Реферат по теме выпускной работы
Содержание
- Введение
- 1. Цель работы
- 2. Актуальность
- 3. Требования, предъявляемые к зубчатым передачам
- 4. Методы упрочнения зубчатых колес
- Выводы
- Список источников
Введение
Актуальной задачей в машиностроении на сегодняшний день является проектирование и изготовление конкурентоспособных машин и агрегатов с высокими эксплуатационными характеристиками. Зубчатые передачи являются наиболее распространёнными типами механических передач. Они находят широкое применение во всех отраслях машиностроения, в частности в металлорежущих станках, автомобилях, тракторах, сельхозмашинах и т.д., в приборостроении, часовой промышленности и др. Их применяют для передачи мощностей от долей до десятков тысяч киловатт при окружных скоростях до 150 м/с и передаточных числах до нескольких сотен и даже тысяч, с диаметром колёс от долей миллиметра до 6 м и более.
1. Цель работы
Целью работы является повышение качества и эксплуатационных свойств зубчатых колес на основе совершенствования этапов отделочной и упрочняющей обработки зубьев и нанесения функционально-ориентированных покрытий.
Для достижения поставленной цели необходимо решить следующие задачи:
- выполнить анализ современного состояния вопроса производства и эксплуатации зубчатых колес;
- исследовать основные конструктивные особенности зубчатых передач а также параметров зубчатых колес, обеспечивающих повышение эксплуатационных свойств;
- разработать общую структуру и алгоритм проведения исследований;
- предложить технологические методы повышения производительности и качества отделочной и упрочняющей обработки рабочих поверхностей зубьев, обеспечивающих повышение эксплуатационных характеристик зубчатых колес;
- разработать рекомендации направленные на повышение эксплуатационных характеристик зубчатых передач.
2. Актуальность
Наиболее часто выход из строя зубчатого колеса связан с износом зубьев. При изнашивании зуб изменяет свою первоначальную геометрическую форму, а это в свою очередь, приводит к кинематической неточности, а как следствие к поломке зуба и выхода передачи из строя. Для уменьшения износа поверхности контакта должны быть выполнены из антифрикционного и износостойкого материала, что может быть достигнуто за счет упрочняющей обработки поверхностей зубьев. В настоящее время существует много способов повышения износостойкости и долговечности зубчатых передач, но проблема не решена до конца и является актуальной.
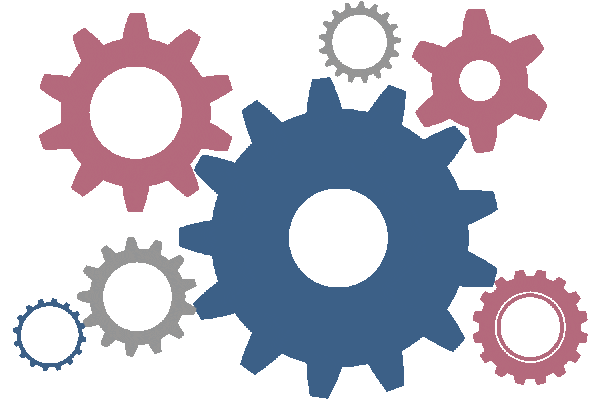
Рисунок 1 – Пример передачи вращательного движения зубчатых колёс
3. Требования, предъявляемые к зубчатым передачам
Основные требования, предъявляемые к зубчатым передачам в приборостроении, сводятся к получению большого значения передаточного числа при малых габаритах передаточного механизма и к необходимости обеспечения наиболее точного перемещения ведомого звена. В отличие от зубчатых передач, применяемых в общем машиностроении, зубчатые передачи в приборостроении передают малые усилия, благодаря чему в большинстве случаев не требуется расчета элементов зубчатых передач на прочность.
Достоинства зубчатых передач:
- Возможность применения в широком диапазоне скоростей, мощностей и передаточных отношений.
- Высокая нагрузочная способность и малые габариты.
