Abstract
- Introduction
- 1. Relevance themes
- 2. Purpose and objectives of the study
- 3. Description of the technological process of ammonia synthesis
- 3.1 Analysis of the ammonia synthesis process as a control object
- 3.2 Analysis of existing solutions
- Conclusions
- List sources
Introduction
One of the most important tasks that each enterprise faces is a steady increase in the quality of products, improvement of production technology, increasing reliability and long-term products.
Modern chemical-technological processes are characterized by the complexity and high rate of leakage, as well as the harmfulness of working conditions, explosive and fire hazardous substances that are processed. With increasing load on the apparatus in order to increase production volumes, to manage the technological processes at high pressures and temperatures, as well as the speed of chemical reactions without the use of modern developments in the field of automation becomes impossible. Deviations of process parameters from rigidly set norms can lead not only to loss of quality of finished products, damage to raw materials, auxiliary substances (for example, catalysts), but also to an emergency situation, including fires, explosions, emissions of a large amount of harmful substances into the environment.
1. Actuality of the theme
Using tools and automation systems allows you to improve the basic performance indicators of production. In addition, at the present stage of the development of automatic control systems, there is also a need to improve the quality and reliability of control and to create integrated systems that include monitoring, control, signaling and locking of technological parameters using the latest analytical and technical means.
Thus, the development of new and modernization of existing control systems for chemical processes is an urgent task. And to solve this problem, it is necessary to perform an analysis of the ammonia synthesis process in order to determine ways to improve the quality of the finished product and management.
2. Purpose and objectives of the study, planned results
Based on the analysis of existing solutions and features of the technological process of ammonia synthesis in a four-column column, that in order to maintain the course of the process within the technological regulations, it is necessary to perform stabilization of the temperatures in the catalyst layers within the strictly defined limits in the presence of disturbing influences.
The main goal of the study is to increase the efficiency of the ammonia synthesis process by developing a temperature management system in the catalyst layers, taking into account the features of the object functioning (transport delay) and the disturbing effect. To achieve this goal, you need to solve the following tasks:
- Analysis of the state of the automation of the ammonia synthesis process.
- Development of the structure of the control system, taking into account the interrelationships of the parameters and the influence of the external disturbance on the temperature in the catalyst layer, using the example of the first shelf;
- The choice of the controllers for the degree of opening of the dampers on bypass flows, the development of algorithms for the operation of the control system, which allow maintaining the optimum temperature over a long period of time;
- Verification of adequacy, developed by ACS by mathematical modeling methods.
Thus, the automatic control system will allow to ensure the quality of temperature control in the catalytic bed of the synthesis column due to the increase of the dynamic accuracy and the time for setting the controllable values, which in turn will increase the capacity of the ammonia synthesis column and increase the maximum volume of the target product.
3. Description of the technological process of ammonia synthesis
To date, a variety of technological schemes for the synthesis of ammonia have been developed and implemented using a wide range of pressures and catalysts, operating mainly under high-temperature conditions. Numerical experiments and the practice of industrial production have shown that the most optimal from the point of view of using raw materials and economic costs is the use of ammonia synthesis reactors of large unit capacity, which work under pressure (250-320 atm). In such technological schemes, raw materials for the production of ammonia are natural gas and nitrogen, which is released from atmospheric air.
The whole process of ammonia synthesis is a complex production within a few blocks, so in this paper we will only consider one of its most important parts - the production of ammonia reactor (synthesis column).
In Fig. 1.1 shows the processes occurring during synthesis. Table 1.1 shows the purpose of the devices and a description of the processes occurring in them.
