Abstract
- Introduction
- 1. Goal and objectives of the study, expected results
- 2. Investigation of existing finishing and strengthening methods of processing for blades of compressor GTE
- 2.1 Vibration Abrasive Processing
- 2.2 Ultrasonic hardening of parts.
- 2.3 Pneumatic blasting
- 3. Features of the implementation of FOP for blades of compressor GTE.
- 4. The structure of the technological process of applying FOP to the blades of compressor GTE
- Conclusions
- List of used literature
Introduction
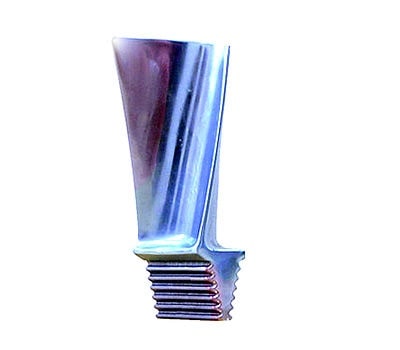
Figure 1 – Blade GTE compressor
Blades of the compressor are the most massive, highly loaded and responsible part of the gas turbine engine (GTE). During its operation, its elements wear out unevenly due to erosion-corrosive wear. The dusty atmosphere negatively affects many gas turbine engine components (GTEs). Most of all suffers a compressor whose blades are susceptible to erosion wear. Under certain conditions, dust deposits on the compressor blades can occur, which also leads to deterioration of the characteristics. Cooling air can also contain dust particles that precipitate in the cooling channels and can clog them, which can lead to overheating of the blades and turbine disk. When the engine enters the air with dust and sand, it results in erosion wear on the blades of the compressor GTE, worsening their characteristics. Soft coatings are also used for erosion wear, which are used to compact (reduce) the radial gaps of the flow part, in which (as in the case of wear of blades) the compressor efficiency decreases and the specific fuel consumption of the engine increases. The stability of the engine is degraded. Initially, erosion can even slightly improve the characteristics of the engine, since the blades are polished and become thinner. However, erosion then leads to a significant deterioration in engine performance and can lead to unstable operation of the compressor (propel) and the engine as a whole, which can lead to an accident. [1]
Corrosive wear. From the experience of operating aviation engines it follows that almost always there are conditions when blades can be exposed to various types of corrosion (point, intercrystalline, salt, gas, etc.). This, besides the intensity of the part, is facilitated by an external environment, including temperature; technological heredity, damage to erosion, scum, etc. The problem of corrosion protection is solved, first of all, due to the correct choice of corrosion-resistant materials, which is facilitated by the wide application of titanium and nickel alloys. The atmospheric air of certain areas (for example, coastal, especially in the tropics, or in areas with intensive application of mineral fertilizers) contains chemically active substances, for example salts of sea water, solonchak dust and the like, which cause corrosion of the compressor blades, especially the last stages where corrosion is activated by elevated temperatures. The finest edges of the working blades are most susceptible to corrosion damage. Corrosion damage develops intensively during parking and storage of equipment. These damages create an increased concentration of stresses and the possibility of developing fatigue cracks in the shoulder blades with oscillations. Protective coatings are applied to the surface of the blades to ensure high corrosion resistance. Increasing the resource of the compressor blades of the GTE due to the implementation of FOP technology is an important and topical problem, the solution of which will increase their resource.
1. Theme urgency
The purpose and objectives of the research
The purpose of this work is to increase the life of the compressor blades of the GTE due to the implementation of FOP technology
Based on this, the following tasks are formed:
- Investigation of existing finishing and reinforcing processing methods for the blades of compressor GTE.
- Features of the implementation of the FOP for blades of compressor GTE.
- Structure of the technological process of applying FOP to the blades of compressor GTE.
- Investigate the design of the application of the FOP to the blades of the compressor GTE.
- Develop general guidelines for the application of functional-oriented coatings.