- Большая долговечность и надёжность работы.
- Постоянство передаточного отношения.
- Высокий КПД (87-98%).
- Простота обслуживания [4].
Недостатки зубчатых передач:
- Большая жёсткость не позволяющая компенсировать динамические нагрузки.
- Высокие требования к точности изготовления и монтажа.
- Шум при больших скоростях.
Виды разрушения зубьев
1. Усталостное выкрашивание рабочих поверхностей зубьев – основной вид разрушения зубьев для большинства закрытых, хорошо смазываемых передач.Разрушение проявляется в виде оспинок (ямок) и начинается вблизи полюсной линии в зоне однопарного зацепления (где действует максимальная нагрузка) у ножки зуба, а затем распространяется на всю поверхность ножки. Со временем ямки выкрашивания сливаются, начинается прогрессивное выкрашивание.
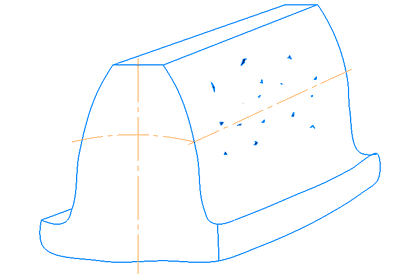
Рисунок 2 – Усталостное выкрашивание
2. Абразивный износ характерен для открытых передач или передач, работающих в засорённой среде (горные, дорожные, строительные и другие машины).
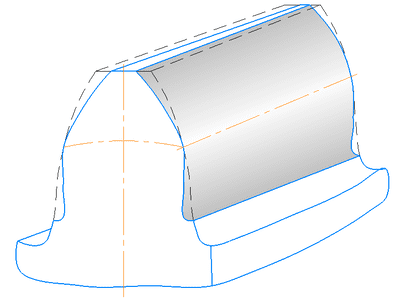
Рисунок 3 – Изнашивание зубьев
3. Заедание зубьев – местное молекулярное сцепление (микросварка) сопряжённых поверхностей зубьев вследствие разрушения смазочной плёнки и местного повышения температуры при относительном скольжении в зоне контакта.
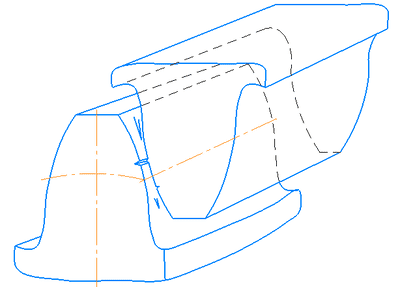
Рисунок 4 – Заедание зубьев
Заедание зубьев предупреждают повышением твёрдости поверхностей, подбором противозадирных масел.
Расчёты на заедание сводятся к проверке температуры в местах контакта и в сопоставлении её с температурой вспышки масел.
4. Излом зубьев является наиболее опасным видом разрушения, т.к. приводит к полной утрате работоспособности передачи. Поломку зубьев относят к категории внезапных и полных отказов.
Излом зубьев является следствием действия от нулевого цикла напряжений изгиба или перегрузки ударного действия.
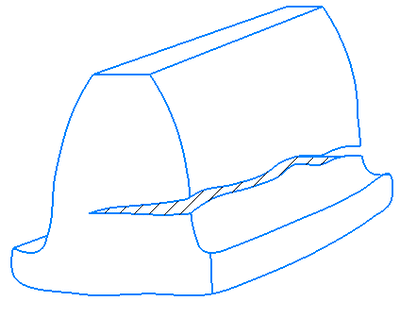
Рисунок 5 – Поломка зуба
Усталостная поломка связана с развитием трещины у основания зуба, где от изгиба возникают наибольшие напряжения растяжения.
