Реферат по теме выпускной работы
Содержание
- Введение
- 1. Актуальность темы
- 2. Цель и задачи исследования
- 3. Описание технологического процесса синтеза аммиака
- 3.1 Анализ процесса синтеза аммиака как объекта управления
- 3.2 Анализ существующих решений
- 4. Моделирование и анализ результатов
- 4.1 Разработка структуры САУ колонной синтеза
- 4.2 Получение математической модели объекта
- 4.3 Результаты моделирования
- Выводы
- Список источников
Введение
Одной из важнейших задач, которые стоят перед каждым предприятием, является неуклонное повышение качества продукции, совершенствование технологии производства, повышение надежности и долгосрочности изделий.
Современные химико-технологические процессы отличаются сложностью и большой скоростью протекания, а также вредностью условий работы, взрыво- и пожароопасных веществ, которые перерабатываются. С увеличением нагрузки на аппараты с целью повышения объемов производства, осуществлять управление технологическими процессами при высоких давлениях и температурах, а также скорости химических реакций без использования современных разработок в области автоматизации становится невозможно. Отклонения параметров процесса от жестко заданных норм может привести не только к потере качества готовой продукции, порчи сырья, вспомогательных веществ (например, катализаторов), но и к аварийной ситуации, включая пожары, взрывы, выбросы большого количества вредных веществ в окружающую среду.
1. Актуальность темы
Использование средств и систем автоматизации позволяет повысить основные показатели эффективности производства. Кроме того, на современном этапе развития систем автоматического управления также возникает необходимость в повышении качества и надежности управления и создании комплексных систем, включающих в себя контроль, регулирование, сигнализацию и блокировку технологических параметров с помощью новейших аналитических и технических средств.
Таким образом, разработка новых и модернизация существующих систем управления химическими процессами является актуальной задачей. И для решения этой задачи необходимо выполнить анализ процесса синтеза аммиака с целью определения способов повышения качества готового продукта и управления.
2. Цель и задачи исследования, планируемые результаты
На основе анализа существующих решений и особенностей технологического процесса синтеза аммиака в четырехполочной колонне можно сделать вывод, что для поддержания протекания процесса в рамках технологического регламента необходимо выполнять стабилизацию температур в слоях катализатора в жестко заданных пределах при наличии действия возмущающих влияний.
Главная цель исследования – повышение эффективности процесса синтеза аммиака за счет разработки системы управления температурой в слоях катализатора с учетом особенностей функционирования объекта (транспортное запаздывание) и возмущающего воздействия. Для достижения данной цели необходимо решить следующие задачи:
- Анализ состояния вопроса автоматизации процесса синтеза аммиака.
- Разработка структуры системы управления с учетом взаимосвязей параметров и влияния внешнего возмущения на температуру в слое катализатора на примере первой полки;
- Выбор регуляторов степени открытия заслонок на байпасных потоках, разработка алгоритмов функционирования системы управления, которые позволяют поддерживать оптимальную температуру в длительном периоде времени;
- Проверка адекватности, разработанной САУ методами математического моделирования.
Таким образом, САУ позволит обеспечить качество управления температурой в слоях катализатора колонны синтеза за счет повышения динамической точности и времени установления управляемых величин, что в свою очередь позволит повысить производительность колонны синтеза аммиака и увеличить максимальный объем целевого продукта.
3. Описание технологического процесса синтеза аммиака
На сегодняшний день разработаны и внедрены разнообразные технологические схемы синтеза аммиака с использованием широкого спектра давлений и катализаторов, работающих в основном в условиях высоких температур. Численные эксперименты и практика промышленного производства показали, что наиболее оптимальным с точки зрения использования сырья и экономических затрат является использование реакторов синтеза аммиака большой единичной мощности, которые работают под давлением (250-320 атм). В таких технологических схемах исходным сырьем для производства аммиака является природный газ и азот, который выделяется из атмосферного воздуха.
Весь процесс синтеза аммиака представляет собой сложное производство в рамках нескольких блоков, поэтому в данной работе будет рассматриваться только одна из его важнейших частей – получение аммиака реакторе (колоне синтеза).