2. Investigation of existing finishing and strengthening methods of treatment for blades of compressor GTE
2.1 Vibration Abrasive Processing
Vibration abrasive processing is performed in the process is carried out at the final processing stage. The operation of the plants is based on the principle of using unbalanced masses, which are created by means of loads fixed at the ends of the vibrator shaft. Most of the vibration abrasive treatment is performed on a vibrating machine with a horizontal shaft and a U – shaped container. The container container is in a cross—section of a rectangular shape, which allows the processing of medium and large-sized parts. The container pours abrasive granules, pours the working fluid, and reports mechanical oscillations with a frequency of 20 – 50 Hz and an amplitude of 1 to 10 mm. Under the action of oscillations, the working zone and the parts, give rise to intense action motion. Particles of the working medium, which differ in mass from the machined parts, are affected by the particles with relative velocity. In this case, slipping of particles on the surface of the parts with a certain pressure, microstrip, rolling and rotation are possible. When slipping over the surface of the parts, the abrasive granules remove the smallest particles of the metal; in the micro-attacks there is a partial pushing of the metal and hardening in the places of contact of the abrasive grains with the surface of the part. The working area consists of their filler and working fluid. As filler apply: china warfare, abrasive circle bomb, molded abrasive granules, sander, glass beads, steel tempered beads. The processing technology provides for the final operations of abrasive grinding, followed by polishing the surface of the blade pier. The use of abrasive chemically active liquids has a great influence on the effectiveness. During processing, the parts must remain clean so as not to impede the interaction between the part and the abrasive. To do this, add fillers to soap or soda ash. Preservation of the light surface of parts from the steels is achieved by the addition of phosphorus salts.
2.2 Ultrasonic hardening of parts
One of the main technological methods of increasing durability, durability and durability of products in modern mechanical engineering is the hardening of details by the method of surface plastic deformation (PPD). The use of powerful ultrasound for the implementation of PPD processes on the parts of the GTE allows for a much lower cost and higher quality to perform BPD operations. The process of hardening of components of a complex form by the method of PPE is based on the message of kinetic energy to the working bodies by means of an ultrasonic field that arises in a closed volume. The details placed in the working chamber are processed simultaneously on all surfaces. As working bodies, steel balls made of material SHX15 or stainless steel are used. The diameter of the balls is determined from the conditions of the processing possibility, as well as the optimum degree of deformation of the surfaces to be processed and the fulfillment of the requirements of roughness. As the diameter of the balls increases, the surface quality deteriorates. For the treatment of blades with thin edges R 0.2mm, balls with a diameter of 1.0 – 1.3 mm are used, for blades with edges R of 0.2 mm, then beads with a diameter of 1.5 – 2.5 mm. The duration of processing in the ultrasonic field, depending on the dimensions of the workpiece, ranges from 20 seconds to 30 minutes.
The unit for the PPD consists of an ultrasonic generator, a mangostostrictive transducer, interchangeable waveguides, a device for fixing a magnetostrictive converter, a worktable for installing a snap and machined parts and a soundproofing casing (Fig. 2.1).