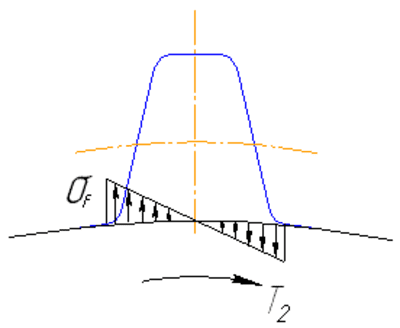
Рисунок 6 – Напряжения на растяжения
При усталостном разрушении на теле колеса после излома остаётся вогнутая, а при поломке от перегрузки – выпуклая поверхность.
Основной причиной выхода из строя зубчатых колес является износ зубьев по рабочей поверхности эвольвентного профиля, который проявляется механическим износом, усталостным выкрашиванием, заеданием и поломкой зубьев вследствие действия напряжений изгиба у основания зуба [4, 10].
4. Методы упрочнения зубчатых колес
Улучшение представляет собой термическую обработку, при которой нагретую до температуры 800–930°С сталь закаливают, т. е. производят быстрое охлаждение в воде или масле до достижения мартенситной структуры. Затем для получения высокой вязкости и пластичности стали производят отпуск после повторного нагрева. При этом, как правило, достигают максимальную твёрдость поверхности зубьев 41 HRC (табл. 1), которая не обеспечивает требуемой долговечности работы зубчатых колёс при высоких нагрузках. Поэтому процесс улучшения очень часто применяют для подготовки сердцевины зуба (твёрдость 33…45 HRC) под последующие азотирование, цементацию или нитроцементацию.
Азотирование и цементация (нитроцементация) относятся к химико-термическoй обработке, которая представляет собой совокупность процессов теплового и химического воздействий, направленных на изменение химического состава и структуры поверхностного слоя зубчатых колёс после их механической обработки. Она характеризуется введением в поверхностный слой металла благодаря химической реакции различных элементов из внешней среды: углерода, азота, кислорода, кремния и др. При этом на поверхности зубчатых колёс образуется твёрдый диффузионный слой, которому свойственно по мере углубления снижение концентрации диффундирующих элементов и микротвёрдости
Азотирование — это процесс насыщения азотом поверхности стали при температуре 500–580°С. В качестве азотосодержащего газа используют аммиак, который при высокой температуре распадается на азот и водород. Температура при азотировании ниже температуры фазовых превращений, поэтому зубчатые колёса имеют незначительные деформации. Азотированию подвергают зубчатые колёса мелкого (m 2 мм) и среднего (m = 2…7 мм) модуля.
Нанесение покрытий на поверхности зубчатых колес имеют основной целью обеспечения свойств наносимого материала (или оксидной пленки наносимого материала) поверхностям зубчатых колес, на которые наносится данный материал. Нанесение покрытий на поверхности зубчатых колес производятся в зависимости от назначения и условий работы соответствующих поверхностей. В зависимости от назначения и исходного материала заготовки зубчатого колеса, выбирают состав наносимого покрытия, способ нанесения и количество наносимого материала. Для повышения износостойкости применяют нитриды титана, для повышения коррозионной стойкости применяют хромоникелевые покрытия, для снижения коэффициента трения на рабочих поверхностях используют покрытия, содержащие бронзу, сплавы олова и графит. В производстве зубчатых колес методы нанесения покрытий не получили широкого применения в качестве метода повышения качества, чаще всего для повышения износостойкости тяжелонагруженных высокоскоростных зубчатых колес. Это связано с необоснованно высокими затратами на выполнение технологического процесса нанесения покрытий. Используемые методы нанесения покрытий, с целью упрощения технологии, в большинстве случаев предполагают нанесение покрытий на всю поверхность изделия. Такой метод в некоторых случаях может привести к снижению параметров качества некоторых зон и участков изделия, поскольку наличие покрытия, не предусмотренного по функциональному назначению, может привести с существенному снижению точности отдельных участков и зон изделия а в некоторых случаях может потребовать дополнительную механическую обработку требуемую вследствие необходимости снятия припуска, образованного покрытием. Большая эффективность достигается при использовании местных покрытий. При этом покрытия наносятся только на рабочие поверхности изделия, а также на прилегающие к ним поверхности, как правило, не принимаю непосредственного участия в процессе работы. В некоторых случаях возможно применение слоистых покрытий, которые обеспечивают выполнение нескольких требований, а также могут адаптировать свойства поверхностей зубчатых колес к условиям эксплуатации.
