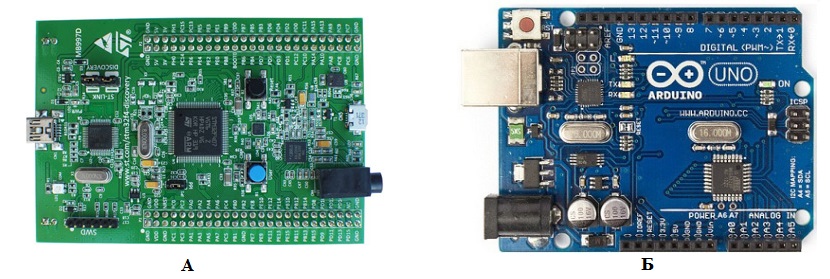
Рисунок 1 – A - STM32F4 Discovery; Б - Arduino Uno;
Для эргономичной компоновки стенда, да и нужд самого стенда, хватило бы ресурса Arduino Uno, но отсутствие встроенного квадратурного алгоритма и программного захвата ШИМ, не заставляет и раздумывать перед выбором STM32F4.
Так же хочется отметить, что созданный лабораторный стенд является уникальной разработкой в целях обучения будущих студентов кафедры Электропривод и автоматизация промышленных установок
.
И очень важно показать, один из возможных вариантов применения отладочной платы STM32F4.
2.2 Выбор драйвера
Имея микроконтроллер, следует подобрать драйвер для управления двигателем. Драйвер должен подходить по соответствующим параметрам нашему микроконтроллеру:
- Потребляемый ток встроенной логики должен выдерживать постоянный ток через выход микроконтроллера;
- Питание логики не выше рабочего напряжения контроллера;
- Иметь малые габариты;
Для моей цели подошли 2 драйвера – это L298n от компании ST и TB6612FNG производства компании Toshiba.
Таблица 2 – Таблица сравнения драйверов
L298n | TB6612FNG | |
Напряжение питания встроенной логики | 5 В | 2.7-5.5 В |
Потребляемый ток встроенной логики | 0–36 мА | 0–36 мА |
Рабочий ток драйвера | 2А (пиковый 3А) | 2А(без радиатора), 3А максимальный |
Напряжение питания драйвера | 5-35 В (максимально 46 В) | 4.5–13.5 В |
Габариты | 4.3х4.3х2.9 см | 2х1.7 см |
Цена | 229 руб | 250 руб |
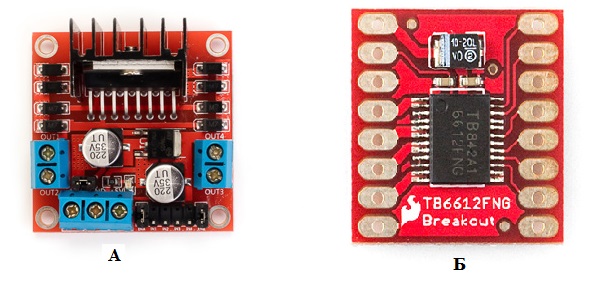
Рисунок 2 – A - L298n; Б - TB6612FNG;
Драйвер TB6612FNG имеет ряд преимуществ таких как: минимальный размер, частота ШИМ 100 кГц, температурный контроль. В сравнении с L298n, чьим аналогом является драйвер компании Toshiba, одним из важных недостатков это ограниченный диапазон напряжения питания (4.5–13.5 В), когда в L298n от 5 до 35В и максимально выдерживаемое напряжение 46 В.
Выбор был в сторону драйвера L298n, но его габариты были велики для стенда, поэтому на основе чипа L298n был разработан и изготовлен малогабаритный аналог с такими же характеристиками на Smd компонентах.
2.3 Выбор двигателя
В лабораторном стенде в качестве измеряемого органа, используем маломощный двигатель постоянного тока. Двигатель подходящий по размерам под стенд достался нам из старого принтера. Поэтому подберем схожие двигатели доступные в продаже.
Таблица 3 – Выбор двигателей из доступных в продаже.
