Реферат
Содержание
- Введение
- 1. Актуальность темы
- 2. Цель и задачи исследования
- 3. Моделирование процессов осадки и разгонки колесных заготовок на прессах силой 20 МН, 50 МН и 100 МН
- 3.1 Моделирование процесса штамповки колёсных заготовок на осадочном прессе силой 20 МН
- 3.2 Моделирование центровки и разгонки заготовок на заготовочном прессе силой 50 МН
- 3.3 Моделирование операции формовки заготовки на формовочном прессе силой 100 МН
- Выводы
- Список источников
Введение
Данная работа посвящена проектированию калибровок валков и штампов при производстве цельнокатаных железнодорожных колес. Проектирование - это процесс создания проекта для изготовления инструмента деформации металла по всей прессопрокатной линии колесопрокатного цеха. В процессе проектирования выполняются чертежи и технические расчеты [1].
Задача проектирования профиля чистового колеса включает выполнение чертежа, а также расчет массы колеса и ряда параметров профиля его радиального сечения. Она возникает как один из этапов при создании новой конструкции колеса. После проектирования профиля колеса выполняют оценку напряженно-деформированного состояния его элементов от приложения механических и тепловых эксплуатационных нагрузок путем конечно-элементного моделирования. В случае получения неудовлетворительных результатов конструкцию изменяют, а затем выполняют проектирование профиля усовершенствованного колеса и указанные проверочные расчеты.
Во-вторых, задача проектирования профиля чистового колеса возникает у завода-изготовителя на этапе согласования с заказчиком его массы в том случае, когда отгружаются чистовые механически обработанные колеса, и на этапе проектирования профиля чернового колеса. Информация о профиле чистового колеса необходима также для реализации его механической обработки на программируемых станках.
1. Актуальность темы
Актуальным для современной теории колесопрокатного производства является создание методов проектирования технологии деформирования точных по массе (отличие заготовок по массе до 1%) заготовок колес, которые бы обеспечивали высокую точность прогноза формоизменения металла и силовых параметров процессов штамповки и прокатки заготовок. Решение данной проблемы требует изменения постановки соответствующих краевых задач и способов их реализации в соответствии с техническими и технологическими особенностями производства колес на конкретной прессопрокатной линии.
2. Цель и задачи исследования
Целью работы является усовершенствование технологии штамповки железнодорожных колёс с плоскоконическим диском в условиях АО “ВМЗ” Ø 957мм . В настоящей работе выполнена постановка задачи моделирования многопереходного процесса деформирования заготовок колес с последующей ее реализацией в системе DEFORM 3D. Моделирование выполнено для нестационарного теплового режима заготовки, то есть с учетом процессов теплообмена обрабатываемого металла с окружающей средой, как при деформации, так и во время междеформационных пауз, а также с учетом теплового эффекта пластической деформации.
3. Моделирование процессов осадки и разгонки колесных заготовок на прессах силой 20 МН, 50 МН и 100 МН
3.1 Моделирование процесса штамповки колёсных заготовок на осадочном прессе силой 20 МН
Предварительная осадка на прессе силой 20 МН производится с целью уменьшения высоты и увеличения площади поперечного сечения заготовок. Осадку применяют для улучшения структуры и механических свойств металла заготовок, а также для уменьшения неравномерности свойств в осевом и радиальном направлениях.
В процессе осадки удаляется окалина с боковых поверхностей заготовок, а также оставшаяся после гидросбива окалина с торцевых поверхностей. Пресс силой 20 МН – гидравлический вертикальный четырехколонный с архитравом и установленной на фундаменте станиной. Между станиной и архитравом расположена траверса, которая перемещается по колоннам пресса. На станину пресса и опору установлена плита, по направляющим которой перемещается стол пресса. Плита с одной стороны упирается в зуб станины, а с другой подпирается двумя гидроцилиндрами, находящимися под постоянным давлением.
Опускание траверсы осуществляется плунжером рабочего цилиндра, подъем траверсы – двумя подъемными цилиндрами, размещенными в приливах архитрава. К траверсе и столу крепятся осадочные плиты.
Рабочий цикл пресса состоит из опускания траверсы до соприкосновения с заготовкой, рабочего хода – осадки заготовки и подъема траверсы в исходное положение. Опускание траверсы начинается после подачи манипулятором заготовки на стол пресса во время его возврата в исходное положение. Установленная величина осадки обеспечивается системой автоматического управления траверсой. Для контроля высоты осаженной заготовки пресс оборудован указателем хода траверсы в виде дискового циферблата с вращающейся стрелкой. Разнотолщинность осаженных заготовок не должна превышать 2 мм.