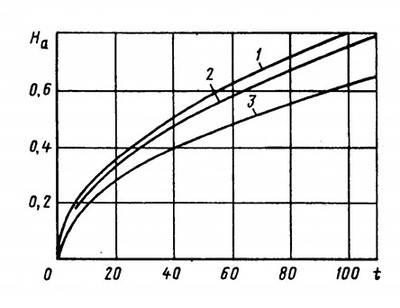
Рисунок 7 – Зависимость глубины азотированного слоя нa от времени t при азотировании зубчатых колёс из сталей: 1-40ХН2 МА; 2-38Х2 Н2 МА; 3-38Х2 МА.
Цементацию — насыщение поверхности углеродом при высоких температурах, применяют для зубчатых колёс из сталей с содержанием углерода 0,10–0,25%. Химико-термическую обработку большинства зубчатых колёс из низко- и среднелегированных сталей производят по схеме, приведённой на рис. 5,а. Температура насыщения составляет 930°С и более. По завершению науглероживания непосредственно с температуры цементации или после незначительного подстуживания (например, для сталей, содержащих менее 2% никеля — 20Х, 25ХГТ, 25ХГМ и др.) выполняют охлаждение (закалку).
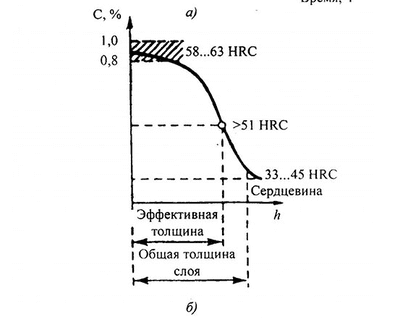
Рисунок 8 – Схемы химико-термического процесса (а) и строения термически упрочнённого поверхностного слоя зубьев (б).
Нитроцементация — это процесс насыщения поверхности стали углеродом и азотом. Для получения необходимых прочностных свойств у стальных зубчатых колес цилиндрических и конических передач преимущественно применяют методы газовой цементации (нитроцементации) в контролируемых эндотермических атмосферах с последующей закалкой в масло [3]. При этом процесс ХТО выполняют в автоматизированных проходных и камерных агрегатах, обладающих высокой производительностью и обеспечивающих полный цикл обработки от нагрева до закалки. Однако практика показала, что применение такой технологии имеет ряд существенных недостатков:
- большой расход атмосферы процесса и высокие затраты на ее изготовление;
- постоянный выброс СО2 и СО в окружающую среду из-за неполного сгорания атмосферы после завершения процесса.
- окисление рабочих поверхностей зубьев колес, которое снижает твердость поверхности зубьев и их контактную прочность;
- большие энергетические расходы и трудоемкость обслуживания оборудования [5, 6, 7].
Термическое упрочнение зубьев
Термическое упрочнение может использоваться как для повышения механических свойств зубчатых колес, так и для повышения параметров качества поверхностного слоя зубьев. Термическим упрочнением достигается повышение предела прочности материала, твердости, ударной вязкости. Также термообработки, наряду с последующей чистовой и отделочной обработкой, способствует снижению абразивного износа, выкрашивания и трещинообразования.
Шестерни, упрочняемые поверхностной закалкой т.в.ч. В зависимости от размеров, модуля и условий работы шестерен применяется несколько вариантов поверхностной закалки при индукционном нагреве. На практике применяется закалка т.в.ч.: со сквозным прогревом зуба; объемно-поверхностная закалка; закалка «по впадине».
