Реферат
- Введение
- 1 Актуальность темы
- 2 Цели и задачи исследования,планируемые результаты
- 3 Описание конструкции
- 4 Обзор исследований по теме
- 5 Основная часть
- Вывод
- Список источников
Введение
В настоящее время идет бурное развитие технологий. Появляются все новые и новые возможности для проведения тех или иных операций, связанных как с повседневными делами, так и в области медицины, сельского хозяйства и металлургии. В металлургии идет развитие старых способов работы с металлами, но и появляться совершенно новые технологии и методы.
Развитие металлургии, тесно связано с возрастающими потребностями человечества в металле, он используется повсеместно: в жилых постройках, в транспорте, в вещах, созданных человечеством для удобства, для исследований, в космической промышленности и т.д.
Только в 2015 году во всех странах мира было выпущено около 1622,80 млн.т. стали. И с каждым годом данная цифра увеличивается. Самым крупным производителем стали является Китай. Его доля выпускаемой стали является половиной от всей продукции созданной на планете.
1 Актуальность темы
В современной металлургии основными способами выплавки стали являются кислородно-конвертерный, мартеновский и электросталеплавильный.
Выплавка стали в электрических печах имеет ряд преимуществ по сравнению с другими сталеплавильными процессами. Основные преимущества – это возможность создания высокой температуры в плавильном пространстве печи (более 2000°С) и выплавки стали и сплавов любого состава, использование известкового шлака, способствующего хорошему очищению металла от вредных примесей серы и фосфора.
Для достижения экономического эффекта все механизмы электродуговой печи должны безотказно функционировать. Обеспечение их работоспособности достигается техническим обслуживанием и ремонтами с применением средств и методов технической диагностики для своевременного распознавания состояния деталей и узлов и поиска развивающихся неисправностей. Это обуславливает актуальность темы исследований.
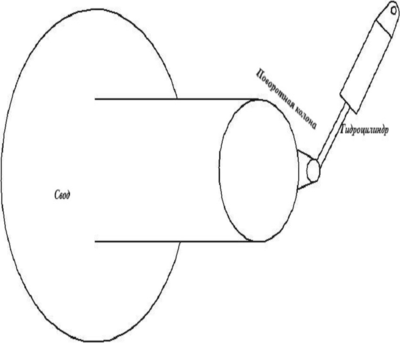
Анимация 1 – Процес поворота колонны. (Рисунок анимирован. Количество кадров 8, size 134kb.)
2 Цели и задачи исследования, планируемые результаты
Целью моей работы является разработка алгоритма диагностирования опорного кольца подъемно-поворотной колонны свода электродуговой печи.
Для этого были поставлены задачи:
- Проанализировать конструкции электродуговой печи
- Выполнить анализ видов и причин неисправностей опорного кольца
- Разработать математическую модель нагружения опорного кольца и рассчитать силы действующие на опорное кольцо
- Провести ряд эксперементов на модели опорного кольца для подтверждения математической модели
- Разработать последовательность действий для распознавания технического состояния опорного кольца
3 Описание конструкции
В конструкции механизма поворота свода электродуговой печи часто используется опорное кольцо [1, 2] на котором устанавливается поворотная колонна с приводом при помощи гидроцилиндра (рисунок 1).
