Реферат по теме выпускной работы
Содержание
- Введение
- 1. Анализ факторов, оказывающих негативное влияние на окружающую среду в условиях работы дуговых печей литейных цехов
- 1.1 Газопылевые выбросы при производстве стали в электродуговых печах малой вместимости
- 1.2 Способы эвакуации газопылевых выделений из рабочей зоны малотоннажных электродуговых печей и оценка эффективности их функционирования
- 1.3 Разработка мероприятий, направленных на повышение эффективности работы систем удаления выбросов из дуговых печей, эксплуатируемых в литейных цехах
- 1.4 Цель и задачи исследований
- 2. Совершенствование конструкции и обоснование параметров механизма поворота зонта системы газоотсоса малотоннажной электродуговой печи
- 2.1 Описание усовершенствованной системы газоотсоса
- 2.2 Конструктивные особенности предложенного механизма поворота зонта дуговой печи зонта дуговой печи
- 2.3 Расчет энергосиловых параметров модернизированного привода механизма поворота зонта
- 3. Экспериментальная проверка правильности технических решений, заложенных в конструкцию усовершенствованного механизма поворота зонта
- 3.1 Конструирование и изготовление действующей модели малотоннажной дуговой печи для проведения лабораторных исследований
- 3.2 Методика проведения модельных экспериментов и анализ полученные результаты
- Выводы
- Список источников
Введение
Электрические печи для выплавки стали в условиях литейного производства являются наиболее распространенными технологическими агрегатами. В них выплавляют широкий сортамент литейных сталей, предназанченных для получения отливок разной массы. При этом, как известно образуется насыщенные пылью газы, оакзывающие негативное влияние на экологическую ситуацию и условия труда в производственных помещениях.
Основное количество газа выходит через зазоры между отверстиями свода и электродами, а также рабочего окна. Газы выделяются из электропечей не только в процессе плавки, но и во время загрузки печи и слива готовой стали в ковш. В связи с ужесточением требований экологичекой безопасности относительно количества выбросов вредных веществ в атмосферу, в полседние годы появилась потребность в совершенствовании существующих систем газоулавливания и газоочистки с целью повышения эффективности их функционирования в условиях литейного производства.
Особую актуальность составляет задача, связанная с разработкой систем газоотсоса для электродуговых печей малой тоннажности (до 10 т), эксплуатируемых в литейных цехах машиностроительных предприятий. Речь идет о печах, оборудованных устаревшими системами газоотсоса и газоочистки. Поэтому тема баклаврской работы, связанной с разработкой мероприятий, направленных на модернизацию систем газоотсоса малотоннажных электродуговых печей с целью повышения эффективности их функционирования, имеет важное практическое значение.[1]
1.1 Газопылевые выбросы при производстве стали в электродуговых печах малой вместимости
В процессе выплавки стали в электродуговых печах температура металла может доходить до 2500 - 3000°С, что влечет за собой выгорание электродов и испарение железа, кремнезема, глинозема, марганца и других элементов, содержащихся в металлическом расплаве.
В состав газов, по литературным данным входит 5—70% СО, 5—15% С02, 0,5 - 5% Н2, 3 - 10% О2, остальное N2. Запыленность газа, зависящее от качества шихты может составить от 2 до 10 г/м3(н) без продувки ванны кислородом и от 14 до 100 г/м3 при его применении.
Дисперсный состав пыли следующий: Размер частиц, мкм <5 5-10 10-20 20-44 >44Содержание, % (по массе) 71,9-67,9 8,3-6,8 9,8-6 9-7,5 6,5-6,3 Дисперсность пыли резко возрастает в случае применения кислорода. При этом содержание возгонов достигает 85 - 95% [2]. Приведенная информация свидетельствует о насущной необходимости установке на электродуговых печах систем эвакуации и очистки отходящих печных газов.
1.2 Способы эвакуации газопылевых выделений из рабочей зоны малотоннажных электродуговых печей и оценка эффективности их функционирования
Выплавка стали в электропечах протекает за счет тепла электрической дуги, возбуждаемой между электродами.
