Content
- Introduction
- 1. Purpose and tasks of the research
- 2. Characteristics of conveyor transport as an object of automation
- 3. An overview of existing technical solutions in the field of automation of conveyor transport
- 4. Development of the device for smooth launch of the conveyor
- Conclusions
- List of sources
Introduction
One of the main technological processes of the mining enterprise is transportation of minerals. At the same time, the main thing Conveyors remain the means of coal delivery to the shaft trunk. It's due to the following advantages of conveyor transport by compared to locomotive: continuity, low power consumption, the possibility of conveying mountain mass with inclines, small the laboriousness of conveyor line build-up, the ability to work conveyor line without human involvement. However, conveyors are inherent in and Some disadvantages: frequent gusts of tape, failure of elements actuator (reducer, motor), danger for people moving on conveyor, etc. The automation equipment allows you to eliminate some of the the aforementioned disadvantages, significantly reducing the labor intensity Conveyor line maintenance, increasing safety by reducing the level Miners' injuries to transport, increasing productivity transport chain.
The main requirements for the automation equipment conveyor transport, the following can be classified as security optimal start and stop drive, control over the condition of the conveyor and its elements, the presence of emergency locks and signaling, reliability and performance of the above functions, durability of equipment operation. Execution of these conditions reduces downtime of pipelines.
One of the most common reasons for downtime of conveyors is the gusts of the tape and the malfunction of the drive elements. The reason for this are dynamic overloads that arise when the conveyor starts, what once again confirms the need to optimize the startup process.
1. Purpose and tasks of the research
Develop a system of automation that will satisfy requirements:
- ensure a smooth start of the conveyor belt;
- provide control of the following process parameters: the speed of the tape, the stroke of the tape, the stitching and the speed of rotation drive drum;
- to ensure automatic shutdown of the conveyor drive at emergency modes;
- to provide an operational stop of the conveyor belt;
- Provide signaling, namely: warning signaling signal before starting the belt conveyor.
2. Characteristics of conveyor transport as an object of automation
Conveyor transport is a technological process of displacement rock mass with the help of conveyors in underground and open development mineral deposits. In a broad sense, a complex, uniting conveyors and accessories (for example, bunkers, feeders, etc.), technical means of production management works, as well as maintenance and repairs
Conveyor installations due to their qualities (significant performance, long transport length, ability Continuously shifting loads, the suitability of automation and remote control, high safety of work, etc.) are the most effective means of moving bulk materials to mines (mines). They are used not only for transportation bulk cargo, but also for transportation of people.
Use of conveyor installations on horizontal and sloping The developments allow in the conditions of many Donbas mines to have pipelining from the socket to the roundabout court, which in turn provides translation of coal transportation to the stream, reduces number of service personnel and creates conditions for work in resource saving mode.
The belt conveyor consists of the following main elements: in fact, conveyor belt, drive, becoming roller bearings, boot and tensioning device. Also, the conveyors are mounted tape catchers, cleaning mechanisms, mechanisms for weighing the cargo, etc.
The belt conveyor (figure 1) can be conditionally divided into three main parts: head, middle and tail. As a carrier (conveying) and pulling body are used rubber-cloth tapes with a smooth surface.
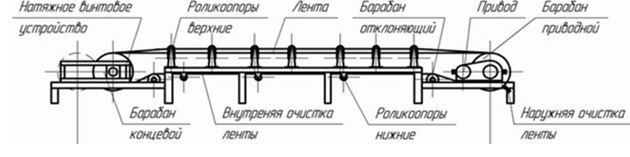
Figure 1 - Scheme of the belt conveyor
At present, almost all conveyor lines are in the mines automated Development of automation of mine conveyor lines on for a long period of time was determined by the need for reduction the complexity of management and increased operational safety conveyor transport. In connection with this, widespread has been received automated control of the conveyor line, technical essence which consists in centralizing the control of the processes of starting the conveyor belt, as well as providing automatic protection against the development of an emergency in the event of emergencies.
