Реферат
Зміст
- Вступ
- 1. Актуальність теми
- 2. Мета і задачі дослідження
- 3. Моделювання процесів опади і розгону колісних заготовок на пресах силою 20 МН, 50 МН і 100 МН
- 3.1 Моделювання процесу штампування колісних заготовок на осадочном пресі силою 20 МН
- 3.2 Моделювання центрування і розгону заготовок на заготівельних пресі силою 50 МН
- 3.3 Моделювання операції формовки заготовки на формувальному пресі силою 100 МН
- Висновки
- Список джерел
Вступ
Дана робота присвячена проектуванню калибровок валків і штампів при виробництві суцільнокатаних залізничних коліс. Проектування - це процес створення проекту для виготовлення інструменту деформації металу по всій прессопрокатной лінії колесопрокатного цеху. В процесі проектування виконуються креслення і технічні розрахунки [1].
Завдання проектування профілю чистового колеса включає виконання креслення, а також розрахунок маси колеса і ряду параметрів профілю його радіального перетину. Вона виникає як один з етапів при створенні нової конструкції колеса. Після проектування профілю колеса виконують оцінку напружено-деформованого стану його елементів від додатка механічних і теплових експлуатаційних навантажень шляхом кінцево-елементного моделювання. У разі отримання незадовільних результатів конструкцію змінюють, а потім виконують проектування профілю вдосконаленого колеса і зазначені перевірочні розрахунки.
По-друге, завдання проектування профілю чистового колеса виникає у заводу-виготовлювача на етапі узгодження з замовником його маси в тому випадку, коли відвантажуються чистові механічно оброблені колеса, і на етапі проектування профілю чорнового колеса. Інформація про профіль чистового колеса необхідна також для реалізації його механічної обробки на програмованих верстатах.
1. Актуальність теми
Актуальним для сучасної теорії колесопрокатного виробництва є створення методів проектування технології деформування точних по масі (відміну заготовок по масі до 1%) заготовок коліс, які б забезпечували високу точність прогнозу формозміни металу і силових параметрів процесів штампування і прокатки заготовок. Рішення даної проблеми вимагає зміни постановки відповідних крайових задач та способів їх реалізації відповідно до технічних і технологічними особливостями виробництва коліс на конкретній прессопрокатной лінії.
2. Мета і задачі дослідження
Метою роботи є удосконалення технології штампування залізничних коліс з плоскоконіческім диском в умовах АТ "ВМЗ" Ø 957мм. У даній роботі виконана постановка задачі моделювання багатоперехідних процесу деформування заготовок коліс з подальшою її реалізацією в системі DEFORM 3D. Моделювання виконано для нестаціонарного теплового режиму заготовки, тобто з урахуванням процесів теплообміну оброблюваного металу з навколишнім середовищем, як при деформації, так і під час междеформаціонних пауз, а також з урахуванням теплового ефекту пластичної деформації.
3. Моделювання процесів опади і розгону колісних заготовок на пресах силою 20 МН, 50 МН і 100 МН
3.1 Моделювання процесу штампування колісних заготовок на осадочном пресі силою 20 МН
Попередня осаду на пресі силою 20 МН проводиться з метою зменшення висоти і збільшення площі поперечного перерізу заготовок. Осадку застосовують для поліпшення структури і механічних властивостей металу заготовок, а також для зменшення нерівномірності властивостей в осьовому і радіальному напрямках.
В процесі опади видаляється окалина з бічних поверхонь заготовок, а також залишилася після гідрозбиву окалина з торцевих поверхонь. Прес силою 20 МН - гідравлічний вертикальний чотириколонний з архитравом і встановленої на фундаменті станиною. Між станиною і архитравом розташована траверса, яка переміщається по колонах преса. На станину преса і опору встановлена плита, по напрямних якої переміщується стіл преса. Плита з одного боку упирається в зуб станини, а з іншого підпирається двома гідроциліндрами, які перебувають під постійним тиском.
Опускання траверси здійснюється плунжером робочого циліндра, підйом траверси - двома підйомними циліндрами, розміщеними в припливах архітрава. До траверсі і столу кріпляться осадові плити.
Робочий цикл преса складається з опускання траверси до зіткнення із заготівлею, робочого ходу - опади заготовки і підйому траверси в початкове положення. Опускання траверси починається після подачі маніпулятором заготовки на стіл преса під час його повернення в початкове положення. Встановлена величина опади забезпечується системою автоматичного управління траверсою. Для контролю висоти осаджені заготовки прес обладнаний покажчиком ходу траверси у вигляді дискового циферблату з обертається стрілкою. Різнотовщинність осаджені заготовок не повинна перевищувати 2 мм.