На рис. 1.1 изображены процессы, протекающие при синтезе. В табл.1.1 приведено назначение аппаратов и описание проходящих в них процессов.
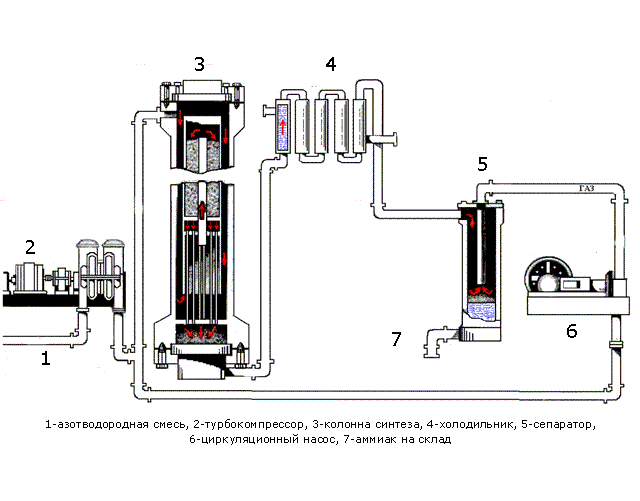
Рисунок 1.1 – Процесс синтеза
(анимация: 12 кадров, 31.9 килобайт)
Таблица 1.1 – Назначение аппаратов и протекающие в них процессы
Аппарат | Назначение аппарата и протекающие в нем процессы |
Трубопровод | Подаётся предварительно готовая смесь, состоящая из 3 обьемных частей водорода и одной объемной части азота. |
Турбо-компрессор | Азотводородная смесь сжимается до определённого давления, необходимого для данного процесса |
Колонна синтеза | Колонна синтеза предназначена для проведения процесса синтеза аммиака. В контактном аппарате расположены полки с катализатором. Процесс синтеза является сильно экзотермическим, протекает с большим выделением тепла, часть которого расходуется на нагревание поступающей азотоводородной смеси. Смесь, выходящая из колонны синтеза, состоит из аммиака (20-30%) и непрореагировавших азота и водорода. |
Холодильник | Предназначен для охлаждения смеси. Аммиак легко сжимаем, при высоком давлении превращается в жидкость. При выходе их холодильника образуется смесь, состоящая из жидкого аммиака и непрореагировавшей азотоводородной смеси. |
Сепаратор | Предназначен для отделения жидкого аммиака от газообразной фазы. Аммиак собирается в сборник, расположенный в нижней части сепаратора |
Циркуляционный насос | Возвращает непрореагировавшую смесь в контактный аппарат, что позволяет увеличить использование смеси до 95%. |
Аммиако-провод | Предназначен для транспортировки жидкого аммиака на склад. = |
3.1 Анализ процесса синтеза аммиака как объекта управления
Поскольку химические реакции в слоях катализатора протекают длительное время, то объект управления можно отнести к классу объектов с транспортным запаздыванием. Кроме того, на температуры в слоях катализатора влияют различные возмущающие воздействия. Наиболее значимым влиянием обладает концентрация аммиака на входе в реактор. В процессе анализа было выявлено, что поскольку все процессы происходят в рамках одного рабочего тела, то подача байпасного газа в любую полку будет оказывать влияние и на реакции в остальных. Таким образом, процесс синтеза аммиака представляет собой многосвязный объект управления при наличии возмущений. .