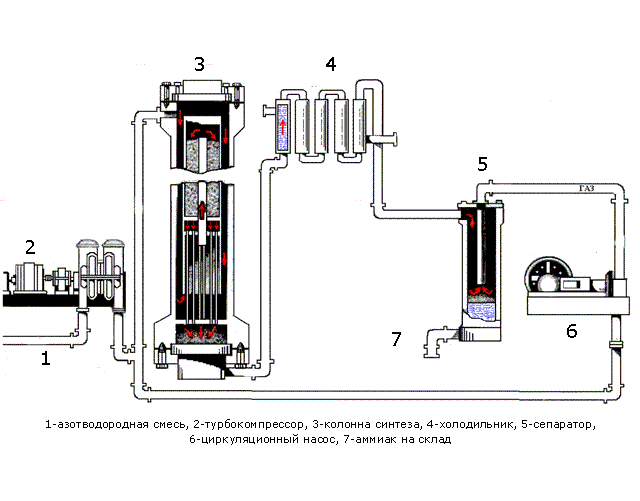
Figure 1.1 - The process synthesis
( animation : 12 frames , 31.9 kilobytes )
Table 1.1 - Assigning devices and processes running in them
Device | Purpose apparatus and the ongoing at him processes |
Pipeline | A pre-prepared mixture consisting of 3 volumetric parts of hydrogen and one volume part of nitrogen is fed. |
Turbo Compressor | The nitrogen mixture is compressed to a certain pressure required for the process |
Column of synthesis | The synthesis column is designed for the ammonia synthesis process. Shelves with a catalyst are located in the contact device. The synthesis process is highly exothermic, flows with a large release of heat, part of which is spent on heating the incoming nitrogen-hydrogen mixture. The mixture emerging from the synthesis column consists of ammonia (20-30%) and unreacted nitrogen and hydrogen. |
Refrigerator | Designed to cool the mixture. Ammonia is easily compressed, at high pressure it becomes a liquid. When they leave their refrigerator, a mixture is formed, consisting of liquid ammonia and unreacted nitrogen-hydrogen mixture. |
Separator | Designed to separate liquid ammonia from the gaseous phase. Ammonia is collected in a collector located at the bottom of the separator |
Circulation pump | Returns the unreacted mixture to the contact device, which increases the use of the mixture to 95%. |
Ammonia - wire | Designed for transporting liquid ammonia to the warehouse. |
3.1 Analysis of the synthesis of ammonia as a control object
Since chemical reactions in the catalyst layers take a long time, the control object can be classified as a class of objects with transport delay. In addition, the temperature in the catalyst layers is affected by various disturbances. The most significant effect is the concentration of ammonia at the reactor inlet. In the course of the analysis, it was found that, since all processes occur within the same working fluid, the supply of bypass gas to any shelf will have an effect on the reactions in the rest. Thus, the process of ammonia synthesis is a multiply connected control object in the presence of perturbations. .
In Fig. 1.2 the scheme of the four-column ammonia synthesis column as the control object (Fig. 1.2-a) and the structural diagram of the interrelationships of the object parameters (Fig. 1.2b) are presented
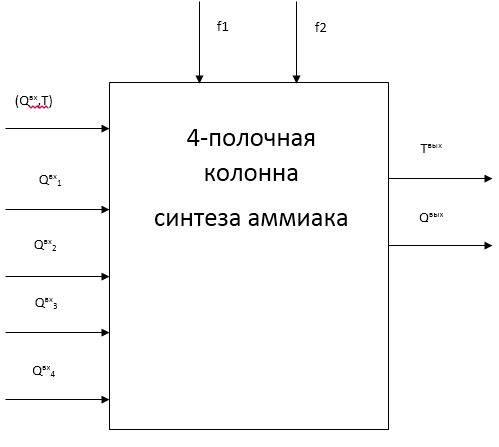
Figure 1.2-a - Scheme of a four-column ammonia synthesis column as a control object
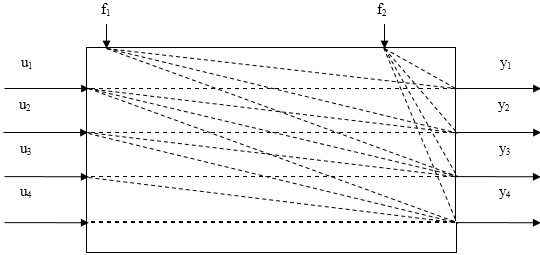
Figure 1.2-b - a block diagram of the relationships of object parameters
Figure 1.2-a takes the following notation:
- (Qin, T) - flow rate, ammonia concentration and temperature of the inlet nitric-hydrogen mixture, respectively;
- Qin1-4 - cold bypass gas flow rate;
- F1 - concentration of ammonia in the input mixture;
- F2 - hydrogen /nitrogen ratio;
- Qout - the concentration of ammonia in the exhaust gas;
- Tout - temperature of the outgoing gas.