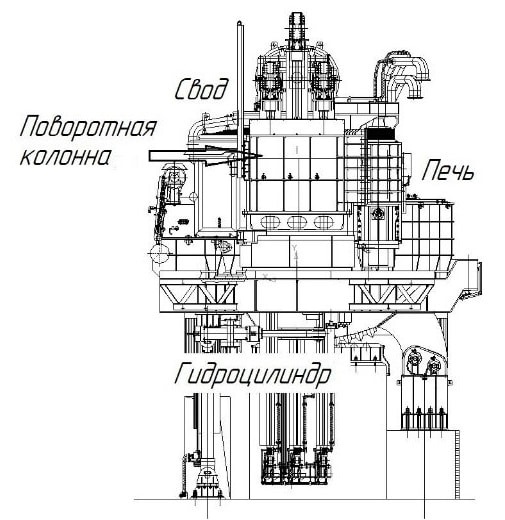
а
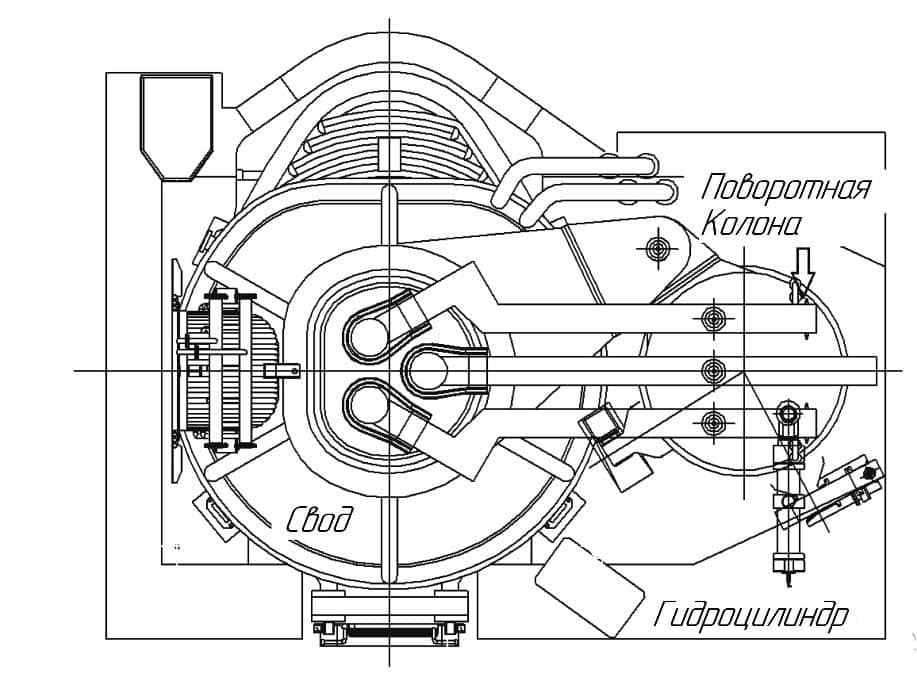
б
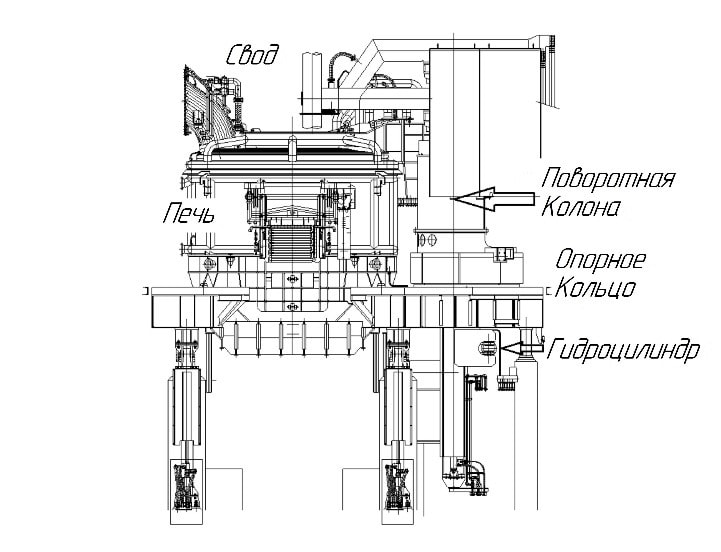
в
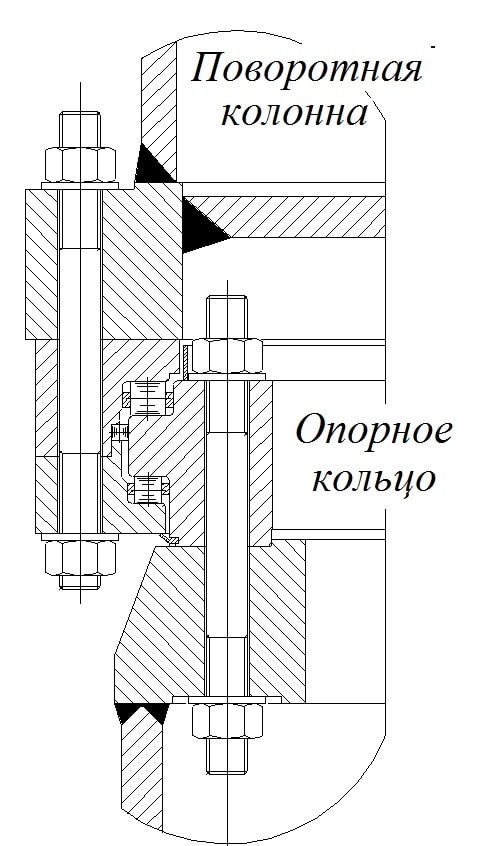
г
Рисунок 1 – Схема расположения механизма поворота свода относительно конструкций электродуговой печи: а) вид от газоотвода; б) вид от рабочего окна; в) вид сверху; г) опорное кольцо
Поворот свода на угол 70…90 осуществляется при помощи гидроцилиндра, шток которого крепится к рычагу поворотной колонны (рисунок 1г). Колонна, соединена со сводом печи, имеющим возможность вертикального перемещения. Для поворота колонны на раме печной платформы установлено трехрядное роликоподшипниковое поворотное кольцо (рисунок 1в). Диаметр опорного кольца составляет 2,5…3,5 м, высота 150…190 мм. Замена опорного кольца приводит к длительной остановке сталеплавильного комплекса: обычно состояние ухудшается внезапно, срок изготовления кольца по индивидуальному заказу составляет 3…4 месяца, длительность замены составляет 3…5 суток из-за необходимости демонтажа и установки поворотной колонны и всех расположенных в ней механизмов.
4 Обзор исследований по теме
Наиболее эффективным и перспективным методом получения стали в настоящее время является выплавка в электродуговой печи. Развитие механического оборудования электродуговых печей привело практически к полному отказу от электромеханического привода. В современных конструкциях печей преобладает гидравлический привод, к достоинствам которого следует отнести реализацию поступательного