На рис. 1.2 представлены схема четырехполочной колонны синтеза аммиака как объекта управления(рис.1.2-а) и структурная схема взаимосвязей параметров объекта (рис.1.2-б)
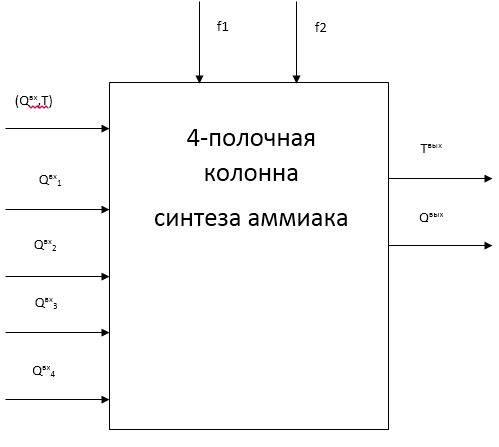
Рисунок 1.2-a – Схема четырехполочной колонны синтеза аммиака как объекта управления
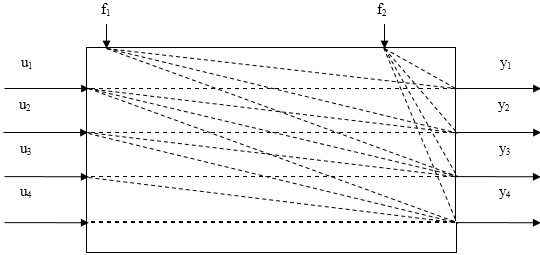
Рисунок 1.2-б – структурная схема взаимосвязей параметров объекта
На рис.1.2-а приняты следующие обозначения:
- (Qвх,Т) – расход, концентрация аммиака и температура входной азотоводородной смеси соответственно;
- Qвх1-4 – расход холодного байпасного газа;
- F1 – концентрация аммиака во входной смеси;
- F2 – соотношение водород /азот;
- Qвых - концентрация аммиака во выходящем газе;
- Tвых - температура выходящего газа.
На рис.1.3-б обозначены:
- u1 – u4 – степени открытия заслонок на байпасных потоках (управляющие параметры);
- y1 – y4 – температура в слоях катализатора (управляемые параметры);
- f1, f2 – концентрация аммиака и соотношение водород/азот (возмущающие воздействия)
- F2 – соотношение водород /азот;
Целью процесса синтеза аммиака в четырехполочном реакторе аксиального типа является получение газообразного аммиака с заданной концентрацией на выходе из реактора. В промышленных условиях, принимая во внимание достаточно большую инерционность изменения концентрации, а также из-за значительных трудностей при ее измерении непосредственно в слоях катализатора реактора, процесс проводят путем стабилизации температуры в регламентных пределах по слоям с учетом изменения степени открытия заслонок на байпасных потоках.
3.2 Анализ существующих решений
Наиболее близким решением к исследуемой системе по технической сущности и необходимому эффекту является система, приведенная на рис.1.3. Данное решение для системы управления включает в себя датчики расхода, давления, температуры и состава циркуляционного газа на входе колонны синтеза, датчики температуры в слоях катализатора, регуляторы степени открытия клапанов в линиях байпасных потоков и вычислительное устройство. Регулирование температур (в соответствии с типичным ПИД-законом регулирования) в слоях катализатора осуществляется путем изменения подачи циркуляционного газа и байпасных потоков в зависимости от расхода, давления, температуры и состава газа на входе в колонну синтеза, заданным и измеряемым значением температур в слоях.
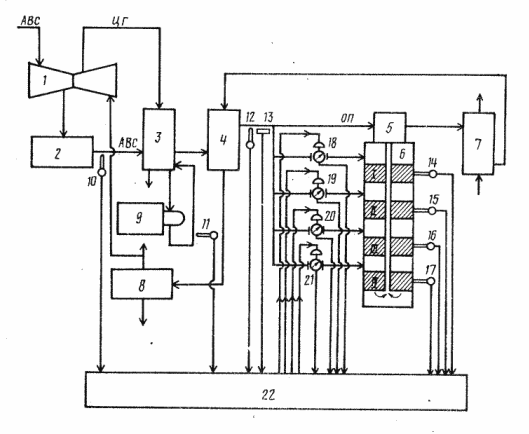
Рисунок 1.3 – Схема управления процессом синтеза аммиака с ПИД–регулятором
Алгоритм предназначен для стабилизации температурного режима колонны синтеза в процессе производства аммиака путем изменения положения клапанов на "холодных байпасах" в зависимости от отклонения текущих температур по каждой полке от заданных. Расчет величины управляющего влияния на изменение положения клапана по каждому байпасу выполняется на основании решения системы уравнений, которые представляют собой зависимость приращения температур газа на выходе из полок колонны синтеза от изменения степени открытия клапанов на соответствующих байпасах. Поскольку в процессе эксплуатации объект управления изменяет свои характеристики, то возникла необходимость в корректировке коэффициентов модели. Корректировка коэффициентов проводится непосредственно в процессе эксплуатации. .