Закалка шестерен со сквозным прогревом зуба применяется для скоростных плавно работающих (без ударов), умеренно нагруженных мелкомодульных (4 мм) шестерен. Основным требованием, предъявляемым к таким шестерням, является высокая износостойкость зубьев. Шестерни изготавливаются из среднеуглеродистых низколегированных марок сталей: 45, 40Х, 40ХН и др.
Оптимальная частота тока для равномерного нагрева зубьев и впадин шестерен определяется по формуле: f = 600/m2[кГц], где m- модуль зуба, мм.
Время нагрева обычно составляет 10-40 св зависимости от модуля и габаритов шестерен, температура нагрева должна быть не выше 900 °С. Такие параметры закалки позволяют прогреть насквозь зубчатый венец шестерни и зону под ним. Охлаждение при закалке ведется спрейером или погружением в масло.
Твердость после закалки составляет HRC50-58. После закалки проводится отпуск или самоотпуск, при этом твердость изделия находится в пределах HRC45-50.
Объемно-поверхностная закалка шестерен проводится для изделий с модулем 4-8 мм. Такие шестерни применяются в задних мостах грузовых автомобилей и не уступают по прочности цементованным и нитроцементованным. Шестерни изготавливаются из стали пониженной прокаливаемости марки 58 (55 ПП). Поковки шестерен проходят ПТО, состоящую из ускоренного охлаждения с температуры конца ковки для получения мелкого зерна и последующей нормализации.
Индукционный нагрев осуществляется токами с частотой 2,5-10,0 кГц, время нагрева 20-100 с. Конкретное время нагрева определяется модулем и размерами шестерни. Режим нагрева подбирают так, чтобы размер аустенитного зерна равнялся 10-12 баллам. Время охлаждения при закалке определяется из расчета того, чтобы обеспечить температуру самоотпуска 200-210 °С, что аналогично отпуску в печи при 150-160 °С.
В результате такой обработки при правильно выбранных режимах нагрева и охлаждения по контуру зубьев и впадин создается закаленный на мартенсит слой с твердостью HRC59-61, твердость впадины составляет HRC30-40 и имеет структуру троостита или сорбита закалки.
Поверхностная закалка «по впадине» применяется для крупномодульных шестерен с модулем >8 мм. Такие шестерни изготавливаются из среднеуглеродистых низколегированных марок стали: 40Х, 40ХН. Нагрев под закалку ведется токами с частотой 2,5-10,0 кГц и ограничивается одной впадиной. Так как нагрев ведется впадина за впадиной, то удельная мощность высокочастотной установки не велика и составляет 1,5-2,0 кВт/см. Конфигурация закаленного поверхностного слоя связана с особенностями работы крупномодульных шестерен. На вершине зуба упрочненный слой отсутствует, так как эта зона зуба при работе не подвергается нагрузкам [1, 4].
Зубохонингование и зубошлифование являются процессами чистовой обработки закаленных цилиндрических зубчатых колес с прямыми и косыми зубьями с внешним и внутренним зацеплением.
Если зубья не шлифуются, то точность зубчатого колеса в основном определяется точностью обработки базовых поверхностей. У колес-валов базовые поверхности (шейки, торцы) после термической обработки шлифуют при установке в центрах, которые перед шлифованием зачищают и удаляют забоины. Точные зубчатые колеса-валы правят на прессах с высокой точностью.
Среди чистовых методов обработки зубьев зубошлифование имеет ряд преимуществ. Этот метод обеспечивает самую высокую точность обработки (3—6-ю степень точности) и малую шероховатость поверхности. Шлифование позволяет устранить неизбежные деформации при закалке и производить профильную и продольную модификацию зубьев для повышения эксплуатационных показателей. Зубошлифование широко используют для обработки зубчатых колес авиационной техники; станков, измерительных колес, шеверов, долбяков, накатников и т. д. В настоящее время применяют два метода шлифования цилиндрических зубчатых колес: копирования и обкатки.
