Abstract
Table of contents
- Introduction
- 1. Theme urgency
- 2. Goal and tasks of the research
- 3. Analysis of works on the topic.
- 4. Planned practical results
- References
Introduction
The development of the DPR industry requires an increase in the volume of construction works, including road construction. The volume and pace of construction is largely determined by the level of mechanization. Therefore, the requirements for road and construction machines, as well as for their maintenance, are constantly being tightened. And there is not only quantitative, but also qualitative growth of the Park: there are new types of equipment, complicated design. Ensuring the efficiency of such a changing fleet of machines requires continuous improvement of the technical operation system. Its importance is characterized by the well-known fact that in the process of operation the cost of maintaining and restoring the performance of machines in 6...10 times higher than the cost of their production. According to researchers, about 80% of the efficiency of road and construction machines is provided by means of their technical operation.
Durability of machine parts-one of the main elements that determine the reliability of machines as a whole. Increasing the durability of parts can reduce the number, volume and duration of repairs, reduce the consumption of spare parts and increase the service life of machines. Increase of durability of details, and, therefore, and increase of reliability of cars are the important national economic problem solved at all stages of production, installation, operation and repair of cars.
A typical part of road and construction machines is a Cam mechanism. The Cam mechanism is a mechanism with a higher kinematic pair, which has the ability to provide the laws of motion of the output link, and the structure contains at least one link with a working surface of variable curvature. Cam mechanisms are designed to convert the movement of the leading link in the desired type of movement of the output link according to a given law. These mechanisms are widely used in transport, technological and other machines.
Figure 1 shows the principle of operation of the Cam mechanism, in which the rotational motion is converted into the translational motion of the pusher.
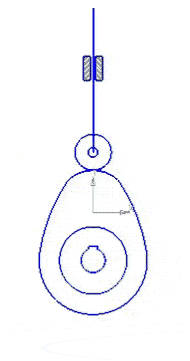
Figure 1 - Principle of operation of the Cam mechanism
The reliability of Cam mechanisms is mainly determined by the durability of the Cams, the working surface of which loses its efficiency due to contact fatigue wear during operation. In accordance with the operational purpose, the Cam has a complex geometric shape in the end section and, in order to improve manufacturability, simple – in the axial section. A priori, it is assumed that there is a linear contact in the coupling of the Cam mechanism parts, which should provide a high load capacity.
It is known that increasing the durability of any part is the most effective technological methods that provide the necessary quality of the surface layer. Developed a large number of different technological methods to improve the wear resistance of friction surfaces, both in the manufacture and repair. However, the problem of reasonable choice of the most effective hardening technology, the search for hardening modes for a particular part is still relevant.
Therefore, the search, research and application of technological methods to ensure the formation of a modified profile of the axial section of the Cams, strengthening the working surface and increase the durability of the Cam mechanisms is an urgent task.
1. Theme urgency
The most effective and economical way to increase the existing fleet of road, construction machines is to increase their durability. One of the main damaging processes that reduce the potential performance of road construction machinery and equipment is the intensive wear of machine elements. Machine failures due to wear reach 70-80% of all failures occurring during the operation of machines. In this regard, more attention is paid to the issues of wear and durability.
Ensuring the reliability of construction and road machines is achieved with an integrated approach to solving this problem at all stages: design, technological and operational.
The durability of the critical parts of the machines is laid as their surface layer of the working surfaces, and therefore at the stage of technological manufacturing, ensuring reliability is laid by forming the specified operational properties of the parts by finishing and hardening treatment.
Analysis of works in the field of durability of details of machines shows the necessity of developing the methodology of improving the wear resistance on the basis of "high" technologies.
2. Goal and tasks of the research
The goal of this work is to develop approaches to the synthesis of combined functional-oriented technologies of finishing and hardening treatment providing a given durability of critical parts of road, construction, machinery.
To achieve this goal it is necessary to solve the following tasks:
- Perform studies of the operating conditions of critical parts of friction pairs of road, construction machines.