Недостатком приведенной системы является неудовлетворительное качество регулирования температуры в слоях катализатора, которое снижает производительность колонны синтеза аммиака из-за отсутствия компенсации внешнего возмущения по концентрации аммиака.
Существует так же класс разработок на основе использования fuzzy-регуляторов для управления исследуемым процессом (рис 1.4).
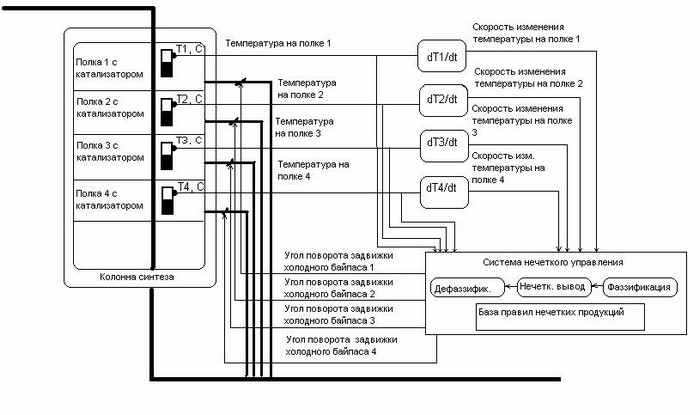
Рисунок 1.4 – Схема управления процессом синтеза аммиака на основе fuzzy–логики.
Недостатком такого рода разработок является то, что для управления данной системой необходимо создать свыше 25 законов регулирования Управление системой с таким большим количеством законов регулирования представляется достаточно сложным, поскольку при изменении параметров объекта возникает необходимость внесения изменений в список правил fuzzy-регулятора, а не просто изменить несколько коэффициентов в настройках. Например, изменение некоторых свойств объекта (состав катализатора) может привести к тому, что созданные законы регулирования уже не будут удовлетворять необходимому качеству регулирования. Еще одним недостатком является то, что для данной системы необходимо использовать численные методы для вычисления производных, которое повышает чувствительность системы для шумов.
Из представленных решений более распространенной является структура рис.1.3, поскольку ее реализация на основе промышленных контроллеров является более простой и в проектировании, и в обслуживании. Схема рис. 1.4 вследствие описанных выше недостатков менее распространена.
Моделирование и анализ результатов
4.1 Разработка структуры САУ колонной синтеза
В промышленных условиях ввиду достаточно большой инерционности концентрации, а также из-за значительных трудностей при ее измерении непосредственно в слоях катализатора реактора, процесс проводят путем стабилизации температуры в регламентных границах по слоям (полкам) за счет изменения степени открытия заслонок на байпасных потоках. Существующая система представляет собой совокупность независимых контуров регулирования. Каждый такой контур может быть представлен структурной схемой рис. 2.1
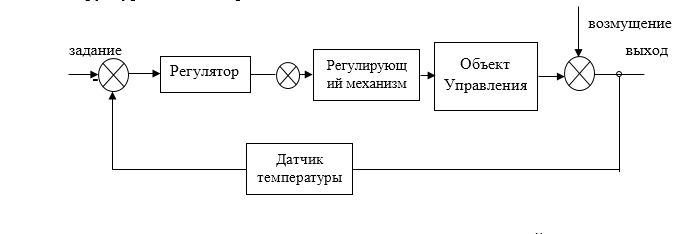
Рисунок 2.1 – Структурная схема САУ колонной синтеза.
Так как существует возможность измерять возмущающее воздействие (концентрацию входящей АВС), а также идентифицировать зависимость между его значением и изменением температуры на выходе полки, предлагается использовать комбинированную структуру управления. Комбинированные САУ применяют при автоматизации технологических объектов, подверженных действию контролируемых возмущений. Введение корректирующего воздействия по возмущению через компенсатор в обычную замкнутую систему позволяет снизить динамическую ошибку регулирования.