Перед подачею заготовки на стіл преса за допомогою дозаторів здійснюється нанесення технологічної підсипання на середину нижньої обжимной плити з метою попередження запрессовки окалини, що не відокремилася після гідрозбиву. Вона спрацьовує навіть на верхню торцеву поверхню заготовки.
Після опади заготівля забирається маніпулятором з робочої зони преса силою 20 МН. Для попередження розігріву і зменшення зносу обтискні плити після видалення заготовки охолоджуються водою. Окалина з нижньої плити також видаляється водою.
Результати моделювання. На першому етапі досліджень було виконано моделювання процесу охолодження заготовки на повітрі при її транспортуванні (час транспортування - 25с) по рольгангу від печі до осадового пресу силою 20 МН. Розподіл температур в заготівлі після її транспортування і витримки (час витримки 5С) на нижній плиті преса 20МН представлено на малюнку 3.1.1. Середня температура металу на поверхні заготовки перед осадкою становить 1260 - 1280°С. Вільну осадку заготовки виробляють до висоти 118-120 мм. Результати моделювання процесу опади заготовки, представлені на малюнку 3.1.2. Отримане значення сили опади (24,9МН) є для даного преса максимально можливим. Його досягають при тиску робочої рідини 31,4МН/м2 [2]
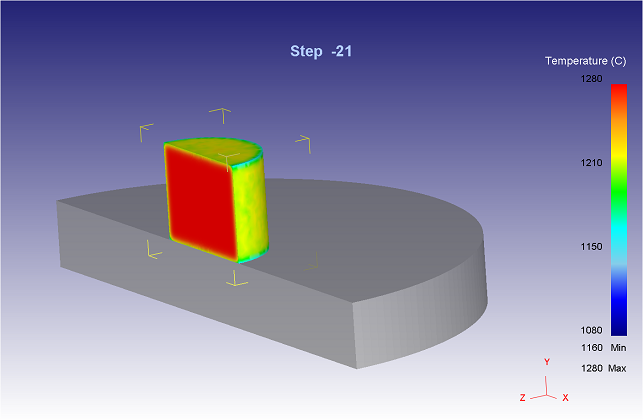
Малюнок 3.1.1 - Заготівля після транспортування і витримки на нижній плиті
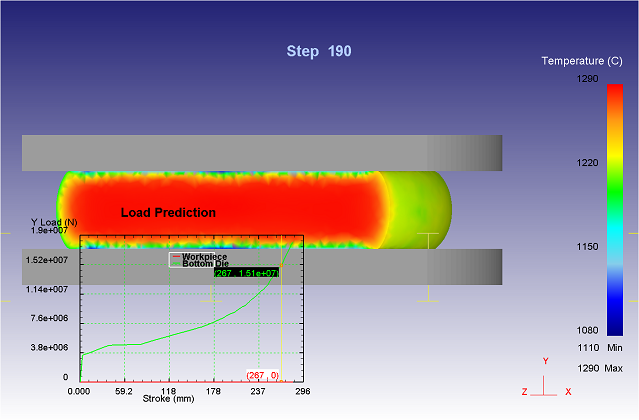
Малюнок 3.1.2 - Заготівля після осідання на пресі силою 20МН
3.2 Моделювання центрування і розгону заготовок на заготівельних пресі силою 50 МН
За рольгангу заготівля подається до кантувач, встановленому перед пресом силою 50 МН, і кантується на 180°. Для більш повного видалити-ня вторинної окалини торцеві поверхні заготовки перед кантователем і після нього піддаються очищенню металевими щітками, після чого заготівля по рольгангу подається до пресу силою 50 МН.
Операції деформації на пресі силою 50 МН виробляються з метою регламентованого розподілу металу між периферійної і центральної частинами заготовки. Прес силою 50 МН - гідравлічний вертикальний чотириколонний складається з нерухомих поперечок - станини і архітрава, з'єднаних між собою колонами.
У нижній частині станини встановлений виштовхувач з гідравлічним приводом. Прес забезпечений центрователем технологічного кільця, що складається з підйомного механізму з гідравлічним приводом і обоймою. Нижній плітодержатель своїм хвостовиком встановлюється в розточення квадратної плити, що переміщається за допомогою чотирьох регулювальних клинів. Нижня і верхня осадові плити встановлюються в плітодержателях.