движения, малые скорости передвижения, минимизацию динамических процессов, создание значительных сил при малых габаритах, возможность бесступенчатого регулирования скорости движения. Данные преимущества гидропривода позволяют наиболее полно использовать их в механизмах: подъёма и поворота свода, наклона печи, перемещения электродов. Одновременно с этим возникает задача изучения эксплуатационных свойств гидропривода в специфических условиях металлургического производства. В статье выполнен анализ характерных повреждений механизмов 120-титонной электродуговой печи с гидравлическим приводом для определения направлений повышения безотказности данного класса оборудования
Основные технические характеристики механизма поворота свода 120-титонной электродуговой печи: угол поворота свода — 95°; скорость поворота свода — 5 °/с; масса свода — 50 т. Для поворота колонны со сводом на раме печной платформы установлено трёхрядное роликоподшипниковое опорное кольцо (рисунок 1) — опорный подшипник. Свод печи соединен с колонной и имеет возможность вертикального перемещения. На поворотной колонне установлены также механизм перемещения электродов и механизм перемещения свода.
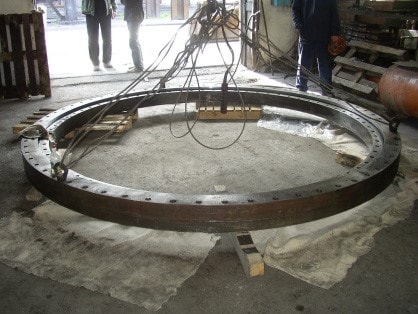
а
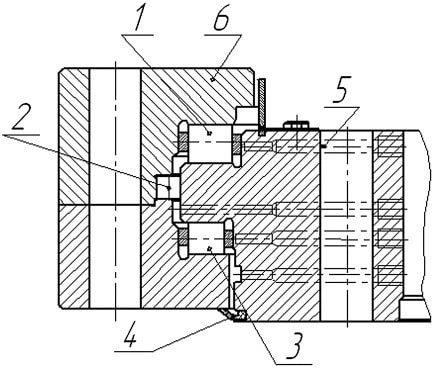
б
Рисунок 2 — Трёхрядное роликоподшипниковое поворотное кольцо разливочного крана а) общий вид; б) конструкция: 1 — опорные ролики; 2 — радиальные ролики; 3 — контропорные ролики; 4 — уплотнение; 5 — неподвижное кольцо; 6 — подвижное кольцо.