Существует два принципа построения комбинированных САУ:
- Система, в которой корректирующее воздействие компенсатора поступает на вход объекта.
- Система, в которой корректирующее воздействие компенсатора подаётся на вход регулятора.
В данной работе используется первая структура, вид которой представлен на рис. 2.2.
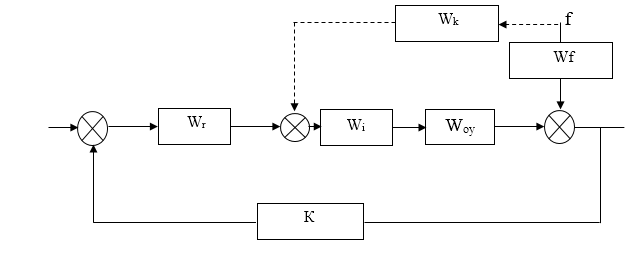
Рисунок 2.2 – Структурная схема объекта с компенсатором на основе передаточных функций элементов
Принятые на рис. 2.2 обозначения: f – возмущение, y – выход объекта, К – передаточная функция датчика (коэффициент передачи), Wf – передаточная функция по возмущению, Wоу – передаточная функция объекта управления, Wk – передаточная функция компенсатора, Wi – передаточная функция регулирующего механизма, Wr – передаточная функция регулятора.
Передаточная функция компенсатора может быть получена на основе принципа инвариантности. Для выполнения принципа инвариантности необходимы два условия: идеальная компенсация всех возмущающих воздействий и идеальное воспроизведение сигнала задания. Очевидно, что достижение абсолютной инвариантности реальных системах регулирования практически невозможно, потому, обычно ограничиваются частичной инвариантностью по отношению к наиболее значительным возмущениям.
4.2 Получение математической модели объекта
На основе анализа объекта и промышленных экспериментов установлена взаимосвязь между процентом открытия заслонок на байпасных потоках и изменением температуры в соответствующих слоях катализатора. Эти данные использованы в блоке Matlab&Simulink Look-up-table (рис. 2.3).
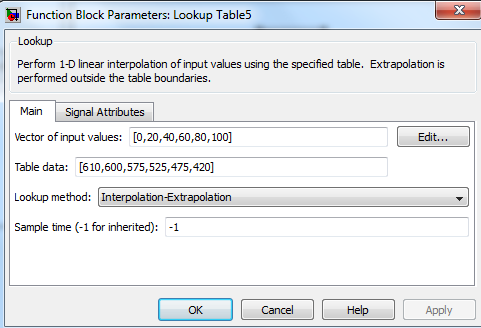
Рисунок 2.3 – Занесение технологических данных в блок Look-up-Table