Перед подачей заготовки на стол пресса посредством дозаторов осуществляется нанесение технологической подсыпки на середину нижней обжимной плиты с целью предупреждения запрессовки окалины, не отделившейся после гидросбива. Она подается также и на верхнюю торцевую поверхность заготовки.
После осадки заготовка убирается манипулятором из рабочей зоны пресса силой 20 МН. Для предупреждения разогрева и уменьшения износа обжимные плиты после удаления заготовки охлаждаются водой. Окалина с нижней плиты также удаляется водой.
Результаты моделирования. На первом этапе исследований было выполнено моделирование процесса остывания заготовки на воздухе при ее транспортировке (время транспортировки – 25с) по рольгангу от печи к осадочному прессу силой 20 МН. Распределение температур в заготовке после ее транспортировки и выдержки (время выдержки –5с) на нижней плите пресса 20МН представлено на рисунке 3.1.1. Средняя температура металла на поверхности заготовки перед осадкой составляет 1260 – 1280°С. Свободную осадку заготовки производят до высоты 118–120 мм. Результаты моделирования процесса осадки заготовки, представлены на рисунке 3.1.2. Полученное значение силы осадки (24,9МН) является для данного пресса максимально возможным. Его достигают при давлении рабочей жидкости 31,4МН/м2 [2]
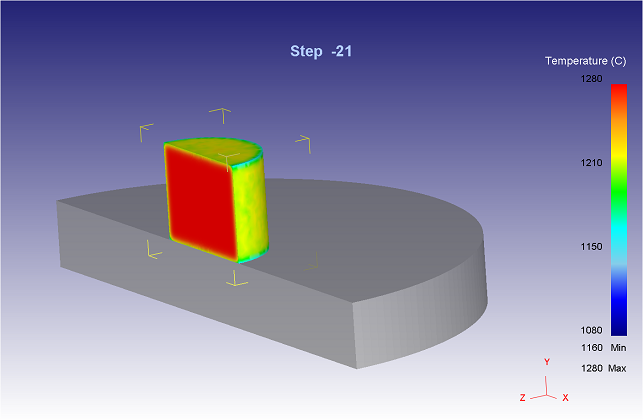
Рисунок 3.1.1 – Заготовка после транспортировки и выдержки на нижней плите
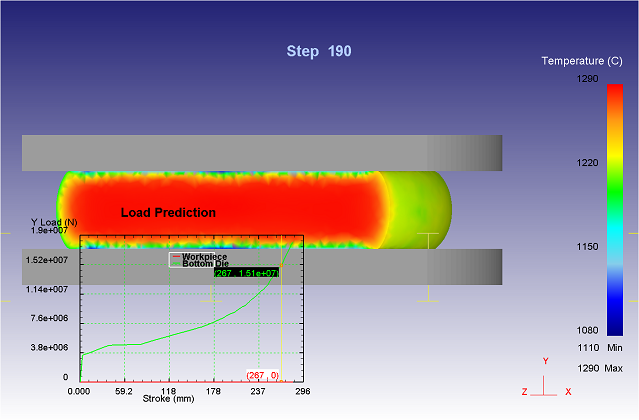
Рисунок 3.1.2 – Заготовка после осадки на прессе силой 20МН
3.2 Моделирование центровки и разгонки заготовок на заготовочном прессе силой 50 МН
По рольгангу заготовка подается к кантователю, установленному перед прессом силой 50 МН, и кантуется на 180°. Для более полного удале-ния вторичной окалины торцевые поверхности заготовки перед кантователем и после него подвергаются очистке металлическими щетками, после чего заготовка по рольгангу подается к прессу силой 50 МН.
Операции деформации на прессе силой 50 МН производятся с целью регламентированного распределения металла между периферийной и центральной частями заготовки. Пресс силой 50 МН – гидравлический вертикальный четырехколонный состоит из неподвижных поперечин – станины и архитрава, соединенных между собой колоннами.
В нижней части станины установлен выталкиватель с гидравлическим приводом. Пресс снабжен центрователем технологического кольца, состоящим из подъемного механизма с гидравлическим приводом и обоймой. Нижний плитодержатель своим хвостовиком устанавливается в расточку квадратной плиты, перемещающейся с помощью четырех регулировочных клиньев. Нижняя и верхняя осадочные плиты устанавливаются в плитодержателях.