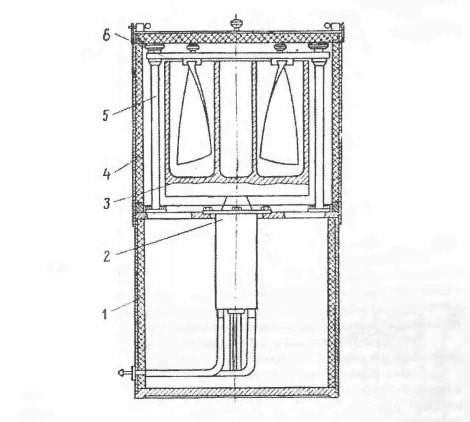
Figure 2.1 – Installation for ultrasonic strain hardening of blades
1 – base; 2 – PMS15A—18; 3 – waveguide; 4 – sound—jacket with cover; 5 – bars; 6 – is a technological flange
2.3 Pneumatic blasting
Pneumatic blasting is characterized by the sliding collision of the balls with the surface of the blade pen, preventing their pernaklepa. It was established that PDO is accompanied by a decrease in structural inhomogeneity and gives a more homogeneous character in the surface layer of the blade pen to the structure, phase distribution and residual compressive stresses. The proposed pneumatic blasting method of finishing-hardening treatment effectively neutralizes the technological microdefects of the surface layer, formed in the previous stages of the process, accompanied by a significant increase in the endurance limit, reducing the scattering of durability and does not require the subsequent finishing of thin edges by hand polishing. The slander depth when blown by a shot does not exceed 0.8 mm. Processing mode is determined by the speed of the fraction, its consumption per unit time and the duration of blowing. Blast-blasting can be subjected to a preform of steels, cast iron and alloys of different hardness. [2]
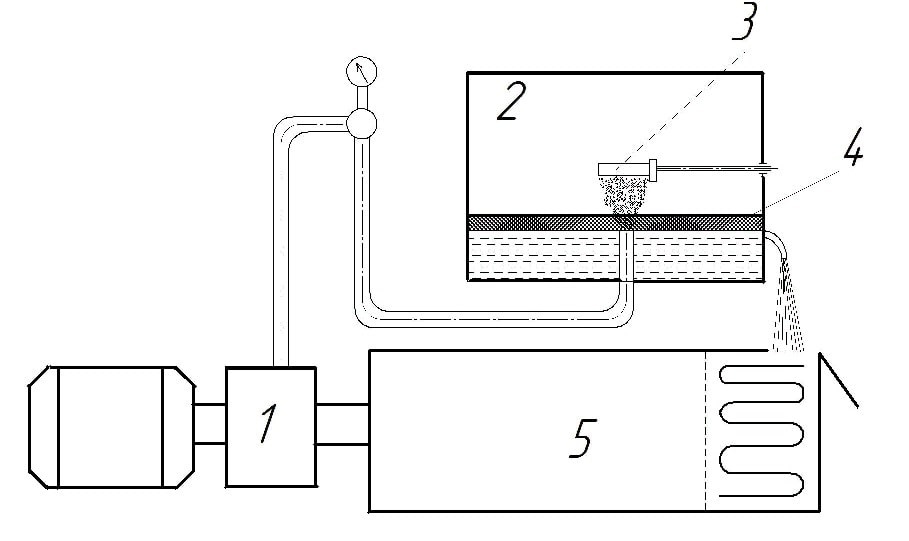
Figure 2.2 – Shot blasting process of blades GTE
1 – pump; 2 – working camera; 3 – treated blades; 4 – nozzles; 5 – tank
3. Features of the implementation of FOP for blades of compressor GTE.
Functional—oriented coatings (FOPs) are used to increase the resource of the compressor blades of the GTE. Protective metal coatings are metal layers applied to the surface of the product to protect against corrosion. The role of the coating, as a means of protection against corrosion, reduces to insulation of the metal from the environment. The most promising method is the use of vacuum ion-plasma coatings of the blade pen. Pre-blades are polished and cleaned in an ultrasonic bath. The figure shows an element of a compressor blade with an ion-plasma coating, where 1 is a blade, and 2 is an ion—plasma coating.
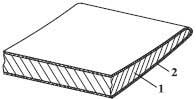
Figure 3.1 – Ion Plasma Coverage of the Compressor Blade GTE
The use of the FOP makes it possible to eliminate local wear of the body of the blade pen, due to the uneven wear of the coating, and thereby increase the consistency of the body of the blade pier after wear. When applying traditional coatings, abrupt wearing of the coating and the body of the pen of the shoulder blade usually occurs along the entrance edge and along the surface of the trough. When applying the FOP it is possible to resolve cardinally the issues of increasing the amount of restoration of the compressor blade and significantly increasing their service life. The FOP allows to solve problems of increasing the number of restorations of the properties of blades up to 2 ... 4 times.
The Bulat—6
plant is installed in the laboratory of the Technology of Machine-building
department, with the help of which the coatings are applied by ion-plasma application.
