Реферат по темі випускної роботи
Зміст
- Вступ
- 1. Мета роботи
- 2. Актуальність
- 3. Вимоги до зубчастих передач
- 4. Методи зміцнення зубчастих коліс
- Висновки
- Список джерел
Вступ
Актуальним завданням у машинобудуванні на сьогоднішній день є проектування та виготовлення конкурентоспроможних машин та агрегатів з високими експлуатаційними характеристиками. Зубчасті передачі є найпоширенішими типами механічних передач. Вони знаходять широке застосування у всіх галузях машинобудування, зокрема в металорізальних верстатах, автомобілях, тракторах, сільгоспмашинах і т.д., у приладобудуванні, годинниковій промисловості та ін. Їх застосовують для передачі потужностей від часток до десятків тисяч кіловат при окружних швидкостях до 150 м/с та передавальних числах до кількох сотень і навіть тисяч, з діаметром коліс від часток міліметра до 6 м і більше.
1. Мета роботи
Метою роботи є підвищення якості та експлуатаційних властивостей зубчастих коліс на основі вдосконалення етапів обробки та зміцнення обробки зубів та нанесення функціонально-орієнтованих покриттів.
Для досягнення поставленої мети необхідно вирішити такі завдання:
- виконати аналіз сучасного стану питання виробництва та експлуатації зубчастих коліс;
- дослідити основні конструктивні особливості зубчастих передач і параметрів зубчастих коліс, які забезпечують підвищення експлуатаційних властивостей;
- розробити загальну структуру та алгоритм проведення досліджень;
- запропонувати технологічні методи підвищення продуктивності та якості обробної та зміцнюючої обробки робочих поверхонь зубів, що забезпечують підвищення експлуатаційних характеристик зубчастих коліс;
- розробити рекомендації, спрямовані на підвищення експлуатаційних характеристик зубчастих передач.
2. Актуальність
Найчастіше вихід із ладу зубчастого колеса пов'язаний із зносом зубів. При зношуванні зуб змінює свою початкову геометричну форму, а це, у свою чергу, призводить до кінематичної неточності, а як наслідок до поломки зуба і виходу передачі з ладу. Для зменшення зносу поверхні контакту повинні бути виконані з антифрикційного та зносостійкого матеріалу, що може бути досягнуто за рахунок зміцнення обробки поверхонь зубів. В даний час існує багато способів підвищення зносостійкості та довговічності зубчастих передач, але проблема не вирішена до кінця і є актуальною.
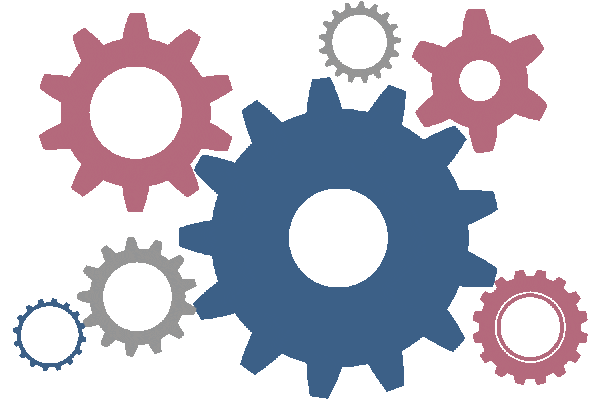
Малюнок 1 – Приклад передачі обертального руху зубчастих коліс
3. Вимоги до зубчастих передач
Основні вимоги до зубчастих передач у приладобудуванні зводяться до отримання великого значення передавального числа при малих габаритах передавального механізму та до необхідності забезпечення найбільш точного переміщення веденої ланки. На відміну від зубчастих передач, що застосовуються у загальному машинобудуванні, зубчасті передачі в приладобудуванні передають малі зусилля, завдяки чому в більшості випадків не потрібно розраховувати елементи зубчастих передач на міцність.
Достоїнства зубчастих передач:
- Можливість застосування у широкому діапазоні швидкостей, потужностей та передавальних відносин.