На прессе силой 50 МН в верхний плитодержатель устанавливается конусная плита. Заготовку после ее предварительной осадки на прессе силой 20 МН укладывают на стол пресса силой 50 МН и центруют технологическим кольцом. Осадку и разгонку заготовок выполняют за одну операцию. Причем, если разгонка осуществляется не на всю высоту клина, то дополнительной осадки заготовки не происходит. Преимущество такой технологии связано с исключением операции разгонки заготовок пуансоном и соответственно с уменьшением цикла на прессе силой 50 МН. Для ее реализации необходимы точные по массе заготовки с разновесом не более ±5 кг. Это связано с тем, что в процессе предварительной осадки исходных заготовок на прессе силой 20 МН требуется получить достаточно стабильный диаметр, обеспечивающий, как указано выше, их центровку технологическим кольцом пресса силой 50 МН.
Установленная величина осадки и разгонки заготовки обеспечивается системой автоматического управления траверсой. Контроль величины осадки выполняют по метке на дисковом указателе хода траверсы. В технологическом кольце заготовка должна обжиматься осесимметрично с получением равномерного отпечатка по всей боковой поверхности заготовки. После деформации окалина с заготовки удаляется воздухом, а с инструмента – водой во время его охлаждения. Несоблюдение технологии и неудовлетворительная настройка оборудования, а также выработка инструмента деформации и других деталей приводит к появлению дефектов на заготовках после пресса силой 50 МН таких как: запрессовка окалины; разнотолщинность заготовок; отклонение от заданной формы заготовки после разгонки конусной плитой; местные углубления на поверхности заготовок; рванины; складки на торцевых поверхностях заготовки.
Результаты моделирования. После свободной осадки заготовка подается на пресс 50 МН (время транспортировки – 10 с) для разгонки в технологическом кольце. Перед прессом 50 МН заготовку кантуют на 180° для выравнивания температуры с верхней и нижней сторон заготовки. На рисунке 3.2.1 а,б представлено распределение температуры в заготовке до и после ее транспортировки к прессу 50 МН и выдержке заготовки (время выдержки – 5с) на нижней обжимной плите пресса. Средняя температура металла на поверхности заготовки перед разгонкой составляет 1250 – 1270°С.
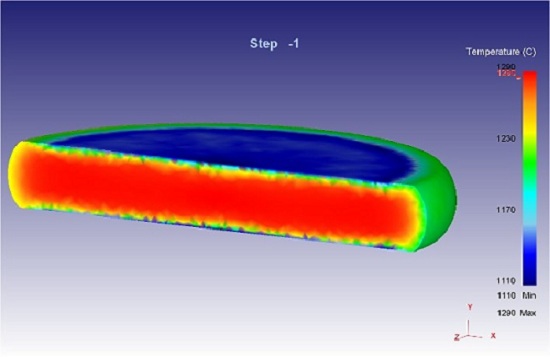
а)
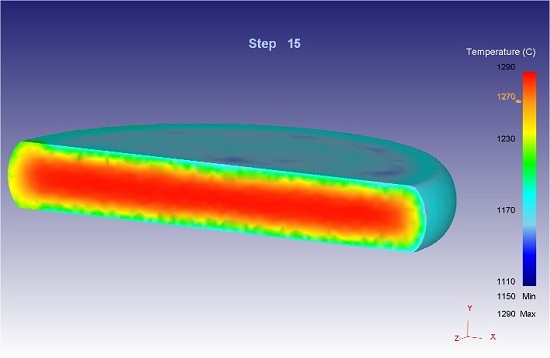
б)
Рисунок 3.2.1 – Заготовка до (а) и после транспортировки и выдержки на нижней плите (б)
После укладки заготовки на обжимную плиту выполняют центровку технологического кольца по оси пресса и выполняют опускание траверсы пресса до вхождения в контакт конусной плиты с заготовкой. Результаты моделирования процесса до и после разгонки заготовки на прессе силой 50 МН представлены на рис. 3.2.2 а,б.