In the working mode of transportation of mountain mass by The following main emergency situations are possible for the conveyor line:
- blockage of rock mass in places of congestion over conveyor;
- roller conveyor roll;
- the tape speed may decrease, which is below 25% of the nominal is not permissible;
- belt slip in relation to drive drum;
- Inadmissible overheating of drive drums;
- easing the tension of the tape;
- there may be a deviation of the technological mode of operation of the flax of the exact conveyor from the passport in terms of its use in terms of performance due to the unevenness in size and discreteness in time of the cargo flow. In this case, the idle time can reach 20 ... 40% of the time of the conveyor;
- the operation of an actuator with variable load is possible, the change of which is rather difficult to foresee due to the random nature of the cargo flow.
3. An overview of existing technical solutions in the field of automation conveyor transport
SAUCL equipment:
The equipment "SAUKL" is intended for automation of mine and mine conveyor transport. Long-term experience of exploitation has confirmed high reliability, convenience in operation, functional completeness and compliance with all operational safety requirements mining equipment, including in mines and mines dangerous on gas and dust.
System of automated control of conveyor lines (SAUCL) is intended for:
- centralized automated control and control work with branched and unbranched conveyor lines, consisting of belt conveyors designed for transportation of goods and transportation of people, with the number of conveyors, controlled through one set of APU and ALS up to 60 units, and unlimited number of routes;
- centralized or local automated control and control the operation of individual conveyors, whether they are included or not included in the conveyor line;
- telecontrol and control of the accompanying state auxiliary equipment;
- automatically register and save work information pipelines and related equipment, management teams and settings, protection trips and locks.
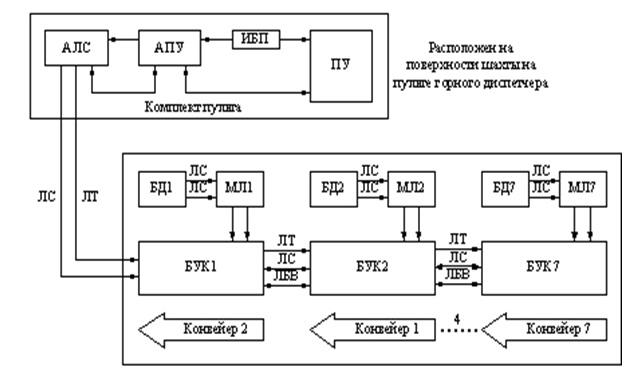
Figure 2 - Structural diagram of the SAUCL system
AUK-1M equipment:
The complex (hereinafter referred to as the apparatus) AUC - 1M is intended for automated control of stationary and semi-stationary unbroken conveyor belts made of tape and scraper conveyors (with a total of up to 10). When applied AUC - 1M complex for controlling ramified conveyor lines with a number of branches up to three, each branch is managed as independent, unbroken line.
Application area:
Equipment AUK - 1M is designed for use in underground the production of mines, hazardous by gas and dust, but can also be applied to mines, concentrating factories and other enterprises.
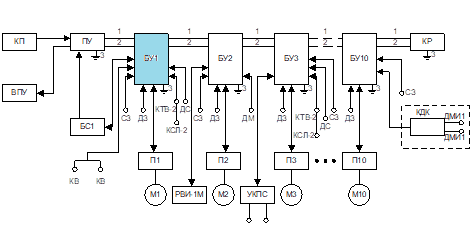
Figure 3 - Structural diagram of the AUK-1M apparatus (animation: 4 frames, delay of 1000 ms, 29.5 kilobytes)
Complex AUK.2M:
The complex of automated control of conveyors AUK.2M is intended for automated control and control work of stationary and semi-stationary unbranched conveyors lines with a number of conveyors up to 10, and also for local management of separate the conveyor, entering and not forming part of the line. The complex is intended for operation in mines, including those that are hazardous to gas or dust, at the ambient air temperature is from minus 10 to 40 ° C relative humidity up to 100% at a temperature of 35 ° С.
AUC-3 equipment:
The complex of automated control of conveyors AUK.3 is intended for automated control of unramified conveyor belts and scraping conveyors with a total number of conveyors in the line up to 10 inclusive, executive ones bodies of storage bunkers, monorail cable cars (freight), rail rope ground-water ways (freight) and multichannel roads of the chair type. The complex is a component of a conveyor belt (lines of conveyors). The complex AUK.3 is compatible with the AUK.1M complex in the part of the control line and communication. The complex is designed for operation in mines, including dangerous ones by gas and / or dust in climatic areas with moderate and cold the climate.