На пресі силою 50 МН в верхній плітодержатель встановлюється конусна плита. Заготівлю після її попередньої опади на пресі силою 20 МН укладають на стіл преса силою 50 МН і центруют технологічним кільцем. Осадку і розгонку заготовок виконують за одну операцію. Причому, якщо разгонка здійснюється не на всю висоту клина, то додаткової опади заготовки не відбувається. Перевага такої технології пов'язано з виключенням операції розгону заготовок пуансоном і відповідно зі зменшенням циклу на пресі силою 50 МН. Для її реалізації необхідні точні за масою заготовки з важками не більше ±5 кг. Це пов'язано з тим, що в процесі попередньої опади вихідних заготовок на пресі силою 20 МН потрібно отримати досить стабільний діаметр, що забезпечує, як зазначено вище, їх центрування технологічним кільцем преса силою 50 МН.
Встановлена величина опади і розгону заготовки забезпечується системою автоматичного управління траверсою. Контроль величини опади виконують по мітці на дисковому покажчику ходу траверси. У технологічному кільці заготовка повинна обжимається Осесиметрична з отриманням рівномірного відбитка по всій бічній поверхні заготовки. Після деформації окалина з заготовки видаляється повітрям, а з інструменту - водою під час його охолодження. Недотримання технології та незадовільна налаштування обладнання, а також вироблення інструменту деформації і інших деталей призводить до порушення нормальної роботи на заготовках після преса силою 50 МН таких як: запрессовка окалини; разнотолщинность заготовок; відхилення від заданої форми заготовки після розгону конусної плитою; місцеві поглиблення на поверхні заготовок; рванини; складки на торцевих поверхнях заготовки.
Результати моделювання. Після вільної опади заготівля подається на прес 50 МН (час транспортування - 10 с) для розгону в технологічному кільці. Перед пресом 50 МН заготовку кантуют на 180° для вирівнювання температури з верхньої та нижньої сторін заготовки. На малюнку 3.2.1 а, б представлено розподіл температури в заготівлі до і після її транспортування до пресу 50 МН і витримці заготовки (час витримки - 5 с) на нижній обжимной плиті преса. Середня температура металу на поверхні заготовки перед розгоном становить 1250 – 1270°С.
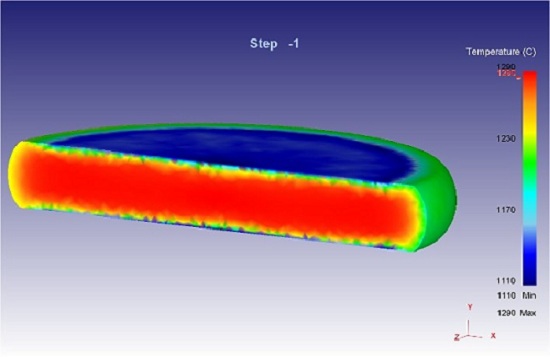
а)
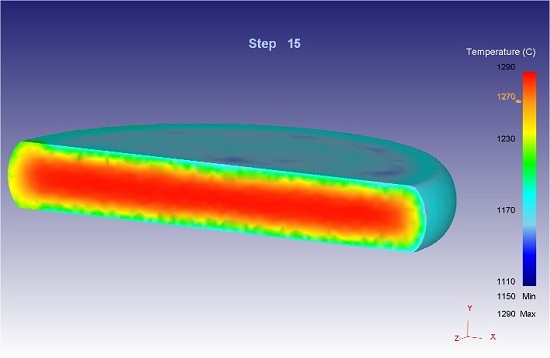
б)
Малюнок 3.2.1 - Заготівля до (а) і після транспортування і витримки на нижній плиті (б)
Після укладання заготовки на обжимную плиту виконують центрування технологічного кільця по осі преса і виконують опускання траверси преса до входження в контакт конусної плити з заготівлею. Результати моделювання процесу до і після розгону заготовки на пресі силою 50 МН представлені на рис. 3.2.2 а,б.