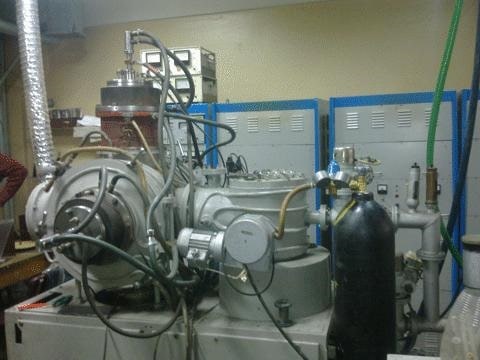
Figure 3.2 – Plant for the application of a vacuum ion—plasma coating Bulat – 6
Strengthening is carried out by application of wear-resistant coatings by a vacuum-arc method of condensation with ion bombardment without ion beam, or with assisted high-energy ion beam.
One of the most effective directions for improving the technology of synthesis of multifunctional coatings is the development of technologies for obtaining multi-layer composite coatings with nano-metric thickness of each layer. Multi-layer coatings based on single, double and triple compounds of refractory metals of groups IV – VI of the Periodic System of Elements (carbides, nitrides, borides, oxides and their mixtures) are used. The use of products with similar coatings effectively solves a variety of tasks for a wide range of engineering problems. Raises productivity, resistance to corrosion and erosion wear.
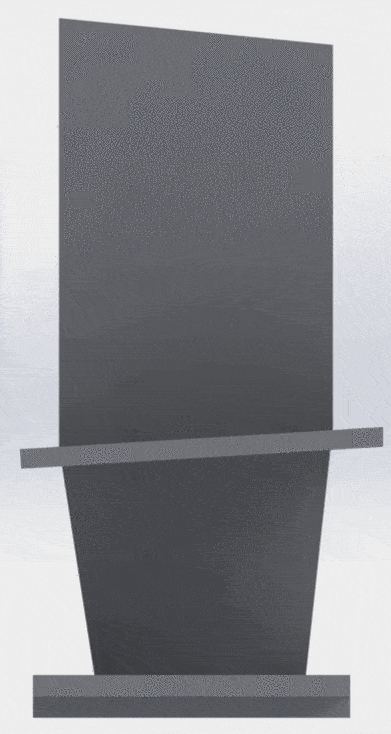
Figure 3.3 – Scheme of formation of mult—layer functionally oriented coating
Thus, the multilayer coating (Fig. 3.3) formed as a result of successive application of single-layer coatings at each stage, taking into account the expression 1 topological orientation of the coating of each layer. Here, the coating №1 is applied with its topological orientation on the surface in accordance with the scheme wear, then coating № 2, then coating № 3 and so on, at the end of the coating is applied to all surfaces of the pen.
4. The structure of the technological process of applying FOP to the blades of compressor GTE
The coating process is implemented on the basis of the following new principles:
- Isomorphic topological correspondence of the geometric parameters of each zone of the product in which the given function is implemented during operation, the zone of application of the required coating with the necessary properties.
- Functional matching of the quality parameters of the coating (type, type, coating, application technology and processing technique) of each zone to the features of the operation function in it.
- Full or partial quantitative matching of a variety of different functional areas of the product surfaces available during operation, to a large number of application areas of different coatings of appropriate quality. [4]
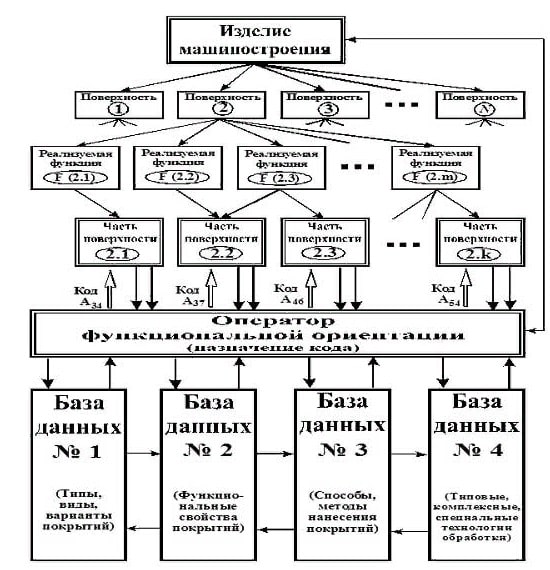
Figure 4 – Schematic diagram of the General methodology for FOP synthesis
Conclusions
The analysis showed that one of the promising ways to increase durability of the blades of compressor GTE is ion-plasma spraying. The main feature of this approach is the best adaptation of the product to the operating conditions. This, in turn, greatly enhances the service life of the compressor torch blade.