- To study and develop the principles of increasing the wear resistance of wearing parts with unevenly distributed load.
- Develop recommendations based on research.
3. Analysis of works on the topic.
The functionality and service life of transport and technological machines depends on the reliability of the friction pairs.
Wear parts of road-building machines due to different factors in nature:
- constructive – the nature of the load; the type of friction of the working surfaces; the combination of materials of the coupling parts; the presence of protective coatings;
- technological methods of processing of working surfaces; the build quality of the mate; the presence of process impurities; the structure of the surface layer of metal; microgeometrical indicators of friction surfaces;
- operational – the nature of the work and modes of use of the machine; climatic conditions; condition of lubricants; types and frequency of maintenance and repairs [9].
The wear resistance of the friction surface is mainly determined by the values of the state of the surface layer formed in the manufacturing process by various technological methods [2, 3]. To increase the durability of parts, finishing and hardening treatment of PPD and application of wear-resistant coatings have been widely used [3]. At OEO PPD in the industry are quite successfully used running-in of parts by rollers and balls, shot blasting, impact tools processing, hydrojet and waterjet processing, etc. [4]. At the stage of technological manufacturing, ensuring reliability is laid by proper and accurate manufacturing of components and assemblies, it is also important to increase wear resistance, static and cyclic strength of parts by heat treatment; hardening of parts by chemical and thermal treatment: hardening of parts by surface plastic deformation; application of wear-resistant coatings on the working surfaces of machine parts; etc.
Work Bezhyazichniy V. F., V. I. Butenko, A. A. Matalin, A. N. Mikhailov, A. V. Orlov, A. G. Suslov, V. P. Fedorov, Y. G. Schneider, etc. convincingly testify to the possibility of increasing the wear resistance as due to the technology of processing and by optimizing the profile of the mating surfaces.
Durability and operational reliability of machines and equipment largely depends on the state and physical and mechanical properties of the surface layer of parts, where the processes of wear and fatigue failure are born and developed. A significant increase in the wear resistance of parts can be achieved by an optimal combination of the properties of the structure of materials and hardening treatment.
In mechanical engineering more and more applications get details with work surfaces, functioning in extreme conditions unevenly distributed load. The use of conventional technologies of finishing and hardening treatment, ensuring uniform distribution of performance properties on the surface does not provide the optimal resource for such parts. Methods of technological influence are chosen on the basis of special principles of orientation of technological influence and providing the set operational properties of working surfaces and their separate functional elements. With modern methods of finishing and hardening treatment, parts with the same quality indicators are mainly created throughout the functional surface, regardless of the actual changes in the external loading conditions in individual zones and even points. This forces to strengthen the entire surface, based on the maximum acting loading factors (pressure, temperature, etc.) in a certain area, which increases the cost of the part, also leads to a decrease in the life of the entire friction unit. The study of the nature of surface wear shows that it is almost impossible to find a friction surface within which all external loading factors would have stable parameters. Almost all friction surfaces wear unevenly at different points.
The details of road, building is the uneven distribution of normal load and sliding speeds on the working surface, resulting in uneven wear and thus to reduction of durability of the friction pair as a whole. Unevenness of wear leads to a violation of the surface macrogeometry and, as a consequence, to the replacement of the entire surface [1].
The article [10] presents energy and resource-saving, import-substituting, environmentally friendly nanotechnology of surface hardening of intensively wearing parts, which allows to strengthen large-size parts from ordinary steels on an industrial scale to obtain structures of the nanoscale range.
Parts with unevenly distributed load include parts of Cam and yoke mechanisms, ball joints, gears, sliding bearings. The durability of Cam mechanisms is determined by the uneven wear of the working surface of the Cams, which is accompanied by a change in the acceleration of the pusher. An effective technological way to increase the durability of Cam Cams of Cam mechanisms is to create a large radius of curvature of the axial profile of the working surface by processing endless elastic diamond tapes with overlap, which allows to increase their bearing capacity and wear resistance compared to traditional technologies in 2 times [5].