Для улавливания и отвода газа, выделяющегося от электропечей, нашли широкое применение следующие устройства [3]. Установку над электропечью специального зонта рисунок 1, полностью перекрывающего в плане свод печи.[2]
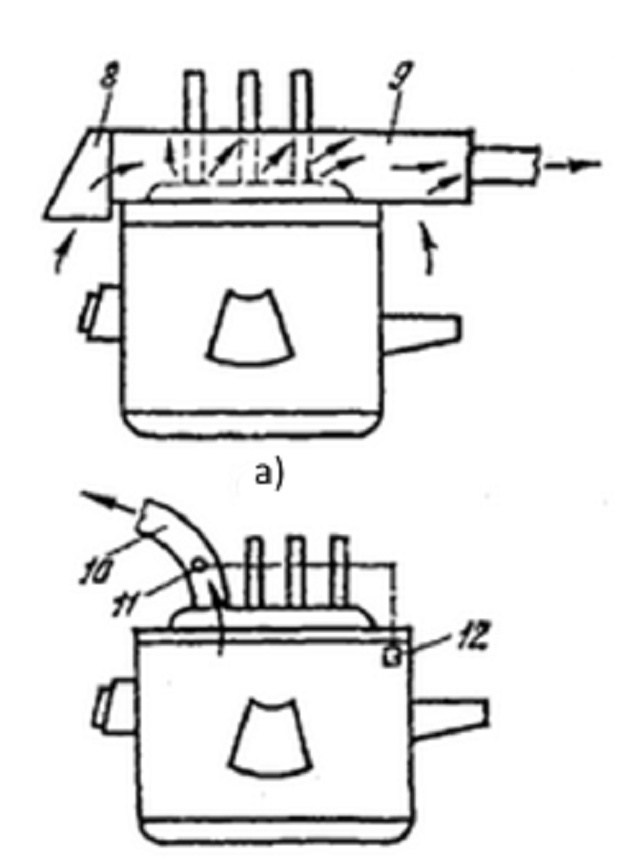
Рисунок 1 – Система отвода газа от электропечей с использованием зонта
Секционный отсос рисунок 2 представляет со¬бой усовершенствованное укрытие.
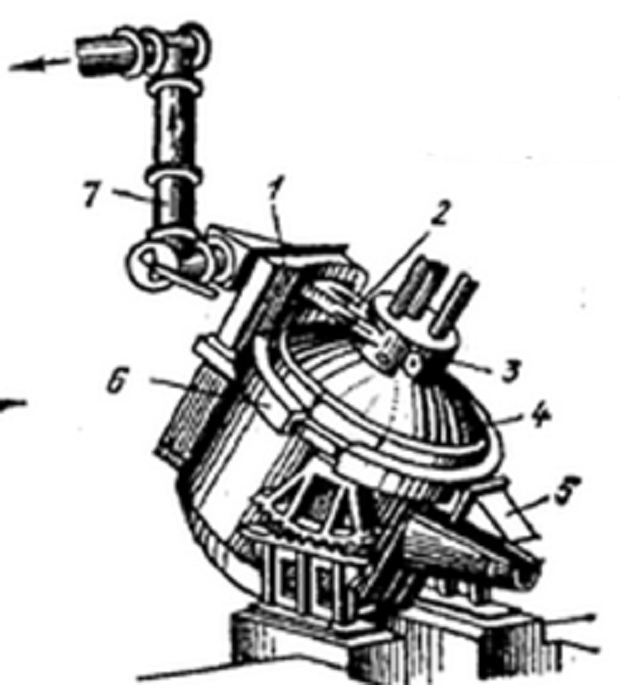
Рисунок 2 – Система секционного газоотсоса
Отвод газа непосредственно из свода печи рисунок 3. В своде печи выполняют специальное отверстие, через которое при помощи водоохлаждаемого патрубка 10, соединенного шарнирно с газоотводящим газопроводом, отсасывают газ, образующийся в процессе плавки стали.
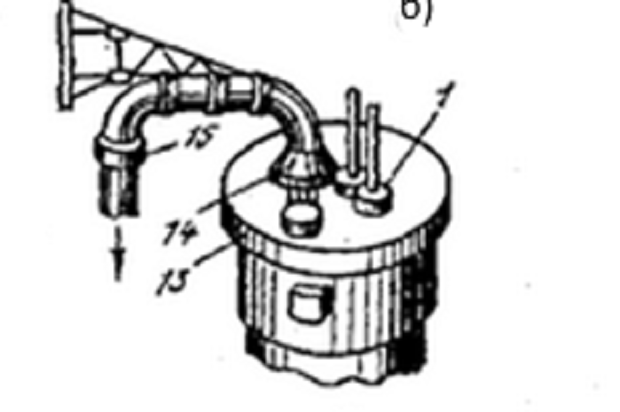
Рисунок 3 – Способ отвода газа из свода дуговой электропечи
1.3 Разработка мероприятий, направленных на повышение эффективности работы систем удаления выбросов из дуговых печей, эксплуатируемых в литейных цехах
Очистку газов, отводимых от электродуговых, осуществляют при помощи специальных пылеуловителей, электрофильтров, тканевых филь-тров и других аппаратных средств.