When writing this abstract, the master's work is not completed yet. Final completion: May 2019. Full text of work and materials on the subject can be obtained from the author or his supervisor after the specified date.
References
- Чичков А. В. Рабочие лопатки авиоционных ГТД. Часть 1. Эксплуатационная повреждаемость рабочих лопаток. Пособие по дисциплинам
Конструкция и техническое обслуживание ЛА и АД
,Конструкция и прочность авиационных двигателей
,Конкретная АТ
для студентов 5 и 4 курсов специальности 160901 всех форм обучения; курсового и дипломного проектирования – М:,2007.-73 с. - Богуслаев В. А., Яценко В. К., Жеманюк П. Д., Пухальская Г. В., Павленко Д. В., Бень В. П. Отделочно-упрочняющая обработка деталей ГТД. – Запорожье: ОАО
Мотор Сич
, 2005. – 559 с. ISBN 966-7108-91-0. - Абраимов Н. В., Елисеев Ю. С. Химико–термическая обработка жаропрочных сталей и сплавов. – М.: Интермет Инжиниринг, 2001. – 622 с. ISBN 5-89594-066-8.
- Михайлов В. А. Основные принципы синтеза функционально-ориентированных покрытий изделий машиностроения / В. А. Михайлов // Машиностроение и техносфера XXI века : сб. тр. XII междунар. науч.-техн. конф., г. Севастополь 12-17 сент. 2005 г. – Донецк: ДонНТУ, 2005. – Т. 2. – С. 277-279.
- Михайлов А. Н. Основы синтеза функционально-ориентированных технологий машиностроения. – Донецк: Технополис, 2008. 346 с.
- Михайлов А. Н., Михайлов Д. А., Грубка Р. М., Петров М. Г. Повышение долговечности деталей машин на базе функционально-ориентированных покрытий / Наукоемкие технологии в машиностр. – М.: Машиностроение, №7. 2015. С. 30-39.
- Михайлов А. Н. Функционально-ориентированные технологии. Особенности синтеза новых и нетрадиционных свойств изделий. // Машиностроение и техносфера XXI века. Сборник трудов XV международной научно-технической конференции в г. Севастополе 15-20 сентября 2008 г. В 4-х томах. – Донецк: ДонНТУ, 2008. Т. 4. 290-314 с.
- Михайлова Е. А., Михайлов Д. А. Технологическое обеспечение нанесения вакуумних ионно-плазменных покрытий на внутренние цилиндрические поверхности изделий // Сборник трудов международной научно-технической конференции
Технологии и техника автоматизации – 2009
. – Ереван: ГИУА, 2010. С. 19-22. - Михайлов Д. А. Основные особенности эксплуатации лопаток компрессора ГТД и классификация их эксплуатационных функций / Прогресивні технології і системи машинобудування: Міжнародний зб. наукових праць. – Донецьк: ДонНТУ, 2014. Вип. 4 (50). С. 121-127.
- Ивченко Т. Г., Михайлов Д. А, Михайлов А. Н., Толстых С. В. Особенности обеспечения функционально-ориентированных свойств лопаток компрессора ГТД / Инженер. Междунар. студ. научно-техн. журнал. – Донецк: ДонНТУ, 2015. С. 48-56.