Модель двигателя | Характеристики | ||
775 DC Motor |
|
Напряжение: 12-24В (макс 36 В); Макс. скорость: 9000 об/мин при 36 В; Номинальная скорость: 3500 об/мин при 12 В; Ток при номинальной нагрузке: 0.14 А; Размеры: 66.7х42 мм (без учета клемм питания и вылета вала); Цена: 652 руб |
|
RS-555 |
|
Напряжение: 12-24 В; Макс. скорость: 12000 об/мин при 24 В; Номинальная скорость: 6000 об/мин при 12 В; Ток при номинальной нагрузке: 0.24 А; Размеры: 57х35.8 мм (без вылета вала); Цена: 574 руб |
|
RS-550 (K825 Германия) |
|
Напряжение: 6-18В; Номинальная скорость: 10400 об/мин при 7.4 В; Ток при номинальной нагрузке: 1 А; Размеры: 60х36 мм; Цена: 630 руб |
|
390 DC Motor |
|
Напряжение: 12-24 В; Макс. скорость: 26000 об/мин при 24 В; Номинальная скорость: 13000 об/мин при 12 В; Ток при номинальной нагрузке: 0.3 А; Размеры: 50х27.6 мм (без вылета вала); Цена: 265 руб |
Из выше перечисленных моторов для робота пылесоса рекомендован двигатель постоянного тока типа 775 DC Motor. Особенностью данного двигателя является то что при напряжении 12-24 В, большой крутящий момент и низкий уровень шума.
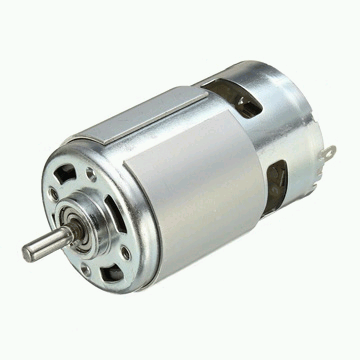
Рисунок 3 – двигатель постоянного тока типа 775 DC motor
(анимация: 5 кадров, 5 циклов повторения, 212 килобайт)
3. Разработка аппаратной части лабораторного стенда
Датчик состоит из подвижной части, соединенной с объектом измерения, и неподвижной части, относительно которой происходит измерение положения. Подвижная часть датчика представляет собой диск со штриховыми метками, нанесенными равномерно по всей окружности [5]. Количество меток определяет главный параметр датчика или его разрешение в метках на оборот Z. Неподвижная часть содержит два свето-излучателя и два свето-приемника, представляющие собой две оптопары. Диск с нанесенными на него метками помещается между излучателями и приемниками таким образом, чтобы при его вращении на выходах светоприемников получились два сигнала в форме меандра. Размещение оптопар по отношению друг к другу выполняют таким образом, чтобы меандры были смещены друг относительно друга на 90°.
4. Способы вычисления угла поворота
Существуют датчики от нескольких десятков до миллионов меток на оборот [5]. Следует отметить, что для датчиков на миллион меток на оборот стеклянный диск не содержит того же миллиона меток.
Его нарезают несколькими тысячами меток, а сигнал приходящий с оптопары, обрабатывают как аналоговый сигнал.
Этот сигнал похож на синус и косинус, его пропускают через АЦП, а затем формируют еще 1000 виртуальных
меток внутри одного периода синуса (или одной физической метки), которые потребитель видит на выходе датчика.
На один оборот датчика по каналу А поступит Z импульсов и по каналу В также поступит Z импульсов. Эти импульсы можно сосчитать с помощью схемы квадратурного декодирования, а по фазовому сдвигу между сигналами А и В вычислить направление вращения.
Помимо количества меток на оборот в паспортных данных датчиков обычно приводится параметр К – количество импульсов на оборот:

Параметр показывает, сколько счетных импульсов будет получено со схемы квадратурного декодера на одном обороте. Число импульсов оказывается в четыре раза больше, так как схема различает фронты сигналов А и В, которых на одну метку датчика приходится 4.
Квадратурный датчик положения подключается ко входам квадратурного декодера микроконтроллера – CAP1/QEP1 и CAP2/QEP2, которые могут функционировать не только в режиме квадратурного декодирования, но в режиме захвата событий. Принцип работы квадратурного декодера представлен на Pисунке 4, где показано, что значение таймера, по сути, определяет текущее положение ротора. Более сложной является задача измерения угловой скорости вращения.