Зубохонингование является высокопроизводительным методом, который применяется для уменьшения шероховатости поверхности шевингованных зубчатых колес до Ra = 1,25–0,32 мкм, снижения уровня шума на 2–4 дБ, удаления небольших забоин и заусенцев величиной до 0,3 мм и увеличения срока службы закаленных зубчатых колес после шевингования или зубошлифования. Сущность процесса зубохонингования состоит в том, что абразивный инструмент (косозубый или прямозубый), находясь в плотном зацеплении с обрабатываемым зубчатым колесом (прямозубым или косозубым соответственно), получает вращение и колебательное движение, а обрабатываемое колесо, приводящееся во вращение инструментом, свершает возвратно-поступательное движение.
Кинематическая схема процесса та же, что и при шевинговании,но вместо металлического шевера используется абразивный хон, который изготовляют в виде зубчатого колеса из пластмассы, пропитанной мелкозернистым абразивом. Зацепляется зубчатое колесо с хоном без зазора. Наибольшая эффективность процесса достигается при угле между осями хона и обрабатываемого колеса = 15-18°. Хонингование производится при обильном охлаждении керосином.. Станки для хоншгования во многом аналогичны станкам для шевингования без устройства для радиальной подачи.
Зубополирование
Эту обработку используют для отделки закаленных колес с числом зубьев менее 20 (трибов). Сущность процесса состоит в относительном скольжении профиля деревянного червячного полировального диска, смазанного полировальной пастой, и профиля зуба, сцепляющегося с ним обрабатываемого зубчатого колеса (триба). В результате зубополирования происходит сглаживание микронеровностей и повышается качество поверхности зуба [4, 8].
Выводы
Таким образом в работе выполнен анализ основных эксплуатационных характеристик зубчатых колес и основных причин выхода из строя зубчатых передач. Исследованы основные причины и виды износа рабочих поверхностей зубьев, а также способы позволяющие повысить работоспособность и износостойкость зубчатых колес учитывая условия эксплуатации зубчатой передачи
Список источников
- Технология термической обработки деталей работающих в условиях износа. Методическое пособие. А.А Перебоева -Красноярск, 2007.- 143с.
- Михайлов А. Н. Основы синтеза функционально-ориентированных технологий машиностроения. – Донецк: ДонНТУ, 2008 – 346 с.
- Лахин А. М., Михайлов А. Н., Фомин И. А. Повышение эксплуатационных свойств рабочих элементов зубчатых колес на базе функционально-ориентированного подхода // Прогрессивные технологии и системы машиностроения:Международный сб. научных трудов. – Донецк: ДонНТУ, 2010 Вып. 39 С. 127–132.
- Кудрявцев В. Н. Зубчатые передачи. – М.: Машгис, 1957 – 263 с.
- Термическая обработка в машиностроении. Справочник. Ред. Ю.М. Лахтин, А.Т. Рахштадт. 1985.- 162-166 с.
- Козловский И. С. Химико-термическая обработка шестерен. М.: Машиностроение, 1970. 232 с.
- Зинченко В. М. Инженерия поверхности зубчатых колёс методами химико-термической обработки. М.: Издательство МГТУ им. Н. Э. Баумана, 2001. 302 с.
- Калашников А. С., Моргунов Ю. А., Калашников П. А. Современные методы обработки зубчатых колёс. М.: Издательский дом «Спектр», 2012. 238 с.
- Михайлов А.Н., Михайлов Д.А., Грубка Р.М., Петров М.Г., Повышение долговечности деталей машин на базе функционально-ориентированных покрытий / Наукоемкие технологии в машиностроении. – М.: Машиностроение, №7. 2015. С. 30-39.
- Айрапетов Э. Л., Апархов В. И., Мельникова Т. Н., Филимонова Н. И. Неравномерность распределения статической нагрузки в косозубых и шевронных зубчатых передачах // Вестник машиностроения, 1997. № 10.