При применении скоростных пылеуловителей газ после дожигания направляют в полый скруббер, где происходит его охлаждение и грубая очистка от пыли.
Мокрый электрофильтр используют после дожигания газа в камере дожигания и охлаждения в полом скруббере при температуре ~250° С. При отсосе газа через свод печи обычно регулируют производительность и напор эксгаустера, так как в процессе плавки количество газовыделеиий из печи меняется.[4-9]
Для повышения степени очистки отходящих от печи выбросов на практике применяют несколько типов сдвоенных систем очистки, предусматривающих установку очистного оборудования как на самой печи, так и после зонта, установленного под фонарем на крыше производственного здания рисунок 4.
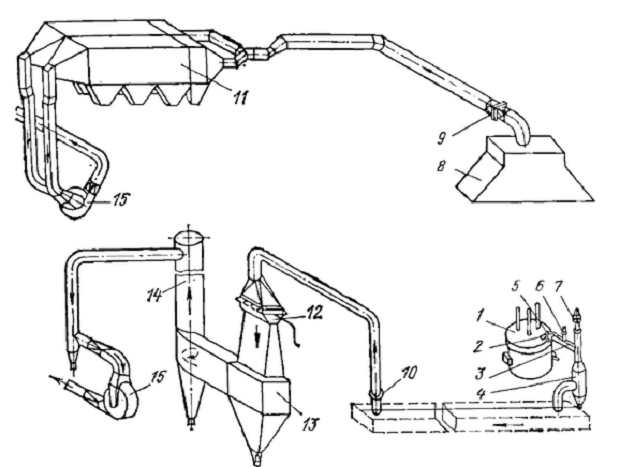
Рисунок 4 – Схема совмещенной очистки газов, отводимых от электропечи и через зонт под фонарем цеха
Опыт эксплуатации подобных установок показал, что наиболее трудоёмкими операциями являются замена гибких рукавов, которую приходится выполнять из-за их разрывов в нижнем креплении (30%) и по шву (30 – 35 %), а также в следствие забивания неотряхиваемым слоем пыли (35 – 40 %).
1.4 Цель и задачи исследований
Цель исследования – совершенствование конструкции и обоснование параметров системы газоотсоса малотоннажной электродуговой печи литейного цеха.
Для достижения поставленной цели необходимо решить следующие задачи:
- Предложить рациональное техническое решение по совершенствованию системы газоотсоса электродуговой печи литейного цеха с целью устранения узких мест
- Обосновать энергосиловые параметры усовершенствованного механизма поворота улавливающего зонта дуговой печи.
- Проверить на действующей модели механизма поворота зонта печи правильность принятых технических решений.
- Оценить технико-экономическую эффективность от внедрения модернизированной системы газоотсоса электродуговой печи литейного цеха.
2.1 Описание усовершенствованной системы газоотсоса
Предлагаемая система отсоса (эвакуации) газа и пыли образующихся в электродуговых печах литейного цеха во время выплавки стали включает зонт, располагаемый на рабочей площадке плавильного агрегата и снабженный модернизированным механизмом его поворота, а также посредством отводящего тракта круглого сечения связанный с входом рукавного фильтра.[11]
В системе предусмотрена установка двух одинаковых дымососов ДН 12,5, один из которых является рабочим, а второй – резервным. Дымососы могут работать раздельно и одновременно, для чего они снабжены шиберными заслонками, каждая из которых переводится в положение закрыто, если соответствующий дымосос выведен в резерв.[13]
2.2. Конструктивные особенности предложенного механизма поворота зонта дуговой печи зонта дуговой печи
С учетом результатов выполненного сопоставительного анализа показателей работы существующих систем газоотсоса малотоннажных дуговых печей разработали усовершенствованную конструкцию механизма поворота улавливающего зонта.
2.3. Расчет энергосиловых параметров модернизированного привода механизма поворота зонта
Для расчета энергосиловых параметров привода механизма поворота зонта воспользуемся методикой, предложенной сотрудниками кафедры МОЗЧМ ДонНТУ и опубликованной в работе.
Момент сопротивления повороту вытяжного зонта состоит из статических моментов трения в центрирующих и опорных роликах, а также сопротивления в песочном затворе:
Мс = (Мсц+Мсо)kз,
где Мсц – момент сопротивления от трения в центрирующих роликах;
Мсо – момент сопротивления от трения в опорных роликах;
kз – коэффициент, учитывающий трение в песочном затворе.