Figure 1.2-b shows:
- u1 - u4 - degree of opening of dampers on bypass flows (control parameters);
- y1 - y4 - temperature in catalyst layers (controlled parameters);
- f1, f2 - ammonia concentration and hydrogen /nitrogen ratio (disturbance effects)
- F2 - hydrogen /nitrogen ratio;
The aim of the ammonia synthesis process in a four-column reactor of the axial type is to produce gaseous ammonia with a given concentration at the reactor outlet. In industrial conditions, taking into account the rather large inertia of the change in concentration, and also because of the considerable difficulties in measuring it directly in the catalyst bed of the reactor, the process is carried out by stabilizing the temperature within the regulatory limits along the layers, taking into account the change in the degree of opening of the dampers in bypass flows.
3.2 Analysis of existing solutions
The closest solution to the system under investigation for the technical essence and the required effect is the system shown in Fig. 1.3. This solution for the control system includes sensors for flow, pressure, temperature and composition of the circulating gas at the inlet of the synthesis column, temperature sensors in catalyst layers, valves opening regulators in bypass lines and a computing device. The temperature control (in accordance with the typical PID control law) in the catalyst beds is carried out by changing the supply of the circulation gas and the bypass streams depending on the flow rate, pressure, temperature and gas composition at the inlet to the synthesis column, the specified and measured temperature values ??in the layers.
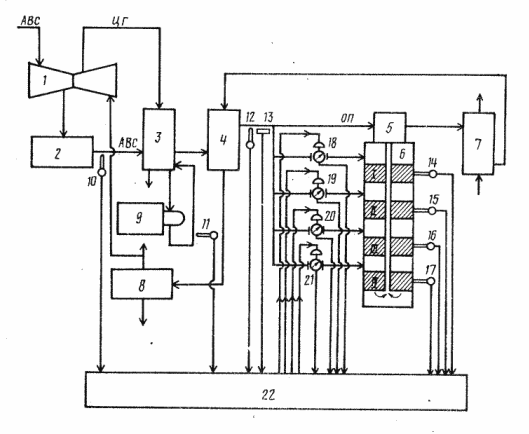
Figure 1.3 - Control scheme for the synthesis of ammonia with a PID regulator
The algorithm is designed to stabilize the temperature of the synthesis column during the production of ammonia by changing the position of the valves in the "cold bypass", depending on the deviation of the current temperatures for each shelf from the specified. Calculation of the magnitude of the control effect on the valve position change for each bypass is performed based on the solution of the system of equations, which are the dependence of the increment of gas temperatures at the outlet from the shelves of the synthesis column from the change in the degree of opening of the valves on the corresponding bypasses. Since in the process of operation the control object changes its characteristics, it became necessary to correct the coefficients of the model. Correction of the coefficients is carried out directly during operation. .
The disadvantage of the above system is the unsatisfactory quality of temperature control in the catalyst layers, which reduces the capacity of the ammonia synthesis column due to the lack of compensation for external perturbations in the concentration of ammonia.
There is also a class of development based on the use of fuzzy-controllers to control the process under investigation (Fig. 1.4).
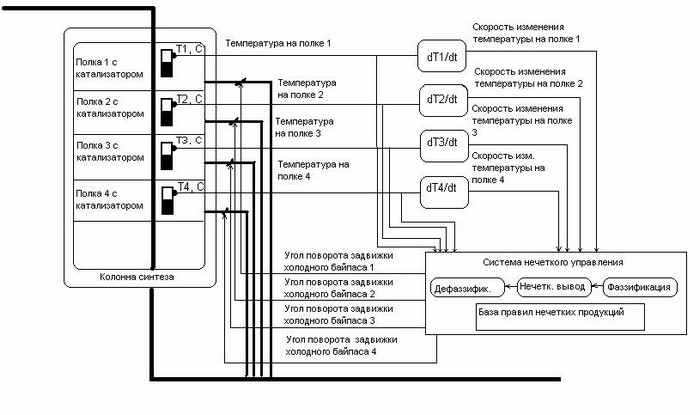
Figure 1.4 - Diagram of the ammonia synthesis process control based on fuzzy logic.