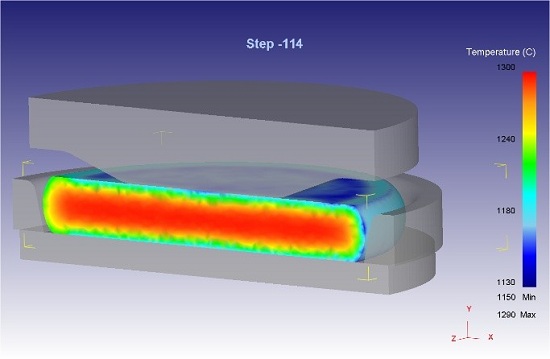
а)
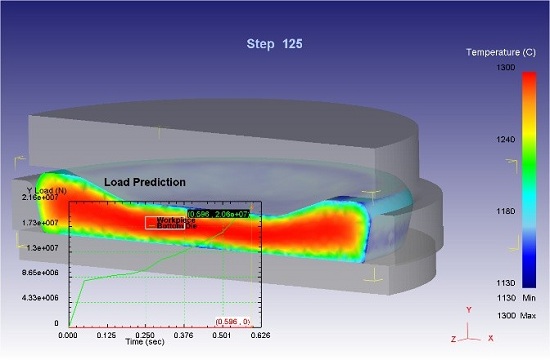
б)
Малюнок 3.2.2 - Заготівля до (а) і після розгону (б) на пресі силою 50МН
3.3 Моделювання операції формовки заготовки на формувальному пресі силою 100 МН
З преса силою 50 МН заготівля прибирають іперекладивателем переміщається на відвідний рольганг і транспортується до формувальних пресу силою 100 МН. При цьому вона піддається очищення від окалини металевими щітками. Деформація заготовки на пресі силою 100 МН проводиться з метою отримання отформованной заготовки з остаточними розмірами маточини і прилеглої до неї частини диска, а також підготовки обода і прилеглої до нього частини диска для подальшої прокатки на колесопрокатному стані.
Прес силою 100 МН - гідравлічний вертикальний чотириколонним має дві нерухомі поперечки - станину і архітрав, з'єднані між собою чотирма колонами. У архітраві встановлений робочий циліндр преса, а також два підйомних диференціальних і два врівноважують циліндра. Плунжери цих циліндрів закріплені на рухомій траверсі. До траверсі кріпиться підштамповою плита, в якій встановлено верхню виштовхувач заготовки. Циліндр поршня працює спільно з підйомними циліндрами траверси. Технологічний цикл роботи преса силою 100 МН включає наступні операції: укладання заготовки на нижній формувальний штамп; центрування заготовку на штампі; опускання траверси до зіткнення верхнього штампа із заготівлею; робочий хід - формовку заготовку; підйом траверси в початкове положення; видалення отформованной заготовки за допомогою виштовхувачів з верхнього і нижнього штампа і видачу її на рольганг.
Величина деформації заготовки на пресі забезпечується системою автоматичного управління траверсой преса. Задану величину товщини диска контролюють по мітці на дисковому покажчику ходу траверси. Також повинні бути забезпечені чітке оформлення торцевих поверхонь маточини і рівномірний відбиток формувального кільця по всьому колу зовнішньої поверхні обода. Недотримання технології та незадовільна настройка пресів, а також вироблення штампів та інших деталей призводить до порушення нормальної роботи на колісних заготовках після преса силою 100 МН таких як: разношірінность і разнотолщинность обода; разнотолщинность диска; товстий або тонкий диск у маточини; складка маточини; зміщення маточини, її не виконання або разностенность; відбитки на поверхні колісних заготовок. Після підйому траверси здійснюється видалення отформованной заготовки з верхнього і нижнього штампів виштовхувачами і утримання її в піднятому стані до моменту захоплення заготовки кліщами перекладивателем.
Результати моделювання. Після операції розгону заготовка подається (час транспортування - 20 с) на формувальний прес силою 100 МН. На малюнку 3.3.1 (а) представлено розподіл температури в заготівлі після її транспортування до пресу 100 МН і витримки на нижньому штампі (час витримки - 8,5 с). Середня температура металу на поверхні заготовки перед формуванням в штампах становить 1130 - 1160 ° С. Результати моделювання процесу формування заготовки на пресі силою 100 МН представлені на малюнку 3.3.1 (б).