The application of microprocessor technology is particularly effective on large ramified conveyor lines with a large amount routes and conveyors. In this case, the micro-computer, receiving information about the productivity and speed of the combine harvesters can issue commands to change the speed of the tape of each conveyor and routes, ensuring even loading of powerful trunk conveyors. Together with the microcomputer control equipment it will provide recognition of causes and places of emergencies, timely issuing information about this to the mine manager.
One of the main requirements of the control system is smoothness Conveyor starting with limited acceleration.
4. Development of the device for smooth launch of the conveyor
The smooth launch of the conveyor allows:
- to ensure reliable tape operation without slipping and sharp jerks, by smoothly changing the torque of the engine with a specific job with the minimum value until the moment of touching and saving the constant dynamic moment in the entire start-up process;
- Controlled smooth start-up without mechanical strokes minimizes Stretching the tape, decreasing the voltage of the counterweight;
- controlled stop without mechanical strokes;
- smooth stop;
- optimum smooth start of the conveyor, even in the case various loads at the time of start, for example, start loaded and not loaded conveyors;
- increase in the service life of mechanical parts and tape;
- no need for daily maintenance.
To control the drives of tape conveyors used for the transportation of minerals to coal mines enterprises, the system of smooth launching of ribbons is being increasingly used conveyors of different manufacturers. Currently operated various systems of smooth launching both domestic and foreign production of different years of release, which differ in principle construction and characteristics, for example, domestic apparatus APM, UKTB, KUVPP and foreign firms of Hansen & Reinders, Elgor & Hansen »,« Hamacher »and others. The devices are available on various currents and constantly improving. Devices for smooth running of ribbons Type conveyors provide a significant reduction in the dynamic overloads when starting the drive, which reduces tension of the tape, also eliminates the need for complex tensioning devices, working in a wide range of tension straps changes. Except this Significantly lower starting currents that have a beneficial effect on issues of organization of the system of power supply of underground consumers, k one of the most important of which is conveying transport. Modern systems of smooth mine belt conveyors are built on The base of the thyristor voltage regulator, which is due to it relative simplicity, low loss of heating elements of the system management, as well as simple enough methods to ensure their work in conjunction with all-round protection devices against leakage current.
Figure 4 shows the functional scheme of the smooth start system belt conveyor for coal mines.
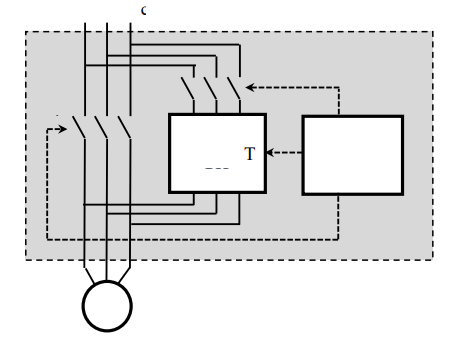
Figure 4 - Simplified Functional Diagram
The figure shows a simplified functional diagram. soft starters similar to UKTV-2-250, KUVPP, which differ in the organization of the method of shunting thyristor regulator voltage (TPH) with the help of a shunt contactor K1, while power contactor K2 is connected only for the time of acceleration electric motor (BP) belt conveyor. Power Contactors K1 and K2, and Also, the thyristor voltage regulator (TPN) is controlled by a specialized control system (SU). The worth of such the solution is no need for a long simultaneous the work of two power contactors, which leads to a decrease in the required power supply circuits of their own needs, as the power contactors are the most significant consumers of nutrition. In this way, transformer dimensions are significantly reduced, which is extremely important with point of view of the layout of the system inside the explosion-proof shell. It should also be noted the possibility of using such an implementation. K2 contactor is slightly lower than the main K1, which is associated with short (up to 20 seconds) time of its work in the launch mode in mode with the actual limitation of inrush currents.
The efficiency of the soft start system the pipeline is determined by the properties, capabilities and algorithm the functioning of the control system. This control system is integrated and combines not only the functions of the control system voltage regulator, but also the control system for power contactors and protection complex in accordance with the requirements for switching devices Mine low-voltage electrical network. To such systems The following specific requirements for TRN management are made:
- TRN control to ensure smooth controlled start-up of the machine;
- engine braking control.
