Abstract on the topic of graduation work
Content
- Introduction
- 1. Purpose of work
- 2. Relevance
- 3. Requirements for gears
- 4. Gear hardening methods
- Conclusions
- List of sources
Introduction
An urgent task in mechanical engineering today is the design and manufacture of competitive machines and units with high performance. Gears are the most common types of mechanical transmissions. They are widely used in all branches of mechanical engineering, in particular in machine tools, automobiles, tractors, agricultural machines, etc., in instrument making, the watch industry, etc. They are used to transmit power from fractions to tens of thousands of kilowatts at peripheral speeds up to 150 m / s and gear ratios up to several hundred and even thousands, with wheel diameters from fractions of a millimeter to 6 m or more.
1. The purpose of the work
The aim of the work is to improve the quality and performance properties of gears based on the improvement of the stages of finishing and hardening of teeth and the application of functionally oriented coatings.
To achieve this goal, it is necessary to solve the following tasks:
- to analyze the current state of the issue of production and operation of gears;
- to explore the main design features of gears, as well as the parameters of gears, which provide an increase in operational properties;
- to develop a general structure and algorithm for conducting research;
- to propose technological methods for improving the productivity and quality of the finishing and hardening treatment of the working surfaces of the teeth, which provide an increase in the operational characteristics of the gears;
- to develop recommendations aimed at improving the performance of gears.
2. Relevance
The most common gear failure is due to tooth wear. When worn, the tooth changes its original geometric shape, and this, in turn, leads to kinematic inaccuracies, and as a result, to tooth breakage and transmission failure. To reduce wear, the contact surfaces must be made of an antifriction and wear-resistant material, which can be achieved by hardening the tooth surfaces. Currently, there are many ways to improve the wear resistance and durability of gears, but the problem has not been fully resolved and is relevant.
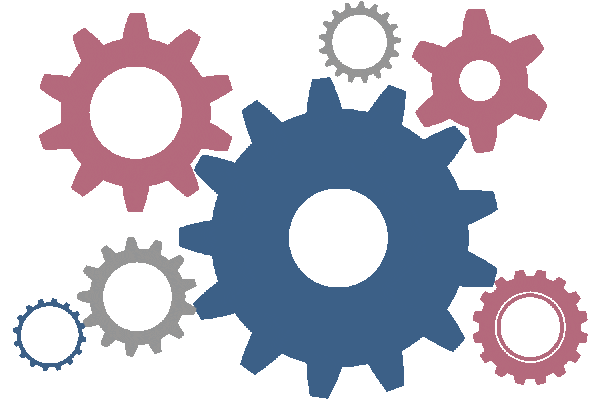
Figure 1 - An example of the transmission of rotational motion of gears
3. Requirements for gears
The main requirements for gears in instrumentation are reduced to obtaining a large gear ratio with small dimensions of the gear mechanism and the need to ensure the most accurate movement of the driven link. Unlike gears used in general mechanical engineering, gears in instrumentation transmit low forces, due to which, in most cases, it is not necessary to calculate the strength of gear elements.
Advantages of gears:
- Ability to use in a wide range of speeds, powers and gear ratios.
- High load capacity and small dimensions.
- Great durability and reliability.
- Gear ratio constancy.
- High efficiency (87-98%).
- Ease of maintenance [4].
Disadvantages of gears:
- High rigidity does not allow compensating for dynamic loads.
- High requirements for manufacturing and installation accuracy.
- Noise at high speeds.
Types of tooth destruction
1. Fatigue chipping of the working surfaces of the teeth is the main type of tooth destruction for most closed, well-lubricated gears. The destruction manifests itself in the form of pockmarks (pits) and begins near the pole line in the zone of single-pair engagement (where the maximum load acts) at the root of the tooth, and then spreads to the entire leg surface. Over time, the pits of chipping merge, progressive chipping begins.