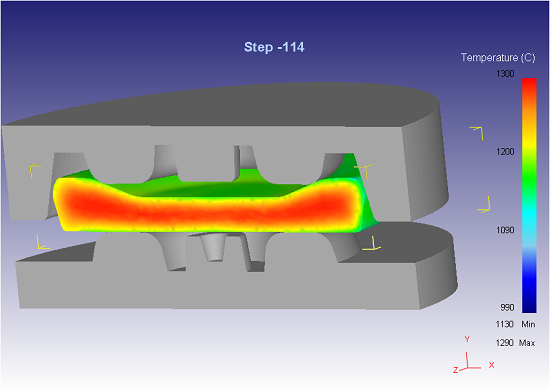
а)
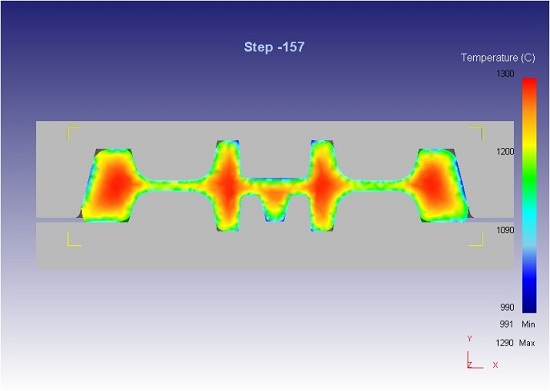
б)
Малюнок 3.3.1 - Заготівля після транспортування, витримки на нижньому штампі (а) і формування на пресі силою 100МН (б)
Невисоке значення сили формування пояснюється тим, що при моделюванні величина розгону заготовки на пресі 50 МН забезпечила з одного боку виконання маточини (див. Рисунок 3.3.1 (б)), а з іншого - виключення перетікання металу з центральної порожнини формувальних штампів в периферійну. Природно, що на практиці так точно підібрати величину розгону не вдається, в тому числі з причини Важок заготовок. Тому в реальних умовах промислового виробництва сила формування з урахуванням втрат може досягати 90 МН через передчасного заповнення центральної порожнини штампів в зоні маточини і зміни напрямку течії металу в зоні диска на одностороннє. За рахунок цього уникають отримання невиправного виду шлюбу, «невиконання маточини», при допустимій на пресі силі штампування.
З малюнка 3.3.1 (б) видно, що периферійна порожнину штампів, що формує верхній торець обода під прокатку, заповнюється металом в повному обсязі і нерівномірно. Така картина формозміни металу добре узгоджується, причому не тільки якісно, але і кількісно, з експериментально встановленими закономірностями формозміни металу в формувальних штампах авторами робіт [3],[4],[5]
Висновки
Таким чином, виконана постановка і реалізація завдання кінцево-елементного моделювання процесів опади, разгонки і формування заготовок коліс з урахуванням умов прессопрокатних ліній ПАТ «ВМЗ». Отримані в системі DEFORM 3D результати моделювання в цілому правильно відображають основні закономірності аналізованих процесів, встановлені в умовах промислового виробництва коліс. Розроблені і реалізовані в DEFORM 3D математичні моделі також були використані для оцінки ефективності нових технологічних режимів і способів деформування, а також при створенні аналітичних залежностей для оперативного розрахунку параметрів формозміни металу і сил під час штампування і прокатки заготовок коліс.
На пресі силою 50 МН осаду і разгонка заготовки виконується одночасно за один хід траверси преса. Але попередньо центрує технологічне кільце разом з поданою на стіл заготівлею. Для реалізації цього процесу необхідні точні за масою заготовки з важками не більше ±5 кг. Це пов'язано з тим, що в процесі попередньої опади вихідних заготовок на пресі силою 20 МН потрібно отримати досить стабільний діаметр, що забезпечує їх центрування технологічним кільцем преса силою 50 МН.
Використовуючи експериментальні дані про силових параметрах процесу прокатки в якості вихідної інформації, оцінку адекватності результатів моделювання виконували шляхом порівняння розрахункових параметрів формозміни заготовки з аналогічними параметрами, зафіксованими в промислових умовах. Отримані при моделюванні значення сил штампування, температур заготовок і параметрів їх формозміни добре узгоджуються з експериментальними даними, отриманими в умовах промислового виробництва коліс Ø 957 мм.
Перелік посилань
- Яковченко, А.В. Проектування профілів і калібрувань залізно-дорожніх коліс: монографія / А.В. Яковченко, Н.І. Івлєва, Р.А. Голишко. - Донецьк: ДонНТУ, 2008. - 491с.
- Гун Г.Я. Теоретичні основи обробки металів тиском / Г.Я. Гун. - М .: Металургія, 1980. - 456 с .: іл.
- Прогнозування і спосіб усунення освіти затискачів при формуванні колісних заготовок / Б.Г. Каплунов, В.Н. Крашевіч, М.І. Староселецкій, А.В. Белущенко // Изв. вузів Чорна підприєм-гія. - 1991. - № 1. - С. 55-56.
- Шифрін М.Ю. Резерви продуктивності і виходу придатного при прокатці коліс / М.Ю. Шифрін. - М .: Металургія, 1989. - 144 с .: іл.
- Шифрін М.Ю. Раціональний режим опади обода колісної заго-товки / М.Ю. Шифрін // Сталь. - 1993. - № 5. - С. 52-54.