Получим математические модели всех элементов структуры рис. 2.3. Из анализа данных следует, что объект управления (колонна синтеза аммиака) может быть представлена в виде апериодического звена первого порядка с запаздыванием вида
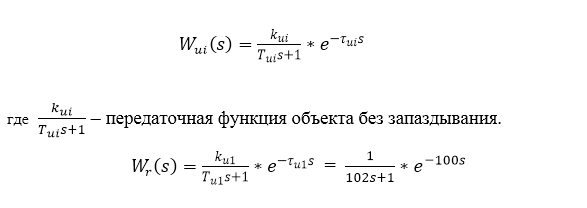
В среде моделирования Matlab/Simulink данная ПФ с учетом данных рис.2.3 примет вид, представленный на рис.2.4:
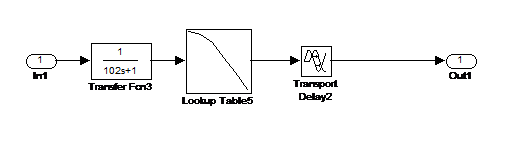
Рисунок 2.4 – Структура модели первой полки катализатора по температуре
Как было сказано ранее, на протекающие в колонне процессы воздействуют несколько возмущений, и наибольшее влияние из них имеет концентрация аммиака в составе входящей АВС. Взаимосвязь этого возмущения и температуры на выходе первого слоя катализатора также может быть представлен передаточной функцией в виде апериодического звена первого порядка с запаздыванием. Эта передаточная функция описывает динамику объекта по каналу возмущения «концентрация аммиака во входящей смеси – температура в слое катализатора»:

В среде моделирования Matlab/Simulink данная ПФ примет вид, представленный на рис.2.5
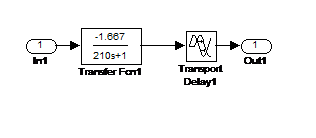
Рисунок 2.5 – ПФ первой полки катализатора по возмущению
В ППП Matlab/Simulink была получена схема моделирования системы управления температурой в первой полке катализатора - рис.2.6
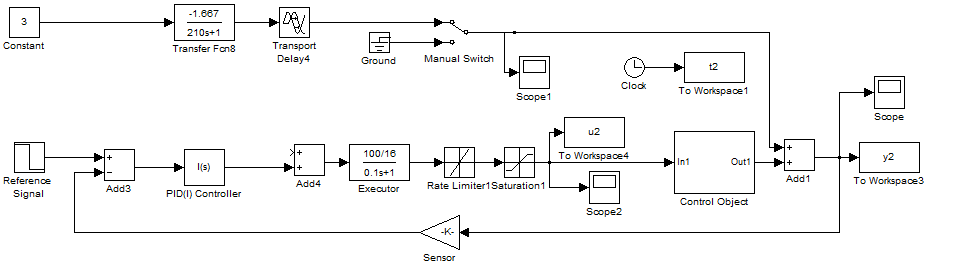
Рисунок 2.6 – Схема моделирования системы с И-регулятором
Рассчитаем идеальный динамический компенсатор:
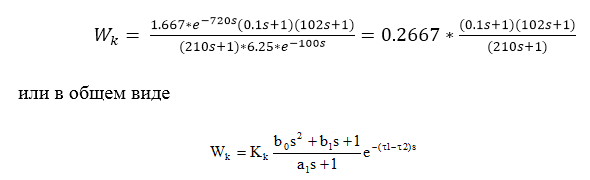
Данная ПФ является физически нереализуемой, поскольку порядок ее числителя больше порядка знаменателя. Существуют методики расчета реального динамического компенсатора, на основе типовых звеньев. Однако анализ литературы показал, что в большинстве случаев улучшить качество регулирования удается даже со статическим компенсатром. На данном этапе работы принято решение ограничиться именно таким компенсатором и в качестве передаточной функции принять Wk=Kk.