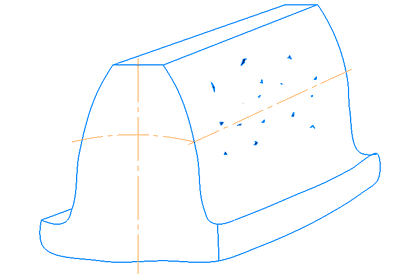
Figure 2 - Fatigue Chipping
2. Abrasive wear is typical for open gears or gears operating in a clogged environment (mining, road, construction and other machines).
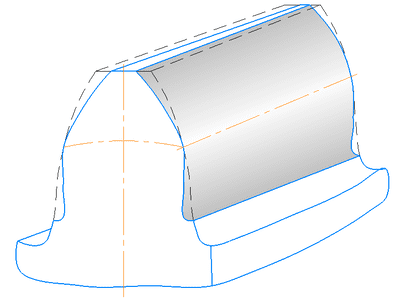
Figure 3 - Tooth wear
3. Tooth seizing is a local molecular adhesion (microwelding) of the mating surfaces of the teeth due to the destruction of the lubricating film and a local increase in temperature during relative sliding in the contact zone.
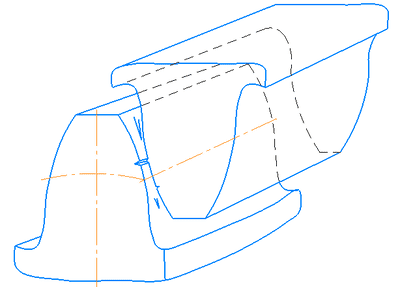
Figure 4 - Jamming
Tooth sticking is prevented by increasing the hardness of surfaces, the selection of extreme pressure oils.
Calculation for seizing comes down to checking the temperature at the points of contact and comparing it with the flash point of the oils.
4. Tooth fracture is the most dangerous type of fracture, because. leads to a complete loss of transmission performance. Tooth breakage is classified as a sudden and complete failure.
Teeth fracture is a consequence of the action from the zero cycle of bending stresses or impact overload.
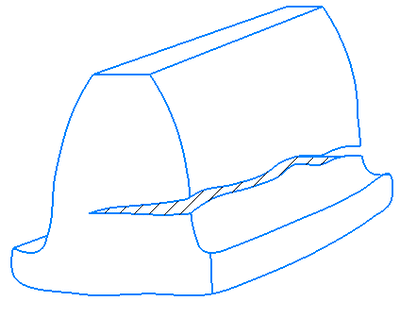
Figure 5 - Broken tooth
Fatigue failure is associated with the development of a crack at the base of the tooth, where the greatest tensile stresses arise from bending.
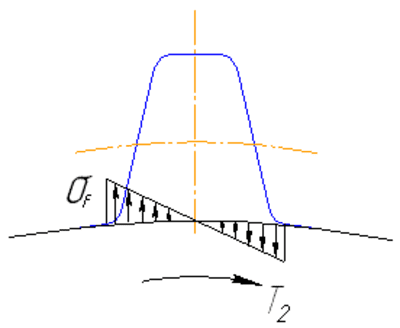
Figure 6 - Tensile Stress
In case of fatigue failure, a concave surface remains on the wheel body after a fracture, and in case of overload damage, a convex surface.
The main cause of gear failure is wear of the teeth along the working surface of the involute profile, which is manifested by mechanical wear, fatigue chipping, jamming and breakage of the teeth due to the action of bending stresses at the base of the tooth [4, 10].
4. Gear hardening methods
Improvement is a heat treatment, in which steel heated to a temperature of 800–930 ° C is quenched, i.e., it is rapidly cooled in water or oil until a martensitic structure is achieved. Then, to obtain high toughness and ductility, the steel is tempered after reheating. In this case, as a rule, the maximum hardness of the tooth surface is 41 HRC (Table 1), which does not provide the required durability of the gears under high loads. Therefore, the improvement process is very often used to prepare the core of the tooth (hardness 33 ... 45 HRC) for subsequent nitriding, cementation or nitrocarburizing.