- Висока здатність навантаження і малі габарити.
- Велика довговічність та надійність роботи.
- Стійність передавального відношення.
- Високий ККД (87-98%).
- Простота обслуговування [4].
Недоліки зубчастих передач:
- Велика жорсткість не дозволяє компенсувати динамічні навантаження.
- Високі вимоги до точності виготовлення та монтажу.
- Шум при великих швидкостях.
Види руйнування зубів
1. Втомне фарбування робочих поверхонь зубів – основний вид руйнування зубів для більшості закритих, добре змащуваних передач.Руйнування проявляється у вигляді оспинок (ямок) і починається поблизу полюсної лінії в зоні однопарного зачеплення (де діє максимальне навантаження) у ніжки зуба, а потім поширюється на всю поверхня ніжки. Згодом ямки фарбування зливаються, починається прогресивне фарбування.
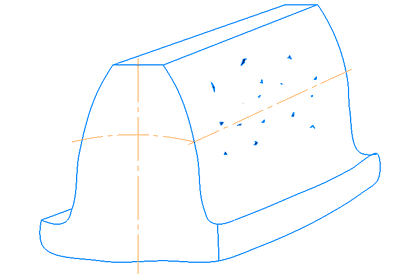
Малюнок 2 – Втомне вифарбовування
2. Абразивне зношування характерне для відкритих передач або передач, що працюють у засміченому середовищі (гірські, дорожні, будівельні та інші машини).
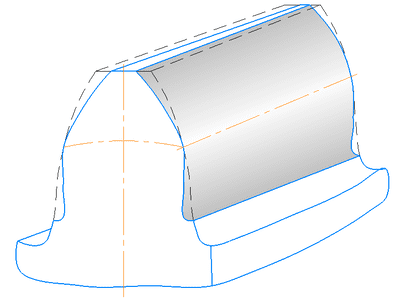
Малюнок 3 – Зношування зубів
3. Заїдання зубів – місцеве молекулярне зчеплення (мікрозварювання) сполучених поверхонь зубів внаслідок руйнування мастильної плівки та місцевого підвищення температури при відносному ковзанні в зоні контакту.
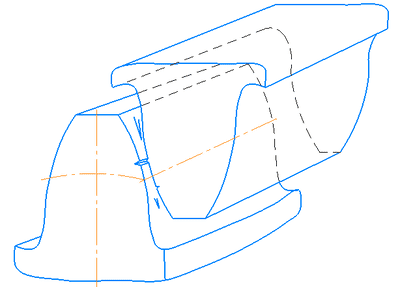
Малюнок 4 – Заїдання зубів
Заїдання зубів попереджають підвищенням твердості поверхонь, підбором протизадирних масел.
Розрахунки на заїдання зводяться до перевірки температури в місцях контакту та зіставлення її з температурою спалаху масел.
4. Злам зубів є найнебезпечнішим видом руйнації, т.к. призводить до повної втрати працездатності передачі. Поломку зубів відносять до категорії раптових та повних відмов.
Злам зубів є наслідком дії від нульового циклу напруг вигину або перевантаження ударної дії.
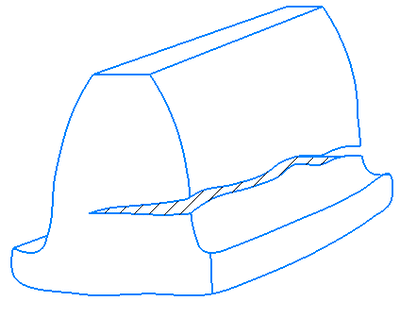
Малюнок 5 – Поломка зуба
Утомна поломка пов'язана з розвитком тріщини біля основи зуба, де від вигину виникають найбільші напруження розтягування.