В ППП Matlab&Simulink реализована схема моделирования системы со статическим компенсатором (рис.2.7).
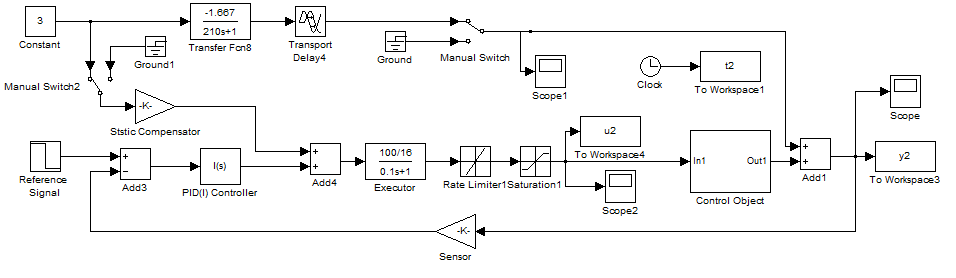
Рисунок 2.7 – Схема моделирования системы с И-регулятором и статическим компенсатором
4.3 Результаты моделирования
В результате моделирования системы без компенсации по возмущению рис. 2.7 были получены следующие графики переходных процессов:
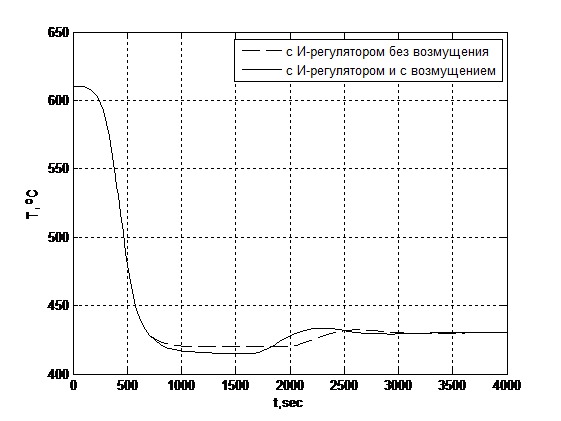
Рисунок 2.8 – График изменения температуры в первой полке катализатора
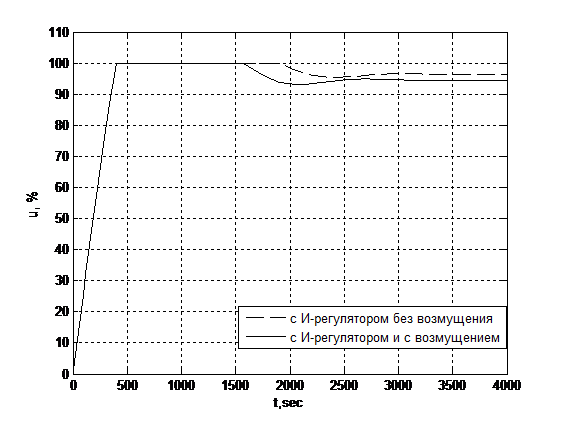
Рисунок 2.9 – График изменения уровня открытия заслонки
Как видно из графиков (рис.2.8-2.9) при подаче возмущения значительно увеличивается перерегулирование и время переходного процесса.
В исходной системе с И-регулятором время переходного процесса составляет 3500 с. При этом перерегулирование составляет около 2.5%. Хотя объект и является чувствительным к перерегулированию и его значение желательно минимизировать, это удовлетворительные показатели качества.
При подаче возмущения время ПП увеличилось до 3600 с, а перерегулирование возросло до 3.5%.
В результате моделирования системы со статическим компенсатором возмущения были получены следующие графики переходных процессов:
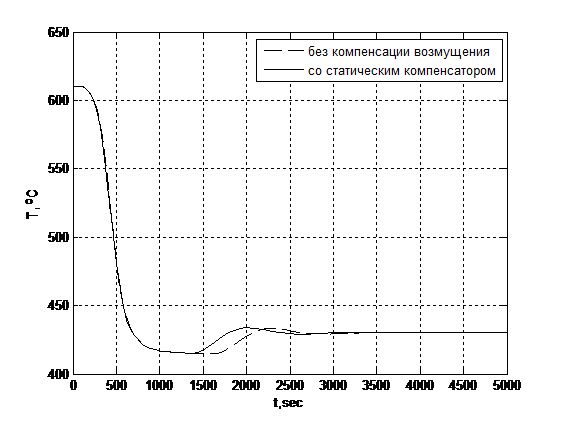
Рисунок 2.10 – График изменения температуры в первой полке катализатора
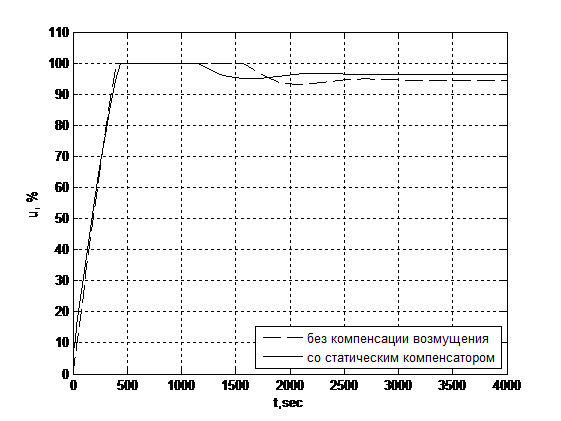
Рисунок 2.11 – График изменения уровня открытия заслонки
Как видно из графиков, использование статического компенсатора хотя и не позволило сократить перерегулирование, однако позволило уменьшить время переходного процесса до 2900 с.