Дальнейший визуальный осмотр опорного подшипника указал на абразивный износ элементов верхнего ряда роликов, при этом износ радиальных и контропорных роликов отсутствовал. На поверхности опорных роликов зафиксирована плёнка продуктов коксования смазочного материала (рисунок 3).
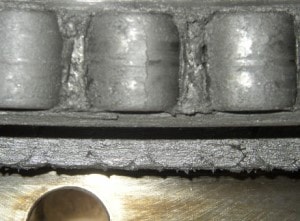
Рисунок 3 — Плёнка продуктов коксования смазочного материала
Сделан вывод, что изнашивание опорных роликов вызвано окислением (коксованием) смазочного материала [6] и накоплением продуктов износа в застойной зоне верхнего ряда роликов. Это привело к ускоренному износу опорных роликов и их беговых дорожек и неравномерному распределению сил между телами качения, которое вызвало перекос роликов, прекращение перекатывания тел качения, деформацию роликов верхнего ряда и повреждение сепаратора (рисунок 4).
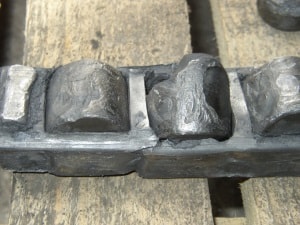
Рисунок 4 — Повреждения сепаратора и деформация роликов
Анализ давления в полостях гидроцилиндра осуществлялся на основании графиков параметров движения свода, предоставляемых системой автоматизированного управления. Для контроля за изменением давления выбраны следующие участки движения: начало движения свода при открытии; установившееся движение свода при открытии; начало движения свода при закрытии; установившееся движение свода при закрытии. Контроль осуществлялся ежедневно при выборе случайной реализации одного цикла открытия и закрытия свода в течение одних суток. На рисунке 5 приведены типовые графики параметров движения свода. Рассмотрение представленных кривых позволяет выделить ряд характерных тенденций изменения параметров.
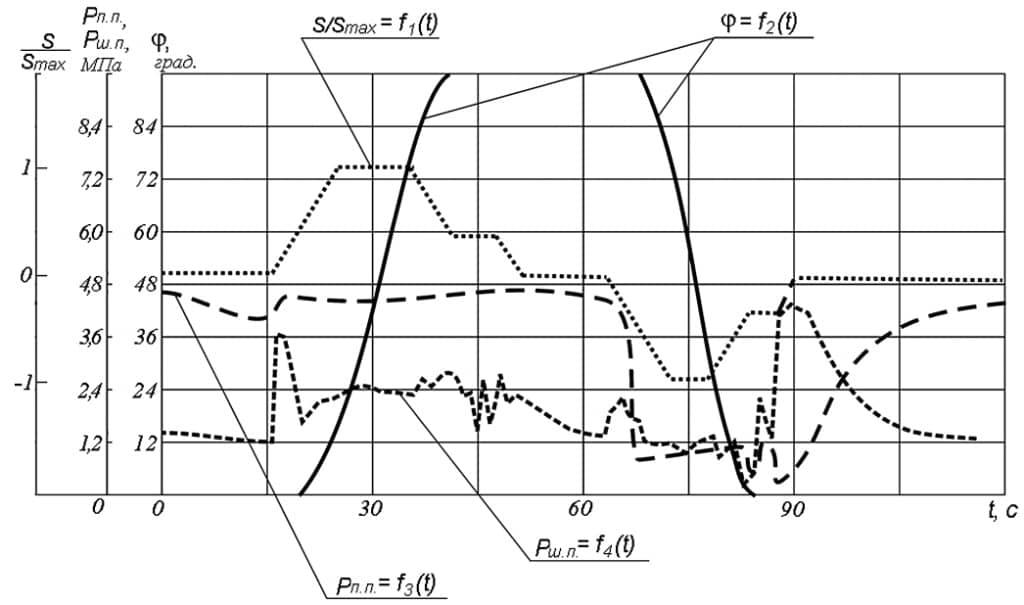
Рисунок 5 типовые графики параметров движения свода
Начало движения свода при открытии сопровождается повышением давления в штоковой полости с последующим снижением давления при начале движения. Это позволяет оценить соотношение между коэффициентом трения покоя и коэффициентом трения движения в опорном подшипниковом кольце. В среднем эти коэффициенты отличаются в два раза. Рассмотрение изменения давления в поршневой полости указывает на то, что при закрытии свода такое явление не наблюдается. Это может быть связано с малым временем остановки при открытии свода и отсутствием воздействия вибрационных колебаний от горящей дуги. При остановке свода в открытом положении наблюдаются динамические колебания, связанные с податливостью элементов крепления.