The disadvantage of this kind of development is that for the management of this system it is necessary to create more than 25 regulatory laws. The management of a system with such a large number of regulatory laws is quite complex, because when changing the parameters of the object there is a need to make changes to the list of fuzzy controller rules, and not just to change several coefficients in the settings. For example, changing some properties of an object (catalyst composition) can lead to the fact that the created regulatory laws will no longer satisfy the necessary quality of regulation. Another disadvantage is that for this system it is necessary to use numerical methods for calculating derivatives, which increases the sensitivity of the system for noise.
Of the solutions presented, the most common is the structure of Figure 1.3, since its implementation based on industrial controllers is more simple in both design and maintenance. The circuit of Fig. 1.4 due to the drawbacks described above is less common.
Conclusions
In this paper we consider the task of managing the ammonia synthesis column. Due to the introduction of a system of automatic stabilization and control, and static compensator have achieved high indicators of quality control system. According to the results of the work can be done the following conclusions:
- study the process of ammonia synthesis chetyrehpolochnoy synthesis column. Made its analysis as a control object, select the control, output and disturbance variables;
- was obtained mathematical model ammonia synthesis column column an ??example of one catalyst shelves. Consistency mathematical model verified by methods of mathematical modeling;
References
- simulation and synthesis multiply digital process control system for producing ammonia [Text]: Monograph /VS Kudryashov, SV RYAZANTSEV; Voronezh. state. tehnol. Acad. - Voronezh: VSTA, 2011. - 171 p.
- Designing control systems /GK Goodwin, SF Grebe, M. E. Salgado - M: Binom. Laboratory Knowledge, 2004 - 911s.
- synthesis of ammonia. - Edited by LD Kuznetsova - M. Chemistry, 1982 - 296s.
- Theoretical bases and ammonia synthesis technology. - Edited by A. M. Nikolaev - Kiev: Vishcha School, 1969 - 256s.
- Khazars, VG Integrated Management Systems. [Text] /VG Khazars. -M. Title: 2009. -592 p.
- AS 1736928 USSR MKI. C 01 C 1/04, G05 D 27/00. A method of automatic control of temperature of the ammonia synthesis tower [Text] /VV Lymarev, NA Nidchenko, GZ Ermolenko, B. S. White (USSR). - ¹ 4819296/26; appl. 24/04/90; publ . 05.30.92, Bull . ¹ 20. - 6 with .
- A . a . 893865 USSR , MKI . C 01 C 1/04, G05 D 27/00. A method of automatic control of the ammonia synthesis process [Text] /I. D. Badikov, AP Kovtun, B. M. Bloch, VP Vasilenko, A. M. Mazur (USSR). - ¹ 2902217 /23-26; appl. 04/01/80; publ. 12.30.81, Bull. ¹ 48. - 3. : Yl.
- Denisenko VV Computer process control, eksperimentom and equipment. - M .: Hotline - Telecom, 2009. - 608s,.
- Ermolovich DA Managing objects with great delay [electronic resource] /DA Ermolovich, AP Movchan //National Technical University of Ukraine "KPI" .
- C. Phillips, R. Harbor control system with feedback. - M .: Basic Knowledge Lab, 2001. - 616 p.
- Denisenko VV PID controllers issues of implementation of part 2 //STA. - 2008. - ¹ 1. - pp 86-99.
- Denisenko VV PID controllers: principles of construction and modification //STA. - 2007. - ¹ 1. - pp 77-88.
- Lucas VA Automatic Control Theory: A Textbook for high schools - 2 ed. - Moscow: Nedra, 1990. - 416 p.
- R. Dorf Modern control systems /R. Dorf, R. Bishop. Trans. with English BI Kopylova. - M.: Laboratory of Basic Knowledge, 2002. - 832 p.
- Perel'muter VM Extension packages MATLAB. Control System Toolbox & Robust Control Toolbox - M :. Solon - Press , 2008. - 224 c .
- Dudnikov EG, Automatic control in the chemical industry: the textbook for high schools - M .: Chemistry, 1987. 368 pp.