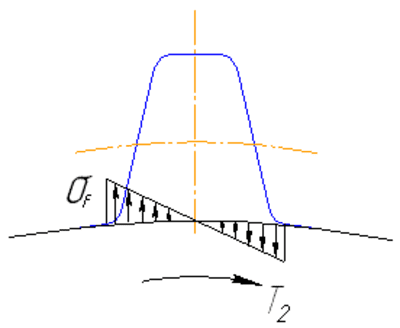
Малюнок 6 – Напруги на розтягування
При втомному руйнуванні на тілі колеса після зламу залишається увігнута, а при поломці від перевантаження – опукла поверхня.
Основною причиною виходу з ладу зубчастих коліс є зношування зубів по робочій поверхні евольвентного профілю, який проявляється механічним зношуванням, втомним вифарбовуванням, заїданням і поломкою зубів внаслідок дії напружень вигину біля основи зуба [4, 10].
4. Методи зміцнення зубчастих коліс
Поліпшення являє собою термічну обробку, при якій нагріту до температури 800–930°С сталь гартують, тобто виробляють швидке охолодження у воді чи олії до досягнення мартенситної структури. Потім для отримання високої в'язкості та пластичності сталі виробляють відпустку після повторного нагріву. При цьому зазвичай досягають максимальну твердість поверхні зубів 41 HRC (табл. 1), яка не забезпечує необхідної довговічності роботи зубчастих коліс при високих навантаженнях. Тому процес покращення дуже часто застосовують для підготовки серцевини зуба (твердість 33...45 HRC) під наступні азотування, цементацію або нітроцементацію.
Азотування та цементація (нітроцементація) відносяться до хіміко-термічної обробки, яка є сукупністю процесів теплового та хімічного впливів, спрямованих на зміну хімічного складу та структури поверхневого шару зубчастих коліс після їх механічної обробки. Вона характеризується введенням у поверхневий шар металу завдяки хімічній реакції різних елементів із зовнішнього середовища: вуглецю, азоту, кисню, кремнію та ін. >
Азотування — це процес насичення азотом поверхні сталі за нормальної температури 500–580°С. Як азотовмісний газ використовують аміак, який при високій температурі розпадається на азот і водень. Температура при азотуванні нижче температури фазових перетворень, тому зубчасті колеса мають незначні деформації. Азотування піддають зубчасті колеса дрібного (m 2 мм) та середнього (m = 2…7 мм) модуля.
Нанесення покриттів на поверхні зубчастих коліс мають основну мету забезпечення властивостей матеріалу, що наноситься (або оксидної плівки матеріалу, що наноситься) поверхням зубчастих коліс, на які наноситься даний матеріал. Нанесення покриттів на поверхні зубчастих коліс виконуються залежно від призначення та умов роботи відповідних поверхонь. Залежно від призначення і вихідного матеріалу заготовки зубчастого колеса, вибирають склад покриття, спосіб нанесення і кількість матеріалу, що наноситься. Для підвищення зносостійкості застосовують нітриди титану, підвищення корозійної стійкості застосовують хромонікелеві покриття, зниження коефіцієнта тертя на робочих поверхнях використовують покриття, містять бронзу, сплави олова і графіт. У виробництві зубчастих коліс методи нанесення покриттів не отримали широкого застосування як метод підвищення якості, найчастіше для підвищення зносостійкості важконавантажених високошвидкісних зубчастих коліс. Це з необгрунтовано високими витратами виконання технологічного процесу нанесення покриттів. Методи нанесення покриттів, що використовуються, з метою спрощення технології, в більшості випадків припускають нанесення покриттів на всю поверхню виробу. Такий метод може призвести до зниження параметрів якості деяких зон і ділянок виробу, оскільки наявність покриття, не передбаченого за функціональним призначенням, може призвести до істотного зниження точності окремих ділянок і зон виробу, а в деяких випадках може вимагати додаткову механічну обробку, необхідну внаслідок необхідності. зняття припуску, утвореного покриттям. Велика ефективність досягається при використанні місцевих покриттів. При цьому покриття наносяться тільки на робочі поверхні виробу, а також прилеглі до них поверхні, як правило, не приймаю безпосередньої участі в процесі роботи. У деяких випадках можливе застосування шаруватих покриттів, які забезпечують виконання кількох вимог, а також можуть адаптувати властивості поверхонь зубчастих коліс до умов експлуатації.