Проведенные измерения давления в октябре 2008 года и в январе 2009 года позволили установить, что давление в штоковой полости для точки начала движения свода увеличилось от 5,5 до 6,3 МПа, а для установившегося движения от 2,4 до 3,2 МПа; давление в поршневой полости также увеличилось от 8,0 до 9,5 МПа при установившемся движении свода.
Исходя из этих данных, рассчитаны сила при открывании свода печи — 159,5…182,7 кН (при начале движения) и 70,2…91,6 кН (при установившемся движении); сила при закрытии свода — 392,0…465,5 кН. Таким образом, увеличение давления за период октябрь 2008 года — январь 2009 года составило 14…18 %. В то же время сила, необходимая при закрытии в 2,5 раза больше силы при открывании свода, что может быть следствием отклонения от вертикальности поворотной колонны и рамы основания. Предположение об отклонении от вертикальности оси поворотной колонны подтвердилось после анализа результатов геодезической съёмки.
Значение коэффициента сопротивления , рассчитанного исходя из полученных данных, превышает принимаемое при расчетах значение
более чем в 10 раз. Это позволило утверждать, что в подшипниковом узле произошли необратимые изменения, а техническое состояние его элементов отклонилось от нормального (перешло в другую категорию).
На основании данных фактов в мае 2009 года и была проведена плановая замена опорного кольца, подтвердившая правильность принятой методики контроля его технического состояния. Следующее 10-тикратное увеличение коэффициента и, соответственно, момента сопротивления могли свидетельствовать об аварийном состоянии подшипникового кольца.[7]
5 Основная часть
Исходными данными являются суммарная вертикальная нагрузка Fa и суммарный опрокидывающий момент Мk (рисунок 6а). Исходя из эмпирического графика допустимых значений нагрузки для базовых 30000 циклов (рисунок 6б) определяется коэффициент нагрузки подшипника fL для вертикальной нагрузки Fa и опрокидывающего момента Мk:
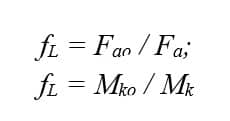
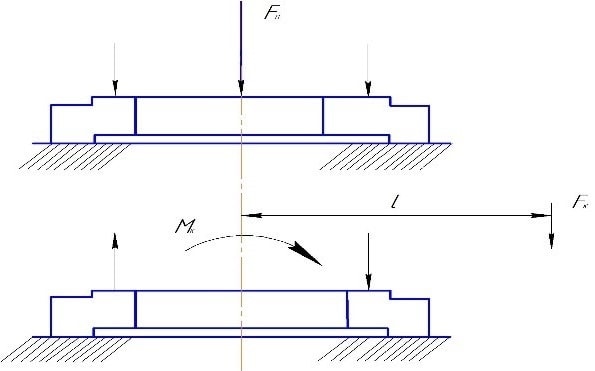
Рисунок 2a
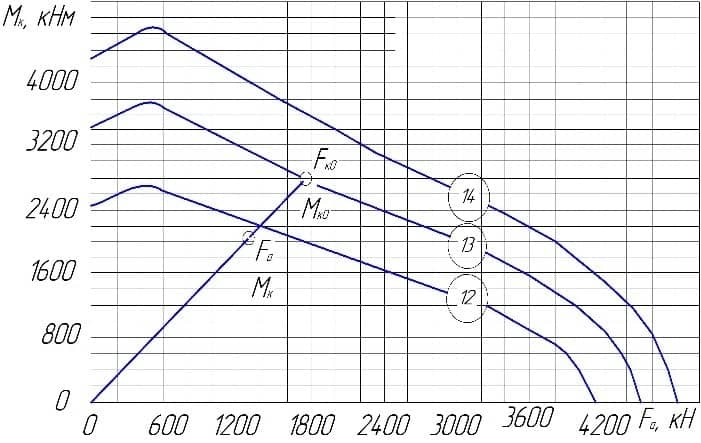
Рисунок 2б
Рисунок 6 - Схема к определению коэффициента нагрузки опорного кольца с условным обозначением 13: а) расположение действующих сил;б) график допустимых значений нагрузки для различных размеров опорных колец с условными обозначениями - 12, 13, 14
Полученное значение использовались для определения срока службы опорного кольца, как допустимого числа циклов работы, рассчитываемого по формуле:
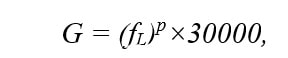
где р = 3 – показатель степени.