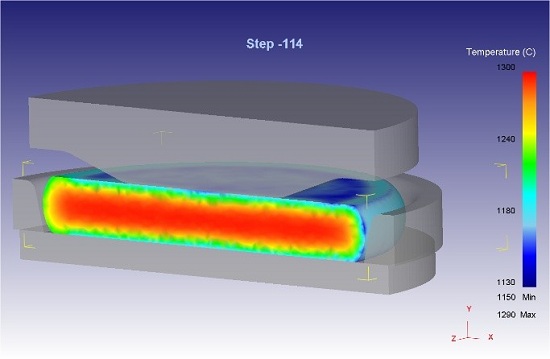
а)
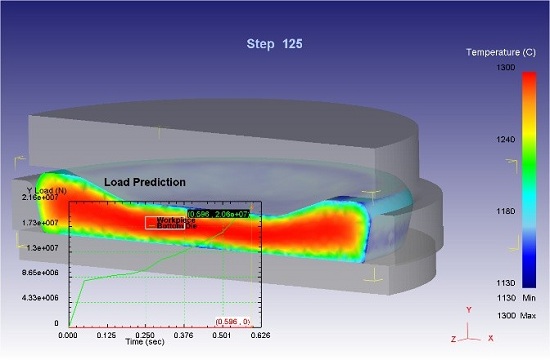
б)
Рисунок 3.2.2 – Заготовка до (а) и после разгонки (б) на прессе силой 50МН
3.3 Моделирование операции формовки заготовки на формовочном прессе силой 100 МН
С пресса силой 50 МН заготовка убирающим перекладывателем перемещается на отводящий рольганг и транспортируется к формовочному прессу силой 100 МН. При этом она подвергается очистки от окалины металлическими щётками. Деформация заготовки на прессе силой 100 МН производится с целью получения отформованной заготовки с окончательными размерами ступицы и прилегающей к ней части диска, а также подготовки обода и прилегающей к нему части диска для последующей прокатки на колесопрокатном стане.
Пресс силой 100 МН – гидравлический вертикальный четырёхколонный имеет две неподвижные поперечины – станину и архитрав, соединённые между собой четырьмя колоннами. В архитраве установлен рабочий цилиндр пресса, а также два подъёмных дифференциальных и два уравновешивающих цилиндра. Плунжеры этих цилиндров закреплены на подвижной траверсе. К траверсе крепится подштамповая плита, в которой установлен верхний выталкиватель заготовки. Цилиндр выталкивателя работает совместно с подъёмными цилиндрами траверсы. Технологический цикл работы пресса силой 100 МН включает следующие операции: укладку заготовки на нижний формовочный штамп; центровку заготовку на штампе; опускание траверсы до соприкосновения верхнего штампа с заготовкой; рабочий ход – формовку заготовку; подъём траверсы в исходное положение; удаление отформованной заготовки с помощью выталкивателей из верхнего и нижнего штампа и выдачу её на рольганг.
Величина деформации заготовки на прессе обеспечивается системой автоматического управления траверсой пресса. Заданную величину толщины диска контролируют по метке на дисковом указателе хода траверсы. Также должны быть обеспечены чёткое оформление торцевых поверхностей ступицы и равномерный отпечаток формовочного кольца по всей окружности наружной поверхности обода. Несоблюдение технологии и неудовлетворительная настройка прессов, а также выработка штампов и других деталей приводит к появлению дефектов на колёсных заготовках после пресса силой 100 МН таких как: разноширинность и разнотолщинность обода; разнотолщинность диска; толстый или тонкий диск у ступицы; складка ступицы; смещение ступицы, её не выполнение или разностенность; отпечатки на поверхности колёсных заготовок. После подъёма траверсы осуществляется удаление отформованной заготовки из верхнего и нижнего штампов выталкивателями и удержание её в поднятом состоянии до момента захвата заготовки клещами перекладывателя.
Результаты моделирования. После операции разгонки заготовка подается (время транспортировки – 20 с) на формовочный пресс силой 100 МН. На рисунке 3.3.1 (а) представлено распределение температуры в заготовке после ее транспортировки к прессу 100 МН и выдержки на нижнем штампе (время выдержки – 8,5 с). Средняя температура металла на поверхности заготовки перед формовкой в штампах составляет 1130 – 1160°С. Результаты моделирования процесса формовки заготовки на прессе силой 100 МН представлены на рисунке 3.3.1 (б).