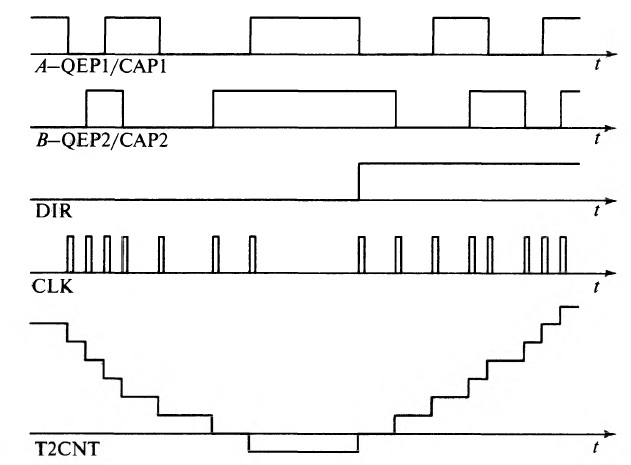
Рисунок 4 – A-QEP1/CAP1 – квадратурный сигнал канала; B-QEP2/CAP2 – квадратурный канала В; DIR – сигнал направления счета таймера; CLK – сигнал тактирования таймера; T2CNT – значение счетчика таймера.
Для измерения скорости обычно применяют два метода:
- Измерение количества импульсов за интервал времени
- Измерение времени прохождения заданного количества импульсов
Первый метод наиболее прост в реализации, но имеет существенный недостаток, связанный с тем что, импульсов с квадратурного декодера за время измерения скорости должно пройти достаточно много, чтобы обеспечить необходимую точность результата. Так сосчитав например, пять импульсов, нельзя сказать точно, что импульсов было пять. Ведь за это время может пройти как 5.1, так и 5.9 реальных меточных секторов, т.е. погрешность составит около 20%. Отсюда можно сделать вывод, что метод лучше не использовать на практике.
Второй метод сложнее реализуем, но в нем отсутствуют недостатки первого метода. Количество импульсов в этом методе величина, известная абсолютно точно. Время прохождения пакета импульсов может измеряться современными микропроцессорными средствами с точностью до значения, обратного тактовой частоте процессора, что для большинства современных DSP-микроконтроллеров семейства Motor Control составляет от 25 до 6.67 нс.
Можно сказать, что все значения, необходимые для расчета скорости, найдены точно:
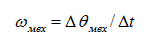
Прежде чем рассмотреть построение системы измерения скорости необходимо прояснить, какие погрешности имеет квадратурный датчик положения. В процессе измерений нужно задавать длину пакета импульсов, воспринимаемого в качестве пути измерения. Понятно, что для измерения малых скоростей разумнее выбирать малые приращения пути, однако есть ограничительные факторы, не позволяющие задавать приращение пути меньше четырех, а также все приращения не кратные четырем.
В первую очередь это объясняется тем, что метки, нанесенные на стеклянный диск датчика, могут быть неодинаковой ширины с прозрачными участками.
Такая неравномерность делает невозможным установку приращения пути равным единице (1
), так как из Pисунка 4 видно, что пути активного и неактивного состояния различны.
Из этого можно сделать вывод, что путь, на котором проводится измерения времени, должен быть кратен двум (2
), ведь только в этом случае путь от метки к метке окажется одинаковым.
Второй вид погрешности датчика связан с тем, что фаза между сигналами А и В не всегда составляет 90°, а в паспортных данных датчиков, например, ЛИР фирмы СКБ ИС допускается отклонение до ±15°, которое может быть непостоянным на обороте.
Таким образом, минимально возможный путь, который можно измерить, оказывается равным четырем (4
) – четырем импульсам датчика или одной метке.
Для измерения скорости необходимо задаться путем, измерить время прохождения заданного пути и, разделив путь на время, вычислить скорость. Очевидно, что чем меньше выбран путь (в пределе четыре импульса), тем выше полоса пропускания измерителя скорости. Однако при малых приращениях положения на высоких скоростях увеличивается погрешность измерения времени. Если время измеряется с точностью 6,67 нс в современных микроконтроллерах с частотой 150 МГц, то точностью измерения времени в четыре десятичных разряда можно получить за 66,7 мкс, т.е. время прохождения пути в четыре импульса или одну метку не должно быть меньше.