A number of parts of brake mechanisms need to increase the life of the strength and wear-resistant characteristics. These parts include brake body parts, in which the stops of intermediate brake discs are subject to increased wear during operation [6].
Spherical joints increase the functionality of the machine and resistance to deformation. Spherical joints include sliding bearings, which are widely used in transport vehicles [14-16]. As a result of research [17], it is determined that the durability of ball joints is mainly determined by the wear resistance of the contacting surfaces of its parts and depends on structural, technological and operational factors. The most important and time-consuming part of the technological cycle in the manufacture of ball pins are roughing and finishing incomplete spherical head. Blanks of ball fingers used in ball joints of the front suspension are made mainly by cold heading or cross-wedge rolling, milling, cold sheet stamping of ball finger housings [18, 19]. As the operation dimension finishing-hardening treatment of incomplete sphere ball finger spread rotation (planetary) running balls, finishing-strengthening aseparator Noah running-finishing-strengthening the orbital forging [18, 21, 22].
To improve the functional properties of engineering products, it is necessary to develop high-tech technologies, the signs of which are: the formation of a qualitatively new set of properties, as a consequence, the implementation of a qualitatively new measure of the usefulness of products, as well as the efficiency of production of engineering parts, achieved by minimizing material, energy, labor costs. The formation of functional properties and ensuring the reliability of the part as a whole, determined accordingly by the quality of their functional surfaces, is based on the principles of utility, similarity of technological systems and criteria assessment. The purpose of manufacturing any product is to provide the specified performance properties and a given level of utility. To do this, the synthesis of innovative methods of processing products should be based on the unity of manufacturing and operation technology. The development of high-tech areas to ensure a given measure of the usefulness of products is an urgent task of mechanical engineering.
4. Planned practical results
As a result of the master's work should be developed technologies to improve the durability of road, construction machines.
In the technological part of the master's work, it is planned to develop "high" technologies of combined finishing and hardening treatment providing a given measure of the usefulness of the manufactured products.
In the research part it is planned to determine the operating conditions of machine parts, to determine the technological and methods of increasing durability and to develop recommendations based on the research.
References
- Разработка классификатора поверхностей деталей для обеспечения синтеза функционально ориентированных технологий отделочно-упрочняющей обработки / Михайлов А.Н., Лукичев А.В., Матвиенко С.А., Стрельник Ю.Н., Пичко А.П. // Прогрессивные технологии и системы машиностроения. – 2017. – №4(59). – С.31–36.
- Суслов, А.Г. Качество поверхностного слоя деталей машин. – М.: Машиностроение, 2000. – 320 с.
- Суслов, А.Г., Федоров, В.П., Горленко, О.А. и др. Технологическое обеспечение и повышение эксплуатационных свойств деталей и их соединений / под общ. ред. А.Г. Суслова. – М.: Машиностроение, 2006. – 448 с.
- Технология и инструменты отделочно-упрочняющей обработки деталей поверхностным пластическим деформированием: справочник. В 2-х томах. Т.1. /под общ. ред. А.Г. Суслова.– М.: Машиностроение, 2014. – 480 с.
- Шоев, А.Н. Технологическое повышение долговечности кулачковых механизмов / А.Н. Шоев // Справочник. Инженерный журнал. – 2010. – № 6. – С. 10–12.
- Кобяков, О.С Повышение износостойкости и ресурса работы многодисковых тормозных механизмов трактора «Беларус» лазерным термоупрочнением быстроизнашивающихся деталей / О.С. Кобяков, Спиридонов Н.В., Баркун А.А. // Вестник БНТУ – 2008. – №5. – С.10–17.
- Густов, Ю.И. Триботехника строительных машин и оборудования: монография. – М.: МГСУ, 2011. – 197 с.
- Гребенникова, Н.Н. Оптимальная стратегия эксплуатации машин / Н.Н. Гребенникова // Вестник развития науки и образования. – 2014. – № 3. – С. 25–29.