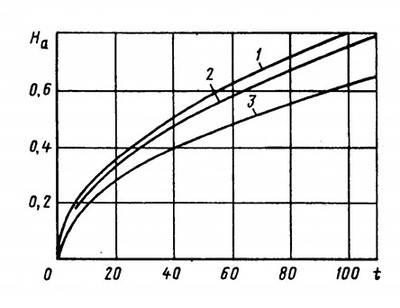
Малюнок 7 - Залежність глибини азотованого шару на час t при азотуванні зубчастих коліс зі сталей: 1-40ХН2 МА; 2-38Х2 Н2 МА; 3-38Х2 МА.
Цементацію — насичення поверхні вуглецем за високих температур, застосовують для зубчастих коліс із сталей із вмістом вуглецю 0,10–0,25%. Хіміко-термічну обробку більшості зубчастих коліс із низько- та середньолегованих сталей виробляють за схемою, наведеною на рис. 5,а. Температура насичення становить 930°С і більше. Після завершення навуглерожування безпосередньо з температури цементації або після незначного підстуджування (наприклад, для сталей, що містять менше 2% нікелю — 20Х, 25ХГТ, 25ХГМ та ін.) виконують охолодження (загартування).
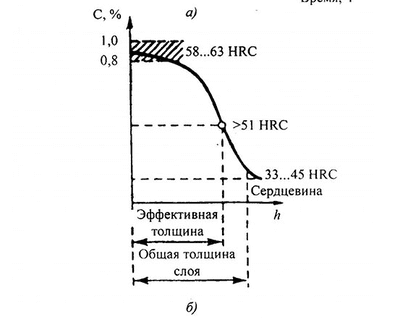
Малюнок 8 – Схеми хіміко-термічного процесу (а) та будови термічно зміцненого поверхневого шару зубів (б).
Нітроцементація – це процес насичення поверхні сталі вуглецем та азотом. Для отримання необхідних властивостей міцності у сталевих зубчастих коліс циліндричних і конічних передач переважно застосовують методи газової цементації (нітроцементації) в контрольованих ендотермічних атмосферах з подальшим загартуванням в масло [3]. При цьому процес ХТО виконують в автоматизованих прохідних і камерних агрегатах, що мають високу продуктивність і забезпечують повний цикл обробки від нагрівання до загартування. Однак практика показала, що застосування такої технології має низку істотних недоліків:
- велика витрата атмосфери процесу та високі витрати на її виготовлення;
- постійний викид СО2 та СО в навколишнє середовище через неповне згоряння атмосфери після завершення процесу.
- окислення робочих поверхонь зубів коліс, яке знижує твердість поверхні зубів та їх контактну міцність;
- великі енергетичні витрати та трудомісткість обслуговування обладнання [5, 6, 7].
Термічне зміцнення зубів
Термічне зміцнення може використовуватися як для підвищення механічних властивостей зубчастих коліс, так і для підвищення параметрів якості поверхневої кулі зубів. Термічним зміцненням досягається підвищення межі міцності матеріалу, твердості, ударної в'язкості. Також термообробка, поряд з подальшою чистовою та обробною обробкою, сприяє зниженню абразивного зношування, фарбування та тріщиноутворення.
Шестірні, що зміцнюються поверхневим загартуванням у т.ч. Залежно від розмірів, модуля та умов роботи шестерень застосовується кілька варіантів поверхневої закали при індукційному нагріванні. На практиці застосовується загартування в т.ч.ч.: зі скрізним прогріванням зуба; об'ємно-поверхневе загартовування; загартування «по западині».