Nitriding and carburizing (nitrocarburizing) refer to chemical-thermal treatment, which is a combination of processes of thermal and chemical influences aimed at changing the chemical composition and structure of the surface layer of gears after their mechanical processing. It is characterized by the introduction into the surface layer of the metal due to the chemical reaction of various elements from the external environment: carbon, nitrogen, oxygen, silicon, etc. At the same time, a solid diffusion layer is formed on the surface of the gears, which tends to decrease the concentration of diffusing elements and microhardness as it deepens. p>
Nitriding is the process of saturating the steel surface with nitrogen at a temperature of 500–580°C. Ammonia is used as a nitrogen-containing gas, which at high temperature decomposes into nitrogen and hydrogen. The temperature during nitriding is below the temperature of phase transformations, so the gears have minor deformations. Nitriding is subjected to gear wheels of small (m 2 mm) and medium (m = 2 ... 7 mm) modules.
Coating the surfaces of gears has the main purpose of providing the properties of the applied material (or the oxide film of the applied material) to the surfaces of the gears to which this material is applied. The application of coatings on the surfaces of gears is carried out depending on the purpose and operating conditions of the respective surfaces. Depending on the purpose and source material of the gear blank, the composition of the coating to be applied, the method of application and the amount of material to be applied are selected. Titanium nitrides are used to increase wear resistance, chromium-nickel coatings are used to increase corrosion resistance, and coatings containing bronze, tin alloys and graphite are used to reduce the coefficient of friction on working surfaces. In the gear industry, coating methods have not been widely adopted as a quality improvement method, most commonly for improving the wear resistance of heavily loaded high speed gears. This is due to unreasonably high costs for the technological process of coating. The coating methods used, in order to simplify the technology, in most cases involve coating the entire surface of the product. In some cases, this method can lead to a decrease in the quality parameters of some zones and sections of the product, since the presence of a coating that is not provided for its functional purpose can lead to a significant decrease in the accuracy of individual sections and zones of the product, and in some cases it may require additional machining required due to the need removal of the allowance formed by the coating. Greater efficiency is achieved with the use of local coatings. In this case, coatings are applied only on the working surfaces of the product, as well as on the surfaces adjacent to them, as a rule, I do not take a direct part in the work process. In some cases, it is possible to use layered coatings that meet several requirements, and can also adapt the properties of the surfaces of the gears to the operating conditions.
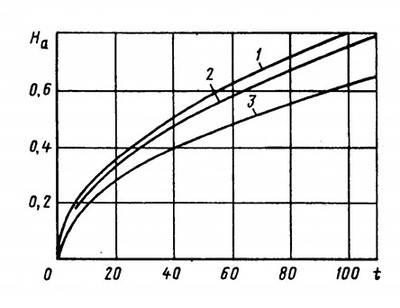
Figure 7 - Dependence of the depth of the nitrided layer na on time t when nitriding gears made of steels: 1-40XH2 MA; 2-38X2 H2 MA; 3-38X2 MA.
Cementation - saturation of the surface with carbon at high temperatures, used for gears made of steels with a carbon content of 0.10–0.25%. Chemical-thermal treatment of most gears made of low- and medium-alloy steels is carried out according to the scheme shown in Fig. 5, a. The saturation temperature is 930°C or more. Upon completion of carburization, directly from the carburizing temperature or after slight cooling (for example, for steels containing less than 2% nickel - 20X, 25KhGT, 25KhGM, etc.), cooling (quenching) is performed.
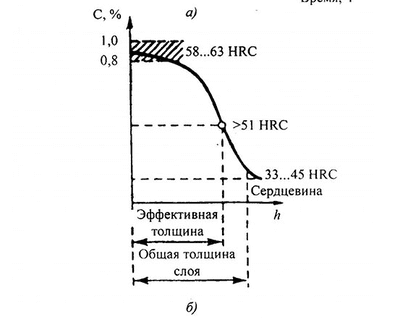
Figure 8 - Schemes of the chemical-thermal process (a) and the structure of the thermally hardened surface layer of the teeth (b).