Выводы
В данной работе рассмотрена задача управления колонной синтеза аммиака. За счёт введения в систему автоматической стабилизации И-регулятора и статического компенсатора были достигнуты высокие показатели качества управления системой. По результатам работы можно сделать следующие основные выводы:
- Исследуется технологический процесс синтеза аммиака в четырехполочной колонне синтеза. Выполнен его анализ как объекта управления, выделены управляющие, выходные и возмущающие параметры;
- Была получена математическая модель колонны синтеза аммиака колонны на примере одной полки катализатора. Состоятельность математической модели проверена методами математического моделирования;
- Была предложена модификация существующей системы с И-регулятором, а именно комбинированная система управления. Выполнен синтез синтеза статического компенсатора основного возмущения. Сравнительный анализ графиков переходных процессов показал, что предложенное решение позволяет улучшить показатели качества регулирования.
Список источников
- Моделирование и синтез цифровой многосвязной системы управления процессом получения аммиака [Текст]: Монография /В. С. Кудряшов, С. В. Рязанцев; Воронеж. гос. технол. акад. – Воронеж: ВГТА, 2011. – 171 с.
- Проектирование систем управления /Г.К. Гудвин, С.Ф. Гребе, М. Э. Сальгадо – М.:БИНОМ. Лаборатория знаний, 2004 - 911с.
- Синтез аммиака. – под редакцией Л. Д. Кузнецова, - М.:Химия, 1982, - 296с.
- Теоретические основы и технология синтеза аммиака. – под редакцией А. М. Николаева – Киев: Вища школа, 1969 – 256с.
- Хазаров, В. Г. Интегрированные системы управления. [Текст] /В. Г. Хазаров. –М. : Профессия, 2009. –592 с.
- А.с. 1736928 СССР, МКИ. С 01 С 1/04, G05 D 27/00. Способ автоматического регулирования температурного режима колонны синтеза аммиака [Текст] /В. В. Лымарев, Н. А. Нидченко, Г. З. Ермоленко, В. С. Белых (СССР). – № 4819296/26; заявл. 24.04.90; опубл. 30.05.92, Бюл. № 20. – 6 с.
- А. с. 893865 СССР, МКИ. С 01 С 1/04, G05 D 27/00. Способ автоматического управления процессом синтеза аммиака [Текст] /И. Д. Бадиков, А. П. Ковтун, Б. М. Блох, В. П. Василенко, А. М. Мазур (СССР). – № 2902217/23-26; заявл. 01.04.80; опубл. 30.12.81, Бюл. № 48. – 3 с. : ил.
- Денисенко В.В. Компьютерное управление технологическим процессом, експериментом, оборудованием. – М.: Горячая линия – Телеком, 2009. – 608с.,
- Ермолович Д. А. Управление объектами с большим запаздыванием [Электронный ресурс] /Д. А. Ермолович, А. П. Мовчан //Национальный технический университет Украины «КПИ».
- Филлипс Ч., Харбор Р. Системы управления с обратной связью. – М.: Лаборатория Базовых Знаний, 2001. - 616 с.
- Денисенко В. В. ПИД-регуляторы вопросы реализации часть 2//СТА. - 2008. - № 1. - С. 86-99.
- Денисенко В. В. ПИД-регуляторы: принципы построения и модификации //СТА. - 2007. - № 1. - С. 77-88.
- Лукас В. А. Теория автоматического управления: Учебник для вузов - 2-е издание. - М: Недра, 1990. – 416 с.
- Дорф Р. Современные системы управления /Р. Дорф, Р. Бишоп. Пер. с англ Б. И. Копылова. – М.:Лаборатория Базовых Знаний, 2002. – 832 с.
- Перельмутер В.М. Пакеты расширения MATLAB. Control System Toolbox & Robust Control Toolbox – М.: СОЛОН-ПРЕСС, 2008. – 224 с.
- Дудников Е. Г., Автоматическое управление в химической промышленности: Учебник для вузов – М.: Химия, 1987. 368 с.