5. Регулируемый электропривод
Одноконтурная схема регулирования скорости ДПТ.
Система регулирования содержит:
- Измерительно-преобразующую часть, представляющее собой датчик скорости (ДС) и датчик тока (ДТ);
- Регулирующую часть, включающую регулятор скорости (РС) и функциональный преобразователь (ТО) в цепи обратной связи по току.
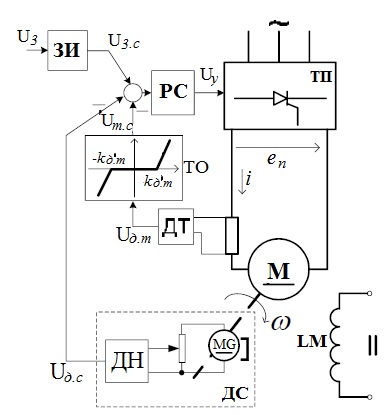
Рисунок 5 – Функциональная схема одноконтурной системы регулирования скорости ДПТ
На входе регулятора скорости (РС) выполняется алгебраическое суммирование сигнала задания скорости UЗ.с и сигналов обратных связей. Постоянно действующая отрицательная ОС по скорости используется для организации контура регулирования скорости. Отрицательная ОС по току ввиду наличия токовой отсечки ТО вступает в работу только при превышении током двигателя некоторого максимального значения Іотс, уменьшая входной сигнал РС. Соответствующая структурная схема системы приведена на Рисунке 6. Датчик скорости принят безынерционным.
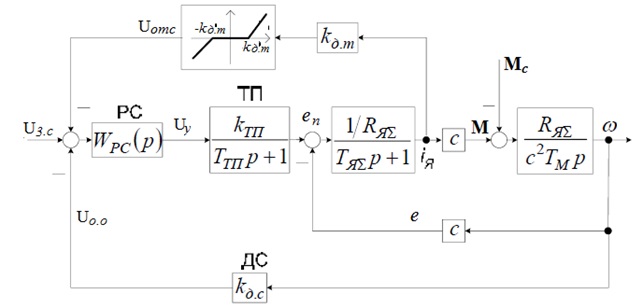
Рисунок 6 – Структурная схема одноконтурной системы регулирования скорости ДПТ
Регулирование скорости в двухконтурной однократно-интегрирующей СПР
Функциональная схема двухконтурной системы подчиненного регулирования скорости представлена на Рисунке 7. Регулирующая часть системы содержит задающее устройство (обычно это задатчик интенсивности), внешний контур регулирования скорости двигателя (регулятор скорости РС) с подчиненным ему внутренним контуром регулирования тока (регулятор тока РТ).
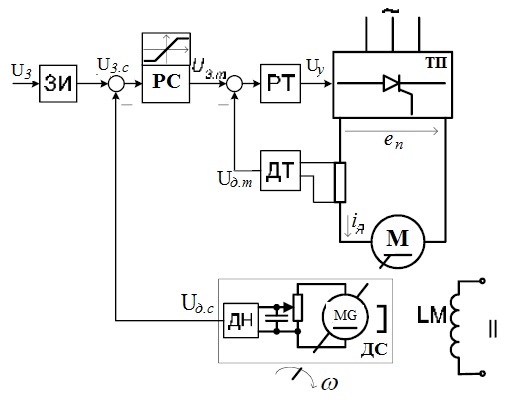
Рисунок 7 – Функциональная схема двухконтурной системы подчиненного регулирования скорости
Измерительно-преобразующая часть обеспечивает передачу в систему регулирования напряжений обратных связей, пропорциональных току якорной цепи и скорости вращения вала двигателя. Для измерения тока в цепи питания обмотки якоря предусматривают шунт (при небольших токах), при больших токах, используют измерительные трансформаторы тока на стороне переменного напряжения. Выходное напряжение шунта (как правило, до 75 мВ) поступает на ячейку датчика тока ДТ, выполняющую согласование по уровню сигнала ОС по току с напряжением системы регулирования. Для измерения скорости обычно используют тахогенератор ТГ (чаще постоянного тока) либо цифровой датчик. Выходной сигнал ТГ поступает на ячейку датчика напряжения ДН, выполняющего функции фильтрации, согласования и гальванической развязки. Соответствующая структурная схема СУЭП представлена на Рисунке 8.