Гартування шестерень із наскрізним прогріванням зуба застосовується для швидкісних плавно працюючих (без ударів), помірно навантажених дрібномодульних (4 мм) шестерень. Основною вимогою до таких шестерень є висока зносостійкість зубів. Шестерні виготовляються із середньовуглецевих низьколегованих марок сталей: 45, 40Х, 40ХН та ін.
Оптимальна частота струму для рівномірного нагрівання зубів і западин шестерень визначається за формулою: f = 600/m2[кГц], де m-модуль зуба, мм.
Година нагрівання зазвичай становить 10-40 св залежно від модуля і габаритів шестерень, температура нагрівання повинна бути не вище 900 °С. Такі параметри гарту дозволяють прогріти наскрізь зубчастий вінець шестірні та зону під ним. Охолодження при загартуванні ведеться спрейєром або зануренням у олію.
Твердість після загартовування становить HRC50-58. Після гарту проводитися відпустка або самовідпустка, при цьому твердість виробу знаходиться в межах HRC45-50.
Об'ємно-поверхневе загартування шестерень проводиться для виробів з модулем 4-8 мм. Такі шестірні застосовуються в задніх мостах вантажних автомобілів і не поступаються міцністю цементованим і нітроцементованим. Шестерні виготовляються зі сталі зниженої прожарюваності марки 58 (55 ПП). Поковки шестерень проходять ПТО, що складається з прискореного охолодження температури кінця кування для отримання дрібного зерна і подальшої нормалізації.
Індукційне нагрівання здійснюється струмами з частотою 2,5-10,0 кГц, час нагрівання 20-100 с. Конкретний час нагрівання визначається модулем та розмірами шестерні. Режим нагріву підбирають так, щоб розмір аустенітного зерна дорівнював 10-12 балів. Час охолодження при загартуванні визначається з розрахунку того, щоб забезпечити температуру самовідпустки 200-210 °С, що аналогічно до відпустки в печі при 150-160 °С.
В результаті такої обробки при правильно вибраних режимах нагрівання та охолодження по контуру зубів і западин створюється загартований на мартенсит шар з твердістю HRC59-61, твердість западини становить HRC30-40 і має структуру трооститу або сорбіту загартування.
Поверхневе загартування «по западині» застосовується для великомодульних шестерень з модулем >8 мм. Такі шестерні виготовляються із середньовуглецевих низьколегованих марок сталі: 40Х, 40ХН. Нагрів під загартування ведеться струмами з частотою 2,5-10,0 кГц і обмежується однією западиною. Оскільки нагрівання ведеться западина за западиною, то питома потужність високочастотної установки невелика і становить 1,5-2,0 кВт/см. Конфігурація загартованого поверхневого шару пов'язана з особливостями роботи шестерень великомодульних. На вершині зуба зміцнений шар відсутній, оскільки ця зона зуба під час роботи не піддається навантаженням [1, 4].
Зубохонінгування та зубошліфування є процесами чистової обробки загартованих циліндричних зубчастих коліс із прямими та косими зубами із зовнішнім та внутрішнім зачепленням.
Якщо зубці не шліфуються, то точність зубчастого колеса в основному визначається точністю обробки базових поверхонь. У коліс-валів базові поверхні (шийки, торці) після термічної обробки шліфують при встановленні в центрах, які перед шліфуванням зачищають і видаляють вибоїни. Точні зубчасті колеса-вали правлять на пресах із високою точністю.
Серед чистових методів обробки зубів зубошліфування має низку переваг. Цей метод забезпечує найвищу точність обробки (3-6 ступінь точності) і малу шорсткість поверхні. Шліфування дозволяє усунути неминучі деформації при загартуванні та проводити профільну та поздовжню модифікацію зубів для підвищення експлуатаційних показників. Зубошліфування широко використовують для обробки зубчастих коліс авіаційної техніки; верстатів, вимірювальних коліс, шеверів, довбаків, накатників і т. д. В даний час застосовують два методи шліфування циліндричних зубчастих коліс: копіювання та обкатки.