- Мухаметшина, Р.М. Трибологические отказы дорожно-строительных машин. /Известия Самарского научного центра Российской академии наук, том 18, №1(2), 2016. – С. 252–255.
- Загорский, Я.В. Повышение долговечности интенсивно изнашивающихся деталей дорожно-строительных машин / Я.В. Загорский Я. В., В.К. Загорский, И.В. Кусова. Электронный научный журнал «Нефтегазовое дело». 2016. №1 http://ogbus.ru.
- Польченко, В.В., Богуславский, В.А. Способы повышения долговечности зубчатых муфт.[Электронный ресурс] – Режим доступа http://ea.donntu.ru/bitstream/123456789/9316/1/В.В.%20Польченко.pdf.
- Мухаметшина, Р.М. Отказы дорожно-строительных машин по параметрам коррозии / Мухаметшина, Р.М.// Известия КГАСУ, 2013, №4(26). – С. 403–408.
- Старостина, Ж.А. Создание комплекса условий развития отечественного производства строительно-дорожной техники. // European Research: Innovation in Science, Education and Technology Сб. ст. по мат.: VIII межд. науч.-практ. конф. М., 2015. – C. 5–8.
- Железков, О.С. Усовершенствованный шаровый шарнир передней подвески легковых автомобилей / О.С. Железков, У.В. Михайлова // Автомобильная промышленность. – 2010. – № 3. – С. 14–15.
- Математическое моделирование технического состояния шарового шарнира в условияхстендовых испытаний / А.Н. Новиков, В.И. Чернышов, В.А. Гордон, А.А. Катунин, М.Д. Тебекин // Мир транспорта и технологических машин. – 2014. – № 4. – С. 39–46.
- Новиков, А.Н. Проблемы эксплуатации шаровых опор легковых автомобилей / Новиков А.Н., Катунин А.А., Тебекин М.Д. // Мир транспорта и технологических машин. – 2010. – № 3. – С. 42–45.
- Родионов, Ю.В. Повышение износостойкости и долговечности шаровых опор автомобилей / Ю.В. Родионов, А.А. Войнов, А.А. Шмелев // Успехи современной науки и образования. – 2017. – Том 4, №4. – С 84–86.
- Гун, И.Г. Совершенствование технологии изготовления шаровых пальцев автомобилей / И.Г. Гун, О.С. Железков, И.А Михайловский. и др. // Бюл. ин-та "Черметинформация". – 2000. – №11-12 (1211-1212). – С. 60–62.
- Катунин, А.А. Комбинированный способ отделочно-упрочняющей обработки головок шаровых пальцев / А.А. Катунин, А.В. Катунин, Н.Н. Самойлов // Мир транспорта и технологических машин. – 2010. – № 1(28). – С. 22–26.
- Катунин, А.А. Формирование шероховатости поверхности неполной сферы при обкатке бессепараторным инструментом / А.А. Катунин // Известия ОрелГТУ. – 2009. – № 3/275(561). – С. 70–75.
- Исследование кинематических параметров процесса обкатки неполной сферической головки шарового пальца / Ю.С. Степанов, А.М. Гаврилин, А.В. Катунин, А.А. Катунин // Известия ОрелГТУ. – 2009. – № 2/274(560). – С.52-56.
- Автореферат магистерской работы Назарчук В.К.Исследование долговечности и разработка предложения увеличения срока службы механизма передвижения мостового крана. [Электронный ресурс] – Режим доступа http://masters.donntu.ru/2007/fema/nazarchuk/diss/index.htm.
- Бобырь, Н. А. Повышение качества поверхностного слоя деталей машин при отделочной обработке [Электронный ресурс] – Режим доступа http://masters.donntu.ru/2003/mech/bobyr/diss/index.html.
- Автореферат магистерской работы Дубоделовой О.С. на тему: «Повышение качества обработки деталей машин с использованием методов поверхностно-пластического деформирования». [Электронный ресурс] – Режим доступа http://masters.donntu.ru/2005/mech/dubodelova/diss/index.htm.