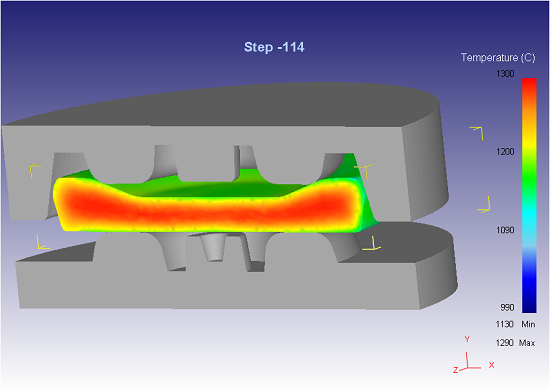
а)
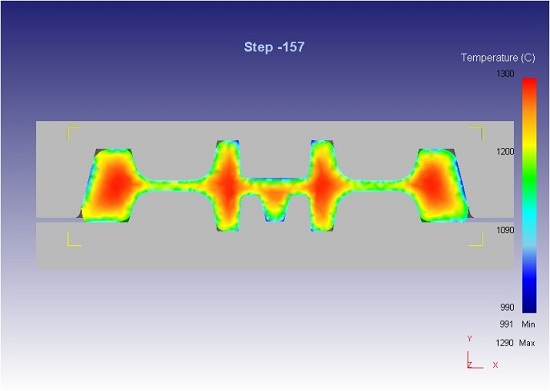
б)
Рисунок 3.3.1 – Заготовка после транспортировки, выдержки на нижнем штампе (а) и формовки на прессе силой 100МН (б)
Невысокое значение силы формовки объясняется тем, что при моделировании величина разгонки заготовки на прессе 50 МН обеспечила с одной стороны выполнение ступицы (см. рисунок 3.3.1 (б)), а с другой – исключение перетекания металла из центральной полости формовочных штампов в периферийную. Естественно, что на практике так точно подобрать величину разгонки не удается, в том числе по причине разновеса заготовок. Поэтому в реальных условиях промышленного производства сила формовки с учетом потерь может достигать 90 МН по причине преждевременного заполнения центральной полости штампов в зоне ступицы и изменения направления течения металла в зоне диска на одностороннее. За счет этого избегают получения неисправимого вида брака, «невыполнение ступицы», при допустимой на прессе силе штамповки.
Из рисунка 3.3.1 (б) видно, что периферийная полость штампов, формирующая верхний торец обода под прокатку, заполняется металлом не полностью и неравномерно. Такая картина формоизменения металла хорошо согласуется, причем не только качественно, но и количественно, с экспериментально установленными закономерностями формоизменения металла в формовочных штампах авторами работ [3],[4],[5]
Выводы
Таким образом, выполнена постановка и реализация задачи конечно-элементного моделирования процессов осадки, разгонки и формовки заготовок колес применительно к условиям прессопрокатных линий ПАО «ВМЗ». Полученные в системе DEFORM 3D результаты моделирования в целом правильно отражают основные закономерности анализируемых процессов, установленные в условиях промышленного производства колес. Разработанные и реализованные в DEFORM 3D математические модели также были использованы для оценки эффективности новых технологических режимов и способов деформирования, а также при создании аналитических зависимостей для оперативного расчета параметров формоизменения металла и сил при штамповке и прокатке заготовок колес.
На прессе силой 50 МН осадка и разгонка заготовки выполняется одновременно за один ход траверсы пресса. Но предварительно центрует технологическое кольцо вместе с поданной на стол заготовкой. Для реализации этого процесса необходимы точные по массе заготовки с разновесом не более ±5 кг. Это связано с тем, что в процессе предварительной осадки исходных заготовок на прессе силой 20 МН требуется получить достаточно стабильный диаметр, обеспечивающий их центровку технологическим кольцом пресса силой 50 МН.
Используя экспериментальные данные о силовых параметрах процесса прокатки в качестве исходной информации, оценку адекватности результатов моделирования выполняли путем сравнения расчетных параметров формоизменения заготовки с аналогичными параметрами, зафиксированными в промышленных условиях. Полученные при моделировании значения сил штамповки, температур заготовок и параметров их формоизменения хорошо согласуются с экспериментальными данными, полученными в условиях промышленного производства колес Ø 957 мм.
Список источников
- Яковченко, А.В. Проектирование профилей и калибровок железно-дорожных колес : монография / А.В. Яковченко, Н.И. Ивлева, Р.А. Голышков. - Донецк: ДонНТУ, 2008. – 491с.
- Гун Г.Я. Теоретические основы обработки металлов давленим / Г.Я. Гун. – М.: Металлургия, 1980. – 456 с.: ил.
- Прогнозирование и способ устранения образования зажимов при формовке колесных заготовок / Б.Г. Каплунов, В.Н. Крашевич, М.И. Староселецкий, А.В. Белущенко // Изв. вузов Черная металлур-гия. – 1991. – № 1. – С. 55–56.
- Шифрин М.Ю. Резервы производительности и выхода годного при прокатке колес / М.Ю. Шифрин. – М.: Металлургия, 1989. – 144 с.: ил.
- Шифрин М.Ю. Рациональный режим осадки обода колесной заго-товки / М.Ю. Шифрин // Сталь. – 1993. – № 5. – С. 52–54.