Во время пуска привода на него дополнительно действует динамический могмент МД, поэтому общий момент сопротивления:
Мо = Мс + МД.
Динамический момент сопротивления определяют по известной формуле
где I – момент инерции вытяжного зонта относительно оси его поворота;
- угловая скорость зонта;
tп ? время пуска привода, которое принимается согласно
рекомендациям ВНИИПТмаша, tп=1с.
3.1 Конструирование и изготовление действующей модели малотоннажной дуговой печи для проведения лабораторных исследований
С целью проверки правильности итехнических решений, заложенных в конструкцию модернизированного механизма поворота зонта ситстемы газоотсоса 5-тонной дуговой печи изготовили ее действующую модель, выполненную в масштабе 1:10.
Данная модель печи, снабженная системой газоотсоса, позволяла в точности имитировать работу натурного образца печи и проверить в динамике функционирование ее системы газоотсоса.
3.2 Методика проведения модельных экспериментов и анализ полученные результаты
Для измерения силы, передаваемой рычагом модели механизма поворота улавливающего зонта использовали контрольно-измерительный комплекс, включавший тензорезисторный преобразователь, усилитель переменного тока, аналого-цифровой преобразователь и ЭВМ с печатающим устройством.
Тензорезисторный преобразователь включал два рабочих фольговых датчика, наклеенные на поверхность рычага вдоль оси симметрии и два компенсационных, которые располагались перпендикулярно рабочим.
Предварительно выполнили тарировку тензорезисторного преобразователя последовательного нагружения подвешенного рычага грузами с известной массой и фиксацией соответствующих им амплитуд сигнала в кодах АЦП.
По полученным результатам построили график тарировочной зависимости (рис. 3.5) и оценили обеспечиваемую точность измерений.
В соответствии с планом эксперимента предполагалось изучение характера изменения нагрузок, действующих на элементы модели механизма поворота улавливающего зонта при его переводе из одного крайнего положения в другое, а также определение доли момента сопротивления повороту зонта, связанного с трением в узлах песочного затвора.
Модельные исследования работы предложенного механизма поворота улавливающего зонта электродуговой печи провели по методике, рекомендованной в работах.
Полученные данные обрабатывали с использованием графика тарировочной зависимости.
Результаты обработки экспериментальных данных свидетельствуют о том, что суммарная сила сопротивления, вызванная трением в нижнем и верхнем песочных затворах при переводе улавливающего зонта из одного крайнего положения в другое, достигает 25 % от общей технологической нагрузки, действующей на исполнительный механизм.[10]
Выводы
1. На основании результатов анализа состояния вопроса, связанного с проблемой эввакуации газо-пылевых выделений из рабочего пространства электродуговых печей малой тоннажности, эксплуатируемых в литейных цехах машиностроительных заводов, установлено, что главным фактором, отрицательно влияющим на эффективность работы систем газоотсоса, является попадание в окружающее пространство мелкодисперсной пыли и газов в узлах сочленения подвижных соединений.
2. Для обеспечения надежной работы системы газоотсоса предложено снабдить механизм поворот зонта песочными затворами.
3. Теоретическим путем обоснованы конструктивные и энергосиловые параметры механизма поворота зонта. В результате расчёта энергосиловых параметров привода поворота вытяжного зонта установлено, что наибольший момент сопротивления на выходном валу мотор-редуктора возникает при повороте зонта на 18? из исходного положения и составляет МСрmax = 792,4 Н•м; максимальное усилие в тяге возникает в начале поворота зонта из исходного положения и составляет Fmax = 1956,5 Н; расчётная мощность привода Nр = 557 Вт.
4. На действующей физической модели 5-тонной дуговой, изготовленной в масштабе 1:10, выполнена проверка правильности принятых технических решений и справедливость полученных расчетных зависимостей для определения рабочих параметров усовершенствованной системы газоотсоса, предложенной для использования в условиях литейного цеха Ясиноватского машиностроительного завода.
5. Результаты обработки экспериментальных данных свидетельствуют о том, что суммарная сила сопротивления, вызванная трением в нижнем и верхнем песочных затворах при переводе улавливающего зонта из одного крайнего положения в другое, достигает 25 % от общей технологической нагрузки, действующей на исполнительный механизм. Информация, полученная расчетным путем при определении составляющих суммарного момента сопротивления повороту полой консоли, несущей улавливающий зонт, свидетельствует о том, что суммарная доля моментов, обусловленных трением в обоих песочных затворах, доходит до 23 % от общего момента. Таким образом, можно говорить о достаточно хорошей сходимости расчетных и опытных данных.