Зубохонінгування є високопродуктивним методом, який застосовується для зменшення шорсткості поверхні шевінгованих зубчастих коліс до Ra = 1,25–0,32 мкм, зниження рівня шуму на 2–4 дБ, видалення невеликих вибоїн та задирок величиною до 0,3 мм та збільшення терміну служби загартованих зубчастих коліс після шевінгування чи зубошліфування. Сутність процесу зубохонінгування полягає в тому, що абразивний інструмент (косозубий або прямозубий), перебуваючи в щільному зачепленні з оброблюваним зубчастим колесом (прямозубим або косозубим відповідно), отримує обертання і коливальний рух, а оброблюване колесо, що приводиться в обертання інструментом рух.
Кінематична схема процесу та ж, що і при шевінгуванні,але замість металевого шеверу використовується абразивний хон, який виготовляють у вигляді зубчастого колеса із пластмаси, просоченої дрібнозернистим абразивом. Зчепляється зубчасте колесо з хоном без зазору. Найбільша ефективність процесу досягається при куті між осями хону і оброблюваного колеса = 15-18 °. Хонінгування проводиться при рясному охолодженні гасом.
Зубополірування
Цю обробку використовують для обробки загартованих коліс із числом зубів менше 20 (трибів). Сутність процесу полягає у відносному ковзанні профілю дерев'яного черв'ячного полірувального диска, змазаного полірувальною пастою, і профілю зуба, що зчепляється з ним зубчастого колеса, що обробляється (триба). В результаті зубополірування відбувається згладжування мікронерівностей і підвищується якість поверхні зуба [4, 8].
Висновки
Таким чином у роботі виконано аналіз основних експлуатаційних характеристик зубчастих коліс та основних причин виходу з ладу зубчастих передач. Досліджено основні причини та види зносу робочих поверхонь зубів, а також способи, що дозволяють підвищити працездатність та зносостійкість зубчастих коліс враховуючи умови експлуатації зубчастої передачі
Список джерел
- Технологія термічної обробки деталей, що працюють в умовах зносу. Методичний посібник. А.А Перебоєва-Красноярськ, 2007. - 143с.
- Михайлов А. Н. Основи синтезу функціонально-орієнтованих технологій машинобудування. – Донецьк: ДонНТУ, 2008 – 346 с.
- Лахін А. М., Михайлов А. Н., Фомін І. А. Підвищення експлуатаційних властивостей робочих елементів зубчастих коліс на базі функціонально-орієнтованого підходу // Прогресивні технології та системи машинобудування: Міжнародний зб. наукових праць. - Донецьк: ДонНТУ, 2010 Вип. 39 С. 127-132.
- Кудрявцев В. Н. Зубчасті передачі. - М.: Машгіс, 1957 - 263 с.
- Термічна обробка в машинобудуванні. Довідник ред. Ю.М. Лахтін, А.Т. Рахштадт. 1985. - 162-166 с.
- Козловський І. С. Хіміко-термічна обробка шестерень. М: Машинобудування, 1970. 232 с.
- Зінченко В. М. Інженерія поверхні зубчастих коліс методами хіміко-термічної обробки. М.: Видавництво МДТУ ім. Н. Е. Баумана, 2001. 302 с.
- Калашніков А. С., Моргунов Ю. А., Калашніков П. А. Сучасні методи обробки зубчастих коліс. М: Видавничий дім «Спектр», 2012. 238 с.
- Михайлов А.М., Михайлов Д.А., Грубка Р.М., Петров М.Г., Підвищення довговічності деталей машин на базі функціонально-орієнтованих покриттів / Наукоємні технології у машинобудуванні. - М.: Машинобудування, №7. 2015. С. 30-39.
- Айрапетов Е. Л., Апархов В. І., Мельникова Т. Н., Філімонова Н. І. Нерівномірність розподілу статичного навантаження в косозубих та шевронних зубчастих передачах // Вісник машинобудування, 1997. №10.