Nitrocarburizing is the process of saturating the steel surface with carbon and nitrogen. To obtain the necessary strength properties for steel gears of spur and bevel gears, gas carburizing (nitrocarburizing) methods are mainly used in controlled endothermic atmospheres, followed by oil quenching [3]. At the same time, the CTO process is carried out in automated through-flow and chamber units, which have high productivity and provide a complete processing cycle from heating to hardening. However, practice has shown that the use of this technology has a number of significant drawbacks:
- high consumption of the atmosphere of the process and high costs for its manufacture;
- constant release of CO2 and CO into the environment due to incomplete combustion of the atmosphere after the completion of the process.
- oxidation of the working surfaces of the teeth of the wheels, which reduces the hardness of the surface of the teeth and their contact strength;
- high energy costs and laborious maintenance of equipment [5, 6, 7].
Heat hardening of the teeth
Thermal hardening can be used both to improve the mechanical properties of gears and to improve the quality parameters of the surface layer of the teeth. Thermal hardening achieves an increase in the tensile strength of the material, hardness, impact strength. Also, heat treatment, along with subsequent finishing and finishing, helps to reduce abrasive wear, chipping and cracking.
Gears hardened by surface hardening Depending on the size, module and operating conditions of the gears, several options for surface hardening during induction heating are used. In practice, hardening is used, including: with through heating of the tooth; volume-surface hardening; hardening "in the hollow".
Hardening of gears with through tooth heating is used for high-speed smoothly running (without impacts), moderately loaded fine-module (4 mm) gears. The main requirement for such gears is high wear resistance of the teeth. Gears are made of medium-carbon low-alloy steel grades: 45, 40X, 40XH, etc.
The optimal current frequency for uniform heating of the teeth and gear cavities is determined by the formula: f = 600/m2[kHz], where m is the tooth modulus, mm.
The heating time is usually 10-40 s, depending on the module and the dimensions of the gears, the heating temperature should not exceed 900 °C. Such hardening parameters make it possible to heat through the gear ring and the area under it. Cooling during hardening is carried out by spraying or immersion in oil.
The hardness after hardening is HRC50-58. After hardening, tempering or self-tempering is carried out, while the hardness of the product is within HRC45-50.
Volume-surface hardening of gears is carried out for products with a module of 4-8 mm. Such gears are used in the rear axles of trucks and are not inferior in strength to carburized and nitrocarburized ones. Gears are made of low hardenability steel grade 58 (55 PP). Gear forgings go through PHT, which consists of accelerated cooling from the temperature of the end of the forging to obtain fine grains and subsequent normalization.
Induction heating is carried out by currents with a frequency of 2.5-10.0 kHz, heating time 20-100 s. The specific heating time is determined by the module and the dimensions of the gear. The heating mode is selected so that the size of the austenite grain is 10-12 points. The cooling time during hardening is determined on the basis of ensuring a self-tempering temperature of 200-210 ° C, which is similar to tempering in a furnace at 150-160 ° C.
As a result of such processing, with correctly selected heating and cooling modes, a martensite-hardened layer with hardness HRC59-61 is created along the contour of the teeth and cavities, the cavity hardness is HRC30-40 and has the structure of troostite or hardening sorbite.
Surface hardening "in the valley" is used for large-modulus gears with a modulus> 8 mm. Such gears are made of medium-carbon low-alloy steel grades: 40X, 40XH. Heating for hardening is carried out by currents with a frequency of 2.5-10.0 kHz and is limited to one cavity. Since heating is carried out cavity after cavity, the specific power of the high-frequency installation is not high and amounts to 1.5–2.0 kW/cm. The configuration of the hardened surface layer is associated with the features of the operation of large-modulus gears. There is no hardened layer at the top of the tooth, since this zone of the tooth is not subjected to loads during operation [1, 4].
Gear honing and gear grinding are finishing processes for hardened spur gears with straight and helical teeth with external and internal meshing.