Данный подход является типовым для определения долговечности опоных колец, работающих в длительном или повторно-кратковременном режиме работы с полным поворотом. Расчётный срок службы выполненный для условий ЭДП-120 и ДСП-50 составляет соответственно 5,6 лет и 48,2 года. Фактический срок службы опорных колец составил 4,2 года для ЭДП-120 и 3,1 года для ДСП-50. Если расхождение в 30% для ЭДП-120 вполне допустимо, то 15-ти кратная ошибка для условий ДСП-50 показывает, что методика не учитывает всех факторов работы опорного кольца в составе механизма поворота свода, в частности ограниченный угол поворота, значительную консольную нагрузку и воздействие динамических сил.
Работа опорного кольца связана с воздействием консольной нагрузки, частыми поворотами, односторонним нагревом от дуговой печи и раскалённого свода, запылённой атмосферой и вибрациями при работе электрической дуги. Перспективным является разработка методики расчёта учитывающей фактическое распределение нагрузки в элементах опорного кольца [3] и эксплуатационные воздействия, снижающие долговечность [4]: повышенная температура, вибрация, повышенное трение и неравномерное распределение нагрузки между телами качения.
Установлено, что преобладающим в опорном кольце является осповидное выкрашивание и абразивный износ в ограниченном секторе. Последовательность развития разрушения связана с нарушениями режима смазывания и в общем случае включает:
- окисление смазочного материала под действием температуры и нарушение движения смазочного материала
- воздействия электрической дуги, особенно в период плавки
- в смешивании окисленного смазачного материала и продуктов износа, приводящих к ускорению абразивного износа
Редкое смазывание (1 раз в 2…3 суток) и повышенная температура опорного кольца приводят к коксованию смазки. Проведенные измерения температуры в районе опорного кольца показали значения 60…800С, что и приводит к окислению смазки. Контроль температуры опорного кольца показал целесообразность использования воздушного охлаждения опорного кольца в летний период, обеспечивая снижение температуры до 55…600С.
Отслоившиеся частицы металла присутствуют в опорном кольце из-за осповидного износа тел качения и беговых дорожек возникающего при переменных нагрузках и высоких давлениях, превышающих предел выносливости. Накопление продуктов износа в смазке приводит к интенсивному абразивному износу. Вторичными признаками развития повреждений, приводящие к заклиниванию опорного кольца являются: повреждения и разрушения сепаратора, деформация и разворот роликов вдоль беговой дорожки.
Определение закономерностей распределения нагрузок в элементах опорного кольца проведено на основании результатов измерений значений износа. Установлено, что кольца подшипника в секторе 90…1200 не имеют следов износа. Характер износа – однотипен.
Износ верхнего поворотного кольца опорного подшипника расположен симметрично относительно оси свода. Сектор износа верхнего поворотного кольца опорного подшипника меньше, а глубина износа больше по сравнению с неподвижным кольцом. Зависимость между износом и удалением от наиболее нагруженной зоны носит линейный характер.
Износ верхнего поворотного кольца опорного подшипника больше, чем износ неподвижного кольца. Верхний ряд опорных роликов перемещался с проскальзыванием относительно поворотного кольца. Зависимость между износом и удалением от наиболее нагруженной зоны носит линейный характер и выражается функцией:

где yВ, yС – износ верхнего и среднего колец; x – угловая координата.