It should be noted that most modern systems of smooth start-up actually function as open-ended control speeds, although usually they have the ability to connect relevant sensors. In connection with these management system TRN is actually carried out according to a mathematical model. Development Mathematical model, it is advisable to keep believing that the tape regarded as absolutely tough.
When starting the conveyor, several situations are possible:
- start-up of an empty conveyor as provided by the technological process;
- start-up of a fully loaded conveyor with a uniform a layer of load on the tape;
- starting a partially loaded conveyor with a uniform or irregular load on the tape.
The first case is the simplest, in this case the linear mass of the cargo at start-up is zero, but this case is quite rare, since the mine conveyors despite the recommendations often shut down without preloading. The third case is not so common and very difficult to simulate. The most severe case is associated with the launch fully loaded conveyor. In this case, the linear mass of the cargo will be maximum at the time of launch, and as it is unloaded, its value will be decrease down to zero.
Conclusions
As a result of the research was conducted existing automation equipment belt conveyor.
This work was done on a topic that is relevant today. since the soft starter increases the service life of all mechanical parts and ensures reliable, high-quality tape without sharp jolts and slip, and use in modern the microcontroller is quite powerful computing device with rich features built on a single chip instead of a whole set, significantly reduces size, power consumption and cost devices built on its base.
When writing this essay master's work is not yet completed. Final Completion: June 2019. Full text of the work and materials on the topic can be obtained from the author or his manager after the specified date.
List of sources
- Будишевский, В. А. Теоретические основы и расчеты транспорта энергоёмких производств / В. А. Будишевский, А. А. Сулима, Донецк 1999 г.- 216 с.
- Полунин, А. И. Оптимизация систем управления плавного пуска ленточными конвейерами / А. И. Полунин, А. В. Лавшонок // Автоматизация технологических объектов и процессов. Поиск молодых; сборник научных трудов XVI Международной научно-технической конференции аспирантов и студентов, 25-26 мая 2016 г., г. Донецк: в рамках 2-го Международного научного форума "Инновационные перспективы Донбасса". – Донецк: ДОННТУ, 2016. – С. 190–193.
- Полунин, А. И. Алгоритм управления системой плавного пуска ленточными конвейерами / А. И. Полунин, Я.А. Киселева, А. В. Лавшонок // Автоматизация технологических объектов и процессов. Поиск молодых; сборник научных трудов XVII Международной научно-технической конференции аспирантов и студентов, 24-25 мая 2017 г., г. Донецк: в рамках 3-го Международного научного форума "Инновационные перспективы Донбасса". – Донецк: ДОННТУ, 2017. – С. 79–83.
- Правила безопасности в угольных шахтах [Электронный ресурс]: утв. приказом Гос. Комитета горного и тех. надзора ДНР и Мин-вом угля и энергетики ДНР 18.04.2016 г. № 36/208: ввод в действие 17.05.2016. –Донецк, 2016. - Режим доступа: https://doc.minsvyazdnr.ru/docs/2476. – Загл. с экрана.
- Будишевский, В. А. Шахтный транспорт: учебное пособие для вузов / В. А. Будишевский [и др.]; В. А. Будишевский, Н. Д. Мухопад, А. А. Сулима, В. А. Кислун; под ред. Н. Д. Мухопада, В. А. Будишевского. - Донецк: Новый мир, 1997. - 350с.
- Баранников, Н. М. Стационарные установки рудников и шахт: Учебное пособие / Н. М. Баранников; Н. М. Баранников. - Красноярск: Изд-во Краснояр. ун-та, 1985. - 194 с.
- Бедняк, Г. И. Автоматизация производства на угольных шахтах / Г. И. Бедняк [и др.]. - К.: Техника, 1989. –269с
- Справочник по автоматизации шахтного конвейерного транспорта / Н. И. Стадник [и др.]. - Киев: Техника, 1992. –438 с.
- Попович, Г. И. Автоматизация производственных процессов угольных шахт / _Н. Г. Попович, Г. И. Данильчук, В. С. Лисовский, Г. М. Янчук. -К.: Вища школа, 1978. -336с.
- . http://mzsha.inf.ua ЧАО «Научно-производственное предприятие «Макеевский завод шахтной автоматики» (г. Макеевка).de for Virtex-4, Virtex-5, Spartan-3, and Newer CPLD Devices [Электронный ресурс]. – Режим доступа: http://www.xilinx.com/support....