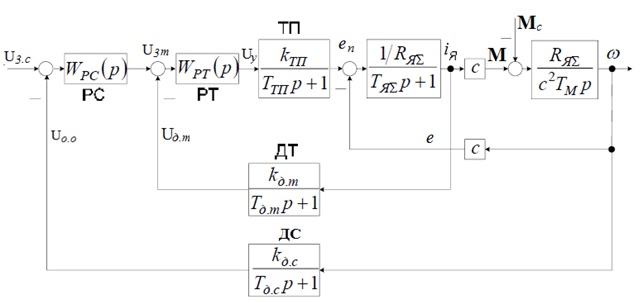
Рисунок 8 – Структурная схема системы управления электроприводом
Коэффициенты передачи датчиков тока ДТ и скорости ДС в предположении о линейности их характеристик, могут быть вычислены по формулам:

где Uд.т.max – максимальное выходное напряжение ячейки датчика тока; Uд.c.max – максимальное значение выходного напряжения датчика скорости; Imax – максимальное значение тока якоря, которое должно быть измерено. При проектировании системы датчик обычно выбирают из условия измерения тока упора (стопорения) Iyn с запасом на динамику: Imax ≥ (1.1…1.25)Iyn ; ωmax – максимальное значение скорости в системе, которое должно измеряться с помощью датчика. В однозонных системах регулирования скорости обычно принимают (с запасом на динамику): ωmax ≥(1.05…1.1)ω0 , где ω0 – скорость идеального холостого хода двигателя.
Выводы
В процессе написания обзора по теме Исследование микропроцессорной системы управления для регулирования механических координат двигателя постоянного тока
были выбраны двигатели постоянного тока типа 775 DC motor, драйвер L298n и отладочная плата STM32F4.
Были изучены способы вычисления угла поворота, а также принцип построения регулируемого электропривода.
Внешний вид стенда, и демонстрация его работы
На момент написания данного реферата магистерская работа еще не завершена. Ориентировочная дата завершения магистерской работы: май 2018 года. Полный текст работы и материалы по теме могут быть получены у автора или его руководителя после указанной даты.
Список источников
- STM32F4 Discovery Datasheet [Электронный ресурс] – Режим доступа: http://www.st.com/content/st_com/en/products/evaluation-tools/product-evaluation-tools/mcu-eval-tools/stm32-mcu-eval-tools/stm32-mcu-discovery-kits/stm32f4discovery.html
- L298N Datasheet (PDF) – STMicroelectronics [Электронный ресурс] – Режим доступа: http://html.alldatasheet.com/html-pdf/22440/STMICROELECTRONICS/L298N/1619/1/L298N.html
- Arduino Uno Datasheet [Электронный ресурс] – Режим доступа: http://arduino.ru/Hardware/ArduinoBoardUno
- TB6612FNG Datasheet [Электронный ресурс] – Режим доступа: http://html.alldatasheet.com/html-pdf/807693/TOSHIBA/TB6612FNG/296/1/TB6612FNG.html
- Анучин А.С. Системы управления электроприводов: учебник для вузов. – М.: Издательский дом МЭИ, 2015. &ndash c.373 137-140.
- 775 DC Motor Datasheet [Электронный ресурс] – Режим доступа: http://www.dsdmotor.com/ProductShow.asp?ID=271
- RS-555 Datasheet [Электронный ресурс] – Режим доступа: https://www.robotshop.com/en/rs-555-12v-6100-rpm-brushed-dc-motor.html
- RS-550 Datasheet [Электронный ресурс] – Режим доступа: http://www.robotstorehk.com/rs_550pcvc.pdf
- 390 DC motor Datasheet [Электронный ресурс] – Режим доступа: https://www.robotshop.com/forum/data-sheets-for-mabuchi-rs-390-and-rs-395-dc-motors-t12037