Преобладание абразивного износа позволяет использовать предположение о пропорциональности между распределением сил на тела качения и диаграммой распределения износа верхнего поворотного кольца, в случае преобладания абразивного износа. Исходя из данного предположения, проведен расчёт фактических напряжений в зоне контакта. Полученные значения 1300…1500 МПа в 2,5…3,1 раза меньше предельного значения 4000 МПа указанного в стандарте [5].
Конкретные значения сектора и глубины износа различны. Однако, результаты расчёта по определению напряжений в зоне контакта показали, что максимальные нормальные напряжения имели один уровень значений. Следовательно, статическая нагрузка не могла послужить причиной возникновения осповидного выкрашивания.
Вибрация опорного кольца изменяется частотой и формой колебаний по режимам работы. Эти различия связаны с технологическими периодами работы электрической дуги. Реализации по этапам плавки отличаются изменением амплитудных значений от 1,8…3,0 в режиме доводки до 5,5…14,2
при начале плавки. При работе электрической дуги зафиксированы значения виброскорости 73
в размахе. Поэтому, снижение срока службы опорного кольца по сравнению с расчётным, связано с увеличенной вибрацией и появлением динамической нагрузки. Ориентировочно оценить значение динамической составляющей можно по формуле:

где m – масса поворотной колонны
Вывод
Составление алгоритма диагностирован опорного кольца подьемно-поворотной колоны электродуговой печи не завершено, он будет окончательно сделан в июне 2018 Года.Полный текст работы и материалы по ее теме могут быть получены у автора или его руководителя.
Список литератури
- Воскобойников В.Г., Кудрин В.А., Якушев А.М.
Общая металлургия: учебник для вузов
;Воскобойников В.Г., Кудрин В.А., Якушев А.М. - 6-изд., перераб и доп. - МИКЦ Академкнига
, 2005 - 768 с.
- Rothe Erde GmbH. D-44137. Dortmund. 2004. – 172 c.
- Сидоров В.А., Аввакумов С.И., Шепель В.М., Золкин И.Г. Определение характера распределения нагрузок в элементах металлургических машин по износу деталей. Научно-технический и производственный журнал
Металлургическая и горнорудная промышленность
№1, 2006 г. - С. 99 - 102
- Сидоров В.А. Ускоренный износ опорного кольца свода электродуговой печи
Сталь
. 2015 г. № 5. С. 71-75
- ГОСТ 18854-94. Подшипники качения. Статическая грузоподъемность. Введ. с 01.09. 1996. - М.: ИПК Издательство стандартов, 1996. – 18 с.
- RENOLIT CXI 2
- Кожевников С.Н. Гидравлический и пневматический приводы металлургических машин С.Н.Кожевников, В.Ф.Пешат. – Машиностроение, 1973. – 360 с.
- Воскобойников В.Г., Кудрин В.А., Якушев А.М.
Общая металлургия: учебник для вузов
;Воскобойников В.Г., Кудрин В.А., Якушев А.М. - 6-изд., перераб и доп. - МИКЦАкадемкнига
, 2005 - 768 с. - Rothe Erde GmbH. D-44137. Dortmund. 2004. – 172 c.
- Сидоров В.А., Аввакумов С.И., Шепель В.М., Золкин И.Г. Определение характера распределения нагрузок в элементах металлургических машин по износу деталей. Научно-технический и производственный журнал
Металлургическая и горнорудная промышленность
№1, 2006 г. - С. 99 - 102 - Сидоров В.А. Ускоренный износ опорного кольца свода электродуговой печи
Сталь
. 2015 г. № 5. С. 71-75 - ГОСТ 18854-94. Подшипники качения. Статическая грузоподъемность. Введ. с 01.09. 1996. - М.: ИПК Издательство стандартов, 1996. – 18 с.
- RENOLIT CXI 2
- Кожевников С.Н. Гидравлический и пневматический приводы металлургических машин С.Н.Кожевников, В.Ф.Пешат. – Машиностроение, 1973. – 360 с.