6. Общие экономические затраты на внедрение выполненной разработки составят …… рублей.
7. Внедрение в производство модернизированного механизма поворота вытяжного зонта системы газоотсоса маллотоннажной электродуговой печи позволит сократить в значительной мере количество выбрасываемых в окружающее пространство газо- пылевых выделений, что позволит улучшить условия труда работников литейных цехов и эклогическую обстановку вблизи них.
Список источников
- Киселев, А.Д. Повышение эффективности газоудаления дуговых сталеплавильных печей / А.Д. Киселев, Ю.Н. Тулуевский, И.Ю. Зинуров .- М.: Металлургия, 1992. 112 с.
- Осипенко, В.Д. Отвод и обеспыливание газов дуговых сталеплавильных печей / В.Д. Осипенко, А.П. Егорычев, Б.Н. Максимов .- М.: Металлургия, 1985. - 104 с.
- Алиев, Г.М.. Техника пылеулавливания и очистки промышленных газов. Справ. изд. М.: Металлургия, 1986. – 544 с.
- Старк, С.Б. Газоочистные аппараты и установки в металлургическом производстве: Учебник для вузов. Изд. 2-е, перераб. и доп. М.: Металлургия, 1990. -400 с.
- Букач, Б.Ф. Рациональная система удаления газов из крупнотоннажных ДСП / Б.Ф. Букач, А.Г. Нотыч // Освоение новых высокомощных электропечей: Темат. Сб. научн. Тр. МЧМ СССР. (НИИМ). -М.: Металлургия, 1982. С. 20-23.
- Рахметова, Э.Р. Разработка системы очистки отходящих газов от электродуговых печей литейного цеха и мер повышения экологического производства // Всероссийский форум научной молодежи «богатство России»: Сб. докладов.- М.: Московский государственный технический университет им. Н.Э. Баумана, 2018.- С. 275 – 276.
- Павлович, Л.Б. Оценка экологического риска от выбросов литейного производства в атмосферу / Л.Б. Павлович. В.В. Садыхова, Д.А. Шульдишова // Вестник Сибирского государственного индустриального университета.- 2014.- № 4 (10).- С. 52 – 55.
- Речкалов А.В. Основные требования к дуговым печам, выплавляющим металл для производства литья / А.В. Речкалов [и др.] // Электрометаллургия.- 2014.- № 11.- С. 2 – 5.
- Крутянский, М.М. Расчет газовыделений из дуговых печей постоянного и переменного тока в литейном цехе / М.М. Крутянский, С.М. Нехамим, Е.М. Ребиков // Электрометаллургия.- 2016.- № 7.- С. 27 – 34.
- Соловьев, В.П. Проектирование новых и реконструкция действующих литейных цехов: Учебное пособие. / В.П. Соловьев, С.А. Гладышев, В.И. Воронцов .- М.: МИСиС, 2004.- 227 с.
- Дробитько, М.Ю. Системы очистки отходящих газов плавки и их использование в литейном производстве / М.Ю. Дробитько [и др.] .-М.: Машиностроение, 2004.- 198 с.
- Расчёты грузоподъёмных и транспортирующих машин / Ф.К. Иванченко [и др.].-К.:Высш.шк.,1978. - 576с.
- Сталинский, Д.В. Газоочистка малотоннажных электросталеплавильных печей в литейном цехе // Д.В. Сталинский [и др.] // Металлургическая и горнорудная промышленность.- 2016.- № 6.- С.100 – 105.
- Еронько, С.П. Совершенствование конструкции и модельные исследования работы системы газоотсоса электродуговой печи литейного цеха / С.П. Еронько [и др.] // Известия вузов. Черная металлургия.- 2019.- № 1.- С. 34 – 41.
- Eron’ko S.P.Improving the Gas-Exhaust System at Foundry Electrofurnaces / S.P. Eron’ko [e.a.] // ISSN 0967-0912, Steel in Translation, 2019, Vol. 49, № 1, pp. 7 – 12.
- Инновационные комплексные решения по очистке отходящих газов в черной металлургии. Технические решения для очистки высокотемпературных газовых потоков / Б.Л. Красный [и др.] // Черная металлургия: Бюл. ин-та «Черметинформация» 2021.- Т. 77. № 2.- С.200 – 208.