If the teeth are not ground, then the accuracy of the gear wheel is mainly determined by the accuracy of the processing of the base surfaces. At wheel-shafts, the base surfaces (necks, ends) after heat treatment are ground when installed in centers that clean and remove nicks before grinding. Precise gears-shafts rule on presses with high precision.
Among the finishing methods of gear processing, gear grinding has a number of advantages. This method provides the highest processing accuracy (3-6th degree of accuracy) and low surface roughness. Grinding allows you to eliminate the inevitable deformations during hardening and produce profile and longitudinal modification of the teeth to improve performance. Gear grinding is widely used for the processing of gear wheels for aircraft; machine tools, measuring wheels, shavers, cutters, knurlers, etc. Currently, two methods of grinding cylindrical gears are used: copying and running.
Gear honing is a high-performance method that is used to reduce the surface roughness of shaving gears to Ra = 1.25–0.32 µm, reduce noise levels by 2–4 dB, remove small nicks and burrs up to 0.3 mm in size, and increase the service life of hardened gears after shaving or gear grinding. The essence of the process of gear honing is that the abrasive tool (helical or spur), being in close engagement with the machined gear (spur or helical, respectively), receives rotation and oscillatory motion, and the machined wheel, driven by the tool, performs a reciprocating movement.
The kinematic scheme of the process is the same as in shaving, but instead of a metal shaver, an abrasive hone is used, which is made in the form of a gear wheel made of plastic impregnated with fine-grained abrasive. The gear wheel engages with the hone without clearance. The highest efficiency of the process is achieved at an angle between the axes of the hone and the machined wheel = 15-18°. Honing is carried out with abundant cooling with kerosene. Honing machines are in many ways similar to shaving machines without a radial feed device.
Tooth polishing
This treatment is used to finish hardened wheels with less than 20 teeth (pinions). The essence of the process is the relative sliding of the profile of a wooden worm polishing disc, lubricated with polishing paste, and the profile of a tooth that engages with it the gear being processed (tribe). As a result of tooth polishing, microroughnesses are smoothed out and the quality of the tooth surface is improved [4, 8].
Conclusions
Thus, the paper analyzes the main operational characteristics of gears and the main causes of failure of gears. The main causes and types of wear of the working surfaces of the teeth, as well as ways to improve the performance and wear resistance of gears, taking into account the operating conditions of the gear, have been studied
List of sources
- Heat treatment technology for wear parts. Toolkit. A.A Pereboeva - Krasnoyarsk, 2007.- 143p.
- Mikhailov AN Fundamentals of synthesis of functionally oriented engineering technologies. - Donetsk: DonNTU, 2008 - 346 p.
- Lakhin A. M., Mikhailov A. N., Fomin I. A. Improving the performance properties of working elements of gear wheels based on a function-oriented approach // Progressive technologies and Engineering Systems: International Sat. scientific works. - Donetsk: DonNTU, 2010 Issue. 39 pp. 127–132.
- Kudryavtsev V. N. Gears. – M.: Mashgis, 1957 – 263 p.
- Heat treatment in mechanical engineering. Directory. Ed. Yu.M. Lakhtin, A.T. Rakhstadt. 1985.- 162-166 p.
- Kozlovsky I. S. Chemical-thermal treatment of gears. M.: Mashinostroenie, 1970. 232 p.
- Zinchenko VM Engineering of gear wheels surface by chemical-thermal treatment methods. M.: Publishing house of MSTU im. N. E. Bauman, 2001. 302 p.
- Kalashnikov AS, Morgunov Yu. A., Kalashnikov PA Modern methods of processing gears. M.: Spektr Publishing House, 2012. 238 p.
- Mikhailov A.N., Mikhailov D.A., Grubka R.M., Petrov M.G., Increasing the durability of machine parts based on functionally oriented coatings / Science-intensive technologies in mechanical engineering. - M .: Mashinostroenie, No. 7. 2015. S. 30-39.
- Ayrapetov E. L., Aparkhov V. I., Melnikova T. N., Filimonova N. I. Uneven distribution of static load in helical and chevron gears // Bulletin of mechanical engineering, 1997. No. 10.